Nuevas propuestas para el mecanizado ecológico de componentes de titanio aeronáutico
El titanio y sus aleaciones son, hoy en día y en un futuro próximo, materiales clave en la industria aeroespacial. La mejora de la productividad en el mecanizado de estos materiales es, por tanto, un requerimiento industrial de primer orden. Este artículo presenta un estudio que demuestra que, en términos económicos y medioambientales, el uso de MQL supone una mejora en el mecanizado de estos materiales, pues reduce el consumo de energía total y el consumo de herramienta por unidad de pieza fabricada bajo condiciones de corte habituales en la industria, hecho que habitualmente se cuestiona cuando se emplea MQL. Para condiciones de corte de muy alta productividad, la refrigeración mediante nitrógeno líquido parece ser una opción con un interesante futuro.
Una gran resistencia en relación con su peso, sus propiedades anticorrosivas y su conductividad térmica y eléctrica han convertido al titanio y sus aleaciones en un material clave en la industria aeroespacial. La necesidad de nuevos aviones más ligeros y eficientes no ha hecho sino incrementar la demanda de este material, a pesar de su precio, convirtiendo al sector aeroespacial en su principal consumidor. El uso de este material en aviones alcanza componentes de muy distinta naturaleza: desde elementos estructurales del tipo perfiles, cuadernas o herrajes como en componentes de turbopropulsores, anillos y carcasas principalmente, o de mecanismos, como los trenes de aterrizaje (Figuras 1 y 2).
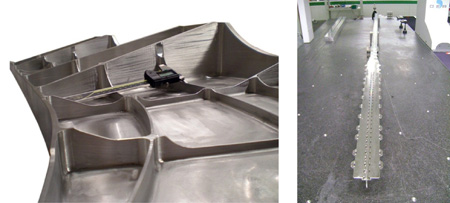
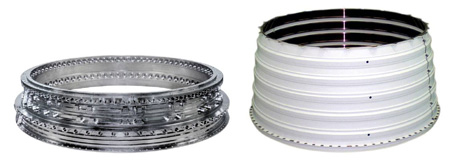
Hoy en día, el proceso productivo más utilizado a la hora de fabricar este tipo de piezas es el mecanizado, proceso que por un lado es complejo por la naturaleza del material y por otro costoso. En primer lugar se trata de un proceso por arranque de viruta que elimina gran parte de un material que, ya de por si, es caro. En segundo lugar, la pobre conductividad térmica del titanio hace que sea la herramienta de corte, y no el componente de titanio, la que absorba el intenso calor que se produce durante la operación de mecanizado. Esto se traduce en un desgaste prematuro e intenso de la herramienta. Asociado a ello se produce un elevado consumo de líquido refrigerante con el fin de evacuar el importante calor generado, máxime cuando el titanio es altamente inflamable. Finalmente, los procesos de corte se realizan a baja velocidad, lo que los convierte en procesos lentos donde el bajo módulo de elasticidad del titanio favorece que la pieza se separe de la herramienta de corte causando ‘chatter’ y problemas de tolerancia en el caso, muy común en aeronáutica, de piezas de paredes delgadas.
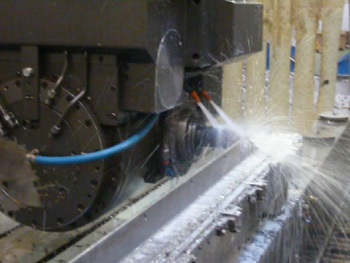
En un entorno como el actual, en el que la complejidad de las piezas de titanio para el sector aeroespacial es cada día mayor y, donde además las empresas necesitan aumentar su competitividad, resulta crítico desarrollar métodos de fabricación más eficientes para los componentes fabricados en este material.
Al margen del análisis económico, hoy en día es necesario considerar el impacto medioambiental de cualquier producto, aplicación o proceso, ya sea por la cada vez más exigente demanda de la sociedad de respeto al medio ambiente, o bien, por la obligación de cumplir nuevas leyes más restrictivas. En especial, la eliminación de los lubricantes resulta crítica, por lo que en los países industrializados se están desarrollando estrictas leyes medioambientales relativas a la utilización y reciclado de fluidos de corte en la industria.
