Se prevé que para el año 2020 circulen por las calles y las carreteras de Alemania un millón de vehículos eléctricos
B&R, en el banco de pruebas
El recorrido que un automóvil eléctrico puede realizar con cada carga de su batería es posiblemente el factor más decisivo en su aceptación entre los consumidores. Esto hace que las baterías recargables de iones de litio sean un elemento clave de los conceptos de electromovilidad en todo el mundo. Cada vez más fabricantes de vehículos eléctricos confían en las plataformas de prueba y simulación de baterías de Gustav Klein para diseñar y optimizar sus soluciones de baterías. Ahora, la avanzada tecnología B&R ha ayudado a la compañía a hacer que sus sistemas sean aún más fáciles de desarrollar, utilizar y mantener.
Alemania ha lanzado el guante para sus compañías automotrices. Hacia el año 2020, está previsto que un millón de vehículos eléctricos circulen por las calles y las carreteras de la nación. El 1 de enero de 2017, el total era de 34 022 vehículos. Entre los escándalos del diésel, las inminentes prohibiciones del tráfico interno en las ciudades y las cada vez más importantes restricciones de los motores de combustión en China y en otros lugres, los fabricantes están recibiendo todo tipo de presiones para pasarse lo antes posible a los vehículos eléctricos.
“Actualmente las cosas están adquiriendo un auténtico impulso”, confirma Bernhard Rill, jefe de ventas y marketing de Gustav Klein. A juzgar por el reciente aumento del interés entre los fabricantes de automóviles por los sistemas de prueba y simulación que produce su empresa, parece que Rill tiene razón. Los ingenieros automotrices utilizan el sistema de prueba de alimentación de Gustav Klein para evaluar el comportamiento preciso de los sistemas eléctricos de sus vehículos y actuadores conectados bajo unas condiciones de suministro de energía claramente definidas y repetibles. “Esto no se puede hacer con una batería real”—explica Rill— “debido a las constantes fluctuaciones en el nivel de carga”. Otros usos del sistema de prueba de alimentación incluyen las pruebas de componentes realizadas durante la producción de baterías y vehículos, o la identificación de la fuente de alimentación óptima para vehículos eléctricos de nuevo diseño.
Ello resulta especialmente sencillo con los sistemas de prueba programables de Gustav Klein. Las variantes multicanal están disponibles con un bus de continua interno que permite combinarlos según convenga. Ello permite, por ejemplo, realizar una descarga controlada en un canal y utilizar la potencia liberada para cargar una batería en el segundo canal. Esto simplifica la ejecución de los ciclos de carga, al mismo tiempo que se reduce el consumo energético. “Para simular con precisión el comportamiento de la batería, se necesita una velocidad de respuesta muy rápida”, explica Rill. “Nuestros sistemas pasan de -900 a +900 amperios en solo 1,2 milisegundos, con una transición perfecta entre la carga y la salida”. Los sistemas actuales pueden ofrecer una salida de hasta 1.000 voltios o 1.000 amperios (una capacidad de hasta 500 kilovatios por dispositivo).
La variedad de productos exige un cambio estratégico
Han pasado quince años desde que Gustav Klein completó los primeros pedidos de sus sistemas de prueba y simulación de baterías. Hoy en día, los productos de la empresa salen de Schongau, en el sur de Baviera, hasta las instalaciones de I+D y de producción de casi todos los principales fabricantes de automóviles del mundo. No obstante, cuanto más generalizado es el uso, más variados son los requisitos. “Tenemos una enorme variedad de configuraciones del sistema que se utilizan en condiciones radicalmente variables”, comenta Jörg Umbreit, jefe de I+D de Gustav Klein. “En consecuencia, tenemos que admitir un número creciente de interfaces y gestionar una mayor variación del producto”.
Ello implica algunas importantes exigencias para el sistema de control. Los lazos de control deben ejecutarse en el intervalo de microsegundos para lograr las velocidades de respuesta necesarias. Al mismo tiempo, los canales deben controlarse con una perfecta sincronización para permitir el funcionamiento paralelo. “La necesidad de transferir grandes volúmenes de datos aún complica más el asunto”, añade Umbreit.
En la primera fase de la evaluación, Gustav Klein analizó a cinco conocidos proveedores de controles y B&R fue el primer clasificado. “Lo que nos convenció fue el conjunto en general”, informa Umbreit. “Nos impresionó especialmente el rendimiento y la flexibilidad del sistema, el entorno de programación universal y la calidad de la asistencia que recibimos. Y a nivel personal, todo encajó desde el principio”.
