Caracterización de la calidad superficial en fresado de alta velocidad con herramienta de punta esférica y aceros para moldes y matrices
La industria de manufactura global (ejemplo, sector automotriz) requiere de piezas moldeadas y vaciadas de alta calidad que cumplan con la satisfacción del cliente, ya sea de percepción en caso de partes cosméticas o de performance en caso de piezas funcionales, desarrolladas en tiempos cada vez más cortos; esto se debe a la alta competencia y exigencia de mercados globales emergentes.
Para lograr esta calidad en dichas piezas es necesario crear superficies adecuadas con rugosidad adecuada y tolerancias cerradas, además, como se mencionó anteriormente es necesario hacerlo en tiempo reducido lo que nos obliga a maximizar la utilización de procesos de manufactura de alta productividad como es el caso del mecanizado de alta velocidad (HSM por sus siglas en ingles) mediante una buena estabilidad dinámica en el proceso de fresado de acabado del herramental
Actualmente en la industria no existen referencias suficientes que ayuden a crear planes de procesos que aseguren esa estabilidad necesaria en dicho proceso para condiciones específicas. En la generación de superficies en moldes, el fresado se utiliza hasta donde la estabilidad del proceso lo permite, de lo contrario se tiene que utilizar el proceso de EDM. El proceso de EDM es significativamente menos productivo que el HSM y ya que el proceso de mecanizado en procesos de fabricación de moldes representa de un 30% a un 50% del tiempo total, puede tener un impacto significativo. Por otro lado el proceso de EDM requiere de procesos adicionales como el pulido manual para poder cumplir con la calidad superficial adecuada, en cambio en el proceso de fresado es posible llegar a rugosidades promedio Ra alrededor de 0.1μm con HSM [1].
Existen algunas recomendaciones acerca de este fenómeno de vibraciones y su efecto sobre la productividad y calidad en el proceso de maquinado tomando con especial atención a una teoría llamada curvas de estabilidad, esas curvas muestran que aumentado las velocidad del husillos, existen zonas de estabilidad libre de vibraciones, aumentando la cantidad de material a remover y por ende la productividad. (ver figura 1).
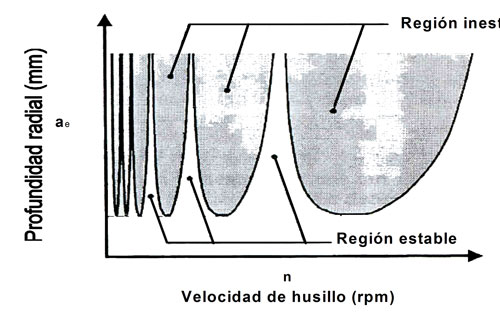
Por el lado de la manufacturabilidad existen recomendaciones que muestran que dependiendo de las condiciones de operación, es decir dureza de material y características de la herramienta, puede se utilizado el proceso de maquinado o bien en ciertas zonas ser remplazado debido a su baja eficiencia por el proceso de EDM [1] (ver figura 2).
![Fig. 2 Gráfica de recomendaciones de procesos de manufacturas para durezas y relación de esbeltez (adaptado de [1]) Fig. 2 Gráfica de recomendaciones de procesos de manufacturas para durezas y relación de esbeltez (adaptado de [1])](https://img.interempresas.net/fotos/817312.jpeg)
1. Experimentación
Para realizar la experimentación fue necesario el diseño de una probeta que nos permitiera arrojar los más datos posibles en el menor número de iteraciones. Cabe mencionar que el experimento consiste en una emulación del proceso de fresado de superficies [2].
Para el diseño de la probeta experimental se utilizó el paquete computacional CAD Mechanical Desktop, y con la ayuda de un CAM, WorkNC, se realizaron los programas CNC que fueron alimentados posteriormente al centro de maquinado HURON KX-10, apropiado para HSM.
La probeta, donde fueron realizadas las pruebas, consta de cinco pestañas, cada pestaña tiene un plano maquinable a 45° grados, esta condición nos permite obtener el mejor resultado de acabado superficial ideal posible.