Estas dos necesidades, mejorar la productividad del mecanizado de titanio y reducir el impacto ecológico de este proceso, hacen necesario la propuesta de nuevas alternativas de mecanizado ecológico de componentes fabricados con este material. Dentro del Proyecto Europeo EMC2 se han llevado a cabo la evaluación de nuevas técnicas de mecanizado que afectan a los lubricantes utilizados durante este proceso desde la doble vertiente del coste económico y el medioambiental.
Nuevas propuestas de mecanizado ecológico de titanio
Realización experimental
El objetivo de la experimentación realizada es poder extraer conclusiones claras sobre el uso de técnicas de refrigeración alternativas a la taladrina, comúnmente utilizada en el proceso de mecanizado de titanio. Para ello, se han analizado la calidad de la pieza mecanizada, la productividad del proceso, el consumo de recursos y el impacto en el medio ambiente.
La experimentación se ha realizado sobre probetas de Ti6AL4V, tipo de titanio más común en aeronáutica también conocido como titanio de grado 5 o Ti 6-4, con una composición química de 6% de aluminio, 4% de vanadio, y casi todo el remanente de titanio. Esta aleación es algo más resistente que el titanio puro teniendo la misma rigidez y propiedades térmicas (excepto la conductividad la cual es aproximadamente un 60% menor que en el titanio puro). Se han llevado a cabo ensayos experimentales de fresado a fin de vida de herramienta sobre probetas, con el criterio de fin de vida de herramienta de valor de desgaste máximo en el flanco (Vb) de 0,4 mm.
Se han comparado tres diferentes técnicas de refrigeración: i) Taladrina exterior, ii) MQL exterior (Minimun Quantity Lubricant), iii) MQL exterior combinado con nitrógeno líquido (N2). Se ha partido de la hipótesis de que desde el punto de vista de la refrigeración las operaciones de desbaste son las más problemáticas en comparación con las operaciones de acabado. Por una parte, el caudal de viruta que se obtiene es mayor por lo que su evacuación puede suponer un problema, y por otra parte la temperatura alcanzada durante el mecanizado es también superior lo que supone un mayor desgaste de la herramienta.
La experimentación se ha llevado a cabo con dos herramientas de desbaste en dos máquinas diferentes, con plato Seco Tools Ø32 mm en la fresadora Ibarmia ZV 25/U600 ubicada en Tecnalia, y con plato Sandvik Ø125 mm en la fresadora Versa W fabricada y ubicada en la planta de fabricación que Nicolás Correa S.A. tiene en la localidad de Burgos. Se han utilizado los mismos parámetros de corte para ambas herramientas, siendo la velocidad de corte la única variable del proceso modificada y manteniendo constantes el resto de parámetros. Como condiciones de corte de referencia se han utilizado los parámetros de corte aconsejados por el suministrador de herramientas que, a su vez, se han contrastado con las condiciones de corte más productivas con el objeto de acentuar las posibles diferencias entre las distintas técnicas de refrigeración. Durante la ejecución de la experimentación se ha utilizado un vatímetro para registrar la potencia consumida por la máquina. Para el suministro de MQL, las dos máquinas utilizadas disponen de su propio equipo de MQL, tal y como se puede apreciar en la Tabla 1 donde se resumen las principales características de la experimentación realizada.
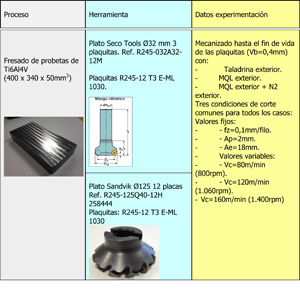
La Tabla 2 resume el equipamiento empleado durante la experimentación.
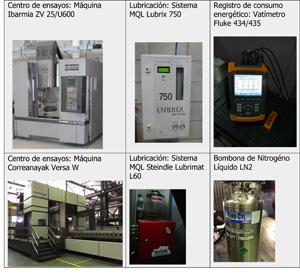
Resultados
Con la finalidad de comparar los resultados obtenidos con las tres técnicas de refrigeración experimentadas (taladrina exterior, MQL exterior y MQL exterior + N2), se han medido y analizado los siguientes parámetros:
- Longitud de superficie mecanizada en función del desgaste de la herramienta.
