Metallic materials of frequent use in aeronautical sector component manufacturing sector component manufacturing: light alloys To the-Li
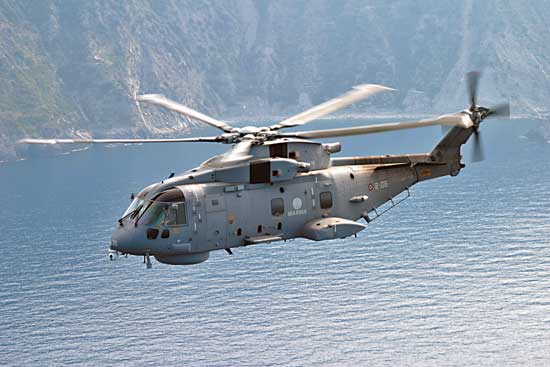
The first quotations on alloys To the-Li date of the year 1920 in Germany but did not go until 1957 when they appeared the first alloys standardised. In this year an alloy containing lithium and baptised like X2020 used for the structure of a small military aeroplane experimental designated RA-SCA in United States. The main reason of his application was the low density and high rigidity of the material but later the alloy withdrew of the production because of technical problems identified when analysing the behaviour of the alloy in conditions of service. They detected problems related with the segregation of some phases in the microstructure of the material, low tenacity and ductility, and the learning of intermetálicos fragile and phenomena of cizalladura of the precipitated To the3Li by the movement of the dislocaciones.
To beginnings of the decade of the 70 and related with the crisis of the oil renewed the interest by the light alloys and set up new projects of investigation related with the To the-Li. They analysed the problems of the previous alloys and investigated in new compositions with a minor contained in lithium and greater presence of copper and/or magnesium. It analysed in depth the relation between the microstructure and the final properties as well as the behaviour of the distinct alloys in front of the thermal sensors treatments By a part appeared a series of new alloys in Russia under the numbering 1400 and finally in 1983 two of the greater producers of alloys of aluminium for the aerospace industry, the British Alcan and the North American Alcoa, announced the introduction of new alloys of To the-Li. 2090, 8090, 8091, etc.
The practical whole of the products manufactured at present with alloys To the-Li are products conformed due to the fact that the high reactivity of the lithium in state melted does unfeasible the manufacture of products by smelting to industrial level and only exist references of some products manufactured by smelting to the stray wax.
The main characteristics of the lithium regarding his utilisation like element aleante in alloys of aluminium are the following:
- The lithium is the lightest of the metallic elements (density 0,534 g/cm3) and his addition to alloys of aluminium reduces the density of the same of considerable way. Adding 1% of lithium arrives to reduce 3% the density of the alloy
- The addition of lithium produces a considerable increase of the rigidity of the material because of the learning of a phase put stable. The addition of 1% of lithium can arrive to suppose an increase of 6% in the module of elasticity of the material.
- Forms to his time other phases with the aluminium and the greater part of the elements aleantes common in alloys of aluminium like the Mg, Cu or Zr (To the3Li, To the2CuLi, To the6CuLi3). These phases produce an effect reforzante of the alloy when preventing the movement of the dislocaciones without a big detriment of the tenacity.
- The addition of lithium favours the soldabilidad of the alloy of aluminium.
- Of general form can say that the addition of lithium provides better resistance to high temperatures that the obtained by the addition of the Zn in alloys To the-Zn like the 7075 with which compete.
- The behaviour of the alloys To the-Li to low temperatures is excellent and thus it has been used for the construction of cryogenic tanks.
- Of general form can affirm that the resistance to fatigue of the alloys To the-Li is upper to the ones of the alloys To the-Zn.
- The resistance to the corrosion of the alloys To the-Li is elevated after the application of the suitable thermal sensors treatment.
In definite, the combination of the low density of the alloys To the-Li, his conformabilidad and his excellent balance of mechanical properties does that it was an ideal candidate for applications in the fuselaje of aeroplanes and helicopters
Against split also exist a series disadvantages or negative factors that it is necessary to consider to the hour to select alloys of To the-Li for a determinate application.
