Nuevos avances en metrología y tomografía
El nuevo modelo metrológico implica la incorporación de sensores en la producción para realizar las mediciones en las propias máquinas donde se fabrican los componentes. De esta forma y con una sólida infraestructura y una rápida conexión entre los componentes de toda la fábrica, será posible alcanzar la fabricación con cero defectos, cero retrasos, cero sorpresas y cero desperdicios. Particularmente, la tomografía computarizada de rayos X se postula como respuesta a la inspección de componentes con características inaccesibles por otros métodos y a la adquisición holística de los datos que describen la geometría de las piezas.
Introducción
La 4ª revolución industrial está siendo cada vez más relevante en el amplio campo de la fabricación. La Industria 4.0 representa la nueva ola de tecnología que impulsa la eficiencia en todas las operaciones, basándose en sistemas ciber-físicos que combinan infraestructura física con software, sensores, nanotecnología y tecnología digital de comunicaciones. La transformación digital es necesaria para que las organizaciones compitan mejor en un entorno económico que cambia constantemente a medida que la tecnología evoluciona.
Son varias las razones clave por las que las empresas de fabricación de componentes industriales adoptan cada vez más las tecnologías de la Industria 4.0. Por un lado, las soluciones de monitorización de máquinas, las estrategias de mantenimiento predictivo y otras tecnologías operativas avanzadas están ayudando a los fabricantes a disminuir tiempos de inactividad, a aumentar el rendimiento y, en general, a reducir el costo de suministro de piezas de calidad. Otro aspecto relevante está relacionado con la democratización de los datos; la fabricación se ha visto afectada a lo largo de los años por disponer los datos en contenedores, donde la información no era compartida ni entre departamentos ni a nivel planta. La deseada conectividad está permitiendo una accesibilidad a fuentes de datos que hace años era impensable y, realizada correctamente, proporciona una manera fácil de utilizar esos datos para una toma de decisiones eficaz. Además, con la información digitalizada se puede almacenar una cantidad casi ilimitada de datos de fabricación a través de la nube que se pueden utilizar para capacitar a nuevos trabajadores, para crear algoritmos avanzados con datos históricos, etc. Las opciones son ilimitadas siempre que los datos estén almacenados y accesibles de tal manera que se puedan construir soluciones. Es un hecho que las tecnologías de digitalización e información brindan nuevas posibilidades a los ingenieros e ingenieras en el ámbito del diseño y planificación.
Metrología y el impacto de la Industria 4.0
La metrología también es un campo afectado por la transformación digital y la Industria 4.0, involucrando grandes desafíos y a su vez el fortalecimiento y mejora de las técnicas de medición. Por ello, muchas empresas ya han empezado a sincronizar y a replantear los procesos de medición para su adaptación a la Industria 4.0, desarrollando el nuevo concepto de la metrología 4.0.
Echando la vista atrás se puede comprobar cómo han ido evolucionando los sistemas metrológicos debido a la necesidad del control de calidad de componentes cada vez más complejos. La figura 1 muestra cómo ha sido el desarrollo de los sistemas de metrología durante las diferentes revoluciones industriales [1].
![Figura 1. Correlación entre los modelos industriales y la medición de la fabricación a lo largo del tiempo [1] Figura 1. Correlación entre los modelos industriales y la medición de la fabricación a lo largo del tiempo [1]](https://img.interempresas.net/fotos/3057609.jpeg)
El modelo metrológico dentro del marco de la Industria 4.0 implica la incorporación de sensores en la producción, a fin de realizar las mediciones en las propias máquinas donde se fabrican los componentes. Empieza a ser habitual el uso de diferentes tecnologías de medición, muchas veces basadas en principios físicos distintos, para la medición de las características de un mismo componente. Esto implica a su vez que las fuentes de error a compensar pueden ser de distinta naturaleza. En este sentido uno de los mayores retos a día de hoy es la fusión precisa de todos los datos captados por los sensores, ya que los resultados difieren entre técnicas y en muchos casos no son comparables.
Como ejemplo, en la figura 2 se muestra una misma superficie captada mediante un método óptico (fotones) y un método táctil (palpador). Debido a que el palpador no puede alcanzar todos los valles del perfil de rugosidad, se construye un falso límite, ignorando una parte importante de la rugosidad de la superficie [2]. Sin embargo, las tecnologías sin contacto pueden alcanzar cualquier región del contorno, evaluando la superficie real con mayor detalle.
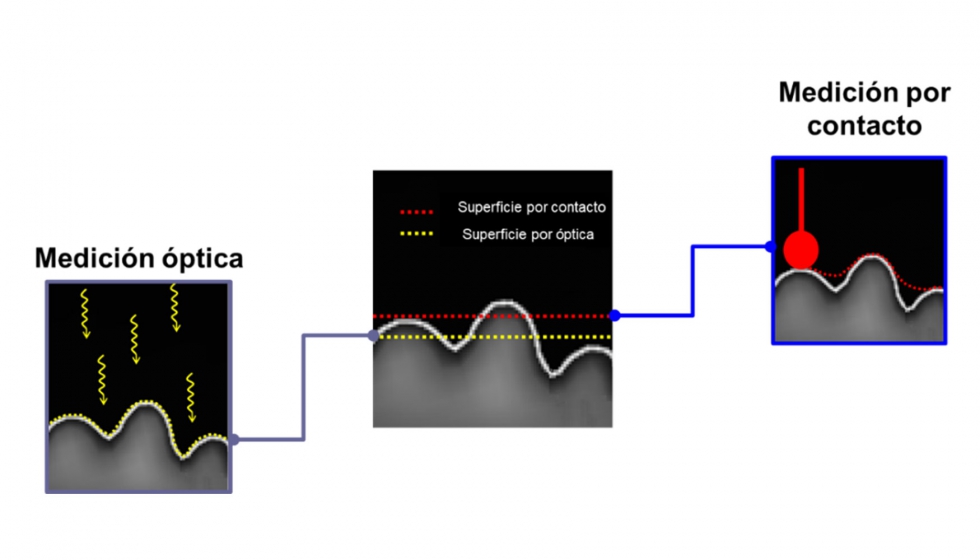
Retos y nuevos conceptos de la metrología 4.0
Uno de los principales retos de la metrología hoy en día es la medición de magnitudes multidimensionales con poca incertidumbre y en tiempo real. En este sentido es donde el rol de la Industria 4.0 se hace imprescindible, ya que permite maximizar la eficiencia y aumentar la calidad del rendimiento de los procesos metrológicos [4].
Otro reto principal de la Industria 4.0 en términos de inspección es aumentar su calidad y maximizar el rendimiento de la fabricación, lo que llevaría a reducir los costos en la línea de producción y a conseguir un sistema productivo con cero desperdicios. A día de hoy, más del 50% del material utilizado en la producción termina en chatarra. Esto no solo es un problema económico, sino medioambiental [5]. Utilizar de manera eficiente la energía, asegurar el origen responsable de los recursos y garantizar el cumplimiento y la expansión de los procesos de reciclaje permitirá el desarrollo de procesos y fábricas sostenibles.
