Taladrado asistido con vibraciones de baja frecuencia de bridas eólicas
1. Introducción
1.1 Necesidad industrial de mejorar el proceso de taladrado
El taladrado es una operación de mecanizado de gran importancia en diversos sectores de la industria, pero a pesar de ser un proceso extendido y conocido tanto por los fabricantes de máquina herramienta como por los talleres de mecanizado, existe la necesidad de emplear métodos cada vez más productivos en un entorno globalizado y de gran competitividad.
Tanto los fabricantes de máquinas como los de brocas están continuamente trabajando para producir agujeros de calidad mejorada y en tiempos de proceso menores que los empleados con las tecnologías actuales. Los fabricantes de máquinas para taladrado necesitan desarrollar nuevos productos que refuercen su posicionamiento y competitividad en el mercado internacional de máquinas. La figura 1 muestra una solución para el taladrado de piezas circulares como anillos de rodamiento o bridas eólicas.
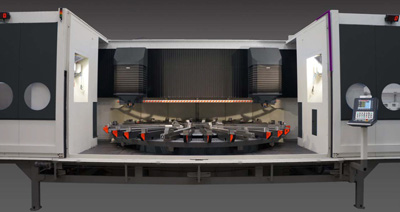
Figura 1. Solución de Ibarmia para taladrado de bridas eólicas.
Los principales problemas que plantea el taladrado de este tipo de piezas de aceros dúctiles, son los referidos a la calidad del agujero mecanizado, el tiempo de ciclo y la extracción de la viruta, tanto del agujero como del propia área de trabajo de la máquina.
Este último punto es todo un problema de primer orden que aun hoy es de difícil resolución y constituye todo un quebradero de cabeza para los diseñadores y usuarios de las máquinas.
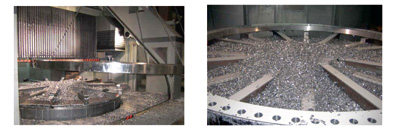
Figura 2. Producción de viruta en el taladrado de bridas eólicas.
La no eficiente extracción de la viruta de la zona de corte conlleva efectos negativos en la calidad de los mecanizados, tanto por interferencias entre pieza y herramienta, como por un exceso de calor que produce deformaciones térmicas y sus derivadas perdidas de precisión geométrica. A menudo es necesario emplear grandes volúmenes de fluidos de corte a elevada presión para facilitar la extracción de la viruta, en muchas instalaciones con máquinas de tecnología punta es muy habitual retirar las largas virutas de taladrado de forma manual.
A fin de superar los principales problemas de la operación de taladrado de este tipo de piezas, el objetivo del presente trabajo ha sido estudiar la viabilidad del taladrado asistido con vibraciones de baja frecuencia para agujeros medios-grandes, ya que esta estrategia de taladrado puede reducir en gran medida los problemas citados.
1.2 ¿Qué es el taladrado asistido?
El taladrado convencional es un proceso de corte en el cual la herramienta (broca) combina un movimiento simultáneo de giro cortante con un movimiento de avance constante en la dirección del eje de rotación. El taladrado asistido consiste en incluir un movimiento vibratorio controlado paralelo al eje de la broca (figura 3), con suficiente amplitud como para provocar la interrupción en el corte. Conceptualmente, se conoce en los talleres de mecanizado como ‘peck drilling’ o’taladrado con picoteo’, pero llevado a cabo a frecuencias mayores a las normalmente empleadas y formas de vibración optimizadas.
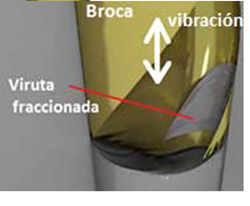
Figura 3. Concepto de taladrado asistido.
