La gran transformación de Industrial de transformados. Proyecto Thames Link
Entorno al año 2005 Industrial de transformados se reorientó la estrategia de la tecnología de prensado de SMC hacia el mundo ferroviario dado que el mercado de la automoción se dirigía claramente a la inyección en el tipo de piezas que realizamos (Front End y parachoques). Se inició entonces la realización de piezas sueltas y progresivamente se fue ganando la confianza de los clientes y ofreciendo servicios más completos, complejos y tecnificados de interiorismo ferroviario, acabando por ofrecer servicios de ingeniería llaves en mano; gestión integral de los proyectos, realización de ingeniería de detalle, realización del 3D de conjuntos de piezas, documentación asociada (planos y estructuras), homologación de materiales, realización de moldes y útiles periféricos para realizar la industrialización de los proyectos asignados por clientes como CAF, Siemens, Bombardier o Ural Locomotive. A las piezas se les monta todo tipo de componentes (herrajes, aislantes, tornillería, etc.) y se entregan completamente acabadas (pintadas según demanda del cliente en nuestras instalaciones).
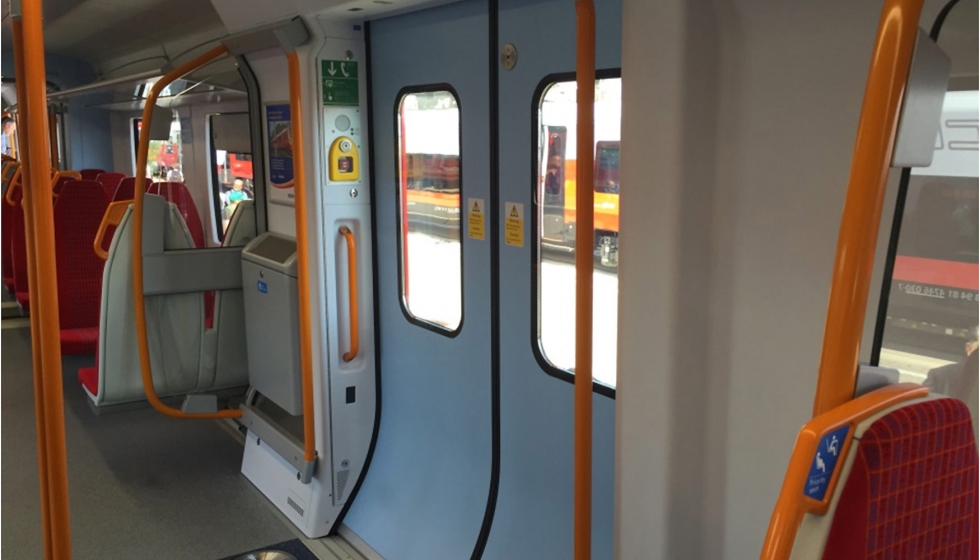
En 2012 se nos planteó la posibilidad de realizar un gran proyecto de interiorismo para nuestro cliente principal. Dada la cantidad de piezas a producir, se trataba de un proyecto de renovación de flota de trenes en Gran Bretaña, en una zona de alta densidad de tránsito de pasajeros y por tanto se requería de un elevado número de coches (más de 1000). Por ello, el proyecto encajaba perfectamente con nuestra tecnología que es principalmente el prensado de piezas de SMC (Sheet Moulding Compound).
Tecnología de prensado de Sheet Moulding Compund (SMC)
Esta tecnología de prensado se basa en la transformación de material composite. El Sheet Moulding Compound es un material plástico termoestable con matriz de resina de poliéster con diversos aditivos y fibra de vidrio. Según la proporción de este último (normalmente cercana al 25%) se tienen muy buenas propiedades mecánicas y los aditivos, en el caso del uso ferroviario están pensados básicamente para darle propiedades de fuego y humo. El SMC se presenta en forma de manta continua. Para su introducción en el molde de prensado se corta en diferentes retales que se introducen dentro del molde (abierto en el momento de la carga), el cual está calefactado por un circuito cerrado de aceite térmico de tal forma que su superficie en el momento de producir esté entorno a los 150 grados. Una vez cargado el material, se cierra el molde ejerciendo una presión muy elevada. La acción de la temperatura y la presión permiten que esta masa licue inicialmente, pudiendo fluir dentro del molde y posteriormente por acción de los catalizadores propios del SMC, el material polimerice y se convierta en sólido. Posteriormente, tras unos pocos minutos para completar la polimerización en todo el espesor de la pieza, se abre el molde y se extrae la pieza ya con su geometría y forma definitivas.
