Sistemas de calibración
4 de noviembre de 2010
El pesaje en plataforma se caracteriza por ser una medida en condiciones próximas a las ideales, además de que, operativamente, con este tipo de pesaje es relativamente fácil y asequible efectuar una operación de chequeo y calibración del sistema.
Consideraciones básicas
Las características estructurales del propio sistema también se deben tener en consideración. Los excesivos acoplamientos estructurales (tuberías, etc.), la existencia de agitadores, acoplamientos mecánicos entre estructura y reactor (tubos, etc.) o la existencia de vacío en el proceso productivo, son factores determinantes a la hora de conseguir y mantener niveles de incertidumbre adecuados.
Otros efectos como las deformaciones estructurales debido a distribuciones de carga, o las debidas a dilataciones térmicas, también deber ser tenidos en consideración a la hora de planificar una calibración efectiva.
Componentes del sistema de pesaje
La célula de carga, es el elemento primario de medida, y por lo tanto el dispositivo que más habitualmente transmite errores del sistema hacia la medida final de peso. A la hora de obtener unos resultados óptimos en la calibración y repetitivos durante el período de producción, resulta imprescindible utilizar células de carga que minimicen los efectos inherentes al proceso productivo. En algunos casos, la existencia de agitadores provoca esfuerzos laterales que se pueden transmitir al transductor. Una de las soluciones adoptadas por muchos fabricantes es la de aislar la célula de la fuente de distorsión mediante acoplamientos mecánicos o arriostramientos. En esos casos, son estos dispositivos los que absorben los esfuerzos y evitan su transmisión en mayor o menor medida hacia las células. El principal inconveniente es que se generan movimientos y fricciones que conllevan desgastes mecánicos difíciles de predecir, y por lo tanto la repetibilidad del sistema se ve afectada considerablemente. Esta incertidumbre conlleva la necesidad de disminuir el tiempo entre calibraciones para mantener los requisitos de precisión del sistema.
Existen, sin embargo, células que absorben dichos esfuerzos sin necesidad de elementos mecánicos adicionales, manteniendo, además, el sistema rígidamente fijado a la base de soportación del recipiente. Los diferentes modelos de la serie KIS de Nobel, son prácticamente insensibles a los esfuerzos laterales, los cuales no afectan mecánica ni eléctricamente a la señal de peso (ver Figura 1).
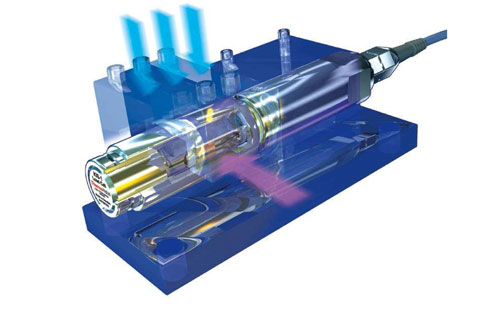
Las unidades electrónicas son un elemento fundamental dentro del sistema de pesaje y, desde el punto de vista de la calibración, deben incluir las características necesarias para asegurar y mantener la precisión requerida al proceso de calibración. Resulta evidente que los elementos mecánicos son siempre una fuente de error a considerar, mientras que los elementos electrónicos han de contribuir lo mínimo posible a la incertidumbre total de la medida.
Es imprescindible que los equipos dispongan de derivas térmicas perfectamente identificadas tanto para la ganancia como para el valor de cero, así como conversores analógicos/digitales (A/D) de alta resolución (16.000.000 de puntos internos). De esta manera podemos conseguir mejorar la repetibilidad del sistema y por consiguiente reducir las calibraciones periódicas.
Una característica a tener en cuenta dentro de los controladores de peso y que está íntimamente relacionada con los procesos de validación son la cantidad de puntos de calibración que permite el equipo. Habitualmente se dispone únicamente de dos valores a programar que suelen corresponder al cero y al fondo de escala. Evidentemente la unidad electrónica establece una recta de pendiente fija entre ambos puntos factor que genera errores en la medida a todo lo largo de dicha recta. Existen equipos que incluyen más puntos de calibración (ver Figura 2) lo cual permite linealizar la señal de respuesta y, por consiguiente, disponer de una señal de peso más precisa.
