El nuevo equipo de acabado para las etiquetas adhesivas en series cortas
Las máquinas Omega Digicon están concebidas con un equipamiento completo y con la máxima automatización posible para conseguir el ajuste y las operaciones de acabado con el mínimo desperdicio de material. La importancia de esta característica es fundamental en las producciones cortas, como la impresión digital, pues no únicamente se reduce el material necesario para el ajuste del equipo, sino que también se reducen los consumibles necesarios para la impresión del trabajo.
Si en un equipo convencional se pueden necesitar un promedio de 300 metros de material para ajustar una unidad de estampado en caliente (‘hot foil’), un barniz a registro, el cuerpo de troquel, corte y rebobinado final en subbobinas, en la Omega Digicon sólo se necesitan unos 10 metros para toda estas operaciones. El ahorro de los 300 metros por orden de trabajo, supone entre material y consumibles un promedio cercano a los 100 euros por pedido. En un análisis anual y si se disponen de unas 400 órdenes de trabajo al mes con estas características, el ahorro puede suponer alrededor de los 500.000 euros al año. Es por ello que la adquisición de una Omega Digicon debe ser analizada más como un ahorro en la producción y no únicamente como una inversión.
El equipo es utilizado por muchos clientes para realizar reimpresiones o acabados de series muy cortas, minimizando el desperdicio de material, y permitiendo la personificación adicional de estas series.
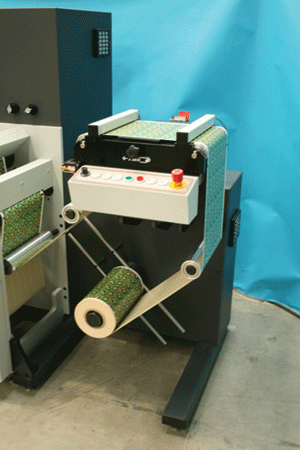
Nuevo diseño modular
Actualmente, y una vez instalados más de 320 equipos en todo el mundo con diferentes configuraciones, A.B. Graphic International ha modificado el diseño básico del equipo. La gran diferencia de diseño radica en la posibilidad de ser un equipo modular y poderse ampliar en el futuro según las necesidades de producción que se presentan al cliente; además de haberse modificado en aspectos ergonómicos gracias a las experiencias obtenidas con los clientes.
El control de la tensión del material por motores servo permite utilizar una amplia gama de materiales, desde soportes adhesivos hasta films.
La estructura básica de la máquina está formada por alimentador de bobinas impresas; cuerpo flexo para el barnizado de protección o brillante, con secado UV; unidad de troquelado; separación del desperdicio, con corte y rebobinado final del producto en subbobinas. Con esta base se puede llegar a configurar un equipo completo que además incluya: cuerpos extras de impresión, para la aplicación de colores determinados (pantones, metalizados, etc.); secado por aire para barnices base agua (tratamiento ‘primer’); unidades de estampado en caliente (‘hot foil’); laminación del material con film adhesivo o aplicando directamente la cola en el equipo; estampado en frío (‘cold foil’); cuerpo de relieve en seco, frío o en caliente; unidades de serigrafía; módulo de inspección total FleyeVision, con cámara para asegurar la exactitud de la impresión con el PDF del cliente, las impresiones secuenciales, etc.; corte completo de la etiqueta y recogida del producto en una cinta transportadora; corte por láser y eliminación de ventanas internas al producto; tratamiento corona, etc.
Este innovador diseño proporciona la ventaja que la nueva Serie2 puede crecer con todas estas opciones a medida que el cliente las necesita y no se debe configurar completamente la máquina en el momento de su adquisición.
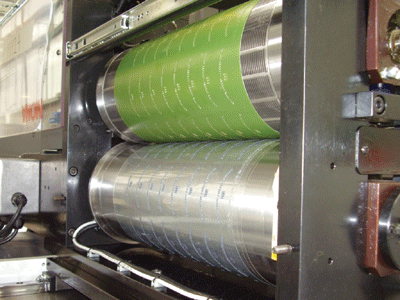
Principios de funcionamiento
La utilización de la tecnología de los motores servo permite cambiar el formato de impresión/troquelado, sin necesidad de cambiar el desarrollo de los cilindros utilizados.
En el proceso de preparación y registro de los cuerpos, el material se posiciona en la máquina hasta que la marca de impresión llega a la unidad de troquel. Una célula de lectura posiciona el material y sitúa el cilindro de troquelado en su posición “0” es decir a punto para que inicie el troquelado a registro. Los cuerpos de la máquina se autoposicionan a lo largo de la bancada y en función del desarrollo de impresión para que la primera impresión sea buena y con registro. Un lector modifica la posición del cuerpo en función de la lectura de la marca de registro. Esta utilización de motores servo que posicionan los cuerpos a lo largo de la bancada, sin que deba ser un operario quien realice esta función, es lo que permite reducir las mermas de preparación de cada trabajo.