Pero para que todo esto sea una realidad a nivel industrial, es necesario transformar el concepto convencional de control de calidad basado en la fabricación en masa, las correcciones estadísticas, ... hacia el nuevo concepto de calidad de la producción con cero defectos. Este nuevo enfoque viene esquematizado en la figura 3, y puede aplicarse tanto a la producción en masa como a piezas individuales [1].
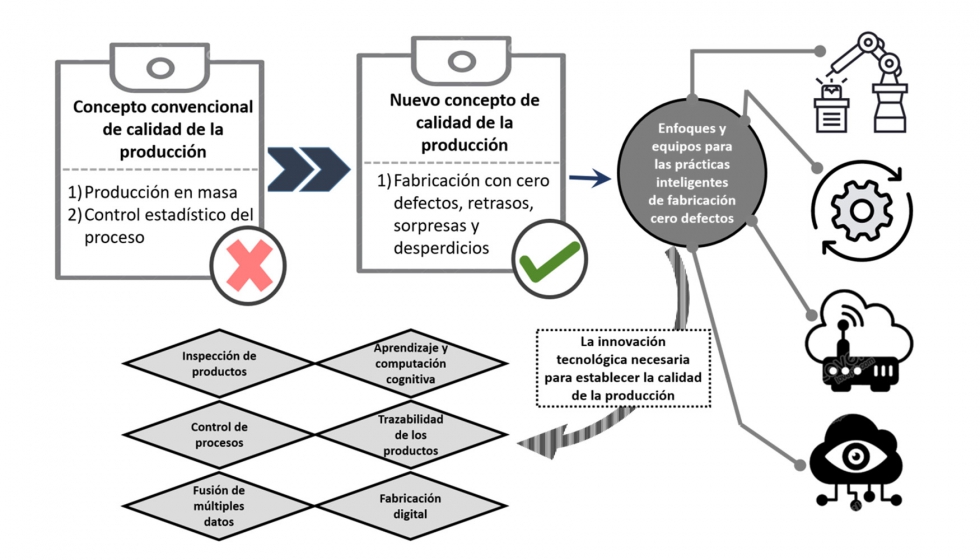
Tal y como puede observarse, al avanzar hacia la metrología 4.0 y en el camino de la fabricación de 0 defectos, los fabricantes deben implementar prácticas de fabricación inteligentes con los siguientes enfoques y equipos [6]:
- Automatización: la carga y descarga robótica de componentes puede involucrar los procesos de medición dentro de la línea de producción. De esta forma se produce una minimización de errores debido a una menor transferencia y manipulación de las piezas. La conectividad entre estos sistemas de medición y las máquinas de fabricación va a permitir un ajuste de las variables y errores en el proceso a tiempo real. Además, eliminar la intervención del operador reduce el error humano, protegiendo la calidad de la línea de producción y asegurando un mayor nivel de confiabilidad dentro de estos procesos. Es por ello que el principal objetivo es emplear mediciones “inteligentes” que permitan al sistema determinar los fallos y corregirlos automáticamente.
- Operación de circuito cerrado: la fabricación de ciclo cerrado integra en el mismo proceso las operaciones de fabricación y de la inspección, lo que reduce los costes y mejora la calidad. Este bucle cerrado no se diseña únicamente para automatizar el control de calidad, sino que también eleva el nivel de precisión de la fabricación, garantizando que su línea de producción sea del nivel más alto posible.
- Monitoreo en la nube: el monitoreo en la nube permite que los sistemas de medición se comuniquen, soliciten y envíen datos, así como que cambien y modifiquen las mediciones mediante funciones autónomas inteligentes. La infraestructura virtualizada puede aportar numerosas ventajas a un sistema de metrología. Por ejemplo, la información relevante puede almacenarse a distancia y recuperarse cuando sea necesario, facilitar la colaboración en el lugar de trabajo, etc.
- Comunicación y conectividad: un gran parte del enfoque de la Industria 4.0 es el intercambio de datos en red entre máquinas para maximizar la eficiencia de la producción. En este sentido, se incorporan sensores de todo tipo en los procesos productivos con capacidad para comunicarse e intercambiar datos, lo que hace posible que la máquina de fabricación produzca cambios, interrumpa o inicie la producción, así como el montaje de una herramienta de sustitución. Además, mediante la rapidez de la nueva tecnología 5G, se tiende a conseguir una producción con cero retrasos.
Con esta nueva forma de proceder se hace hincapié en la garantía de calidad/funcionalidad de las piezas mediante la informatización de todos los procesos de fabricación, y no sólo en la magnitud geométrica de las piezas fabricadas como índice para medir la calidad.
No obstante, un aspecto fundamental a tener en cuenta son los factores críticos que introducen las no deseadas fuentes de error de los procesos de fabricación. Estos factores han de ser informatizados para su control y corrección, pudiendo garantizar una fabricación con cero defectos [1]. La figura 4 muestra esquemáticamente dichas fuentes de error.
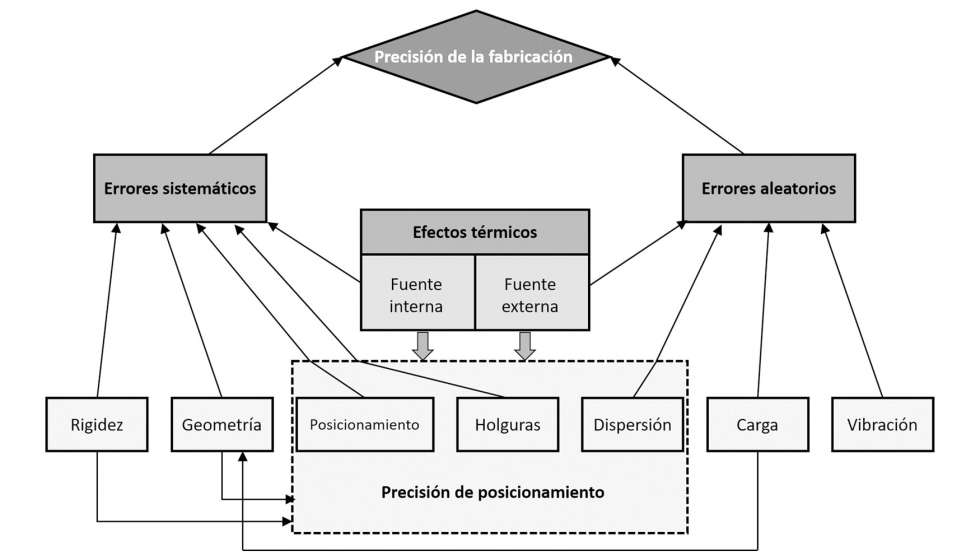
Sin embargo, para llevar a cabo estos nuevos controles de calidad, se requiere de una innovación tecnológica en lo que concierne a las máquinas de medición o sistemas de captación de datos [5]. Afortunadamente, el crecimiento y desarrollo de equipos de medición más sofisticados y el desarrollo de nuevos softwares se ajustan a los requerimientos de la metrología 4.0, haciendo todo esto posible. Los sistemas o sensores de digitalización y escaneado 3D son los más prometedores debido a la gran cantidad de datos que pueden captar. Este es el caso de los sistemas de procesamiento de imágenes y de visión, la tomografía computarizada por rayos X (TC), la luz estructurada, entre otros [7].
