Certificación de la fabricación aditiva metálica en el sector aeroespacial
A día de hoy, el impacto que la fabricación aditiva ha tenido en la industria es incuestionable. Estos procesos han irrumpido en prácticamente todos los sectores industriales, siendo especialmente significativa la acogida por parte del sector biomédico y el aeronáutico. La tasa de crecimiento del mercado de la fabricación aditiva metálica y la inversión cada vez mayor en investigación en este campo son testigos de este fenómeno.
Las ventajas de la fabricación aditiva son, lógicamente, los principales impulsores de su implementación industrial. En el caso del sector aeroespacial, la libertad geométrica, la eficiencia de material, y la reducción de peso, son los aspectos clave que justifican el interés de las compañías líderes del sector en esta tecnología. De esta forma, los principales fabricantes de componentes aeronáuticos y aeroespaciales están invirtiendo un volumen de recursos sustancial en adaptarse a esta tendencia de mercado, con el fin de aprovechar al máximo esta oportunidad.
Sin embargo, la implementación de procesos de fabricación aditiva metálica en la industria aeroespacial no está exenta de retos. El mercado aeronáutico está altamente regulado, y la certificación para vuelo de sus componentes es imprescindible para garantizar la seguridad de las aeronaves. De hecho, la certificación de componentes producidos mediante fabricación aditiva es uno de los principales retos que afronta el sector aeroespacial actualmente. El rápido crecimiento de las tecnologías de fabricación aditiva ha impedido que las agencias gubernamentales responsables de esta certificación respondan a esta necesidad de una forma garante y rápida, de forma que, hoy en día hay una carencia importante en lo que a directrices, estándares y rutas de certificación públicas que regulen estos aspectos.
Principales procesos de fabricación aditiva metálica
En contraposición con los procesos de fabricación formativos y substractivos, la fabricación aditiva se refiere a aquellos procesos que se fundamentan en la sucesiva adición de material para generar una geometría. La fabricación aditiva se considera uno de los pilares de la cuarta revolución industrial y se percibe como una tecnología disruptiva por parte de la industria. Esto se debe a que los procesos aditivos han traído consigo un cambio en el paradigma de fabricación y consecuentemente, la propia estructura de la cadena de producción debe ser adaptada para acoger este tipo de tecnologías de una forma eficiente.
De todos los procesos aditivos disponibles hoy en día, la fabricación aditiva metálica es probablemente el que más interés industrial presenta en la fabricación de componentes sometidos a altas solicitaciones. Concretamente, los procesos que más presencia industrial tienen son los procesos de deposición de energía focalizada (Directed Energy Deposition, DED) y la fusión de lecho de polvo (Powder Bed Fusion, PBF). Es por esto que dichos procesos se describen brevemente a continuación y se muestran esquemáticamente en la figura 1.
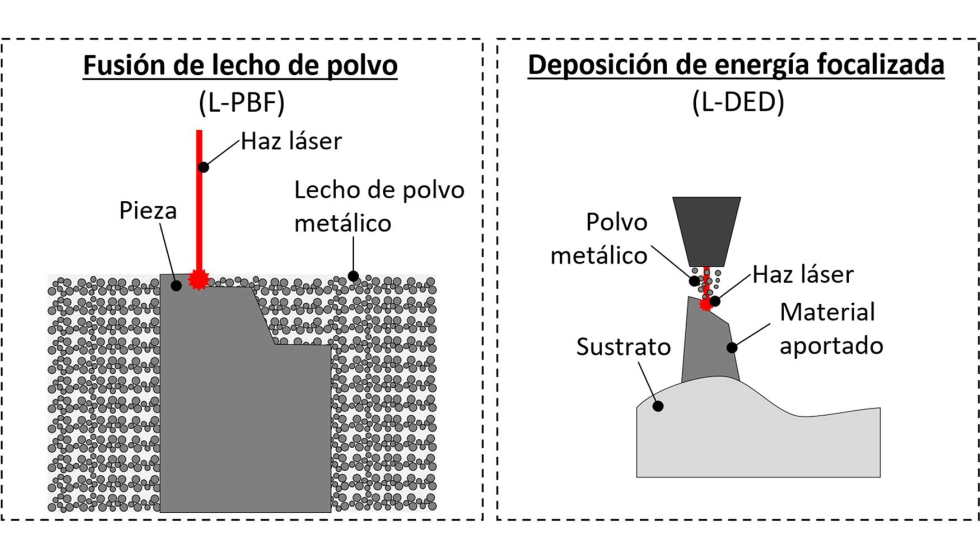
En los procesos de fusión de lecho de polvo, el haz láser incide sobre una capa de polvo previamente extendida en forma de lecho de polvo, de forma que se funden selectivamente las regiones de la capa que se corresponden con la geometría deseada. Mediante la fusión y solidificación selectiva de las regiones de interés se consolida la pieza final. Es importante resaltar que en los procesos de lecho de polvo se pueden emplear otras fuentes de energía, por ejemplo, un haz de electrones; siendo el principio de funcionamiento homólogo.
