Informe Leuze de aplicación: cómo se fabrica una placa de circuito
Producir una placa de circuito de la máxima calidad con hasta 1.500 componentes electrónicos requiere muchos conocimientos. Esos se pueden hallar en Unterstadion, Alemania, una comunidad formada por unos 800 residentes en el distrito de Alb-Danubio. Es aquí donde se encuentra la sede central de Leuze Electronic Assembly GmbH. Más de 200 empleados trabajan en tres turnos en esta planta, que ocupa más de 3.000 metros cuadrados. LEA, una filial del grupo Leuze Electronic, existe desde 1977 y es una de las seis plantas de producción de Leuze en todo el mundo que se ha especializado en Servicios de Producción Electrónica (EMS, por sus siglas en inglés), la producción de componentes electrónicos.
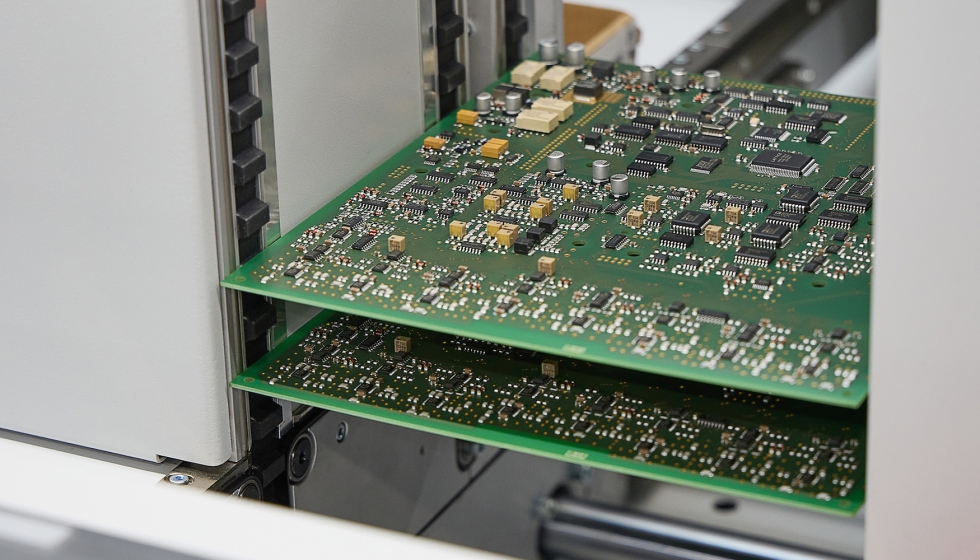
Un socio fiable
Leuze Electronic Assembly GmbH ha seguido evolucionando de forma continua y exitosa desde su fundación en 1977. En 2022, su facturación ascendió a unos 64,5 millones de euros; su producción ha experimentado un crecimiento medio anual del 17% durante los diez últimos años. Una historia de éxito que se debe en parte a una característica especial de esta sede, como explica el director de producción, Georg Denkinger: “Dos tercios de nuestra producción se destinan al grupo Leuze global y un tercio corresponde a clientes externos. Esta combinación de producción propia y externa es bastante única. Muchos competidores lo intentan, pero no lo consiguen”. Según Denkinger, exige una mentalidad diferente y estructuras adaptadas, también por lo que se refiere al software utilizado. Y por último, pero no por ello menos importante, la perseverancia, porque hace falta que transcurra un cierto tiempo para amortizar algunas inversiones. Los clientes de Leuze Electronic Assembly saben que aquí están bien atendidos: “Tratamos igual a los clientes externos e internos. Esto se dice fácilmente en los buenos tiempos, pero también se ha de demostrar cuando las cosas se complican y, desde luego, significa asignar un orden de prioridad externa si el cliente tiene un problema. Esto sólo es posible si estamos preparados”, explica Georg Denkinger. Y Leuze Electronic Assembly en Unterstadion lo está, como demuestran sus plantas de producción ultramodernas con tres líneas de producción.
