El análisis del aceite lubricante online responde a eventos inesperados y reduce costes de mantenimiento
Nuevo sistema sensor para la monitorización online del aceite lubricante en motores de turbinas de gas
La monitorización online de la calidad del aceite lubricante en las turbinas de gas de los aviones mediante un sistema sensor es ya una realidad. Las principales ventajas de utilizar un sistema sensor online son el acceso a puntos de lubricación en condiciones extremas de trabajo, el aporte de información sobre el comportamiento de los diferentes componentes mecánicos del sistema de lubricación y la posibilidad de implementar un plan de mantenimiento predictivo y proactivo para la detección de las primeras etapas de la degradación del aceite lubricante. Todas están ventajas dan lugar a un ahorro significativo en costes de mantenimiento y operación.
Las turbinas de gas de los aviones pueden sufrir graves fallos mecánicos provocados por la degradación y/o contaminación del aceite de lubricación. Tradicionalmente, el control del aceite lubricante se ha llevado a cabo por medio de análisis periódicos en laboratorio, pero mediante este tipo de análisis no es posible detectar las primeras etapas de la degradación del lubricante y en muchos casos el tiempo que se tarda en recibir los resultados de laboratorio es demasiado largo. Es por ello que el análisis del aceite lubricante debería ser online, a fin de responder a eventos inesperados y reducir costes de mantenimiento [1, 2].
La aplicación de sensores online puede ser la solución de varios problemas no resueltos en la industria aeronáutica tales como el acceso a puntos de lubricación en dispositivos y motores que trabajan en condiciones extremas, la detección de las primeras etapas de la degradación del lubricante, proporcionar información sobre el estado de los componentes mecánicos en el sistema de lubricación y el establecimiento de un buen sistema de mantenimiento predictivo y proactivo con el consecuente ahorro en los costes de mantenimiento [3].
El objetivo principal de este trabajo es describir el proceso de fabricación y calibración de los sensores online Vis-NIR y OPD desarrollados por IK4-Tekniker y utilizados en la monitorización del estado de degradación del aceite lubricante de las turbinas de gas de los aviones. Estos sensores también han sido utilizados en la monitorización de otro tipo de lubricantes y fluidos hidráulicos, tales como el Skydrol LD-4, el cual es un fluido hidráulico que se utiliza en los actuadores de los aviones [4, 5]. El objetivo de estos sensores es no tener la misma exactitud y precisión de un equipo de laboratorio, sino el desarrollo de un sistema sensor online con la suficiente exactitud y precisión como para determinar la calidad del lubricante con el fin de decidir si el cambio de aceite es necesario. Como resultado, los costes de mantenimiento y el impacto medioambiental debido a innecesarios cambios de aceite pueden ser reducidos.
Los sensores Vis-NIR y OPD han sido testeados en los bancos de pruebas de la Universidad Libre de Bruselas (ULB) e IK4-Tekniker durante las diferentes pruebas realizadas en el proyecto europeo ELUBSYS, perteneciente al séptimo programa marco. Las pruebas en ULB se han llevado en condiciones de presión y temperatura comprendidas entre 2-6 bares y 40-120°C y con un flujo máximo de aceite de 5500 l / h [4]. En cambio las pruebas en el banco de ensayos de IK4-Tekniker han sido realizadas a presiones comprendidas entre 2-7 bares y a 30°C de temperatura ya que no era posible calentar el aceite en el interior del banco de ensayos. La figura 1 muestra los sensores Vis-NIR y OPD conectados al banco de ensayos de ULB [5].
