Ulma realiza para Altadis una moderna instalación de paletización y almacenamiento automático
Altadis, la antigua Tabacalera, ha emprendido una renovación de su modelo logístico, con el fin de ofrecer una respuesta eficaz y eficiente a unas condiciones del mercado marcadas por el dinamismo del consumo y, especialmente, por una pujanza de su actividad comercial en el exterior. Estos requerimientos han influido de manera decisiva para que la compañía haya migrado desde una organización logística tradicional hasta un concepto que incorpora la automatización de sus procesos internos.
Hasta la implantación del sistema automático de almacenamiento y preparación de pedidos, Altadis contaba con unos medios de almacenamiento convencionales, basados en la utilización de estanterías dinámicas por gravedad, que limitaban en gran medida la capacidad de respuesta de la compañía a unas necesidades que se resumían en una fuerte demanda y en una necesidad de satisfacerla con rapidez. Sin duda, ésta fue la razón que llevó a Altadis a replantearse su logística interna y optar finalmente por un sistema innovador que cubriera las funciones de almacenamiento y paletización automática.
Tras analizar diversas soluciones tecnológicas, la decisión de Altadis se inclinó por la innovadora solución logística que ofrecía Ulma Handling Systems, una empresa con larga trayectoria en el sector de la automatización y capaz de acreditar numerosas referencias en diversos campos de la industria.
La respuesta al reto planteado por la compañía tabaquera consistió en la instalación de cuatro robots paletizadores, cuyo funcionamiento se basa en hasta veinte modelos de mosaicos prefijados, según la tipología de los embalajes y presentación de productos de la compañía. A partir de estos mosaicos se preparan los palets identificados mediante una etiqueta de código de barras y después son almacenados en el sistema. Este se compone de cuatro transelevadores y un traverser que operan en 17 pasillos.
Los dos elementos esenciales del sistema, el núcleo de robots paletizadores y el sistema de almacenamiento, se hayan unidos mediante una línea de trasporte automático. Tanto la ingeniería como el equipamiento logístico y el software que soporta toda la instalación, fueron diseñados, desarrollados y equipados por Ulma Handling Systems.
El área de almacenamiento del centro de Logroño funciona las 24 horas del día y requiere tan solo de la participación de tres operarios y un capataz por turno. Este es un ejemplo del alto grado de productividad logrado por este centro en lo que atañe a las funciones de logística interna.
A día de hoy, el sistema funciona a pleno rendimiento y satisfacción de sus responsables. La rápida renovación de referencias –100 nuevas cada año- sitúa el plazo de permanencia de los palets en almacén en tan sólo seis días, lo que equivale a una rotación de su contenido equivalente a 60 veces al año. La instalación en que se ha operado esta transformación ha sido la fábrica de Logroño, convertida hoy en un auténtico referente para el sector tabaquero y, en general, para toda la industria de la transformación.
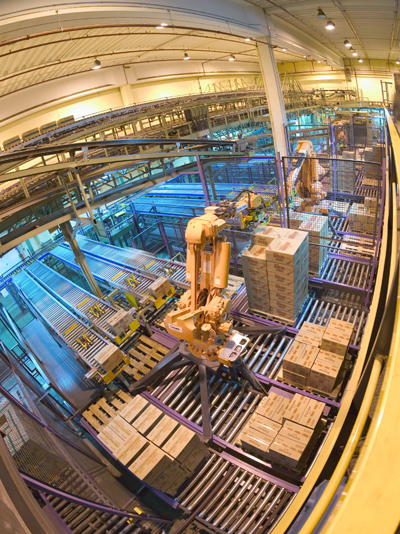
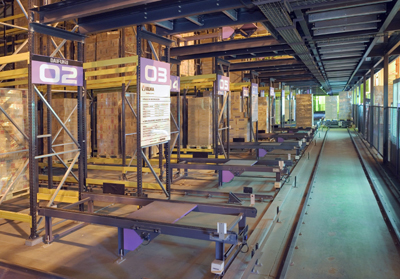
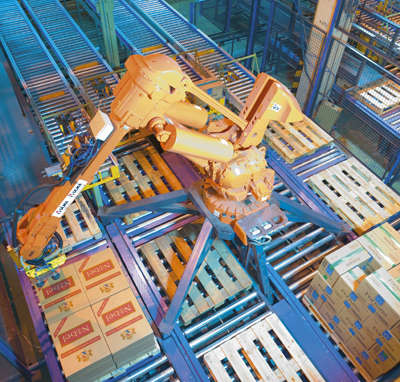