Combinando soluciones de diseño de materiales y rodamientos para mejorar la OEE y el TCO de las máquinas-herramienta
Mejorar el rendimiento y la robustez de los rodamientos del husillo principal es un factor clave para mejorar el rendimiento de la máquina-herramienta y reducir los costes de mantenimiento para hacer frente a la petición de los clientes de un mayor OEE y un menor TCO.
Además de la optimización del diseño, el rendimiento y la robustez de los rodamientos del husillo pueden verse muy afectados por el propio material. Vacrodur es un innovador material para rodamientos desarrollado por Schaeffler que permite a los fabricantes de máquinas-herramienta incrementar significativamente la capacidad de carga de sus husillos y ampliar enormemente su vida operativa incluso en condiciones extremadamente difíciles. Mecánica y térmicamente estable incluso por encima de los 400 °C, la vida nominal puede ser incrementada en un factor de 13.
En combinación con los rodamientos de diseño M de alto rendimiento para el husillo principal, puede utilizarse para aumentar el rendimiento o la fiabilidad. Aprovechando la mayor capacidad de carga en comparación con el acero estándar, se puede aumentar el rendimiento y la capacidad de carga del husillo y la productividad de la máquina herramienta.
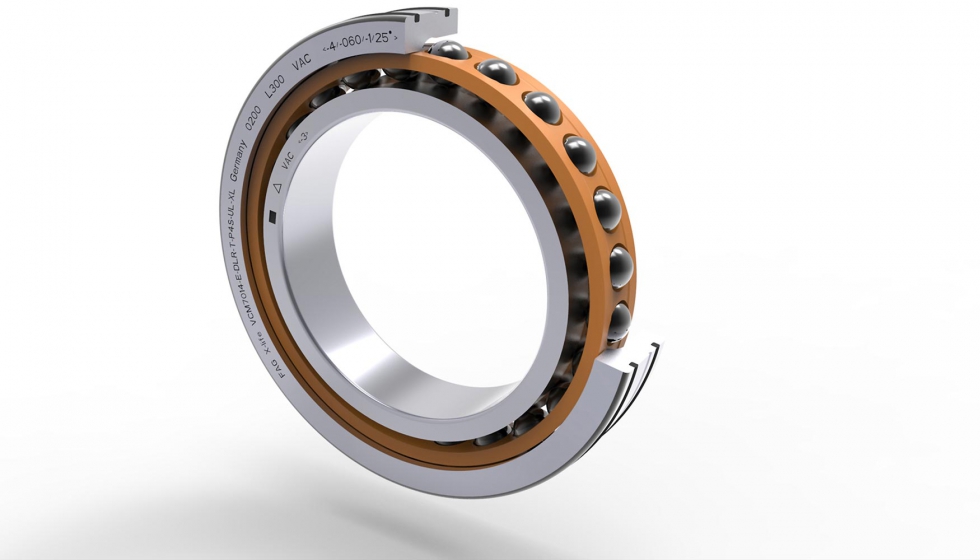
1. Introducción
En el caso de la tecnología de producción, el objetivo general de todo desarrollo es siempre la mejora de la productividad del equipo de producción, lo que puede expresarse como eficacia global del equipo (OEE). La OEE es el producto del factor de rendimiento (PF), el factor de disponibilidad (AF) y el factor de calidad (QF): 𝑂𝐸𝐸=𝑃𝐹 ∙𝐴𝐹 ∙𝑄𝐹
En cuanto a las herramientas mecánicas, el enfoque tradicional de la investigación siempre ha sido el aumento del rendimiento. Gracias al desarrollo continuo de los materiales de corte, la velocidad del husillo y las velocidades de avance, la velocidad de corte y la tasa de eliminación de material de las máquinas-herramienta han aumentado continuamente durante las últimas décadas.
El desarrollo actual se centra en la automatización. Para hacer frente al creciente coste de la mano de obra y permitir la producción sin tripulación, un número cada vez mayor de máquinas-herramienta están encadenadas y equipadas con robots de manipulación y almacenes para la manipulación automática de las piezas de trabajo para permitir un mecanizado completo y sin tripulación.
Para la eficacia de estos sistemas productivos, la fiabilidad es un factor más crucial que nunca. El tiempo de inactividad en los turnos no tripulados destruye la productividad y crea costos excesivos. Por consiguiente, la atención se centra en la fiabilidad de los componentes y la supervisión del estado.
Las estadísticas muestran que alrededor de un tercio del tiempo de inactividad de las máquinas-herramienta es causado por el husillo principal. Las investigaciones actuales indican que un buen 80% de todos los daños en el husillo que conducen a la falla de la máquina pueden ser rastreados hasta el soporte de los rodamientos del husillo, por lo que los rodamientos juegan un papel clave en el rendimiento y la disponibilidad de la máquina.
2. Velocidad, capacidad de carga y fiabilidad. Objetivos del conflicto
Hoy en día, los rodamientos de bolas de contacto angular de alta precisión son el tipo de rodamiento más importante para los husillos principales, razón por la cual se les denomina comúnmente ‘rodamientos para husillos’. Estos rodamientos permiten la combinación de cargas axiales y radiales. El punto de contacto permite altas velocidades debido a la baja fricción y puede compensar las diferencias de temperatura mejor que una línea de contacto. Para cumplir con los requisitos de precisión y rigidez, los rodamientos se llenan con la máxima cantidad de bolas y generalmente funcionan en condiciones de precarga.