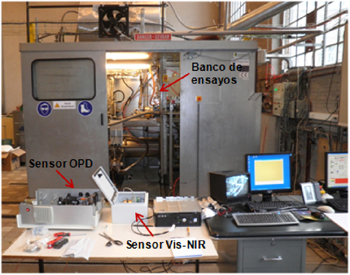
Cabe destacar que ambos sensores han sido utilizados en otras aplicaciones como en la monitorización del fluido hidráulico Skydrol LD4, utilizado en los actuadores de los aviones. Dicho trabajo fue realizado en colaboración con el Centro de Tecnologías Aeronáuticas (CTA) de Vitoria en el marco del proyecto Airhem II (Etortek) subvencionado por el Gobierno Vasco. En este proyecto el sensor OPD ha sido utilizado para la detección de partículas y burbujas mientras que el sensor Vis-NIR ha sido utilizado en la monitorización de la viscosidad y el número de acidez del Skydrol LD-4 [4].
Sensor visible- Infrarrojo cercano (Vis-Nir)
El sensor Vis-NIR es un prototipo empleado para la monitorización online del contenido de aditivos del aceite Mobil Jet Oil II utilizado como aceite lubricación en las turbinas de gas de los aviones.
El sensor tiene un sistema óptico que separa el haz de luz que atraviesa la muestra de aceite en diferentes longitudes de onda obteniendo el espectro de transmitancia de la muestra. Los componentes utilizados para el desarrollo del sistema óptico del sensor son los siguientes: una luz halógena blanca, un pinhole de 150 micras para dirigir el haz de luz que atraviesa la muestra, un espejo esférico para colimar la luz hacia la red de difracción, una red de difracción que separa el haz de luz en diferentes longitudes de onda y un segundo espejo esférico que focaliza la luz hacia el detector, el cual es un array de 128 píxeles que trabaja en el rango espectral comprendido entre los 400-1.100 nm, cubriendo el rango visible (400-780 nm) y parte del infrarrojo cercano (780-1.100 nm).
El diseño mecánico del sensor ha de asegurar un fácil mecanizado de las piezas a un coste bajo de fabricación, así como la robustez del sensor. Los componentes fabricados y ensamblados fueron eran el housing, el alojamiento de los componentes ópticos y la celda fluídica. El diseño mecánico del housing y sus diferentes componentes ha sido realizado teniendo en cuanto las siguientes consideraciones: precisión en la posición tanto de los componentes ópticos como del detector, sencillez del montaje, ligereza y estanqueidad del conjunto. Para el alojamiento de la muestra, la fuente de luz y el filtro de luz se ha diseñado un cuerpo independiente a la caja, donde van alojados todos estos elementos, denominado celda fluídica. En la celda fluídica el haz de luz atraviesa la muestra, luego atraviesa el filtro de luz y finalmente pasa por el pinhole, antes de incidir sobre el primero de los espejos esféricos en el interior del housing. La celda fluídica ha sido fabricada de aluminio y tiene un paso óptico de 1 mm. Con el objetivo de que una vez montado todo el conjunto sea lo más ligero posible, y a la vez no sea difícil de fabricar y mantenga las precisiones necesarias se han fabricado todas las piezas en aluminio. A cada pieza se le ha dado un tratamiento de anodizado en color negro mate con el fin de que si algún rayo de luz se desvía de la trayectoria deseada no se refleje e incida sobre el detector. En la figura 2 se muestra una vista isométrica del diseño del housing, mientras que en la figura 3 se muestra una fotografía del montaje final de los diferentes componentes ópticos en el interior del housing. En cuanto a las condiciones de trabajo, el sensor puede trabajar a presiones hasta 7 bares y 120 °C de temperatura.