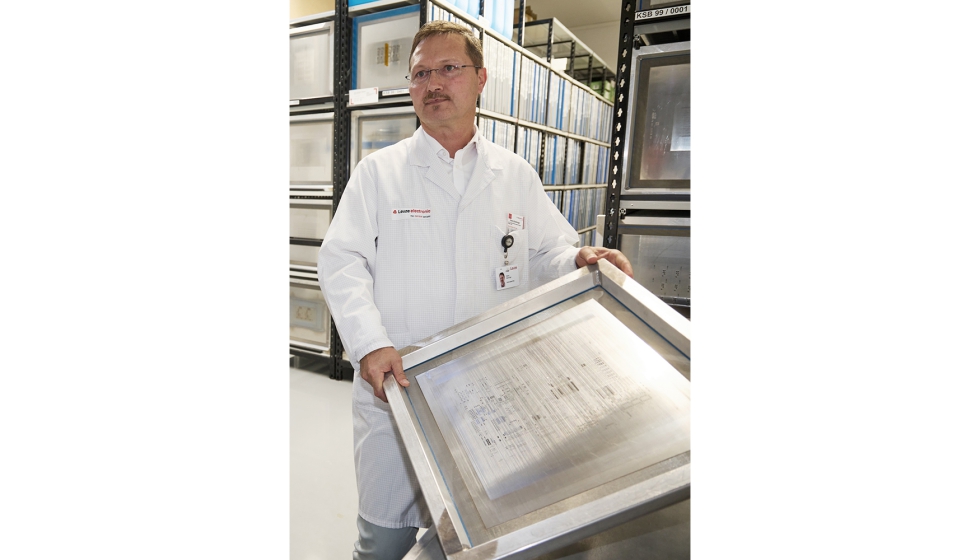
Millones de piezas pequeñas
“La complejidad del montaje de una placa de circuito se parece a la fabricación de un smartphone moderno”, señala Georg Denkinger. Leuze Electronic Assembly procesó más de 320 millones de dispositivos de montaje superficial (SMD) en 2022. Se trata de componentes electrónicos de pequeño tamaño que se sueldan a la placa del circuito, además de unos diez millones de componentes de montaje por inserción (THT). Se trata de componentes cableados que se conectan a la placa del circuito y se sueldan a la parte posterior.
La precisión es imprescindible
El montaje de la placa del circuito empieza por la programación. Para ello, Leuze utiliza una máquina que programa todo tipo de dispositivos. Más de 500.000 componentes pasan por esta etapa cada año. Un código Data Matrix, que contiene el número de referencia, el número de pedido y el número de serie, se graba mediante láser sobre el componente. Su ventaja es que, si posteriormente se determina que un componente es defectuoso, el código se puede utilizar para el seguimiento preciso; por ejemplo, cuándo se fabricó el dispositivo, por qué estaciones pasó y cómo se comprobó. Una vez grabado con láser, el componente pasa a la línea SMD de ‘Impresión de pasta de soldadura’: se aplica un troquel a la placa de circuito vacía como patrón y la pasta de soldadura rellena las cavidades del troquel. “La pasta es comparable al cable de soldadura del pasado; conecta los componentes de montaje superficial a la placa del circuito”, dice Georg Denkinger. La altura de la pasta es importante, debido a que se aplica con mucha precisión hasta una micra. En comparación, un cabello humano tiene un grosor medio de unas 50 a 80 micras. Una máquina mide la placa del circuito mediante una inspección 3D para determinar si la pasta se ha aplicado correctamente por todas partes.