- The price of the lithium is high compared with other elements aleantes common in alloys of aluminium (Zn, Cu, Mg etc.) and in consequence the alloys that contain lithium are between 2-4 more expensive times that other conventional alloys.
- The tenacity of the alloys is not elevated in comparison to alloys To the-Zn.
- The mechanical properties of the alloys To the-Li are very sensitive to the homogeneity of the microstructure and composition
- The lithium is a highly reactive element and toxico by what the manipulation of the lithium in the manufacture of the alloy and the back manipulation of the alloy in operations of mechanised or recycled has to take into account this factor.
Giving a review to the history of this type of alloys, the alloy X2020 produced in United States in the years 50 was the first alloy of commercial aluminium containing lithium. It was an alloy of the series 2000 that contained 3% of lithium and besides 4% of copper, a 0,5 % of manganese and Cadmium like elements aleantes main. Simultaneously they developed alloys To the-Mg-Li in Russia such as the alloys 1429, 1420 and 1421 and from 1964 the Russian company Kumz has gone developing new alloys used mainly by the Russian aerospace industry. These alloys however presented a ductility and tenacity too low and in the following years developed a new generation of To the-Li pertaining to the series 2000 (To the-Cu-Mg-Li-Zr) and 8000 (To the-Li-Cu-Zr) in which it reduced the concentration of lithium until 2%.
The most known alloys of this second generation are probably the 8090 (To the-Li-Cu-Mg), 2090 and Weldalite 049 manufactured by Alcan, Alcoa and Pechiney. They are alloys commercially available at present although they are being progressively substituted by the new generation of alloys To the-Li.
The alloy 8090 presents a composition Li - 2,45, Zr - 0,12, Cu - 1,3, Mg - 0,95. It was developed to compete with the alloys To the-Cu like the 2024 in front of which presents 10% less than density and 11% more than rigidity. In addition to this presented a substantial improvement of the behaviour in cryogenic temperatures. The alloy is available in shape of plates, tubes extracted and forges and can use in applications soldered. The alloy 2090 presents a composition Cu - 2,7, Li - 2,2, Ag - 0,4, Zr -0,12. And it developed like alternative to the alloy 7075.-T6 in front of which presents 8% less than density and 10% more than rigidity. The new alloy offered besides a better behaviour in front of the corrosion in essays realised simulating a marine environingingment. It was registered in 1984 and since have developed a big number of specific thermal sensors treatments. It presents some characteristics that suits to remark. By a part presents an anisotropy of the properties to upper traction to the conventional alloys as well as an excellent behaviour in front of the growth of crack in fatigue, the need of an operation of work in frio to obtain his optimum properties.
Later developed the alloy 2091 thought to replace to the alloy 2024-T3 in front of which presented some similar improvements in addition to a greater tenacity.
The alloy Weldalite 049 presents a composition Cu - 5,4, Li - 1,3, Ag – 0,4, Mg - 0,4, Zr - 0,14. It is an alloy that presents like main characteristic his big soldabilidad. It presents besides a big mechanical resistance in diverse states of temper. It is an alloy with a very elevated answer in front of the natural aging after a stage of cold work (treatment T3) but also to a treatment of type T4 without the endurecimiento by means of the pulled in frio (cold work).
Later have been the two big multinationals of the industry of the aluminium, Alcan and Alcoa those that have continued in the investigation of new alloys of To the-Li directed mainly to the needs of the aeronautical sector component manufacturing sector component manufacturing industry and to compete with materials like the compound materials reinforced with fibre of carbon for the manufacture of fuselajes and profiles extruidos of the new models of aeroplane. The new alloys like the AA2094, AA2096, AA2097, AA2099, AA2199, AA2196, AA2197, AA2198 and AA2050 are based in the combination of the elements Cu-Li-Mg-Ag-Zr and present characteristics of a big conformabilidad and improvement in the tenacity and ductility.