En los procesos de deposición de energía focalizada un haz láser incide sobre la superficie del sustrato, de forma que se genera un baño fundido. Simultáneamente partículas de polvo metálico se inyectan en dicho baño fundido. Cuando el material solidifica se genera un cordón, que debidamente solapado con otros cordones, da lugar a la geometría deseada. En este caso también se podría trabajar con fuentes de energía de diversa naturaleza (como son el arco eléctrico o el haz de electrones) y materias primas de diversa índole (hilo o polvo).
Los procesos de fabricación aditiva metálica previamente descritos son tecnologías de relativa madurez que ya se han consolidado en la industria. En ese sentido, se pueden fabricar componentes de gran integridad metalúrgica y excelentes propiedades mecánicas. Otra de sus principales ventajas es el amplio rango de materiales procesables, desde aceros inoxidables y de herramientas, hasta superaleaciones base níquel o cobalto, además de materiales híbridos como materiales compuestos o materiales con gradiente funcional de composición.
No obstante, bien es cierto que también tienen múltiples limitaciones que restringen su aplicación a casuísticas muy concretas. La fusión de lecho de polvo tiene una limitación inherente al proceso en lo que al tamaño máximo del componente se refiere. Esto se debe a que el proceso tiene lugar en una cámara inerte y, por tanto, el espacio de trabajo útil está directamente restringido por el tamaño de la misma. Los procesos de deposición de energía focalizada, por su parte, son muy flexibles en lo que a la geometría del sustrato se refiere, de forma que permiten la adición de material sobre superficies complejas. En lo que a calidad superficial se refiere, los procesos de fusión de lecho de polvo permiten alcanzar una resolución dimensional considerablemente mayor que los de deposición de energía focalizada y, por tanto, se puede obtener una rugosidad superficial menor. Sin embargo, en pocos casos es lo suficientemente buena como para poder prescindir de un post-procesado. En la misma línea, los procesos de fusión de lecho de polvo disponen de una mayor libertad geométrica en lo que a complejidad de geometría se refiere. Es por esto que, por regla general, los procesos de fusión de lecho de polvo se emplean principalmente para la fabricación de piezas funcionales, y el uso de los procesos de deposición de energía focalizada está más dirigido al recubrimiento y a la reparación de componentes de alto valor añadido.
En la figura 2 se muestran dos ejemplos de componentes aeroespaciales producidos mediante procesos de fabricación aditiva metálica. En ambos casos el material empleado es la aleación base Níquel Inconel 718 y se han realizado en el marco del proyecto de investigación Elkartek Imagine (KK-2021/00120) financiado por el Gobierno Vasco.
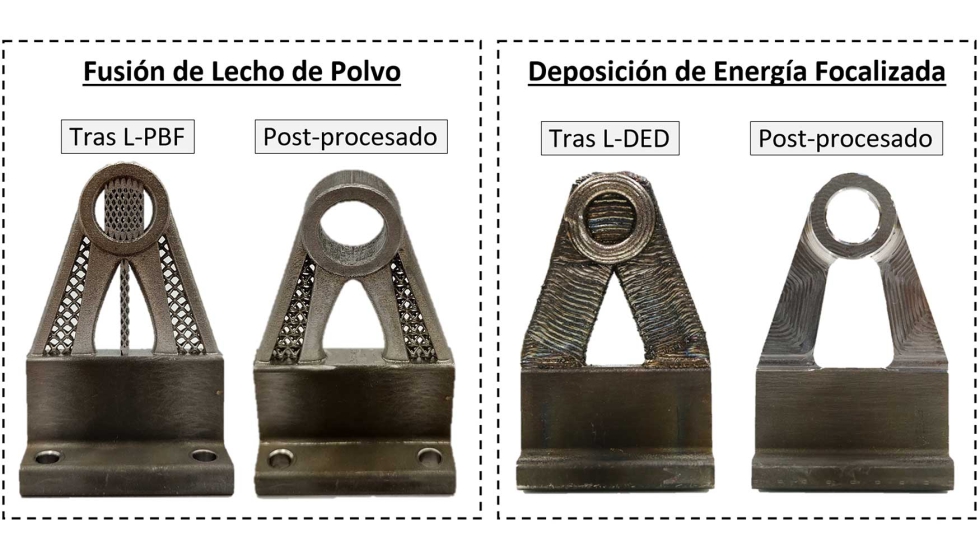
En todo caso, ambos procesos tienen cabida en el sector aeroespacial, y así lo demuestran las tendencias de mercado, ya que la industria aeroespacial es la que mayor tasa de crecimiento ha reportado en los últimos años en lo que a implementación de procesos de fabricación aditiva se refiere.
