Almacén de estanterías de alto rendimiento para botellas
2 de septiembre de 2010
El grupo empresarial HassiaGruppe con sede en Bad Vilbel, cerca a Frankfurt es el cuarto embotellador más grande en volumen de agua mineral en Alemania. En 2008 HassiaGruppe puso la primera piedra para un almacén de estanterías completamente automatizado de Krones para almacenar los palés con aprovechamiento óptimo del espacio disponible. El nuevo almacén de estanterías de 8.400 metros cuadrados puede almacenar un total de 38.688 palés. Hassia Mineralquellen es una de las pocas empresas alemanas productoras de aguas minerales de marca con un sistema de almacén tan sofisticado y moderno.
El grupo HassiaGruppe está compuesto por ocho subsidiarias: la empresa matriz Hassia Mineralquellen con plantas en Bad Vilbel y Rosbach y las empresas Lichtenauer Mineralquellen, Thüringer Waldquell, Glashäger Brunnen, Wilhelmsthaler Mineralbrunnen así como las empresas de zumos Rapp’s Kelterei, Höhl y Kumpf. Con sus aproximadamente 1.200 empleados, HassiaGruppe es una de las empresas manantial de mayor facturado en Alemania. HassiaGruppe ocupa con sus fuertes marcas regionales el segundo lugar del ranking nacional en volumen de ventas entre los productos de marca, incluso delante de competidores internacionales.
Creciente diversidad de productos y complejidad de embalajes
Con un volumen de ventas total de 730 millones de litros, el grupo empresarial logró en 2009 un facturado de 231 millones de euros. En un mercado marcado por el aumento de las ventas por el canal discount y por la disminución de las ganancias promedio, el volumen de ventas en 2009 de HassiaGruppe permaneció prácticamente estable en comparación con los años anteriores. Al igual que en los años anteriores y en calidad de productor convencido de productos de marca, HassiaGruppe mantuvo consecuentemente su estrategia corporativa del desarrollo permanente de sus marcas propias, las cuales cubren una amplia franja de compradores gracias a su distribución a nivel regional. Michael Schmidt, el director ejecutivo de técnica e intralogística de HassiaGruppe, explica la estrategia así: “Si los consumidores pueden escoger entre diferentes marcas de una misma empresa, entonces no tienen que escoger entre la marca propia y la marca de un competidor”.
Partiendo de esta fuerte presencia regional de marcas y de una prospección eficiente del mercado, las exigencias de la clientela se satisfacen con una amplia oferta de diferentes formas de envases y embalajes y de nuevos productos innovadores. HassiaGruppe, tradicionalmente un fabricante con envases retornables ecocompatibles, ya había reaccionado en 2007 a los cambios importantes en el mix de envases a favor de los envases no retornables con la instalación de una nueva línea de embotellado aséptico en frío para PET no retornable de gran rendimiento en su planta en Bad Vilbel. “Por principio”, enfatiza Michael Schmidt, “la higiene es una prioridad máxima en todas nuestras 19 plantas. Esto significa la renuncia casi total a un embotellado con conservantes y un embotellado en PET de nuestros productos en salas limpias y bajo las mejores condiciones higiénicas”.
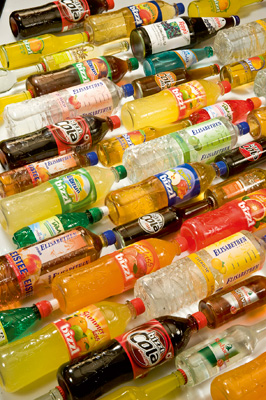
Centralización de la logística mejora la eficiencia
“Naturalmente una empresa como HassiaGruppe debe buscar permanentemente mejoras en sus operaciones para poder mantener su posición en el reñido mercado de las aguas minerales y de los refrescos. Por este motivo hemos revisado nuestros flujos de productos y de volumen de materiales entre la empresa manantial Rosbach y Bad Vilbel, distantes 20 kilómetros entre sí. Muy pronto quedó claro que podemos obtener claras ganancias en eficiencia con la creación de una logística central”, explica Schmidt sobre el proyecto de centralización. Hasta ahora todos los productos podían ser despachados tanto en Rosbach como en Bad Vilbel, lo que exigía un tráfico considerable de camiones entre Rosbach y Bad Vilbel para garantizar la disponibilidad permanente de todos los artículos en ambos emplazamientos. HassiaGruppe ofrece a sus clientes alrededor de 500 artículos diferentes, de los cuales aproximadamente 200 artículos son de las plantas en Bad Vilbel y Rosbach de la subsidiaria Hassia Mineralquellen. Con 1,8 hasta 3 millones de unidades embotelladas por día y un volumen de carga de 3.500 hasta 6.000 palés por día se despachan diariamente entre 150 hasta 300 camiones, dependiendo de la temporada.
