Soluciones Industria 4.0 para la producción cotidiana
En el stand de Pepperl+Fuchs, los visitantes de la feria de Hannover pudieron ver el parecido con su doble digital (digital twin) y experimentar la producción en lote de tamaño uno. Los visitantes se pudieron escanear en 3D y tener su imagen impresa en la portada de una revista de la feria. Con la ayuda de un gemelo digital, se simuló el proceso de producción de una máquina dobladora de chapa y los resultados se utilizaron en vivo para la optimización en respuesta a las diferentes propiedades de varias materias primas.
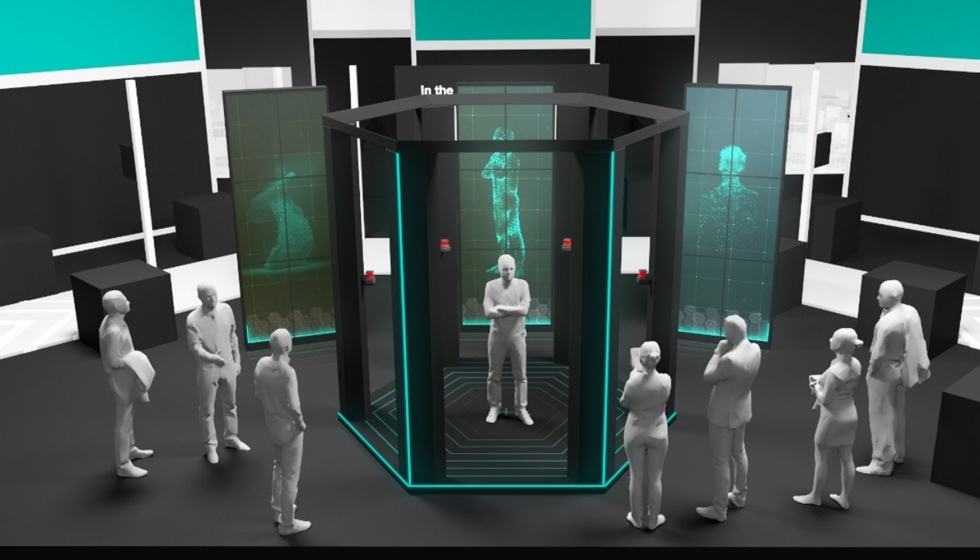
Como parte de su Solutions Park, Pepperl+Fuchs presentó dos nuevas exhibiciones en la feria, en las que se demostraron procesos integrados en línea con los estándares de la Industria 4.0 en tiempo real.
Con el concepto Connected Customization (personalización conectada) de la empresa, se pudo experimentar de primera mano la producción en lote de tamaño uno: los visitantes en la feria fueron escaneados en 3-D de los pies a la cabeza con seis sensores LiDAR 2-D de la serie R2000. Los datos de las siluetas estuvieron disponibles en un formato de datos estándar para su posterior procesamiento en todo el mundo en la nube NeoNeon dirigida por Neoception, una filial de Pepperl+Fuchs. En la feria, los datos se convirtieron en una imagen y se imprimieron en la portada de una revista de la feria personalizada, pero también se usaronc omo base para producir una imagen tridimensional en cualquier parte del mundo.
Con el concepto Digital Twin (doble o gemelo digital), los visitantes del stand podían configurar el producto que escogían a partir de una pieza de chapa metálica. Como parte de la demostración, los datos se transferían a una de las máquinas dobladoras de chapa del fabricante austríaco Salvagnini, que inmediatamente comenzaba la producción del producto individual.
Para que esto fuera posible en lote de tamaño uno sin pruebas de doblado, el proceso debía optimizarse para cada lote de material ya que las propiedades de doblado de la chapa metálica podían variar significativamente. Para ello, el comportamiento de la chapa (metálica) real se analizaba al principio del proceso de plegado y se alineaba con un doble digital del metal y la dobladora desarrollada por el centro de fabricación de Linz (Linz Center of Manufacturing, LCM). Los parámetros de ajuste se calculaban y transferían a la máquina durante el proceso de doblado en marcha.
La máquina estaba equipada con sistemas de medición de posición inductivos y sensores ultrasónicos fabricados por Pepperl+Fuchs. Con propósitos de control de calidad, la silueta del producto final se verificaba con un sensor de sección de luz de la serie SmartRunner Matcher.