Entrevista a Jordi Salud, CEO y fundador de Refisa
Jordi Salud, CEO i fundador de Refisa, lleva 30 años innovando y fabricando piezas con materiales compuestos para la industria del ferrocarril des de Lleida. Con la central en Cataluña y dos filiales en Serbia y Chile para potenciar el negocio en Centroeuropa y Latinoamérica, la empresa se ha posicionado como proveedor especialista de piezas para los fabricantes de ferrocarril internacionales con una gran cartera de proyectos realizados por todo el mundo. En esta entrevista realizada para el Clúster de Materials Avançats de Catalunya —Clúster MAV—, Jordi Salud explica las ventajas de utilizar materiales compuestos en el sector del ferrocarril, los principales retos actuales y los ejes estratégicos de la empresa para su desarrollo y crecimiento para la fabricación de trenes más rápidos, ligeros, eficientes y sostenibles.
Nacida en 1987, ¿cómo ha cambiado Refisa a lo largo de más de tres décadas de experiencia?
Hemos ampliado nuestra capacidad tecnológica pero manteniendo siempre la esencia y la ilusión del primer día para innovar y aplicar el potencial de los materiales compuestos a la industria, especialmente para el ferrocarril, sector en el cual estamos muy vinculados desde la fundación de la empresa.
A lo largo de más de tres décadas de experiencia, Refisa se han ido integrando más y más en la cadena de valor de los fabricantes de ferrocarril internacionales, ofreciéndoles nuestros servicios desde el momento en el que cliente se prepara para presentarse a una licitación, y hemos evolucionado para ponerles proporcionar un servicio de ingeniería integral que incluya desde un estudio de los requerimientos, el diseño, la industrialización y la fabricación de piezas.
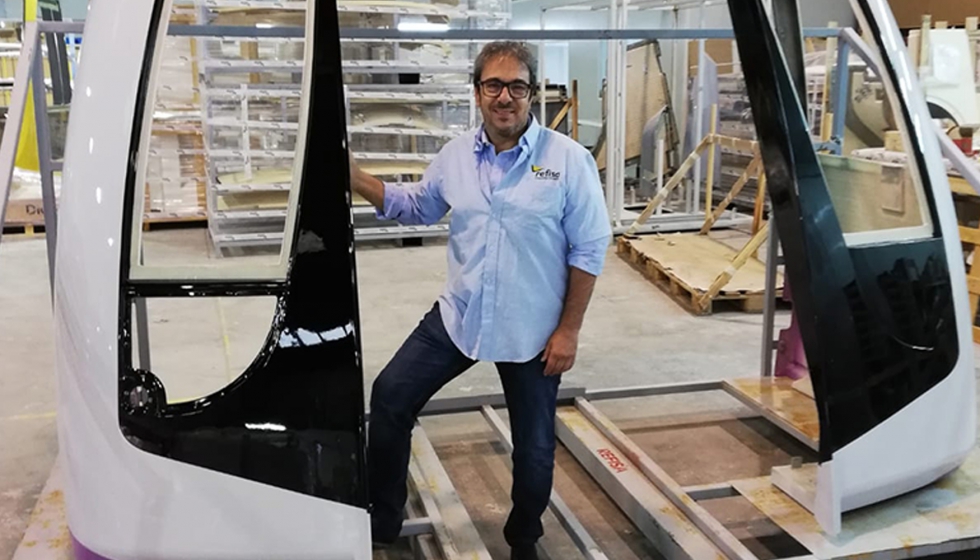
¿Cuál es el grado de aplicación de materiales compuestos en el sector del ferrocarril?
Los composites se llevan utilizando de forma recurrente durante los últimos 30 ó 40 años en sustitución de materiales como la fórmica, que no permitía acabados tan estéticos.
