Mecanizar sin defectos, visión global
En sectores como el aeronáutico, aeroespacial, eólico o médico, el mecanizado de componentes de alto valor añadido es una etapa crítica en el proceso productivo, máxime cuando se trata de grandes componentes de series cortas o pieza única. La idea de mecanizado sin defectos es hoy en día una necesidad para obtener pieza buena a la primera. Partiendo del diseño y la utilización de modelos predictivos para procesos; siguiendo con la simulación virtual de procesos y la monitorización online para detección y corrección de errores; y terminando con controles de calidad tanto en etapas intermedias como finales de la cadena; podremos estar cerca de conseguir buenos resultados en esta línea. A continuación se presenta una visión global de las necesidades y tendencias actuales relacionadas con el control y gestión de defectos durante el proceso de mecanizado.
Aumentar el peso que tiene la industria en el PIB global se ha convertido en una preocupación creciente en los últimos años. De hecho, se está asistiendo a una reorientación global del sector secundario donde uno de los objetivos de la Comisión Europea es incrementar esta participación industrial para pasar de los valores medios actuales de 15%, hasta un 20% en el año 2020. Este reto pasa por la incorporación de innovación y tecnología a lo que hoy se denomina la Fábrica del Futuro, y de esta forma tratar de conseguir una reducción de costes complementada con una mejora de la calidad de los productos finales, obteniendo productos de calidad con un control absoluto sobre la gestión de defectos.
1. Fabricación sin defectos y su contexto industrial
A nivel general, sectores de gran importancia en Europa como el de automoción, el aeronáutico y el eólico están impulsando las inversiones en I+D+i, focalizando gran parte de los recursos en procesos de fabricación y producción por mecanizado. En este contexto, la fabricación avanzada se perfila como concepto clave para las grandes empresas y grupos de investigación y se entiende como la generación y aplicación de conocimiento, experiencia y tecnología de vanguardia para la creación de productos, procesos de producción y servicios de alto valor añadido. La fabricación avanzada ha sido definida por el Gobierno Vasco como uno de los pilares de la estrategia de especialización inteligente de Euskadi, y la fabricación sin defectos constituye un factor clave en ello.
En esta línea, la industria está demandando soluciones para evitar piezas defectuosas en etapas finales de producción, soluciones capaces de predecir defectos antes de que se generen y sistemas de reacción inmediata capaces de actuar sobre los defectos generados una vez producidos, todo ello sin tener que esperar a la fase final de control. Con este fin, la demanda se centra en nuevas soluciones flexibles que permitan la inspección online de los productos, esto es, durante el proceso de fabricación. Existe una clara necesidad de desarrollar nuevos métodos de control de calidad que eviten la generación de los defectos en el momento mismo que el producto se está fabricando.
El objetivo industrial es generar producto final de alta calidad a un precio razonable, sin defectos y reduciendo gastos. Esto se consigue mediante el uso de técnicas avanzadas de diseño, simulación, monitorización y medición, integradas en el proceso de forma inteligente y con la capacidad de ayudarnos a obtener una producción estable y libre de defectos. Este hecho se hace más importante en sectores basados en series cortas o pieza única, donde la necesidad de realizar la pieza bien a la primera es crítica y donde un defecto en las operaciones de acabado puede suponer la pérdida de miles de euros en chatarra. Este es el caso por ejemplo de grandes componentes de alto valor añadido en el sector aeronáutico, como discos de turbinas, o en el sector eólico, como componentes de grandes multiplicadoras para aerogeneradores.
Conocer en qué condiciones está trabajando una máquina-herramienta en tiempo real ha sido siempre un sueño compartido tanto por el usuario de la máquina como por su fabricante. Se puede por lo tanto plantear aumentar la productividad, la precisión, la calidad del acabado o reducir el consumo energético según las prioridades de cada momento concreto.
2. Construyendo desde los cimientos: diseño y modelos para máquinas y procesos
Las operaciones de mecanizado han constituido el corazón de la industria de la fabricación desde la revolución industrial. Pueden definirse como el conjunto de actuaciones de arranque de material de un componente mediante el uso de herramientas de corte y máquinas para la obtención del producto requerido a las dimensiones deseadas y con buen acabado superficial. Esto debe hacerse además bajo el mínimo coste productivo o la máxima tasa de producción (o bajo una combinación de las dos).
El proceso de fabricación viene dado por una serie de variables de entrada y salida. Las variables de entrada son variables independientes del proceso: máquina-herramienta (rigidez, precisión, …); herramienta de corte (material, recubrimiento, geometría, …); condiciones de corte (velocidad, avance y profundidad de corte); propiedades del material (dureza, resistencia mecánica, composición química, microestructura, conductividad térmica, proceso de fabricación, …); propiedades del fluido de corte, etc. Las variables de salida del proceso son variables dependientes del mismo e incluyen: vida de herramienta, desgaste, fuerzas de corte, consumo de potencia, acabado superficial, tolerancia dimensional, tasa de arranque de viruta, ruido de corte, vibraciones, clase de viruta o temperatura de corte.
La figura 1 muestra la necesidad de simulación debido al continuo reajuste en los requisitos del producto a fabricar. De forma general, los modelos buscan siempre alguno de los objetivos siguientes:
- Una manera rápida de optimizar los procesos de forma rápida y realista
- Predicciones realistas de magnitudes de procesos
- Obtener nuevos conocimientos sobre las etapas y el diseño del proceso de fabricación
- Generar oportunidades para la monitorización de procesos y el mayor control sobre el proceso que puede derivarse

Los procesos de mecanizado incluyen procesos tradicionales (torneado, fresado, rectificado, taladrado, …) como avanzados (electroerosión, mecanizado electroquímico, por ultrasonidos, chorro abrasivo, mecanizado por haz laser, etc.). Debido a su complejidad y cierta incertidumbre, las técnicas de computación ligera o soft computing (redes neuronales, algoritmos genéticos, recocido simulado, algoritmo de colonia de abejas, etc.) pueden ser los elegidos frente a planteamientos tradicionales, más físicos, para predecir el comportamiento de los procesos de mecanizado y optimizarlos.
La figura 2 muestra la evolución desde el diseño a la fabricación y la marcada influencia de los datos de entrada del proceso, herramientas, materiales y requisitos de la pieza. Evidentemente, los datos de proceso y los modelos apropiados pueden conducir las decisiones de diseño y de fabricación hacia objetivos con niveles mayores de complejidad. Modelos con características sutiles del proceso y combinados con herramientas sofisticadas como inteligencia artificial por ejemplo, pueden ser de gran utilidad para el ingeniero en las etapas preliminares de diseño para verificar los efectos del diseño sobre el rendimiento del proceso. En los últimos años, herramientas de simulación del tipo de modelos mecanísticos y térmicos han probado su utilidad en la predicción de variables del mecanizado dentro de un amplio rango de parámetros de operación. Sin embargo, estos paquetes de simulación raramente se integran en módulos de optimización de parámetros. Los enfoques tradicionales para la planificación de las operaciones de mecanizado se basan en resultados que a su vez son más bien experimentales o en reglas de operación basadas en la experiencia humana (de tipo intuitivo y sin base fundada). La pregunta es por tanto, si las herramientas de simulación de procesos se incorporan de manera eficiente sobre un procedimiento de optimización multivariable para seleccionar óptimos parámetros de mecanizado.
Muchas veces un modelo (de fuerza, térmico) combina tanto componentes físicos como experimentales y de hecho esto es una ventaja frente a modelos analíticos en forma cerrada ya que permite obtener representaciones más precisas. Se suele proceder de forma iterativa para reajustar (optimizar) las simulaciones a los resultados reales, mediante la sintonización de los parámetros del modelo que dependen de la experimentación. Algunas variables clave en el día a día de la empresa son:
- Predicción de la vida (desgaste) de la herramienta
- Predicción de la precisión del componente (tolerancias de forma y acabado superficial)
- Predicción de la integridad superficial
- Predicción de los esfuerzos sobre la herramienta y/o sobre la pieza y/o sobre los amarres (fuerzas estacionarias)
- Predicción de la estabilidad del proceso de corte (fuerzas dinámicas)
- Predicción del flujo (control) de viruta
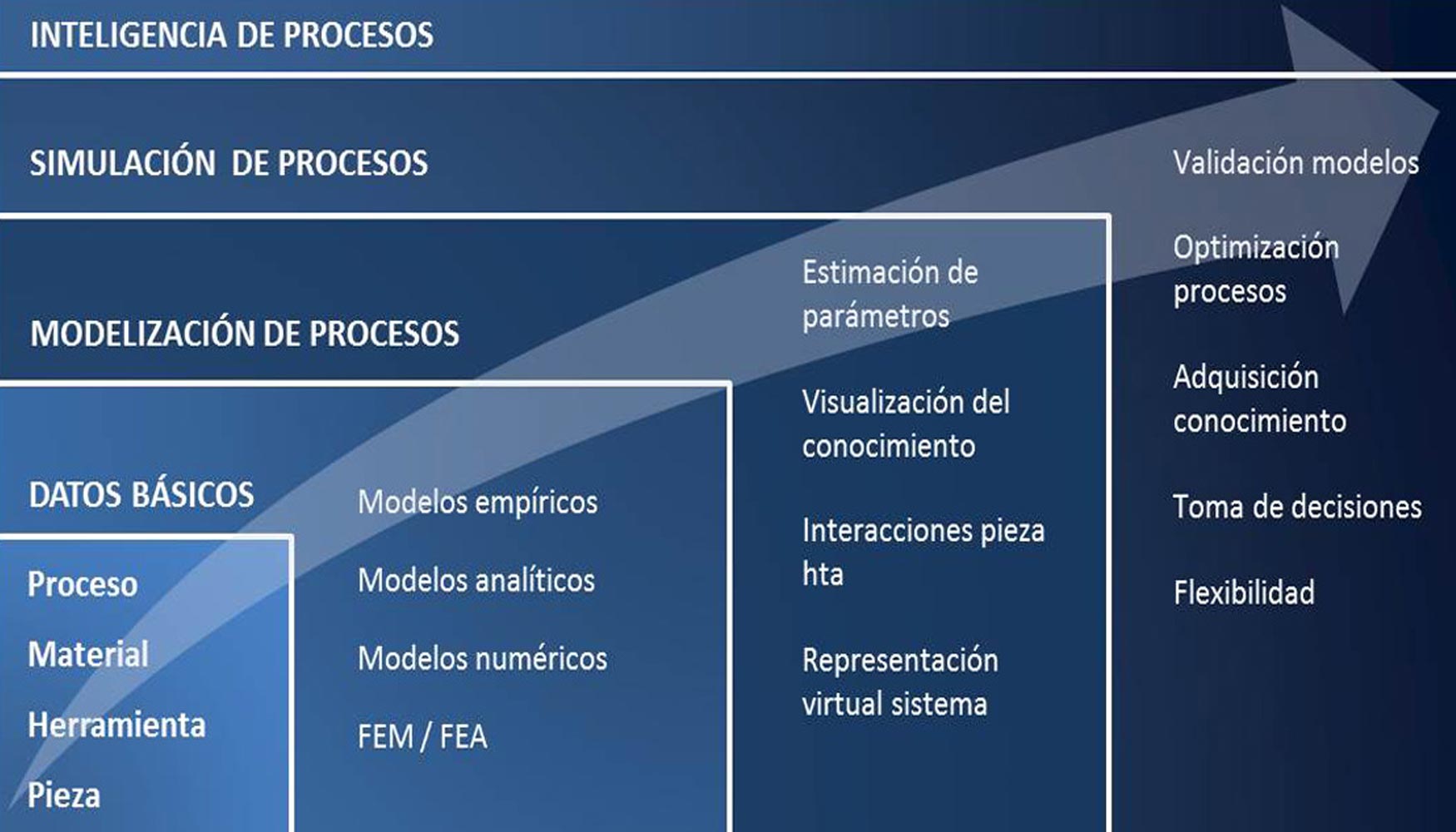
2.1. Caso de aplicación: Caracterización del comportamiento dinámico de una máquina
La exigencia del cliente de piezas con tolerancias cada vez más precisas ha llevado al fabricante de máquina herramienta al diseño de máquinas más flexibles en el tipo de operaciones que permitan realizar la pieza en una única atada. Por ello, la tendencia en los últimos años ha sido la de hacer tornos que realicen operaciones de fresado y a la inversa, por lo que la división entre tornos y fresadoras es cada vez más difusa. Sin embargo, el fabricante tradicional de centros de fresado desconoce el comportamiento real de su nuevo concepto de máquina en operaciones de torneado siendo necesario una puesta a punto de la misma que garantice niveles de calidad, fiabilidad y repetibilidad antes de la venta. Muchas veces, estas pruebas se llevan a cabo delante del propio cliente para que éste verifique en primera persona las capacidades de la máquina y dé el visto bueno final a su compra.
La modelización del comportamiento dinámico es una herramienta clave para el fabricante de máquinas. Para ello, puede realizarse la estimación de la profundidad máxima de corte sin vibraciones (regenerativas o chatter) que puede conseguirse, una vez conocidas las características del sistema. Esto se lleva a cabo mediante los conocidos como diagramas de lóbulos, los cuales separan el espacio de trabajo —revoluciones de la pieza x profundidad de corte— entre condiciones estables (recomendables) e inestables (prohibidas) mediante una curva límite. Para ello son necesarios:
- Los parámetros dinámicos del sistema: dados por el elemento más flexible (pieza, herramienta, máquina, etc.).
- Condiciones de corte: geometría de operación de corte, material, geometría de herramienta.
En este caso, se representa la metodología seguida para evaluar las capacidades de arranque de una máquina multiproceso, dadas unas condiciones concretas (exigidas por ejemplo por el cliente). Para la resolución de la ecuación dinámica y representación de los lóbulos, se utiliza un comando del programa Matlab junto con teoría de ecuaciones diferenciales. El modelo necesita como entradas los datos de coeficientes de corte del material, herramienta así como los parámetros modales del elemento más flexible.