La fuerza de guía y por lo tanto la fricción para las jaulas guiadas por bolas crece por cuadrado de la velocidad. Por lo tanto, las jaulas para los rodamientos de alta velocidad se hacen generalmente guiadas por el anillo exterior. El diseño de las jaulas para los rodamientos para husillos de FAG de Schaeffler se ha optimizado en los últimos años para reducir la fricción de deslizamiento entre la jaula y el anillo exterior y en las cavidades de la jaula. Además, el diseño se ha optimizado para reducir la tendencia a los ruidos de la jaula, un fenómeno común para las jaulas guiadas por el anillo exterior.
Dado que las dimensiones externas de los rodamientos para husillos están estandarizadas y vinculadas a la interfaz de la herramienta, el rendimiento de un rodamiento para husillos depende del diseño interno, la lubricación y los materiales. Desde el punto de vista de un diseñador de rodamientos, los requisitos de velocidad y carga son objetivos contradictorios. El diseño de los rodamientos es siempre un compromiso entre la posible capacidad de velocidad, la rigidez, la capacidad de carga y la robustez. Los principales parámetros de diseño son el tamaño y el complemento de la bola, la curvatura y el diseño de la jaula.
Todos los rodamientos de bolas de contacto angular se caracterizan por un movimiento combinado de giro y rodadura en el contacto de la pista de rodadura de la bola. La relación entre la magnitud del giro y el vector de rodadura en la zona de contacto se denomina comúnmente relación giro-rodadura. Las cargas radiales provocan diferencias en los ángulos de contacto y, en consecuencia, diferentes velocidades orbitales de las bolas.
Debido a las altas velocidades, las fuerzas de la masa tienen un impacto relevante en la distribución de la carga en los rodamientos del husillo principal. La fuerza centrífuga da lugar a diferentes ángulos de contacto en el anillo exterior y en el interior. Como resultado, la relación giro-rodillo y las diferencias en las velocidades orbitales aumentan significativamente y se convierten en factores limitantes para el funcionamiento del rodamiento. Una relación giro-rodillo demasiado alta crea una tensión excesiva en el lubricante en la zona de contacto y puede conducir a un desgaste excesivo debido a la falta de lubricación. Si las diferencias en la velocidad orbital son demasiado altas para ser compensadas por la jaula, las bolas experimentarán un movimiento de deslizamiento forzado, resultando en un desgaste prematuro o en la rotura de la jaula si la fricción adicional es demasiado alta.
Las bolas más pequeñas dan lugar a menores fuerzas centrífugas en la bola y, por tanto, a una menor relación giro-rodillo. El resultado es una menor fricción y una mayor capacidad de velocidad. Sin embargo, para tener suficiente holgura radial para hacer frente a las altas diferencias de temperatura en los husillos motorizados, deben elegirse ángulos de contacto más grandes. Esto hace que los rodamientos de bolas pequeños sean generalmente más sensibles a la desalineación. Las diferencias de temperatura tienen un gran impacto en la desalineación, lo que requiere un control estricto de las temperaturas de funcionamiento para utilizar rodamientos de bolas pequeños en disposiciones de precarga rígidas.
Las bolas más grandes producen una mayor capacidad de carga y reducen la sensibilidad a la desalineación y la temperatura. El tamaño de las bolas está limitado por la sección transversal del rodamiento, así como por el espacio necesario para las juntas y la jaula. Debido al mayor impacto de las fuerzas de la masa, la diferencia en
El ángulo de contacto y, en consecuencia, también los efectos de la relación giro-rotación y la excursión de la pelota aumentan con el tamaño de la misma, lo que limita la posible velocidad.
Una curvatura abierta de las pistas de carreras resulta en una elipse de contacto más pequeña. El resultado es un menor movimiento de deslizamiento, una menor fricción y, por tanto, una mayor capacidad de velocidad. Además, una curvatura abierta reduce el efecto de la inclinación a la cinemática. Esto hace que el rodamiento sea más robusto contra la inclinación y más adecuado para cargas combinadas. Además, el efecto de las tolerancias de las partes circundantes y la diferencia de temperatura se reduce, lo que hace que el rodamiento sea más adecuado para una disposición de precarga rígida. El precio es una mayor presión de contacto y, por tanto, una menor capacidad de carga.
La nueva serie de husillos de diseño M en calidad X-life está optimizada para los requisitos de velocidad y fuerza de los actuales husillos de alta velocidad para máquinas herramientas. El diseño interno combina la fricción minimizada y la capacidad de alta velocidad de los rodamientos para husillos de alta velocidad de bolas pequeñas de FAG en diseño HS y la capacidad de carga y la robustez de los rodamientos para husillos de alta velocidad de bolas grandes de FAG en diseño RS.
Las influencias externas debido a la interferencia entre el agujero y el rodamiento, las altas velocidades y los grandes gradientes de temperatura entre el eje y el alojamiento reducen el juego radial interno. La construcción optimizada X-life reduce en gran medida el aumento de la precarga del rodamiento en comparación con los rodamientos existentes de las series HS y RS, lo que hace que el rodamiento sea robusto y tolerante a las cambiantes condiciones de funcionamiento en los husillos de motor.