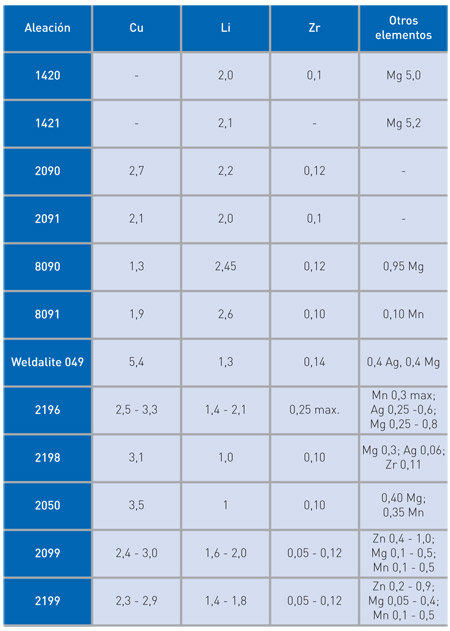
The last generation of the alloys To the-Li presents a lower relation Cu/Li in comparison to the previous alloys. They belong to the system To the-Cu-Li-Mg and present also witnesses of some elements aleantes additional like the silver, zirconium and manganese. The most remarkable examples are the alloys 2050 of plates of half thickness-high that has been selected by Airbus and Bombardier for his utilisation in the aeroplanes Airbus 350 XWB and of the series C respectively. The alloy 2196 in shape of alloys extruidas and the 2198 that presents in shape of sheet manufactured by the company Alcan and the alloys, 2099 and 2199 of Alcoa.
These alloys present a conformabilidad and characteristic upper mechanics to the alloys precedents because of the intense work realised to control the microstructure of the alloys and the corresponding thermal sensors treatments.
Exists a high variety regarding the form and dimensions of the materials supplied and the quantity of applicable thermal sensors treatments is also very high having to study each application individually.
The table 2 presents some values of typical mechanical properties alcanzables by these materials.
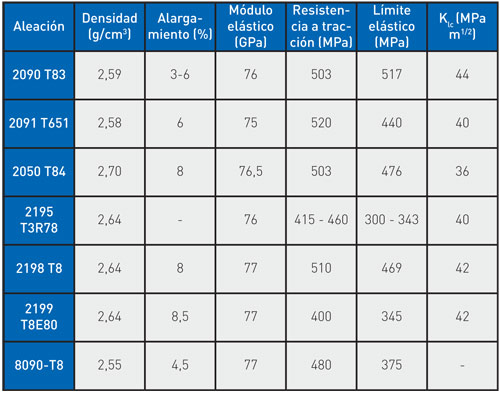
The alloys of aluminium that contain lithium are treatable térmicamente and present a microstructure and a sequence of precipitation of phases during the thermal sensors treatment very complex because of the presence of different phases put stable. The diagram of phases calculated of the binary alloy To the-Li is simple but, however, complicates when they go in at stake elements like the Cu, Mg or zirconium in the alloy.
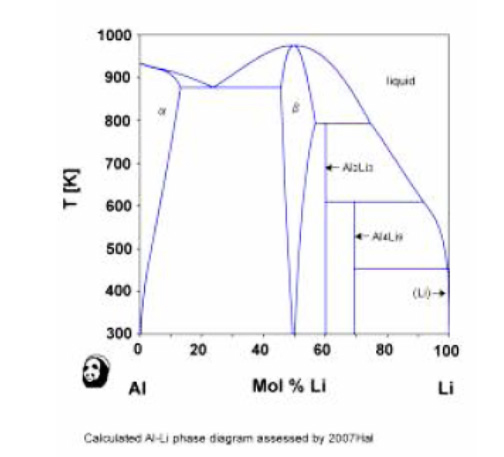
Depending on the application of the alloys can promote , by means of the selection of the concentration of the elements aleantes and the convenient thermal sensors treatment, the apparition of other phases like the phase T2 (To the6CuLi3) to achieve an additional increase of the tenacity or particles of To the2CuMg that form the phase S'.