La máquina elegida para la validación del modelo es un centro de mecanizado multiproceso. Se trata de una máquina que debe garantizar altas prestaciones en grandes piezas para las operaciones de torneado, fresado y taladrado suministrando una potencia máxima hasta 115 [kW] (6600 [Nm] hasta 180 [rpm]). Posee cinco grados de libertad: X(0/2200) - Z(0/1500) y giro tilt B sobre el cabezal e Y(0/1600) – C(0/360º) sobre el plato de amarre (figura 3), el cual puede alcanzar un máximo de 300 [rpm] (20 [rpm] en fresado). En modo torno, la máquina bloquea un adaptador HSK100 a Capto. El diseño del cabezal permite la interpolación del eje en operaciones complejas de fresado o trabajar con el eje del portaherramientas en dirección horizontal o vertical en operaciones de torneado (Figura 3).
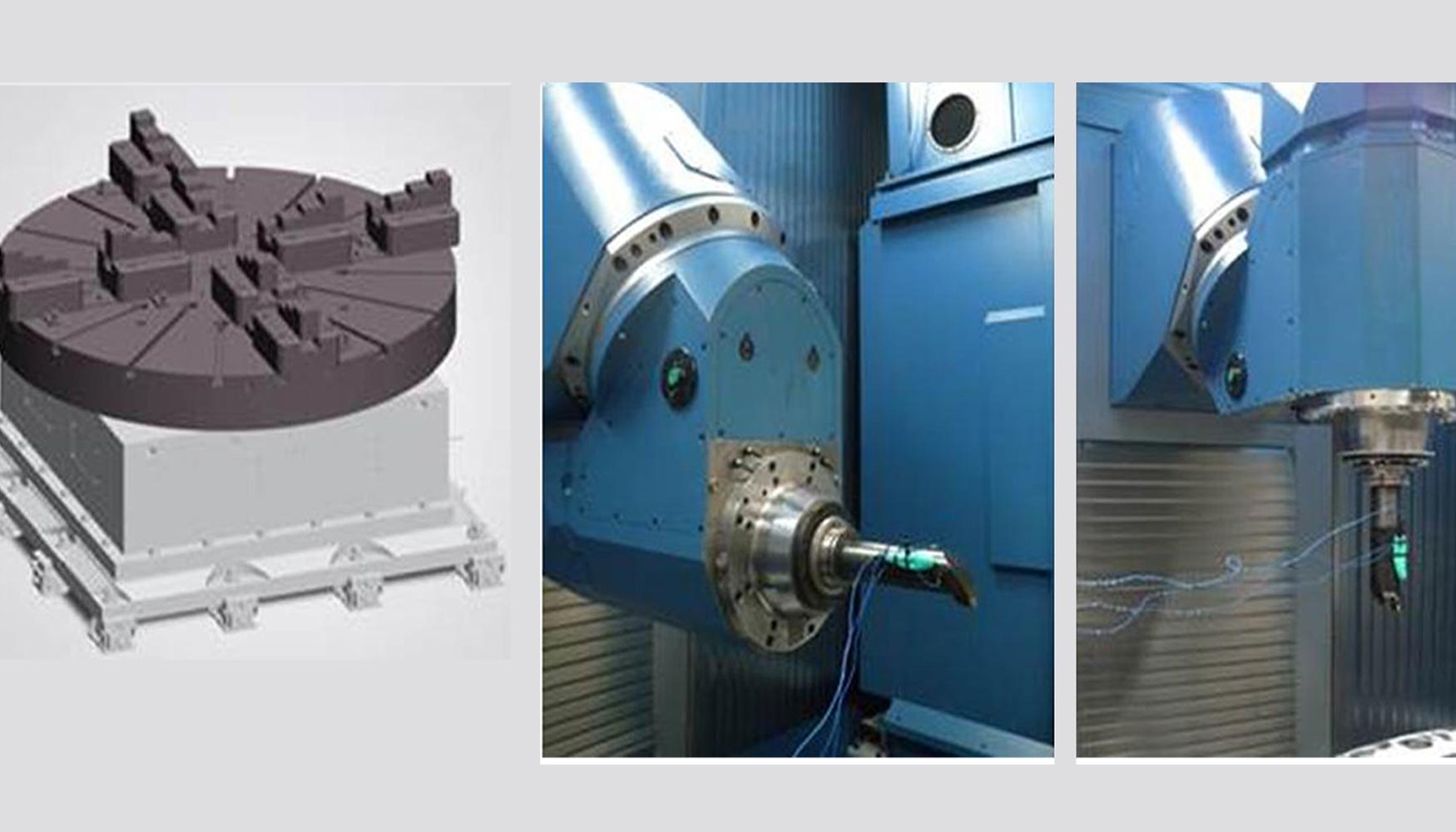
Figura 3. a. Vista CAD del plato accionado por motor de par; b. Configuraciones de husillo horizontal (H) y vertical (V).
En primer lugar, del análisis por elementos finitos de los planos máquina se obtienen los datos generales de pesos de los elementos fundamentales. La tabla 1 representa para dos máquinas con la misma arquitectura la diferencia en el peso concentrado sobre la bancada, reducido a más de la mitad en la nueva máquina. De aquí, se deduce la notable disminución en el peso propio de la máquina entre los dos diseños: es lo que se conoce como optimización topológica. La notación de la máquina se refiere al curso en X. Así, el nuevo modelo permite mecanizar piezas de mayor diámetro.
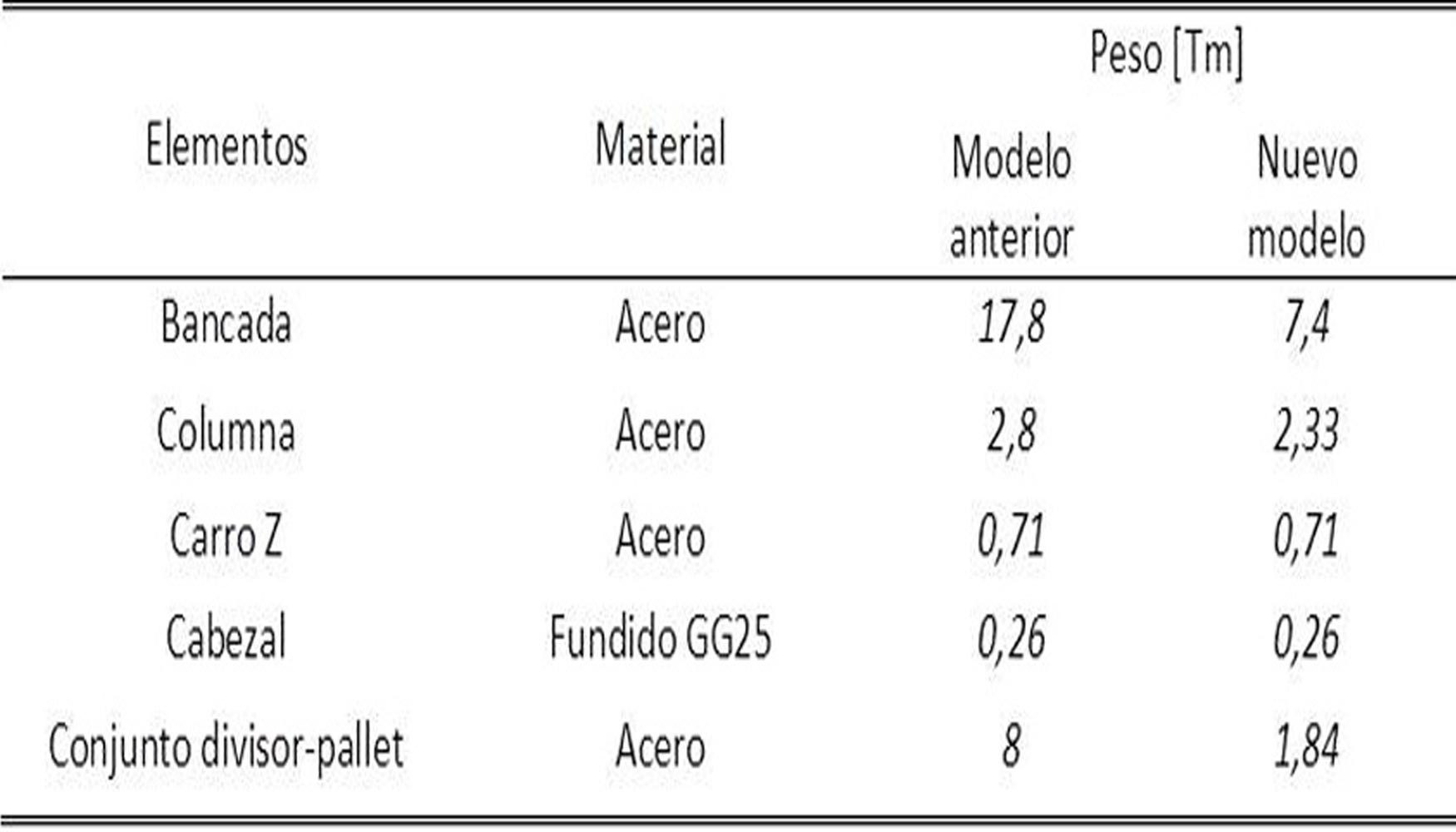
Tabla 1. Propiedades de máquina prototipo nuevo modelo y comparación con modelo anterior.
Para la estimación de la rigidez estática, se realizó una simulación por elementos finitos de la máquina, partiendo de los ficheros 3D facilitados por el fabricante. Se tomaron las simplificaciones habituales del MEF, además de la forma de modelizar husillos, transmisiones, masas auxiliares, elementos de apoyo y de unión. Para el cálculo, se aplicó una fuerza genérica de 1.000 [N] en punta de herramienta (TCP) en las tres direcciones. También se tuvo en cuenta el efecto de la gravedad. Los resultados principales se muestran en la Figura 4. En este caso, únicamente se consideran las deformaciones directas; las cruzadas son, en comparación, residuales.
![Figura 4. MEF y tabla de diagnóstico de máquina (con pieza 8 [t]) Figura 4. MEF y tabla de diagnóstico de máquina (con pieza 8 [t])](https://img.interempresas.net/fotos/1065502.jpeg)
Para la caracterización dinámica de la máquina, se llevaron a cabo ensayos de impacto con martillo instrumentado de Dytran (5803A), acelerómetros y analizador de vibraciones. La caracterización sobre el lado del cabezal suele realizarse con mandrino estándar pero en este caso se optó por realizar las pruebas con capto C6 de voladizo L = 245 [mm]. Se tomaron las funciones de respuesta en frecuencia (FRF) en las posiciones de trabajo del cabezal bajo las configuraciones horizontal (H) y vertical (V). Se determinó un único modo como determinante en cada caso. La tabla 2 muestra los parámetros modales donde los pesos ux, uy y uz tienen en cuenta la rigidez del modo en cada dirección. En este caso, la velocidad de corte está alineada con el eje X.
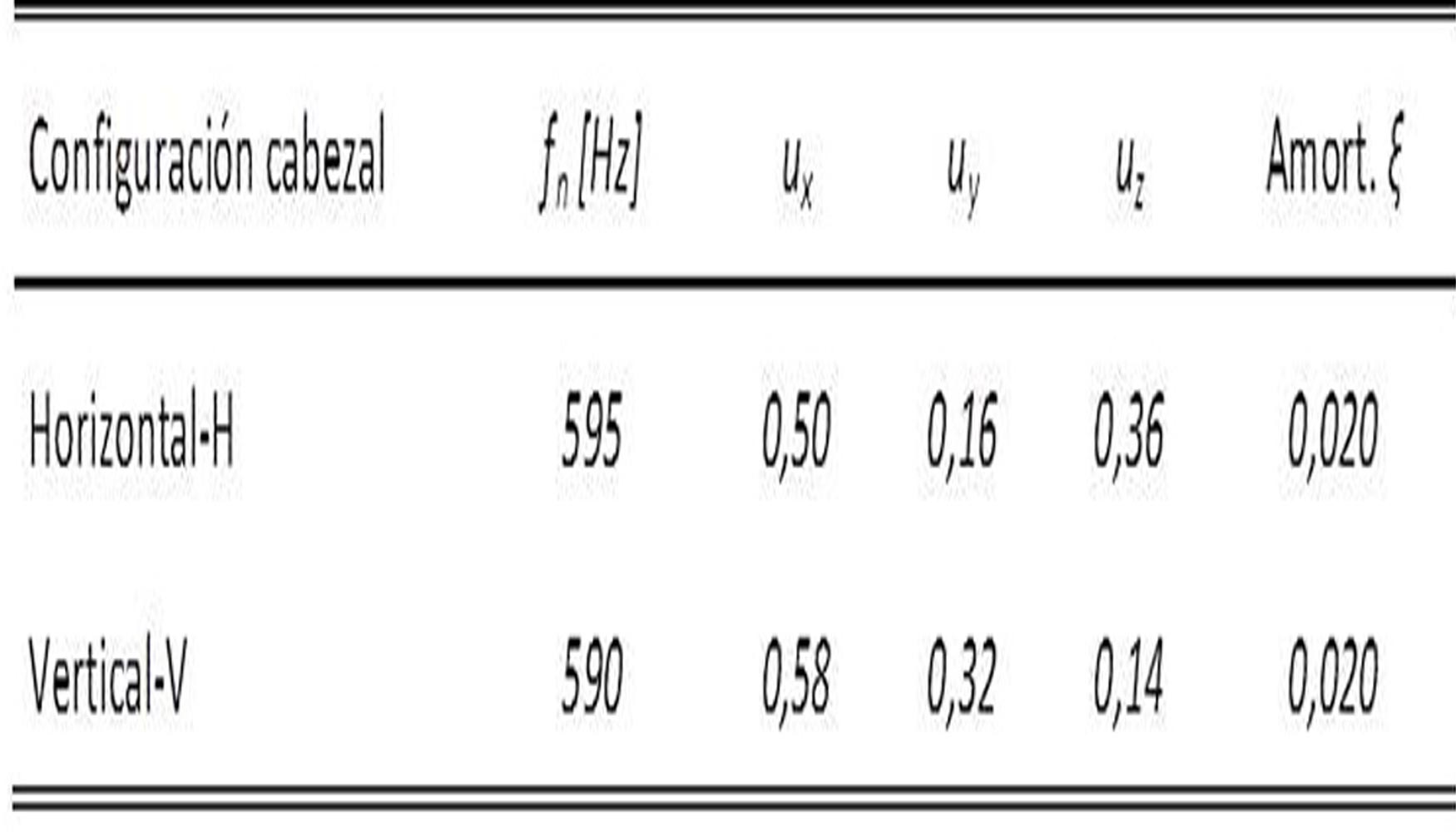
Las operaciones se llevaron a cabo con herramienta rómbica de 80 [°] (CNMG 120408-PR con κr = 95 [°] y calidad 4325), portaherramientas HSK a capto C6-PCLNR-45165-12H y longitud de voladizo L = 245 [mm]. Esta herramienta también es habitual entre las operaciones a realizar sobre el tipo de componente a fabricar por la máquina. En cuanto a las energías específicas de corte, dado que la herramienta trabaja por encima del radio de acuerdo, se admitió la hipótesis de coeficientes de corte constantes: Ktc = 2.900 [MPa], Krc = 850 [MPa] y Kac = 625 [MPa]. El avance fue fijado en todos los casos como fz = cte = 0,5 [mm/rev].