Con las consideraciones sobre el cierre del centro logístico en Rosbach quedó claro, que la única opción viable era un almacén de estanterías automático en la sede matriz de la empresa en Bad Vilbel. “Nos encontramos en una zona residencial e industrial mixta y actualmente la producción está conectada con el centro logístico mediante un monocarril aéreo de un kilómetro, parcialmente sobreterráneo y parcialmente subterráneo”, explica el administrador delegado la situación de partida. “Debíamos construir utilizando las estructuras existentes y respetando las condiciones marco fijadas por la ciudad”.
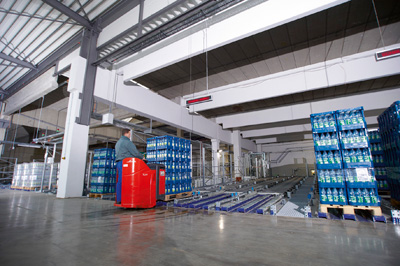
Intralogística rentable con almacén de estanterías
El resultado de esta reestructuración en la empresa manantial tradicional con más de 140 años de historia es la integración del almacén automático APW Sistema T de Krones con 39.000 puestos de ubicación, 16 transelevadores y ocho puertas de despacho para carga trasera de los camiones, adicionalmente a los siete carriles de carga lateral ya disponibles.
El almacén de estanterías de apenas 20 metros de altura cumple los límites de altura de edificación de la zona residencial vecina. Ha sido dimensionado para almacenar 250 palés por hora provenientes de la producción, 100 palés adicionales por hora provenientes de la recepción de mercancía y para recuperar 350 palés por hora para el despacho. En la sección de picking integrada son preparados adicionalmente 100 palés surtidos por hora conforme a pedidos específicos de clientes. Los palés de carga empleados son europalés y medios palés tipo Düsseldorf sobre europalés madre.
16 transelevadores
La construcción de acero ha sido ejecutada como almacén compacto automatizado de tipo almacén autoportante con un ancho de compartimiento de dos palés en dirección X, es decir a lo largo del pasillo de los transelevadores y de máximo diez palés en dirección Z, es decir en la profundidad del carril. Las estanterías miden 67 metros de largo y 111 metros de ancho. El almacén posee ocho niveles y cuatro pasillos. Los 16 transelevadores, ejecutados con carril anclado en el suelo y con un carro satélite, atienden respectivamente dos niveles.
El control de los palés que ingresan al sistema es de suma importancia para un funcionamiento sin contratiempos y libre de incidentes de la estantería automática de paletización. Por lo tanto todos los palés llenos son controlados por un control del contorno antes de ingresar al sistema automático. El volumen de suministro de Krones incluía por tanto también los dispositivos de control en la sección de entrada de mercancías así como después de la entrega de los palés producidos provenientes del monocarril aéreo.
Integración del monocarril eléctrico aéreo
El almacenamiento y la extracción de los palés de embalajes con botellas llenas al o del almacén automático de estanterías son realizados por el monocarril aéreo existente con vehículos colgantes de carga y descarga automática estacionaria al nivel del piso superior a nueve metros de altura. Antes el monocarril aéreo ya cruzó una calle de tránsito público a través de un túnel de casi 100 metros de largo. Una vez que los palés son entregados al almacén de estanterías, los diferentes niveles son alcanzados mediante ascensores. Ahí existe la posibilidad de girar los palés para su carga lateral o trasera.
