Monitorización de maquinaria con fines predictivos dentro de la Industria 4.0
Marta Alberdi, Customer Care Manager para Iberia en la empresa I-care
05/03/2021El sector del metal se ha beneficiado históricamente de estos beneficios y cuenta con una amplia cultura en cuanto a mantenimiento predictivo, si bien es cierto que los modelos predictivos han cambiado en el tiempo y no en todas las plantas han seguido la misma evolución. Actualmente en muchas plantas se sigue el modelo tradicional en base a medidas periódicas con equipos portátiles, muy válido para muchos de los activos, pero no para todos. Del análisis de criticidad, de los modos de fallo y del tiempo de desarrollo al fallo se extrae la necesidad o no de un sistema de monitorizado en continuo.
Digitalización e Industria 4.0
El monitorizado de la maquinaria entra con fuerza dentro del marco de la digitalización y la industria 4.0. La correcta sensorización, procesamiento y analítica de datos nos dan información objetiva sobre el estado de nuestros activos, lo que nos capacita para la correcta toma de decisiones. En los proyectos de monitorizado de maquinaria se requieren equipos multidisciplinares y plataformas capaces de gestionar información proveniente de distintas fuentes.
La función principal de estos sistemas es la detección temprana de anomalías de funcionamiento para evitar eventos catastróficos. También permiten la detección de desviaciones de comportamiento ante situaciones imprevistas o transitorias como arranques, paradas y disparos. Se protege a la máquina frente a fallos aleatorios cuando estos son detectables y no son admisibles por su criticidad.
El monitorizado de maquinaria supone la automatización de la toma de datos, asegurando la repetibilidad de las medidas y el reporte de los valores medidos y las alarmas a los sistemas de control de planta; aumenta la información disponible y, en caso de un evento, existe el registro de lo que ha ocurrido antes del mismo, pudiendo realizar análisis causa raíz del fallo.
Los sistemas de monitorizado aportan información no solo al departamento de mantenimiento, sino también a calidad, proceso, etc. Cada departamento puede filtrar la información de su interés y tener alertas/alarmas diferenciadas. Se pueden generar lógicas de alarmas provenientes de diferentes parámetros medidos con un sensor (por ejemplo, un acelerómetro), o de sensores diferentes (vibraciones, temperaturas, análisis de aceites, parámetros eléctricos).
La fiabilidad del diagnóstico depende de la correcta combinación de parámetros y técnicas aplicadas sobre un activo, sumada a los ajustes de alarmas de acuerdo al histórico. Hoy en día existen herramientas para automatizar este ajuste o alarmas estadísticas.
Las nuevas plataformas IoT permiten la modelización de activos y procesos gracias a la información proveniente de sensórica de máquina y hardware de procesamiento de datos. Esta inteligencia artificial se basa en tener correctamente resueltas las primeras fases, sensorización y tratamiento del dato.
Ingeniería del proyecto de monitorización
La correcta implantación y automatización de los sistemas depende de haber dedicado el tiempo y recursos necesarios para su ingeniería y puesta en marcha. A la vez de dar el paso de monitorizar todas las plantas, debemos de contar con un personal experto para la generación de la base de datos, la configuración de los puntos, de los parámetros de medida, de las alarmas, la comunicación con el DCS y con el software predictivo. Se necesita optimizar la estrategia de almacenamiento de datos para no saturar las bases de datos con información irrelevante. Además, el sistema va generando un histórico, frente al que hay que ir ajustando las alarmas a lo largo del tiempo.
Una vez el sistema de monitorizado está correctamente implantado, llega el momento de la explotación del mismo; este es el punto donde realmente se verá el retorno. Tras de la inversión en tiempo y dinero que supone instrumentar una máquina, instalar los armarios o cabinas, el servidor donde se aloja el software, verificar todas las comunicaciones, etc. En este momento se necesita un experto que se conecte al sistema periódicamente y supervise los datos registrados, ajuste alarmas o genere una configuración adicional si aplica. Con esta información el experto emite un informe de diagnóstico con unas recomendaciones concretas del estado del activo y que se van a utilizar para planificar las próximas intervenciones.
