Componentes de turbomaquinaria mediante mecanizado súper abrasivo: enfoque global
Dentro de los procesos innovadores que han surgido dentro de la fabricación de componentes aeronáuticos se encuentra el mecanizado súper abrasivo (“Super Abrasive Machining”, SAM). Esta técnica consiste en el empleo de pequeñas herramientas abrasivas de CBN bajo condiciones de corte de fresado de gran desbaste. Como resultado, se obtienen mayores ratios de arranque de material a altas velocidades que en comparación con los procesos de rectificado convencional, obteniendo una geometría muy próxima a la final requerida. Actualmente, una de las principales aplicaciones más prometedoras de esta técnica es su aplicación para la fabricación de juntas de montaje de los álabes individuales que componen las partes rotativas de los motores aeronáuticos conocidas como fir trees. El mecanizado mediante SAM presenta un mejor comportamiento a la hora de enfrentarse a materiales de baja maquinabilidad, como son las aleaciones de titanio o base níquel presentes en muchos de los componentes críticos rotativos de los motores aeronáuticos.
El trabajo que se presenta en este artículo desarrolla una metodología para la fabricación de componentes rotativos de motor aeronáutico. Concretamente una serie de álabes en Inconel 718. Para ello se han realizado una serie de ensayos con el objetivo de obtener las condiciones óptimas de fabricación mediante SAM de dicho componente. Como reto adicional, cabe destacar que la complejidad del mecanizado de dicha geometría reside en que se trata de una superficie no desarrollable. Por tanto, para su mecanizado se ha utilizado un algoritmo desarrollado por el centro de matemáticas aplicadas del País Vasco, BCAM. Gracias este algoritmo se ha posibilitado la generación de una trayectoria de acabado mediante la técnica flank milling con la intención de optimizar el proceso de mecanizado y reducir costes en términos de tiempo máquina y durabilidad de herramienta.
1. Introducción
La industria aeronáutica se encuentra actualmente en constante crecimiento, siendo uno de los sectores estratégicos del mercado. Según afirma el Tedae (Asociación de Empresas Tecnológicas de Defensa, Aeronáutica y Espacio), este sector genera una facturación del orden de 7.600 millones de euros, de los cuales el 9,5% es destinado para I+D+i [1]. Esta inversión surge de la necesidad de afrontar la competitividad existente a nivel mundial, lo que se traduce en unas exigencias no sólo relacionadas con las propiedades mecánicas de los componentes durante su vida útil, sino en la optimización de los procesos de fabricación para la obtención de éstos.
Esta tesitura toma especial relevancia en componentes críticos presentes en los turbopropulsores aeronáuticos; entre ellos, cabe destacar los compresores axiales utilizados en aviación civil. Este tipo de componentes son conocidos como blisk (bladed disk) e IBR (Integrally bladed rotor), los cuales se diferencian por el tipo de unión de los diferentes álabes al disco. Como se muestra en la figura 1, los blisk se caracterizan por tener sus álabes independientes al disco, ensamblados mediante uniones conocidas como fir tree. En cambio, los IBRs están formados por una sola pieza en las que los álabes son solidarios al propio disco, en este caso son mecanizados a partir del mismo material de partida.
![Figura 1. Esquema de disco de compresor y turbina. (a) Blisk. (b) IBR. [2] Figura 1. Esquema de disco de compresor y turbina. (a) Blisk. (b) IBR. [2]](https://img.interempresas.net/fotos/1614817.jpeg)
Figura 1. Esquema de disco de compresor y turbina. (a) Blisk. (b) IBR. [2].