Durante los ensayos, se colocaron sobre el portaherramientas lo más cerca posible de la punta de la herramienta dos acelerómetros (352C22) en las direcciones de avance y de corte (Z-X para cabezal en horizontal e Y-X para cabezal en vertical) y un micrófono (ICP-130D20) para captura de ruido de corte. Para el caso de cabezal en H, las simulaciones realizadas generaron profundidades críticas de ap, cri = 1,5 [mm] y de ap, cri = 3,5 [mm] para los procesos de cilindrado (C) y refrentado (R), respectivamente (figura 5). Se observa un acuerdo razonable entre el límite crítico predicho por las simulaciones y el límite experimental (puntos indicados con rombos). Teniendo en cuenta que la herramienta escogida presenta un ángulo de posición κr = 95 [⁰] independientemente de la operación considerada y de la configuración de cabezal, para el caso CH la componente dominante se produce en la dirección Z (aproximadamente) mientras que para el caso RH es la dirección en X (también aprox.). Se observa que incluso para el límite cercano a la zona del radio como es el caso de la Figura 5, el diagrama de lóbulos alcanza una precisión razonable con respecto a los puntos ensayados.
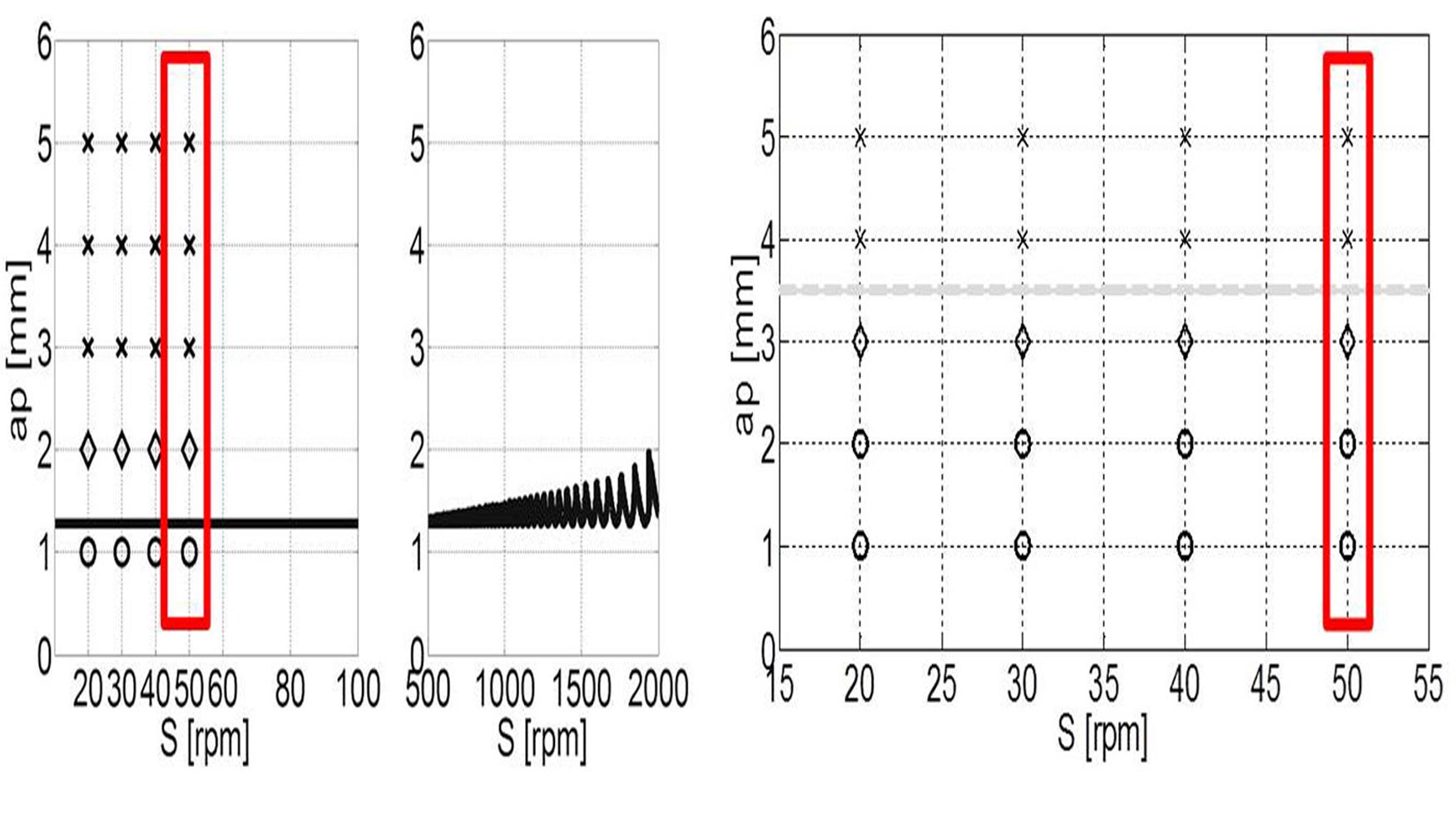
Las curvas de estabilidad se han contrastado además con un modelo temporal que utiliza el mismo comando de Matlab para resolver en el tiempo la ecuación dinámica. La fiigura 6 muestra la evolución del comportamiento vibratorio para la velocidad S=50 [rpm] y fz=0,5 [mm/rev], donde se comprueba una buena correspondencia con las gráficas de estabilidad anteriores.
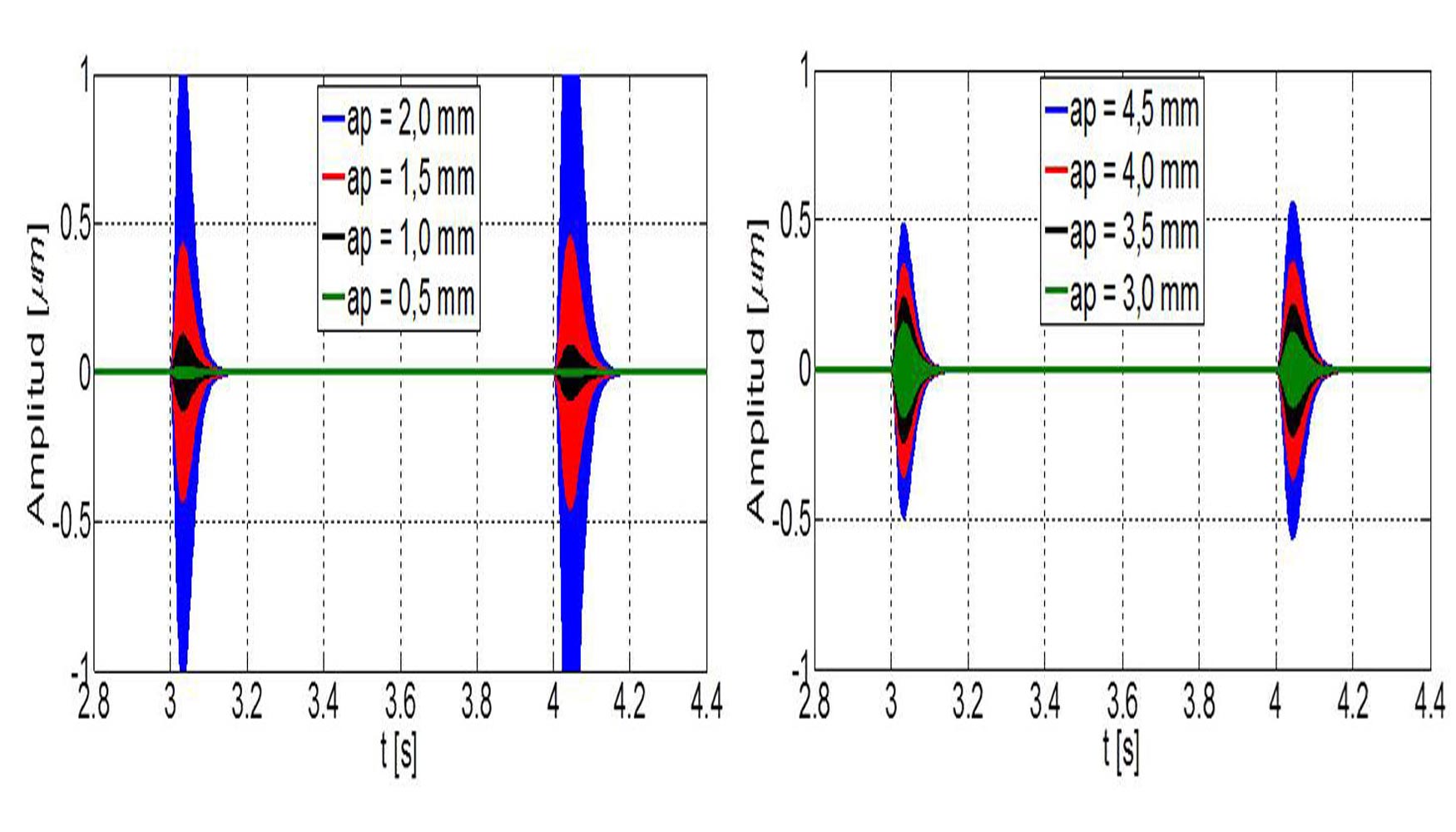
Por tanto, el modelo ensayado ha sido capaz de corroborar ensayos experimentales sobre la máquina y queda verificado para su uso posterior por parte de la empresa. La utilización del modelo es doble:
- Por un lado, permite estimar las profundidades de corte máximas de diferentes arquitecturas de máquinas (para casos de chatter de máquina en desbastes, donde la flexibilidad de la herramienta se desprecia). Es de utilidad, en máquinas que sólo están en fase de diseño para su optimización.
- Por otro, la modelización puede usarse para evaluar las capacidades de arranque bajo una configuración dada (chatter de herramienta, pieza o máquina): material, herramienta, portaherramientas, condiciones de corte concretas (caso estudiado).
3. Verificación virtual, cada día más cerca de la realidad
Una vez generados modelos virtuales de procesos y máquinas, la simulación computacional puede ayudarnos a predecir defectos, optimizar parámetros o controlar las variables dependientes del proceso. En esta línea, cualquier etapa de fabricación es susceptible de ser sometido a simulación, siempre y cuando exista un modelo matemático o numérico que así lo permita. La simulación de procesos es una técnica que posibilita, entre otras cosas, comprobar si las operaciones que se están llevando a cabo en el proceso son las más adecuadas o yendo más allá, permite variar determinadas operaciones dentro de un proceso, su orden u otros aspectos para obtener una pieza final en las mejores condiciones posible, disminuyendo las distorsiones finales.
Dentro de la palabra simulación, se abre un abanico muy grande de posibilidades. En el campo de la fabricación mecánica se pueden simular las operaciones de mecanizado a las que se le va a someter a una pieza para obtener un valor de las distorsiones que va a sufrir después de mecanizado; se puede simular el proceso de forjado, teniendo una representación muy visual del flujo del material entre los troqueles, lo cual permite mejorar su diseño para lograr que el material alcance todos los huecos; también es posible simular el proceso de colada en un proceso de fundición, lo cual permite optimizar y dimensionar los canales que va a atravesar el fundido, mazarotas, bebederos etc.; así como procesos de inyección y otros donde las simulaciones son de gran ayuda para la toma de decisiones.