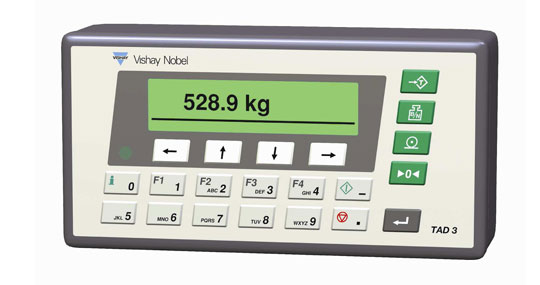
Procedimientos de calibración
Existen diversos métodos para realizar una comprobación y calibración de un sistema de pesaje, cada uno de ellos con sus ventajas y desventajas. Conviene reseñar que en algunos casos la solución más efectiva puede resultar de la variación de uno de esos procedimientos o la combinación de dos o más de ellos. Los procedimientos más habitualmente utilizados son:
· Carga patrón al 100% de la capacidad
· Calibración por sustitución de carga
· Aplicación de cargas segmentadas
· Simulación electrónica
· Aplicación de fuerza mecánica / hidráulica
· Calibración mediante caudalímetro (volumétrico / másico)
Carga patrón hasta el 100% de la capacidad nominal
Este procedimiento es utilizado en sistemas de baja y media capacidad, especialmente en plataformas y reactores donde se requieran precisiones elevadas. Se estima que los resultados que se pueden obtener están entre el 0,02% y 0,1% siempre que la instalación mecánica se haya realizado adecuadamente. La repetibilidad obtenida es elevada y si los pesos pueden ser ubicados uniformemente, el método permite modelar adecuadamente las características mecánicas del sistema, absorbiendo posibles errores generados a diferentes rangos del fondo de escala. En estos casos, resulta conveniente disponer de unidades de control de peso, con más de dos puntos de calibración. Habitualmente los amplificadores de peso disponen únicamente de dos valores de calibración: cero y fondo de escala. Una vez se ajustan y calibran ambos valores, la propia unidad electrónica genera una recta. La ejecución suele tener un coste elevado dado que se requiere un tiempo considerable para la manipulación de las cargas, además de disponer de las mismas en las condiciones metrológicas requeridas. No puede utilizarse en muchas ocasiones debido a limitaciones operativas y espaciales-
Es el método más frecuentemente utilizado para calibrar plataformas de pesaje, pues en aquéllas no suele haber problemas de espacio o manipulación. Además, si las plataformas son de baja capacidad (inferiores a 2000 kg), el método es extremadamente rápido.
Los principales pasos a considerar a la hora de realizar este procedimiento son los siguientes:
1. Efectuar el cero del tanque.
2. Aplicar las cargas patrón hasta un 10% (10 puntos) o el 20% (5 puntos) del sistema.
3. Añadir nuevas cargas patrón y comprobar.
4. Repetir el punto 3 hasta completar la capacidad del sistema.
Calibración por sustitución de carga
Se trata de una solución aplicable en la mayoría de los pesajes de reactores, tanques y silos. Permite alcanzar precisiones del sistema de entre el 0,05% y 0,2% consiguiendo cerrar el lazo de medida y por lo tanto comprobar la práctica totalidad del sistema mecánico y eléctrico. Como contrapartida, las operaciones pueden resultar relativamente lentas y generar problemas de precisión si las cargas son excesivamente pequeñas para el sistema.
Los pasos a seguir a la hora de proceder a la calibración son similares al anterior:
1. Efectuar el cero del tanque.
2. Aplicar la carga patrón (habitualmente una carga contrastada en una plataforma o sistema de pesaje de muy inferior capacidad al que se desea comprobar), de forma que la calibración se traza respecto a un sistema de confianza.