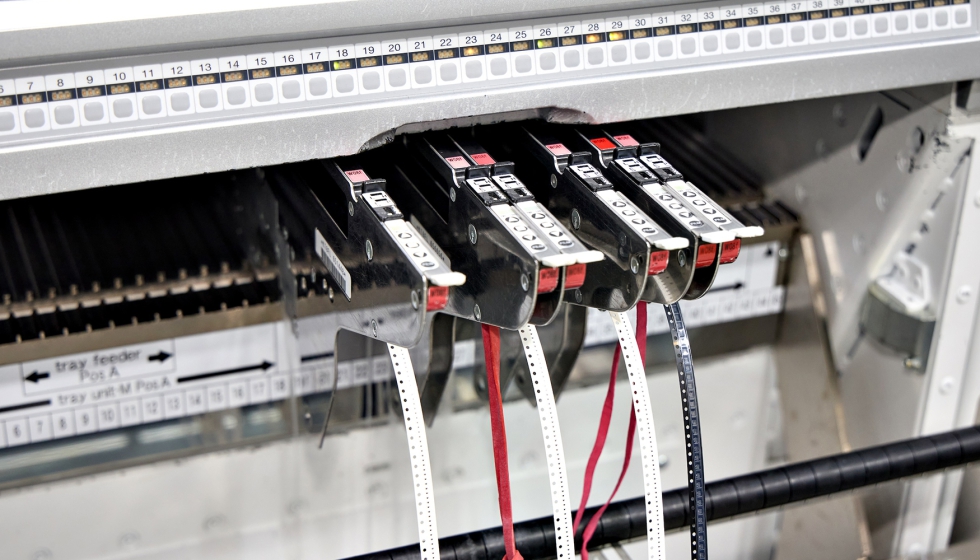
Tres líneas flexibles
En el proceso posterior, los rollos previamente comprobados con componentes estándar entran en la máquina de montaje, que retira los componentes y los coloca en los respectivos depósitos de la pasta de soldadura. Gracias a un sistema ‘Pick-by-Light’, la selección de pedidos está diseñada para ofrecer eficiencia y evitar errores: las señales luminosas indican al empleado responsable con exactitud dónde se ha de colocar cada rollo. A continuación, se acusa el recibo. Otra ventaja del montaje de placas de circuitos en Leuze es que sus tres líneas pueden procesar todo tipo de componentes, tanto pequeños como grandes. Esto se controla por un ordenador central de ASYS. A continuación, vamos al horno: la temperatura correcta es primordial para que la pasta se funda. El perfilado de la temperatura se realiza en conformidad con J-STD-020, y la soldadura se lleva a cabo en una atmósfera de gas inerte definida.
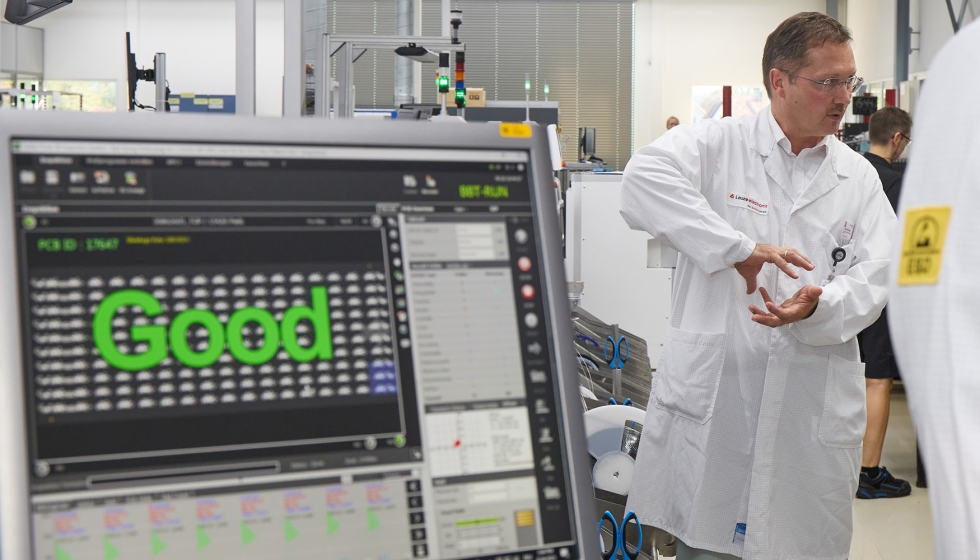
La calidad es clave
A continuación, se realiza la inspección óptica de la placa del circuito de forma totalmente automática. Aquí se utiliza alta tecnología, con un sistema de inspección óptica automática (AOI-3D) de KohYoung. Un láser proyecta una trama cuadriculada sobre la placa del circuito, facilitando así la medida de la superficie. Además, la máquina comprueba los componentes mediante el procesamiento de imágenes. Con absoluta precisión, como enfatiza Georg Denkinger: “Nada puede ocultarse de sistema. Tanto si se trata de un componente electrónico que falte, que no haya sido soldado correctamente o si su alineamiento y la altura no son correctos, estos y otros muchos posibles errores se detectan de manera fiable, en cuyo caso la placa es expulsada y reprocesada”. Hacen falta 17 segundos como máximo para inspeccionar una placa de circuito de esta forma. Para centenares de componentes extremadamente pequeños, esto constituye un gran logro. Para el director de producción, el AOI-3D es un paso importante para garantizar la calidad: “Hemos venido utilizando el proceso AOI desde 2007, y en 2019 hicimos la transición a la versión 3D. Esto nos coloca por delante de muchos competidores”. Los clientes de Leuze Electronic Assembly se benefician de la máxima seguridad operativa de los montajes electrónicos fabricados en Unterstadion.
