Materials of high performance for the most demanding sector
During the next 20 years, has predicted that there will be a significant increase of the demand of the air transport. The economic growth of diverse regions of the world up to now marginales like Brazil, Russia, India and China will place them in these twenty years in the first places of the world-wide classification. It is possible that the number of travellers by the air arrive to duplicate with the every time greater demand of new aeroplanes, which estimates between 13.500 and 19.000. What comports annual deliveries from among 685 and 950 aeroplanes, with a total value estimated of roughly 1,35 trillion dollars. Limiting us only to Europe, foresees that the number of flights in this period increase 50% and only Germany will sue 1.000 new aeroplanes according to the global forecast of the market of Airbus.
In the global market, the innovation assumes a paper determinante to keep and do grow the quotas of market. It works already in the development of aeronautical sector component manufacturing sector component manufacturing motors increasingly reliable, economic and that produce low levels of chemical and acoustic pollution. In this context, the environingingmental aims in Europe for 2020 centre in reducing the broadcasts of carbonaceous anhydride in 50%, nitric oxide 80% and of the noise in 50%.
The important paper of the materials advanced
The remarkable characteristic of performance of the current aerospace vehicles are, to a large extent fruit of the advances in the field of the materials of high performance and in the different technologies of manufacture used in the distinct parts of the aeroplane. To obtain continuous increases of performance, the designers are looking for constantly material lighter, resistant and durable.
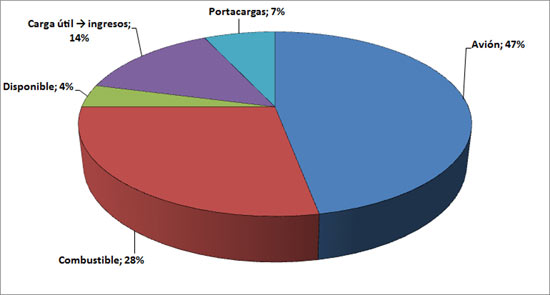
As we can observe in the figure 1, in a commercial aeroplane only uses 14% for the transport of passengers, that is what generates profits. Thus, a saving of weight by small that it was, supposes an optimisation of big value. For example, a saving of weight of 1% of the aeroplane increases the useful load in 15%. What supposes an increase of almost 7%.
As it is very known, the most effective way to reduce the weight of the fuselaje and improve his performance consists in reducing the density and increase the mechanical properties. It has estimated that the reductions in the density of the material are around 3 to 5 more effective times that the increase of the strength to the traction, module or tolerance of damage. For the turbines of motors to reaction, the advances in materials have allowed significant increases in the temperatures of operation, that translate in greater levels of push, increasing again the performance.
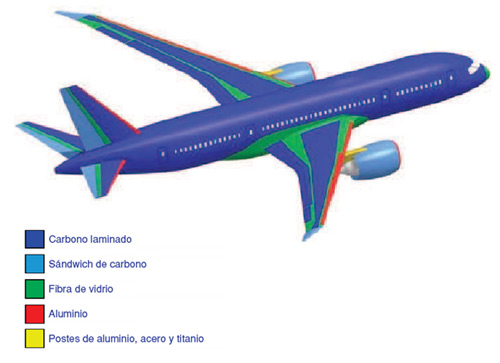
Diverse materials
To continuation collect the traditional materials employees in this demanding aeronautical sector component manufacturing sector component manufacturing sector and aerospace.
Alloys of aluminium
The alloys of To the have been the main material of the fuselaje of the aircraft since they began to substitute to the wood in the decade of 1920. Although the paper of the aluminium en el futuro of the aerospace industry like structural material probably was something eroded by the increasing use of compound materials, the alloys of aluminium of high resistance are, and will keep on being, a notable material for the fuselaje. The appeal of the aluminium is that it treats of a metal of cost relatively low and light weight, that can be subjected to levels of strength quite elevated in heat and is one of the materials of high performance of easier manufacture, what generally correlaciona directly with costs lower.
The main reasons for his use are:
- High resistance to the weight.
- Interesting cryogenic properties. The alloys of aluminium no fragilizan to low temperatures and go back even more strong to measure that diminishes the temperature without significant losses of ductility.