3. Material de primera calidad como solución
Una forma de aumentar aún más la capacidad de velocidad, la capacidad de carga y la robustez de los cojinetes después de optimizar el diseño es el uso de materiales de primera calidad. Un ejemplo bien conocido es el uso de bolas de cerámica que aumenta la capacidad de velocidad de los rodamientos mediante un mejor comportamiento tribológico y fuerzas de masa más bajas sin reducir la capacidad de carga y la vida útil.
Otra forma es utilizar materiales avanzados para los anillos. En el pasado, FAG ha establecido el estándar de mercado con el acero premium Cronidur, que combina una mayor capacidad de carga y un buen comportamiento en condiciones de fricción mixta. Hoy Vacrodur es el nuevo acero premium de Schaeffler para rodamientos de husillos. Este acero combina una gran dureza con una gran ductilidad. El resultado es una capacidad de carga aún mayor para una vida útil infinita del cojinete, combinada con una mejor resistencia al desgaste, que puede ser causado por la falta de fricción o contaminación, y el impacto estático.
Hay dos vías principales para aprovechar el rendimiento de este avanzado material:
- Aumentar el rendimiento del husillo aprovechando la mayor capacidad de carga
- Aumentar la fiabilidad del husillo aprovechando la mayor robustez contra la contaminación y la mala lubricación
3.1. Desarrollo de un nuevo material: enfoque de solución
Las siguientes propiedades de un material determinan la resistencia a la fatiga por rodadura y la resistencia al desgaste:
- Ductilidad y dureza
- Evitar las texturas
- La homogeneidad de la estructura
- La estabilidad térmica de la estructura
- Dureza
- Pureza material
Con estas propiedades, el rendimiento de un rodamiento puede verse significativamente influenciado (entre otras influencias por el diseño y la lubricación).
Ciertos elementos de aleación y tratamientos térmicos específicos pueden utilizarse para aumentar específicamente las propiedades individuales. El material más conocido para los rodamientos es el 100Cr6 con los componentes de aleación C (carbono) y Cr (cromo), otro material de alto rendimiento muy conocido es el Cronidur 30 con los componentes de aleación C, Cr, N (nitrógeno) y Mo (molibdeno).
El Cr (cromo) reduce la velocidad de enfriamiento, aumenta la resistencia al desgaste, la resistencia al calor, la resistencia a las incrustaciones y la resistencia a la tracción (formadores de carburo).
N (nitrógeno) estabiliza la austenita residual y así evita su descomposición. La austenita residual juega un papel crucial en la fatiga del material. La descomposición de la austenita residual cambia el tensor de tensión en la microestructura y esto es un factor importante en la formación de grietas. En Cronidur 30 el nitrógeno lleva a la formación de finos carbo-nitruros, lo que lleva a un aumento de la fuerza.
El Mo (molibdeno) mejora la capacidad de endurecimiento y también aumenta la resistencia a la tracción. Para la resistencia a la tracción, los carburos tienen un efecto positivo. Al igual que el cromo, el molibdeno asegura una buena formación de carburo.
La figura muestra un corte transversal a través de una estructura endurecida de 100Cr6. En parte se ven acumulaciones de carburo y áreas con austenita retenida.
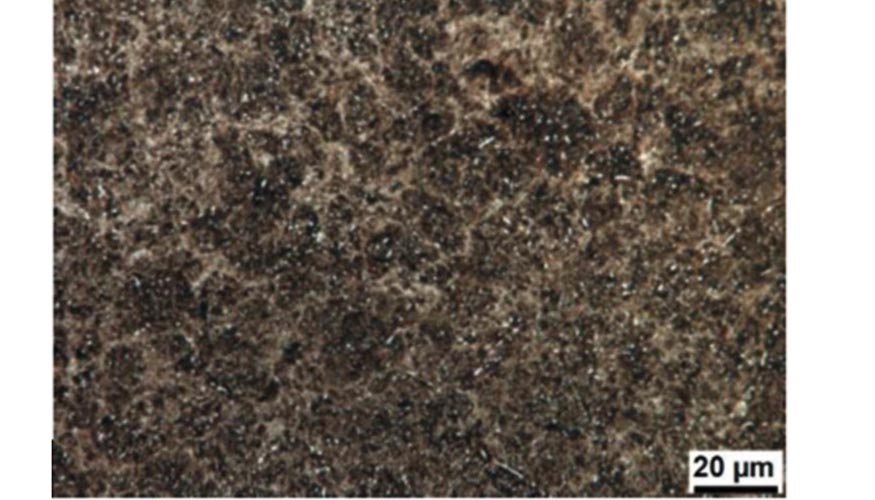
La base del nuevo material de rodamiento llamado Vacrodur es un material de partida pulvimetalúrgico. Mediante la producción pulvimetalúrgica del material de partida, se puede lograr una mejor homogeneidad de la estructura. Los componentes de aleación del material son C, V (vanadio), Cr, Mo y W (tungsteno). Sobre todo, el vanadio, pero también el tungsteno, proporcionan un mayor aumento de la resistencia a la tracción. También actúan como formadores de carburo como el cromo.