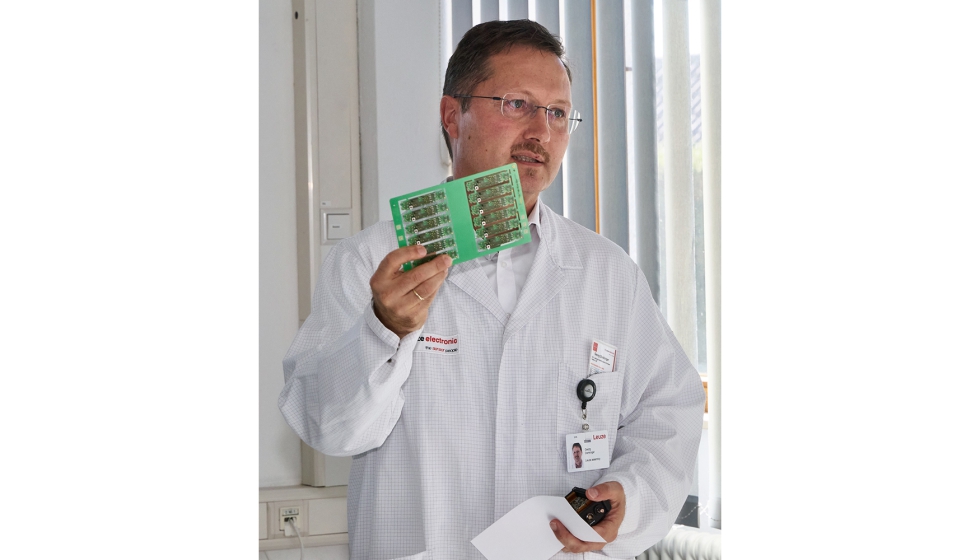
Placas de circuitos incluso para entornos adversos
En el siguiente paso, una máquina coloca diafragmas sobre los sensores correspondientes, con una exactitud de unas 15 micras. Por consiguiente, reciben un claro nivel de conmutación de oscuro a luminoso. Cada año se colocan aquí entre 600.000 y 700.000 diafragmas, tras lo cual se someten al ‘Flying-Pobe-Test’, que consiste en una sonda con hasta ocho agujas que se desplaza sobre la placa del circuito. Las agujas establecen contacto con los componentes electrónicos y comprueban su funcionalidad; se repite lo mismo en la parte inferior. Además, se dispone de un sistema de prueba de cama de agujas con más de 1.500 agujas, en el caso de que el montaje se fabrique en cantidades muy grandes.
Por último, pero no por ello menos importante, Leuze Electronic Assembly suministra placas de circuitos con un revestimiento de protección, si así lo desea el cliente. “Un revestimiento resulta útil, entre otros, en entornos en los que pueda aparecer condensación”, explica Georg Denkinger. “Por ejemplo, producimos placas de circuitos para grandes camiones en minería y motos de nieve, que deben funcionar de manera fiable incluso en condiciones extremas”. Tras este paso, las placas de circuitos ya están casi acabadas: ahora se cortan automáticamente mediante una fresadora o un láser. Si el cliente quisiera módulos completos, los empleados de Unterstadion instalan las placas de circuitos en carcasas y montan los componentes adicionales. Programación, parametrización y pruebas de funcionamiento al nivel del módulo completan el proceso. Estos módulos se crean, por ejemplo, para dispositivos destinados al análisis de sangre.