- Rugosidad superficial (Ra) de la pieza mecanizada para analizar la calidad superficial del mecanizado.
- Consumo total durante la operación de mecanizado.
A su vez, se ha realizado un análisis económico y de impacto medioambiental generado con cada técnica de refrigeración.
a) Longitud de superficie mecanizada
Se mide la longitud de la viruta mecanizada hasta el fin de vida de la herramienta, es decir, hasta un desgaste en el flanco (Vb) de 0,4 mm. El Gráfico 1 muestra el valor de la longitud de viruta mecanizada que se obtiene en función de la velocidad de corte y la técnica de refrigeración utilizada.
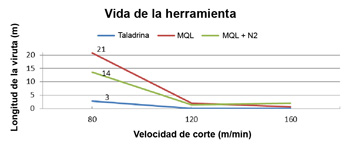
Gráfico 1: Longitud mecanizada para los diferentes métodos de refrigeración y diferentes velocidades de corte para un desgaste establecido de Vb=0,4 mm.
Se puede apreciar que a Vc=80m/min, la longitud de la superficie mecanizada es de 21 m al utilizar MQL exterior, frente a los 14 m obtenidos al utilizar la combinación de MQL exterior y N2. En cambio, al usar taladrina convencional, se han generado solamente 3 m de viruta. Estos datos indican que el desgaste generado en la herramienta es mayor con el uso de taladrina. Esto se debe a que el MQL accede mejor que la taladrina a la zona de la herramienta a enfriar, incrementando su vida.
Los condiciones de corte con Vc suprior a 120m/min son demasiado duras, ya que, a partir de aproximadamente ese límite, el desgaste aumenta considerablemente y la longitud de viruta mecanizada disminuye siendo prácticamente la misma en los tres casos. La mayor longitud de viruta mecanizada se obtiene con el uso de MQL combinado con N2 como refrigerante, aunque los valores de 2 m mecanizados con MQL+N2 frente a los 0,7 m obtenidos con solo MQL son bastante similares. En el caso de la taladrina, no se ha considerado realizar ensayos a estas velocidades dados los resultados obtenidos para una velocidad de corte de 80 m/min.
b) Análisis de la calidad superficial del mecanizado
La calidad superficial de la pieza suele ser un requisito industrial fundamental por lo que también se ha tenido en cuenta en este estudio. Se ha medido y comparado la rugosidad superficial Ra en la pieza mecanizada en función de la técnica de refrigeración utilizada. El análisis se ha realizado para Vc=80 m/min, debido a su mayor vida de herramienta. El Gráfico 2 muestra la media de los valores de rugosidad Ra obtenidos en las diferentes pasadas de mecanizado en función de la técnica de refrigeración.
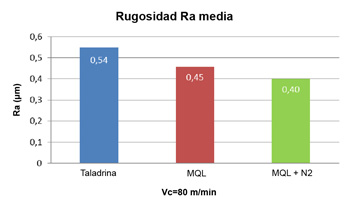
Gráfico 2: Media de los valores de rugosidad Ra en función del tipo de refrigeración para Vc=80 m/min.
Se observa que el menor valor de rugosidad Ra=0,4 µm se obtiene con el uso de MQL+N2, mientras que el peor resultado de Ra=0,54 µm se obtiene con el uso de taladrina.
c) Consumo total durante la operación de mecanizado.
Para comparar el consumo total de la operación en función de la técnica de refrigeración utilizada, se han tenido en cuenta diferentes consumos generados durante el mecanizado: el consumo energético (obtenido por mediante vatímetro de la potencia consumida por la máquina durante el mecanizado), el consumo de aceite, el consumo de agua y el consumo de nitrógeno. Para la comparativa se toma como referencia el mecanizado con taladrina asignándole un valor del 100%, y calculando el porcentaje correspondiente a las otras dos técnicas de refrigeración. En el Gráfico 3, se puede observar la comparativa de los consumos totales para cada uno de los aspectos estudiados, en función de la técnica de refrigeración utilizada.