En definitiva, el control de calidad de la producción basado en la medición holística (información de todo el proceso de fabricación), junto con la buena gestión de la gran cantidad de datos, es la clave para lograr un sistema de producción predictivo y una fabricación con cero defectos, cero sorpresas, cero retrasos y cero desperdicios. En muchas ocasiones, todo esto viene respaldado por modelos multifísicos de simulación, que, junto al gran input de datos de los sensores, es posible acabar prediciendo la representación digital de los componentes. Ejemplos de herramientas utilizadas para este tipo de simulaciones son la fluidodinámica computacional (CFD) y el análisis de elemente finitos (FEA).
Las tareas de digitalización y medición holística de todo el proceso de fabricación generan nuevos modelos como es el caso de los modelos cíber-físicos (CPS) [1]. Estos modelos tienen dos partes, una virtual y otra física (la máquina), las cuales están conectadas por la infraestructura del Internet Industrial de las Cosas (IIoT). Como la principal misión es ajustarse de manera inteligente y predictiva a los cambios holísticos de la medición en tiempo real según el contenido medido (información sobre el entorno de la medición, la condición de la medición, la cantidad medida, el objeto de la medición, la condición del mecanizado, la precisión requerida, la tolerancia, la incertidumbre, etc.), la configuración de la fusión de los datos captados por los sensores cambia y se adapta continuamente para lograr una predicción avanzada. Capacidades como el auto-reconocimiento de las piezas, el auto-mantenimiento de la propia máquina y la auto-predicción son obtenidas por los modelos CPS.
El IIOT es por tanto la red de medición inteligente en proceso/en máquina conectada en el espacio virtual, como se muestra en la figura 5, el contenido almacenado de las mediciones y la información de las mismas se comparte entre las máquinas de fabricación bajo el control de IIOT.
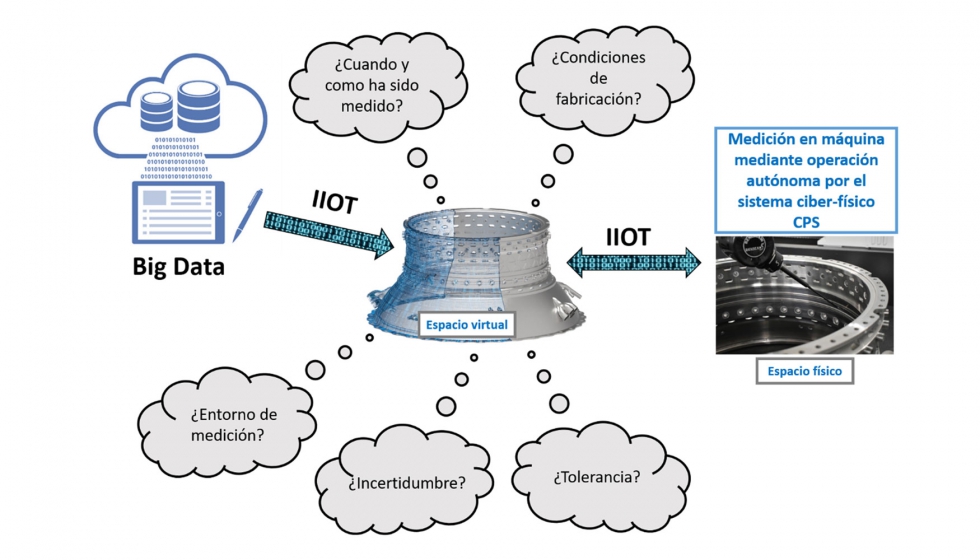
Desde la perspectiva de la Industria 4.0, el concepto CPS implica el desarrollo de la medición inteligente para realizar el control de calidad de la producción. Como resumen, la estrategia de medición fundamental en la metrología 4.0 consiste en realizar la “informatización de todos los procesos relacionados con la fabricación” mediante el desarrollo de la medición holística basada en la integración de diferentes principios de medición y la fusión de datos multiescala.
Concepto de medición holística
El concepto de medición holística implica grandes conjuntos de datos que son analizados por el Big Data mediante técnicas de inteligencia artificial (IA), generando las características metrológicas clave y simplificando la gran cantidad de datos almacenados. El desglose de esta información se realiza mediante el IIoT, y sus elementos conforman la infraestructura del modelo global CPS (Ver figura 5). No obstante, toda esta nueva forma de proceder requiere de calibraciones y validaciones avanzadas, de nuevas teorías para evaluar la incertidumbre, así como del desarrollo de nueva normativa a fin de regular los requisitos actuales y futuros de la industria [8].
Un ejemplo actual de medición holística inteligente son las nuevas MMC multisensor con rayos X (medición volumétrica) [9]. Gracias al desarrollo de la tecnología de fusión de datos, con herramientas que integran datos como CAD/CAE/CAM/CAT, se definen nuevas bases para un control de calidad de la producción avanzado, conectando los diferentes sistemas de medición entre sí a través de IIoT, como ya se ha comentado anteriormente. Una utilización eficiente de la IIoT dentro del marco de metrología 4.0 se describe en bibliografía [10].
Un punto clave en la captación de datos es hacerlo sin interferir en la pieza en un tiempo relativamente corto. En este sentido, las tecnologías que mayor potencial demuestran son las técnicas de escaneado 3D y sin contacto (sin interferir con la pieza). Por ejemplo, la tecnología de medición óptica, incluyendo los rayos X, está progresando rápidamente y a día de hoy ya se han desarrollado sistemas capaces de alcanzar resoluciones que permiten medir el microperfil de una superficie, el perfil 3D y la estructura interna 3D simultáneamente [11]. La metrotomografía (metrología mediante tomografía computarizada), en particular, está progresando de forma significativa y se está proponiendo su incorporación a los procesos en línea y a las aplicaciones para la inspección del proceso de los ensamblajes dado su gran potencial [12]. En la figura 6 se muestran diferentes técnicas de escaneo sin contacto, así como la velocidad de escaneo de cada una de ellas.