Esta tecnología fue presentada por Kumabe1, e incluye el taladrado asistido de baja frecuencia y el taladrado ultrasónico. Algunos estudios han revelado que el taladrado ultrasónico produce el efecto de aumentar la rigidez de la broca, la vida de herramienta y reducir la fuerza de avance y los errores dimensionales en los agujeros 2-3. El taladrado asistido de baja frecuencia, en cambio, permite controlar la forma de la viruta4, lo cual facilita su rotura y posterior evacuación, pudiéndose mejorar el resultado del taladrado en términos de temperatura alcanzada y mejora la precisión del agujero5. El taladrado asistido por vibraciones de baja frecuencia se aplica en materiales de baja maquinabilidad y en taladrado profundo 6-7.
En los últimos años Tecnalia ha investigado el proceso de taladrado asistido a bajas frecuencias (hasta 100Hz), y en líneas generales se ha podido concluir que las ventajas que se obtienen son:
- Menor generación de calor en la zona de corte
- Favorecer la fragmentación de viruta
- Aumentar la productividad (mayores avances alcanzados)
- Aumentar la vida de la herramienta
- Mejorar la calidad superficial y dimensional
Existe un interés en el entorno científico e industrial sobre la asistencia del taladrado mediante vibraciones de baja frecuencia y la manera de conseguir dicha vibración. El mercado ofrece soluciones para realizar el taladrado asistido, como los porta-brocas que proponen las compañías M4Science8 (porta dotado de actuadores piezo-eléctricos para generar la vibración) y Mitis Engineering9 (vibración generada mediante resonancia mecánica del sistema), los cuales permiten utilizar brocas de diámetros hasta aproximadamente 12-14 mm. Como fruto a la labor de investigación en este ámbito, Tecnalia ha desarrollado también una alternativa propia (ver figura 4).
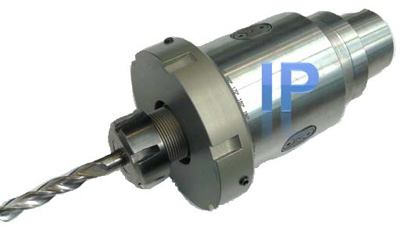
Figura 4. Porta-herramientas vibratorio de Tecnalia.
Las tres soluciones mencionadas no permiten taladrar agujeros de tamaño medio/grande, principalmente por falta de capacidad de vibración por encima de cierto valor de fuerza de avance. En la actualidad no existen soluciones comerciales para llevar a cabo el taladrado asistido con brocas de tamaño medio-grande.
2. Taladrado asistido: Frecuencia y amplitud óptima
El taladrado asistido presenta ciertas peculiaridades con respecto del taladrado convencional debido al movimiento oscilante relativo entre la herramienta y la pieza (ver figura 5). Este movimiento es la suma del movimiento lineal de avance más el de vibración (forma sinusoidal, triangular, …), y produce variaciones en el espesor de viruta no deformado. Éste varía entre un máximo y mínimo (hasta cero) dependiendo de la frecuencia y amplitud de vibración utilizada, es decir, el espesor de viruta no se mantiene constante, como ocurre en una operación convencional de taladrado.
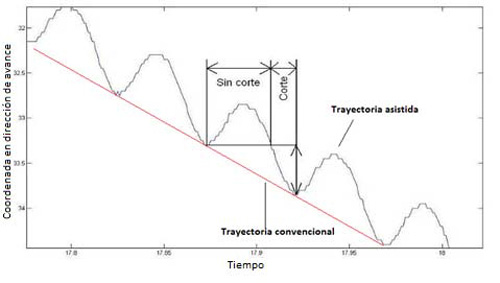
Figura 5. Comparación entre trayectoria de la herramienta en un proceso de taladrado convencional y asistido.
2.1 Frecuencia Óptima
El valor de la frecuencia de vibración tiene una influencia directa en el espesor máximo de viruta y la longitud de la viruta generada, y por tanto en la utilidad de la estrategia asistida.
Para un caso dado de diámetro de broca, velocidad de corte, avance por vuelta y amplitud de vibración, el espesor máximo y mínimo de viruta sin deformar varía con la frecuencia tal y como se muestra en la figura 6.