La figura muestra un corte transversal a través de la estructura endurecida de Vacrodur. El material de partida de la pulvimetalurgia conduce a una estructura muy homogénea. Mediante un proceso de endurecimiento en varias etapas, los carburos se forman de forma muy fina y uniforme. Esto da como resultado una combinación superior de propiedades de dureza, resistencia al desgaste, resistencia al calor y resistencia al templado.
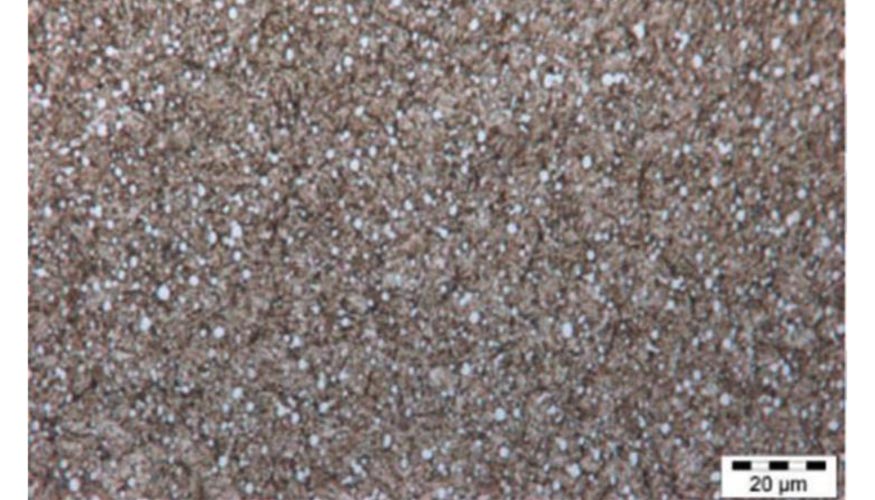
La siguiente visión general muestra las propiedades resultantes de los cojinetes híbridos, que consisten en 100Cr6, Cronidur 30 o Vacrodur y que se elaboraron experimentalmente durante la fase de desarrollo:
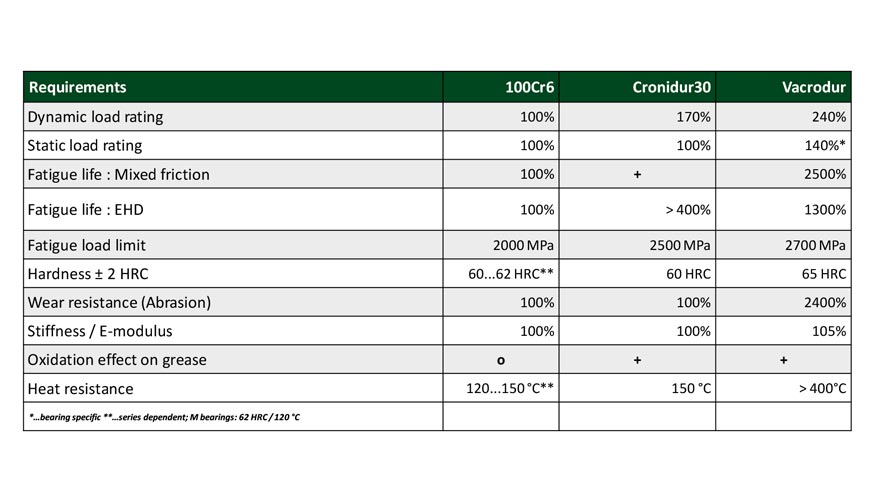
En particular, la alta resistencia al desgaste, la resistencia a la temperatura y el límite de carga de fatiga establecieron nuevos estándares para los rodamientos fabricados con Vacrodur. Abren posibilidades de aplicación y límites de aplicación completamente nuevos.
3.2. Validación
La validación se hace en bancos de prueba certificados. Se utilizan rodamientos de bolas de contacto angular híbridos para las pruebas. El número mínimo de muestras es de 24. La dirección de la carga es axial y la presión debe ser típicamente superior a 2.500 MPa. La velocidad del rodamiento de prueba depende de la viscosidad del lubricante utilizado. La viscosidad y la velocidad se establecen en función de la condición de lubricación deseada (relación de viscosidad), para alcanzar ya sea la fricción mixta o la lubricación completa EHD (lubricación elastohidrodinámica).
3.2.1. Vida del rodamiento
Las pruebas de vida de los cojinetes se realizaron en condiciones de plena lubricación EHD y de fricción mixta a presiones de contacto superiores a 2500 MPa.
Bajo la lubricación EHD los 42 rodamientos hechos de Vacrodur no mostraron ningún daño después de un tiempo de funcionamiento de 13 veces comparado con B10 de 100 Cr6 (B10 = tiempo de funcionamiento con 90% de probabilidad de supervivencia). En ese momento, todas las pruebas se terminaron sin la ruptura de un solo cojinete. El criterio para el fracaso es únicamente la fatiga del material. Ninguno de los anillos Vacrodur muestra tal fatiga al final de la prueba.
Bajo fricción mixta, las 24 muestras de prueba Vacrodur alcanzan 25 veces el tiempo de funcionamiento del material estándar comparado con el tiempo de funcionamiento del B10. Todos los experimentos con Vacrodur se terminaron en este momento sin la ruptura de un solo cojinete. Todos los anillos de los rodamientos hechos con Vacrodur tienen plena funcionalidad después de este tiempo de funcionamiento - sin picaduras, sin desgaste medible, sin fatiga.