- Maquinabilidad. The alloys of aluminium are the easiest of all the metals to form and mechanise.
- Resistance to the corrosion in natural environingingments.
- Idoneidad For the storage of foods and drunk.
- High electrical and thermal sensors conductivity.
- Ease of recycling.
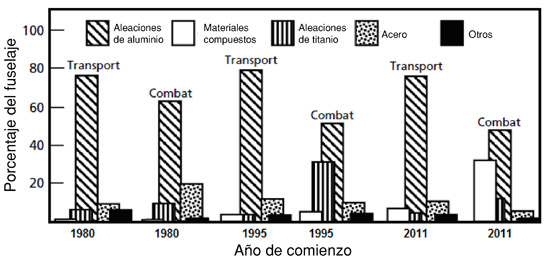
The alloys of aluminium-copper (series 2XXX) and aluminium-zinc (series 7XXX) are the main alloys used in structural applications of the fuselaje. The alloys 2XXX use in applications of tolerance to failures, such as the pieces of the inferior wing and the structure of the fuselaje of the commercial aircraft, whereas the alloys 7XXX use where requires greater resistance, such as the surfaces of the upper wing. The alloys 2XXX also have a light advantage, when having a greater capacity to bear the temperature (150 vs 120 °C).
The improvements in the control of the composition and of the processing have gone generating of continuous form alloys improved. The reduction of impurities, in particular ironinging and silicon, has translated in a greater hardness to the fracture and better resistance to the initiation of cracks by fatigue and growth of the crack.
Examples of these new alloys are the 2524-T3, 7150-T77 and 7055-T77, which use , specifically, in the Boeing 777. The famous alloy 2024-T3 has been one of the more widely used in the construction of the fuselaje. Whereas it only has a moderate elastic limit, has a very good resistance to the growth of cracks by fatigue in addition to a good tenacity to the fracture. However, the most recent alloy 2524-T3 has an improvement of the 15-20% in resistance to the fracture and the double of the resistance to the growth of the cracks by fatigue in comparison to 2024-T3.
The alloys 7XXX have greater advantages that the alloys 2XXX and use in plates, plates, pieces of forge and of extrusion. Like the 2024-T3, the 7075-T6 has used during a lot of years in the construction of the fuselaje; however, the cracks by corrosion has been a recurrent problem. The new alloys, like the 7055-T77, have greater resistance and tolerance to failures that the 7050-T7451, whereas the 7085-T7651, has greater hardness in thick sections. Together with the reinforcement of the controls of composition and deleting the unwanted impurities, the development of better thermal sensors treatments of aging for the alloys 7XXX has given place to very reduced agrietamientos by corrosion under tension and resistance to the fracture improved, with a minimum impact in the strength.
The improvements in the technology of manufacture of pieces of aluminium, includes the mechanised of high speed and welding by friction and repercuten directly in the descent of costs.
Magnesium and beryllium
Although so much the magnesium like the beryllium are material extremely light, both have serious problems that limit his applications. The alloys of magnesium compete generally with the alloys of aluminium for structural applications. In comparison with the alloys of high resistance of aluminium, the alloys of magnesium are not usually so resistant and have a module of lower elasticity. However, the alloys of magnesium are significantly lighter and therefore they are more competitive in front of a specific density and basic specific module. The greater obstacle for the use of the alloys of magnesium is his extremely poor resistance to the corrosion. The magnesium occupies the position anódica higher in the galvanic series, and thus, is not potentially resistant to the corrosion. Besides it results a difficult material to work since it is explosive.
The beryllium is also a very light metal with an attractor trucks combination of properties. However, the beryllium has to be processed using the metallurgy of dusts, a costly technology, although interesting from the punto of the maintenance. Besides, the manipulation of the dusts of beryllium are toxic, which increases even more his cost, since it requires of environingingments of manufacture controlled, and measures of extra hygiene for the repair/service of structures deployed. The beryllium is used to employ in alloys beside the copper, especially in pieces of turbines or for moulds of tools.
The titanium is used to to employ often to save weight by means of the replacement of the alloys of steel more weighed in the structure of the aeroplane and superaleaciones in the pieces of low temperature in the turbines. The titanium also uses in place of the aluminium when the requirements of temperature exceed the capacities of the aluminium (150 °C), or even in areas where the fatigue or corrosion has been a recurrent problem.