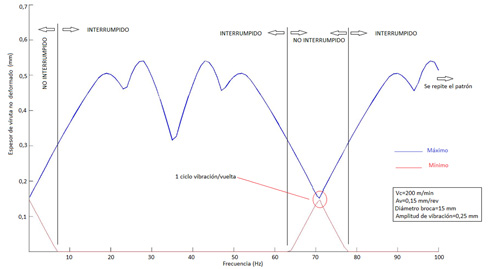
Figura 6. Espesor de viruta máximo y mínimo en función de la frecuencia de vibración para un taladrado de diámetro 15 mm, a 200 m/min, 0,15 mm/rev y amplitud de vibración 0,25 mm.
Esta curva se ha obtenido a través de un programa de cálculo en el que se han introducido las ecuaciones que rigen el movimiento de los filos (Tabla 1) y discriminado los puntos de espesor máximo y mínimo cortado por el filo durante su movimiento.

Tabla 1. Ecuaciones que rigen el movimiento del filo en taladrado asistido.
Donde A y f son la amplitud y frecuencia respectivamente, Vr es la velocidad relativa entre la broca y la pieza, Vl la velocidad lineal constante de avance y Z la posición del filo.
De la figura se extrae que cuando la frecuencia de vibración es cercana o coincide con la frecuencia de giro de la herramienta o sus múltiplos (en este caso 4244 rpm ó 70,74 rev/s), el espesor de viruta máximo y el mínimo coinciden con el avance por vuelta del ciclo convencional (0,15 mm), es decir, no se produce la interrupción en el corte al producirse una resonancia entre la frecuencia de giro y la asistida, independientemente de la amplitud de vibración. A bajas frecuencias, entre 0 y 7 Hz, no llega a producirse la interrupción del corte, aunque el espesor de viruta varía entre un máximo y un mínimo.
Para frecuencias por encima de 7 Hz y menores a 63 Hz, el espesor de viruta máximo aumenta considerablemente (hasta 3-4 veces el avance por vuelta), y el mínimo alcanza un valor de 0 mm, es decir, se produce una interrupción en el corte.
Valorar qué frecuencia es la óptima para un caso dado de taladrado es algo que exige un análisis profundo de diversos factores, tanto desde el punto de vista del proceso de corte en sí, como desde una perspectiva más global de diseño y/o selección de la forma en conseguir la vibración.
Teniendo en cuenta únicamente el proceso de corte, cabe esperar que un aumento excesivo del espesor de viruta sin deformar, por encima de valores recomendados y habitualmente utilizados en taladrado de acero (0,1-0,3mm), podría inducir inestabilidad, sobrecarga y rotura prematura del filo. Por tanto, a priori sería recomendable no sobrepasar valores 2-3 veces mayores al espesor dado para una combinación de broca-material.
Esto lleva a pensar que una frecuencia adecuada es aquella que no produzca un aumento excesivo del espesor de viruta y garantice la interrupción del corte y, por tanto, la fragmentación de la viruta y la correcta refrigeración/lubricación del filo. Según la figura 6, los puntos óptimos corresponderían a 7 Hz, 63 Hz y 78 Hz, siguiendo la serie de valores hasta el infinito por cada múltiplo de la velocidad de giro.
En estos puntos, los valores de espesor máximo y mínimo de viruta coinciden, pero la diferencia reside en el tiempo transcurrido entre las interrupciones del corte, ya que como se indica en la Tabla 2, el número de ciclos de vibraciones por cada giro de la broca difiere.

Tabla 2. Ciclos de vibración por vuelta para taladrado a 4.244 rpm para frecuencias que garantizan la interrupción en el corte.