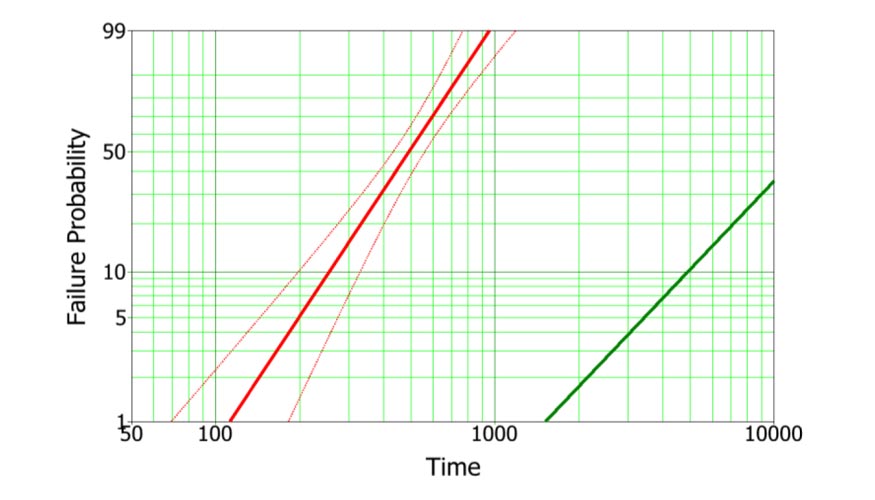
3.2.2. Capacidad de carga estática:
La capacidad de carga estática se asegura mediante pruebas de identificación. Aquí se presiona una bola de cerámica con diferentes presiones en una muestra de disco y se mide la deformación permanente. En este caso, se desea una deformación permanente de 1,9 micras. (-> Definición de la capacidad de carga estática en función del diámetro del elemento rodante = deformación residual de 0,5 * 0,01% del diámetro del elemento rodante). Entre las curvas características a la misma profundidad de impresión en función de la presión de contacto hay una relación de aproximadamente 1,16 entre 100 Cr 6 y Vacrodur. Para una deformación permanente de 1,9 µm esto significa una compresión a 100 Cr6 de aprox. 4850 MPa y para Vacrodur de aprox. 5650 MPa. La capacidad de carga estática de Vacrodur es, por lo tanto, un 40% más alta que la de un rodamiento de 100Cr6.
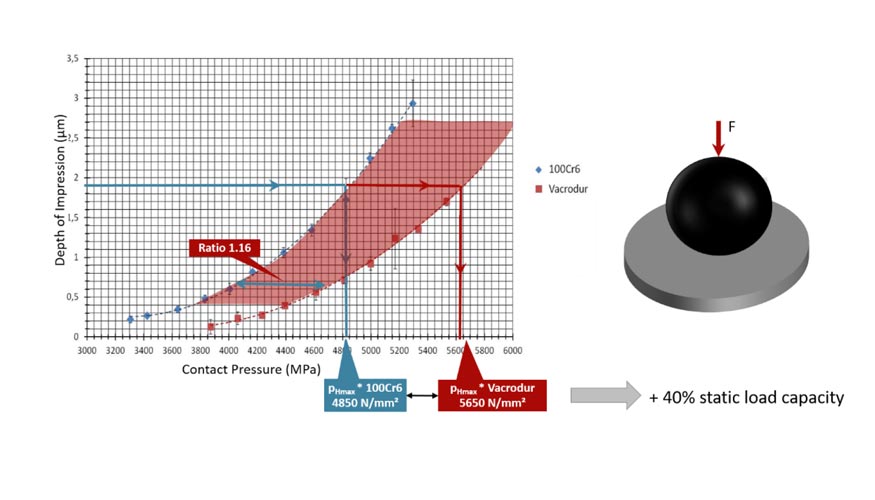
3.2.3. Resistencia al desgaste
La resistencia al desgaste desempeña un papel especialmente importante en la práctica, ya que la contaminación con partículas a menudo no puede evitarse completamente durante el período de uso. Para poder comparar los materiales en cuanto a su resistencia al vuelco de las partículas duras, deben crearse condiciones experimentales reproducibles. Las pruebas se realizan con rodamientos engrasados (tipo HCB7006) de diferentes materiales. Estos se engrasan con una cantidad estándar de grasa. La grasa se mezcla uniformemente con una cantidad definida de partículas duras minerales Al2O3. El tamaño típico de las partículas está entre 16 - 18 µm. Los rodamientos funcionan con una relación de velocidad de n × dm 1,6 millones de mm/min bajo una carga axial y radial adicional definida, después de que una distribución de grasa funciona hasta que la temperatura del rodamiento alcanza un límite de 70 °C.
En total, se probaron 4 rodamientos por cada prueba de anillo. Los rodamientos con anillos de 100 Cr 6 alcanzaron el límite de temperatura media de 70 °C después de 5 h, de forma similar a los rodamientos de Cronidur 30. Los rodamientos con anillos de Vacrodur alcanzaron el límite de temperatura después de más de 100 h de media. Esto demuestra que Vacrodur puede aumentar el tiempo de funcionamiento en estas condiciones por un factor de 20.