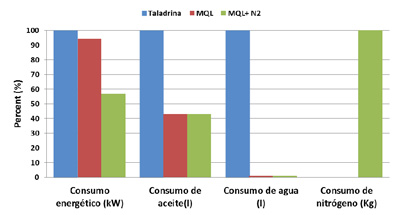
Se puede observar cómo en el caso del MQL y del MQL+N2, los consumos de energía, aceite y agua son inferiores que en el caso de la taladrina, pero al incluir el consumo de Nitrógeno en el MQL+N2, la principal conclusión es que desde el punto de vista de los consumibles, el MQL es la opción más interesante. En el caso del consumo energético la principal diferencia es debida a la bomba de taladrina y MQL y en el caso del MQL +N2 es inferior dado que para el mismo volumen de viruta evacuado, al ser la Velocidad de corte el doble (de 80 a 160 m/min) el tiempo que la bomba está en funcionamiento es la mitad. En el siguiente apartado, se valorarán económicamente las diferentes opciones.
Análisis económico
El coste por volumen de material mecanizado (€/cm³), que depende directamente del caudal de viruta (cm³/min), es un parámetro que permite realizar un estudio económico del proceso de mecanizado. Se ha estimado el caudal de viruta correspondiente al mismo valor de desgaste de herramienta de Vb=0,4 mm para cada técnica de refrigeración (taladrina, MQL exterior, MQL ext+N2). Para cada una de las técnicas se ha elegido la velocidad de corte más productiva para el valor de desgaste mencionado. El Gráfico 4 muestra los valores de caudal de viruta con valor de desgaste 0,4 mm para cada una de las herramientas y técnicas de refrigeración.
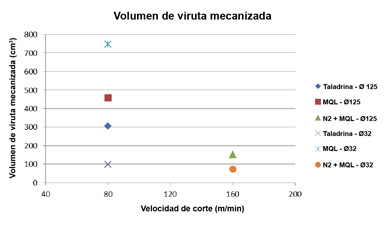
Para calcular el coste de la operación de fresado se han tenido en cuenta los diferentes costes de la herramienta, del refrigerante (aceite, agua y Nitrógeno) y el consumo de energía de la máquina. Se ha tomado como referencia una pieza tipo de perfil en T de titanio de la empresa Aciturri, cuyo volumen de viruta a eliminar es de 512 cm3.
Los costes de la herramienta se han calculado con los datos obtenidos de la experimentación realizada con la herramienta de Ø32 mm con tres plaquitas, siendo el coste estimado de cada plaquita de 15 €. Con estos valores, se obtiene el coste de desgaste de la herramienta para cada técnica de refrigeración, teniendo en cuenta el volumen eliminado con cada una de las técnicas a la velocidad de corte que se ha considerado más idónea para cada técnica de refrigeración, Vc=80m/min en el caso de la taladrina y del MQL y Vc=160 m/min en el caso del MQL+N2.
El coste de taladrina se calcula a partir de la estimación de consumo de taladrina de una máquina de aproximadamente 6.000 litros/año. Se considera taladrina con una concentración de aceite de un 7%, y considerando costes de aceite y agua estándares estimados de 2,8€/l en el caso del aceite y de 0,00068 €/l en el caso del agua.
El coste de MQL se calcula a partir de datos suministrados por el fabricante del sistema MQL. En este caso, del sistema Lubrix 750. El consumo de aceite en el nivel 15 para la fresa ensayada es de 35 ml/h (180l/año) a un precio estimado de 16 €/l.
El coste del Nitrógeno se estima en 5,57€/pieza calculado teniendo en cuenta el tiempo de emisión del gas durante el tiempo de mecanizado.
El coste del consumo de energía se basa en datos obtenidos durante la experimentación (consumo de la máquina en vacío y durante el proceso) y datos suministrados por el fabricante (datos de las bombas de MQL Lubrix 750 y de taladrina).
No se han incluido los costes de la inversión inicial necesaria para cada una de las técnicas.
En la Tabla 3 se muestran los diferentes costes calculados, para cada una de las técnicas de refrigeración.