The titanium every time is more important like material of the structures of the aircraft. Because of his exceptional resistance to the fatigue, high temperature and resistance to the corrosion, the alloys of titanium comprise roughly 42% of the structural weight of the new fighter jet F-22, what supposes more than 4.000 kilos. In the commercial aeroplane, however, the Boeing 747-100 so only contained 2,6% of titanium, whereas the new Boeing 777 contains 8,3%. Between the new applications of the titanium include the trains of landing, which traditionally realised from steels of high resistance.
For example, to save weight and delete the risk of fragilización by hydrogen, the alloy beta of the You-10V-2Faith-3To the uses for the components of the train of landing in the Boeing 777. The alloys of titanium also use widely in the regions of temperature lower of turbines of motors to reaction.
Although they have developed a lot of new alloys from mediated of the decade of 1980, the alloy alpha-beta of You-6To the-4V is still the alloy of titanium more used. However, distinct alloys alpha-beta and beta more resistant, are beginning to substitute to the You-6To the-4V in determinate applications.
Whereas the steels of high resistance usually represent so only around the 5-15% of the weight of the fuselaje structural, often use for the very critical pieces such as the components of gears of the train of landing. The main advantages of the steels of high resistance are his extremely high resistance and rigidity. This can be extremely important in the applications of gears of the train of landing where is critical to minimise the volume of the components of the gear.
The disadvantages are his high densities and the susceptibility to fragile fracture. Like result of his levels of high resistance, often are susceptible to the fragilización by hydrogen and to the corrosion under tension, that can cause sudden fail brittle. it is working To develop a stainless steel of ultra high resistance to relieve some of the problems of corrosion and fragilización with these materials.
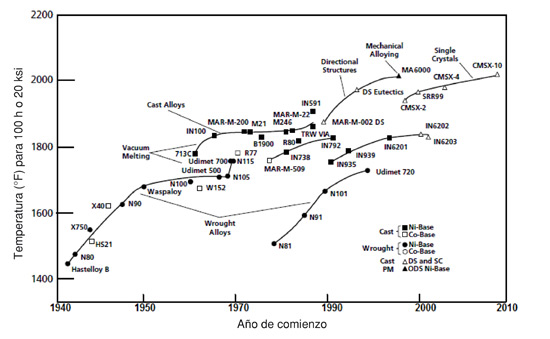
The superaleaciones
The superaleaciones or alloys of high performance present an excellent mechanical resistance and resistance to the fluencia to high temperatures, good superficial stability and high resistance in front of the corrosion and oxidation.
The basic elements of the superaleaciones employed in the aerospace sector are mainly the nickel, cobalt and nickel-ironinging. The ones of nickel have a good behaviour until temperatures of 1.000 °C and the ones of cobalt bear still greater temperatures without degrading substantially. This type of metallic materials use , for example, in the manufacture of shovels of turbine for hot sections of the motors to reaction, turborreactores and cameras of combustion. Inside the superaleaciones to base of nickel and for typical applications oriented to this demanding sector can quote:
- Hastelloy D, strong, tenaz and extremely hard, what by the contrary is of difficult mechanisation;
- Inconel, that combines mechanical resistance, to the corrosion and tenacity, characteristics of the Neither, with the resistance to the oxidation to high typical temperatures of the Cr. It resists to the thermal sensors fatigue without doing fragile. It uses in the manufacture of exhaust pipes and heaters of the motors of aeroplane.
- Nimonic 90, mainly used by his resistance to the fluencia, his high tenacity and stability to high temperatures. It is the basic alloy for the motors to reaction.
The superaleaciones to base of cobalt keep his resistance to high temperatures. In addition to incorporating refractory metals and metallic carbides, contain high levels of Cr, what increases the resistance to the corrosion. They are easier to solder that other superaleaciones and forge better. They employ to manufacture the structure of the camera of combustion of the turbines and motors of rockets, among others.
With basic elements like the aluminium and the chromium, comport well in front of the oxidation and corrosion since it forms a layer of oxide when the metal is exposed to the oxygen encapsulando to the material and protecting the rest of the components.