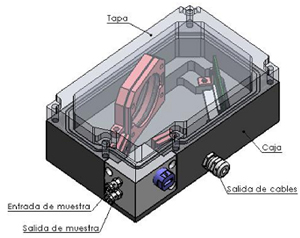
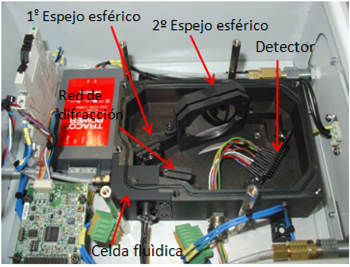
La calibración del sensor ha sido llevado a cabo mediante el análisis multivariable de datos aplicando diferentes técnicas quimiométricas, obteniéndose dos modelos de calibración para la monitorización del contenido de aditivos del aceite lubricante Mobil Jet Oil II. El primer modelo de calibración ha sido desarrollado para la monitorización del contenido de aditivo en un rango comprendido entre el 100-30% mientras que el segundo modelo cubre el rango comprendido entre el 100-70%. El primero de los rangos ha sido seleccionado con el fin de monitorizar la degradación casi total del aceite mientras que el segundo rango ha sido seleccionado debido a que en aviación este tipo aceite generalmente se cambia cuando su contenido de aditivo disminuye hasta un 80-70%. Los espectros obtenidos con el sensor han sido correlaciones con el contenido de aditivo (RULER, ASTM-D 6810-2) de las muestras analizadas en el laboratorio de análisis industrial de Wearcheck Ibérica. Para ello se han seguido los siguientes pasos: pre-procesamiento de los espectros obtenidos, generación del modelo de calibración y finalmente la validación del modelo. A la hora del pre-procesado se han probado diferentes métodos, desde el suavizado de los espectros hasta métodos para corregir efectos dispersión. Los modelos de calibración fueron obtenidos mediante Regresión sobre Mínimos Cuadros Parciales o Partial Least Squares Regression (PLS). PLS es una de las técnicas de regresión lineal más utilizadas en el análisis multivariable de datos. Se trata un método que relaciona las variaciones en una o más variables respuesta (Y-variables) con la variación en múltiples variables predictoras (X-variables) [6]. Finalmente la validación de los modelos de calibración ha sido realizada mediante un método de validación cruzada conocido como leave-one-out cross validation. Es un método de validación basado únicamente en los datos utilizados para la calibración por el cual se crean tantos sub-modelos como muestras hay en la calibración, dejando cada vez una muestra fuera para utilizarla en la validación. El proceso se repite hasta que cada muestra utilizada en la calibración haya sido dejada una vez fuera para la validación. Después todos los residuales son combinados para obtener una estimación del error de predicción del modelo. Todo el análisis quimiométrico fue realizado con el software The Unscrambler ver. 9.8 (Camo process AS, Oslo, Noruega). La tabla 1 muestra los resultados de los modelos de calibración desarrollados para la monitorización del contenido de aditivos del aceite lubricante Mobil Jet Oil II. A pesar de que los resultados obtenidos durante la calibración son satisfactorios todavía es necesario mejorar la exactitud de los modelos de calibración desarrollados para la monitorización del contenido de aditivos.
Resultados obtenidos durante la calibración del sensor Vis-NIR
Parámetros del modelo |
Contenido Aditivo: 100-40% |
Contenido aditivo: 100-70% |
Número de muestras |
30 |
13 |
Componentes Principales (PC) |
6 |
3 |
Correlación |
0,962 |
0,879 |
SECV a |
4,809 |
4,827 |
aSECV: error estándar de la validación cruzada
Detector de partículas Óptico (OPD)
El sensor OPD sensor es un prototipo cuyas funciones son la detección y cuantificación de burbujas y partículas metálicas y no-metálicas en el aceite lubricante. El sensor toma una imagen de la muestra aceite y mediante la inteligencia artificial que tiene implementada es capaz de distinguir las burbujas de las partículas y realizar su clasificación en función de su tamaño. El sensor da como resultado un informe en formato pdf en el que se muestra una imagen de la muestra aceite con las partículas marcadas en rojo y las burbujas en verde y el número de partículas clasificados en tres rangos: ≥ 4 μm, ≥ 6 μm y 14μm por ml de muestra. Finalmente el número de partículas se codifica tomando en cuenta la norma ISO 4406.
El conjunto del sensor OPD está formado por un filtro de partículas de 190 micras que impide que entren partículas de gran tamaño que puedan obturar algún componente del sensor, un presostato (0-25 bar) que permite la entrada de aceite siempre y cuando la presión en el sistema sea inferior a 7 bares, un caudalimetro, una cámara CMOS (Edmund EO 5012 C), una celda fluídica iluminado por leds blancos y una tarjeta de adquisición de datos. La figura 4 muestra los diferentes componentes del sensor OPD.