Cada vez más los composites están teniendo una aplicación más importante en elementos tanto de uso interior como exterior de los trenes. Poco a poco, su aplicación se ha ido ampliando de piezas estéticas pensadas para el interior del tren, a utilizarse para una gran diversidad de aplicaciones como la fabricación de cabinas de tranvías autoportantes, frontales de trenes o elementos aerodinámicos para techos de trenes de alta velocidad.
Estoy convencido que en los próximos años, su uso todavía se extenderá más y los materiales compuestos pasarán a formar parte, de manera significativa, de elementos estructurales, sustituyendo piezas metálicas.
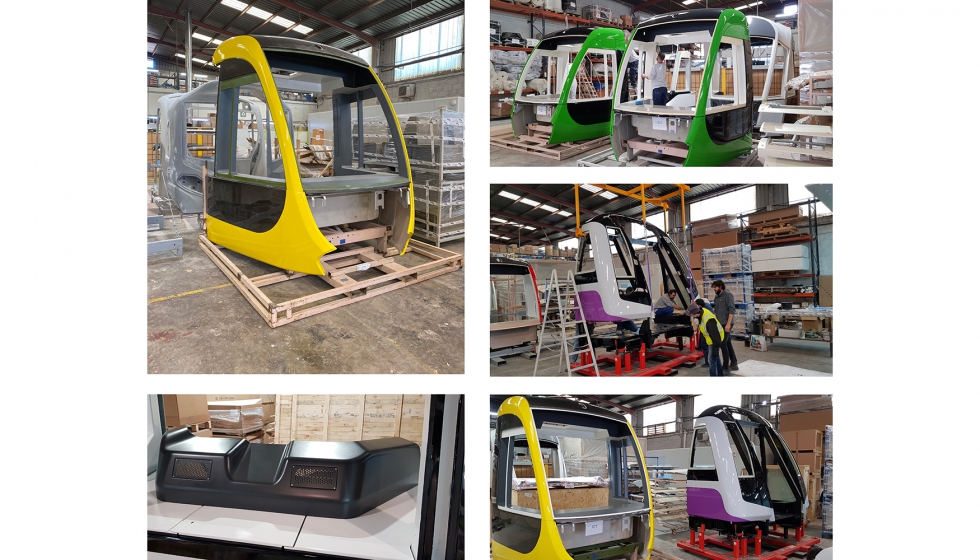
El uso de los composites en el sector ferroviario se ha ido ampliando, pasando de piezas estéticas para el interior del tren a utilizarse en la fabricación de cabinas de tranvías autoportantes, frontales de trenes o elementos aerodinámicos para techos de trenes de alta velocidad, entre otros.
¿Qué ventajas aporta el uso de composites en este sector?
Los composites contribuyen muy significativamente en la reducción del peso final de la pieza, lo que supone un impacto positivo en el ahorro energético y la huella de carbono del tren durante su vida útil.
Por otro lado, en térmicos aerodinámicos, las piezas que fabricamos aportan, con muy poco peso una resistencia estructural y estabilidad igual o más elevada que las piezas de acero o aluminio. Además, este tipo de materiales permiten la fabricación de piezas con geometrías complejas, mucho más costosas de realizar con otro tipo de materiales o procesos.
¿Cuáles son los principales retos con los cuales se encuentran durante la fabricación de piezas de composite?
Actualmente nuestro reto más importante es la reciclabilidad de la pieza y el material usado. Estamos avanzado muy positivamente a la hora de dar respuesta a todos los requerimientos que nos marcan nuestros clientes, pero el uso de resinas que sean reciclables todavía es una asignatura pendiente para la industria puesto que no se han dado avances importantes sobre este tema. Es cierto que ya existen resinas bio en el mercado, pero no cumplen aún con los demás requisitos necesarios para poder aplicarse en el sector del ferrocarril.
La reciclabilidad del material, así como su huella de carbono, empieza a ser ya un requisito concursal. En este sentido, seguimos explorando diferentes opciones de reciclabilidad y reutilización del material, así como la reducción de material sobrante par reducir nuestro volumen de residuos.
