Schaeffler integra la tecnología de sensores en los rodamientos para cabezal
Schaeffler ha desarrollado un sistema revolucionario para maximizar la eficiencia General (Overall Equipment Effectiveness, OEE) de las máquinas-herramienta, una nueva gama de sensores para la monitorización del cabezal que están integrados en los propios rodamientos. Por primera vez, los fabricantes de máquinas pueden ofrecer a sus clientes un instrumento altamente efectivo y fácil de usar para aumentar la disponibilidad, la productividad y la calidad de la máquina. El uso de este sistema reducirá la frecuencia de los fallos mientras se prolonga simultáneamente la vida útil del cabezal.
La mayor parte de los fallos de las máquinas-herramienta se debe a los cabezales defectuosos y, en particular, a los daños de los rodamientos producidos por colisiones y sobrecargas permanentes sin detectar. Por ejemplo, la colisión de la herramienta con la pieza a mecanizar puede dañar el rodamiento y otros componentes del cabezal. Durante el proceso de fresado, la combinación de elevadas cargas radiales, herramientas que sobresalgan mucho y altas velocidades que afecten, en particular, al rodamiento para cabezal montado cerca de la herramienta, generará cargas importantes y condiciones cinemáticas desfavorables. En casos extremos, se pueden producir fallos de los rodamientos a corto plazo. En este contexto, los ingenieros de Schaeffler han desarrollado un sistema cuyo objetivo es reducir los fallos de los cabezales y que posibilita una desconexión muy rápida del cabezal en situaciones de colisión. Además, el sistema permite al operador de la máquina detectar las condiciones desfavorables de funcionamiento y modificar el proceso de mecanizado de manera específica.
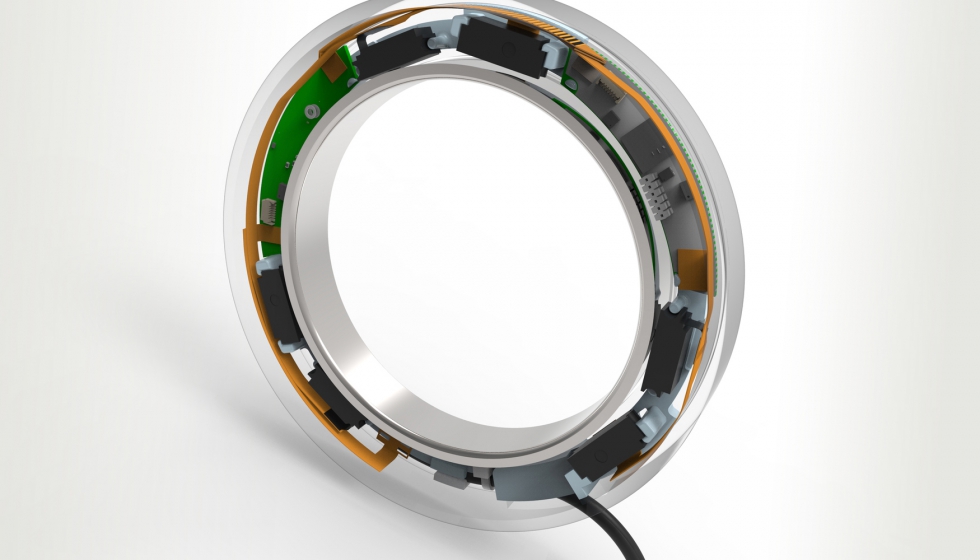
El nuevo sistema de sensores que se ha desarrollado específicamente para esta aplicación mide el desplazamiento del eje del cabezal bajo carga con alta resolución en cinco direcciones, tres de tipo traslativo y dos de tipo rotativo.
Desplazamiento del cabezal para medir la carga en la zona de contacto
El nuevo sistema de sensores que se ha desarrollado específicamente para esta aplicación mide el desplazamiento del eje del cabezal bajo carga con alta resolución en cinco direcciones, tres de tipo traslativo y dos de tipo rotativo. Como ventaja adicional, cabe destacar que gracias a nuestro know-how sobre rodamientos, las magnitudes relevantes del funcionamiento, como la presión, la relación de rodadura y agujero y el juego de jaulas con alojamiento de elementos rodantes, son claramente predecibles. Si las deformaciones registradas en los elementos rodantes superan un valor límite específico, el anillo de sensores emitirá una señal eléctrica de aviso a la unidad de mando de la máquina. Se establece individualmente un valor límite para cada tipo de cabezal y máquina. También se puede determinar el valor límite individualmente para otros componentes de accionamiento cuyo límite de carga sea inferior al del cabezal y cuya carga esté en correlación con la de éste.