Oportunidades y retos de la fabricación aditiva en el sector aeroespacial
Desde una perspectiva general, las principales ventajas de la fabricación aditiva son (i) el incremento de la eficiencia del material, (ii) la capacidad de fabricar componentes con alta complejidad geométrica, (iii) la posibilidad de implementar estrategias de personalización aún en producción seriada, y (iv) la agilización de la cadena de suministro. Estas oportunidades de la fabricación aditiva están totalmente alineadas con los requerimientos de la industria aeroespacial, donde la tendencia actual es hacia la optimización geométrica de los componentes, que resulta en un incremento de su complejidad, y a la capacidad de personalización. De esta forma, el potencial impacto de la fabricación aditiva en la industria aeroespacial es innegable (Figura 3).
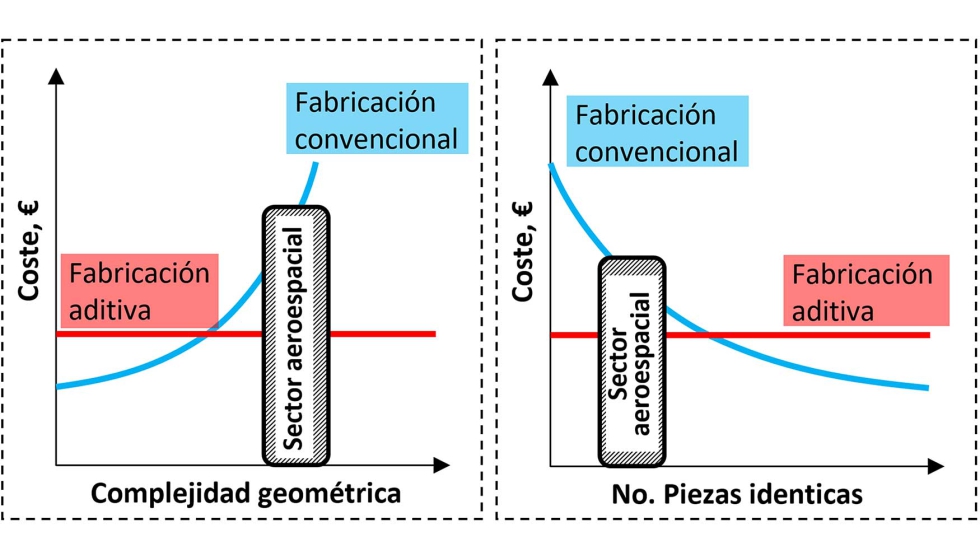
Una demanda que prevalece en el sector aeroespacial y que permanece inalterable a lo largo de los años es la necesidad de reducir el peso de los componentes. La principal motivación de esta tendencia es la mejora de la eficiencia energética de las aeronaves, con el fin de reducir el consumo de combustible y las consiguientes emisiones. Lógicamente, y de forma paralela, hay que mejorar la fiabilidad de los componentes y respetar los criterios que velan por la seguridad y el correcto funcionamiento de las aeronaves.
Es por esto que en el sector aeroespacial se emplean materiales altamente sofisticados que tienen una relación resistencia-peso muy alta, como pueden ser las aleaciones de titanio. Por otra parte, se requiere de materiales que además de ser altamente fiables y resistentes, no se degraden al operar a altas temperaturas, por ejemplo, las aleaciones base níquel. Este tipo de materiales tienen un coste alto, con lo que maximizar su utilización es uno de los retos de la industria, para reducir los costes de operación. En este sentido y debido a su naturaleza, los procesos de fabricación aditiva permiten un mejor aprovechamiento del material. En la industria aeronáutica se emplea la ratio buy-to-fly para cuantificar este aspecto. Este parámetro relaciona el peso de la materia prima requerida para la fabricación con el peso del componente que finalmente vuela. En el sector aeronáutico es habitual toparse con ratios buy-to-fly de hasta 40:1 en fabricación por medios convencionales, mientras que la fabricación aditiva permite reducir este parámetro a, virtualmente, 1:1.
Otra estrategia para la reducción de peso de los componentes aeronáuticos es la optimización de la distribución del material mediante herramientas de optimización topológica. De esta forma, se puede adecuar el diseño de componentes estructurales a los modos de carga concretos que tengan que soportar. Si bien el empleo de herramientas de optimización topológica no está explícitamente restringido a la fabricación aditiva, la libertad geométrica proporcionada por esta tecnología facilita la explotación de este tipo de recursos de una forma eficiente. En la figura 4, se muestra un ejemplo de esta herramienta, cuya implementación fue posible gracias a la fabricación aditiva. Cabe destacar, asimismo, que el componente mostrado ha sido certificado para su empleo en el espacio.