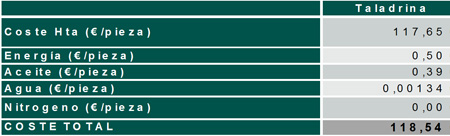
Se puede observar cómo el mecanizado con MQL es el de menor coste por pieza de las tres técnicas analizadas. En el caso del MQL+N2, el coste por pieza obtenido da un valor interesante comparándolo con la taladrina, pero habría que prestar especial atención al tiempo de cambio de placas y pensar en un tiempo de preparación externo para la puesta a punto de las herramientas superior a los otros dos casos dado que el volumen de viruta evacuado es menor que en los otros dos casos.
Impacto medioambiental
Hoy en día se cuenta con una motivación ambiental especial desde que de la eliminación de los lubricantes resulta una menor polución. En los países industrializados, están evolucionando estrictas leyes medioambientales entorno a la utilización de los fluidos de corte. Por ello, se ha considerado interesante realizar un análisis del impacto medioambiental que supone cada una de las técnicas de refrigeración analizadas.
Se han utilizado los siguientes dos ratios para medir el impacto medio ambiental, además de los consumos previamente calculados.
- Gestión de Eficiencia energética: determina el porcentaje de consumo energético del proceso de mecanizado con respecto del consumo energético total.
- Huella de Carbono: se calculan las emisiones de gases de efecto invernadero de la operación analizada y del ciclo de vida de los productos que han intervenido durante uno u otro proceso. En este caso se han tenido en cuenta la huella del aceite, de la electricidad y del metal duro de las herramientas.
En la Tabla 4 se muestran los valores obtenidos para estos indicadores en los tres casos.

Se puede observar cómo el uso de MQL es el caso de menor porcentaje de eficiencia energética o, lo que es lo mismo, donde el consumo energético durante al proceso de mecanizado es menor con respecto al consumo total para las tres técnicas de refrigeración. Por otra parte, desde el punto de vista de la huella de carbono, el caso del MQL +N2 presenta una huella ligeramente inferior a los otros dos casos. Hay que tener en cuenta en este caso que las condiciones de corte en las que se utiliza MQL +N2 (160m/min) duplican, para el mismo desgaste, las alcanzables con MQL o taladrina, reduciendo el tiempo de mecanizado a la mitad.
Conclusiones
Este trabajo ha permitido obtener las siguientes conclusiones:
- Es posible mecanizar titanio Ti6Al4V en operaciones de desbaste en fresado con MQL de manera productiva, obteniéndose resultados de rugosidad Ra similares a los obtenidos con taladrina.
- La calidad final de las piezas mecanizadas no presenta diferencias sustanciales, ni dimensionales ni en la rugosidad superficial, dependiendo de la técnica refrigeración de herramienta elegida.
- El consumo de energía resulta ser un factor diferenciador, debido principalmente al consumo de la bomba del circuito de taladrina. En el caso del MQL+N2 el consumo resulta aproximadamente la mitad que las otras dos técnicas estudiadas, dado que la velocidad de corte es el doble que en el caso del MQL.
- El precio de la herramienta supone un porcentaje muy alto en relación con los costes de consumo de energía y fluido de corte en el coste total del proceso de mecanizado, por lo que la vida de herramienta es un factor clave a la hora de obtener la relación coste/productividad.
- Para considerar la opción MQL+N2 en operaciones de alta productividad habría que considerar otros aspectos como la preparación de varias herramientas y el cambio rápido de las mismas en máquina, datos que no se han valorado en este estudio.
En resumen, este estudio demuestra que, en términos económicos y medioambientales, el uso de MQL en el mecanizado de componentes de titanio para la industria aeronáutica supone una mejora frente a refrigerantes tradicionales, hecho que habitualmente se cuestiona. Esta ventaja económica es factible gracias a la identificación de unas condiciones de corte productivas y a la reducción en el consumo de energía total durante el ciclo vida que produce el uso de MQL. Más aún, el uso de MQL en el mecanizado de titanio puede suponer un ahorro considerable en el coste total de este proceso, dado el alto porcentaje que supone el precio de la herramienta en el coste total del mismo.
Agradecimientos
Este trabajo ha sido parcialmente financiado por la Comision Europea a través del Proyecto del 7º Programa Marco NMP-285363 ‘EMC2-Factory- Eco Manufactured transportation means from Clean and Competitive Factory’.