The ones of basic titanium resist less the high temperatures in front of the ones of Co and Neither although in the last ten years have realised technological advances in the development of modern motors of turbines for aircraft and airships using these materials.
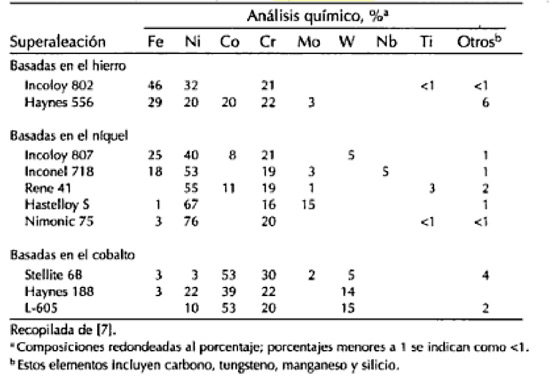
Material composed or composites
The advantages of the materials composed of high performance are many. Could stand out the following: weight lighter, optimum resistances and rigidities, improved resistance to the fatigue, resistance to the corrosion, and, with best practices of design, reduction in the costs of assembling, because of the lower number of pieces of detail and fasteners.
The specific resistance and the specific module of the materials composed of fibre of high resistance, especially the fibres of carbon, are greater that other metallic aerospace alloys comparable. This translates in a greater saving of weight that repercute in a better performance, a greater useful load, an elder reach/autonomy and a saving of fuel.
The army of EE UU developed and was pioneering in using the compound materials. The aeroplanes AV-8B had a fuselaje with 27% of his structure in composites at the beginning of the decade of 1980. The first use on a large scale of materials composed in commercial aeroplanes produced in 1985, when the Airbus To320 flew for the first time with horizontal and vertical stabilisers realised in compound materials. Airbus has applied the compound materials, until in 15% of the total weight of the fuselaje for his models To320, To330 and To340.
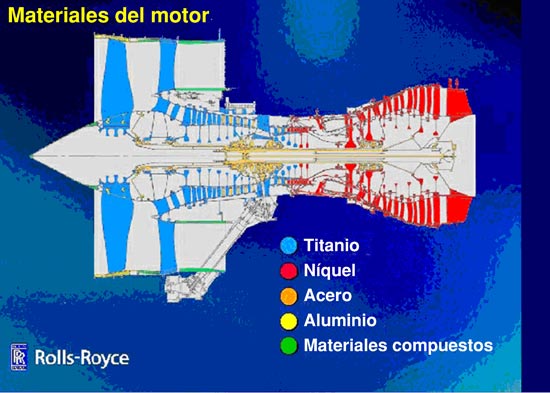
Although the percentages are lower in the commercial aviation that in the one of fight, the size of the pieces is a lot greater. The cost of the compound materials is the main reason disuasoria for his wider application. Thus, to be able to increase the employment of this type of materials of way more generalised, results indispensable to reduce the costs through innovative designs and debugged technologies of manufacture.
The assembling generally represents roughly 50% of the cost of the fuselaje. The compound materials offer the opportunity to reduce significantly the hand of work and fasteners in the setting, by means of diverse technicians of cured and adhesive unions.
The materials composed of matrix of metal offer a series of advantages in comparison with his basic metals, such as greater specific resistances and modules, a greater resistance to high temperatures, lower coefficients of thermal sensors expansion and, in some cases, better resistance to the wear. In the negative side, comment that they result more expensive that his basic metals and have lower resistance. The compounds of matrix of metal also have some advantages in comparison with the compounds of polymeric matrix, especially remarkable are some greater matrices depending on resistance and modules, a greater resistance to high temperatures, the no absorption of the humidity, greater electrical and thermal sensors conductivity, and the no inflamabilidad.
However, the materials composed of metallic matrix are usually more expensive that even the compounds of polymeric matrix, and the processes of manufacture are much more limited, especially for the complex structural forms. Because of his high cost, the commercial applications for the compounds of metallic matrix are scarce. Since it foresees that they will be important for future vehicles of hypersonic flight, so much material composed of matrix of metal and of ceramics result of vital importance.
The metallic fibres laminadas, especially the fibre of glass reinforced of aluminium laminado (Glare) results another form of compound material that offers advantages of performance of fatigue on structure of monolithic aluminium.