Otro método para probar la resistencia al desgaste es el ensayo tribológico FAG FE 8, que se lleva a cabo con un rodamiento axial de rodillos cilíndricos:
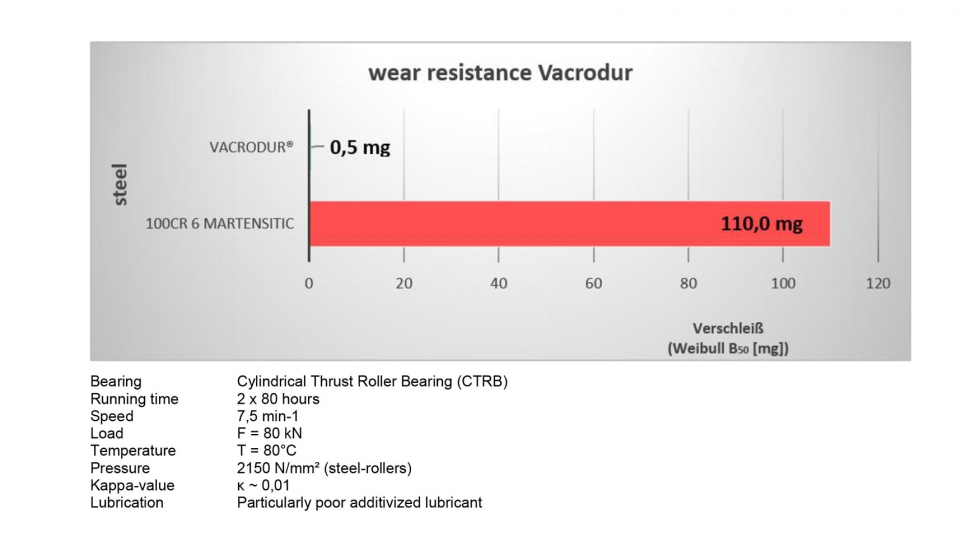
En este caso, el rodamiento axial de rodillos cilíndricos está equipado con rodillos estándar de acero para rodamientos. Después de un total de 160 horas de funcionamiento, se examina el desgaste de los anillos. Después de este tiempo de funcionamiento, se obtuvo una cantidad de desgaste de aproximadamente 0,5 mg con Vacrodur y aprox. 110 mg con 100 Cr 6. La superior resistencia al desgaste de Vacrodur es por lo tanto también confirmada en la prueba tribológica FE 8.
3.2.4. Pruebas de alta velocidad
En la prueba de alta velocidad, se comprueba el concepto global de un rodamiento de alta velocidad. Una vez más, el material del anillo juega un papel importante. En particular, el material de los anillos, el material de los elementos rodantes y el lubricante utilizado forman un sistema tribológico. La siguiente figura
muestra una prueba de alta velocidad de un cojinete híbrido hecho de Vacrodur en una prueba a varias velocidades hasta un índice de velocidad de n x dm = 3,3 millones de mm/min.
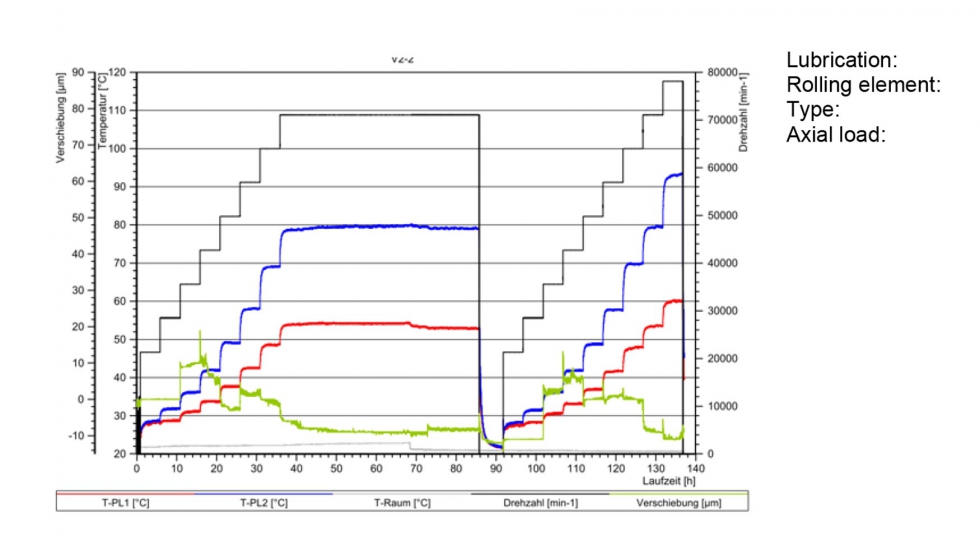
El criterio para la evaluación de este experimento es un perfil de temperatura estable. El perfil de temperatura, medido directamente en el anillo exterior del rodamiento (línea azul) debe seguir la forma de la curva de velocidad (línea negra) en la medida de lo posible. Un comportamiento de temperatura estable térmicamente indica un contacto de rodadura tribológicamente estable y robusto. El perfil de temperatura muestra que la combinación de materiales Vacrodur / cerámica es ideal para los rodamientos de alta velocidad.
4. Más potencia de husillo
Una mirada a los datos básicos de los rodamientos muestra que los rodamientos de husillo híbridos en diseño M tienen una mayor capacidad de carga y velocidades límite en comparación con los rodamientos de husillo de alta velocidad de bolas pequeñas en diseño HS. En el caso de Vacrodur, la capacidad de carga aumenta incluso más allá del nivel del diseño Cronidur y RS. Así, Vacrodur permite aumentar el rendimiento de los husillos existentes.