To continuation details the most important paper of the elements aleantes main:
The zirconium adds to the alloys of To the-Li to form dispersoides that act like inhibidores of the re crystallisation. With the end to present a finer microstructure and a better behaviour in front of fatigue.
By his part the manganese adds by the increase of the resistance of the alloy that comports when adding in inferior levels to 5%.
Also forms dispersoides incoherent with the copper To the20Cu2Mn3 that improve the tenacity and behaviour to fatigue of the alloys through mechanisms of homogenisation of the movement of slide of the dislocaciones.
The alloys To the-Li modern present also the presence of one some quantity of cinc to improve the properties in front of the corrosion of the alloys and magnesium to improve the mechanical resistance.
The incorporation of the magnesium and the silver in alloys To the-Li-Cu is based in the effects known of these two elements aleantes in the alloys of To the- Cu and has showed that have a paper determinante in the answer to the treatment of aging and in consequence to the maximum resistance in alcanzable. The combination of 1,3% of lithium with the magnesium and silver can suppose an increase of 100% in the elastic limit of the alloy.
Until the year 2005 the applications of the alloys To the-Li had restricted to his utilisation in military applications for fighter jets, cryogenic tanks and space applications such as the utilisation of the alloy 2195 in the external tank of the lanzaderas space of the NASA. The low density of the alloys and his mechanical properties had attracted the interest of other sectors like the one of the commercial aviation but his high cost joined to some doubts arisen on characteristics of resistance to the corrosion, tenacity and ductility that presented the first generations of the alloys To the-Li developed prevented his application on a large scale.
Later the development of new alloys created by the big producing companies of aluminium like answer to the threat of other alternative materials like the materials composed of organic matrix and the increase in the mechanical requests of the new generations of aeroplanes like the Airbus 350 or the Boeing 787 have gone back to update the interest of the aerospace industry in the alloys aluminium-lithium.
The utilisation of materials composed of organic matrix has increased drastically in models like the Airbus To380, To350XWB and the Boeing 787 but present the disadvantage of his cost. So much the prime matter as especially the need to adapt the equipment and the installations to the manufacture, union, mechanised and repair of the materials composed of organic matrix advanced supposes an important extra cost. To this it is necessary to add the problems of recycled of the thermostable polymers used. Like this, the industry of the aluminium has seen in the development of the alloys of To the-Li an opportunity to counter the advance of the materials composed for the manufacture of the fuselaje and structural elements in the aeroplanes and thus in the last five years have commercialised new alloys to answer to this threat.
To continuation will review some examples of utilisation of this type of materials.
In the aeronautical sector component manufacturing sector component manufacturing sector, whereas the company Boeing evaluated the possibility to use alloys To the-Li in his future projects realising finally an important bet by the compound materials reinforced with fibre of carbon that will be the basic material in the construction of the fuselaje of his model 787 Dreamliner, the another aeronautical sector component manufacturing sector component manufacturing giant, Airbus, seems by the contrary have bent by other materials for the fuselajes of his next aeroplanes and the alloys of To the-li of last generation have a big possibility. They exist in fact programs of companies like Airbus or Bombardier in where they have selected alloys like the 2050 or the 2196 and that are already in phase of manufacture.
By his part Airbus decided to build the section of the fuselaje of the cabin in aluminium-lithium in front of the monolithic structure in fibre of carbon that had been evaluated previously. The main technical reasons of the selection of the alloy of aluminium in front of the compound material base in the greater resistance of the first in front of the impact of external objects. On the other hand, Airbus uses the alloy 2099-T83 in shape of profiles extruidos in the fuselaje and floor. (See detail in figure 5).
The same alloy selected by Airbus will be applied also by Bombardier in his new models of the series C. Aeroplanes designed for the rank of 100-149 passengers and in which the material of Alcan Engineered Products designated Airware will suppose 20% in weight of the aeroplane. This new alloy is composed by aluminium, copper, lithium, magnesium and silver and is the answer of Alcan to the threat of the materials composed of organic matrix. His main characteristics are the ones of a high mechanical resistance, tenacity and resistance to the corrosion. The aeroplanes will be manufactured finally by Shenyanng Aircraft Corp. (SAC) In China and expects that they are operative in the year 2013.