Este sistema tiene la gran ventaja de tener un muy buen acabado superficial permitiendo superficies con diversas formas y radios muy pequeños, espesor de la pieza muy homogéneo, posibilidad de integrar refuerzos locales en la cara no vista en forma de nervios, integrar insertos para atornillado de componentes y una gran repetividad dimensional entre piezas. Sin embargo tiene la contrapartida de la inversión inicial del molde que es mayor a la requerida en Laminado manual o RTM. Este punto afecta al número de piezas a partir del cual resulta rentable esta tecnología y es en donde desde la ingeniería de ITSA también se realiza un importante esfuerzo en minimizar los costes, optimizando y minimizando el número de versiones sea con postizos en molde o en el diseño propio de la pieza, reduciendo así la inversión inicial necesaria, así como reforzando la pieza allá donde sea necesario con nervios, reduciendo o eliminando los refuerzos metálicos en la cara no vista.
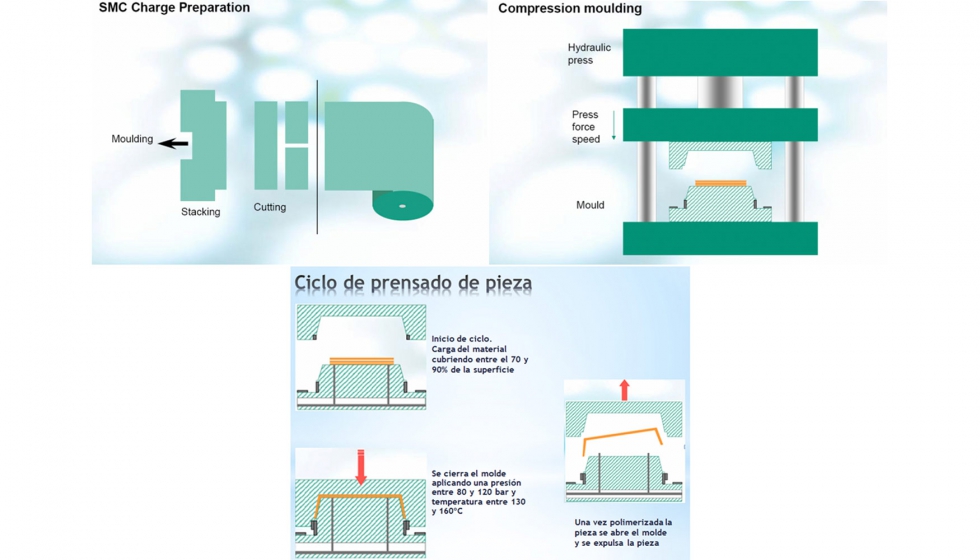
Ese mismo año se nos habían adjudicado dos proyectos, uno de pilares de entrada para alta velocidad alemana y otro para el conjunto de marco entre coches para un proyecto de Inglaterra. Pero el cliente tenía otro conjunto de muchas piezas sin adjudicar que requería de ejecución urgente: Todo el marco de entrada (pilares, trampillas de acceso, conducto de aire y dintel) y el plazo de diseño e industrialización era extremadamente reducido. Finalmente ITSA ganó el proyecto que hasta la fecha mayor importancia ha tenido para la empresa, no solo por su futura facturación sino por el cambio organizativo que supuso tanto a nivel de recursos necesarios como en metodología de trabajo. Este proyecto, junto con la aplicación de una sistemática implementada para la certificación IRIS, supuso una revolución dentro de nuestra empresa.
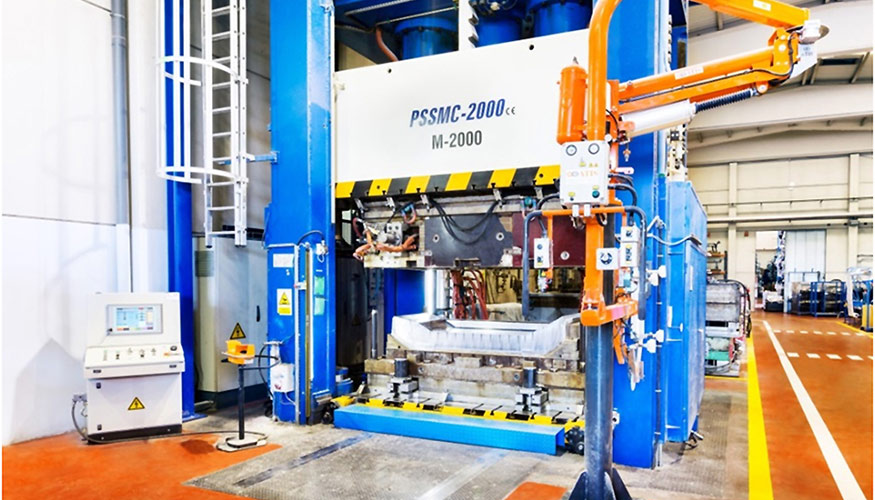
El proyecto, en el momento de la asignación, se basaba en unas pieles en 3D y una definición de interacciones entre piezas que se tuvo que replantear por completo para simplificarla, reducir en lo posible costes, peso, número de moldes y hacer las piezas moldeables en tecnología SMC. Para ello, desde el departamento de ingeniería se tuvo que contratar a nuevo personal y contar con apoyo de personal externo de ingenieros siempre con la premisa que fueran ‘in house’, es decir que estuvieran durante todo el desarrollo del proyecto en nuestras instalaciones. Todo el proyecto se desarrolló con el programa CAD Creo (antiguo Pro-Engineer).