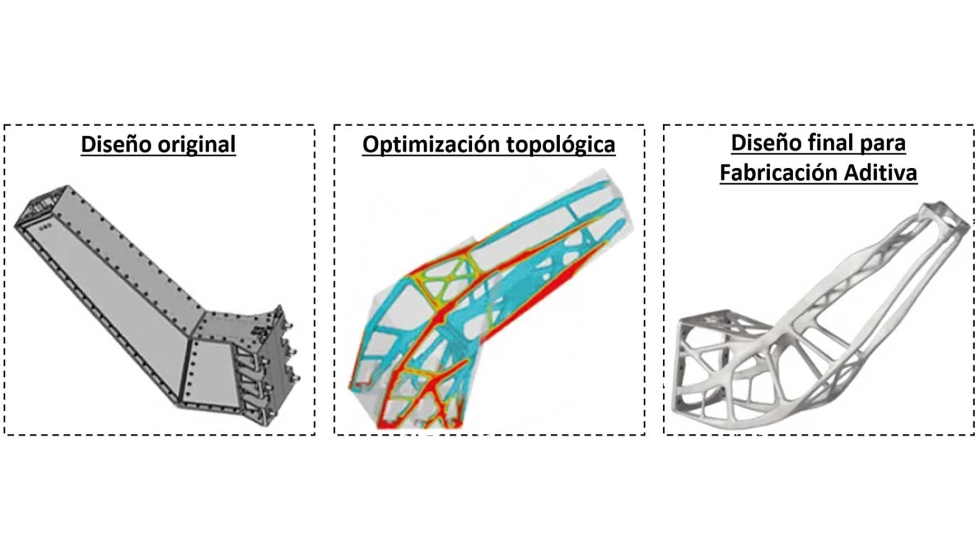
Por último, otra de las grandes ventajas de la fabricación aditiva en tanto en cuanto al sector aeronáutico se refiere es la agilización de la cadena de suministro. En este sentido, Airbus estimó que los tiempos para la producción de componentes de reemplazo podría reducirse a dos semanas gracias a la fabricación aditiva [1]. Igualmente, los costes asociados al mantenimiento y la reparación de componentes también pueden disminuirse sustancialmente gracias a estas tecnologías. En la figura 5 se resumen las oportunidades de la fabricación aditiva metálica en el sector aeroespacial, acorde a un estudio realizado por Deloitte.
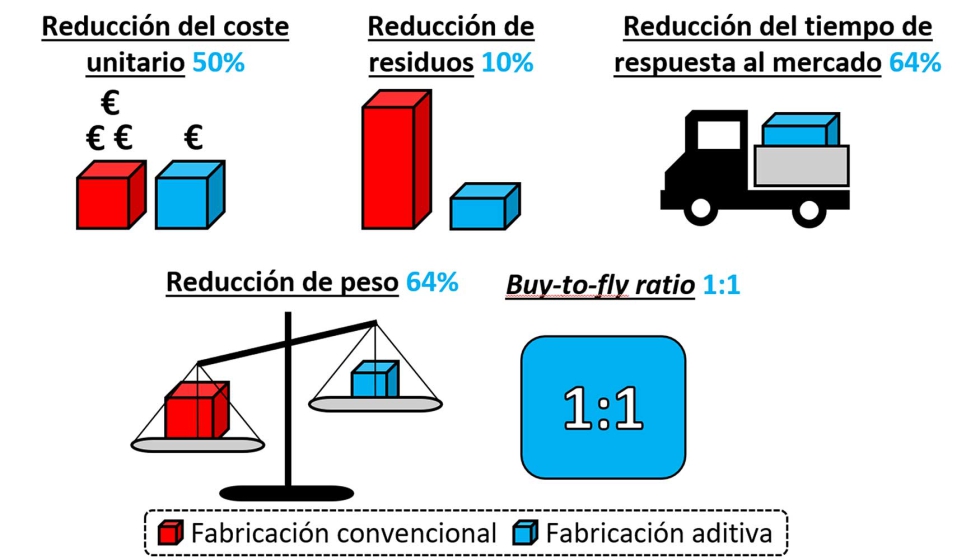
Sin embargo, hay una serie de retos que aún hoy en día dificultan la implantación de los procesos de fabricación aditiva en el sector aeroespacial. Por una parte, todos los procesos de fabricación aditiva metálica tienen, en mayor o menor medida, limitaciones en lo que a la resolución geométrica se refiere. Es por esto que, en la mayoría de los casos, es necesario introducir etapas de post procesado, ya sea para alcanzar la geometría deseada o mejorar la calidad superficial. Asimismo, es habitual que se generen defectos metalúrgicos durante la fabricación, tales como grietas o poros, lo cual genera incertidumbre en cuanto a la calidad de los componentes. Por otra parte, al tratarse de procesos basados en la fusión y solidificación local, se generan tensiones residuales y/o distorsiones que son difícilmente predecibles.
