Cuando la sostenibilidad y la rentabilidad van de la mano
Michael Holzapfel, Senior VicePresident, Business Unit Rail – Industrial Europe, Schaeffler
03/02/2025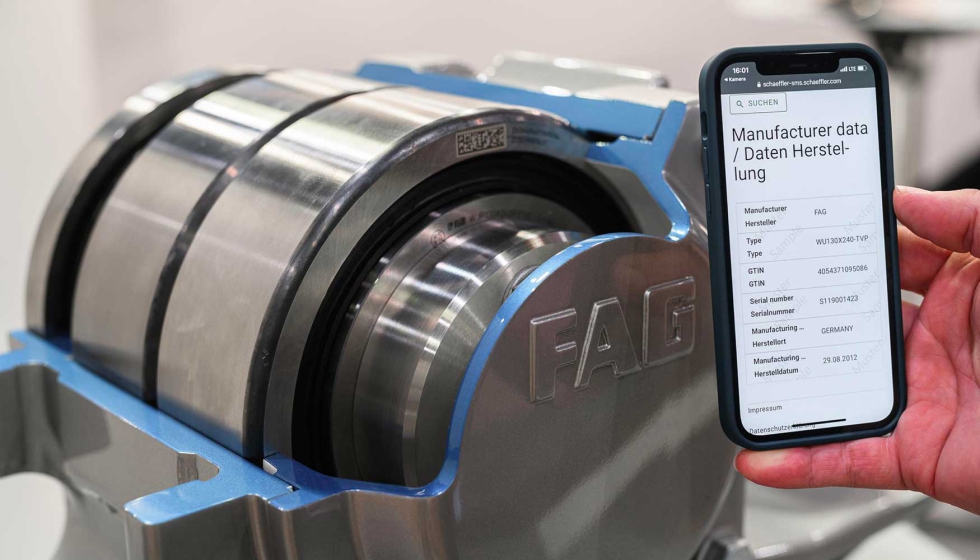
Los rodamientos para cajas de grasa son buenos candidatos para el reacondicionamiento, puesto que sus lubricantes suelen envejecer antes de que falle por fatiga el acero de los contactos de rodadura. Por lo tanto, si el lubricante se sustituye en el momento adecuado, los rodamientos pueden seguir funcionando con normalidad. Los rodamientos para cajas de grasa reacondicionados son igual de fiables y robustos que los rodamientos nuevos. Además, pueden utilizarse los sistemas de condition monitoring para garantizar el funcionamiento continuo sin fallos de estos rodamientos hasta que aparezcan daños por fatiga o los signos iniciales de daños debidos a obturaciones defectuosas o a la entrada de partículas extrañas, etc.
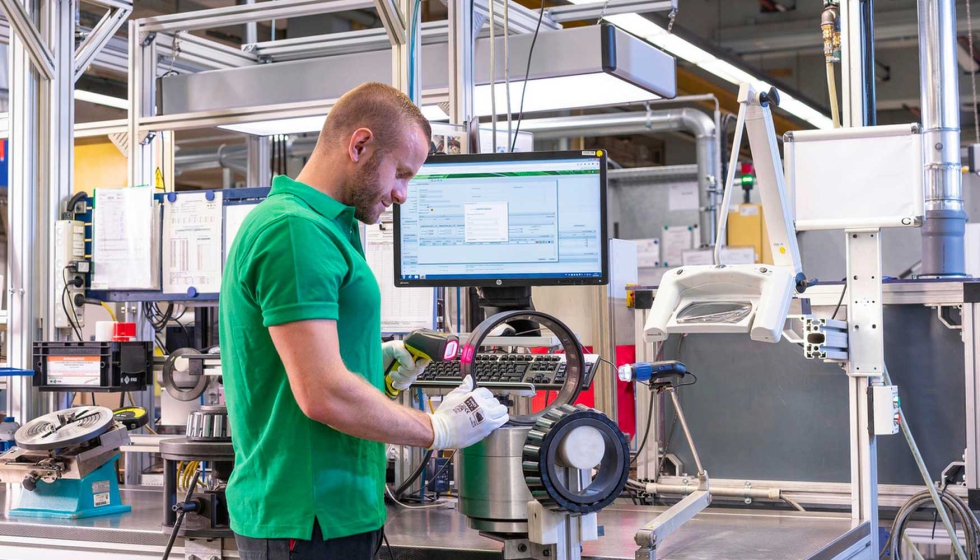
Reacondicionamiento y el concepto de devolución del 100%
El reacondicionamiento de los rodamientos para cajas de grasa que se lleva a cabo en las plantas de Schaeffler ubicadas en Wuppertal (Alemania), Yinchuan (China) and Vadodara (India) y en los talleres de reparación de los distribuidores consiste en el desmontaje, la limpieza, la inspección y la medición de los rodamientos. Los rodamientos que no presentan daños se engrasan con lubricante nuevo, y los defectuosos se apartan. En este caso, Schaeffler ofrece dos modelos de devolución del 100%. Con el primer modelo, se devuelven a los clientes sus propios rodamientos tras el reacondicionamiento, exceptuando los rodamientos defectuosos, que se sustituyen por otros nuevos. Con el segundo modelo, el cliente se beneficia de la sustitución inmediata con rodamientos reacondicionados procedentes de un pool. El segundo modelo reduce considerablemente el tiempo de espera.