De la tabla se concluye que a 7 Hz se produciría la interrupción cada 10 vueltas, hecho que para el taladrado de materiales muy dúctiles implicaría longitudes de viruta relativamente largas. Suponiendo el taladrado con una broca de 15 mm de diámetro, se obtendrían virutas de más de 0,5 m de longitud, y de más de 1 m para brocas a partir de 32 mm.
A las frecuencias cercanas a la de giro en cambio, se garantiza la interrupción del corte cada giro de la herramienta aproximadamente, produciéndose virutas más cortas y la refrigeración/lubricación de la zona de corte. Por tanto, a priori, podría deducirse que un buen criterio de selección de la frecuencia es que sea cercana a 1 ciclo/vuelta o sus múltiplos y que garanticen la interrupción en el corte.
2.2 Amplitud
Las ecuaciones que rigen el movimiento de un taladrado asistido (ver Tabla 1) incluyen la amplitud como variable a fijar o a calcular. Para el mismo caso dado de diámetro de broca (15 mm), velocidad de corte (200 m/min), avance por vuelta (0,15 mm/rev), y fijando las frecuencias en 7, 63 y 78 Hz, el espesor máximo y mínimo no deformado en función de la amplitud se muestran en la figura siguiente.
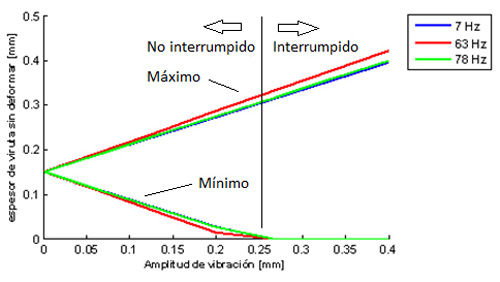
Figura 7. Espesor de viruta sin deformar en función de la amplitud a 7, 63 y 78 Hz.
Se observa que existe una amplitud mínima (0,25 mm) de vibración que garantiza la interrupción en el corte. El valor de amplitud que limita las dos zonas tiene que ser calculado para cada caso de taladrado dado.
3. Estudio Experimental
Se ha realizado un estudio experimental que se ha dividido en 2 fases. En primer lugar, con el objetivo de analizar la viabilidad de esta estrategia de taladrado mediante brocas con placas intercambiables utilizadas en el taladrado de bridas eólicas, se han llevado a cabo ensayos en un centro de mecanizado horizontal situado en las instalaciones de Tecnalia, que ha permitido comparar el taladrado convencional con el asistido a 2 frecuencias diferentes. En segundo lugar, se han realizado pruebas de validación en una máquina ubicada en IBARMIA dimensionada para taladrar bridas basándose en un caso real de diámetro de broca de 40 mm de diámetro.
3.1. Fase 1: Pruebas de viabilidad en Tecnalia
Los ensayos de viabilidad han consistido en comparar el taladrado convencional con el asistido a dos frecuencias diferentes. Para ello, se ha utilizado un centro de mecanizado horizontal, modelo Agil-2g de Fatronik-Tecnalia, de 3 ejes (XYZ) con control Fidia, cuya característica principal es la aceleración (2g) y elevada velocidad de avance (hasta 120 m/min) que proporcionan sus motores lineales, que permiten ejecutar el taladrado asistido hasta 25 Hz. La trayectoria de taladrado asistido se ha conseguido ejecutando programas de CN que contienen una serie de coordenadas en Z, las cuales definen una trayectoria resultante igual a la suma de un movimiento lineal a uno vibratorio. El procedimiento seguido para ajustar los programas ha sido similar al descrito en la ponencia10 presentada en este congreso en 2010 sobre un estudio sobre taladrado asistido de aluminio.
Debido a la limitación en potencia del cabezal de esta máquina, se ha optado por seleccionar una broca de diámetro 15 mm de plaquitas intercambiables (figura 8), cuya geometría básica (plaquita central+exterior) es similar para las brocas entre 15-70 mm, típicamente utilizadas en el taladrado de bridas. El material taladrado ha sido una placa de 400 x 300 x 50 de acero laminado ST-52, comúnmente utilizado en la fabricación de bridas eólicas.