Aún con todo, el principal reto que afronta la fabricación aditiva en el sector aeroespacial es la falta de estándares sobre los que fundamentar la cualificación y certificación de componentes. Esta falta de consenso para la normalización de procesos aditivos por parte de los cuerpos de regulación genera una gran incertidumbre en torno a los procedimientos certificación. Esta brecha entre la madurez de la fabricación aditiva y la falta de estándares y regulaciones se debe principalmente a que los organismos de certificación no han podido anticiparse al rápido crecimiento de la fabricación aditiva metálica.
Certificación de la fabricación aditiva en el sector aeroespacial
La principal barrera que frena la certificación de componentes aeronáuticos es la falta de estándares consensuados que permitan asegurar su calidad y funcionamiento seguro. Por tanto, no existen protocolos claros y transparentes que guíen a las empresas durante las etapas de certificación en el caso de componentes producidos mediante fabricación aditiva, al menos no en el dominio público. Las empresas del sector perciben este proceso como ambiguo, ya que las entidades reguladoras no han establecido hojas de ruta para guiar la certificación de este tipo de componentes.
A nivel europeo, la EASA (European Union Aviation Safety Agency) es la agencia responsable de la certificación de componentes aeronáuticos. En Estados Unidos, por otra parte, la FAA (Federal Aviation Authority) es la responsable de esta tarea. Ambas entidades están trabajando en el desarrollo de estándares consensuados y protocolos de cualificación para facilitar la certificación de componentes aeronáuticos producidos mediante fabricación aditiva, de forma que la seguridad de los mismo quede absolutamente garantizada. En la figura 6, se muestra la jerarquía de los recursos y los documentos que gobiernan el proceso de certificación, desde directrices, hasta regulaciones y leyes.
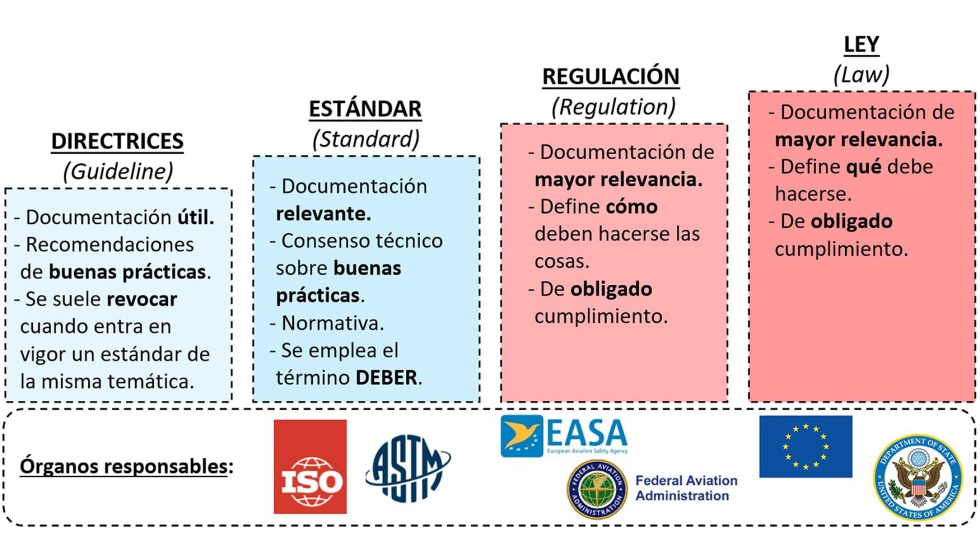
Por su parte, entidades internacionales dedicadas al desarrollo de estándares tales como la ASTM (American Society for Testing and Materials) o la ISO (International Organization for Standardization) también están trabajando de forma conjunta en este ámbito [2]. De hecho, en 2016, desarrollaron una hoja de ruta con el fin de acordar una estructura común para definir la jerarquía de estándares en tres niveles, a saber:
(i) Estándares generales de primer nivel para la definición de conceptos generales, y de requerimientos comunes y aplicables a todas las tecnologías.
(ii) Estándares específicos para categorías de proceso, dedicados a tipos de material base (filamentos, polvos) y/o categorías de proceso.
(iii) Estándares especializados, específico para el material, proceso de fabricación, y aplicación.
Fruto de esta colaboración, ya han sido publicados una serie de estándares cuyo objetivo es regular y homogeneizar los diferentes aspectos de los procesos de fabricación aditiva: desde la caracterización del polvo metálico, hasta la inspección micro estructural, o tratamientos térmicos de piezas metálicas producidas mediante fabricación aditiva.
La principal dificultad a la que se enfrentan las agencias de estandarización y de certificación es la falta de conocimiento integral de los fenómenos que gobiernan la generación de defectos como porosidad, anomalías microestructurales, o tensiones residuales, y cómo controlarlos. Esta incertidumbre complica notablemente la gestión de riesgos derivada de la implementación de los procesos de fabricación aditiva. El concepto que subyace bajo este reto es el hecho de que en los procesos de fabricación aditiva la calidad y el rendimiento del componente está estrictamente condicionado por el proceso de fabricación, las características del material base, y el post-procesado. Asimismo, las condiciones de fabricación dependen de una infinidad de parámetros y condiciones de contorno, cuya contribución a las propiedades del material no es siempre evidente.