La combinación perfecta: reacondicionamiento y DMC
Al grabar un código Datamatrix (DMC) en el rodamiento para cajas de grasa se sientan las bases para el mantenimiento digitalizado. El código contiene de forma encriptada la referencia única del rodamiento según la norma GS1, así como un número de pieza serializado. Tanto los operadores ferroviarios como los empleados de Schaeffler implicados en el reacondicionamiento utilizan el código DMC para registrar todos los datos relevantes, como los detalles de fabricación, montaje, funcionamiento y mantenimiento, y para intercambiar esta información, sin errores, de acuerdo con el estándar EPCIS. Basta con escanear el código para que todas las partes puedan conocer el estado del pedido del rodamiento, su ubicación actual y el historial completo de su ciclo de vida.
Configuración digitalizada de los bogies y los vehículos ferroviarios
Schaeffler está trabajando en un proyecto compartido con SBB, Stadler y Alstom, en el que se utilizan los códigos DMC para identificar los rodamientos en el momento del montaje y vincular digitalmente cada uno de ellos a sus respectivos conjuntos superiores, en este caso, ejes montados y bogies. En definitiva, el resultado es una jerarquía que va desde el vehículo completo hasta cada uno de sus componentes individuales. Obviamente, no se limita a los rodamientos para cajas de grasa. También se pueden equipar con estos códigos DMC los demás componentes de los ejes montados y bogies relevantes para el sistema.
Este enfoque ofrece importantes ventajas en combinación con los equipos de medición en la vía. En este caso, el vehículo se conecta con el sistema de vía al pasar por esta. Basándose en la jerarquía digital almacenada en el vehículo, entonces el sistema puede correlacionar sus lecturas de medición con los componentes individuales pertinentes. Así es posible, por ejemplo, realizar un análisis del estado de rodamientos individuales. El enfoque descrito en la presentación de la prueba de concepto aportará transparencia y permitirá seguir el historial del ciclo de vida y el estado de cada uno de los bogies.
Sistema de condition monitoring (CMS) para vías con cámaras acústicas
Utilizando únicamente un sistema fijo, los sistemas de condition monitoring para vías permiten que los fabricantes de vehículos y los operadores ferroviarios monitoricen una amplia gama de componentes, prácticamente todos los bogies del vehículo, independientemente del tipo de vehículo. Con este sistema se eliminan por completo los sensores montados en los vehículos y toda la infraestructura relacionada de instalación, cableado y transmisión de datos por radio.