![Figura 6. Avances en las tecnologías de medición 3D para la medición industrial [1] Figura 6. Avances en las tecnologías de medición 3D para la medición industrial [1]](https://img.interempresas.net/fotos/3057615.jpeg)
Un grupo muy competitivo y que contiene técnicas de inspección de mucho valor dentro de la metrología 4.0 son las que tradicionalmente se identifican como tecnologías no destructivas (END). Entre este tipo de técnicas encontramos las corrientes inducidas, los ultrasonidos o las imágenes de transmisión directa de rayos X. Estas técnicas permiten el análisis cualitativo y en algunos casos el cuantitativo tanto de las características externas como internas de las piezas. La figura 7 muestra una clasificación en la que se comparan las técnicas END en función de la localización de la característica a medir y la complejidad de la geometría de la pieza frente a la resolución espacial. Tal y como se observa en la figura 7, los métodos ópticos pueden alcanzar resoluciones de medición relativamente altas (en el rango de los nanómetros) cuando se emplean técnicas de interferometría, pero, en el caso de las muestras opacas, sólo pueden inspeccionar características en la superficie. Los ensayos por corrientes inducidas y las técnicas ultrasónicas pueden detectar características dentro del volumen, pero el único inconveniente es la limitada resolución espacial, que se sitúa en el rango de los milímetros y que depende de la profundidad de la característica por debajo de la superficie [13]. En cambio, el mejor método para la inspección no destructiva y cuantitativa de estructuras y geometrías complejas dentro del volumen de una pieza es actualmente la tomografía computarizada de rayos X, con un rango de resolución que va de los milímetros a los nanómetros.
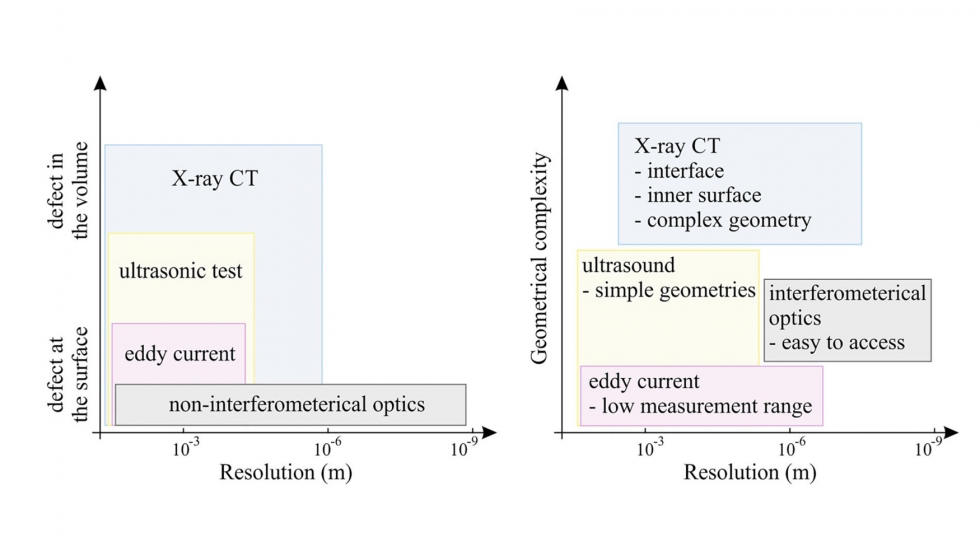
Como resumen, los esfuerzos para desarrollar la tecnología de fusión de medidas son continuos, tal y como lo demuestran muchos estudios recientes [1]. Sin embargo, siguen existiendo retos técnicos específicamente relacionados con la fusión de datos multiescala, como la calidad de los datos de medición, incluida la incertidumbre y los métodos de normalización y calibración, entre otros. Aun así, la tomografía computarizada por rayos-X (TC) es actualmente considerada como la mejor técnica para la inspección holística y no destructiva de estructuras y geometrías complejas y no complejas, pudiendo medir tanto características internas como externas de las piezas [11].
Tomografía computarizada e Industria 4.0
Para la Industria 4.0, el uso eficiente del Big Data es de gran importancia ya que permite el desarrollo de algoritmos que se ajustan al proceso de fabricación, favoreciendo una producción consistente, eficiente y, sobre todo, con cero defectos. En este sentido, dentro de la medición holística impulsada por la Industria 4.0, la captación de los datos 3D mediante sistemas de no contacto durante todo el proceso de fabricación juega un rol vital. Con los datos 3D, es posible analizar y comparar el diseño inicial de un componente y el resultado final tras su fabricación. Con la buena calidad y gestión de estos datos, apoyado con las nuevas herramientas que ofrecen los sistemas ciber-físicos (CPS) y el internet industrial de las cosas (IIOT), se pueden resaltar las áreas problemáticas y se pueden realizar ajustes instantáneos en el proceso de fabricación, por ejemplo, actualizando continuamente los archivos CAM que dirigen las trayectorias de las herramientas.
Automatizando un proceso de captación de datos 3D, se reducen drásticamente las tasas de fallos y de desechos, mejorando la eficacia general y la rentabilidad de la producción. Por esta razón, las soluciones avanzadas de metrología óptica 3D no destructiva mejoran la calidad, la cantidad y la rapidez con la que se recogen los datos, perfeccionando los procesos de fabricación.
Actualmente, las nuevas tecnologías emergentes de fabricación, como es el caso de la fabricación aditiva, ofrecen la posibilidad de fabricación de geometrías muy complejas, pero no exentas de la posibilidad de contener defectos internos. Los nuevos y complejos diseños requieren métodos de inspección avanzados, como es el caso de la tomografía computarizada de rayos X (TC) que puede medir de forma no destructiva las características internas y externas de las piezas, sea cual sea la geometría. Más en detalle, la TC puede utilizarse para la evaluación cuantitativa de la porosidad, el análisis dimensional, caracterizar estructuras complejas e incluso rugosidades de superficie.
En la práctica un escaneo TC consiste en someter al espécimen a una radiación de rayos X a lo largo de un giro completo (360º) mediante incrementos angulares pequeños. En cada incremento angular, un detector de rayos-X capta la información de la atenuación de los rayos X a través de la pieza, creando imágenes 2D para cada posición angular. Estas imágenes son posteriormente utilizadas por un algoritmo para realizar la reconstrucción 3D del objeto escaneado. Este modelo 3D está basado en muchos vóxeles, el cual tiene el tamaño del pixel del detector digital interpolado en una tercera dimensión (pixel volumétrico). La figura 8 muestra un esquema del funcionamiento típico de un escaneo por tomografía computarizada de rayos X [13].
