Trumpf avanza hacia la responsabilidad medioambiental con un sistema de corte que ahorra toneladas de CO2
La empresa de alta tecnología Trumpf presentó en su feria interna Intech 2023 el nuevo sistema TruLaser 8000 Coil Edition de corte láser 3D. Este novedoso sistema puede procesar hasta 25 toneladas de chapa metálica enrollada de principio a fin sin intervención del operario. Es una opción atractiva para cualquier empresa interesada en soluciones flexibles y de alto volumen para la fabricación de chapa metálica, incluidos proveedores y fabricantes de automóviles, fabricantes de armarios eléctricos, productores de ascensores y fabricantes de HVAC.
“La TruLaser 8000 Coil Edition es otro ejemplo de cómo Trumpf ayuda a sus clientes a unirse al impulso hacia una mayor sostenibilidad en la industria manufacturera y, al mismo tiempo, aumentar la eficiencia. En comparación con las máquinas de corte por láser convencionales, la solución permite a las empresas ahorrar casi 1.700 toneladas de acero al año, lo que equivale a un ahorro de unas 4.000 toneladas de CO2 y una reducción en los costes de material de 1,6 millones de euros”, afirma Richard Bannmüller, CEO de Trumpf Laser Technology Germany.
Gran flexibilidad que se aplica a la producción en volumen
[texto gracias al nuevo sistema de corte láser de trumpf, las empresas podrán disfrutar de las ventajas del procesamiento láser incluso en entornos de producción de gran volumen. “los fabricantes de gran volumen emplean a menudo prensas para procesos de blanking. esto significa que necesitan ajustar o incluso reemplazar la herramienta cada vez que realizan la más mínima modificación en sus componentes, lo cual cuesta tiempo y dinero. muchos sectores industriales están viendo reducciones significativas en la escala de las series de producción individuales, lo que hace que estas modificaciones sean aún más costosas y que consuman mucho tiempo. el láser permite a los usuarios llevar a cabo estas modificaciones sin necesidad de una nueva herramienta, por lo que es mucho más fácil, más rápido, más barato y más flexible”, explica el director del proyecto oliver müllerschön, responsable del nuevo sistema en trumpf. la compañía de alta tecnología desarrolló el nuevo sistema en cooperación con siemens y la empresa de ingeniería mecánica arku. junto con trumpf, siemens es responsable del sistema de control y arku del sistema de bobinas. “la implementación de una línea de láser-blanking es un nuevo enfoque para nosotros. ofrece enormes beneficios a nuestro proceso de producción, en parte debido a su alta flexibilidad y calidad, pero también gracias al hecho de que apenas necesitamos herramientas en comparación con las prensas de corte convencionales “, dice hans-peter fischer, ceo y propietario del grupo fischer. la empresa es una de las primeras en adoptar el sistema de corte láser de trumpf, que la utiliza para producir componentes estructurales de aluminio de alta resistencia para la fabricación de carrocerías de vehículos.
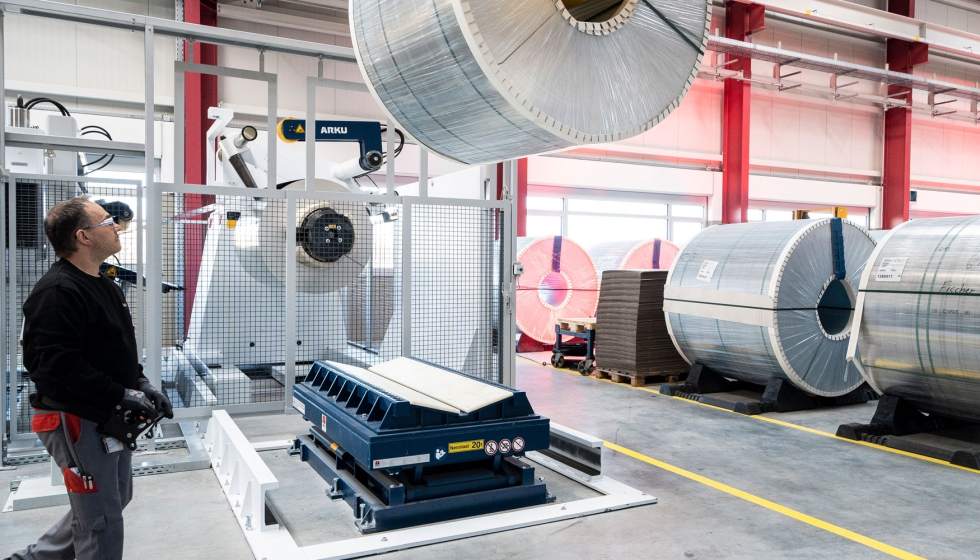
Ahorro de material para una producción sostenible
La producción de bobinas permite a los usuarios lograr un anidamiento más eficiente de las piezas. Las láminas convencionales están limitadas por sus cuatro bordes exteriores, lo que a menudo dificulta que los trabajadores de producción hagan un uso completo de toda la hoja. Las secciones no utilizadas de la hoja deben desecharse como chatarra o fundirse. Una bobina, que puede tener hasta 1,5 kilómetros de largo, resuelve este problema al permitir a los usuarios anidar un número casi infinito de piezas en la hoja. Esto reduce el consumo de material en un 15%, aproximadamente. En comparación con las prensas de corte convencionales, el nuevo sistema también propicia una reducción significativa en los costes de construcción y logística. Hace que la producción sea más rentable al eliminar los costes de las herramientas, optimizar el uso de material, reducir los costes de ensamblaje y aumentar la flexibilidad en el entorno de producción. El flujo de material es diferente al de las máquinas láser 2D convencionales, lo que propicia ciclos mucho más bajos y nuevas oportunidades de automatización para series de producción de alto volumen. El sistema está diseñado para el procesamiento de láminas delgadas y puede manejar espesores de chapa de hasta 6,5 milímetros.