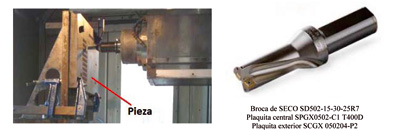
Figura 8. Set-up experimental y broca y plaquitas utilizadas.
Las frecuencias seleccionadas para el ciclo de taladrado asistido han estado condicionadas por la limitación de los 25Hz máximos disponibles en la máquina. Por ello, se ha decidido probar el valor de 7Hz que, según la figura 6, corresponde a la primera frecuencia en la que se da la interrupción en el corte, y 20 Hz que conlleva un espesor de viruta máximo, a priori desfavorable para el proceso. Las pruebas realizadas se muestran en las tablas siguientes. Se han realizado una tanda inicial de 10 agujeros para cada condición para evaluar las posibles diferencias en diámetro y rugosidad de los agujeros taladrados. Posteriormente, se ha llevado a cabo un ensayo a fin de vida (hasta la rotura de plaquitas) para comparar el taladrado convencional con el asistido 7Hz.
Es importante recalcar que para las tres condiciones testadas el tiempo de ciclo del taladrado ha sido el mismo.
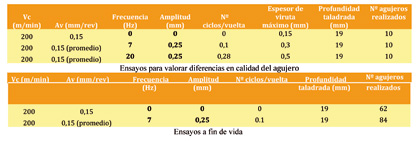
Tabla 3. Resumen condiciones de corte para ensayos realizados.
Cabe comentar que para el uso de brocas con placas intercambiables siempre se aconseja el uso de aire o taladrina a través de la herramienta para facilitar la extracción de viruta. La no disponibilidad de refrigeración interior en la máquina ha podido condicionar los resultados en términos de rugosidad alcanzable de los agujeros y vida de herramienta ya que el ángulo de hélice de las brocas de plaquitas es bajo (casi 0º) comparándolo con las brocas helicoidales lo cual impide la correcta extracción de la viruta si no se dispone de un fluido a presión.
El error diametral se ha medido tanto para la entrada como para el fondo del agujero (Figura 9 y Figura 10) para los ensayos iniciales, los datos obtenidos no han revelado diferencias significativas entre las 3 condiciones probadas. El carácter disperso de los resultados puede estar relacionado con la falta de refrigeración interior durante los ensayos.
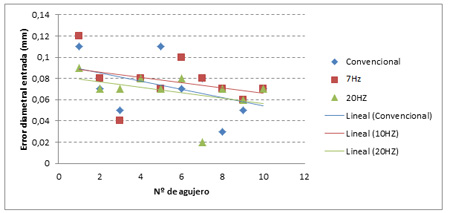
Figura 9. Error diametral en la entrada del agujero.
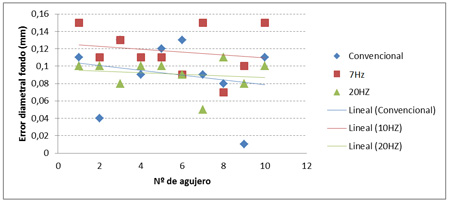
Figura 10. Error diametral en la salida del agujero.
La rugosidad medida en la pared de los agujeros tampoco revela diferencias apreciables. Tal y como se observa en la Figura 11 los resultados no son tan dispersos como las medidas de error diametral, correspondiendo los mejores valores al caso de 20 Hz. Este fenómeno de mejora en la rugosidad, se ha podido comprobar en otros estudios10 realizados en otros materiales en Tecnalia.
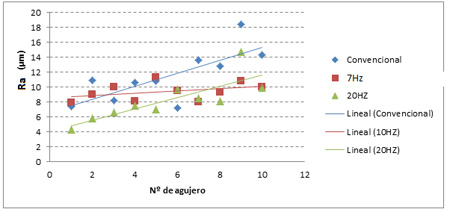
Figura 11. Rugosidad Ra (µm) en la pared.