Es por esto que, la certificación de componentes aeronáuticos producidos mediante fabricación aditiva hay que abordarla desde un punto de vista global y transversal a toda la cadena de suministro, implementando herramientas de control que aseguren la trazabilidad a lo largo de todas las etapas de producción. Sólo así podrán lograrse protocolos de cualificación que den lugar a una certificación segura. En la figura 7, se resumen los niveles en los que se tienen que aplicar los métodos de cualificación, según GE.
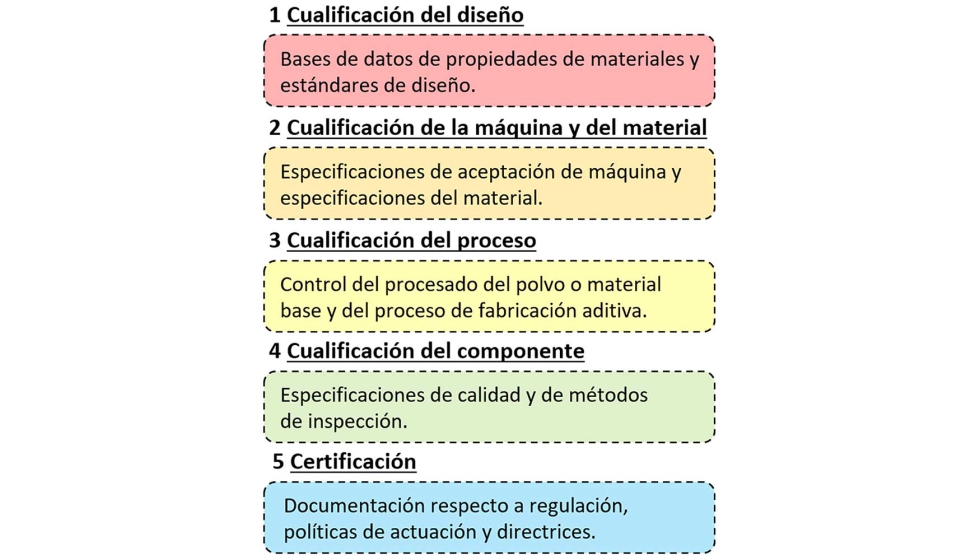
Sin embargo, los recursos para la cualificación y certificación disponibles hoy en día son insuficientes, por lo que compañías del sector aeroespacial han desarrollado sus propios procedimientos internos para el control de la calidad y la cualificación de componentes producidos mediante fabricación aditiva. Esta tarea requiere de una inversión ingente en ensayos experimentales, con el fin de garantizar que no surgen problemas de escalabilidad en la transición del entorno de laboratorio al de producción. De esta forma, es necesario demonstrar que, por una parte, los ensayos realizados a nivel de laboratorio son representativos de la pieza final, y que, por otra parte, los métodos de inspección no destructivos implementados a nivel de componente son garantes de su correcto rendimiento.
En este sentido, probablemente el caso de éxito más conocido en el ámbito de la aviación comercial es el de GE, que logró, ya en 2015, la certificación por parte de la FAA para el vuelo de un alojamiento de un sensor de presión y temperatura que forma parte del sistema de control del motor (Figura 8a) [3]. Asimismo, y bajo el amparo de los procedimientos de cualificación desarrollados internamente, GE logró la certificación, tanto por parte de la FAA como de la EASA, de un inyector de combustible para su modelo LEAP (Figura 8b) [4]. Este componente, además, entró en producción seriada y ya son más de 30.000 los inyectores producidos mediante fabricación aditiva [5].

Tras el éxito de estos dos proyectos, GE ha apostado por la fabricación aditiva metálica de un número elevado de componentes para su nueva serie GE9X que se empleará en el modelo 777X de Boeing. Concretamente, esta turbina cuenta con 304 piezas fabricadas mediante tecnologías aditivas. Entre ellos se incluyen álabes de aleaciones TiAl para la turbina de baja presión fabricados por fusión del lecho de polvo (en este caso con haz de electrones), intercambiadores de calor, vanos estáticos para la refrigeración de las primeras etapas de la turbina, y componentes de la cámara de combustión; todos ellos fabricados mediante fusión de lecho de polvo. [6]
En lo que a procesos de deposición de energía focalizada se refiere, Norsk Titanium fue la primera compañía en lograr por parte de la FAA la certificación para piezas estructurales de titanio. Estos componentes forman parte del modelo 787 Dreamliner de Boeing [7]. De hecho, Norsk Titanium se incorporó a la lista de proveedores autorizados de Boeing en 2015 y en 2018 uno de sus centros fue añadido a la lista de productores cualificados de Boeing. En la figura 9, se muestra uno de los componentes certificado por la FAA. Asimismo, Norsk Titanium está expandiendo su alcance en el mercado comercial del sector aeroespacial y se encuentra actualmente a la espera recibir la aprobación final que cualifique su tecnología para la producción seriada de componentes aeronáuticos para unos de los proveedores de primer nivel (tier one) de Airbus [8].