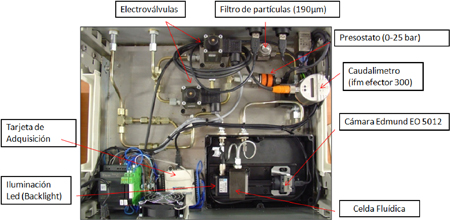
La celda fluídica es de de acero inoxidable y tiene un paso óptico de 1 ml. La iluminación de la muestra de aceite se realiza mediante un panel de leds blancos tipo backlight obteniendo una iluminación totalmente uniforme de la muestra. La iluminación ha sido montada independiente de la celda fluídica con el fin de evitar las altas temperaturas debido al flujo de aceite a través de la celda. El sensor OPD tiene un modo de ajuste automática de la iluminación, por el cual el es capaz de adaptar el tiempo de exposición de la cámara a la absorbancia del aceite, ya que no todos los aceites absorben la misma cantidad de luz, siendo algunos más oscuras que otros. En cuanto a las condiciones de trabajo, el sensor que puede soportar presiones de hasta 7 bares y 120 °C de temperatura.
La calibración del sensor OPD ha consistido en el desarrollo del algoritmo para la detección y cuantificación de partículas y burbujas en el aceite lubricante Mobil Jet Oil II. Las burbujas son detectadas en función de su morfología, ya que se tratan de cuerpos más redondos que las partículas, y por el agujero o agujeros que poseen en su interior. Las partículas también son detectadas en función de su morfología, siendo cuerpos más amorfos que las burbujas y por el tamaño, generalmente más pequeñas que las burbujas. La calibración del sensor ha sido realizada en el banco de ensayos de de IK4-Tekniker a una temperatura de 30°C y un rango de presión de 2-7 bares. En la calibración han sido utilizadas tres tipos de partículas: acero inoxidable (tamaño max. = 45μm), hierro (tamaño máx. = 60μm) y arena (tamaño máx. = 40μm). Dichas partículas han sido mezcladas en diferentes concentraciones con el aceite lubricante en el banco de ensayos. Además durante la calibración se ha ido añadiendo diferentes cantidades de aceite lubricante degrado que contenían partículas formadas durante el propio proceso de degradación del aceite. El algoritmo ha sido desarrollado con el software HALCON (MVtec Software GmbH, Alemania). La figura 5 muestra claramente la diferencia entre las burbujas, de forma redonda y con un agujero en el medio, y las partículas que son más pequeñas y alargadas.
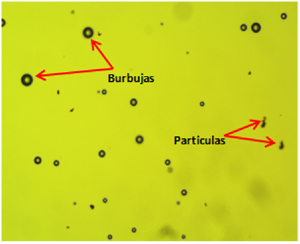
En el informe de resultados aparece la imagen grabada originalmente por la cámara con las partículas remarcadas en rojo y las burbujas en verde. La figura 6 muestra la imagen grabada por OPD durante el proceso de calibración realizada en banco de pruebas de IK4-Tekniker a 30°C y 6 bares y la imagen resultante del análisis para diferenciar entre partículas y burbujas, en la que las burbujas a esta imagen de las burbujas se señaló en grado n y las partículas se señalan en rojo.