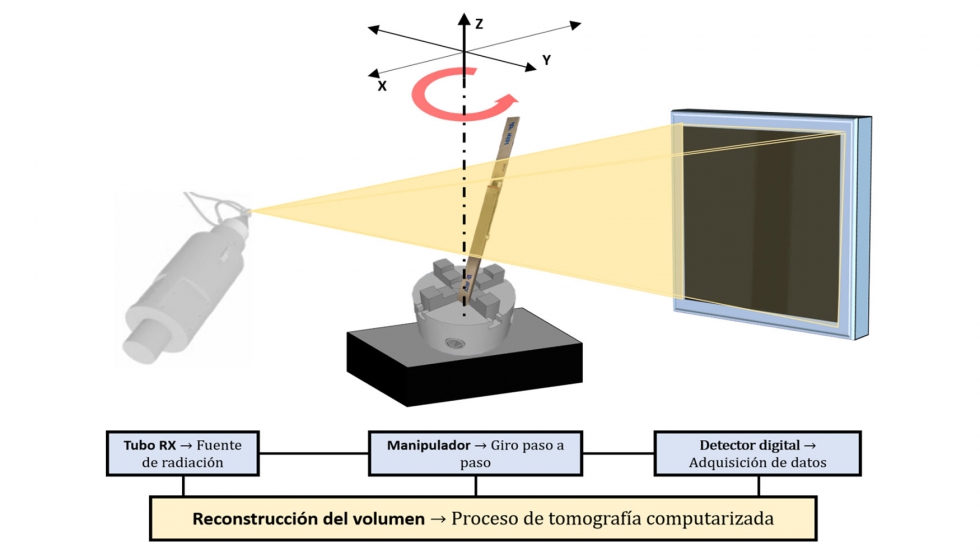
Una vez obtenidos los escaneos, son varios los pasos a seguir para alcanzar la aplicación metrológica de la TC. En la siguiente figura 9 se describen los pasos que figuran en las guías alemanas VDI 2630, parte 1.2 [14], las cuales son un método aceptado por la comunidad metrológica internacionalmente [11].
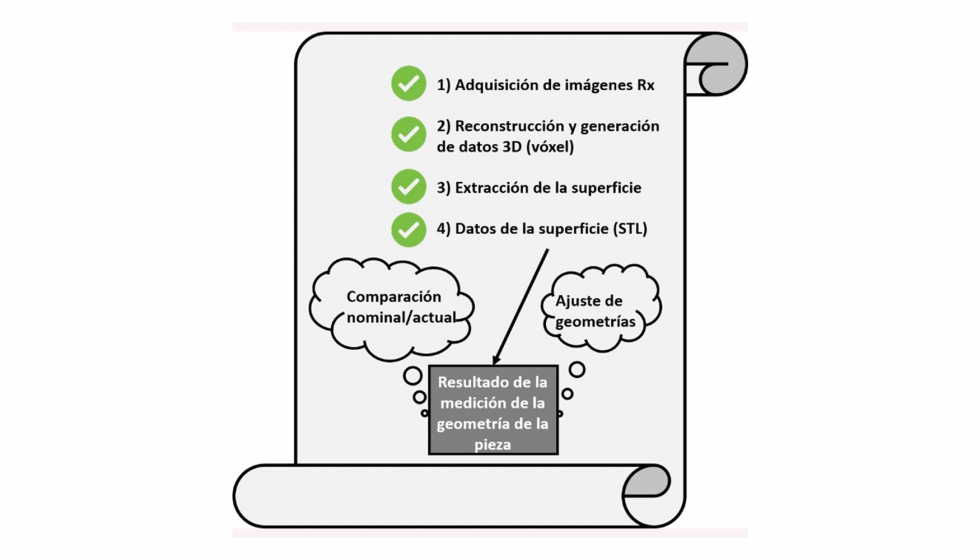
Los pasos son los siguientes:
- En primer lugar, el escaneado del objeto. Los parámetros seleccionados para esta tarea son la magnificación, orientación del objeto, energía de los rayos-X y tiempo de integración del detector.
- Obtenidas las proyecciones 2D de toda la pieza, se reconstruye el volumen 3D. Este volumen se modela como una matriz 3D de vóxeles, donde cada vóxel representa el coeficiente de atenuación local del objeto escaneado (nº de gris). En este punto se pueden aplicar diferentes técnicas de corrección sobre las proyecciones 2D para minimizar diferentes efectos no deseados como el beam hardening, la radiación dispersa, etc.
- Se selecciona un valor para el threshold, es decir, el valor de gris límite que va a separar lo que es pieza del ambiente en el que se encuentra. Para ello, existen diferentes métodos de segmentación, siendo el método global (ISO50) y el local adaptativo lo más utilizados [15]. La segmentación es un paso crucial ya que afecta directamente a la geometría que se va a medir.
- Una vez segmentada la pieza del entorno en el que se encuentra, es posible crear un modelo en formato STL, caracterizado por una malla poligonal con forma de triángulos sobre la superficie del objeto.
- Medición directa del modelo.
- Obtención de resultados.
Cabe destacar que los volúmenes 3D obtenidos mediante TC suelen ser muy pesados debido a la gran cantidad de información que contienen. Por ejemplo, cuando se emplea un detector común de 1.000 x 1.000 pixeles, y cada pixel recibe y almacena un valor de 2 bytes, se obtiene un tamaño de datos de 2 Gbytes de volumen 3D (1.000 x 1.000 x 1.000 vóxeles). Con tal tamaño de archivos, es vital un uso eficiente del Big Data.
En general, la TC ofrece posibilidad de análisis de datos a gran escala gracias a la recopilación de un conjunto completo de datos volumétricos. Además, proporciona un nivel de flexibilidad y velocidad sin precedentes para las tareas de metrología que no pueden ser alcanzadas con los métodos clásicos de contacto, ya que éstos recogen los datos característica por característica o punto por punto. La principal diferencia entre la tecnología TC y los métodos clásicos proviene directamente del modo en el que se recogen los datos, como se muestra en la figura 10. Se compara un sistema óptico (TC) con uno táctil (MMC), Como se puede ver en este ejemplo, el cilindro A es de muy difícil acceso y el método de contacto sólo puede adquirir puntos de los extremos superior e inferior del cilindro. Sin embargo, la tecnología TC adquiere un gran número de puntos en todo el volumen.
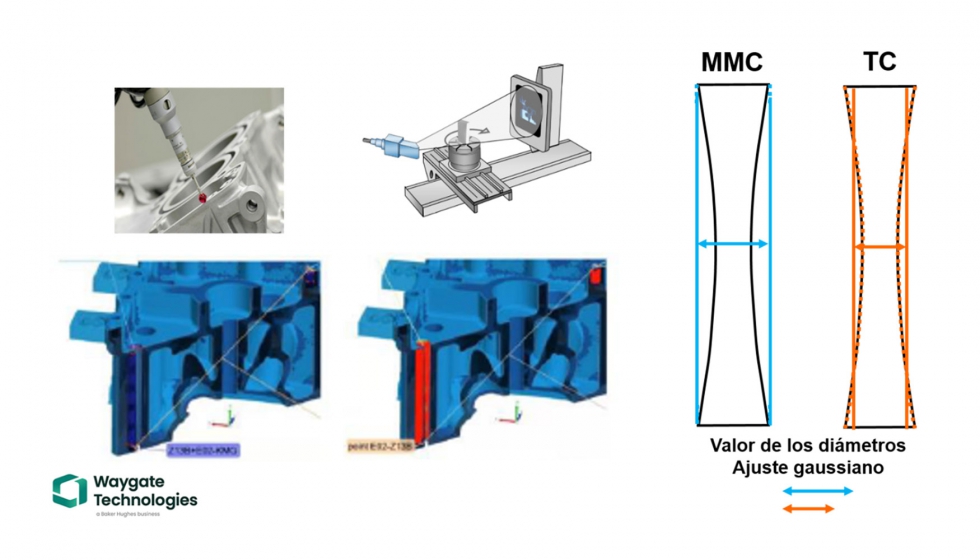
Por otro lado, la figura 11 muestra el tiempo de escaneado frente al número de características a medir en una pieza mediante la TC y la tecnología táctil CMM. El resultado muestra que la tomografía es mucho más rápida que las máquinas de medir por coordenadas cuando el número de características a medir aumentan.