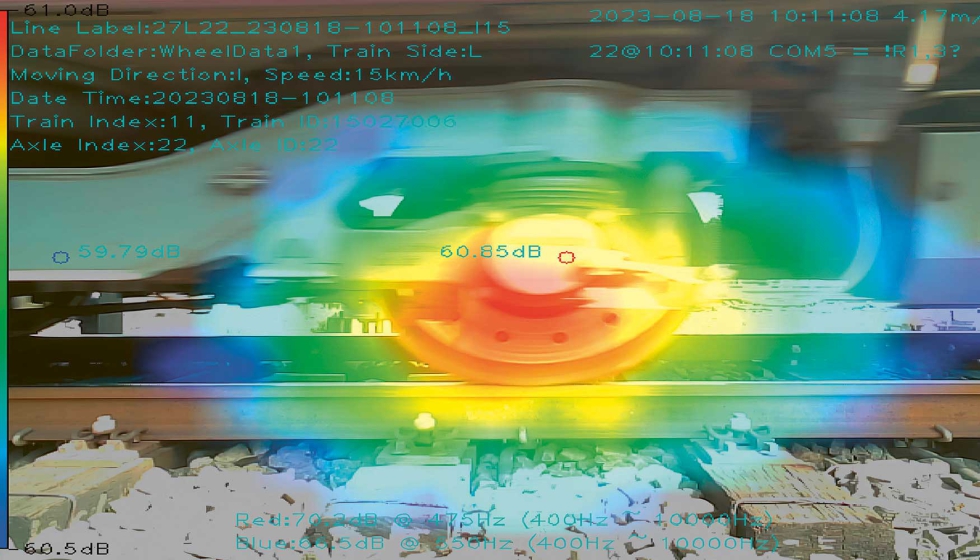
El sistema Acoustic Thermal Management System (ATMS), que ha desarrollado una empresa conjunta de Schaeffler y CARS Railway Technology Co. Ltd., ofrece precisamente estas ventajas. Explicado en términos sencillos, el ATMS se compone de una cámara acústica, una cámara óptica, cámara termográfica (opcional), dos sensores para la monitorización de las ruedas y una antena AEI o sensor RFID para identificar el vehículo/número del vehículo. La cámara acústica fija para las vías identifica los ruidos emitidos por los rodamientos del eje averiados. Con la ayuda del ATMS basado en el entorno cloud, la tecnología, que funciona en tiempo real, genera mapas de intensidad sonora, muy parecidos a las imágenes térmicas, los superpone digitalmente a una fotografía y utiliza esta información para diagnosticar fallos y analizar tendencias.
El desarrollo del ATMS ya se ha completado y se utiliza con éxito en la red de metro de Pekín. El objetivo ahora consiste en dar a conocer esta tecnología en Europa y realizar los primeros proyectos en este continente. Comparado con los sistemas de detección convencionales de ‘caja caliente’, el ATMS avisa con bastante más antelación, en torno a una semana.
Sistema de monitorización inalámbrico como parte de un proyecto de colaboración
Además de su sistema de condition monitoring con cable, Schaeffler ofrece una solución de condition monitoring inalámbrica que no incluye ningún elemento de hardware de Schaeffler. Esto es posible gracias a un proyecto de colaboración con la empresa ZF Friedrichshafen, proveedora del sector de automoción y fabricante de cajas de cambio, y su plataforma connect@rail. La contribución de ZF al proyecto es un sensor de vibración y temperatura alimentado por batería, que se monta en el soporte del rodamiento para cajas de grasa. El sensor inalámbrico Heavy Duty TAG de ZF transmite los datos de las vibraciones y la temperatura vía radio/Bluetooth a la puerta de conexión de la Unidad de a bordo VCU Pro, y desde ahí a un entorno cloud de ZF. A continuación, el equipo de ZF utiliza los datos para analizar el estado de las cajas de cambio, las ruedas con llantas y el desgaste de estas últimas. Por su parte, Schaeffler proporciona un módulo de software que se basa en esta solución de ZF para poder analizar el estado de los rodamientos para cajas de grasa.