En cuanto a la alimentación del material, la máquina está preparada para poder trabajar con diferentes tipos de avances y combinar los mismos. Un sistema de rodillos balancines permite cambiar de trabajar con un sistema rotativo al semirrotativo o al discontinuo en las diferentes secciones simultáneamente.
El avance rotativo se produce si la velocidad lineal del cuerpo impresor rotativo coincide con la del material. Se imprime y avanza todo el desarrollo del cilindro impresor. El avance discontinuo se efectúa un movimiento de avance y paro. Es utilizado en las secciones que necesitan mantener el material parado mientras trabajan (troquelado o estampado en plano, troquel láser, etc.). La técnica de la alimentación semirrotativa permite con un solo cilindro realizar todos los desarrollos en función del avance del material. La alimentación del material está gobernada por dos cilindros de arrastre (inicio y final del equipo) que actúan con motores servo para realizar un ciclo completo: acelerar el material hasta igualar su velocidad lineal con la de los cilindros de cada cuerpo; mantener la velocidad lineal constante hasta que se ha impreso el avance correspondiente; efectuar una desaceleración del material, hasta llegar al paro del mismo; realizar una aceleración en sentido contrario; producir un retroceso del material; efectuar una desaceleración y paro del movimiento en sentido contrario. Así se puede iniciar con una alimentación de la bobina en continuo, para realizar un estampado en caliente en plano, un barnizado en continuo y un troquelado semirrotativo, para acabar en un corte y rebobinado final de las subbobinas de nuevo en rotativo.
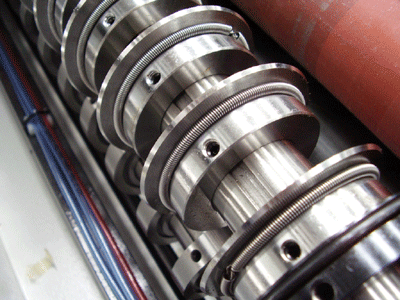
Colaboración con Hp Indigo
Pese a que la Omega Digicon es un equipo para ser utilizado en el acabado de cualquier tipo de producción, desde el principio de la impresión digital, A.B.Graphic International ha colaborado estrechamente con Hp Indigo, desarrollando un producto adaptado a la configuración particular de sus máquinas.
Fruto de esta colaboración existe la posibilidad de disponer de interface de conexión entre las dos máquinas para trabajar ambas en línea, el diseño con el mismo sentido de trabajo (derecha a izquierda), la capacidad de aplicación del tratamiento ‘primer’ en los materiales para que acepten la recepción de la impresión digital.
Actualmente A.B.Graphic International es el único socio estratégico de Hp Indigo en este tipo de producto.
Tecnología de precisión para la etiqueta adhesiva
A.B.Graphic International es una firma que se inició en la década de los 50 por la familia Burton, produciendo máquinas de tickets colgantes. El propio mercado les llevó hacia los años 70 al sector de la etiqueta adhesiva y distribuir en Europa las impresoras japonesas Lintec y Sanjo. Es a finales de los 80 que se inicia la fabricación de la gama actual de equipos:
· Omega, inspeccionadoras/rebobinadoras.
· Vectra, rebobinadores automáticos tipo revolver.
· Omega Converting, para soluciones especificas en la producción de etiqueta neutra o en necesidades especificas de cada cliente.
· Omega RFID, para los acabados de etiquetas inteligentes.
· Omega Digicon, para el acabado de bobinas preimpresas sean o no digitales.
· Omega Digilam, para el laminado de films con aplicación precisa de cola en huecograbado y secado por aire térmicamente controlado.
· Omega Digicoat, para la aplicación de tratamiento “primer”.
· Flytec, para la inspección total y comparación de la producción con un master.
Con tres fábricas, dos en Inglaterra y una en Alemania, se ha convertido en una multinacional pues dispone también de centros propios de servicio técnico, distribución y atención comercial en Estados Unidos, España y Holanda.
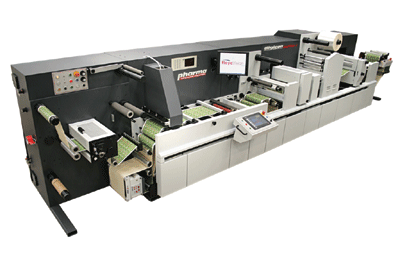