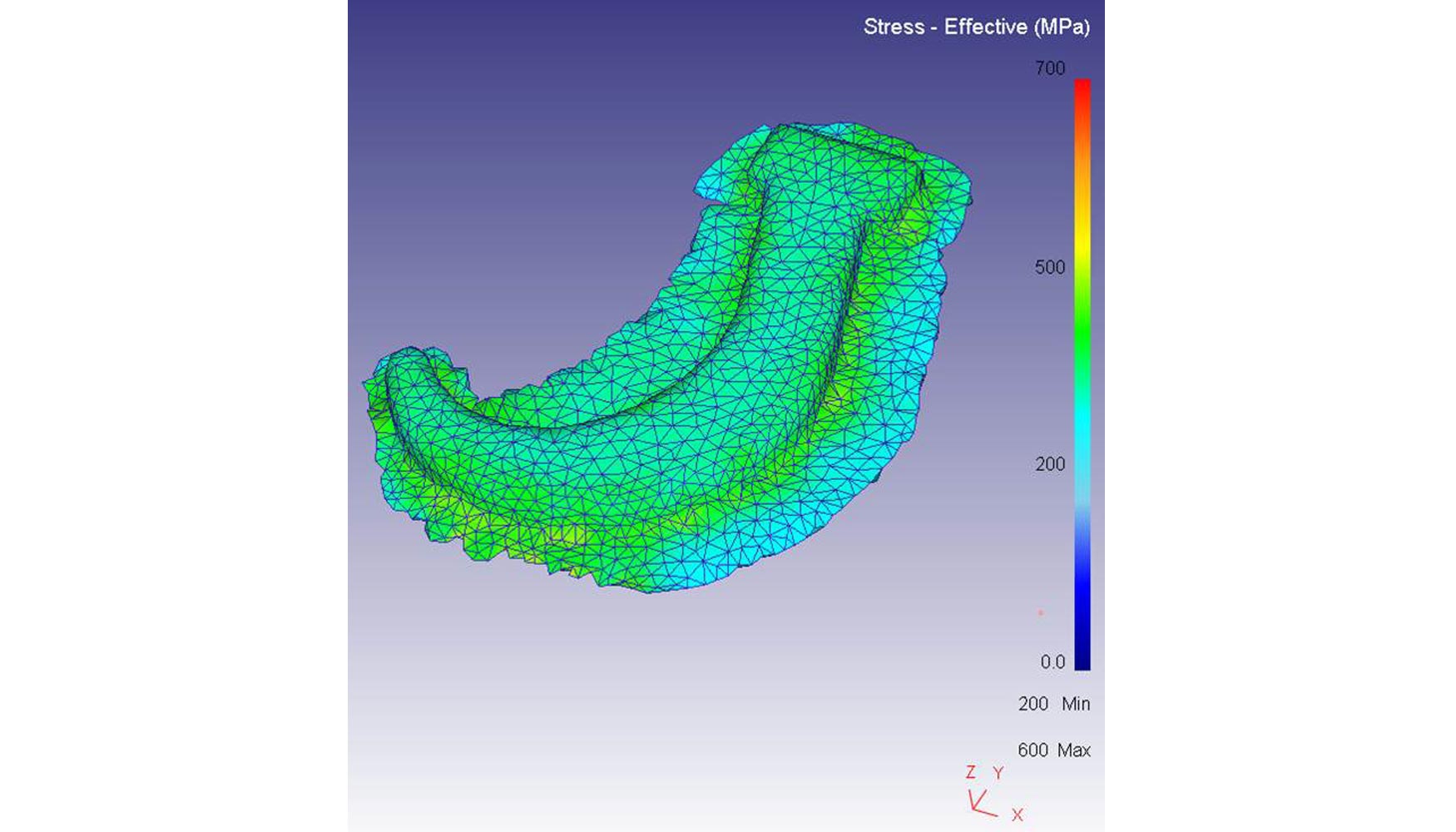
La simulación no es algo nuevo. En el campo del mecanizado se viene utilizando desde hace muchos años cuando los pioneros Ernst y Merchant realizaron en 1945 los primeros estudios de la mecánica del corte. Posteriormente Armarego generalizó para el corte oblicuo los estudios realizados para el corte ortogonal. Más adelante otros científicos desarrollaron otros modelos de fuerzas para el caso de fresas helicoidales y de geometría esférica. Quizá el término correcto en estos casos sea el de modelización, aunque en el fondo no deja de ser una simulación, ya que lo que se persigue es estimar determinadas variables, como fuerzas o potencias, en base a ecuaciones matemáticas o datos empíricos de ensayos simples. Estos son los llamados modelos analíticos, que son básicos pero pierden utilidad cuando el fenómeno físico se complica. Ahí entran en juego los métodos numéricos, de entre los cuales el más ampliamente difundido y utilizado es el conocido Método de los Elementos Finitos (MEF), aunque hay otros como el Método de las Diferencias Finitas, comúnmente utilizados también en otros campos de la ciencia.
El MEF tiene mucho tiempo de vida en otras disciplinas como en el cálculo resistente de estructuras, o en el diseño industrial de piezas de máquinas y mecanismos, sin embargo en el ámbito de la fabricación no tiene tantos kilómetros. En este campo de la ciencia, el MEF es muy útil para obtener el campo tensional o la distribución de temperaturas durante el corte en un proceso de mecanizado, tanto en el material como en la herramienta. También es válido para predecir las distorsiones que va a sufrir una pieza después de su mecanizado, siempre haciendo previamente ciertas hipótesis, por ejemplo sobre los flujos de calor entre los diferentes elementos intervinientes en un modelo térmico, o el campo inicial de tensiones residuales en un tocho a mecanizar si no es posible su cuantificación mediante medida directa. La necesidad de estas hipótesis de partida es precisamente una de sus desventajas.
Actualmente, en el campo del mecanizado, son tres los software de simulación por elementos finitos más utilizados: AdvantEdge, Deform 3D y Abaqus. En una primera fase inicial, los resultados obtenidos en las simulaciones con este software, son comúnmente verificados con resultados experimentales para aceptar su validez. En ocasiones, es muy común el uso conjunto de más de uno de ellos en los diferentes pasos de la simulación de un proceso, por ejemplo obteniendo los campos tensionales y térmicos con Deform 3D usualmente y posteriormente introduciéndolos como entrada en un modelo de mecanizado en Abaqus.
En la figura 8 se puede ver a la izquierda un modelo de simulación térmico en un arranque de viruta de Inconel 718 en 2D con herramienta de torno realizado en la Escuela de Bilbao con el software Thirdware AdvantEdge, y a la derecha otra imagen similar pero esta vez un modelo en tres dimensiones de un brochado de Waspaloy realizado también en la UPV/EHU usando el software Deform 3D.

Un aspecto de gran importancia en la fabricación mecánica es el de las tensiones residuales. Como es sabido, las tensiones residuales surgen como respuesta a los diferentes procesos de fabricación a los que se va sometiendo a una pieza hasta llegar a su estado final. Durante estos diferentes procesos, a la pieza se le va eliminando material, y por ello, por ejemplo en un mecanizado, surgen deformaciones plásticas y variaciones muy localizadas de temperatura, que pueden provocar variaciones microestructurales y aparición de tensiones residuales. Estas tensiones están presentes en el interior del material aún en ausencia de fuerzas exteriores, es decir, están auto-equilibradas, es por ello que durante el proceso de fabricación de una pieza esta pueda sufrir distorsiones como respuesta a la liberación de estas tensiones hasta lograr un nuevo estado de equilibrio interno de fuerzas.
Conocer el campo de tensiones residuales en el tocho de partida es de vital importancia antes de acometer el mecanizado de determinadas piezas, o en caso de no ser posible obtenerlo de forma cuantitativa, por lo menos poder simularlo adecuadamente conociendo la forma en la que se ha obtenido ese tocho inicial, por ejemplo mediante forjado. Un ejemplo muy claro de este tipo de piezas son los discos de turbina de gas aeronáutica o de producción de energía, los cuales poseen un alma de muy poco espesor en relación a su tamaño. Estas piezas son enterizas, mecanizadas de un tocho inicial, por tanto es de suponer que el volumen de material eliminado sea muy alto, y esto hace que a medida que el tocho inicial va reduciendo su volumen, las tensiones residuales juegan cada vez un papel más importante, ya que debido a la perdida de rigidez que va sufriendo la pieza como consecuencia de la pérdida de material, esta puede llegar a sufrir distorsiones nada despreciables. Es en este caso donde la simulación entra en juego. Gracias a ella, y conociendo determinados datos de entrada, como por ejemplo la estrategia de mecanizado, el mapa de tensiones residuales inicial, el tipo de material o el proceso de fabricación a emplear, es posible cuantificar las distorsiones, y por ello actuar en consecuencia variando la estrategia de mecanizado, orden de las operaciones de mecanizado, o incluso los parámetros del corte para lograr reducir al máximo estos problemas.
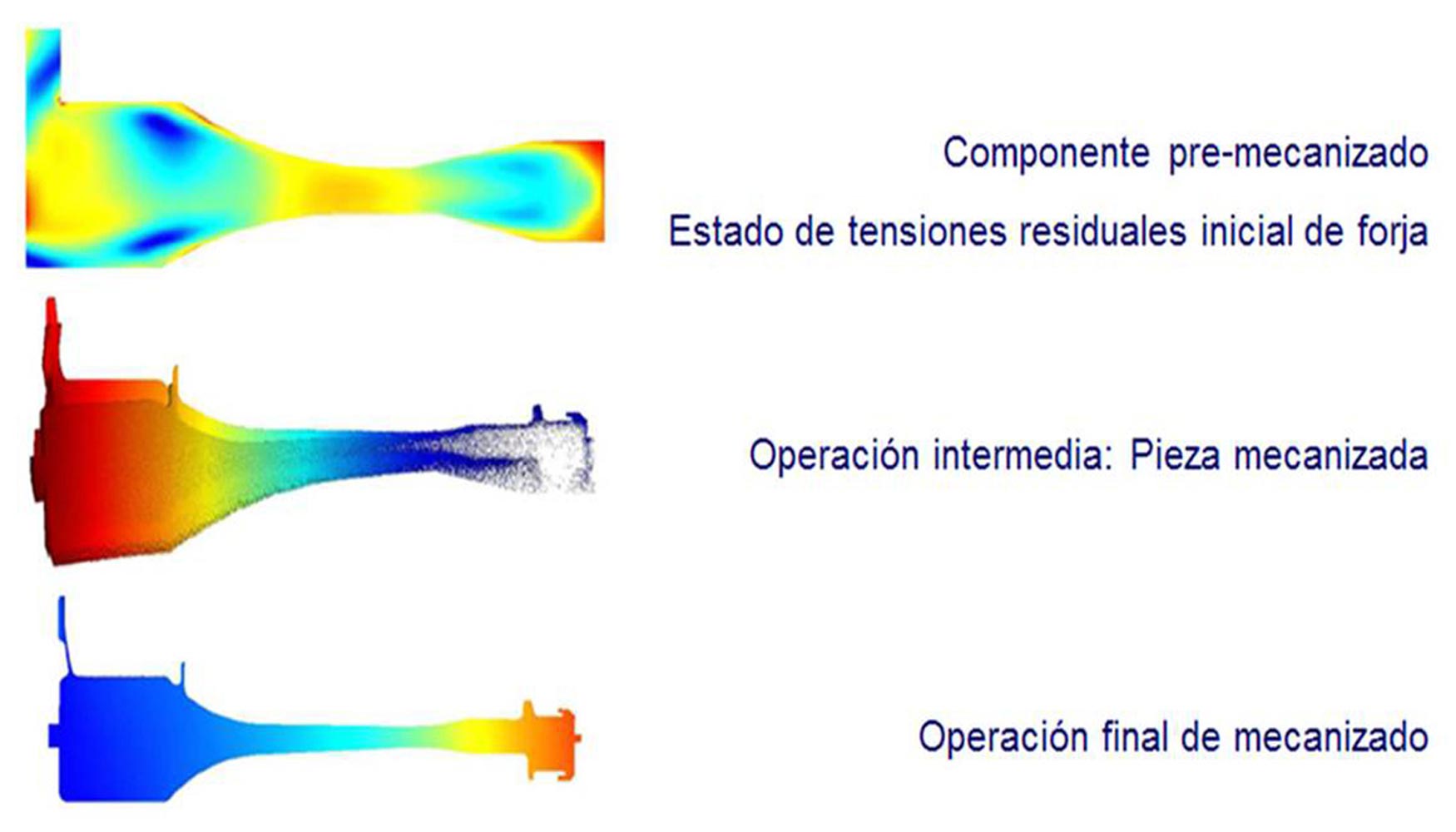
Antes se ha comentado que para poder simular el mapa de tensiones residuales inicial del tocho de partida en el mecanizado de una pieza, es necesario conocer la forma en la que se ha obtenido este tocho. De hecho, gran parte del trabajo de simulación se centra en estas primeras etapas, simulando los procesos más habituales para la obtención de la preforma que constituye el tocho de partida para el mecanizado de una pieza, como por ejemplo procesos de forjado, fundición o estampado. Así mismo, cuando el tocho de partida sufre algún proceso de temple o tratamiento térmico que confiera al material determinadas propiedades mecánicas o de otro tipo, este es susceptible de ser simulado, como por ejemplo el conocido ‘water quenching’ para lograr un enfriamiento rápido después de un tratamiento de solubilizado previo al precipitado en las aleaciones de alta temperatura. Este enfriamiento rápido crea unos gradientes de temperatura muy elevados en el interior de la pieza mientras el proceso de enfriamiento se está llevando a cabo, lo que puede ocasionar que el estado tensional interior de la pieza quede sustancialmente alterado, el cual a la hora de mecanizar piezas de pared delgada, como por ejemplo el disco de turbina antes comentado, favorezca la aparición de grandes distorsiones en la pieza. Ahí es cuando la simulación se hace fuerte, previendo la magnitud y sentido de las distorsiones para adelantarse a ellas variando la estrategia de mecanizado y lograr una pieza final libre de defectos.
Como en todas las cosas de la vida, no todo son ventajas, también hay inconvenientes. Primero de todo hay que tener presente que en sentido general, una simulación no deja de ser una simulación, es decir, una representación virtual de la realidad, que no tiene por qué serle completamente fiel. A esto hay que añadir que muchas veces hay que realizar hipótesis de partida con datos estimados o que directamente no se conocen, lo cual favorece esta separación entre la realidad y el resultado simulado. Por supuesto otro inconveniente es el tiempo de cálculo necesario para que las simulaciones se lleven a cabo, el cual cuando el fenómeno es muy local con mallas muy refinadas en el caso de los elementos finitos, resulta muy elevado.
En el caso que nos ocupa de las simulaciones en el mecanizado la cosa se complica. La simulación de un proceso de mecanizado actualmente solo es posible prácticamente mediante modelos de elementos finitos, y esto representa un esfuerzo computacional muy elevado incluso tratándose del arranque de un pequeño fragmento de viruta que en la realidad puede ser tan poco tiempo de mecanizado como milisegundos. Hay que tener en cuenta que el proceso de arranque de viruta es un fenómeno físico muy complejo, donde se juntan no solo grandes deformaciones sino también elevadas tasas de deformación. Este fenómeno tan localizado en la escala de la viruta tiene problemas en el contacto, con efectos debido a la fricción y a la cortadura, los cuales son sumamente difíciles de evaluar y posteriormente resolver mediante la simulación del proceso.