Arquitectura de control flexible
En 2014, los ingenieros de Gustav Klein empezaron a desarrollar una nueva arquitectura de control para la tercera generación de su sistema de prueba de alimentación. Para la plataforma de control, Gustav Klein seleccionó un módulo CPU montado en un carril del sistema X20 de B&R. “Pudimos utilizar un control X20 con relativamente poca memoria”, comenta Umbreit. “A medida que aumentan los requisitos, la adaptabilidad de la solución de B&R nos permite actualizar fácilmente a un control más potente sin necesidad de realizar ningún cambio en el software”.
La nueva arquitectura también permite a Gustav Klein adaptarse más fácilmente a los requisitos de interfaces de sus clientes. Con el módulo CPU puede utilizarse una serie de módulos de comunicaciones X20.
El sistema de control se utiliza con una pantalla de terminal Power Panel T30 remota. “Dado que la aplicación de HMI también se ejecuta en el módulo CPU montado en un carril, podemos entregar el sistema sin pantalla si es necesario”, comenta Rill. “Gracias a ello podemos seguir el ritmo de los usuarios, que cada vez más utilizan sus sistemas a través del acceso remoto”. En cualquier caso, las interfaces de usuario son idénticas y solo deben programarse una vez.
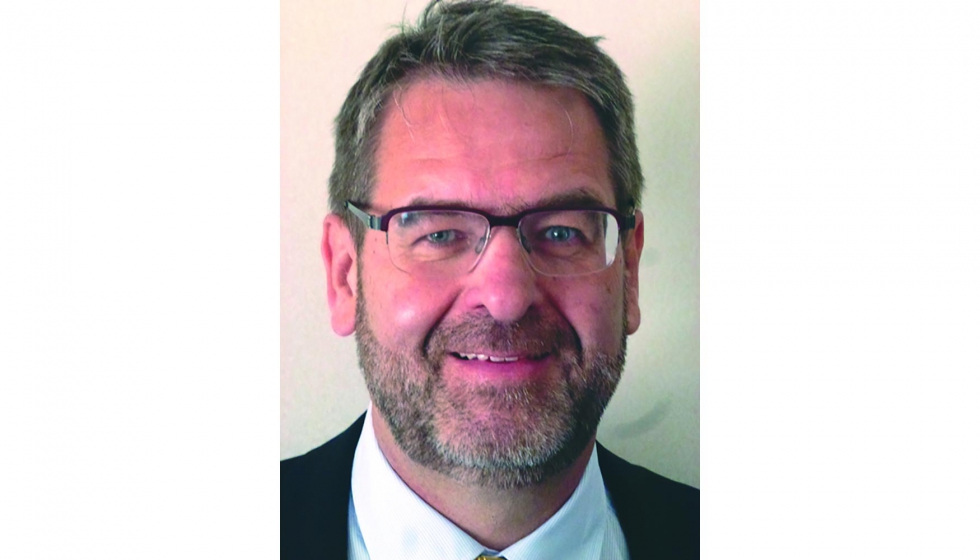
Bernhard Rill, jefe de Ventas y Marketing, Gustav Klein: “Trabajar con B&R siempre resulta productivo, incluso cuando les planteamos sugerencias o preguntas complejas. Gracias a B&R, ahora disponemos de un sistema de automatización consistente, flexible y adaptable. El tiempo y el coste de integrar la seguridad, el control y la funcionalidad de HMI se ha reducido considerablemente”
Un proyecto de software, un entorno de ingeniería
“Uno de los aspectos más destacados de la solución de B&R es sin duda el entorno de ingeniería, donde pudimos crear la aplicación de HMI y el software de control, todo en el mismo proyecto”. Y lo mismo puede decirse de la tecnología de seguridad integrada, por lo que Gustav Klein también decidió sustituir su hardware de seguridad independiente con la tecnología de seguridad integrada X20. Esa decisión simplificó la ingeniería considerablemente.
El cambio a la tecnología de B&R aportó también unas apreciables mejoras en lo relativo a mantenimiento y administración de variantes. Actualmente Gustav Klein puede administrar todo su sistema de prueba, incluidas todas las opciones y ampliaciones futuras, en un mismo proyecto de software. “Basta con desactivar en el software lo que no esté instalado”, explica Umbreit. “De este modo, solo tenemos una aplicación de software para probar y mantener para cada lanzamiento”.
Los comentarios de los usuarios acerca de la nueva tecnología de control y HMI han sido muy positivos, y por ello Gustav Klein tiene previsto trasladar la solución de HMI a su mayor grupo de productos: sus sistemas de suministro de energía, que incluyen módulos UPS y variadores de red.