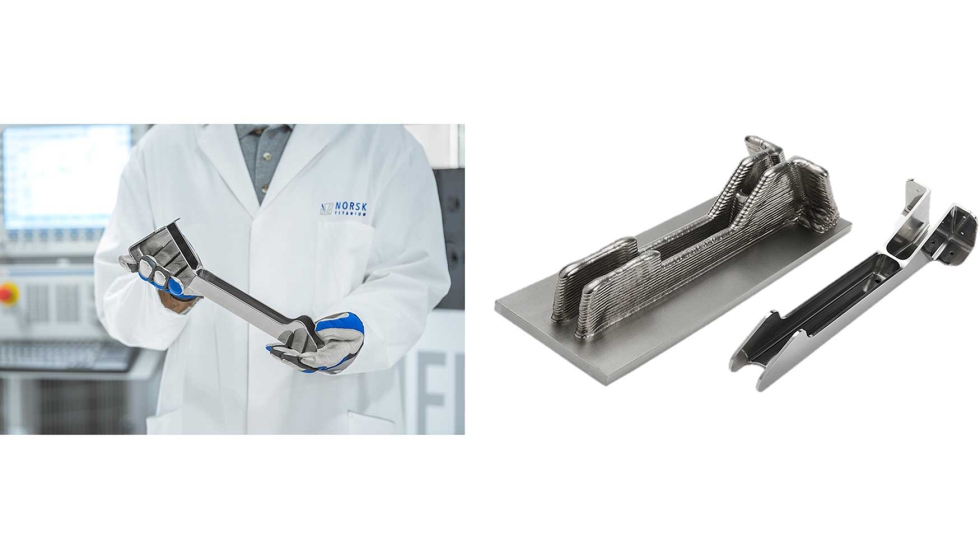
Además de haberse demostrado la valía de la fabricación aditiva para la producción de componentes funcionales, las oportunidades de estas tecnologías en el mercado de las operaciones de MRO (Maintenance, Repair and Overhaul) no pasan desapercibidas. De hecho, empresas de primer nivel ya están invirtiendo en la investigación de tecnologías de fabricación aditiva. Sin ir más lejos, en 2018 Lufthansa inauguró el Additive Manufacturing Center con el objetivo de establecer lazos de colaboración entre expertos de Lufthansa y especialistas en fabricación aditiva de otras empresas colaboradoras y/o instituciones, con el fin de impulsar la industrialización de los procesos de fabricación aditiva en el sector aeronáutico. Asimismo, Pratt & Whitney, compañía motorista líder del sector, también cuenta con su propio centro para el desarrollo de tecnologías aditivas, el Pratt & Whitney Additive Manufacturing Center. Estas compañías ya han implementado la fabricación aditiva para la reparación de componentes aeronáuticos, entre otras cosas.
Un caso de éxito en este ámbito es el del instituto Fraunhofer ILT que fue certificado por Rolls-Royce Deutschland para 15 aplicaciones de reparación. Entre ellas las mostradas en la figura 10, para la carcasa BR715 HPT. En esta misma línea cabe destacar el caso de la compañía Optomec que desarrolló la LENSTM Blisk Repair Solution específicamente para la reparación de rotores de álabes integrales u otros tipos de componentes aeronáuticos de alta complejidad geométrica.