Para definir la serie de experimentos a realizar primero fijamos algunos parámetros con el objetivo de simplificar el estudió y definimos los diferentes niveles de las variables que consideramos importantes probar, esto como resultado de los experimentos preliminares que nos dieron la pauta a seguir para delimitar dichos niveles. Por último definimos variables a evaluar como resultado de los diferentes niveles de experimentación.
Condiciones fijas:
Aleación del acero: AISI S1.
Desgaste de la herramienta: carburo de tungsteno aglomerado con matriz de cobalto con recubrimiento cerámico de TiAlN (MDM-201-06 Robb Jack) nueva para cada experimento, además de randomizar el orden las diferentes pruebas para disminuir el factor de desgaste en el acabado superficial.
Tipo de sujeción: boquilla.
Geometría de la superficie: plano a 45° grados para idealizar el acabado superficial [3].
Diámetro de la herramienta: 6 mm de dos filos.
Avance por diente: 0,044 mm/rev, cambiar este parámetro pudiera resultar en una fractura de la herramienta.
Profundidad de corte normal: ap igual a 0,6 mm en el plano maquinable de 45° grados, an de 0,42 mm.
Ángulos de corte de la herramienta: Bf de 90° grados y Bfn de 45° grados.
Condiciones variables:
Relación de esbeltez, L/D: 6,0 y 8,6.
Dureza del material: 30 HRC, mismo material de 40 HRC. (El tratamiento térmico para llegar a dicha dureza fue el siguiente, se elevó a la temperatura de austenitización 950°C para después templarlo en aceite y terminar con un revenido a aproximadamente 650 °C).
Profundidad radial, ae (mm): 0,1, 0,15, 0,2, 0,25
Velocidad de husillo (rpm) y velocidad de corte (m/min)
n (VC) = 9.000 (170), 10.000 (188), 11.000 (207), 12.000 (226), 13.000 (245), 14.000 (264), 15.000 (283).
*VC máxima recomendada 226 m/min (12.000)
Parámetros a evaluar:
- Rz-f y Rz-fn
- Zonas de trabajo de más productividad
- Calidad cualitativa del acabado
2. Resultados
2.1. Influencia de flexibilidad (L/D), paso radial (ae) y velocidad de husillo (n)
2.1.1. Limites de estabilidad generales. Proceso estable (L/D=6.0) vs. zona de transición (L/D=8,6)
La información que existe en la literatura (ver figura 2) limita el proceso de manufactura de remoción de material ya sea HSM o LSM a la utilización de EDM en superficies que requieran trabajar con relaciones de L/D menores a 3 para materiales con dureza de 30 HRC típicamente materiales utilizados en la fabricación de herramentales, esto para poder garantizar un proceso estable con un acabo superficial adecuado entre 0,5 μm y 1,8 μm [4].
Los experimentos realizados muestran que a esos niveles de dureza es posible obtener acabados superficiales excelentes libres de vibración en zonas donde se requiera utilizar relaciones L/D igual a 6,0.
Al aumentar el valor de L/D a 8,6 que equivale a un aumento en carga a la herramienta donde la recomendación de la literatura es también la utilización del proceso de EDM, todavía podemos encontrar zonas estables de maquinado con algunos parámetros de operación, sin embargo con ciertas condiciones de corte los resultaron no fueron favorables mostrando notablemente distorsión, por lo que supone un zona de transición al proceso de EDM (ver figura 3).
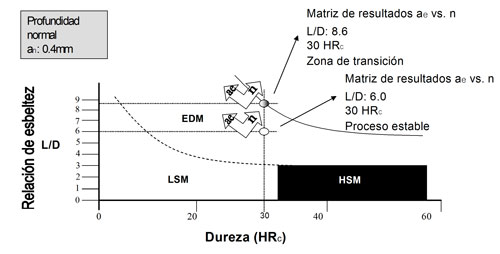
Los resultados de la experimentación nos permite deducir un rango más amplio en la zona de HSM es decir un movimiento positivo de la curva de transición que se traduce en mayor de aprovechamiento de la utilización del proceso de maquinado que la recomendada.