En un plazo de 3 meses con continuo contacto con nuestro cliente se completaron los nuevos 3D de manera que se superó la fase de Design Freeze (fijación de los 3D) para poder lanzar los moldes. Lógicamente, como en todo proyecto, hubieron modificaciones posteriores a este punto que se tuvieron que gestionar e implementar en los moldes, siendo finalmente necesarios 9 moldes de entre 1 y 36 toneladas. Así mismo se tuvo que realizar estudios de elementos finitos para poder confirmar que la pieza aguantaría con una papelera de carga estática de 35 kg anclada en ella bajo unas condiciones de colisión, con una aceleración de 6 g.
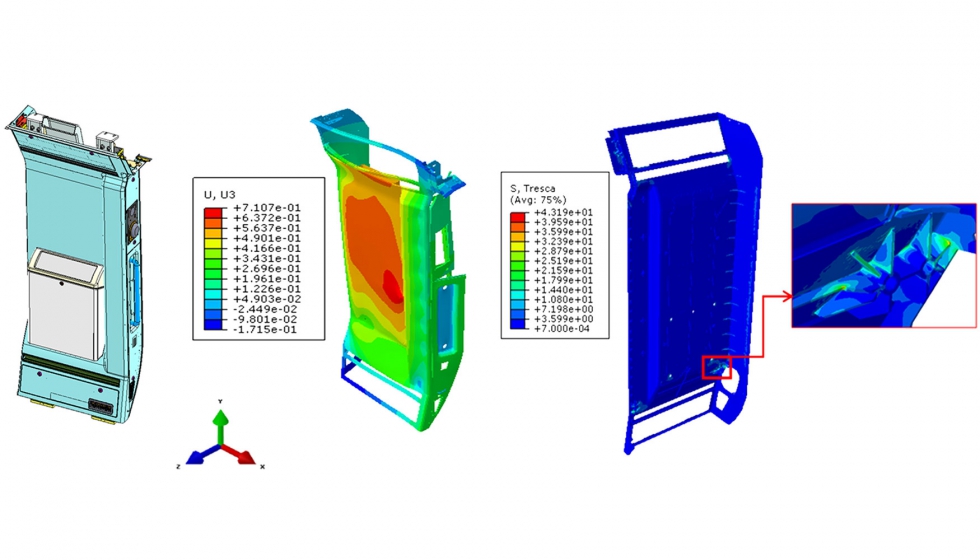
El proyecto se basaba en unas pieles en 3D y una definición de interacciones entre piezas que se tuvo que replantear para reducir en lo posible costes, peso y número de moldes. Finalmente fueron necesarios 9 moldes de entre 1 y 36 toneladas.
Se superaron las diferentes etapas de Design Freeze, Design Aproval (realización de toda la documentación de planos y estructuras), Type Test (prueba de montaje preliminar de primeras piezas sin pintado y acabados definitivos) en nuestras instalaciones en el que diseñamos el correspondiente Mock Up para simular el montaje del conjunto en el tren y finalmente se superó la FAI (First Article Inspection), cumpliendo también los requerimientos de fuego y humo de la normativa British Standard 6853 Categoría 1b.
Una vez pasada la FAI, empezó el segundo gran reto para la empresa: la subida en cadencia serie. Durante la fase de desarrollo se trabajó en la definición de proveedores estratégicos y se establecieron con ellos unos stocks de seguridad básicos para poder tener garantías de disponibilidad de componentes en todo momento y evitar el retraso en entregas a nuestro cliente por falta de componentes. Una buena planificación en las compras así como en la planificación de producción nos permitió cumplir en la rampa de lanzamiento de entregas y llegar a una plena cadencia superior a la que el cliente nos había solicitado inicialmente dado que al año de arrancar con el proyecto recibimos una ampliación del mismo para el proyecto de South Western Train (SWT) con nuevas referencias para otro cliente final, pero basado en los mismos componentes.