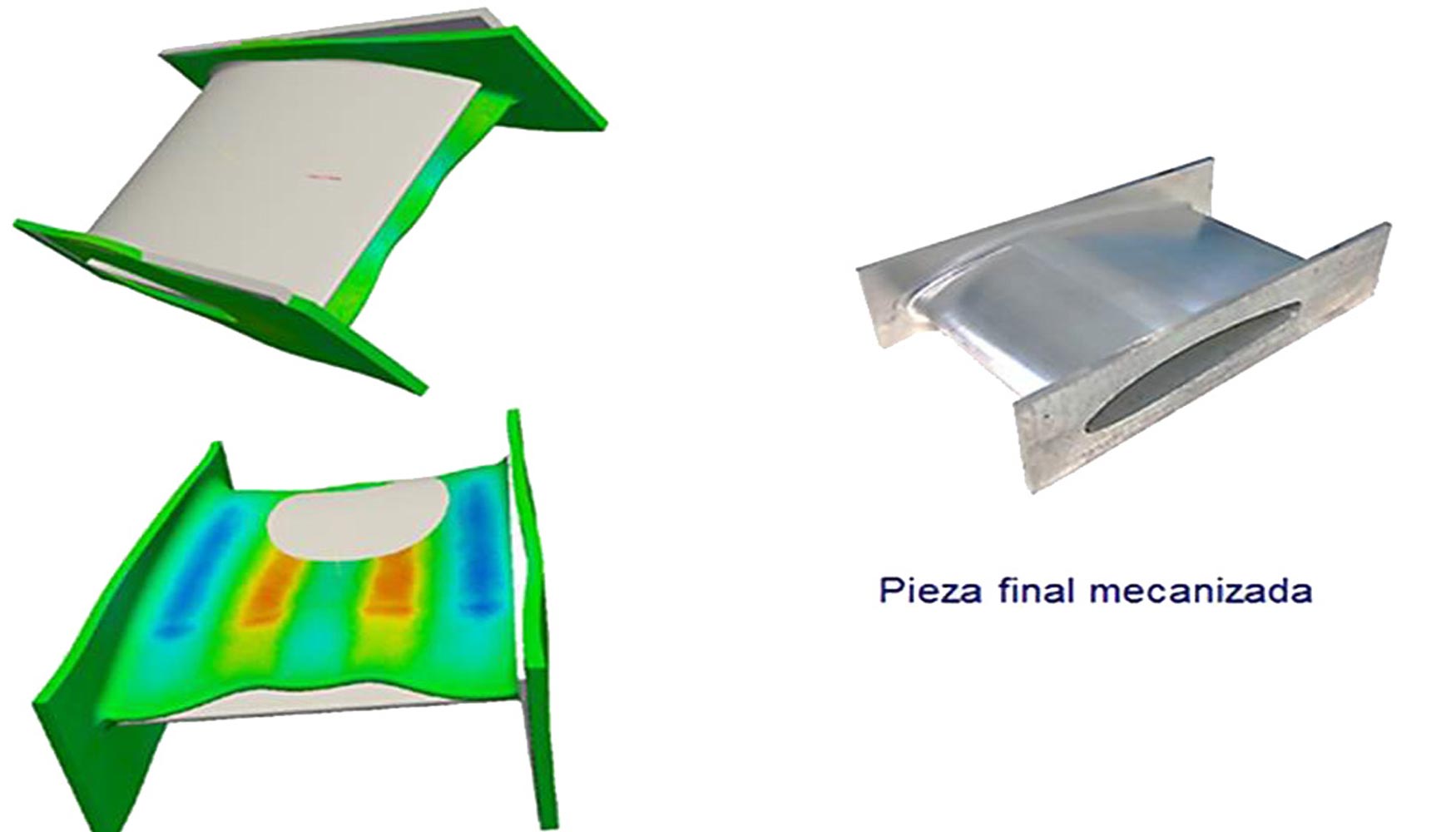
4. Monitorización y control: La clave para conocer qué sucede
Desde el primer CNC realizado por John T. Parsons (Detroit 1913-2007) junto con su empleado Frank L. Stulen en la década de los 40 la monitorización para la optimización de los procesos de mecanizado ha ido evolucionando gradualmente.
El primer hito vino en los años 70 de la mano de la aparición de los ordenadores debido a que tenían una capacidad de procesamiento superior a las antiguas tarjetas electrónicas y grandes hardware que componían los controles de las máquinas de CNC. Con su implementación hubo una mayor resolución de los sensores que se tradujo en una mejor respuesta de los servomecanismos de control en la generación de interpolaciones además de una programación más ‘amigable’ para el operario. Como consecuencia, la calidad de las piezas se vio incrementada pero aún no se tenía una monitorización en tiempo real del proceso de mecanizado tal y como se conoce en nuestros días.
La forma tradicional de trabajar durante los años posteriores consistió en la generación de un programa de CNC inicial en función de la geometría de la pieza y que a medida que se mecanizaban e inspeccionaban las piezas se iban modificando los parámetros de mecanizado como las condiciones de corte, trayectoria de herramienta, etc. con el fin de lograr corregir las posibles desviaciones y obtener la pieza deseada, es decir, en cierta manera se trabajaba en un proceso de prueba-error.
Hoy en día la forma de control de los procesos de corte está clasificada en tres niveles en función de su objetivo. El primero de ellos es el lazo de servomecanismo de control cuya función es regular la posición y velocidad de los ejes y husillos para compensar las desviaciones provocadas por la fricción, el backlash, las fuerzas de mecanizado, etc. El segundo nivel es el lazo de interpolación cuyo objetivo es coordinar el movimiento simultáneo de varios ejes para mantener la trayectoria deseada de la herramienta. El tercer nivel es el lazo de control adaptativo o continuo cuyo objetivo está centrado en aumentar la productividad y la calidad final de la pieza con la ayuda de la monitorización de los parámetros críticos en el mecanizado que aplicados a un modelo mecanístico, algoritmos de control, etc. ajuste automáticamente los parámetros de mecanizado anteriormente mencionados.
Los dos primeros niveles son los que a día de hoy toda máquina-herramienta posee y con los que se ha trabajado hasta nuestros días, pero para lograr mecanizar con “cero defectos” se hace necesario focalizar el interés en el lazo de control adaptativo ya que es la única forma de llegar a optimizar en tiempo real los procesos de mecanizado.
4.1. ¿Qué se mide en el control adaptativo? ¿Cómo se obtienen y aplican los datos?
En el caso del mecanizado, con el lazo de control adaptativo se pueden medir parámetros críticos derivados del proceso de mecanizado como las vibraciones, fuerzas de corte, la potencia consumida por los servomotores o la temperatura de corte. Esto es debido a que gracias a ellos se puede predecir y corregir de forma continua el proceso de corte. Consecuentemente la vida de herramienta se ve aumentada, se produce una mejora de los ciclos productivos, mejora de la integridad superficial de la pieza así como su acabado final.
Para la obtención de este tipo de datos en tiempo real se necesita la instalación de diferentes sensores en la máquina, en la herramienta y/o la pieza en función del tipo de mecanizado que se esté llevando a cabo. Por otra parte, hoy en día la mayoría de las máquinas-herramienta controladas por CNC carecen de los sensores necesarios para la obtención de este tipo de datos y sus PLC carecen del lazo de control adaptativo, por lo que su implementación requiere una actualización de la máquina-herramienta. Dicha actualización consiste principalmente en dotar a la máquina-herramienta de una tarjeta amplificadora para la transformación de las señales y un PC que adquiera, procese la señal obtenida mediante la aplicación de los modelos mecanísticos y que le indique al PLC de la máquina-herramienta la corrección a realizar en el avance, posición y/o velocidad. En la figura 11 se muestra un esquema simplificado de una máquina-herramienta con los tres niveles de control de los procesos implementados.
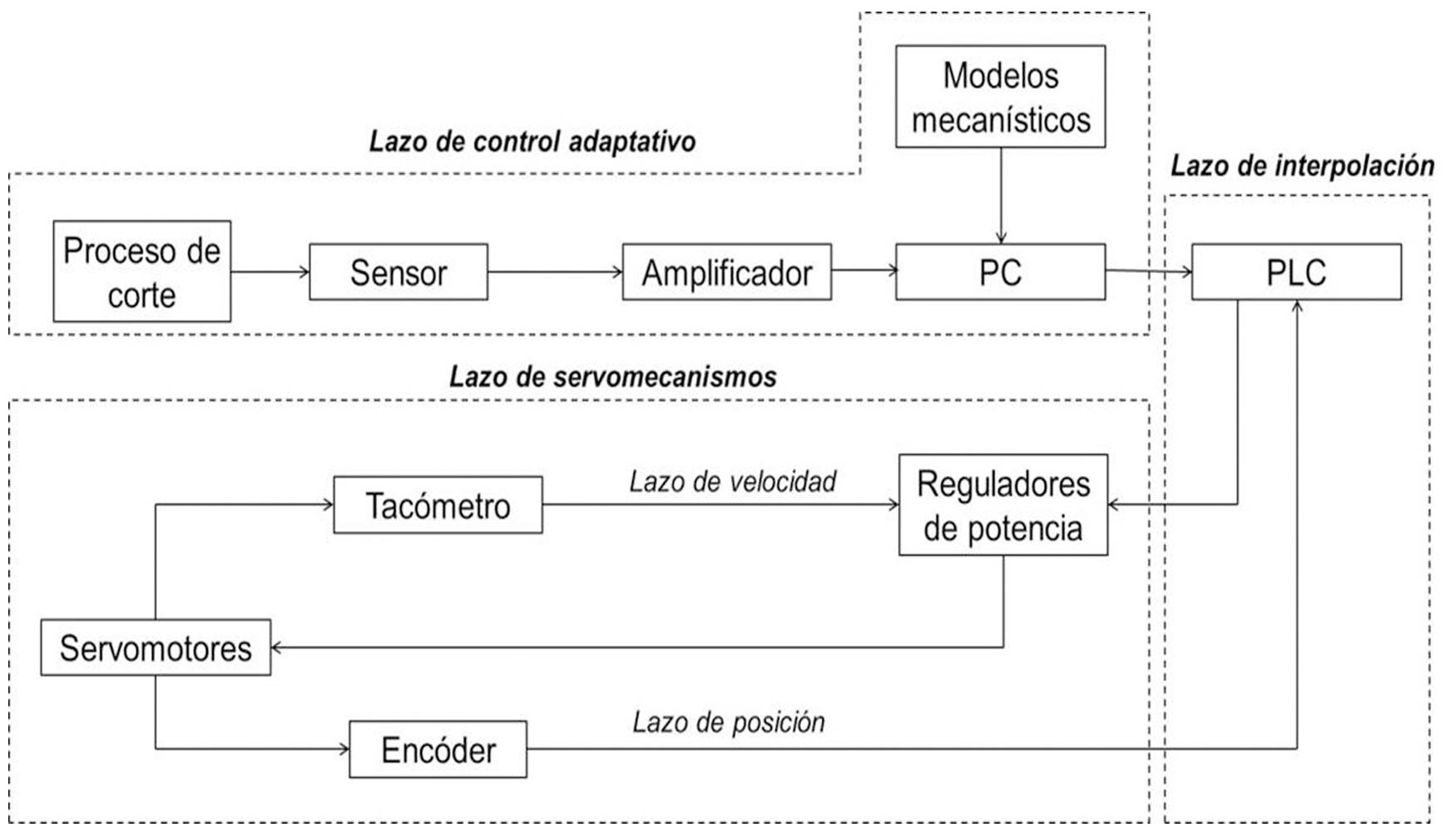
4.2. ¿Qué sensores se utilizan? ¿Qué quieren decir los datos obtenidos? ¿Para qué sirven?
Como se indicó anteriormente, para obtener los datos necesarios de los parámetros críticos se necesita la instalación de unos sensores que sean capaces de captar la magnitud física en cuestión y transformarla en una señal analógica. Por ejemplo, para la medición de las vibraciones normalmente se utilizan unos sensores conocidos como acelerómetros que pueden ser mecánicos, capacitivos, micromecánicos o piezoeléctricos. Estos últimos son los más utilizados en el sector del mecanizado y su funcionamiento generalmente se basa en la producción de una carga eléctrica en función de la fuerza aplicada sobre un retículo cristalino piezoeléctrico. Estos sensores deben de estar colocados lo más cerca posible de la zona de corte. En caso de ser usados en procesos de fresado se recomienda utilizar un acelerómetro triaxial, el cual mide las vibraciones en los tres ejes cartesianos, y colocarlo sobre la pieza mecanizar. Por otra parte, si se procede al torneado se recomienda colocarlo en el portaherramientas en la cara opuesta al inserto. En este caso la utilización de un acelerómetro uniaxial en la dirección de corte sería suficiente.
Con los acelerómetros se puede prevenir la aparición del chatter regenerativo que se traduce en un mal acabado superficial, desgaste prematuro de la herramienta y un aumento considerable de las fuerzas de corte. Con las señales obtenidas por el acelerómetro se pueden calcular las varianzas de los rangos de las frecuencias altas y bajas, respectivamente y de ahí obtener su ratio. Si el valor de su ratio tiene un valor considerablemente menor que uno indica la presencia de chatter regenerativo con lo cual las condiciones de corte deben ser modificadas para evitar sus efectos adversos.
En cambio, para la medición de las fuerzas de corte se utilizan unos sensores conocidos como dinamómetros. Los más utilizados para el mecanizado son basados en la tecnología de cuarzo. En el caso de los dinamómetros se recomienda la utilización de mesas dinamométricas que sean capaces de medir fuerzas en los tres ejes, es decir, triaxiales. Esto es debido a que de este modo se puede obtener la fuerza total de corte a raíz de sus tres componentes (fuerza de corte, avance y radial). En el caso del fresado la mesa dinamométrica será colocada de tal modo que esté amarrada a la pieza a mecanizar. En el caso del torneado ante la imposibilidad de amarrar la mesa dinamométrica a la pieza, ésta amarrará a la herramienta.
Con las mesas dinamométricas se puede predecir el desgaste de herramienta y así optimizar los ciclos productivos evitando dañar piezas por la rotura prematura de ésta. Además en función de las fuerzas de corte se puede optimizar las condiciones de corte para lograr en medida de lo posible una mayor vida de herramienta. Concretamente, en caso de analizar la componente radial de la fuerza de corte se puede observar como un aumento de ésta implica un desgaste de la punta del inserto. En cambio si el aumento viene dado por la fuerza de avance, éste implica un desgaste excesivo del filo de corte. Un caso concreto estudiado en la UPV/EHU en AISI 304L con diferentes técnicas de refrigeración/lubricación se observó como un aumento de la fuerza de avance implicaba la rotura inminente del inserto como se muestra en la figura 12.