Una propiedad específica en la época del cloud computing
El software completo y todos los algoritmos necesarios están integrados en el sistema de sensores, con lo cual el sistema no requerirá otros componentes adicionales. El sistema funciona a nivel local y emite una señal individual de alarma a la unidad de mando de la máquina que posibilita las siguientes aplicaciones:
- Detectar una colisión: el sistema de sensores puede detectar una sobrecarga de una salida digital en un intervalo de 2 ms. La rápida desconexión de la máquina permite minimizar o prevenir graves daños.
- Protección a largo plazo de los cabezales de máquinas-herramienta: en la aplicación práctica, las sobrecargas mecánicas permanentes de los rodamientos para cabezal no se suelen detectar inmediatamente, como por ejemplo, en el proceso de desbaste con una herramienta desgastada. Si en este caso o en un caso parecido el sistema emite una señal de alarma, el operador podrá modificar el programa de mecanizado en la fase inicial, después de la primera pieza, y reducir la carga del husillo montando una nueva herramienta, cambiando los valores de corte e incluso empleando un tipo de herramienta más indicado. Con estas medidas conseguiría reducir las cargas punta, reducir la cantidad de las mismas y beneficiarse de una mayor duración de vida útil del cabezal, así como de menores períodos de inactividad de la máquina-herramienta. En definitiva, el operador tendrá más tiempo de producción y menos costes de reparación.
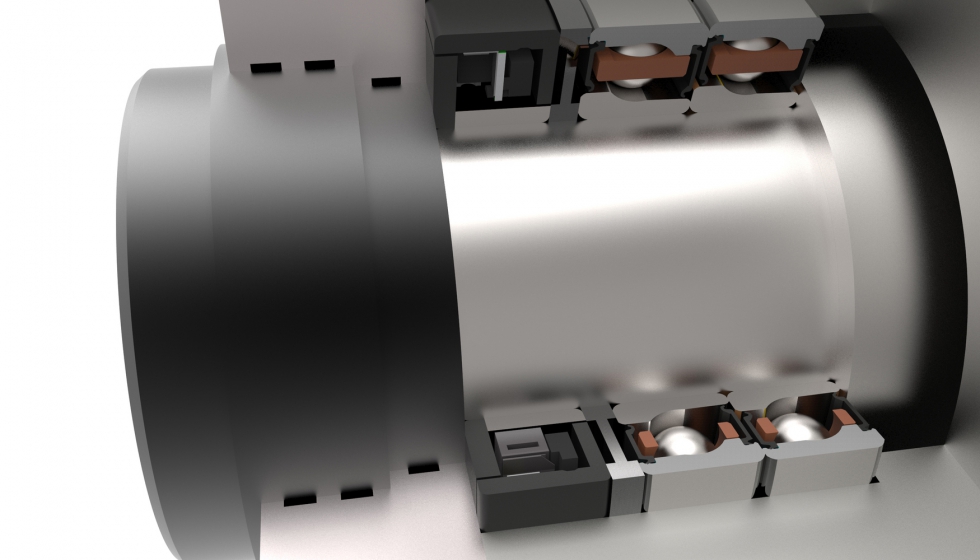
La medición del desplazamiento mediante el anillo de sensores y la monitorización integrada de la carga están en fase previa de desarrollo a la producción en serie. Ya hay un primer tamaño disponible para que los clientes puedan llevar a cabo ensayos prácticos. Asimismo, actualmente los ingenieros de Schaeffler desarrollan una nueva herramienta de análisis para optimizar la ocupación del husillo. Con este sistema, no solo se establecerá un valor límite, sino que además se visualizará el conjunto de deformaciones registradas por el anillo de sensores durante el proceso de mecanizado en el eje temporal. El operador de la máquina sabrá por primera vez con gran precisión el porcentaje de carga mecánica del cabezal durante los diferentes procesos de mecanizado. Ello le permitirá modificar con mayor precisión el proceso de mecanizado de la máquina por lo que respecta a la ocupación y la duración de vida útil. Así se podrán evitar sobrecargas perjudiciales pese a la alta ocupación del cabezal. Gracias a un funcionamiento seguro en el rango límite, el operador aumentará la productividad de la máquina, se beneficiará de una mayor duración de vida útil del husillo y de una menor cantidad de fallos del mismo.