Tras esta primera tanda de ensayos, se ha concluido que el taladrado asistido con brocas de plaquitas intercambiables es viable incluso a frecuencias que aumentan considerablemente el espesor de viruta máximo (caso de 20 Hz), y que la asistencia de vibraciones no perjudica la calidad del agujero, incluso puede mejorar la calidad del agujero en algunos casos, además de producir viruta más pequeña (ver Figura 12).
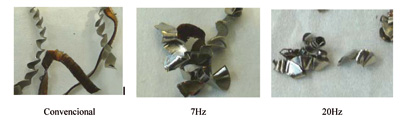
Figura 12. Virutas obtenidas.
Tras la primera tanda de ensayos se ha procedido a analizar si la asistencia de vibraciones tiene un efecto negativo en la vida de la herramienta. Para ello, se ha llevado a cabo un ensayo a fin de vida de las plaquitas para la estrategia convencional y la asistida a 7 Hz.
El ensayo a fin de vida ha consistido en realizar taladrados hasta la rotura catastrófica de la placa central. El resultado ha sido que el número de agujeros taladrados ha sido mayor a 7 Hz, 84 agujeros frente a 62 con la estrategia convencional (ver Figura 28). A pesar de que un estudio a fin de vida debería de realizarse en condiciones reales, es decir, con el uso de refrigeración interior, el ensayo realizado ha servido para comprobar que las vibraciones podrían alargar la vida de herramienta, o al menos no reducirla.
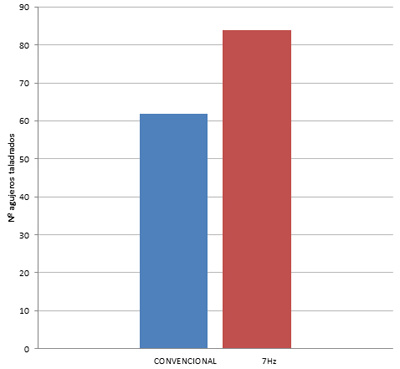
Figura 13. Resultado ensayo a fin de vida (convencional vs. 7 Hz).
3.2 Fase 2: Pruebas de validación industrial
La fase 2 de los ensayos ha consistido en realizar pruebas de validación en una máquina, la ZVH 58 L4000 Multiprocess de Ibarmia adecuada para taladrar bridas eólicas y con la posibilidad de realizar taladrados con refrigeración interior. Se ha basado en un caso real de taladrado de diámetro 40 mm para definir el plan de ensayos siguiente:
- Puesta a punto de un ciclo de taladrado asistido y evaluación de la calidad de los agujeros en probeta
- Ensayos de vida y de mejora de la productividad en pieza real (el análisis de los datos y resultados de este punto están siendo analizados en la actualidad y no se han podido incluir en este texto)
Para la puesta a punto del ciclo de taladrado se ha seguido el mismo procedimiento que para la fase 1. Las condiciones probadas y el set-up experimental se pueden observar en la figura siguiente.
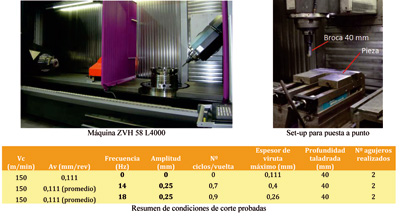
Figura 14. Máquina y set-up experimental (arriba) y condiciones de corte probadas (abajo).
Las frecuencias seleccionadas para el ciclo de taladrado asistido no han estado condicionadas, esta vez, por una limitación de máquina. Teniendo en cuenta que para el caso industrial bajo estudio de taladrado de bridas eólicas, los diámetros a realizar se sitúan en el rango de 15-70 mm (dependiendo del tamaño de la brida), y que las velocidades de corte típicas son del orden de 50-300 m/min para el acero St-52, las frecuencias de vibración para alcanzar un ciclo de vibración por vuelta son las que muestra la siguiente figura.