Durante su vida útil, este tipo de componentes son sometidos a condiciones de trabajo extremas. Esto hace necesaria la utilización de aleaciones de titanio y termorresistentes como las aleaciones de base níquel [3] ya que este tipo de materiales se caracterizan por combinar altas durezas con baja conductividad térmica y alta ductilidad. La combinación de dichas propiedades mecánicas se traduce en materiales difficult to cut, es decir, son aleaciones que presentan una baja maquinabilidad [4]. Además, en el caso concreto del Blisk, no sólo existen dificultades a la hora de ser mecanizado, sino que como reto adicional se encuentra la generación de las uniones fir tree de las que está dotado el disco. Dichas uniones se caracterizan por estar compuestas de una geometría compleja con estrechas tolerancias tanto dimensionales como superficiales [5]. Por todo ello, tradicionalmente dichas uniones se fabrican mediante la tecnología EDM (Electro discharge Machining). Este proceso no convencional de mecanizado destaca por ofrecer la posibilidad de mecanizar cavidades con geometrías completas en materiales de alta dureeza, aportando buena precisión dimensional, combinada con un excelente acabado superficial [6]. Sin embarto, el principal inconveniente de esta tecnología se encuentra e nlos bajos ratios de arranque de material que presenta, lo que supone que los tiempos de fabricación de estos componentes sea elevado. Es por esta razón que se están realizando diversos estudios en busca de nuevas tecnologías que puedan suplir dicha carencia.
Por todo ello, y con el fin de aumentar la productividad, actualmente se encuentra en desarrollo una tecnología que combina las condiciones de corte de mecanizado convencionales con herramientas de rectificado. Esta técnica es conocida como Super Abrassive Machining (SAM) y se caracteriza principalmente por combinar las ventajas del mecanizado por arranque de viruta con las del rectificado. Su aplicación al mecanizado de fir trees está suponiendo un aumento exponencial de la productividad de los blisk que hace que su implementación esté siendo un hecho (figura 2).
![Figura 2. SAM aplicado al mecanizado de fir trees. `7, 15] Figura 2. SAM aplicado al mecanizado de fir trees. `7, 15]](https://img.interempresas.net/fotos/1614818.jpeg)
Por otra parte, este proceso se está extrapolando a otras geometrías de mayor complejidad geométrica como es la fabricación de los propios álabes de los IBRs o impellers. Entre las principales ventajas que ofrece dicha tecnología cabe destacar que en su fabricación se obtienen mayores ratios de arranque de material a altas velocidades y, a su vez, se consigue, una geometría muy próxima a la final requerida.
Además, el SAM ofrece un comportamiento excelente de la hora de enfrentarse a materiales de baja maquinabilidad, como es el caso de aleaciones de titanio y base níquel, utilizadas en este tipo de componentes, debido a que las herramientas utilizadas son de nitruro de boro cúbico policristalino (PCBN). Sin embargo, hay que destacar que, a diferencia de otros procesos de mecanizado convencionales, donde se utilizan herramientas de PCBN, se hace necesario la utilización de fluidos de corte (refrigeración mediante aceite) debido a las temperaturas y condiciones tan extremas a las que es sometida la herramienta [8,9].
Por todo ello, en este trabajo se propone la utilización, no sólo de la tecnología SAM para el mecanizado de álabes de blisk, sino también de una técnica derivada de la misma. Esta técnica es conocida como Flank SAM la cual aún está en desarrollo y está ideada para el acabado de los propios álabes. Gracias a ello se busca, no sólo reducir tiempos de fabricación, sino mantener la integridad superficial de la pieza a la vez que se posibilita la realización de la totalidad del blisk en una sola atada y pasada.
2. Montaje experimental
Para realizar la fase experimental se ha escogido como material el Inconel 718. Este material es una la aleación de base níquel-hierro endurecido mediante precipitado de sus fases secundarias de su matriz metálica (45HRc). Se ha escogido dicho material a razón de que constituye uno de los materiales más utilizados en la industria aeronáutica y, por consiguiente, es idóneo para testear el comportamiento del SAM frente al mecanizado convencional. A continuación, se muestra (Tabla 1) la composición química de dicho material.
