Massivit 3D transforma la fabricación de materiales compuestos con el lanzamiento de Massivit 10000
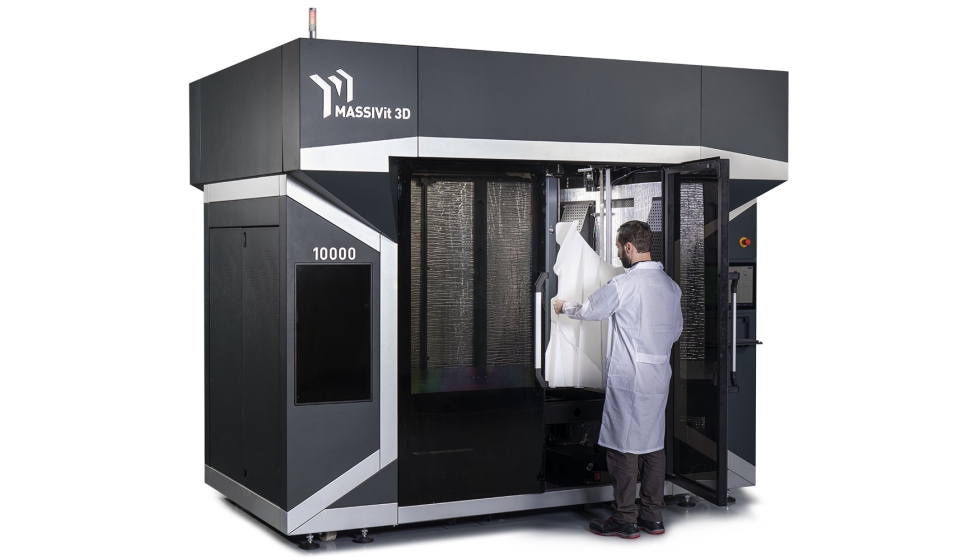
Massivit 3D Printing Technologies, proveedor especialista en sistemas de impresión 3D a gran escala, ha lanzado el sistema de herramientas de fabricación aditiva Massivit 10000. Los visitantes de JEC World (los pasados días 3, 4 y 5 de mayo) pudieron reservar una demostración en vivo del Massivit 10000.
Diseñado para superar los cuellos de botella reconocidos en la fabricación de materiales compuestos, el nuevo sistema automatiza y acorta los procesos convencionales de fabricación de materiales compuestos que son lentos, costosos, derrochadores y dependen en gran medida de la mano de obra cualificada.
El 10000 aprovecha la nueva tecnología 'Cast-In-Motion' de la empresa, que permite imprimir directamente en 3D moldes, patrones, mandriles y prototipos complejos. Proporciona libertad de geometría para diseños altamente eficientes, así como precisión digital. La tecnología está diseñada para servir a una serie de sectores, como el naval, el ferroviario, el de la automoción, el de la defensa y el aeroespacial, así como el de los artículos deportivos, los artículos de baño y los muebles.
El sistema de utillaje aditivo Massivit 10000 fue seleccionado como ganador del prestigioso Premio ACE a la Excelencia en Composites por la American Composites Manufacturers Association en el evento CAMX 2021 en Dallas, TX. Hasta la fecha se han realizado 17 pedidos previos, dos de los cuales incluyen acuerdos beta con la empresa israelí Kanfit (fabricantes de piezas de material compuesto para actores clave del mercado mundial de la aviación) y la empresa estadounidense Lyons (especialistas en artículos de baño de lujo). Massivit 3D entregará los sistemas Massivit 10000 a los clientes a partir del segundo semestre de 2022.
La tecnología 'Cast-In-Motion' de Massivit 3D permite a los fabricantes de materiales compuestos acortar sus flujos de trabajo de utillaje de los 19 pasos tradicionales a 4 pasos. Elimina la necesidad de producir un tapón o patrón inicial, imprimiendo y fundiendo directamente el molde mediante una fabricación aditiva ultrarrápida combinada con materiales de fundición de calidad industrial. Este proceso de vanguardia acorta el tiempo de fabricación de herramientas en un 80% y ofrece un sinfín de ventajas empresariales, entre las que se incluyen la reducción de la mano de obra, una disminución del 90% de los costes asociados a la mano de obra, una reducción del inventario y el transporte asociados, y una disminución significativa del desperdicio de materiales costosos.
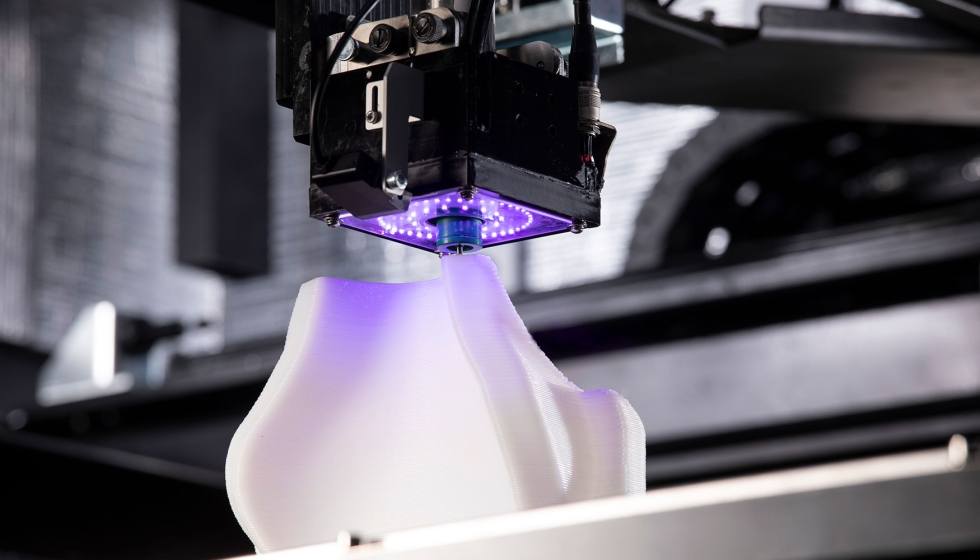
El Massivit 10000 aporta al mercado el primer molde isotrópico impreso en 3D para la fabricación de materiales compuestos. A diferencia de los sistemas de herramientas aditivas termoplásticas existentes, el Massivit 10000 utiliza materiales de base termoestable de alto rendimiento para producir un molde único y uniforme que da lugar a un verdadero molde isotrópico. Además, proporciona a los moldeadores materiales de fundición con propiedades mecánicas y térmicas altamente predecibles, un bajo coeficiente de expansión térmica y una alta temperatura de deflexión térmica.
El director general de Massivit 3D, Erez Zimerman, declaró: “esperamos con impaciencia esta ocasión trascendental, que marca un hito importante para la empresa y que inyecta innovación en el mercado de la fabricación de materiales compuestos. El ámbito de las herramientas para materiales compuestos se ha visto frenado durante mucho tiempo por procesos y tecnologías anticuadas. Ya es hora de facilitar la transformación digital en este mercado y estamos orgullosos de aportar los conocimientos técnicos, la experiencia y la innovación necesarios para ello”.
La tecnología de segunda generación de la empresa, 'Cast-In-Motion', se basa en su exitosa tecnología de impresión por dispensación de gel, que ha proporcionado una nueva liga de impresión 3D de alta velocidad y a gran escala a clientes de más de 40 países.