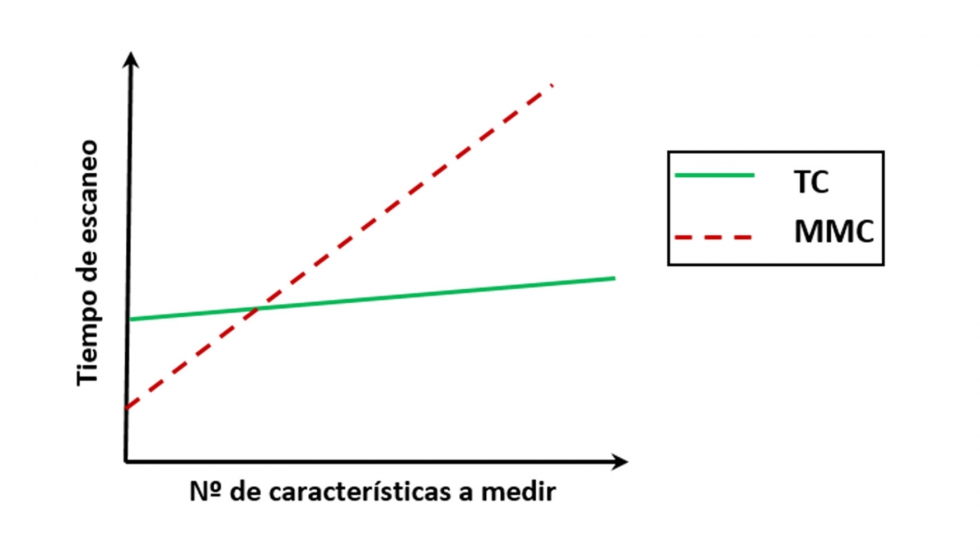
Casos implementados en la industria
Tal y como se ha mencionado a lo largo del artículo, la Industria 4.0 induce a una evolución de medición en línea con el proceso productivo. Un ejemplo actual son los sistemas de Tomografía Computarizada operados por robots industriales que cargan y descargan de forma autónoma los componentes a inspeccionar [16]. La figura 12 se muestra una aplicación de la empresa Zeiss.
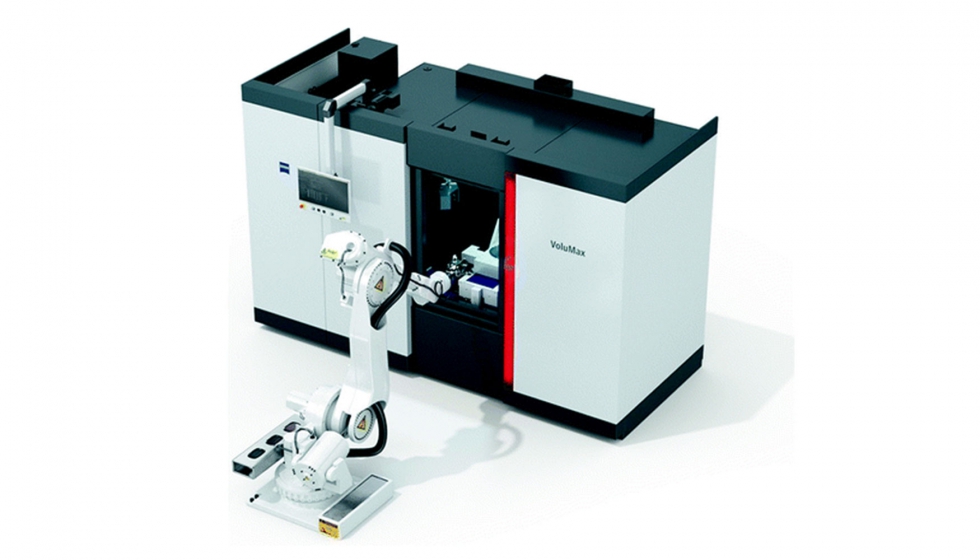
Este tipo de automatizaciones tendrá sin duda cabida en el nuevo término de la metrología 4.0 y reducirá el camino hacia la fabricación cero defectos. Además, la TC se puede integrar en los sistemas inteligentes de control de calidad con el apoyo de sistemas ciber-físicos CPS comentados anteriormente. La amplia información de datos de medición de las piezas escaneadas por TC también puede ser analizada mediante Big Data y transferida con rápidas conexiones inalámbricas de IIoT, modificando y corrigiendo al instante la producción.
Otro ejemplo es la opción presentada por la empresa General Electric (GE), que utiliza un sistema TC de inspección en línea mediante una cinta transportadora y una trayectoria de escaneo helicoidal de TC, tal y como se muestra en la figura 13.
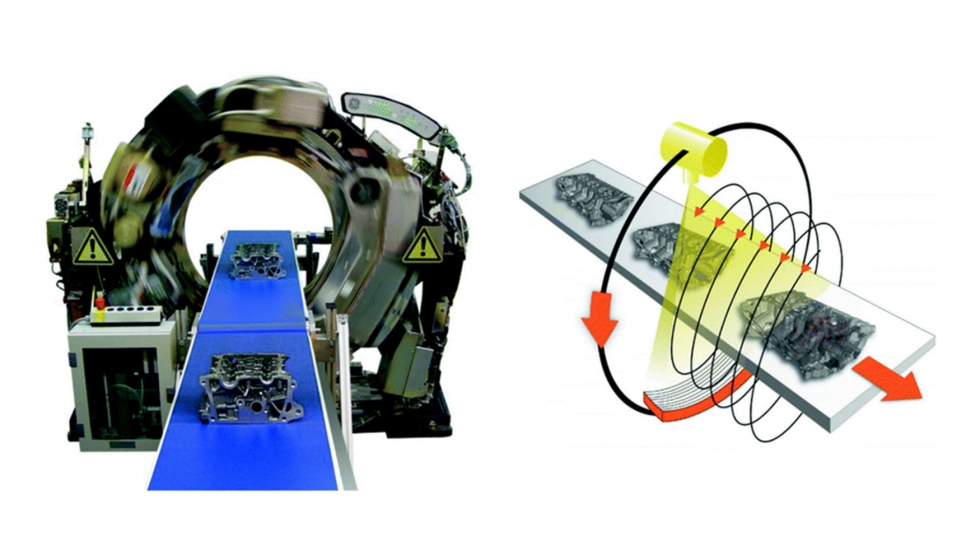
El movimiento de traslación puede lograrse mediante el movimiento de la pieza producido por una cinta transportadora, o con un movimiento combinado de la fuente y el detector [15]. En la mayoría de casos, la TC helicoidal adquiere datos mientras el tubo de rayos X y el detector giran a una velocidad angular constante a la vez que la pieza se desplaza (a una velocidad constante) a lo largo del eje normal a ambos componentes. Este tipo de escaneos tienen un gran potencial en las aplicaciones industriales [17] ya que son escaneos muy rápidos, alcanzando velocidades de inspección de entre uno y cinco minutos por pieza.