Ni |
Cr |
Co |
Fe |
Nb |
Mo |
Otros |
52,5% |
19% |
1% |
17% |
5% |
3% |
1,79% |
Ti |
Al |
B |
C |
Mn |
Si |
|
1% |
0,6% |
0,01% |
0,08% |
0,35% |
0,35% |
|
Este tipo de superaleación termorresistente se caracteriza por disponer entre sus propiedades mecánicas una buena resistencia a fatiga y creep combinado con una alta resistencia a la corrosión trabajando a altas temperaturas. Sin embargo, estas propiedades provocan que durante el mecanizado se obtengan altas fuerzas de corte, bajas tasas de arranque de viruta, adhesiones y otros problemas como difusiones y desgastes abrasivos en la herramienta [10-14]. De este modo, al utilizar este material durante las pruebas experimentales se obtienen unas condiciones de mecanizado agresivas que muestren de forma inequívoca las ventajas de un proceso frente al otro. Los ensayos experimentales se han realizado en un centro de mecanizado Ibarmia ZV-25/U600 del tipo RRLLL, es decir, dicho centro está caracterizado por constar de 5 ejes de los cuales tres son lineales (X, Y, Z) y dos son rotativos (A, C).
Por otra parte, para las operaciones de desbaste mediante fresado se ha utilizado una fresa de diámetro 16 mm de metal duro recubierto de AlTiN; para el SAM se ha utilizado una muela de PCBN de 16 mm de diámetro y 20 mm de longitud de corte. Para las operaciones de acabado mediante fresado se ha optado por una herramienta de 6 mm de diámetro y 1 mm de radio de punta, y para las operaciones de SAM se ha utilizado la misma muela utilizada en el desbaste. En la Tabla 2 se resumen las diferentes condiciones de corte utilizadas en cada una de las estrategias de mecanizado.
DESBASTE ACABADO
|
Milling |
Flank SAM |
Flank Milling |
Flank SAM |
ap (mm) |
20 |
20 |
20 |
20 |
ae (mm) |
16 |
16 |
0,2 |
0,2 |
F (mm/min) |
45 |
2 |
45 |
500 |
S (rpm) |
400 |
18.000 |
400 |
18.000 |
En cuanto a las estrategias de mecanizado, éstas consistieron en un desbaste y acabado con cada una de las técnicas descritas anteriormente, respectivamente. Durante el proceso, se registraron los datos de las fuerzas de corte mediante la utilización de un dinamómetro triaxial piezoeléctrico Kistler 9255 y un analizador OROS(r) OR35 con una frecuencia de muestreo de 16.384 muestras/segundo. El montaje experimental se muestra en la figura 3.
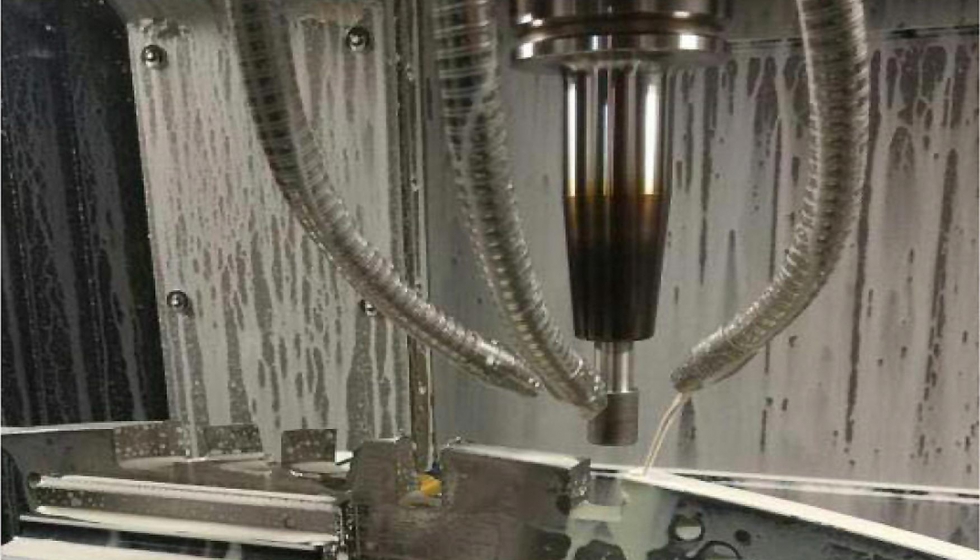
3. Resultados y discusión
En los siguientes subapartados se procede a la exposición y análisis de los resultados obtenidos con ambas estrategias de mecanizado mediante fresado convencional y SAM, así como las fuerzas de corte obtenidas durante su ejecución.