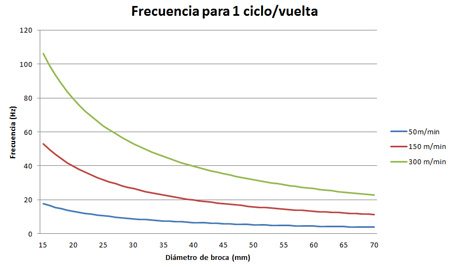
Figura 15. Frecuencia de vibración para obtener 1 ciclo/vuelta en función del diámetro de la broca y velocidad de corte.
De la figura 15 se concluye que cuanto mayor es el diámetro de la broca menor es la frecuencia de vibración requerida para alcanzar el criterio de cercanía a 1 ciclo/vuelta. Para la velocidad de corte ensayada, 150 m/min, y el diámetro de herramienta, 40 mm, la frecuencia recomendable se situaría en torno a 20 Hz.
Una vez comprobada la capacidad de vibración de la máquina (en torno a 20 Hz), se ha decidido fijar le frecuencia de corte en 18 Hz, valor que produce la interrupción en el corte y es el más cercano a 20 Hz. También se ha decidido probar una frecuencia intermedia, en principio más desfavorable, de 14 Hz, en la que el espesor de viruta ha alcanzado espesores mayores. La evolución del espesor de viruta sin deformar en el tiempo se muestra en la Figura 16 Para los tres casos ensayados.
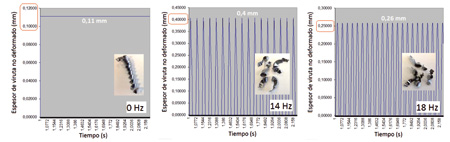
Figura 16. Variación en el tiempo del espesor de viruta y muestra de viruta obtenida.
Esta parte de la experimentación ha servido para confirmar que el taladrado asistido con brocas de tamaño medio grande es técnicamente viable. Las mediciones tolerancia diametral en el taladrado asistido son equiparables a las obtenidas por el taladrado convencional o tradicional. Las mediciones en la rugosidad en cambio revelan valores ligeramente superiores para los agujeros realizados con la estrategia asistida. Estos resultados contradicen la tendencia observada en los ensayos de la fase 1. A pesar de ello, la rugosidad alcanzada ha sido mejor que en la experimentación de la fase 1, en la que no se disponía de refrigeración a través del interior de la broca.
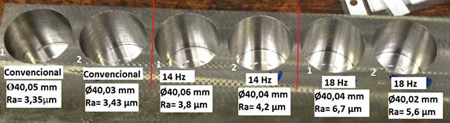
Figura 17. Agujeros de 40 mm taladrados.
4. Conclusiones
La principal conclusión del trabajo realizado ha sido demostrar que el taladrado asistido a bajas frecuencias con brocas de tamaño medio/grande es técnicamente viable. Las pruebas realizadas con diferentes diámetros de brocas (de 15 y 40 mm) y a diferentes frecuencias de vibración (desde 7 Hz hasta 20 Hz) han revelado que el taladrado asistido produce el efecto de la ruptura de la viruta, hecho que facilita su extracción, sin perjudicar al diámetro ni a la rugosidad obtenible.
En algunas de las condiciones testadas el espesor de viruta no deformado ha alcanzado valores hasta 3-4 veces lo establecido por el fabricante de la herramienta, no obstante, las mediciones no han revelado un efecto negativo en el proceso de taladrado.
A falta de contemplar los resultados con ensayos de mejora de la productividad, se ha concluido que el taladrado asistido puede alargar la vida de la herramienta. Asimismo, el taladrado asistido podría considerarse una alternativa factible y aconsejable para el taladrado de diámetros medios y grandes.