2.1.2. Limites de estabilidad específicos. Evaluación cualitativa y cuantitativa (rugosidad) del proceso estable (L/D=6,0)
Se realizaron experimentos con diferentes valores de n desde 9.000 rpm (Vc 170 m/min) hasta 15.000 rpm (Vc 283 m/min) y variando el ae desde 0,1 mm hasta llegar a 0,25 mm como valor máximo, con una herramienta de una relación L/D igual a 6,0 con el objetivo de evaluar la condición superficial. Mediante una evaluación cualitativa realizada visualmente se verificó la condición de todas las pruebas realizadas, no se detectaron presencia de marcas relacionadas con el fenómeno de vibración de la herramienta en ninguna de ellas.
Para poder tener un detalle más preciso, cuantificable, de la estabilidad del proceso de mecanizado en este experimento se realizaron medidas Rz-f de todas las superficies tomando como resultado el promedio de 5 muestras de 0,8 mm
Los resultados muestran lecturas alrededor de 1 μm lo que nos da un acabado superficial ideal en una operación de acabado en un herramental [4].
Si se quiere maximizar la productividad pudiéramos utilizar una combinación de parámetros de corte de 15.000 rpm (Vc 283 m/min) con un ae de 0,25 mm pudiendo obtener un acabado superficial del orden de 1,2 μm en dirección al avance (ver figura 4).
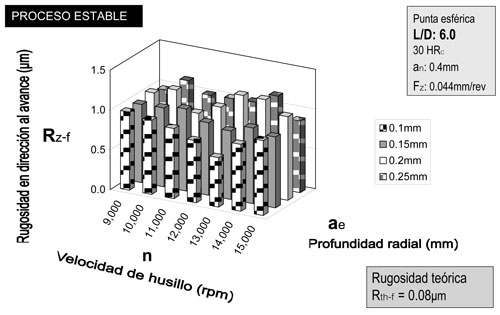
2.1.3. Evaluación cualitativa y cuantitativa (rugosidad) de la zona de transición (L/D=8,6)
Para probar la influencia de la flexibilidad de la herramienta en la estabilidad del proceso se realizaron los mismos experimentos variando los valores de la velocidad del husillo y paso radial pero con un valor de L/D de 8,6. Igualmente se efectuó una evaluación cualitativa realizada visualmente donde arrojó como resultado superficies donde se puede apreciar un acabado superficial adecuado hasta superficies donde el acabado muestra presencia completamente del fenómeno de vibraciones. Este resultado comprueba que existe una fuerte relación de presencia de vibraciones en el sistema con valores mayores de L/D, por otro lado también comprueba que podemos obtener zonas estables con cierta combinación de condiciones de corte.
Para poder evaluar la magnitud en la influencia de la flexibilidad de la herramienta en el acabado superficial se cuantificó el acabado mediante la medición de la Rz-f, los resultados oscilan entre 1 μm hasta 11 μm para algunas condiciones.
Se observa claramente que para un ae específico como de 0.1 mm se puede mejorar la calidad de la superficie elevando la velocidad del husillo de valores en el orden de 3.5 μm con 9.000 rpm (Vc 170 m/min) a valores de 1 μm incrementando a 13.000 rpm (Vc 245 m/min). Por otro lado se puede observar un compartimiento similar en la velocidades 15.000 rpm (Vc 283 m/min) donde a un ae de 0,1 mm obtenemos superficies de 3 μm y disminuye dramáticamente a la mitad 1,5 μm al aumentar el ae 0,25 mm, lo cual nos permita retirar mayor cantidad de material en menor tiempo sin sacrificar la calidad del acabado en dirección al avance (ver figura 5).