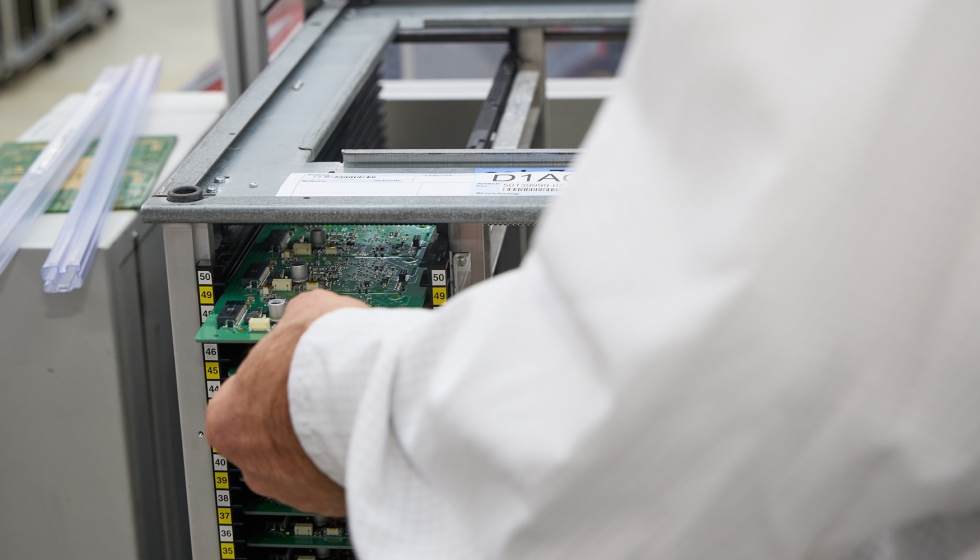
Gran demanda
Gracias a su amplia experiencia en la producción EMS y a sus altos niveles de calidad, Leuze Electronic Assembly GmbH es un socio fiable para sus clientes. El 99,7% de los componentes electrónicos producidos en Unterstadion ya están libres de errores a la primera. Gracias a los empleados formados en la planta, las máquinas de última generación y las patentes de los sistemas de desarrollo propio, LEA ha allanado el camino para un futuro de éxito continuo: “Nos gustaría seguir creciendo e incrementar la cuota de la fabricación subcontratada hasta el 50%. Existe un enorme potencial para ello y estamos registrando un gran número de solicitudes de clientes”, señala Georg Denkinger. Por tanto, las previsiones son buenas para los especialistas en placas de circuitos de Unterstadion.
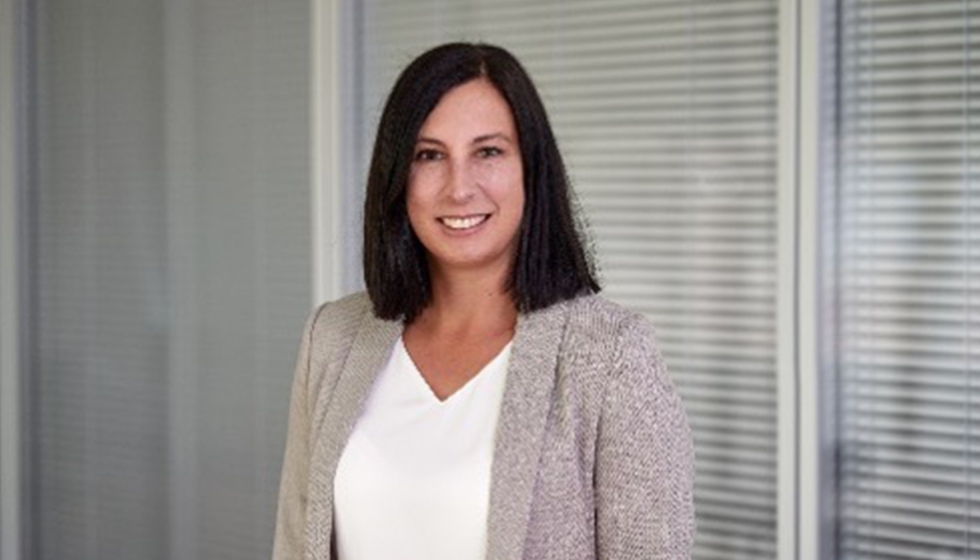