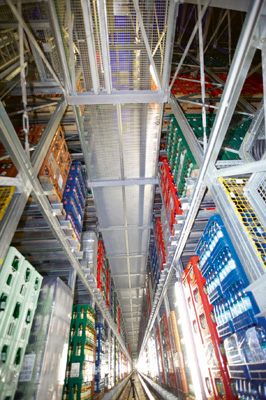
350 palés por hora en la zona de despachos
La zona de despachos posee dos secciones: una calle de carga existente para la carga lateral por el lado corto del almacén automático así como una sección de despachos nueva en el lado largo del almacén para la carga trasera de los camiones a través de ocho puertas de carga. Los segmentos de entrega son transportadores de rodillos con pendiente y con cabezales de entrega y una capacidad de carga de respectivamente 13 palés. Transpalés eléctricos cargan los palés al camión por la parte trasera. En la zona de carga trasera existen tres módulos de expedición para el despacho de mercancías y para la recepción de embalajes con botellas llenas o bien para el tráfico satélite de Hassia para el respectivo camión individual. Esto permite despachar hasta 350 palés por hora con carga lateral y trasera contemporánea, en temporadas pico se despachan hasta 400 palés por hora. Los carriles de despacho, tanto para la carga lateral como trasera, son alimentados a través de un carro satélite, el cual recibe los palés provenientes ya sea del transportador de palés o directamente de los equipos de elevación asignados. Los equipos de elevación unen el nivel de expedición ubicado al nivel del piso con el nivel a nueve metros, en el cual se mueve el monocarril aéreo.
Sobre el transportador en los módulos de carga trasera se pueden colocar tanto palés con cajas de botellas vacías como llenas. El transportador de palés transporta los palés con cajas de botellas vacías al sistema de clasificación de cajas con botellas vacías o directamente a las líneas de embotellado. La decisión la toma un sistema de detección de cajas ya existente pero integrado en el sistema de Krones. Los palés con cajas de botellas llenas provenientes de otras plantas de HassiaGruppe son almacenados en el almacén de estanterías.
En caso de carga lateral del camión, los palés de expedición son entregados al camión sobre transportadores siguiendo una secuencia de carga óptima del camión. El sistema ERP le entrega para ello al sistema un plano de carga, elaborado mediante la función “arrastrar y soltar“por el recogedor o por el empleado de la empresa de carga mismo en un terminal disponible en la zona de expedición. Los palés de expedición son cargados por carros satélite. Para Michael Schmidt esta secuenciación es uno de los factores determinantes para la alta flexibilidad de los nuevos procesos logísticos: “De esta manera hemos ganado mucha flexibilidad sobre todo en la carga lateral, y a la cual ya no podríamos renunciar. Esto permite la programación óptima de las rutas, la preparación flexible de los correspondientes pedidos y la carga rápida de los camiones”.
Picking con lista de picking
La integración del picking manual con palés de reposición automatizada provenientes del almacén automático de estanterías es llevado a cabo por técnica de transportadores a nivel del piso. El picking basado en listas de picking consta de tres vías para la puesta a disposición de un total de 240 artículos diferentes en el nivel de picking. Para la reposición automatizada de los palés vacíos necesarios durante el picking hay una reserva de palés individuales en la cabeza de cada módulo. Antes de iniciar con la preparación de los palés surtidos en el picking, el operador primero se debe identificar en una impresora de órdenes con su carnet de identificación. Aquí recibe una orden correspondiente a su posición de trabajo para acortar los trayectos necesarios para reunir todos los artículos pedidos. Un ordenador instalado especialmente para esta “asignación de órdenes de acuerdo a la posición” determina con base en la posición del empleado, cuáles son las superficies de picking más cercanas. Los palés terminados de clientes son conducidos a través de dos carriles de entrega de cada vía de picking a la unidad de aplicación de una banda con el código seriado SSCC. La asignación de órdenes de acuerdo a la posición evita recorridos vacíos innecesarios dentro de la zona del picking y permite alcanzar un rendimiento de ocho a once palés por hora por empleado de picking en promedio mensual.
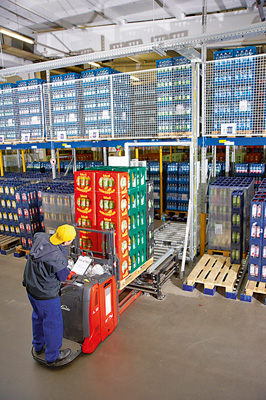
Trazabilidad de datos con un sistema informático de flujo de materiales
El mando de la instalación es un mando PLC Simatic S7 de Siemens independiente y fijo. El sistema informático de flujo de materiales controla y gestiona las órdenes de transporte generadas por el sistema de gestión de almacenes existente para la técnica de transporte, el monocarril aéreo y el almacén de estanterías. El sistema informático de flujos de materiales se encarga también de funciones de gestión del almacén tales como la administración de los puestos de ubicación en el almacén de estanterías, la gestión de los carriles de preparación de rutas y la secuenciación de los transportes para la entrega.
