Grandes planes de mantenimiento y seguridad para grandes plantas petroquímicas
14 de abril de 2011
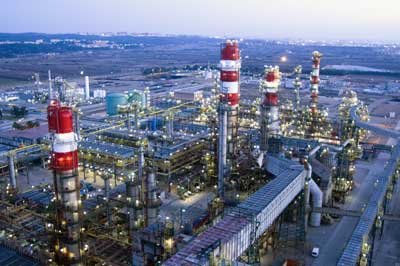
Hemos tenido la oportunidad de entrevistar a José Luis Alonso y Jordi Mas Rubio, jefes de Mantenimiento y Seguridad respectivamente de la planta tarraconense de Repsol, que desde sus inicios ha desarrollado planes integrales de prevención, detección y extinción que abarcan desde el diseño de las instalaciones hasta la formación de su personal, fijando como meta la consecución de cero accidentes en sus operaciones mediante la implantación de hábitos de comportamiento seguros y a la cultura de seguridad. No obstante, se establecen planes de actuación anticipando posibles incidencias, siempre siguiendo el Plan de Emergencia del Sector Químico de Tarragona (PLASEQTA) y en colaboración con diversos entes oficiales como la Organización de Protección Civil de Tarragona.
Siguendo eso de más vale prevenir que curar... ¿el mejor mantenimiento es el preventivo?
¿Cómo organiza Repsol el mantenimiento de sus plantas? ¿Qué órganos dentro de la empresa se encargan de gestionarlo?
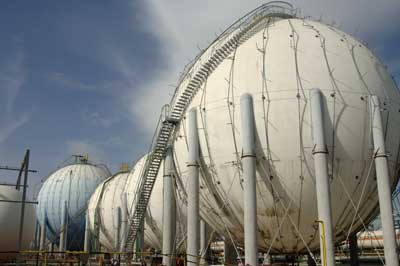
¿Qué mejoras técnicas han aparecido recientemente para aplicar a esta actividad?
Podemos decir que las mejoras técnicas que han aparecido recientemente tienen mucho que ver con un tipo de mantenimiento más eficiente y flexible que los ya conocidos —preventivo y correctivo— y que se denomina ‘mantenimiento según condición’. Se trata de detectar el deterioro significativo de un equipo basándose en la variación de un parámetro de control indicativo del funcionamiento de dicho equipo. Como ejemplo de ello podemos poner el estudio de vibraciones en máquinas rotativas.
En cuanto al mantenimiento predictivo, ¿qué ventajas aporta en el día a día de sus plantas?
Como hemos comentado, el mantenimiento predictivo o según condición aporta mayor eficiencia y flexibilidad a la hora de ejecutar los planes de preventivo y correctivo. Podemos citar algunas ventajas concretas, como la reducción de la probabilidad de accidentes causados por la maquinaria; el incremento de disponibilidad —menos tiempo de mantenimiento al evitar posible averías catastróficas y definición del momento más favorable para una posible intervención—; incremento de productividad, porque permite a algunos tipos de máquinas funcionar a sobrecapacidad y se pueden detectar pérdidas de rendimiento o incremento de consumo energético; y permite la planificación con antelación para reducir los efectos de próximas paradas sobre los clientes de productos o servicios.
Por contra, podemos decir que existen dos razones fundamentales para no aplicar de forma sistemática el mantenimiento según condición: no todas las causas de fallo de la planta pueden ser detectadas mediante este tipo de técnicas; y el control de condición requiere, por su propia naturaleza, costos en mano de obra o en equipo o en ambos.
A lo largo de los últimos años, ¿cómo han evolucionado los planes de mantenimiento de las plantas? Es decir, ¿se le da más importancia actualmente a los planes de mantenimiento preventivo que hace años?
En general se observa una tendencia al incremento de planes de preventivo y de mantenimiento según condición frente a los de correctivo, teniendo en cuenta todas las consideraciones mencionadas en los puntos anteriores.
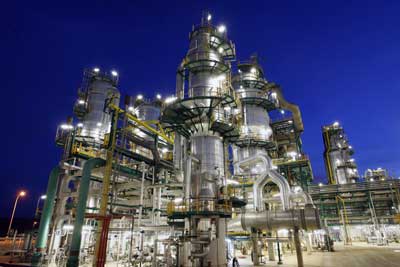
En complejos suyos como el de Tarragona han suscrito un Plan de Ayuda Mutua (PAM) con las empresas del entorno. ¿Nos puede explicar en qué consiste?
Las empresas ubicadas en el Complejo Químico de Tarragona, si bien disponen de niveles de protección de acuerdo a los estándares universalmente aceptados para este tipo de instalaciones industriales, pueden encontrarse ante situaciones de emergencia que haga necesaria una cooperación entre las distintas compañías con el fin de afrontar de un modo más eficaz la lucha y control ante los imponderables de determinados escenarios.