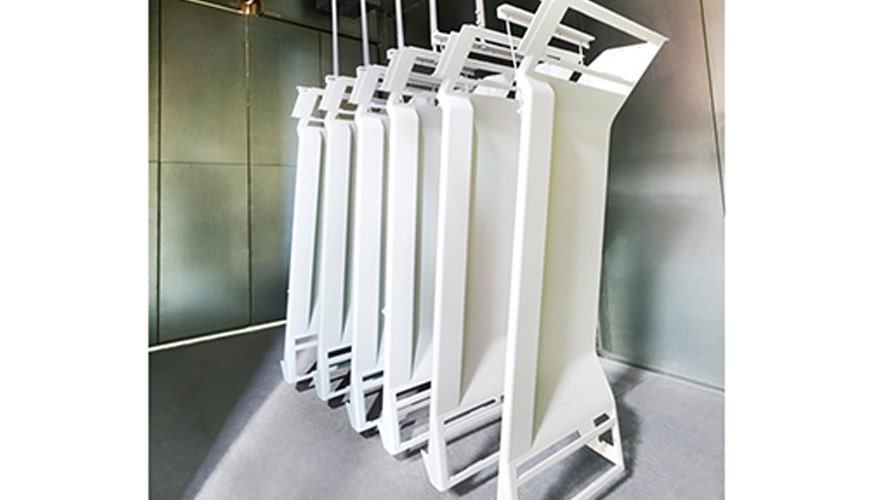
ITSA fue superando las diferentes etapas, desde la aprovación del diseño hasta la prueba de montaje de las primeras piezas sin pintado.
A día de hoy seguimos entregando estos componentes y hemos recibido recientemente una nueva ampliación para el proyecto Moorgate de Inglaterra en el que se crearon nuevas combinaciones de piezas basado en el proyecto Thames Link y con un nuevo requerimiento de fuego y humo según la normativa EN 45545 HL3 R1. Esto nos obligó a trabajar con nuestros proveedores de materiales para poder homologar este material y aprovechamos también el desarrollo para homologar un material SMC según normativa British Standard 6853 Categoría 1a, que pasa a ser una alternativa a las piezas de laminado manual en fenólica para futuros proyectos.
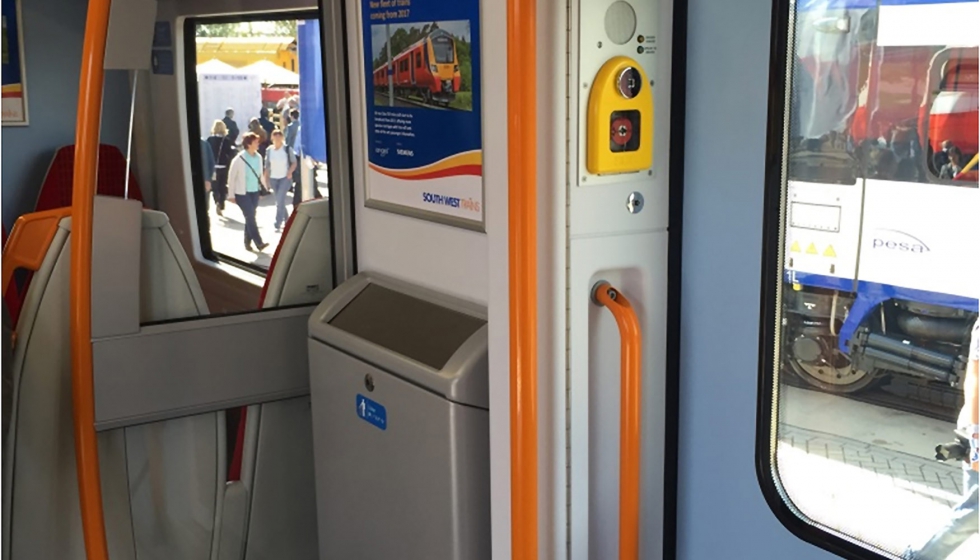
Recientemente, para poder dar un mejor servicio y coste a nuestros clientes hemos introducido en interno la tecnología RTM para poder realizar pequeñas series complementarios a las de gran tirada que realizamos en SMC. Así mismo hemos apostado por introducir la tecnología de PIMC para acabado de piezas de SMC de tamaño pequeño o mediano directamente en molde.