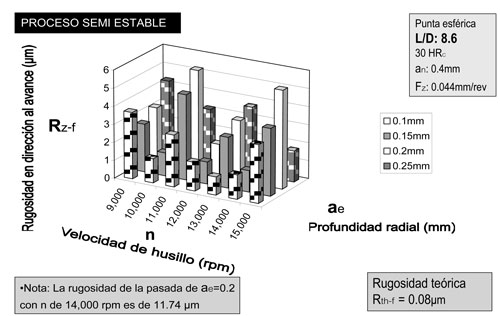
2.2. Influencia de dureza, profundidad normal (an) y velocidad de husillo (n)
2.2.1. Limites de estabilidad generales. Zona estable a 30 HRC vs. 40 HRC con L/D=6,0
Después de encontrar una nueva zona de estabilidad en donde es posible maquinar con relaciones de L/D igual a 6,0 obteniendo un acabado superficial adecuado con un material de 30 HRC, se realizaron experimentos para conocer la influencia de la dureza, incrementándola a 40 HRC, en la estabilidad del proceso, dicho experimento se realizó disminuyendo la ap a 0,18 mm, dando como resultado una an igual a 0,13 mm ya que al aumentar la dureza aumente la fuerza de corte. El objetivo fue caracterizar el proceso y encontrar la curva limite donde nos permita seguir utilizando el proceso de maquinado con acabados superficiales adecuados en relación con la dureza del material contra un proceso de EDM (ver figura 6).
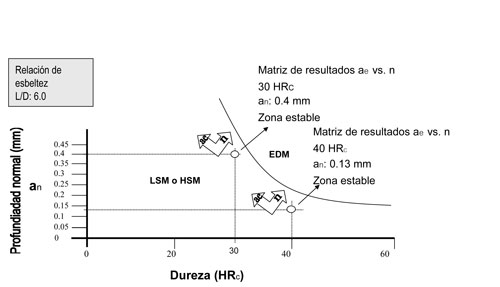
La evaluación cualitativa muestra que en la mayoría de las condiciones de corte presentan acabados adecuados resultado de un proceso estable, solamente a 10.000 rpm (Vc 188 m/min) se alcanza a apreciar una ligera presencia del fenómeno de vibraciones en todos los valores de ae. Al realizar la medición de la Rz-f y hacer una evaluación cuantitativa podemos observar que al aumentar la n es posible mejorar considerablemente la calidad de la superficie de valores como 1,4 μm a 10.000 rpm (Vc 188 m/min) a 0,6 μm al aumentar 15.000 rpm (Vc 283 m/min) con un ae de 0,15 mm (ver figura 7).
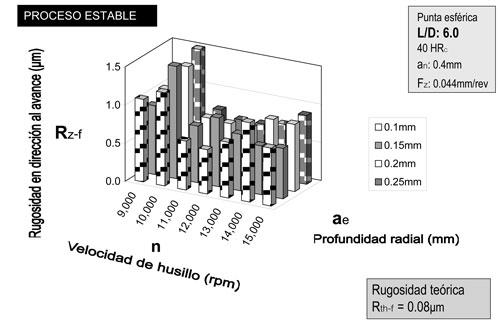
3. Discusión de resultados
3.1. Calidad vs. productividad
Los resultados de los experimentos realizados muestran que es posible maquinar un acero herramienta de 30 HRC con un L/D igual a 6,0 en una condición de proceso estable libre de vibraciones, y alcanzar un acabado superficial con una rugosidad en el orden de 1μm en la dirección del avance.
El cambio en la calidad superficial utilizando un ae de 0,1 a 0,25 mm es muy poco significativo, es decir podría maquinarse con un ae de 0,25 mm si sacrificar calidad superficial, aumentando 2,5 veces más la productividad del proceso.
Un aumento en la productividad del proceso de fresado de acabado, es decir remover mas área en menos tiempo, representa una disminución directa de su costo.