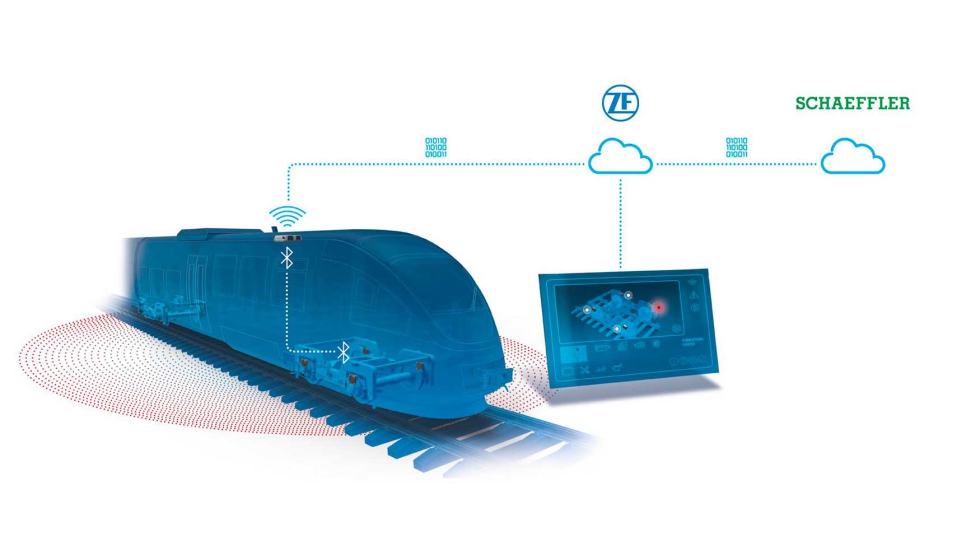
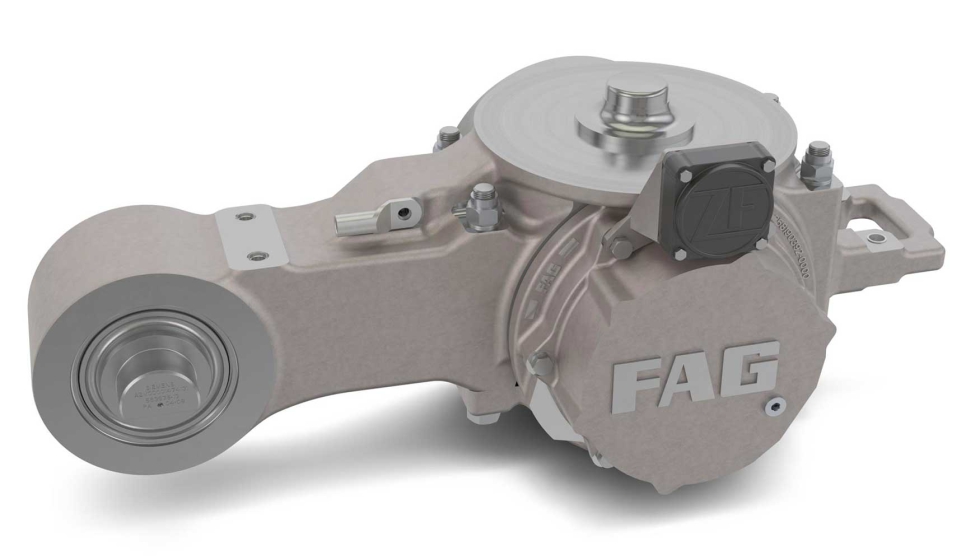
Schaeffler decidió deliberadamente no desarrollar su propio sistema inalámbrico. Mediante su participación en esta empresa conjunta y su oferta de un servicio digital basado en el sistema de su partner, Schaeffler pone de relieve una forma eficiente de utilizar el hardware y la infraestructura existentes y de maximizar su utilidad. Las plataformas abiertas de este tipo contribuyen a abaratar costes, reducir el número de soluciones aisladas y aumentar la aceptación de los sistemas digitalizados en el mercado, lo que está en consonancia con la filosofía adoptada por la dirección de Schaeffler. La empresa quiere impulsar la cooperación lograda en torno a las nuevas tecnologías, aprovechar su experiencia en el ámbito de los rodamientos para continuar desarrollando plataformas abiertas y ofrecer una mejora continua del rendimiento de los rodamientos para el sector del transporte ferroviario.