3. Comprobar la indicación del instrumento de pesaje. Sacar la carga patrón y llenar con material hasta que el instrumento vuelva a indicar exactamente lo mismo que con la carga patrón.
4. Aplicar de nuevo la carga patrón y comprobar.
5. Repetir los puntos 3 y 4 varias veces hasta completar la capacidad del sistema.
Aplicación de cargas de forma segmentada
Evidentemente la precisión obtenida con estos sistemas es inferior a las anteriores (entre 0,5% y 2%) y existe el riesgo de no detectar posibles errores generados en zonas específicas del rango de medida. Como contrapartida se trata de un sistema de rápida ejecución y que en casos puntuales puede ser utilizado para localizar posibles no linealidades en puntos determinados del rango de trabajo.
El procedimiento a seguir incluye los siguientes pasos:
1. Hacer el cero del sistema.
2. Comprobar la carga a aplicar en otro sistema de pesaje.
3. Aplicar la carga conocida y verificar la indicación.
4. Sacar la carga conocida y añadir el material al tanque hasta un punto conveniente. Volver a aplicar la carga conocida y verificar si la indicación del instrumento de pesaje aumenta en la cifra esperada.
5. Efectuar esta última operación en diversos puntos del tanque.
Simulación electrónica
Este tipo de procedimiento es habitualmente utilizado en las aplicaciones donde el uso de cargas conocidas no es factible. La complejidad en la instalación de las pesas patrón, o una elevada capacidad de los silos o tanques a calibrar, son las razones más habituales para decidirse por este tipo solución. Se debe tener en cuenta, en estos casos, que las restricciones mecánicas han de ser las mínimas posibles, ya que el sistema difícilmente las va a poder predecir y corregir. Por el contrario, la principal ventaja de esta opción es la de proponer una calibración rápida de ejecución de bajo coste de realización.
Las precisiones estimadas en este tipo de procedimientos están entre el 0,25% y el 1%, dependiendo en gran medida del dispositivo o calibrador a utilizar, así como de los datos indicados en la hoja de calibración de la propia célula de carga. La principales ventajas están en el bajo coste de ejecución así como la reducción de tiempo de calibración. Como contrapartida, se trata de un sistema que no cierra el lazo de medida, ya que no considera las diferentes fuentes de error mecánicas del sistema así como de la propia calibración de las células.
1. Desconectar una de las células de carga de la caja suma y conectar un puente de Wheatstone (PW) de resistencias fijas que simulen la impedancia de la célula.
2. (alternativamente podrían desconectarse la totalidad de las células).
3. Conectar la fuente de mV en paralelo con el PW.
4. Hacer un cero del sistema con la señal adecuada.
5. Simular una señal en mV que corresponda a un valor en kg conocido, calculado de acuerdo con la hoja de calibración de la célula. Ejecutar el ajuste del instrumento de pesaje en este punto con la indicación adecuada.
6. Volver a conectar la célula original y verificar el sistema con una carga conocida.
Aún siendo este procedimiento el que se ha venido utilizando con anterioridad, existen actualmente sistemas “inteligentes” formados por un calibrador (ejemplo en Figura 3) y una caja suma asociada. En estos casos, no es necesario actuar sobre las conexiones eléctricas, sino que la propia caja sumadora dispone de una conexión directa para el calibrador. Una vez el calibrador se conecta a la caja, es esta la que realiza la desconexión automática pasando a ser el calibrador el que alimenta y recibe la señal de las células de carga, así como suministra la señal en MV al amplificador de peso para poder linealizar la respuesta.
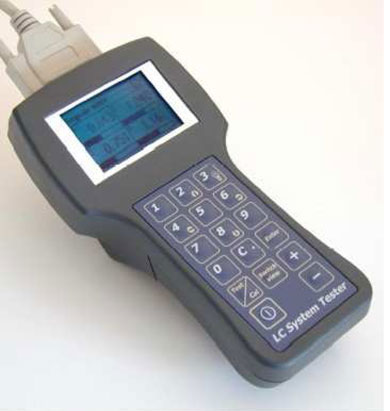
Aplicación de fuerza mecánica / hidráulica
La precisión estimada para estos procedimientos está entre el 0,25% y el 1%, dependiendo en gran medida de la célula patrón, así como del dispositivo utilizado para la aplicación de las fuerzas y su correcta distribución.