A last example of the important impulse that has supposed the selection of the alloys To the-Li for structural components of the model To350 of Airbus constitutes it the Commercial Aircraft Corporation of China Ltd. (COMAC) That has subscribed in 2010 an agreement with Alcoa for the development of components for his New model ARJ-21 and the C919.
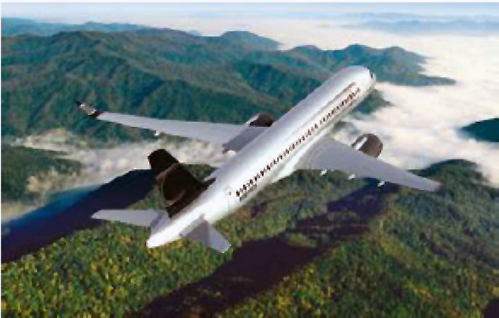
Another sector where already use alloys of To the-Li is the one of the helicopters being the case of the fuselaje of the helicopter of AgustaWestland EH101 the most known. In the figure 4 detail the components of the fuselaje manufactured in To the-Li (blue colour).
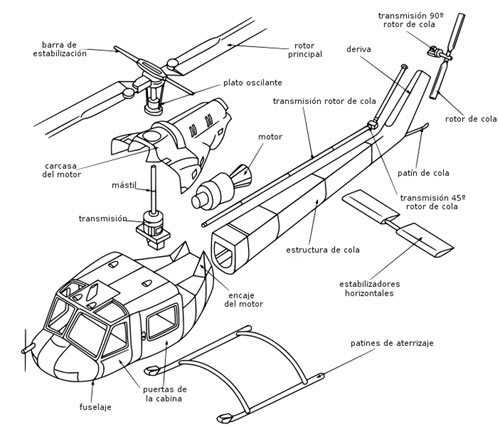
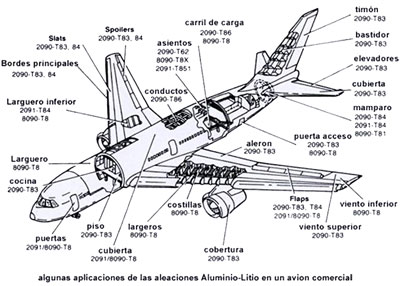
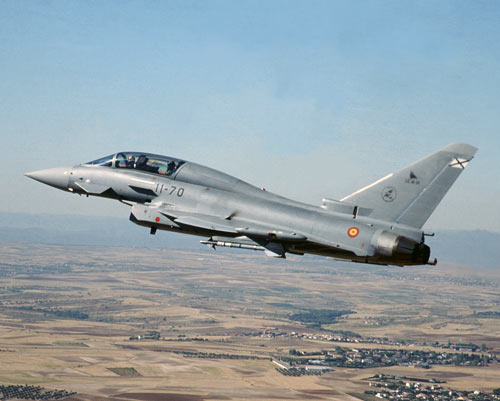
In another military application the fighter jet advanced Eurofighter Typhoon also presents components manufactured with alloys To the-Li. (See figure 5). 70% of the surface of the aeroplane is manufactured with compound material reinforced with fibre of carbon and 15% contains aluminium and titanium being 12% compound material reinforced with fibre of glass and 3% of other materials.
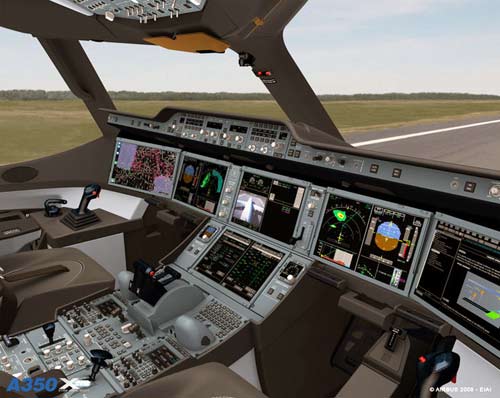
Other commercial applications of the alloys Aluminium-Lithium find in the sector space and cryogenic tanks. The NASA carry applying alloys To the-Li in his space programs from does more than ten years like material for the construction of the tanks of fuel of his lanzaderas and rockets (see photos 9 and 10) and for the manufacture of structural pieces.