3.2. Zonas de estabilidad para fresado vs. EDM
Según el análisis cuantitativo de la superficie maquinada con acero herramienta a 30 HRc, dureza en materiales como el AISI P20 preendurecido comúnmente utilizada en la fabricación de moldes y matrices, con un L/D de 6,0 arroja que la vibración se presenta más agresivamente en la dirección normal a la dirección de corte donde la mínima encontrada de de 1,5 μm con un ae de 0,1 mm.
Dada esta condición el aumento en la productividad del proceso se refleja en el aumento de la velocidad del husillo para un mismo ae, es decir aumentar la n de 9.000 rpm (Vc 170 m/min) a 15.000 rpm (Vc 283 m/min) por consecuencia un aumento en la velocidad de corte y por ende remoción del mismo material en menor tiempo.
Otra recomendación consiste en que es posible maquinar acero herramienta a 30 HRC con un L/D de 8,6 y obtener un acabado superficial optimo con sólo variar los parámetros de la maquinaria.
Poder fresar superficies esculpidas, con buen acabado superficial, en zonas donde es necesario utilizar herramientas con L/D de 8,6, nos da la ventaja de disminuir drásticamente el tiempo de fabricación de moldes y matrices si lo comparamos con el proceso alternativo de EDM recomendado para dichas relaciones de L/D (ver figura 3).
Sustituir el proceso de fresado por el proceso de EDM aumenta la productividad en la realización del acabado en las superficies esculpidas, disminuyendo su costo.
3.3. Zonas de estabilidad para durezas de 40 HRC
En el caso del proceso de maquinado en un aumento en la dureza del acero herramienta a 40HRC es posible obtener zonas de estabilidad y acabado superficial en condiciones optimas en el orden de 1μm al disminuir el factor de carga en este caso la an.
Aunque normalmente en la mayoría de los casos lo moldes y matrices son fabricados con acero grado herramienta con durezas alrededor de los 30HRc, en ocasiones por la condición de la pieza a fabricar es necesario utilizar materiales con mayor dureza como el AISI H13 donde el uso del proceso de EDM es inminente, el uso del proceso de maquinado con las condiciones de parámetros especificados como proceso alterno disminuye drásticamente el tiempo de fabricación de moldes y matrices y por ende su costo.
Contribuciones
En la fabricación de herramentales para piezas moldeadas y vaciadas él acabado superficial es muy importante.
Encontrar zonas de estabilidad libre de vibraciones a revoluciones mayores, repercute directamente en un aumento en la productividad del proceso de fresado de acabado de superficies esculpidas.
Los resudados obtenidos traen grandes beneficios a la industria de moldes.
- La Rz-f y Rz-fn medida muestran planes de proceso para lograr acabados superficiales adecuados.
- Los experimentos realizados nos muestran que existen zonas donde es posible obtener acabados superficiales a mayores velocidades de husillo, aumentando la productividad (cm²/min) más del doble, con respecto a la literatura y trabajos previos en operaciones de fresado de acabado para superficies esculpidas.
- Otro resultado obtenido muestra que, a diferencia de la gráfica de recomendaciones de procesos de manufactura en relación de condiciones de la dureza del material y la relación de esbeltez encontrada en la literatura (ver figura 2), con ciertos parámetros de maquinado es posible tener un proceso estable con L/D grandes, del orden de 8, dando como resultado acabados superficiales adecuados, que se refleja en un aumento de productividad considerable comparándolo con el proceso alternativo recomendado de EDM (ver figura 8).
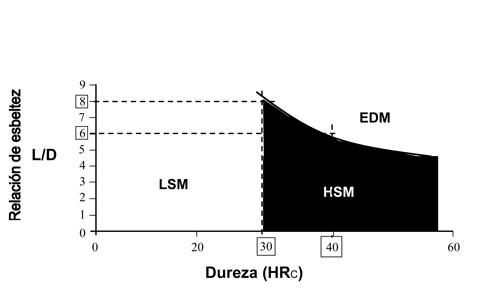
Conclusiones
Los resultados mostrados podrían aplicarse solo en superficies planas en donde la carga es uniforme y no varia respecto a la trayectoria de corte o en superficies convexas, donde la carga no es constante pero disminuye
En las superficies cóncavas donde el radio de corte es igual al radio de la herramienta, los resultados se verían alterados debido al incremento de carga resultado del incremento en el tamaño de la viruta.