Se trata de un procedimiento que suele resultar más económico que utilizar cargas, consiguiendo, además, una comprobación efectiva de las distintas partes mecánicas del sistema de pesaje (tuberías, deflexiones estructurales, etc.). Su aplicación, sin embargo, requiere de un diseño especial en los tanques (cartelas especiales, etc.) y el equipo de medida correspondiente. En la Figura 4 se muestra una posible tipología para este procedimiento.
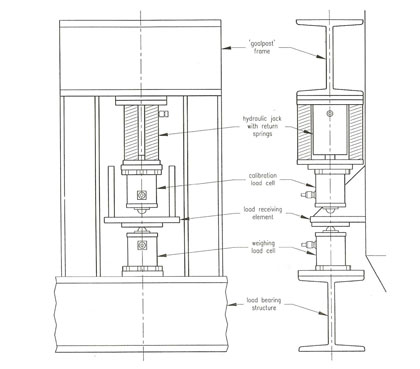
1. Instalar el equipo de aplicación de fuerza y la célula patrón de comprobación, en uno o varios puntos de apoyo del depósito.
2. Hacer un cero del sistema de pesaje con las nuevas condiciones.
3. Aplicar una fuerza conocida, levantando o cargando el depósito hidráulicamente. Leer el valor de la célula patrón y calibrar el sistema de forma conveniente respecto a esta indicación.
4. Efectuar esta última operación en al menos 5 puntos a lo largo de la curva de calibración, con el fin de compensar las no linealidades potenciales del sistema.
Calibración mediante caudalímetro (volumétrico / másico)
Este procedimiento puede resultar especialmente conveniente cuando los instrumentos de medida de caudal se encuentran ya instalados en las tuberías. El método permite comprobar razonablemente todas las características mecánicas intrínsecas al sistema de pesaje. Se debe tener en cuenta, sin embargo, los posibles errores acumulativos, así como los generados durante las fases transitorias de arranque y paro de flujo. Para minimizar este efecto puede utilizarse una válvula de tres vías, de forma que no se interrumpa el caudal.
Actualmente se disponen de diferentes tecnologías dentro de la medida de caudal que implican requerimientos también diferentes a la hora de preparar y realizar la calibración. Aún siendo diversas las opciones existentes (electromagnéticos, turbinas, desplazamiento positivo, coriolis, ultrasonidos, etc), los caudalímetros se pueden agrupar básicamente en volumétricos y másicos.
El primer grupo suministra valores de caudal y totalizado en unidades de volumen (m3, litros, etc) hecho que implica la necesidad de corregir los posibles cambios de densidad mediante la integración de la presión y temperatura del líquido utilizado. Por otro lado, el medidor másico trabaja directamente con señales de masa (kg, tn, etc), factor que le permite ser, a priori, una mejor opción a la hora de contrastar la señal obtenida del controlador de peso, ya que se evitan correcciones y por consiguiente los posibles errores de cálculo generados. Existen otras características propias de los medidores coriolis, que le infiere una ventaja ante la mayoría de las alternativas indicadas anteriormente. Por un lado el hecho de no disponer de piezas móviles susceptibles de desgaste y por lo tanto reducir la repetibilidad del sistema. Por otro lado, el hecho de no depender de características físicas de los líquidos utilizados (por ejemplo conductividad) le permite utilizar cualquier producto para contrastar el peso del sistema sometido a calibración.
A la hora de plantear una calibración mediante este medidor de caudal, conviene asegurar si se dispondrá de líquido para ser vehiculado, así como sistema de bombeo, o por el contrario se deberá incluir junto con el sistema de calibración.