Nuevos desarrollos de rodamientos para vehículos ferroviarios. Rodamientos ‘de talla única’
Los ingenieros de Schaeffler han logrado nuevos e importantes avances en el diseño detallado de los rodamientos al utilizar un enfoque de ingeniería de circuito cerrado que integra pruebas y simulaciones. Por ejemplo, han mejorado el diseño y los métodos de ingeniería para topologías de superficie y áreas de contacto de los labios. El resultado de estas medidas son rodamientos de alto rendimiento con rozamiento interno reducido, temperaturas de funcionamiento más bajas y, por tanto, una menor carga para el lubricante e intervalos de mantenimiento más largos. Las medidas individuales se han implementado en el paquete de software OPTI-Kit. Para dar un ejemplo actual, se ha utilizado el OPTI-Kit para desarrollar un tipo de rodamiento universal. En este caso, el cliente de Schaeffler tuvo la idea de desarrollar un rodamiento ‘de talla única’, es decir, una familia de rodamientos adecuados para múltiples tipos de trenes, desde los regionales hasta los de alta velocidad, pero todos con medidas externas idénticas. Este enfoque simplifica la gestión del inventario para los OEM y agiliza el mantenimiento para el operador. Además, el efecto del elevado número de unidades genera un ahorro de costes que Schaeffler puede repercutir en los clientes.
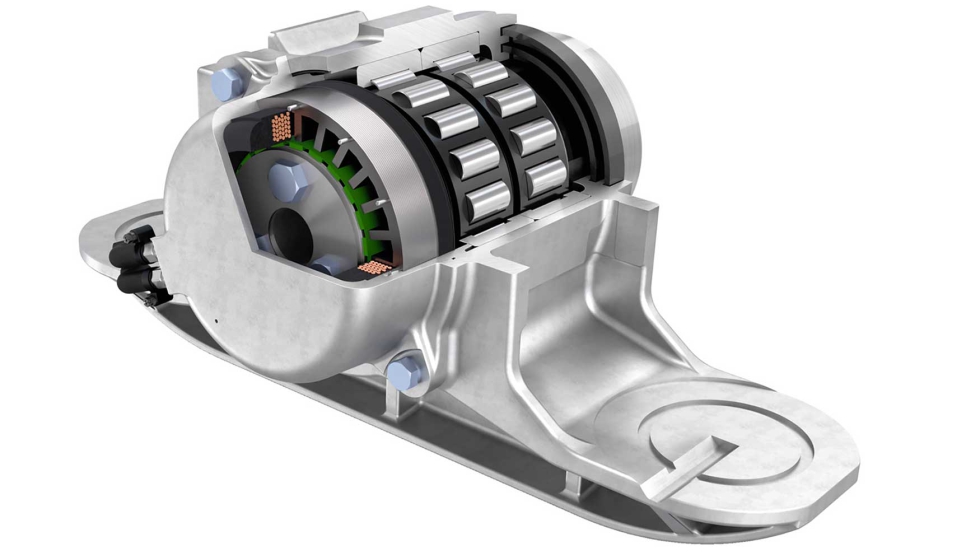
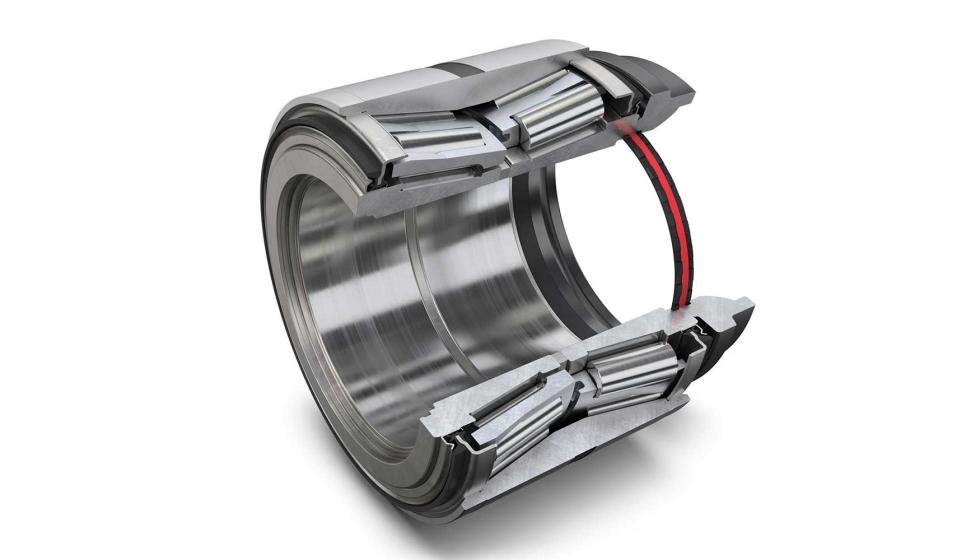