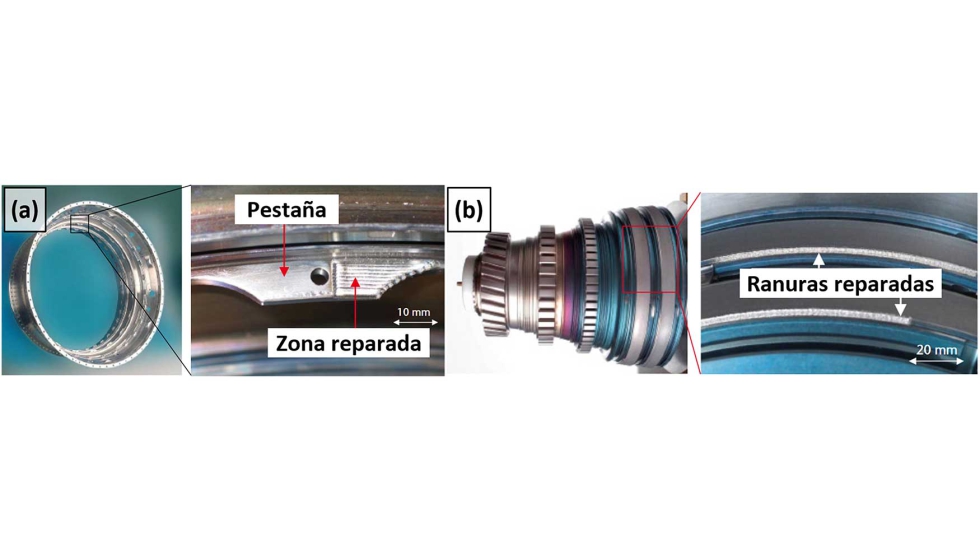
Por último, cabe citar que todos los ejemplos que se han indicado en este apartado corresponden con casos de aviación civil, los cuales, además de ser representativos, son de dominio público. En el caso del sector de defensa o espacial existen diversos casos de componentes que se han empleado tanto en aplicaciones estructurales como en componentes para los motores. En estos casos, se lleva a cabo un proceso de certificación diferente, ya que los requisitos funcionales y la vida esperada de los componentes es muy diferente. En cualquier caso, se trata de procedimientos que en muchas ocasiones son similares a los comentados y que exigen la máxima calidad de los componentes fabricados. La principal dificultad en este campo es que la información pública es mucho más limitada debido a la naturaleza secreta de estos componentes.
Conclusiones
Con todo lo descrito anteriormente, es innegable el interés de las empresas líderes del sector aeroespacial por la fabricación aditiva. No sólo eso, sino que la elevada inversión realizada por las mismas en lo que a la fabricación aditiva metálica respecta, pone en evidencia el rol de esta tecnología para aplicaciones aeroespaciales. De hecho, se espera que la fabricación aditiva siga creciendo en el sector, a medida que la investigación abra camino a nuevas oportunidades que o bien permitan reducir los costes de producción de componentes existentes o bien mejorar la eficiencia de las aeronaves a través de diseños avanzados.
No obstante, para alcanzar todo el potencial de la fabricación aditiva, es necesario que tanto las agencias gubernamentales como las propias compañías del sector se mantengan constantes en sus esfuerzos por garantizar la calidad y el correcto funcionamiento de componentes aeronáuticos. Para ello, es necesario ir adaptando los protocolos de cualificación y certificación que regulan hoy en día el mercado a la fabricación aditiva, y desarrollar nuevas metodologías de aseguramiento de la calidad e inspección cuando así se requiera. Así pues, es imprescindible que los lazos de colaboración ya establecidos sigan produciendo estándares y protocolos de certificación, pero también que se generen nuevas alianzas para maximizar el aprovechamiento de los esfuerzos realizados en la dirección de la certificación de componentes aeroespaciales producidos mediante fabricación aditiva.
Referencias
[1] J. C. Najmon, S. Raeisi y A. Tovar, «Review of additive manufacturing technologies and applications in the aerospace industry, » de Additive Manufacturing for the Aerospace Industry, 2019.
[2] ISO, «New agreement strengthens partnership bewteen ISO and ASTM on additive manufacturing., » 2011. [En línea]. Available: https://www.iso.org/news/2011/10/Ref1481.html. [Último acceso: 06 02 2023].
[3] General Electric, «The FAA Cleared the First 3D Printed Part to Fly in a Commercial Jet Engine from GE, » 2015. [En línea]. Available: https://www.ge.com/news/reports/the-faa-cleared-the-first-3d-printed-part-to-fly-2. [Último acceso: 06 02 2023].
[4] G. Daugherty, «CFM Leap-1A achieves dual certification, » GE Aerospace | The Blog, 2015. [En línea]. Available: https://blog.geaerospace.com/technology/cfm-leap-1a-achieves-dual-certification/. [Último acceso: 06 02 2023].
[5] General Electric, «New manufacturing milestone: 30,000 additive fuel nozzles, » 2018. [En línea]. Available: https://www.ge.com/additive/stories/new-manufacturing-milestone-30000-additive-fuel-nozzles. [Último acceso: 06 02 2023].
[6] B. Blakey-Milner, P. Gradl, G. Snedden, M. Brooks, J. Pirot, E. Lopez, M. Leary, F. Berto y A. du Plessis, «Metal additive manufacturing in aerospace: A review, » Materials & Design, vol. 209, 2021.
[7] Norsk Titanium, «Norsk Titanium to Deliver the World's First FAA-Aproved, 3D-Printed, Structural Titanium Components to Boeing, » 2017. [En línea]. Available: https://www.norsktitanium.com/media/press/norsk-titanium-to-deliver-the-worlds-first-faa-approved-3d-printed-structural-titanium-components-to-boeing. [Último acceso: 06 02 2023].
[8] Norsk Titanium, «Innovating the future of metal manufacturing, » 2022. [En línea]. Available: https://www.norsktitanium.com/storage/home/NTI-Q322-Update_Final.pdf. [Último acceso: 06 02 2023].