La automatización reduce los tiempos de ciclo
El sistema de producción está totalmente automatizado. El innovador sistema para transportar la chapa durante el corte mantiene el material en rápido movimiento durante todo el proceso, con impresionantes ganancias en productividad. El nuevo sistema también utiliza muchas de las funciones probadas por las que Trumpf es reconocido. Estos incluyen Smart Collision Prevention, que evita que las piezas cortadas se inclinen y dañen el cabezal de corte por láser. Toda la línea, desde el stock de bobinas hasta los palets de piezas terminadas, se puede monitorear y controlar convenientemente desde un solo módulo de operador. Los puntos en los que se extraen y almacenan las piezas se programan automáticamente y se muestran en la pantalla, por ejemplo, y el módulo de operador portátil se puede utilizar en cualquiera de los puntos clave del sistema para tareas de configuración y mantenimiento.
El robot facilita la descarga
Se utiliza un robot para descargar todo el sistema y garantizar así una extracción rápida y fiable de las piezas. El software TruTops de Trumpf, que se fusionará con Oseon en el futuro, calcula los datos de entrada para ciclos listos para usar o programas de piezas que se ejecutan en el Sinumerik. Esto significa que los usuarios no tienen que preocuparse por los movimientos específicos del robot o por cómo se programan, ya que se puede manejar el robot sin ninguna experiencia o formación previa. Trumpf colaboró con Siemens en la unidad de control para el sistema de descarga, que consta de un transportador de soporte y un robot. Este hace uso del nuevo software de control CNC Sinumerik One, que está totalmente integrado en el TIA Portal. El TIA Portal forma el centro de un proceso de ingeniería digital de extremo a extremo. Los datos del TIA Portal se pueden alimentar a Create MyVirtual Machine para crear el gemelo digital de la automatización. Esta representación digital de la unidad de control, el comportamiento de la máquina y la cinemática permite la prueba virtual y la puesta en marcha del sistema directamente dentro del TIA Portal.
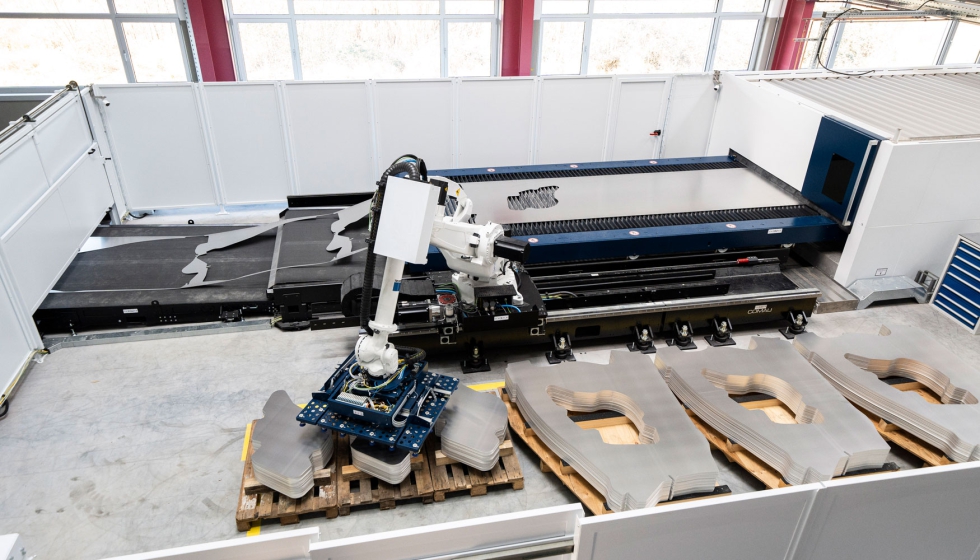
Menor tiempo de comercialización, mejor rendimiento
“Sinumerik One se encuentra en el corazón de los esfuerzos para transformar globalmente la industria de la máquina-herramienta y para una fabricación preparada para el futuro en un sector cada vez más digitalizado. Gracias a la perfecta interacción entre las carteras virtual y real, Sinumerik One permite a los fabricantes de máquinas como Trumpf reducir significativamente el tiempo de comercialización al tiempo que ofrece a los usuarios los beneficios de un rendimiento mejorado de la máquina”, dice Uwe Ruttkamp, jefe de Sistemas de Máquina-Herramienta de Siemens. El módulo de carga fue desarrollado por ARKU, especialista mundial en el mercado y la innovación de niveladores de rodillos. Puede acomodar bobinas de hasta 2.150 milímetros de ancho y acepta una variedad de materiales. El sistema ya está disponible para su compra.