3.1. Proceso de desbaste
Para las operaciones de desbaste se han realizado dos ranuras aplicando para cada una de ellas fresado convencional y mecanizado mediante SAM respectiva mente. El principal objetivo de realizar el desbaste mediante estas dos técnicas es comparar una tecnología innovadora (SAM) frente a la técnica tradicional (fresado). Esta nueva tecnología de taca por su comportamiento frente a materiales de baja maquinabilidad aleaciones de titanio y de base níquel) proporcionando mayores ratios de arranque de material y mejor respuesta de herramienta. Por otra parte, cabe destacar que, al tratarse de herramientas de rectificado, se evita un desgaste pronunciado análogo al de las fresas y por tanto, la rotura incontrolada de la herramienta, proporcionando una mayor precisión dimensional que los procesos de fresado convencionales. En la figura 4 se muestran dos imágenes representativas e ambos procesos.
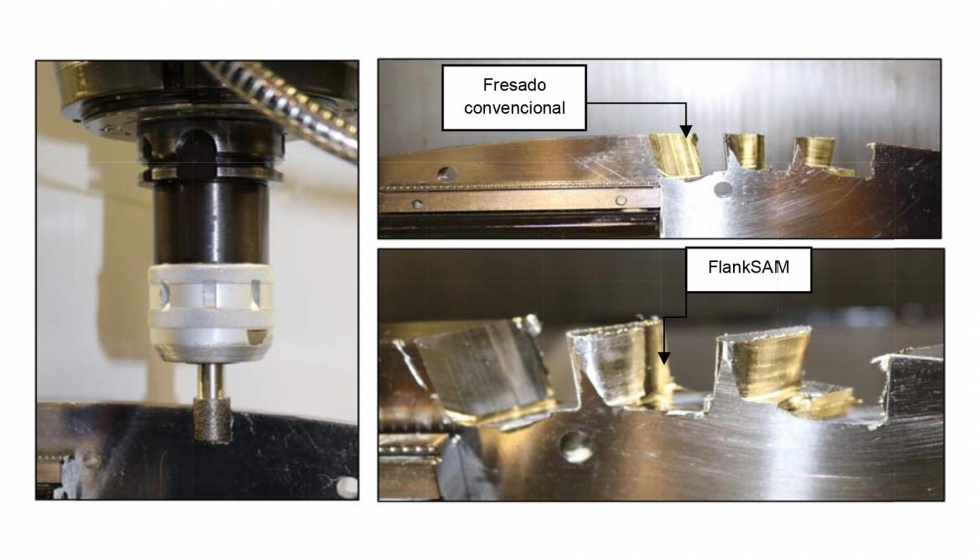
Figura 4. Desbaste mediante fresado convencional y mediante Flank SAM (UPV/E HU).
A raíz de la ejecución del desbaste se ha observado que el mayor inconveniente a tener en cuenta con la técnica de mecanizado mediante SAM son los requisitos de máquina que exige esta tecnología. Entre ellos la necesidad de refrigeración mediante aceite y velocidades de husillo entre 20.000 y 80.000 rpm [15]. Por esta razón, las condiciones aplicadas en el desbaste se han visto limitadas por la capacidad del equipo disponible, lo que a su vez ha condicionado que los ratios de arranque de material sean inferiores a los esperados para dicha tecnología.
3.2. Proceso de acabado
Para la realización de las estrategias de acabado se ha utilizado un algoritmo desarrollado en Pengbo Bo et al. [16] para la aproximación de formas libres mediante evolventes, adaptándose a una geometría de herramienta en concreto. Gracias a este algoritmo se posibilita la realización de un mecanizado mediante la técnica de Flank milling. Por tanto, para las operaciones de acabado de los álabes individuales se ha aplicado dicho algoritmo desarrollado por BCAM para adaptar la superficie definida y poder mecanizar tanto el acabado con la fresa como con la muela mediante Flank milling y Flank SAM respectivamente. En la figura 5 se muestran dos imágenes de la aplicación de dicho algoritmo a dos componentes rotativos.