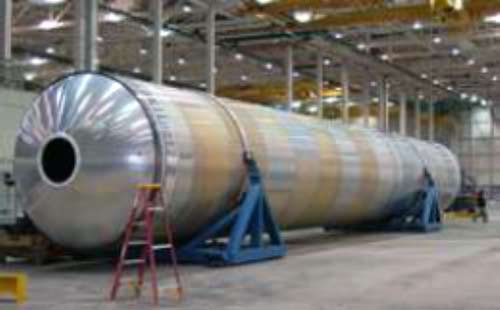
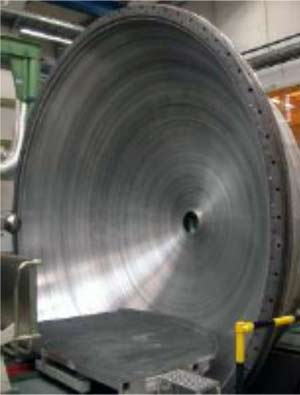
To conclude some considerations in relation with his processed and conformed.
The lithium is a very volatile element what hampers the manufacture of the alloys To the-Li that it has to realise low atmosfera controlled. They exist diverse methods of manufacture of the alloys of To the-Li between which are the processes of pulvimetalurgia, the colada direct and processes of fast solidification like the deposition by atomisation.
Alcan And Alcoa, the two big producers of this alloy use derivative processes of the traditional process of metallurgy of ingots (ingot metallurgy) through processes semicontinuos of direct cooling.
The colada direct is the traditional method of manufacture but the process of sprayado contributes greater flexibility and is being adopted also for the manufacture of these alloys. It consists basically in the atomisation of the compound To the-Li in liquid state and in his deposition under atmosfera of Argon or helium.
Finally exists also the possibility to manufacture these alloys by meltspinning or temperate giratorio. They are variants pulvimetalurgicas in which the material clear is not atomizado but a small current of the metal falls on a metallic wheel that turns quickly where solidifies. The result is a material in shape of threads or copos of 20-50 micras of thickness and several millimetres of diameter.
Regarding the conformed, the alloys of To the-Li present in general a good conformabilidad and at present there are alloys commercially available in shape of materials extraíbles, forjables and conformables by the traditional processes of conformed.
One of the properties of the alloys To the-Li that more interest presents for the aerospace industry is his superplasticidad what makes possible to conform components that can not manufacture in other alloys with which can arrive to compete diminishing besides the disadvantage regarding the cost of the prime matter.
Regarding the smelting of alloys of aluminium-lithium, this presents serious difficulties by the reactive nature of the lithium. By a part the alloys in state melted tend to absorb hydrogen of a noticeably upper way to other alloys and also exists the problem of loss of the lithium to these temperatures. The fusion of the alloys in atmospheres that contain Or2, N2 or steam of water poses the problem of the apparition of defects in shape of absorption of gases.
The aeronautical sector component manufacturing sector component manufacturing industry has showed interest in the technology of the smelting to the stray wax of these alloys by the advantages that presents regarding the possibility of obtaining of pieces very complex with form almost final. Historically they have realised a lot of efforts in developing this technology and any of the big foundries in United States like Howmet or Hitchiner offers the possibility to melt alloys To the-Li for pieces for the aeronautical sector component manufacturing sector component manufacturing sector.
Because of the technical problems commented, to the fault of development of specific alloys for the smelting and to the high cost of the manufacture of pieces the manufacture of components melted of To the-Li is merely testimonial and restricts to the manufacture of short series and prototypes.
Finally, the conventional thermal sensors treatment for the alloys To the-Li consists in a stage of solubilización in which the elements aleantes dissolve in the aluminium until obtaining a structure homogénea and composed of an only phase, temper to obtain a solution been used to supersaturada and the final treatment of artificial aging.