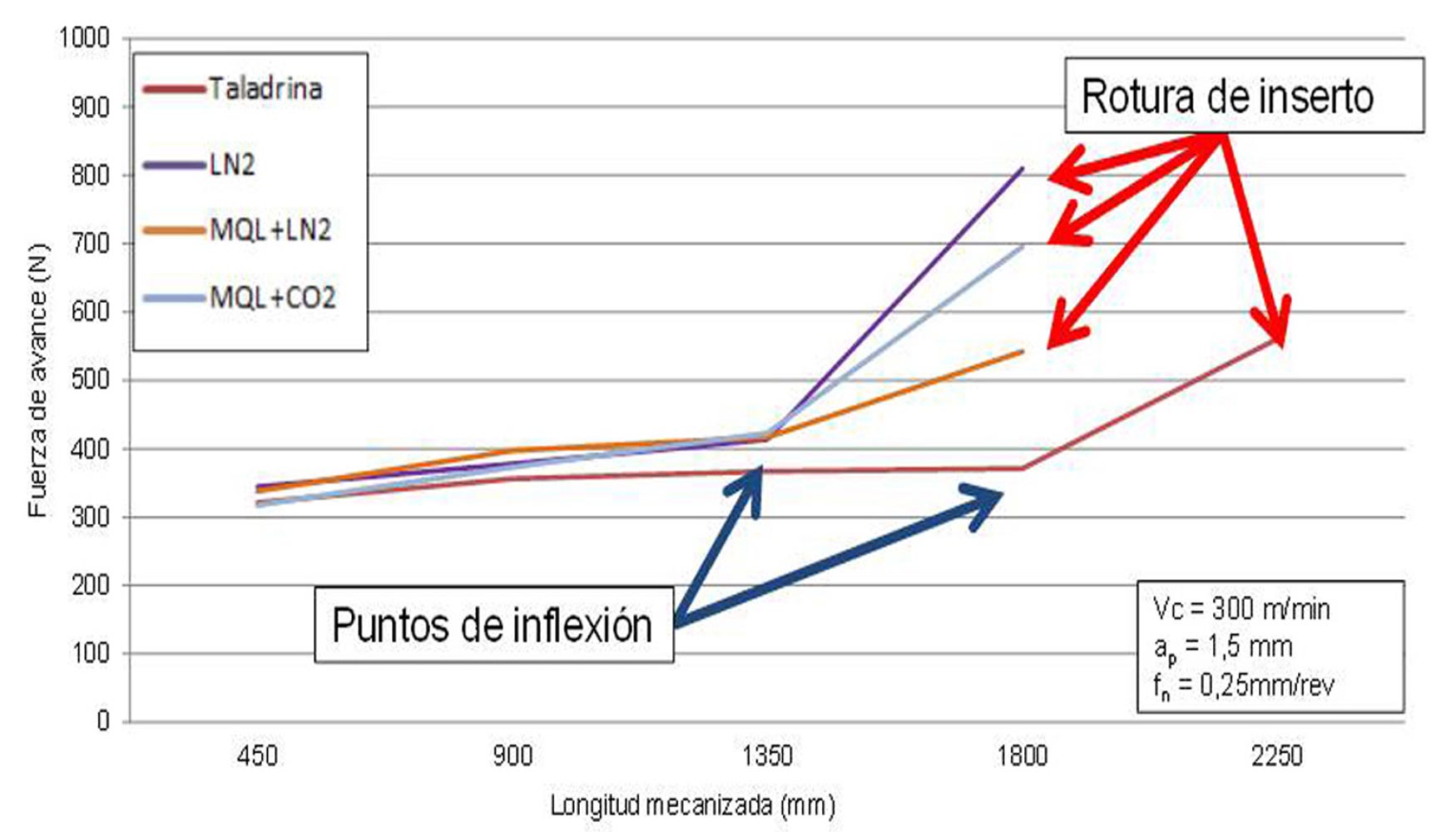
Para poder realizar la medición de la potencia consumida se necesita instalar un medidor de potencia por efecto hall. Este debe ser colocado en las fases de los cables de alimentación al regulador de potencia del servomotor del cual se desea obtener información. En el caso del fresado generalmente el consumo de potencia se suele medir en el servomotor del husillo, en cambio para el torno habitualmente se mide la potencia del servomotor del plato de garras. Un aspecto importante a destacar es la necesidad de controlar el consumo nominal del servomotor por el simple hecho de moverse, es decir, discernir entre la potencia consumida por el propio servomotor y la consumida realmente por el proceso de corte. Por ello, en caso del mecanizado de piezas en serie es recomendable realizar primeramente el mecanizado en vacío con el fin de cuando se tomen los datos durante el mecanizado de la pieza poder realizar el cálculo de cuál es la potencia real consumida por el proceso de corte. En cambio, si se trata de una pieza unitaria existen modelos mecanísticos que realizarían una aproximación del valor real de la potencia consumida.
Con la medición de potencia consumida por los servomotores en el corte lo que se busca es que a partir de dichos valores de potencia eléctrica se pueda establecer un modelo que permita obtener las fuerzas de corte sin necesidad de medirlas directamente. El uso de esta técnica industrialmente es más atractiva desde un punto de vista de operatividad ya que si se utiliza un medidor de potencia por cada eje de la máquina se logra eliminar la necesidad de colocar una mesa dinamométrica y por lo tanto la incomodidad que esta genera por ejemplo en procesos de torneado donde por lo general se utilizan varias herramientas en cada fase de mecanizado.
En cuanto a la medición de la temperatura de corte existen dos métodos para llevar a cabo su medición, pero con ninguno de ellos se obtiene la temperatura exacta ya que la zona de interacción herramienta-viruta-pieza es inaccesible. El primero se basa en la utilización de una cámara termográfica por infrarrojos pero que debido al uso de fluidos de corte la medida real se distorsiona ya que la emisividad de la zona de corte queda totalmente obstruida por éstos. El segundo método es más fiable ya que lo que se hace es colocar el termopar en lo más próximo a la zona de corte con lo cual se obtienen datos que no son reales porque cierta cantidad de energía se disipa hasta alcanzar al termopar, pero lo que sí dan son valores cualitativos de su valor, es decir, a lo largo del mecanizado se puede obtener la variación de la temperatura durante el corte lo cual es de utilidad en los procesos de mecanizado. Los termopares son los más utilizados en ensayos experimentales, pero la problemática de su implementación en el día a día industrial viene dado en que para realizar una medida correcta de la temperatura estos deben ser embebidos dentro de la herramienta de corte o pieza, con lo cual no deja de ser una tecnología “invasiva” que altera el producto final o herramienta de corte, dependiendo donde sea introducido. Por estas razones a día de hoy, a pesar de la importancia de este factor, en los talleres industriales no se utiliza esta variable.
En resumen…
…con una inversión inicial relativamente pequeña se pueden equipar las máquinas-herramienta que hay actualmente con un lazo de control adaptativo en el que gracias a los modelos mecanísticos se pueda predecir desde el comportamiento y desgaste de la herramienta hasta la prevención de la aparición de chatter regenerativo que deteriore el acabado superficial de la pieza. De este modo se elimina el método “prueba-error” que se lleva realizando tradicionalmente, mejorando así los ciclos productivos y optimizando los parámetros de corte en función de sus necesidades de forma continua tratando de alcanzar así un mecanizado con ‘cero defectos’.
5. Metrología en proceso y control activo
En la búsqueda de la competitividad y la mayor rentabilidad de los procesos de fabricación se hace necesaria la integración de un sistema de control que pueda detectar cualquier perturbación y poder tratarla desde su origen. El control metrológico de los procesos de fabricación puede minimizar considerablemente las piezas desechadas y la ineficacia así como mejorar la calidad de las piezas y disminuir el mantenimiento de las máquinas. Todo esto significa evitar retrasos en las entregas y produce una alta trazabilidad de las piezas.
Para desarrollar un proceso de fabricación uniforme, automático y productivo se ha de ejecutar un programa de control metrológico desde el origen. Un método eficiente necesitará de diferentes fases en las cuales se ajustan todas las variables comprendidas entre los diferentes elementos que participan en la fabricación de la pieza, es decir, el centro de mecanizado, las herramientas de corte y la propia pieza a fabricar.
La primera fase está dirigida a maximizar la estabilidad del entorno en el cual se va a realizar el proceso. De esta manera se impide que las causas inherentes al propio proceso de arranque de viruta tengan un impacto en las fases posteriores. Para ello se ha de realizar un análisis exhaustivo de la máquina, pieza y herramientas antes de proceder al mecanizado:
• Control de la máquina: es necesario revisar los componentes de la maquina como la alineación de los ejes y las guías. Estas relaciones se ven afectadas por la desviación térmica, por lo que siempre se produce alguna variación, incluso en los entornos más estables. También es importante mantener los niveles de aceite óptimos para el correcto funcionamiento de los componentes móviles de la máquina. Mantener la maquina limpia evitará que restos de polvo o virutas puedan interferir en los diferentes componentes de la misma. Por último, se ha de revisar los utillajes o elementos de fijación necesarios para sujetar la pieza ha mecanizar. Los errores de máquina sin corregir pueden ser un factor determinante en los errores de conformidad del proceso y pueden aumentar los tiempos de reglaje.
• Control de la pieza: es de vital importancia conocer la posición y orientación exacta de la pieza en nuestro centro de mecanizado para poder establecer un sistema de coordenadas de trabajo. De igual manera, es necesario conocer el tamaño del bruto de la pieza que se va a fabricar para determinar las tolerancias y la secuencia de desbaste. El reglaje de piezas reduce costes de utillaje, y elimina la intervención del operario y las consecuencias de un reglaje incorrecto en el mecanizado.
• Control de las herramientas: Al igual que en el caso de la máquina y de la pieza, el reglaje de las herramientas que se van a emplear en el proceso de fabricación conducirá a piezas dimensionalmente más ajustadas al diseño inicial. Para ello se debe realizar un control metrológico de la longitud y diámetro de las herramientas para establecer una compensación de altura y de radio en el control numérico así como para detectar roturas y niveles de desgaste inadmisibles para la operación requerida.
La segunda fase del control metrológico se efectúa durante el proceso de mecanizado, ‘In process metrology’. La metrología durante el proceso de mecanizado está tomando cada vez más peso en el control productivo y de calidad, ya que permite tener un control en tiempo real de las condiciones del proceso.
Al tratarse de acciones integradas en el propio proceso de arranque de viruta, estas pueden responder automáticamente a las perturbaciones que se puedan dar en el material, en las herramientas o incluso corregir situaciones imprevistas antes de que la pieza quede fuera de tolerancias. Asegurando así unas condiciones para que el proceso finalice correctamente. Las mediciones que se toman en esta fase están relacionadas con las herramientas y con las piezas que están siendo mecanizadas.
• El control de las herramientas se efectúa para detectar el nivel de desgaste de las mismas o la posible rotura durante los ciclos de mecanizado. Los efectos térmicos pueden provocar desviaciones en las herramientas, controlando estas desviaciones se pueden realizar compensaciones automáticas en el control numérico de la máquina para evitar piezas que no cumplan las condiciones dimensionales establecidas.
• De la misma manera, el control dimensional de la pieza tras cada ciclo de mecanizado, proporciona mayor estabilidad al proceso. Mediante un sistema de visión o de contacto (sondas de palpado) se conoce las cotas reales de la pieza y se puede actualizar los sistemas de coordenadas, parámetros y la línea del programa lógico en función de las condiciones reales del componente.
Por último, la fase más conocida por la industria es la que se encarga del control dimensional de la pieza terminada. Para ello se emplean maquinas CMM o similares. Evidentemente en esta fase no se pueden evitar piezas dimensionalmente no válidas y únicamente se realiza para el control de calidad por lo que no se profundizará en este artículo.
Un esquema similar al anteriormente descrito es el que propone la empresa de metrología para la industria Renishaw, la cual subdivide el control metrológico del proceso productivo en 4 etapas divididas en una escala cronológica como se puede observar en la figura 13.
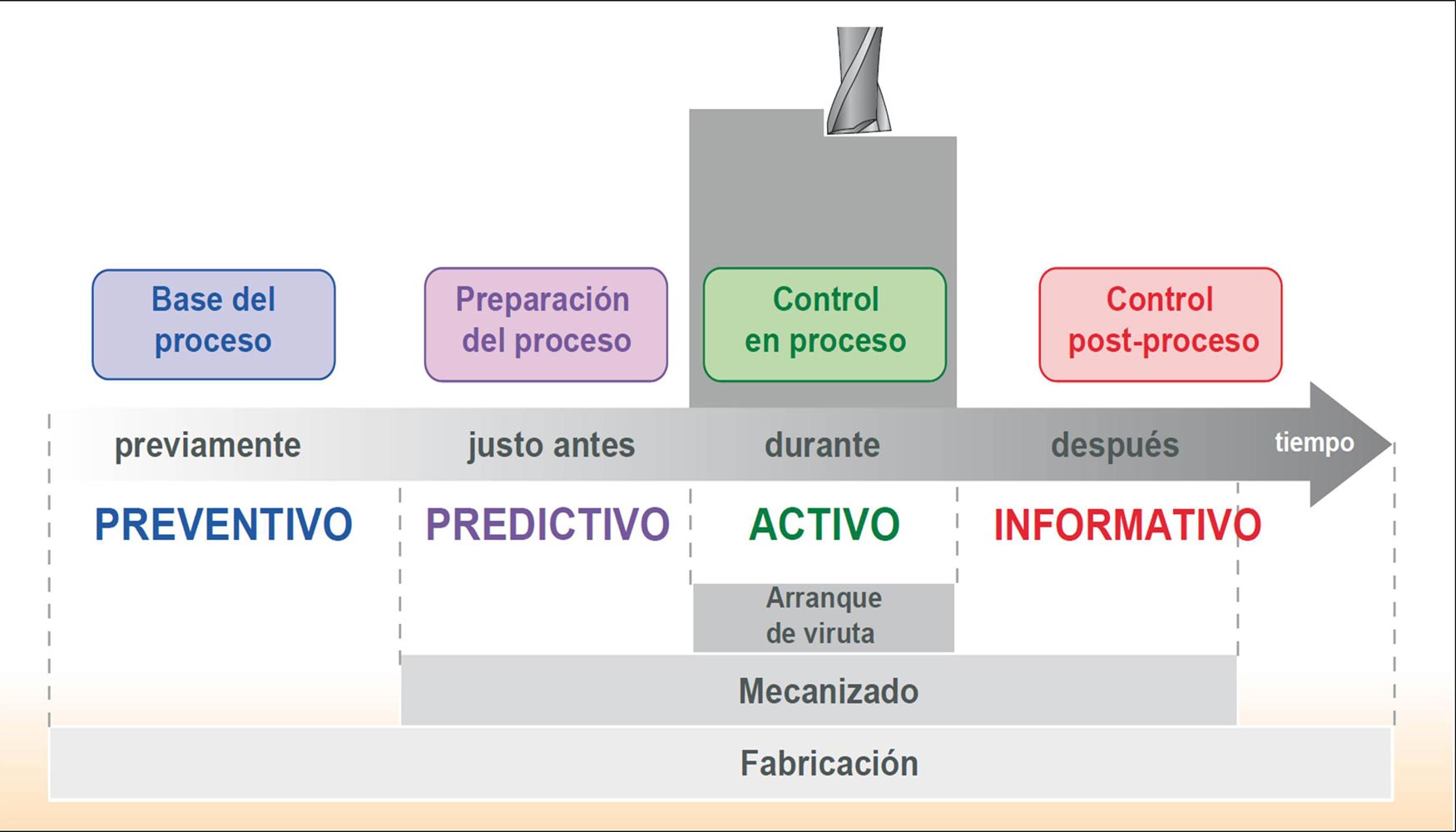
Dentro de las tecnologías disponibles para llevar a cabo una exhaustiva inspección metrológica, las más conocidas son la ya mencionada tecnología por contacto mediante el empleo de sondas de palpado y los sistemas de visión o sin contacto. Estos últimos, más novedosos, no están tan expandidos en el ya, industrialmente asentado, control por contacto.