![Figura 5. Algoritmo aplicado a un blade y a un impeller [10] Figura 5. Algoritmo aplicado a un blade y a un impeller [10]](https://img.interempresas.net/fotos/1614821.jpeg)
Cabe destacar que esta solución ofrece la posibilidad de utilizar toda la superficie útil de la herramienta contra la superficie de la pieza y, en este caso en concreto, y debido al diseño, realizar el acabado de la superficie de una sola profundidad axial (20 mm). La realización del acabado con todo el flanco de la herramienta supone una reducción importante de los tiempos de mecanizado y, a su vez, disminuye el desgaste de la herramienta.
Debido a la funcionalidad de este tipo de componentes rotativos, que se recogen en este artículo, las exigencias de acabado superficial son muy estrictas. En muchos casos no se permite salto entre las diferentes pasadas alrededor del mismo álabe. En estas situaciones es donde el algoritmo coge fuerza al ofrecer soluciones para el acabado de una sola pasada. En la figura 6 se muestra la ejecución del acabado mediante ambos procesos durante los ensayos realizados.
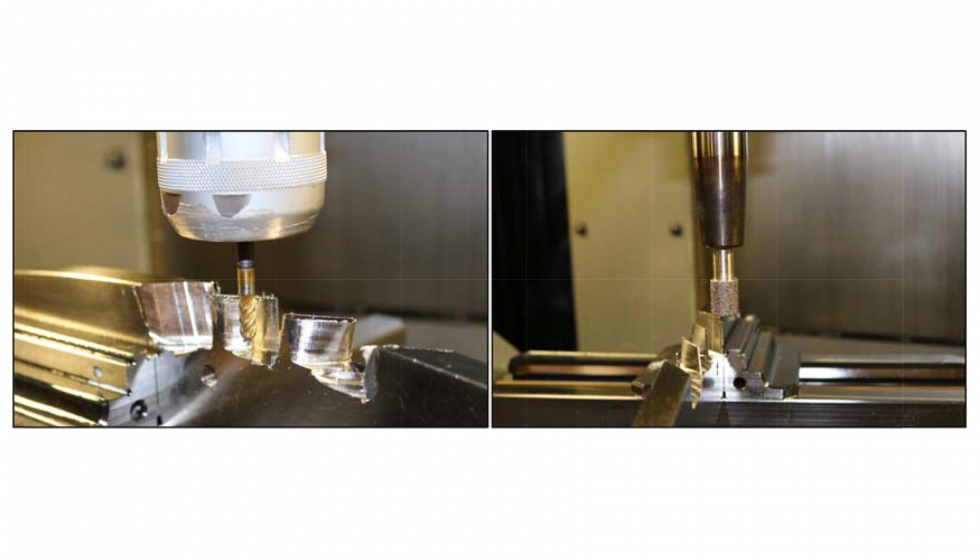
Tras la realización del mecanizado mediante ambas técnicas, se ha observado un mejor comportamiento de la técnica del Flank SAM para este tipo de materiales termorresistentes. De hecho, en la muela no se observa ningún deterioro, lo que conlleva que esta técnica mantenga una precisión dimensional sin desgaste o rotura de herramienta.
3.3. Análisis de fuerzas
Como se ha indicado en el apartado de montaje experimental, las fuerzas fueron registradas durante el mecanizado de los álabes mediante las técnicas de fresado convencional y SAM tanto en el proceso de desbaste como de acabado. En la figura 7 se recogen los resultados obtenidos en cuanto a fuerzas medias y máximas registradas.