Because of the reactivity of the lithium to high temperatures the thermal sensors treatment of these alloys presents a greater degree of complexity that other conventional alloys
Conclusions
The characteristics of ligereza and excellent mechanical properties of the alloys of aluminium containing percentages of lithium between a 1-3% were discovered does more than 50 years but the commercial utilisation of these alloys on a large scale has been possible only in the last anuses. The main reasons of the use restricted of these alloys has been the one of the high cost in comparison to other alloys of aluminium with which competed (alloys of the series 2000 and 7000) and the existence of technical appearances without resolving in the alloys To the-Li developed until then such as his poor tenacity and ductility, the behaviour in front of the corrosion or the fault of development of thermal sensors and superficial treatment adapted.
However this situation of paralización in the development of the technology of the alloys of aluminium-lithium has suffered an important change had to mainly to the need of the big constructors of commercial aeroplanes (Boeing, Airbus, Bombardier, etc.) to access to materials with better provision for his new designs of aeroplanes of big capacity.
The aeronautical sector component manufacturing sector component manufacturing industry needs for the manufacture of the fuselajes and elements extracted of material reinforcement that present a combination of ligereza and upper mechanical properties to the presented by the alloys of conventional aluminium like the alloy 7075. The alternative of the utilisation of the titanium is excessively expensive and in this stage have arisen new materials like the compounds reinforced with fibre of carbon.
The industry of the aluminium to his time has answered to this threat of loss of competitiveness of his alloys betting by the development of new alloys between which stand out the new generations of aluminium-lithium such as the alloy 2050 of Alcan. The argument in favour of the alloys of To the-Li is the one to present a combination of upper properties to the previous alloys and the one to be able to compete in cost with the designs in compound material reinforced with fibre of carbon.
The main arguments in favour of the utilisation of the alloys To the-Li centre in his best adaptation to the requests of the models of middle-sized aeroplane, with a fuselaje more rigid that can bear the solicitaciones cíclicas of a greater number of landings and despegues to the day.
In concrete, some arguments in favour of the utilisation of the alloys of To the-Li in comparison to the compound materials are:
Resistance to the impact: the fuselajes are subjected to continuous impacts in the operations of load and download of cases in the cellar and trucks used in routine operations. The compound materials reinforced with fibre of carbon present a high resistance but can suffer give us internal because of these solicitaciones and to the impact of rays. In consequence needs implement essays no destructive routine to control that the internal structure of the material composed has not suffered give us and needs evaluate the need of a repair for salvaguardar the feasibility of the group. In the case of the alloys aluminium-lithium the reparabilidad of the pieces is simpler and less costly. A possible solution would be logically add a layer more than reinforcement in the case of the compound materials but in this case the advantages of cost and weight of the materials composed would not be already so tangible.
Processes of manufacture: the technology of the aluminium and his application in the aeronautical sector component manufacturing sector component manufacturing industry is a cheap technology and optimised. In the case of the materials composed of thermostable matrix require processes of different manufacture based in the utilisation of autoclaves, systems of empty and processes of union and different ass
Cost and durability: the cost of manufacture of the components in compound material is higher but present the advantage of a greater resistance to the corrosion. In spite of the improvement experienced in this field by the last generations of alloys To the-Li the problems of corrosion are still a worry for the industry of aluminium. The materials composed by his part present another type of problems when they are subjected to the atmosphere in conditions of service. They can absorb humidity and produce defects in shape of delaminaciones and do not have sufficient data regarding his resistance on a long-term basis in structural aeronautical sector component manufacturing sector component manufacturing applications.
Environingingmental appearances: the alloys To the-Li are easier to recycle that the compound materials and only is necessary to take into account the presence of lithium in alloys where is not allowed. The reciclabilidad of the components of material composed of fibre of carbon is lower and the recycled is costlier. They are components formed by fibre of carbon, thermostable resins and usually present an intermediate wire mesh to bear the effect of the rays.