Schaeffler mostrará en EMO2019 con SpindleSense cómo reducir los fallos de las máquinas
Durante el proceso de fresado, la combinación de elevadas cargas radiales, herramientas que sobresalgan mucho y altas velocidades que afecten, en particular, al rodamiento para cabezal montado cerca de la herramienta, generará cargas importantes y condiciones cinemáticas desfavorables. Estas cargas desfavorables, y a veces incluso inadmisibles, se producen porque hasta ahora los operadores carecían de una herramienta adecuada que permitiera monitorizar las cargas límite de los rodamientos para cabezal. Schaeffler resuelve este problema con el innovador sistema de monitorización SpindleSense.
Listos para la producción en serie
Coincidiendo con la EMO 2019, los clientes podrán disponer de las primeras unidades de anillo de sensores SRS, listas para la producción en serie, que incluyen anillos de medición radial y axial con un diámetro interior de 70 mm, para llevar a cabo un test práctico. Para finales de este año estarán disponibles otros tamaños con diámetro interior de 80 y 100 mm. La anchura uniforme es de 16 mm. El volumen de suministro también incluye el Setup-Service-Tool SST (herramienta de instalación), que permite ajustar los parámetros del SpindleSense y ponerlo en servicio.
El sistema de sensores integrado en el rodamiento para cabezal mide el desplazamiento del eje del husillo bajo carga con alta resolución en cinco direcciones, tres de tipo traslativo y dos de tipo rotativo. Si las deformaciones registradas en los elementos rodantes superan un valor límite específico, el anillo de sensores emitirá una señal eléctrica de aviso a la unidad de mando de la máquina. Se establece individualmente un valor límite para cada tipo de cabezal y máquina. Este valor límite se basa en una evaluación de los parámetros relevantes para el funcionamiento del rodamiento, como la presión, la relación de rodadura y agujero, y el juego del elemento rodante en la jaula, a los que se aplican los conocimientos sobre rodamientos que Schaeffler ha adquirido a lo largo de los años.
Software integrado en el anillo de sensores con información sobre rodamientos
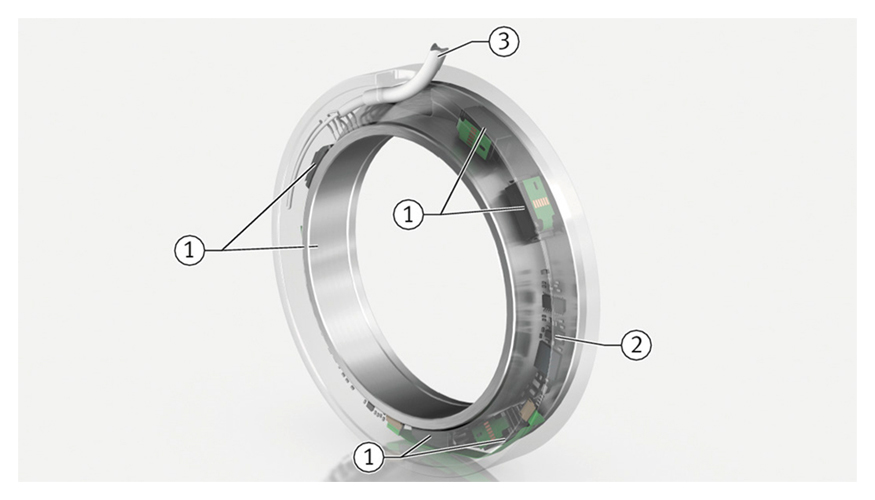
El software completo y todos los algoritmos necesarios están integrados en el anillo de sensores de una anchura de 16 mm, con lo cual el sistema no requerirá otros componentes adicionales. El sistema funciona a nivel local y emite una señal individual de alarma a la unidad de mando de la máquina que posibilita las siguientes aplicaciones:
- Detectar una colisión: el sistema de sensores puede detectar una sobrecarga de una salida digital en un intervalo de 2 ms. La rápida desconexión de la máquina permite minimizar o prevenir graves daños consecutivos.
- Protección a largo plazo de los cabezales de máquinas-herramienta: en la aplicación práctica, las sobrecargas mecánicas permanentes de los rodamientos para cabezal no se suelen detectar. En cambio, SpindleSense emite inmediatamente una señal de advertencia si se ha ajustado de manera adecuada el parámetro de sobrecarga correspondiente. El operador podrá modificar el programa de mecanizado en la fase inicial, después de la primera pieza, y reducir la carga del cabezal montando una nueva herramienta, cambiando los valores de corte e incluso empleando un tipo de herramienta más indicado. Con estas medidas conseguiría reducir las cargas punta, reducir la cantidad de las mismas y beneficiarse de una mayor duración de vida útil del cabezal, así como de menores períodos de inactividad de la máquina-herramienta. En definitiva, el operador tendrá más tiempo de producción y menos costes de reparación.
Para la transferencia de los valores medidos hay dos opciones. La variante C-A0 emite señales de alarma cuando se hayan alcanzado los valores límite establecidos individualmente para la carga y la cinemática del rodamiento. La variante C-A1 transmite los valores de los desplazamientos radiales y axiales medidos, incluyendo las inclinaciones a través del bus CAN. Con estos valores de desplazamiento, los fabricantes de máquinas-herramienta y de cabezales pueden desarrollar herramientas de análisis para optimizar la ocupación de los cabezales, visualizando, por ejemplo, el espectro de deformación medido por el anillo de sensores como espectro de carga. Así, el operador de la máquina conocerá por primera vez con exactitud el porcentaje con que podrá cargar mecánicamente los cabezales durante el proceso de mecanización. Ahora podrá modificar aún con mayor precisión este proceso de mecanización de la máquina por lo que respecta a la ocupación y la duración de vida útil. A pesar de la carga máxima del cabezal, se evitarán sobrecargas perjudiciales. Gracias a un funcionamiento seguro en el rango límite, el operador aumentará la productividad de la máquina, se beneficiará de una mayor duración de vida útil del cabezal y de una menor cantidad de fallos del mismo.
Otra aplicación de los desplazamientos medidos a través del bus CAN consiste en utilizarlos para la compensación del punto cero. Ello permitirá producir la misma calidad con mayores valores de corte, o producir una mayor calidad con valores de corte sin modificar. Del mismo modo, la monitorización del desplazamiento máximo se puede utilizar para controlar la calidad.
Sistema de sobrecarga electrónico versus sistema mecánico
En comparación con los sistemas mecánicos de sobrecarga pasiva, SpindleSense de Schaeffler no solo representa una protección del cabezal en caso de colisión, sino que también es un sistema revolucionario para maximizar con seguridad la ocupación del cabezal. Los fabricantes de maquinaria pueden ofrecer por primera vez a sus clientes una herramienta altamente eficaz para aumentar la productividad, la disponibilidad y la calidad de las máquinas.