Para los casos en que la propia instalación ya disponga del sistema y producto adecuado par realizar la calibración, el hardware necesario únicamente deberá incluir el medidor y el conjunto de valvulería correspondiente para su conexión a proceso (ver ejemplo en Figura 5). Por el contrario si la instalación no dispone de sistema de bombeo o producto a vehicular, será necesario que el conjunto de calibración incluya un segundo skid con un depósito y bomba auxiliar (ver Figura 6).
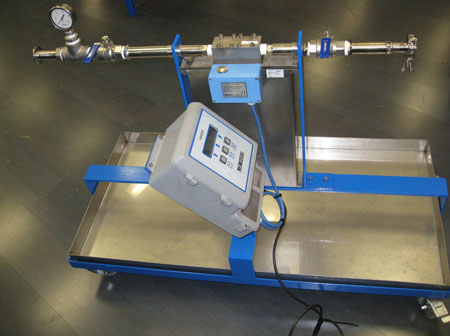
1. Adquirir el cero con el tanque vacío.
2. Abrir el paso de fluido hasta un 20% de la capacidad del tanque. Calcular la masa a partir del caudalímetro y calibrar ese punto de la curva.
3. Repetir el punto 2 para el 40, 60, 80 y 100% de la capacidad de la báscula.
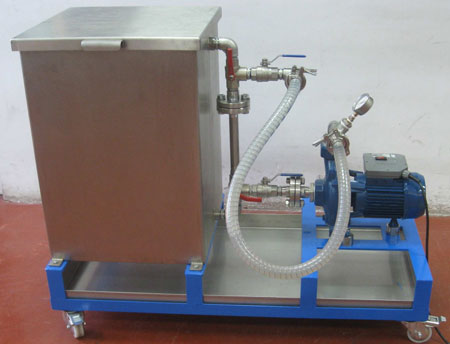
Resulta evidente que, tal como se indica al inicio de este artículo, existen otros métodos de calibración, no enumerados en el listado inicial y que en la mayoría de casos resultan de variaciones sobre los mismos. Si los estudiamos detenidamente, podremos comprobar que básicamente siguen dos patrones diferenciados.
Por un lado existen los basados en la reproducción más o menos fiel del propio proceso de pesaje. En este caso, la calibración intentará aproximarse a la situación real de trabajo del depósito o reactor. Resulta evidente, que la mejor manera, en este caso, pasa por que el recipiente a calibrar soporte a una carga conocida ya sea en su interior o en su exterior. Dentro de este grupo, se podrían considerar como incluidos, todos aquellos procedimientos que a partir de una cargas patrón, o mediante la adición de producto en el interior del recipiente, puedan contrastar la medida indicada por el controlador de peso.
Estos sistemas disponen como principal ventaja el poder cerrar el lazo de medida, contrastando la respuesta dinámica del sistema. Un inconveniente, que suele existir en este tipo de procedimientos, es la lentitud de ejecución de los mismos. Por el contrario, el segundo grupo incluiría todos aquellos procedimientos de carácter indirecto, que tipifican la respuesta eléctrica del transductor o célula de carga. Las diferentes variantes que se pueden adoptar, siempre coincidirán en no cerrar completamente el lazo de medida, y por lo tanto no poder integrar y solventar los posibles errores del sistema. Si embargo, se trata de soluciones rápidas de ejecución y que en caso de instalaciones sencillas de inspeccionar aportar una fiabilidad elevada.
A la hora de escoger el procedimiento más adecuado, resulta evidente que no existe una regla concreta que permita esa selección. Debido a las características singulares de cada una de las aplicaciones, es necesario tener en cuenta los aspectos positivos y negativos de cada uno, eligiendo el más efectivo en cada caso. Los métodos comentados no pretenden ser más que una guía genérica y suele ser recomendable la consulta previa a un especialista o al propio proveedor del sistema de pesaje, antes de efectuar la elección final de un programa de comprobaciones y calibraciones adecuadas.