Principio de trazabilidad de segmentos
El sistema informático de flujo de materiales trabaja según el principio de la trazabilidad de segmentos con generación de juegos de datos a nivel del sistema de control del flujo de materiales. En este caso el palé es notificado en la fuente uno al sistema informático de flujo de materiales y al mando PLC. El palé recibe un código seriado unívoco (Serial Shipping Container Code SSCC), el cual es manejado exclusivamente en el sistema informático de flujo de materiales. El sistema informático de flujo de materiales recibe automáticamente el Código Seriado de Contenedor de Embarque (SSCC) a través de escáneres ubicados junto a los carriles de transporte. Los demás datos adicionales necesarios al SSCC (por ejemplo fecha de conservación mínima, lote, código EAN) los recibe el sistema informático de flujo de materiales del sistema ERP (Enterprise Resource Planning) de Hassia. El sistema informático de flujo de materiales garantiza una precisión del cien por ciento durante el seguimiento del código SSCC. El código SSCC es controlado por última vez poco antes de los puntos de entrega mediante un escáner de control y entregado al sistema ERP de Hassia para la contabilidad.
El seguimiento de los datos tiene lugar a nivel del sistema informático de flujo de materiales en el banco de datos del sistema informático de flujo de materiales. En cada segmento del recorrido del paé el mando PLC transmite los datos del paé al sistema informático de flujo de materiales, el cual compara la asignación y ordena la continuación del recorrido. En puntos de decisión el sistema informático de flujo de materiales asume el mando del recorrido y define este recorrido para el mando PLC. El sistema informático de flujo de materiales es un sistema redundante para garantizar una disponibilidad segura.

Gestión del almacén
El sistema de control del almacén WCS (Warehouse Control System) administra los puestos de ubicación de los palés del almacén automático de estanterías. Los palés son identificados en los diferentes puntos de recepción de mercancía mediante escáner de espejo oscilante. Los datos pertenecientes a los palés individuales tales como código de artículo, fecha de conservación, lote o cantidad de las unidades de venta sobre el palé son transmitidos a través de una interfaz desde el sistema de gestión del almacén existente al sistema de control del almacén.
El sistema de visualización representa en una interfaz gráfica los elementos de transporte necesarios incluyendo su estado y modo operativo. La visualización es posible desde cualquier ordenador autorizado de la red interna de Hassia.
Mantenimiento a distancia a través de acceso a la red VPN
Con la conexión a través de una red privada virtual (Virtual Private Network o VPN) existe una conexión de red rápida y sencilla entre Hassia y Krones. Gracias a esta conexión, el sistema de control del almacén y el sistema informático de flujo de materiales pueden ser mantenidos a distancia. El intercambio de datos entre Krones y la red de Hassia tiene lugar a través de una línea Internet punto a punto. Es la opción más económica para unir dos redes ya que genera sólo costos de conexión por Internet y no por teléfono.
Krones realizó capacitaciones en relación con los bloques de puesta en servicio a manera de preparación para las respectivas marchas de prueba. Las capacitaciones se hicieron según el principio 'train the trainer'. Es decir que los multiplicadores en las diferentes divisiones operativas de Hassia fueron capacitados de manera intensiva por los especialistas de ingeniería de flujo de materiales de Krones. Posteriormente estos colaboradores capacitaron a los usuarios finales.
Éxito cuantificable
Michael Schmidt resalta que esta reestructuración general está sujeta a un exhaustivo control del éxito, sobre todo ante el telón de fondo de la actual difícil situación económica. “La fusión de estas dos divisiones logísticas representa un ahorro del transporte de alrededor de 50 millones de litros, los cuales ya no tenemos que transportar de un emplazamiento a otro”. Además la alta eficiencia en el picking también repercute en el presupuesto del personal. Y debido a la gran variedad de productos seguirá aumentando el sector del picking, es muy sensato invertir en este segmento". En calidad de empresa que debe rendir cuentas a la familia de propietarios, la amortización de una inversión es un criterio importante". Para el almacén automático de estanterías operativo desde 2009, Schmidt prevé un plazo de amortización de entre cinco a seis años.