Hablemos del futuro. ¿Qué objetivos e hitos puede destacar en el ámbito empresarial?
Actualmente estamos trabajando en el escenario 2020-2022, que está muy orientado a la tecnificación y mejora de los procesos internos. Basado en tres grandes líneas, nuestro plan estratégico contempla la búsqueda de una nueva ubicación para agrupar, en una sola sede, los empleados y los dos centros productivos de la provincia de Lleida, la puesta en marcha de un proyecto de ‘lean manufacturing’ para mejorar la gestión de la fabricación, y la incorporación de una persona en el departamento de I+D para el desarrollo e implementación de mejoras.
En esta línea, hemos robotizado la parte de la empresa basada en el mecanizado de fibras y núcleos y estamos investigando e incorporando nuevas tecnologías menos contaminantes, para una mayor protección al empleado y que permitan la reciclabilidad de los elementos auxiliares, algo que hace tiempo era impensable. Un caso de éxito del cual estamos muy satisfechos ha sido la fabricación del frontal del metro de Singapur para Alstom, que también es miembro del Clúster MAV, con tecnología de vacío con un molde reutilizable de silicona.
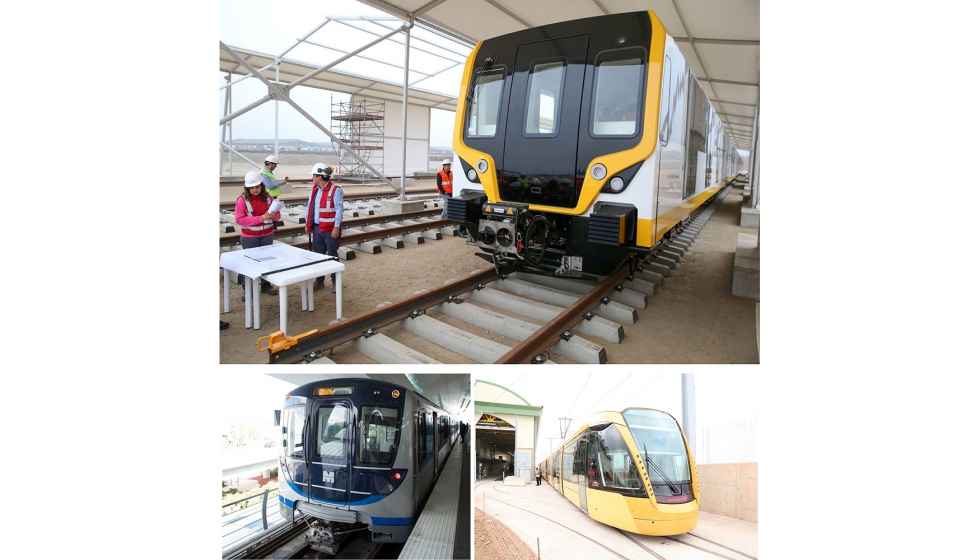
Hablando del Clúster MAV. Forman parte de él desde su fundación en 2015. ¿Cuáles son los principales beneficios de pertenecer a una asociación como esta, para Refisa?
Para nosotros, formar parte del Clúster MAV es una ventana a otras iniciativas. Nos permite conocer cómo se desarrollan otras empresas, conocer nuevas tendencias y tener una visión muy próxima de los mercados y de un entorno internacional al que, a menudo, desde una pyme no tienes acceso fácilmente. El Clúster nos permite sentirnos vinculados a un grupo y acompañados en el camino empresarial.
Refisa es una empresa puntera en la fabricación con materiales compuestos de piezas y estructuras ligeras y resistentes. Con más de 30 años de experiencia, son especialistas a aportar soluciones que integren desde el diseño conceptual a la fabricación del producto. La empresa trabaja con operadores y empresas de transporte internacional como Alstom, CAF, Talgo, Hitachi y Stadler, entre otros, en el desarrollo tecnológico y fabricación de piezas.