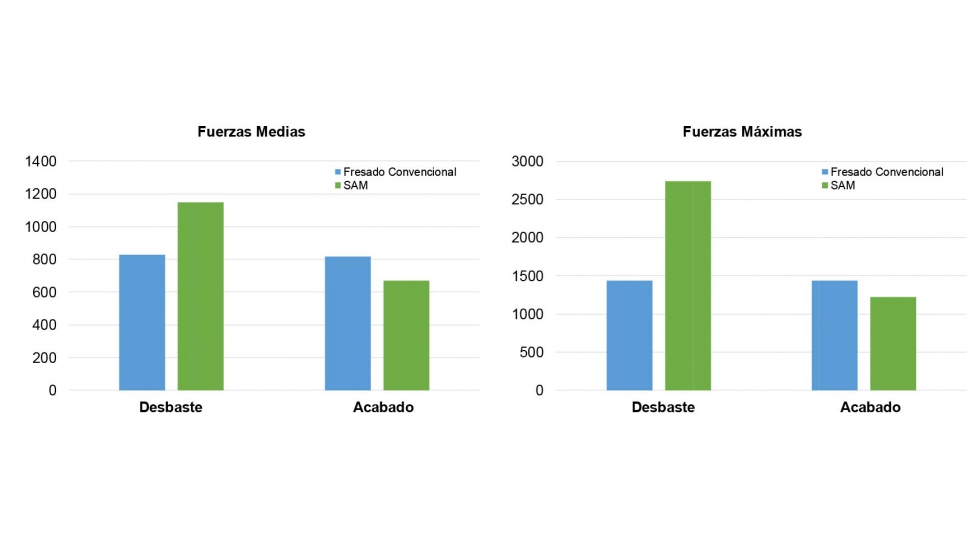
Como se observa, las diferencias más acusadas entre ambas técnicas se registran durante el proceso de desbaste; esto se debe a las condiciones de corte más agresivas utilizadas durante el mecanizado. En el caso del SAM se obtienen valores medios que superan los 1.100 N con un pico máximo por encima de los 2.500 N. Esto supone un aumento de las fuerzas en un ˜40 y un ˜100% respectivamente, frente al fresado convencional Este comportamiento se deriva de que durante el fresado convencional, el desbaste se debe realizar mediante varias pasadas hasta obtener la profundidad total del álabe frente al mecanizado con Frank SAM, que se realiza en una sola pasada. Esto se traduce en una mayor sección de viruta durante el desbaste con SAM frente al fresado convencional que implica mayores fuerzas de corte, pero a su vez menores tiempos de mecanizado.
Sin embargo, durante el proceso de acabado esta diferencia se invierte, obteniendo por tanto valores menores durante el mecanizado con SAM. Concretamente, con este proceso se obtienen valores que superan ligeramente los 600 N para la fuerza media con un pico por que alcanza los ˜1.200N. Por tanto, en comparación con el fresado convencional las fuerzas se reducen en un ˜20 y ˜15%, respectivamente.
Por tanto, a raíz de los resultados obtenidos desde el punto de vista de los esfuerzos mecánicos a los que es sometido la herramienta durante el mecanizado mediante SAM se observa que estos no son una limitación para la utilización de esta técnica en centros de mecanizado convencionales como el utilizado durante estos ensayos, siempre y cuando las condiciones de corte sean adecuadas a la capacidad de giro del husillo de dicha máquina.
4. Conclusiones
En este trabajo se ha realizado el mecanizado de un modelo de álabes de turbinas en Inconel 718 mediante dos tipos de procesos de mecanizado. Concretamente se ha comparado el mecanizado de dichos componentes mediante fresado convencional y la técnica de SAM. El objetivo de esta comparativa ha sido analizar la viabilidad de la técnica de SAM para la fabricación de dichos componentes. De este modo se posibilita una nueva vía de mejora para los procesos convencionales de fabricación utilizados en el entorno industrial de tal modo que se aumente la productividad de éstos incidiendo directamente en los tiempos de mecanizado.
A raíz de los ensayos realizados se desprenden las siguientes conclusiones:
- La técnica de Flank SAM aplicada a procesos desbaste ha presentado una mayor tasa de arranque de viruta frente al fresado convencional, es decir, se consigue un aumento en la productividad mediante la reducción de tiempos de mecanizado.
- Por otra parte, esta mayor tasa de arranque de viruta viene condicionado por un aumento de las fuerzas de corte durante el desbaste mediante SAM. No obstante, durante los procesos de acabado donde dicha tasa se vuelve similar, el SAM presenta menores fuerzas de corte.
Por último, hay que tener en cuenta que para la realización del mecanizado de álabes de turbina mediante SAM se hace necesario disponer de un centro de mecanizado robusto, con un electrohusillo capaz de llegar a las 80.000 rpm y disponer de aceite como fluido de corte.