A continuación se describen ambas tecnologías así como los equipos que pueden ser empleados en la fase del control metrológico durante el proceso de mecanización.
5.1. Control por contacto
En la inspección por contacto existe un contacto físico entre la pieza a medir y el dispositivo de medición, que típicamente se trata de una sonda mecánica u otro dispositivo que toca el componente y produce la acotación, en el espacio de coordenadas de la máquina, del punto palpado en superficie.
Cuando se produce el contacto entre el elemento palpador y la pieza, la sonda se activa y se produce la conexión con el control de la máquina mediante un receptor que capta la señal emitida por la sonda, la cual puede ser una señal de radiotransmisión u óptica (infrarrojos). Esto conexión se produce casi simultáneamente. El control, capta automáticamente la posición de la sonda a través de los encóderes de los ejes principales de la máquina.
Una vez capturado un punto, la sonda se mueve a otro punto de la superficie de la pieza. Cuando se conocen varios puntos se pueden establecer diferentes formas y características de la pieza. El mínimo número de puntos necesarios para conocer el tipo de forma se basa en los grados de libertad de la propia forma que se desea analizar.
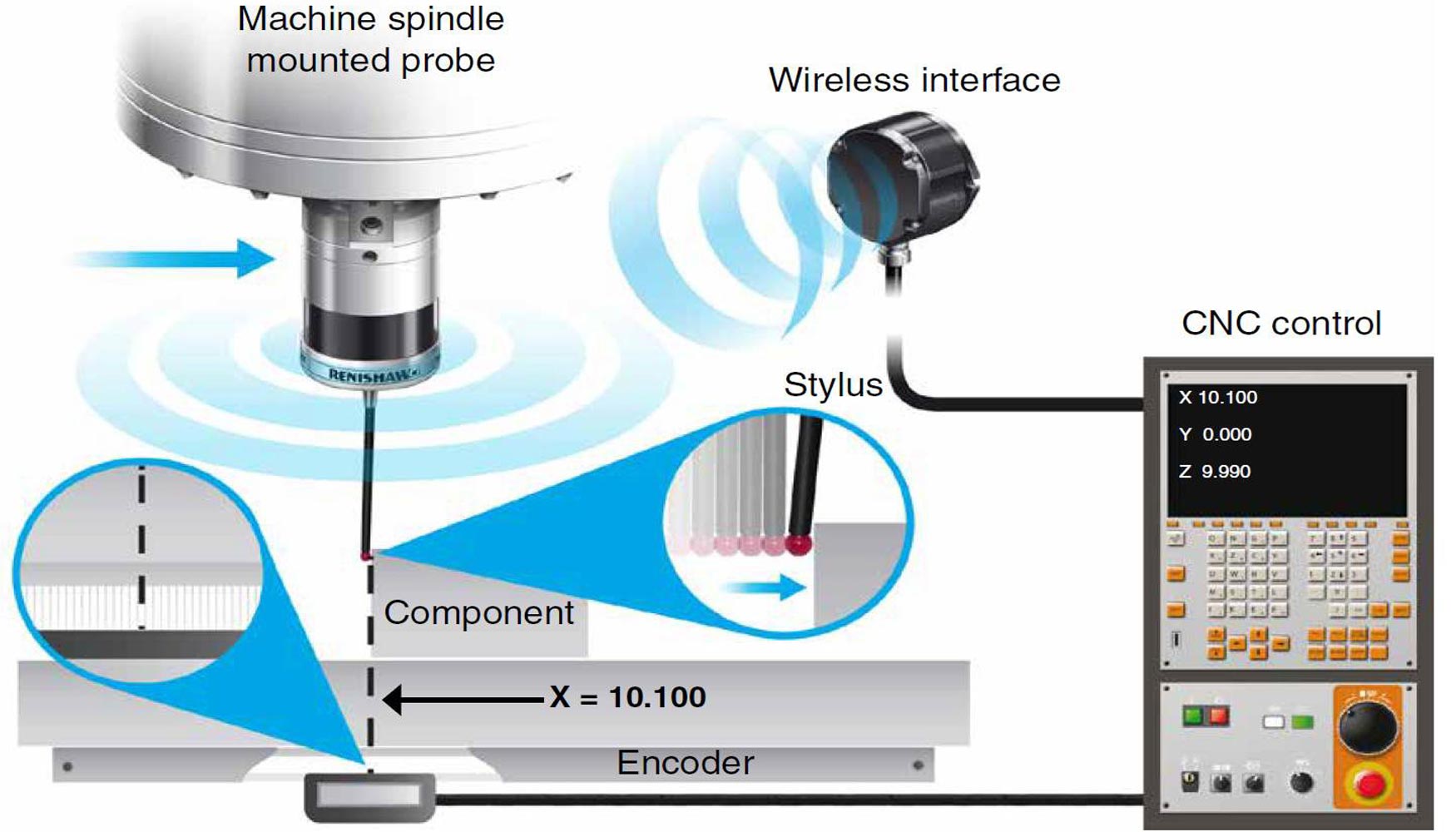
La comparación entre la dimensión real tomada y la dimensión que se debía esperar, da la desviación producida durante el mecanizado y permite la corrección automática en el control de la máquina. La retroalimentación resultante es la base de un control preventivo, predictivo, activo e informativo, el cual es esencial para un control eficaz del proceso de fabricación.
Existen diferentes tipos de sondas en función del centro de mecanizado donde se van a emplear. De esta manera, se pueden catalogar sondas para centros de mecanizado verticales, horizontales o las destinadas para su uso en centros de torneado. Incluso sondas de palpado multieje y cabezales para la inspección de rugosidad de superficie directamente en la MMC como el comercializado por Sariki Metrología que se muestra en la figura 15.
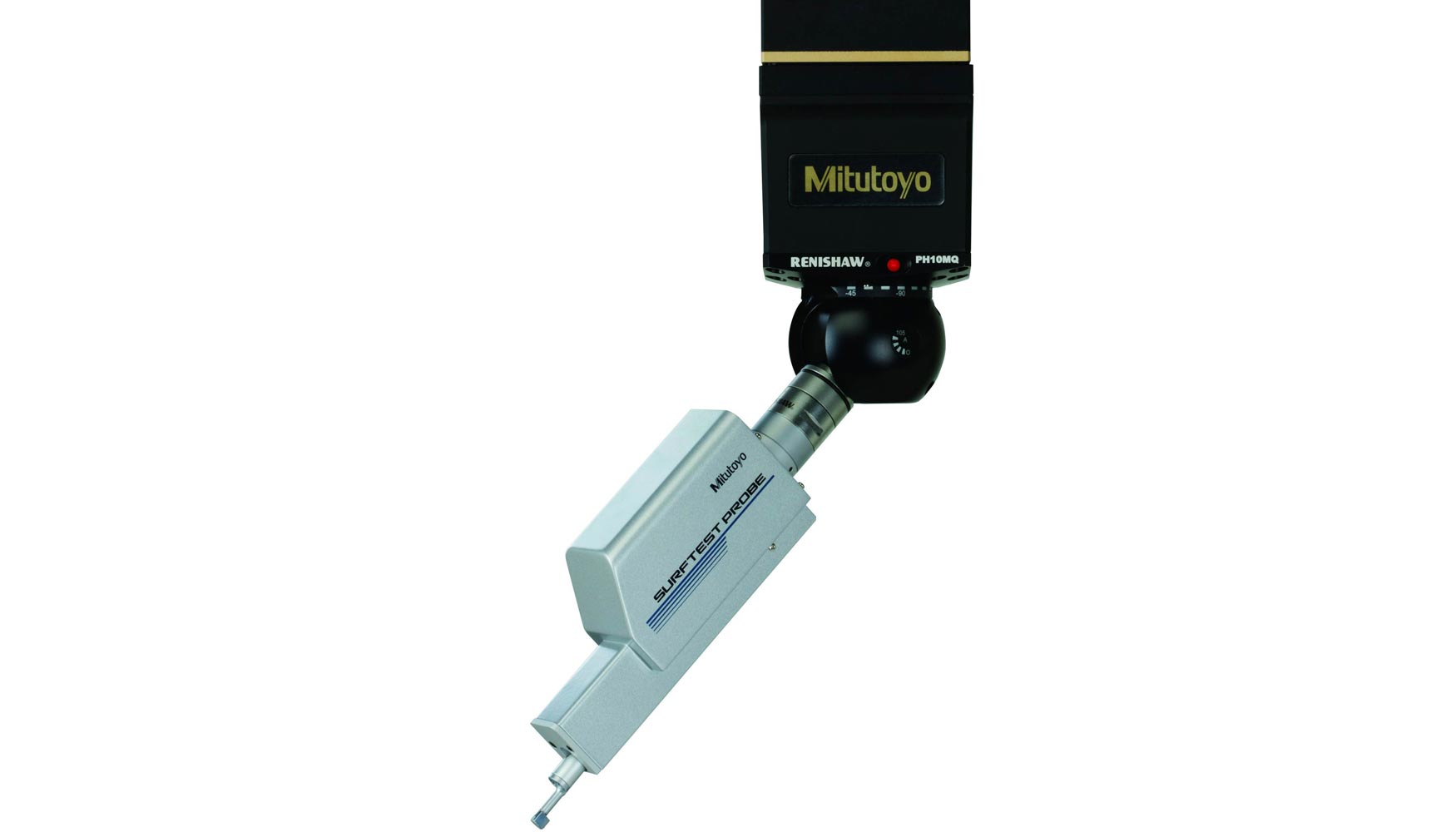
Para el reglaje y detección de roturas en las herramientas también existen diferentes dispositivos (figura 16), que mediante contacto, determinan la posición exacta de la herramienta y pueden corregir las desviaciones de las mismas en el control de la máquina, compensando los valores de altura y diámetro de la herramienta.
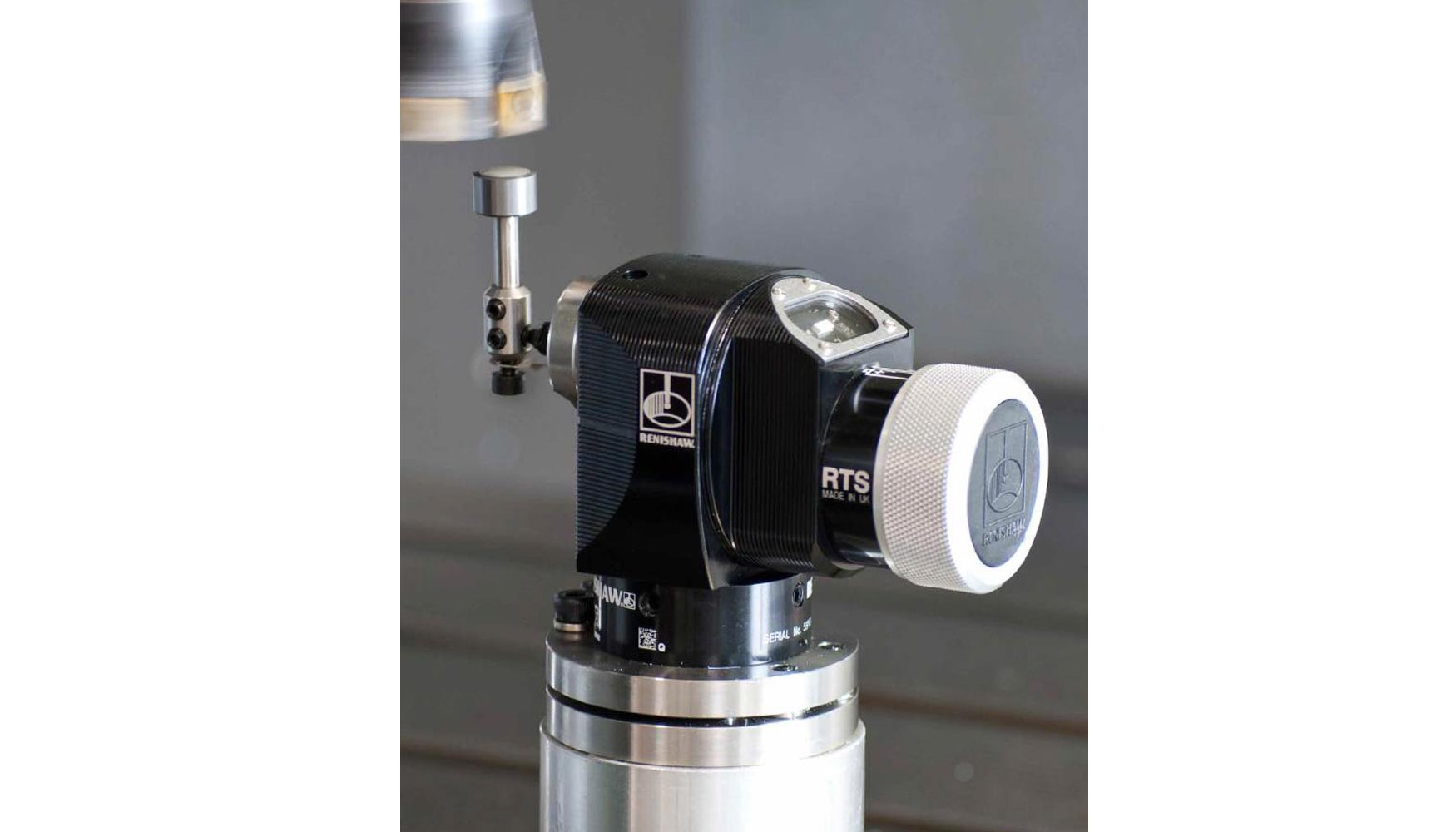
5.2. Control por visión o sin contacto
Los sistemas sin contacto y de visión para el control metrológico durante el proceso de fabricación están menos extendidos que las ya descritas sondas de contacto. Aun así, son métodos mucho más rápidos que los anteriores y poco a poco se van abriendo camino en el sector industrial.