Desafíos y tendencias de la tomografía computarizada
A pesar de estar en el camino correcto, todavía quedan muchos desafíos que superar para alcanzar las fabricaciones con cero defectos. Sin embargo, tal y como se ha desarrollado en este artículo, la tomografía computarizada de rayos X puede ser una respuesta a la inspección de características inaccesibles y a la adquisición holística de los datos que describen la geometría de las piezas. Las tecnologías de medición por contacto que aún se utilizan en la inspección de piezas industriales, requieren de mediciones adicionales por cada característica a inspeccionar. Además, algunas de las características ni siquiera pueden adquirirse con una incertidumbre adecuada, por ejemplo, las características de ensamblaje. En la figura 14 se muestran las principales ventajas y desventajas de la tomografía computarizada como método de inspección en el contexto de la metrología 4.0.
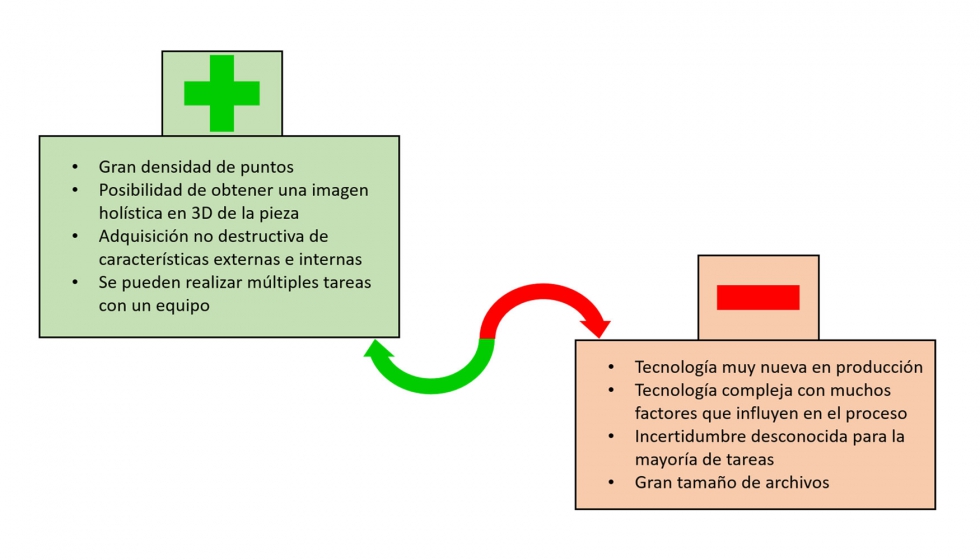
Tal y como se indica, uno de los principales desafíos es ampliar el conocimiento y reducir la influencia de las fuentes de error del proceso de tomografiado. En la figura 15 se pueden visualizar las fuentes de error que contribuyen tanto al proceso de medición como al análisis de los datos de la TC para las mediciones dimensionales [13].
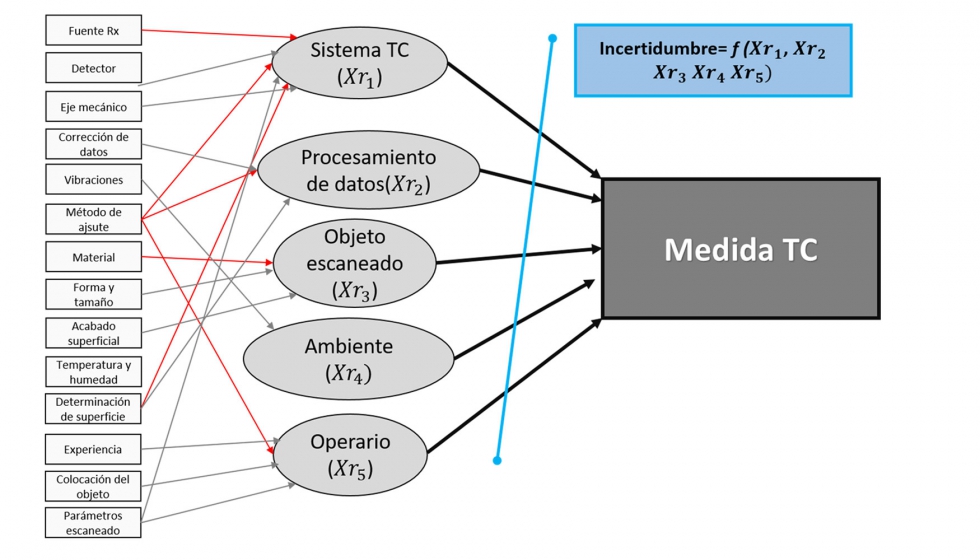
Por todo ello, a pesar de los recientes esfuerzos de normalización, hasta la fecha todavía no existen normas internacionales que proporcionen procedimientos y directrices completos para la verificación del rendimiento de la metrología dimensional de los sistemas de TC. Además, para determinar la incertidumbre de medición del proceso de tomografía, la normativa que recoja los procedimientos de medición deberá reflejar el uso real del instrumento de medición e incluir procedimientos de prueba que sean sensibles a todas las fuentes de error ya mencionadas en la Figura 16, algo todavía inexistente.
Por ahora, el único documento de referencia con procedimientos para la estimación de incertidumbre de las mediciones TC es la directriz 2630-1.3 publicada por la asociación de ingenieros alemanes VDI/VDE en 2011 [18]. Sin embargo, los procedimientos descritos en las directrices VDI/VDE no son exhaustivos. Por lo tanto, los esfuerzos por crear normas internacionales para los ensayos de aceptación de la metrología dimensional de TC se han intensificado recientemente, lo que ha dado lugar a nuevas ideas de ensayo que se están debatiendo actualmente en diferentes comités científicos en todo el mundo. Actualmente, existe un documento borrador que está siendo debatido a nivel de normalización internacional por el grupo de trabajo TC del comité técnico 213, del grupo de trabajo (WG) 10 de la ISO. Este grupo es el responsable de crear normas internacionales (serie ISO 10360) para los ensayos de aceptación de los sistemas de medición por coordenadas.