Agradecimientos
Los autores agradecen la financiación recibida por el Ministerio de Economía y Competitividad mediante el proyecto Turbo (DPI 2013-46164-C2-1-R). Así mismo quieren agradecen el soporte económico recibido por el programa Hazitek del Departamento de Desarrollo Económico e Infraestructuras del Gobierno Vaso y de los fondos europeos Feder recibidos mediante el proyecto con acrónimo Hematex.
Referencias
[1] https://www.tedae.org/uploads/attachments/1461082017_retos-del-sector aeronutico-en-espaa-gua-estratgica-2015-2025-pdf.pdf
[2] A. Mateo. On the feasibility of Blisk produced by linear friction welding. Revista de Metalurgia. 2014. DOI: http://dx.doi.org/10.3989/revmetalm.023.
[3] Klocke, F., Zeis, M., Klink, A., & Veselovac, D. (2013). Technological and economical comparison of roughing strategies via milling, sinking-EDM, wire-EDM and ECM for titanium- and nickel-based blisks. CIRP Journal of Manufacturing Science and Technology, 6(3), 198–203. http://doi.org/10.1016/j.cirpj.2013.02.008
[4] Pereira, O., Rodríguez, A., Barreiro J., Fernández-Abia, A.I., and López de Lacalle, L.N. Nozzle design of combined use of MQL and cryogenic gas in machining. International Journal of Precision Engineering and Manufacturing-Green Technology. 2017. 4, 87-95.
[5] http://www.mmsonline.com/articles/wire-edm-for-jet-engine-fir-trees
[6] I. Ayesta, B. Izquierdo, J.A. Sánchez, J.M. Ramos, S. Plaza, I. Pombo, N. Ortega, H. Bravo, R. Fradejas, I. Zamakona. Influence of EDM Parameters on Slot Machining in C1023 Aeronautical Alloy. Procedia CIRP. 2013. 6, 129-134.
[7] Curtis, D. T., Soo, S. L., Aspinwall, D. K., & Sage, C. (2009). Electrochemical superabrasive machining of a nickel-based aeroengine alloy using mounted grinding points. CIRP Annals - Manufacturing Technology, 58(1), 173–176. http://doi.org/10.1016/j.cirp.2009.03.074
[8] M.K. Sinha, R. Madarkar, S. Ghosh, P. V. Rao. Application of eco-friendly nanofluids during grinding of Inconel 718 through small quantity lubrication. Journal of Clenaer Production. 2017. 141, 1359-1375.
[9] A. Caggiano, R. Teti. CBN grinding performance improvement in aircraft engine components manufacture. Procedia CIRP. 2009, 9, 109-114.
[10] Bhatt A, Attia H, Vargas R, Thomson V (2010) Wear mechanisms of WC coated and uncoated tools in finish turning of Inconel 718. Tribology International 43:1113–1121
[11] Hosokawa A, Ueda T, Onishi R, Tanaka R, Furumoto T (2010) Turning of difficult-tomachine materials with actively driven rotary tool. CIRP Annals - Manufacturing Technology 59:89–92
[12] Klocke F, Krämer K, Sangermann H, Lung D (2012) Thermo-mechanical tool load during high performance cutting of hard-to-cut materials. Procedia Fifth Conference on High Performance Cutting 1:295–300
[13] Thakur DG, Ramamoorthy B, Vijayaraghavan L (2009) Study on the machinability characteristics of superalloy Inconel 718 during high speed turning. Materials and Design 30:1718–1725
[14] Costes JP, Guillet Y, Poulachon G, Dessoly M (2007) Tool-life and wear mechanisms of CBN tools in machining of Inconel 718. International Journal of Machine Tools and Manufacture 47:1081–1087
[15] Aspinwall, D. K., Soo, S. L., Curtis, D. T., & Mantle, a. L. (2007). Profiled superabrasive grinding wheels for the machining of a nickel based superalloy. CIRP Annals - Manufacturing Technology, 56(1), 335–338. http://doi.org/10.1016/j.cirp.2007.05.077
[16] Pengbo Bo, Michael Barto?n, Denys Plakhotnikc, Helmut Pottmannd. Towards efficient 5-axis flank CNC machining of free-form surfaces via fitting envelopes of surfaces of revolution. CAD Computer Aided Design, 79, 1–11. http://doi.org/10.1016/j.cad.2016.04.004