Estas técnicas emplean sensores en vez de sondas mecánicas para tomar datos dimensionales de las piezas y herramientas. Los sensores se colocan a una cierta distancia del objeto a medir, normalmente dentro de la maquina donde se mecaniza la pieza, pero también se pueden colocar en robots antropomórficos para obtener un proceso de medición completamente automatizado.
Los sistemas de escáner de luz blanca son soluciones integrales de medición óptica 3D, enfocados hacia la mejora de los procesos de ingeniería y fabricación en la industria de la automoción y otras industrias manufactureras. La compañía Hexagon Metrology ofrece este tipo de sistemas, se trata de una solución flexible para la metrología de taller en tiempo real. Dicho sistema adquiere abundante información dimensional a partir de los objetos medidos independientemente de su tamaño, su complejidad o sus características geométricas.
Por otro lado, la empresa Gom también ofrece un sistema de medición óptica 3D. El equipo ATOS de dicha compañía combina el escaneado 3D y la fotogrametría para medir diferentes tamaños de objetos, acabados superficiales y geometrías independientemente de las condiciones de iluminación ambientales. Apoyado en un completo software, este sistema ofrece gran versatilidad a la digitalización 3D, ya que obtiene coordenadas precisas de la superficie de la pieza escaneada y sus desviaciones respecto al CAD.
Este tipo de escáneres ópticos también pueden ser implementados directamente en máquina MMC, como por ejemplo la gama de escáneres láser 3D para máquinas de medición3D comercializados por Sariki, que permiten disponer de precisiones comparables al de probetas táctiles.
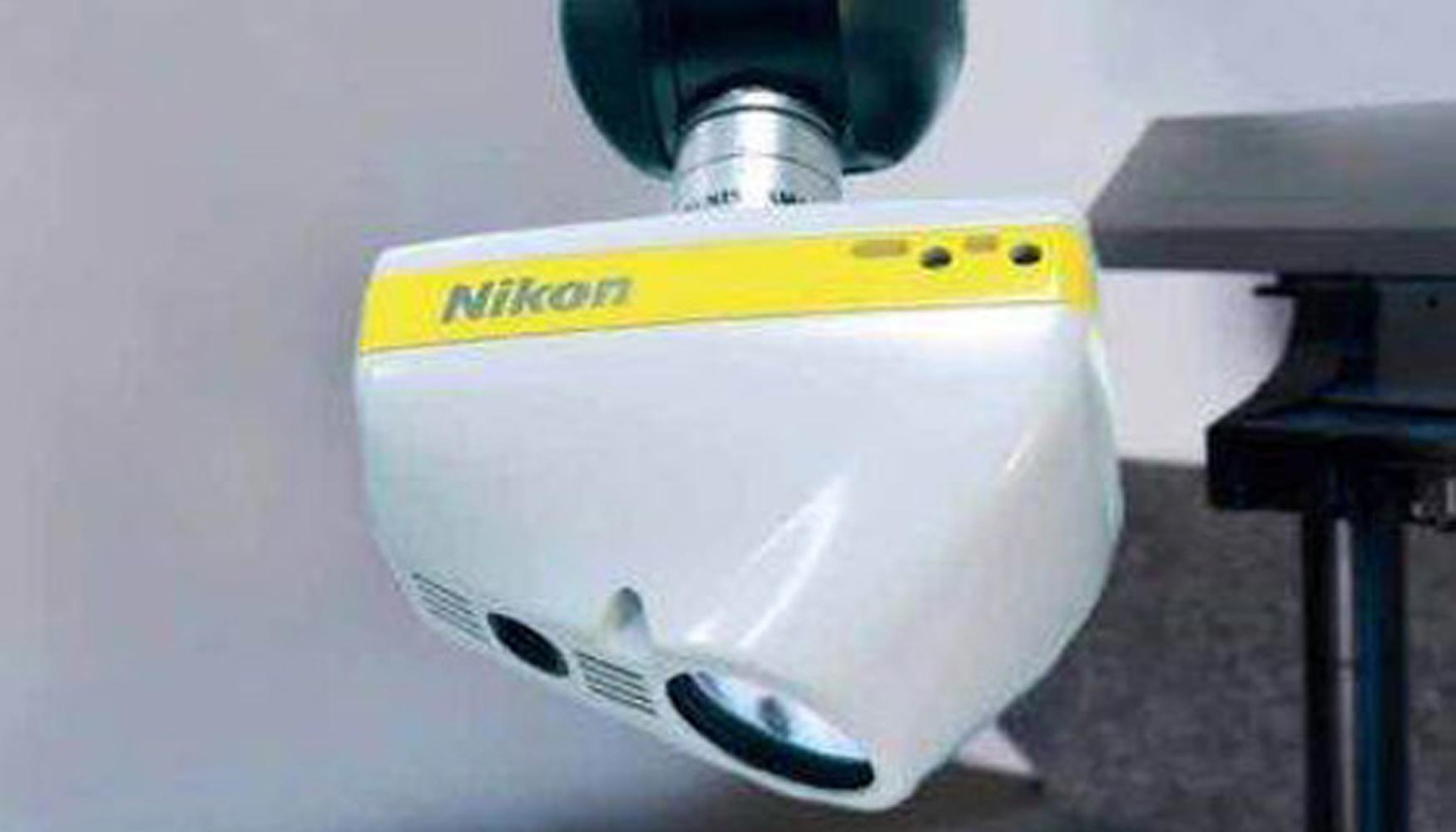
Pero no sólo las piezas pueden ser analizadas mediante estos sistemas, el control dimensional de las herramientas también se puede llevar a cabo con equipos de medición sin contacto.
Para ello existen diferentes equipos de medida en función de la herramienta que se desea analizar. Los más comunes son los sistemas láser, que permiten el reglaje de herramientas y la detección de roturas a alta velocidad, incluso si se emplea refrigerante. Estos sistemas pueden reducir tiempos de ajuste hasta en un 90%, además de disminuir las piezas desechadas y los fallos.
El empleo de estos sistemas tiene ciertas ventajas, como la adquisición a alta velocidad de medidas sin la necesidad de dañar la pieza por un contacto no deseado, la posibilidad de medir piezas o componentes que están calientes así como piezas susceptibles a deformaciones por contacto. Todo esto, además, se puede automatizar logrando un proceso repetitivo y notablemente más rápido que los sistemas por contacto.
El proyecto Muprod y el clúster europeo 4ZDM
El Grupo de Fabricación de Alto Rendimiento del Dpto. de Ingeniería Mecánica de la ETSI de Bilbao (UPV/EHU) ha participado en el Proyecto Europeo del FP7 de acrónimo Muprod y título ‘Innovative Proactive Quality Control System for In-Process Multi-Stage Defect Reduction’. El proyecto ha sido coordinado por el Centro Tecnológico Tecnalia, y en él han participado varias empresas y universidades europeas de prestigio. Este proyecto, financiado por la Unión Europea bajo el 7º programa marco, tiene como objetivo desarrollar un sistema de control de calidad innovador como alternativa al concepto actual de control de calidad a fin de línea. Se evita de esta forma la generación de defectos en cada etapa del proceso y la propagación de los defectos entre los procesos a nivel de sistema multietapa. Los avances desarrollados en este proyecto cubren un amplio abanico de aplicaciones, centrándose principalmente en sectores estratégicos emergentes en Europa, como la producción de motores eléctricos, la fabricación de grandes piezas de multiplicadoras para el sector eólico y la producción de micro-componentes médicos.
El principal rol de nuestro Grupo en este proyecto ha consistido en la generación de modelos para procesos de corte y predicción de regiones de estabilidad, enfocando los avances al mecanizado de grandes componentes de multiplicadoras para aerogeneradores. De esta forma se ha integrado en un paquete software los modelos matemáticos desarrollados por el Grupo para las operaciones de fresado, torneado y taladrado. Utilizando este software se pueden predecir de manera rápida y sencilla los valores de fuerzas, consumo de potencia y acabado superficial que se obtendrán durante las operaciones más comunes de mecanizado. Este trabajo permite realizar los cálculos para diferentes tipos de herramientas, condiciones de corte, y geometrías, cubriendo una amplia gama de posibilidades.
En la línea de trabajo de Muprod se ha creado un clúster europeo formado por 4 proyectos relacionados con el concepto de la fabricación sin defectos. Entre ellos destacan los dos liderados por centro tecnológicos del entorno: el Muprod, liderado por Tecnalia y el proyecto Midemma, liderado por IK4 Ideko. Este clúster 4ZDM (Four Zero Defects Manufacturing) enfoca su actividad al desarrollo de sistemas que permitan prevenir los defectos y evitarlos reduciendo de manera notable los costes derivados de las no conformidades al final del proceso. Estos desarrollos están orientados principalmente a los sectores de automoción, tecnología médica, energía, aeronáutica e industria. En www.4zdm.eu se puede encontrar más información sobre 4ZDM, las entidades participantes, los proyectos en curso y sus actividades.
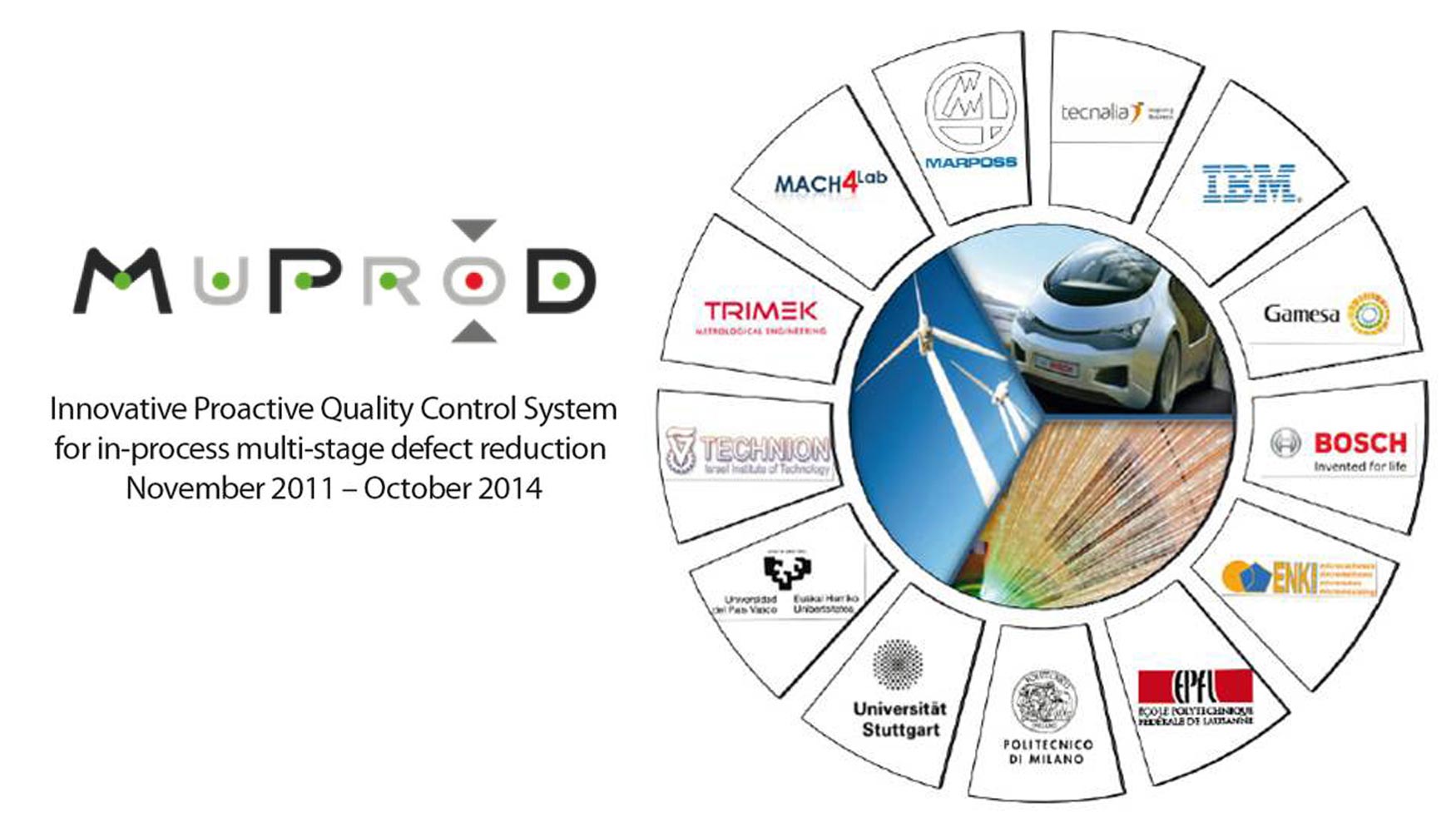