Hoy en día, se alcanzan las máximas tasas de eliminación de material en el mecanizado de alto rendimiento del aluminio. Las condiciones de carga típicas se caracterizan por herramientas largas y altas fuerzas radiales incluso a la máxima velocidad. La potencia del motor instalado está aumentando constantemente en los últimos años. Como consecuencia, la disposición de los rodamientos debe ser capaz de soportar cargas radiales cada vez mayores. El posible aumento de rendimiento puede demostrarse comparando las posibles cargas de un husillo típico para esta aplicación.
En estas aplicaciones, las diferencias de temperatura entre el eje y el alojamiento pueden alcanzar fácilmente los 25 K debido a la alta potencia del motor. Por esta razón, para los rodamientos de husillo de alta velocidad de bolas pequeñas con un ángulo de contacto nominal de 25º (‘E’) se debe elegir un juego radial suficiente para evitar la precarga radial en funcionamiento.
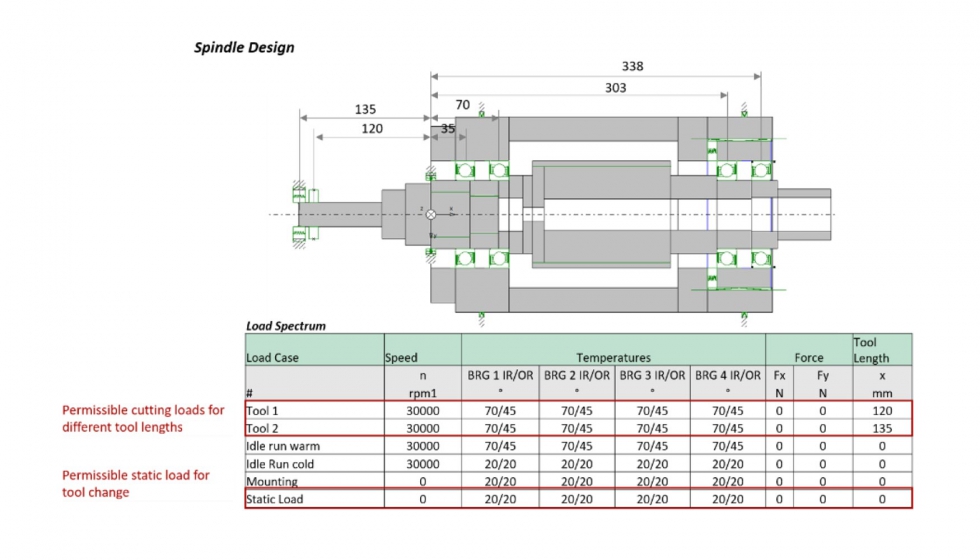
Dado que un ángulo de contacto mayor aumenta la sensibilidad de la cinemática del rodamiento al inclinarse, la capacidad de carga para las cargas radiales con un brazo en voladizo elevado está limitada por la cinemática, no por la presión de contacto. Por lo tanto, la carga permisible es la misma cuando se compara los rodamientos híbridos de bolas pequeños HC con los rodamientos híbridos de bolas pequeños con anillos Cronidur XC. La ventaja de un mayor límite de carga de fatiga de Cronidur no puede utilizarse, ya que los altos valores de excursión de las bolas y de la relación entre el giro y el rodamiento indican el riesgo de un fallo prematuro del rodamiento.
Incluso cuando se utilizan rodamientos HCM con un ángulo de contacto nominal de 25º, la carga admisible sólo aumenta ligeramente. Sin embargo, debido al diseño interno optimizado, los rodamientos HCM con un ángulo de contacto nominal de 17º (‘C’) presentan aproximadamente el mismo juego radial que los rodamientos HC con un ángulo de contacto nominal de 25 grados y, por tanto, pueden utilizarse como alternativa.
Gracias al menor ángulo de contacto, se reduce la influencia de la inclinación en la cinemática del rodamiento. Para las longitudes de herramienta dadas, la carga permisible está ahora limitada por la presión de contacto, mientras que la cinemática se mantiene dentro de límites estables. Así, al cambiar del diseño de bola pequeña HC con ángulo de contacto ‘E’ al diseño de bola mediana HCM con ángulo de contacto ‘C’, la carga permisible puede aumentarse en un factor de 3.
Ahora, también es posible alcanzar una mayor mejora aprovechando el mayor límite de carga de fatiga de Vacrodur. En el ejemplo de aplicación dado, la carga admisible puede aumentarse en un factor de 7 mediante el uso del diseño de bola mediana VCM con ángulo de contacto ‘C’ en comparación con el diseño de bola pequeña HC o XC con ángulo de contacto ‘E’.
Por supuesto, el menor ángulo de contacto reduce la capacidad de carga axial. Sin embargo, en el ejemplo dado, la capacidad de carga axial es principalmente importante para el cambio de herramientas.
En comparación con el rodamiento de bolas pequeñas HC y XC con ángulo de contacto ‘C’, el rodamiento HCM con ángulo de contacto ‘E’ tiene aproximadamente la misma capacidad de carga axial. En el caso del rodamiento HCM con ángulo de contacto ‘C’, la carga admisible para el cambio de herramienta se reduce. Esto puede compensarse aprovechando la capacidad de carga axial un 40% más alta del material Vacrodur.