En la siguiente figura 16 se detalla qué entidades se prevé que van a avanzar en las labores más importantes para la aceptación de la tomografía como la herramienta del futuro de la metrología 4.0 [19].
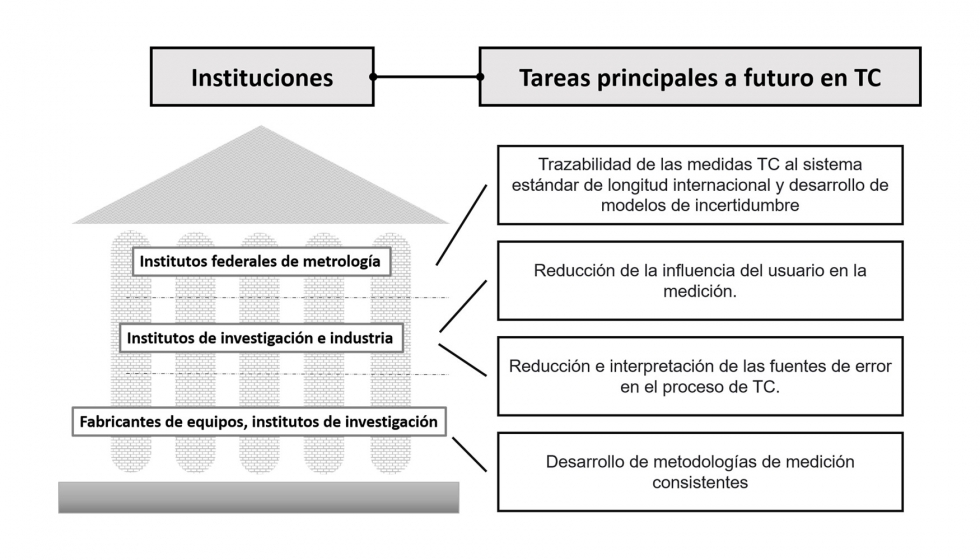
El CFAA tiene actualmente 2 líneas de investigación abiertas dentro de la inspección por tomografía computarizada. Actualmente se están desarrollando procedimientos trazables de medición en piezas de Inconel 718, muy utilizadas en aeronáutica. En este sentido, ya han sido varias las contribuciones del grupo sobre la influencia de ciertas variables del proceso de escaneado en la incertidumbre de medida TC. Por ejemplo, se han desarrollado estudios sobre el efecto del material de filtrado sobre las mediciones TC, el efecto de la magnificación y el tamaño de foco, entre otros.
Por otro lado, son necesarias metodologías de medición consistentes para que la TC pueda considerarse una tecnología precisa y fiable. Actualmente se están desarrollando metodologías trazables de inspección en componentes multimaterial, lo que supone todo un reto a día de hoy. Por otra parte, ya están siendo desarrollados e implementados en el centro procesos de inspección de ciclo cerrado mediante la automatización del proceso de medición, algo vital para avanzar en la metrología 4.0.
Bibliografía
[1] TAKAYA, Y. Strategic Vision for Smart Machining Tool and Measuring Instrument.
[2] Boeckmans, B., Tan, Y., Welkenhuyzen, F., Guo, Y., Dewulf, W., & Kruth, J. P. (2015). Roughness offset differences between contact and non-contact measurements. In Proceedings of the 15th international conference of the European society for precision engineering and nanotechnology (pp. 189-190).
[3] https://www.powerdata.es/big-data Visitada el 16/10/2021
[4] Castelo-Branco, I.; Cruz-Jesus, F.; Oliveira, T. Assessing Industry 4.0 readiness in manufacturing: Evidence for the European Union. Comput. Ind. 2019, 107, 22–32.
[5] Varshney, A., Garg, N., Nagla, K. S., Nair, T. S., Jaiswal, S. K., Yadav, S., & Aswal, D. K. (2021). Challenges in Sensors Technology for Industry 4.0 for Futuristic Metrological Applications. MAPAN, 1-12.
[6] https://www.ogpuk.com/news/industry-4-0-future-metrology/ Visitada el 12/10/2021
[7] TAKAYA, Y. Strategic Vision for Smart Machining Tool and Measuring Instrument.
[8] M. Compare, P. Baraldi and E. Zio, Challenges to IoT-Enabled Predictive Maintenance for Industry 4.0, IEEE Internet of Things Journal, 7, 5, 4585–4597, 2020.
[9] Weckenmann, A., Jiang, X., Sommer, K. D., Neuschaefer-Rube, U., Seewig, J., Shaw, L., & Estler, T. (2009). Multisensor data fusion in dimensional metrology. CIRP annals, 58(2), 701-721.
[10] Ministry of Economy, Trade and Industry, Ministry of Health, Labor and Welfare, Ministry of Education, Culture, Sports, Science and Technology, 2017 White Paper on Manufacturing Industries Overview; FY2016 Promotion measures of core manufacturing technology (Overview), (2017).
[11] Villarraga-Gómez, H., Herazo, E. L., & Smith, S. T. (2019). X-ray computed tomography: from medical imaging to dimensional metrology. Precision Engineering, 60, 544-569.
[12] L. De Chiffre, S. Carmignato, J.-P. Kruth, R. Schmitt, A. Weckenmann, Industrial applications of computed tomography, CIRP Annals – Manufacturing Technology, Vol.63/2, (2014), 655-677.
[13] Khosravani, M. R., & Reinicke, T. (2020). On the use of X-ray computed tomography in assessment of 3D-printed components. Journal of Nondestructive Evaluation, 39(4), 1-17.
[14] Technical guideline (draft) VDI/VDE 2630, Computed tomography in dimensional measurement, Part 1.1. Basics and definitions (2007), Part 1.2. Influencing variables on measurement results and recommendations for computed tomography dimensional measurements (2008) and Part 1.4. Measuring procedure and comparability (2008)
[15] Runje, B., Horvatic Novak, A., Orošnjak, M., & Beloševic, A. Influence of surface determination on CT measurement results. Matrib 2018, Materials, Tribology, Recycling.
[16] Ametova, E., Probst, G., & Dewulf, W. (2018). X-ray computed tomography devices and their components. In Industrial x-ray computed tomography (pp. 69-98). Springer, Cham.
[17] Aloisi V, Carmignato S, Schlecht J, Ferley E (2016) Investigation on metrological performances in CT helical scanning for dimensional quality control. In: 6th conference on industrial computed tomography (iCT), 9–12 Feb, Wels, Austria
[18] VDI/VDE 2630-1.3. Computed Tomography in Dimensional Measurement - guideline for the application of DIN EN ISO 10360 for coordinate measuring machines with CT sensors. Berlin (Germany): Beuth Verlag GmbH; 2011.
[19] Kruth, J. P., Bartscher, M., Carmignato, S., Schmitt, R., De Chiffre, L., & Weckenmann, A. (2011). Computed tomography for dimensional metrology. CIRP annals, 60(2), 821-842.