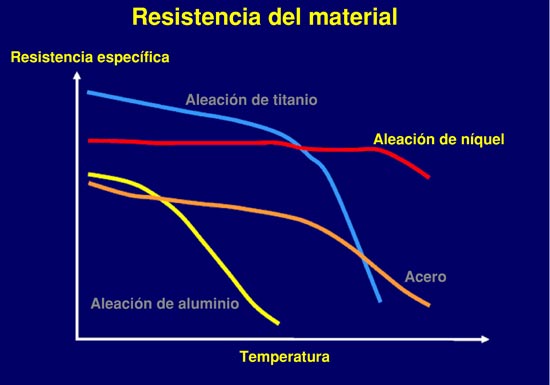
The ceramics present a lot of desirable properties, such as high modules, high resistance to the compressesion and high temperature, high hardness and resistance to the wear, low thermal sensors conductivity, and inactividad chemical. However, because of his very low tenacity to the fracture, the ceramics is limited in structural applications. Have a very low tolerance to break , what can occur already was during the manufacture or in the service. Even a very small crack can grow quickly to critical size, what carries to the sudden failure.
Whereas the reinforcements such like fibres, filaments or particles use to reinforce polymers and composed of metallic matrix, the reinforcements in materials composed of ceramic matrix use mainly to increase the tenacity.
Because of his high costs and problems of reliability, there is very few commercial applications of compounds of ceramic matrix. However, the compound carbon-carbon (CC) have found applications in the aerospace sector for the thermal sensors protection. The compound materials carbon-carbon are the most ancient and mature of the materials composed of ceramic matrix. They developed in the decade of the pasts fifty for uses like carcasas of motors of rocket, protective of heat, edges of attack and thermal sensors protection. For applications of high temperature, the compound materials carbon-carbon offer an exceptional thermal sensors stability, whenever they are protected with coatings resistant to the oxidation.
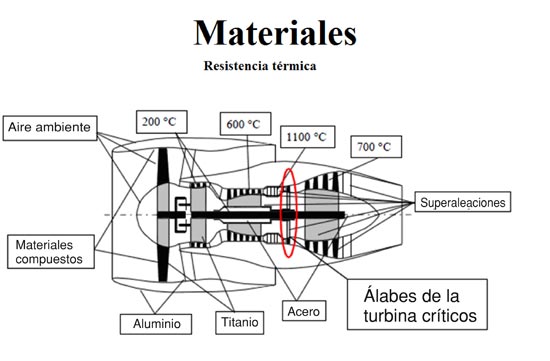

Relative comparison of different classes of materials
Material Class |
Strength Tension |
Strength Compressesion |
Rigidity |
Ductility |
Capacity Temperature |
Density |
Cost |
Metals Ceramics Polymers |
Alta Drop Very low |
Alta Alta Very low |
Average Very high Very low |
Alta Invalid Alta |
Alta Very high Drop |
Alta Average Drop |
$$ $$$ $ |
PMC MMC CMC |
Very high Alta Average |
Alta Alta Alta |
Very high Very high Very high |
Drop Drop Drop |
Average Alta Very high |
Drop Average Average |
$$$ $$$$ $$$$$ |
PMC: Composite Of Polymeric Matrix
MMC: Composite of Metallic Matrix
CMC: Composite of Ceramic Matrix
To conclude
- Fits to signal that an alone material does not fulfil all the needs of the current or future aerospace vehicles. All they have some deficiencies, already was in provision or in the costs. With the increasing emphasis in the price, the materials of today and of morning, will have to be processed and manufactured in some surroundings of costs very competitive. Although it has done a lot to this respecto in the 20th century, of face to future antojan necessary even more improvements so much in the materials as in the technologies of manufacture.
- Like tendencies that will observe to short and half term can quote :
- A greater utilisation of the ‘Metallurgy of dusts'. It presents big eases in the repairs in the pieces. The only problem is the price. Create pieces from metallic dusts is expensive; if it solves this escollo them augura a big future.
- A generalised implantation of ‘Superaleaciones' with advanced provision.
- Big use of ‘Compound Materials' in structures of the aircraft and other applications conexas.