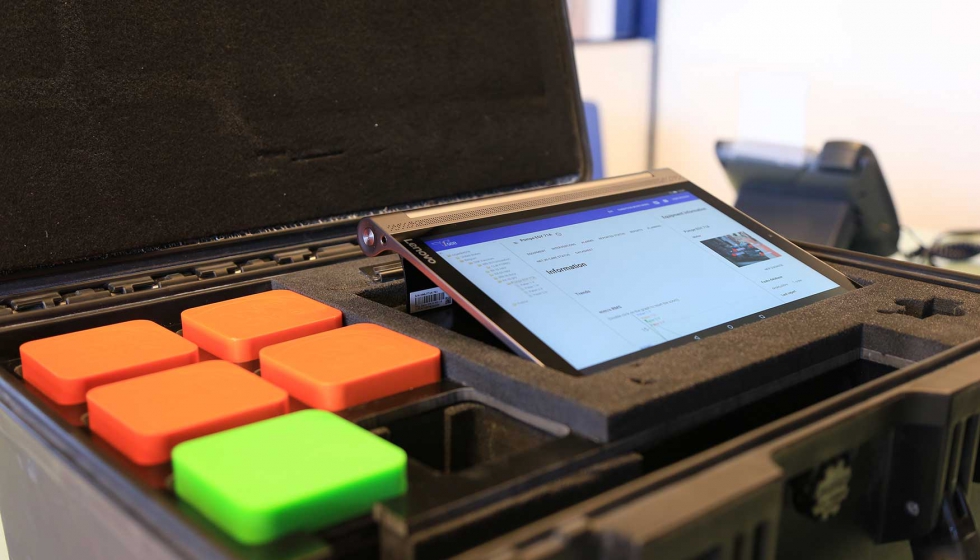
Grúa pórtico y puente grúa: soluciones innovadoras en mantenimiento predictivo
Desde 2013, I-care, empresa especializada en mantenimiento predictivo y fiabilidad, trabaja junto a un actor importante de la industria del metal en su evolución de un mantenimiento correctivo costoso e ineficiente a un programa de mantenimiento 4.0 para sus grúas pórtico y puentes grúa. Este cliente opera con un total de 227 puentes grúa, de los cuales 55 son muy críticos para la producción.
En la industria del metal, así como en otras industrias, las grúas pórtico y los puentes grúa se encuentran entre los activos de producción más críticos. El tiempo de parada no programado a menudo conduce a enormes pérdidas financieras. Sin embargo, a diferencia de la gran maquinaria rotativa existente en planta, el mantenimiento predictivo sigue siendo una estrategia poco común para los rodamientos de estas grúas. Si bien el análisis de vibraciones es una técnica ampliamente aceptada como estrategia predictiva para evitar fallos inesperados en los equipos, rara vez se aplica a este tipo de grúas por tres principales razones. La primera es una baja velocidad, concretamente de entre 20-50 RPM; el difícil acceso para los trabajadores a la hora de realizar las mediciones y el elevado ruido de fondo causado por el contacto de las ruedas con los rieles.
Para cumplir con las expectativas del cliente, I-care ha desarrollado un programa de monitorización basado en análisis de vibraciones, termografía infrarroja, análisis de aceite y análisis de corriente del motor. Para poder ofrecer las mejores recomendaciones y realizar el diagnóstico más exacto, I-care ha creado un sistema personalizado para recolectar los datos y así evitar cualquier tipo de interferencia causada por el ruido.
En cuanto a la ejecución, el proyecto se dividió en tres fases diferentes:
- Fase 1: Primeras pruebas y desarrollo de la técnica de medición
- Fase 2: Monitorización periódica basada en mediciones de vibraciones portátiles
- Fase 3: Monitorización inalámbrica de las grúas
Fase 1: Primeras pruebas y desarrollo de la técnica de medición
Se realizaron diferentes pruebas para determinar la viabilidad de la monitorización de vibraciones en las ruedas de la grúa utilizando recolectores de datos portátiles. Concretamente se midieron 16 rodamientos de rueda de grúa (con un diámetro de 1m) y 8 rodamientos de carro.
Debido a las dimensiones del puente grúa (ancho 35 m, altura 20 m, 447 toneladas), la opción de elevarlo era totalmente inviable. Por ello, se decidió colocar los acelerómetros lo más cerca posible de los rodamientos de las ruedas. Sin embargo, seguía existiendo un alto ruido de fondo. Para poder solucionar este desafío, se utilizó un filtro de paso alto que elimina cualquier tipo de vibración causada por el contacto de las ruedas y los rieles.
Con las técnicas clásicas de alta frecuencia se calcula el espectro basándose en la forma de onda analógica obtenida con el envolvente de la señal rectificada. Las técnicas más avanzadas utilizan un muestreo de muy alta frecuencia (> 80 kHz) para detectar los impactos en la forma de onda causadas por el defecto del rodamiento.
Como las amplitudes medidas eran muy bajas, no quedaba claro si el defecto detectado sería visible en el rodamiento. Pocas semanas más tarde, el rodamiento defectuoso revela daños graves de la pista exterior.