El PAM está dirigido a prestar a las empresas adheridas el soporte de medios materiales que facilite, en caso de necesidad, la minimización de los daños tanto a las personas como al medio ambiente, así como evitar o reducir la destrucción de las instalaciones y pérdidas por interrupción de negocios.
Pretende, por tanto, planificar y organizar el uso de procedimientos para la ayuda de forma rápida y eficaz, ante las consecuencias de una emergencia que pueda desbordar los medios disponibles de la empresa/s afectada/s.
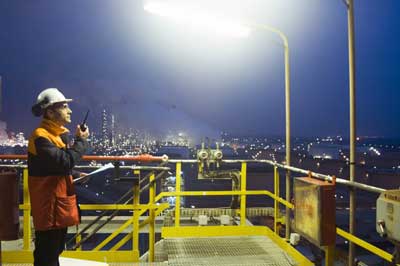
Carlos Felipe Videla, subdirector de Auditoría de riesgos y Proyectos de Seguridad de Repsol: “En seguridad nunca hay que estar satisfecho ya que siempre se puede hacer algo más”
En el apartado de seguridad industrial laboral de la Memoria de Responsabilidad Social Corporativa de Repsol dice lo siguiente: "Nuestro objetivo es conseguir lugares libres de accidentes. Asumimos el compromiso de brindar unas condiciones de trabajo óptimas en cuanto a seguridad y salubridad. Exigimos un alto nivel de seguridad en los procesos, instalaciones y servicios, prestando especial atención a la protección de los empleados, contratistas, clientes y al entorno local, y transmitimos este principio de actuación a toda la organización”. Sobre esta declaración de principios y sobre todo sobre seguridad industrial en plantas, hablamos con uno de los responsables de su seguridad, Carlos Felipe Videla.
Las plantas nuevas se diseñan incluyendo todas las medidas posibles ante accidentes... ¿Qué ocurre con instalaciones antiguas cuyo diseño no lo contemplaba?
Como parte de la gestión de la seguridad de procesos tenemos implantado un proceso de adaptación continua de las plantas existentes a los avances en el hardware de seguridad.
Todos los centros industriales tienen un ‘gap analysis’ de su situación con respecto a las mejores prácticas internacionales y un plan progresivo de adaptación en función de los presupuestos y de la disponibilidad de plantas. Algunos ejemplos de elementos incluidos en dicho plan son: válvulas de corte de acción remota, ignifugado de estructuras, dobles sellos en bombas críticas, doble bloqueo y venteo en las líneas de combustible a hornos, etc.
¿En qué normativas se basa la seguridad de las instalaciones de sus plantas? ¿Difieren mucho las normativas españolas de las europeas? ¿Y las del resto del mundo?
Seguimos el principio de la Política de Salud, Seguridad y Medio Ambiente de Repsol YPF en cuanto al cumplimiento de las normas. Por lo tanto es obligatorio el cumplimiento con la legislación local aplicable a cada planta más las normas de compañía en todos los centros industriales. Las normas de compañía utilizan las mejores prácticas internacionales tanto europeas como del resto del mundo aunque no estén todavía recogidas en las legislaciones de ningún lugar. Por ejemplo las recomendaciones de las compañías de reaseguro o las normas API.
“Las protecciones se implantan tras de identificar escenarios accidentales siguiendo el concepto de ‘capas de protección’ hasta reducir el riesgo todo lo posible”
¿Cómo evalúan y gestionan los riesgos industriales de sus instalaciones?
Utilizamos varios mecanismos entre los que se puede mencionar la Norma de Compañía de Gestión del Riesgo de Seguridad y Medio Ambiente en Activos Industriales 353-NO03MG donde se fijan los estudios obligatorios y los niveles de riesgo de referencia que no deben ser superados, auditorías de Riesgo Corporativas y un Mapa de Riesgos de todas las actividades e instalaciones de la compañía.
¿Cuáles son sus principales herramientas para evitar accidentes?
El sistema de gestión que incluye la prevención de riesgos laborales y la seguridad de procesos (seguridad industrial) y las inversiones en seguridad.
¿Con qué sistemas de seguridad activa cuentan sus plantas?
Dada la heterogeneidad de plantas y entornos en los que trabaja la compañía es imposible describir los sistemas de seguridad activa en pocas líneas. En términos generales podemos mencionar que las protecciones se implantan tras de identificar escenarios accidentales siguiendo el concepto de ‘capas de protección’ hasta reducir el riesgo todo lo posible.
Una de las prioridades de Repsol es conseguir la accidentalidad ‘0’ en sus puestos de trabajo. Los accidentes laborales siguen disminuyendo en su compañía pero, según su opinión ¿qué hace falta para pasen a la historia?
En seguridad nunca hay que estar satisfecho ya que siempre se puede hacer algo más. En esa línea estamos trabajando en el liderazgo de toda la línea de mando y en el estudio del fallo humano como causa de accidentes.
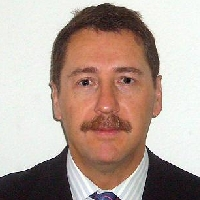