Obviamente, el posible aumento del rendimiento utilizando Vacrodur depende de la aplicación específica. La resistencia del material sólo puede ser utilizada después de que la cinemática de los rodamientos se optimice y se mantenga dentro de los límites tolerables. Sin embargo, combinando el avanzado diseño interno de la serie M con las propiedades del material Vacrodur es posible alcanzar un impresionante aumento del rendimiento, especialmente para combinaciones de altas velocidades y cargas radiales como las que se pueden encontrar en los modernos husillos de alto rendimiento.
5. Mayor fiabilidad
Otra forma de aprovechar las propiedades del material de Vacrodur es aprovechar la mayor robustez del material en caso de fricción mixta y contaminación, lo que puede aumentar considerablemente la fiabilidad de los husillos principales y ayuda a evitar fallos prematuros.
Para funcionar a altas velocidades, los cojinetes del husillo principal requieren una alta precisión de las piezas de acoplamiento junto con temperaturas controladas, un entorno limpio y una buena lubricación. Por otro lado, el espacio de trabajo está lleno de virutas, polvo y fluidos lubricantes. Además, hay un impacto de calor por las pérdidas del motor y la energía de deformación en el corte que causa tensión en el lubricante.
Por lo tanto, los constructores de husillos principales se esfuerzan mucho en proteger los rodamientos contra la contaminación externa mediante sistemas avanzados de laberinto de sellado, mantienen las diferencias de temperatura constantes mediante una refrigeración activa y mantienen la lubricación estable utilizando grasa de alto rendimiento o controlando la distribución de la presión en el husillo y filtrando el aire para la lubricación con aire de aceite.
Aun así, incluso para los diseños probados, hay un cierto porcentaje de husillo que falla prematuramente, lo que causa altos costos de garantía para el productor de la máquina-herramienta o el fabricante del husillo. En algunos casos, el motivo del fallo puede atribuirse a condiciones específicas de la aplicación, que pueden ser el material específico de la pieza de trabajo, fluidos de corte agresivos o contaminación en el sistema de lubricación, y el fallo puede evitarse con medidas correctivas. Sin embargo, especialmente si la perturbación sólo se produce de manera intermitente, es difícil rastrear la razón original del fallo.
Por otra parte, los requisitos de fiabilidad de las máquinas-herramienta están aumentando, especialmente debido al reciente desarrollo debido a la carga automatizada de las piezas de trabajo y a la producción encadenada. Para los clientes finales, la fiabilidad y la disponibilidad adquieren mayor relevancia, para los productores de máquinas herramienta, la garantía se convierte en un argumento de marketing.
Las estadísticas muestran que alrededor de un tercio del tiempo de inactividad de la máquina está relacionado con el sistema de husillo principal. La mayor parte está relacionada con los rodamientos. Las razones típicas de fallo pueden ser la sobrecarga, la contaminación, la falta de lubricación y el desgaste.
Como se muestra, Vacrodur ha demostrado una enorme ventaja en comparación con el acero estándar en caso de problemas de lubricación y contaminación. En caso de problemas ocasionales de lubricación, por ejemplo, por temperaturas temporalmente más altas o fallos en el sistema de lubricación, el daño en la pista de rodadura causado por el contacto directo entre la bola y la pista de rodadura se reduce. Debido al desgaste significativamente menor, la precisión del rodamiento se mantiene y las propiedades de rendimiento no se ven afectadas.
Además, en caso de contaminación, por ejemplo, causada por la contaminación externa causada por un mal funcionamiento del sistema de sellado o por la contaminación ocasional del aire de lubricación, el daño en la pista de rodadura del rodamiento se reduce gracias a la mayor dureza y resistencia al desgaste de Vacrodur.
Por lo tanto, para un diseño de husillo probado, al mantener las condiciones de funcionamiento y los límites de carga, es posible mejorar la fiabilidad y evitar fallos prematuros al cambiar el material del anillo a Vacrodur. Esto puede conducir a un enorme ahorro de costes. Los costos por el tiempo de inactividad por fallo del husillo pueden alcanzar fácilmente varios miles de euros por máquina cada año. Si cada segundo de estas fallas es eliminado por Vacrodur, los costos más altos de los rodamientos se compensan con creces.
Referencias
(1) Rudy, Dietmar / Claus, Sven / Dr. Pausch, Michael: Entwicklung eines neuen Materials für Wälzlager; Vortrag 13. VDI- Fachtagung Gleit- und Wälzlagerungen; 05./06.06.2019, Schweinfurt
(2) O.V.: SP1 Super Precision Bearings; © Schaeffler Technologies AG & Co. KG, Issued: 2016, June
(3) O.V.: SSD40 X-life High-Speed Spindle Bearings M; © Schaeffler Technologies AG & Co. KG, Issued: 2017, October
(4) O.V.: SSD41 Vacrodur; © Schaeffler Technologies AG & Co. KG, Issued: 2017, September
(5) Dr. Voll, Martin: Neue Konstruktionslösungen mit Vacrodur – Lagern; Vortrag Seminar Gestaltung von Spindellagersystemen, Aachen, 22.06.2017