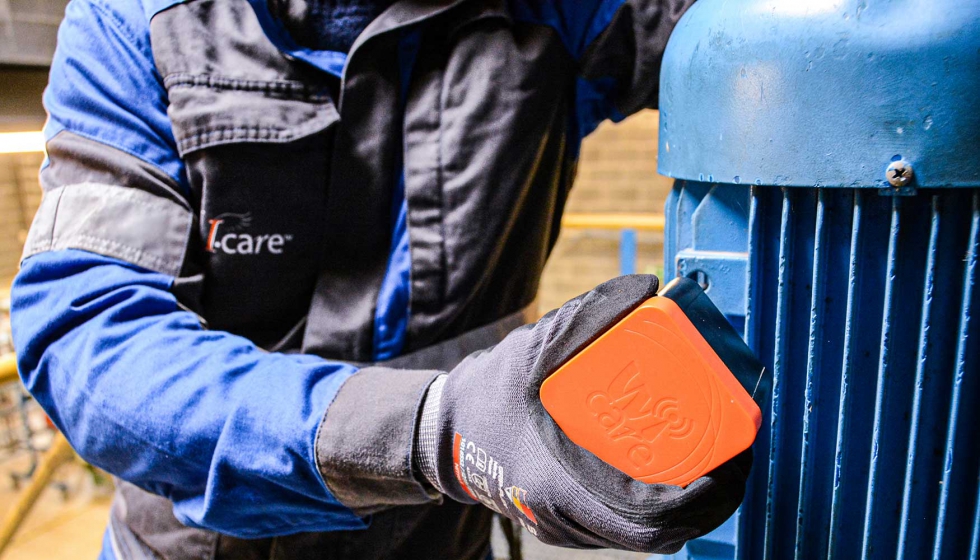
Fase 2: Monitorización periódica basado en mediciones de vibraciones portátiles
Siguiendo los resultados de la campaña de prueba, se configuró un programa de monitorización completo para 70 grúas puente (± 1500 rodamientos), que se realizaría en mediciones periódicas.
Durante 2 años se reemplazaron 45 rodamientos, gracias a los resultados del monitoreo, y hubieron 13 fallos inesperados en los rodamientos de grúas que aún no estaban implementadas en el programa.
Según se iban examinando los rodamientos reemplazados, se ajustaron y perfeccionaron los criterios con el objetivo de ser lo más eficientes posibles.
Durante esta misma fase, las mediciones también indicaron la aparición de defectos en las frecuencias de los rodamientos en una de las grúas, y que mejoraron considerablemente a partir de diferentes tareas de lubricación. Gracias a un correcto plan de lubricación la condición de muchos rodamientos mejoró, evitando un reemplazo demasiado temprano.
Si bien es cierto que durante los años que duró la segunda fase hubo una reducción de tiempo de inactividad, seguían teniendo que parar su producción algunas de las grúas durante las mediciones para que los analistas pudiesen hacer su trabajo. Para poder reducir el riesgo laboral de los empleados y disminuir aún más el tiempo de parada de las grúas, se propuso realizar la monitorización con los sensores inalámbricos Wi-care.
Fase 3: Monitorización inalámbrica de las grúas
Con esta última fase, se dio el paso hacia el mantenimiento 4.0. Pese a que en este tipo de maquinaria presenta dificultades para ser monitorizada de forma online, la empresa I-care ha desarrollado los sensores inalámbricos Wi-care 200, que ofrecen:
- Detección de fallos de los rodamientos mediante muestreo de alta velocidad
- Captura de datos inteligente con trigger externo (velocidad)
- Fuente de alimentación local para su funcionamiento continuo
La comunicación bidireccional y flexible de los Wi-care 200 permiten una fácil integración de otras tecnologías y sensores, como temperatura, análisis de aceite en línea, espesor...
Durante esta fase se instalaron un total de 97 sensores:
- 50 de vibraciones
- 21 de aceite en el que miden la calidad del aceite, el desgaste y el nivel de aceite
- 26 de ultrasónicos encargados de medir el espesor de varios componentes como: revestimientos, cables y escobillas
Conclusión
El sistema inalámbrico Wi-care 200 permitió aumentar la fiabilidad del programa de monitorización de las grúas, al tiempo que eliminó las desventajas de las mediciones periódicas.
Gracias al conocimiento y los años de experiencia en el campo, I-care pudo afrontar el desafío de automatizar la monitorización de condición en las grúas utilizando sensores inalámbricos. Además, supuso un ahorro económico para el cliente, ya que se redujo el tiempo de inactividad de las grúas y destinaron el tiempo de trabajo de los empleados en realizar otras tareas.
La tecnología Wi-Care permitió al cliente solucionar los problemas y encontrar la mejor solución para optimizar el mantenimiento de sus máquinas.
Marta Alberdi
Cuenta con una experiencia de más de 10 años ayudando a la industria en el desarrollo de la estrategia predictiva para la optimización del mantenimiento, la fiabilidad industrial y la gestión de activos. Especialista en proyectos de monitorizado de la condición de maquinaria crítica dentro del marco de la digitalización e Industria 4.0.