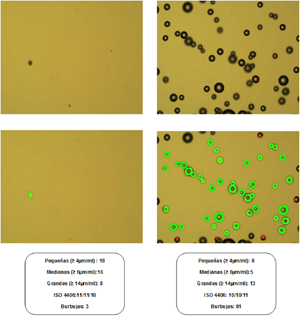
Durante el proceso de calibración se fueron tomaron diferentes muestras de aceite del banco de ensayos para analizar el contenido de partículas en el laboratorio y de esta manera poder saber si el algoritmo realizaba la detección y cuantificación de las partículas de manera correcta. Los resultados muestran que en líneas generales el sensor realiza una correcta detección y cuantificación de las partículas obteniendo valores muy próximos a los de laboratorio. En cuanto al contenido de burbujas no fue posible comparar el resultado obtenido con el sensor con ningún valor de laboratorio. A pesar de ello los resultados obtenidos en la calibración han sido realmente satisfactorios, se ha podido observar como el algoritmo tiene problemas para detectar aquellas burbujas que están en los bordes de la imagen, ya que en algunos casos o no las ha detectado o la confunde con una partícula grande. En cambio el resto de burbujas que aparecen en la imagen las detecta sin ningún tipo de problema.
Conclusiones
Los nuevos sensores Vis-NIR y OPD desarrollados por IK4-Tekniker han mostrado que pueden llegar ser una herramienta realmente útil en la monitorización del estado de degradación y contaminación del aceite lubricante de las turbinas de gas de los aviones. La implantación de este tipo de sistema sensor en el avión daría lugar a una reducción significativa del coste en mantenimiento y un aumento en la seguridad del avión al poderse realizar un diagnostico a tiempo real del sistema de lubricación de la turbina.
A pesar de que los resultados obtenidos durante el proceso de calibración con ambos sensores han sido realmente satisfactorios es necesario mejorar los modelos de calibración y los algoritmos desarrollados para el sensor Vis-NIR y OPD respectivamente. En el caso del sensor Vis-NIR los resultados obtenidos han sido bastante satisfactorios aunque es necesario mejorar la exactitud de los modelos de calibración desarrollados para la monitorización del contenido de aditivos. Respecto al sensor OPD los resultados han mostrado que el algoritmo realiza una correcta detección y cuantificación de partículas mientras que es necesario mejorar la detección de las burbujas.
Una vez mejorados los modelos de calibración y los algoritmos el siguiente en paso en el proceso de industrialización de los sensores seria la reducción de tamaño y peso de ambos sensores, sobre todo el OPD cuyo tamaño y peso actual hacen no viable que se pueda embarcar el sensor dentro de un avión. Además es necesario que los modelos de calibración, algoritmos e inteligencia artificial se encuentren embebidos en la electrónica de los sensores sin que sea necesario tener que conectarlos a un PC.
Referencias
[1] Schalcosky, D.C., and Byington, C.S., (2000). Advances in Real Time Oil Analysis. Practicing Oil Analysis Magazine, 11, pp.28-34.
[2] Gorritxategi, E., Arnaiz, E., Aranzabe, E., Aranzabe, A., Villar, A. (2009). On-line sensors for condition monitoring of lubricating oil. Proceedings of 22nd International Congress on Condition Monitoring and Diagnostic Engineering Management COMADEM, San Sebastian, Spain.
[3] Halme, J., Gorritxategi, E., Bellew, J., in: Holmberg, K., Jantunen, E., Adgar, A., Mascolo, J., Arnaiz, A., Mekid, S. (Eds.). (2010). E-Maintenance, Springer-Verlag, London.
[4] A. Villar, A. Arnaiz, D. Otaduy, E. Gorritxategi, I. Jorge, O. Berten. (2012). New On-line Sensors for Condition Monitoring of Lubricant and Hydraulic Fluids in Aeronautics. Proceedings of the International Congress on Lubrication, Maintenance and Tribotechnology LUBMAT’12, Bilbao, Spain.
[5] O. Berten, P. Hendrick, A. Villar, D. Seveno. (2012). Integration Of Oil Quality Monitoring Sensors Into A Test Bench For Aircraft Gas Turbine Engine Lubrication Systems. Proceedings of the International Congress on Lubrication, Maintenance and Tribotechnology LUBMAT’12, Bilbao, Spain.
[6] K. H. Esbensen. (2006). Multivariate Data Analysis in practice, 5th Edition.CAMO Software AS, Oslo, Norway.