[1] M.R. Alam; K.S. Lee; M. Raham; K.S. Sankaran: ‘Decision algorithm for selection of high-speed machining, EDM or a combination for the manufacture of injection moulds’, International Journal of Production Research, 2002, 40, 4, 845-872.
[2] L. H. González, H. R. Siller, C. A. Rodríguez, N. J. Hendrichs: ‘Caracterización de la calidad superficial en el fresado de acabado con herramienta de punta esférica de aceros para molde y matrices’. Tesis de L. H. González, Instituto Tecnológico y de Estudios Superiores de Monterrey, Monterrey, N.L. Mayo 2012, 91.
[3] A.L. Mantle; D.K. Aspinwall: ‘Surface integrity of a high speed milled gamma titanium aluminide’, Journal of Materials Processing Technology, 2001, 118, 1, 143-150.
[4] R. Baptista; J.F. Antune Simões: ‘Three and five axes milling of sculptured surfaces’, Journal of Materials Processing Technology, 2000, 103, 398-403.
[5] F. Abrari; M.A. Elbestawi; A.D. Spence: ‘On the dynamics of ball end milling: modeling of cutting forces and stability analysis’, International Journal of Machine Tools and Manufacture, 1998, 38, 3, 215-237.
[6] Tae-Soon Lim; Chea-Moon Lee; Seok-Won Kim;Deug-Woo Lee: ‘Evaluation of cutter orientations in 5 axis high speed milling of turbine blade’, Journal of Materials Processing Technology, 2002, 130-131, 401-406.
[7] S. Engin; Y. Altintas: ‘Mechanics and dynamics of general milling cutters. - Part I: helical end mills’, International Journal of Machine Tools and Manufacture, 2001, 41, 2195-2212.
[8] Balkrishna Rao, Yung C. Shin: ‘Analysis on high-speed face-milling of 7075-T6 aluminum using carbide and diamond cutters’, International Journal of Machine Tools and Manufacture, 2001,41, 1763-1781.
[9] Y. Altintas: ‘Modeling approaches and software for predicting the performance of milling operations’ at MAL-UBC, University of British Columbia (UBC) Manufacturing Automation Laboratory (MAL) 2000.
[10] E.O. Ezugwu; J. Bonney; Y. Yamane: ‘An overview of the machinability of aeroengine alloys’, Journal of Materials Processing Technology, 2003,134, 233-253.
[11] F.J. Campa, L.N. López de Lacalle; A. Lamikiz; J.A. Sánchez: ‘Selection of cutting conditions for a stable milling of flexible parts with bull-nose end mills’, Journal of Materials Processing Technology, 2007, 191, 279-282.
[12] González, L.H., Siller, H.R., Rodriguez, C.A., Hendrichs, N.J. ‘Caracterización de la calidad superficial en fresado de alta velocidad con herramienta de punta esférica y aceros para moldes y matrices’. Congreso Internacional de la Sociedad Mexicana de Ingeniería Mecánica, Salamanca, México (2012).
- Vf velocidad de avance (m/min)
- Vc velocidad de corte (mm/min)
- n velocidad de husillo (rpm)
- ae profundidad radial (mm)
- an profundidad normal (mm)
- ap profundidad axial (mm)
- fz avance por diente (mm/rev)
- L/D relación de esbeltez
- Rz-f rugosidad superficial real en dirección
- al avance (μm)
- Rz-fn rugosidad superficial real en dirección
- normal al avance (μm)
- Rth-f rugosidad superficial teórica en
- dirección al avance (μm)
- Rth-fn rugosidad superficial teórica en
- dirección normal al avance (μm)
- EDM proceso de electro-erosión
- LSM proceso de maquinado convencional
- HSM proceso de maquinado de alta velocidad