5. Líneas futuras
El esfuerzo investigador se está centrando en dar con la solución técnico-económica más adecuada que permita conseguir el efecto vibrador en el proceso de taladrado. Las alternativas que se barajan las resume la figura siguiente.
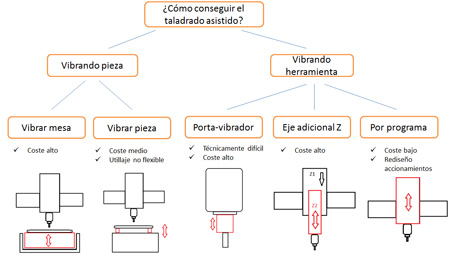
Figura 18. Diferentes formas de conseguir el taladrado asistido.
Cada una de las alternativas planteadas conlleva sus pros y contras, tanto en el apartado técnico como en el económico.
La posibilidad de hacer vibrar la pieza conlleva una gran inversión económica que habría que justificar con las posibles ventajas que se obtienen por el proceso. Tanto el rediseño de la mesa o un posible utillaje que haga vibrar la pieza debería de garantizar que la vibración fuera perfectamente paralela a la dirección de avance de la broca para garantizar la calidad del agujero. A priori, esta alternativa presenta una dificultad técnica alta, y costosa desde el punto de vista energético, ya que hacer vibrar una gran pieza de acero como una brida eólica implica un consumo de energía alto.
Dentro de las alternativas de hacer vibrar la herramienta, la opción de diseñar un porta vibrador podría resultar en principio la más flexible. La dificultad para esta opción reside en garantizar que el sistema vibre superando las fuerzas de avance que se dan en el taladrado de este tamaño de agujeros, del orden de toneladas (1.000-2.000 kg), típico en taladrados de diámetros grandes. La opción del eje Z adicional es una solución válida a nivel técnico, cuya principal desventaja puede ser el coste adicional para la máquina. Finalmente, la posibilidad de conseguir el efecto vibrador a través del código de programa, tal y como se ha hecho en los ensayos realizados, se presenta como la posibilidad más adecuada pero abre la incógnita de la respuesta a fatiga de los elementos de transmisión y accionamientos bajo cargas altas y repetitivas.
Ibarmia está actualmente analizando cada una de las soluciones, pues requiere de un análisis que contempla los aspectos técnicos descritos, que afectan a todos los elementos de una máquina que intervienen para hacer posible el taladrado asistido, pero indudablemente, el objetivo final es diseñar máquinas que reduzcan el coste por agujero taladrado, y esto en definitiva es lo que hace realmente que una solución sea interesante para el comprador de una máquina.
Agradecimientos
Los autores quieren agradecer el apoyo recibido desde el CIC marGUNE y el Gobierno Vasco a través sus programas de apoyo a la realización de proyectos de desarrollo de nuevos productos.
Referencias
[1] J. Kumabe, Fundamentals and Application of Vibration Cutting. Jikkyo Publishing Co. Ltd, Japan, 1979.
[2] D. Y. Zhang, Study on the drill skidding motion in ultrasonic vibration microdrilling, International Journal of Machine Tools and Manufacture, 1994, 34, 847-857.
[3] J. Pujana, et al., Analysis of ultrasonic-assisted drilling of Ti6Al4V, International Journal of Machine Tools and Manufacture, 2009, doi:10.1016/j.ijmachtools.2008.12.014
[4] Z. Deyuan, W. Lijiang, Investigation of chip in vibration drilling, International Journal of Machine Tools and Manufacture, 1998, 38, No.3, 165-176.
[5] K. Okamura, H. Sasahara, T. Segawa, Low-Frequency Vibration Drilling of Titanium Alloy, JSME International Journal, Series C Vol. 49 No.1 (2006)
[6] G. L. Chern, J. Liang, Study on boring and drilling with vibration cutting, International Journal of Machine Tools and Manufacture, 2007, 47, No.1, 133-140.
[7] K. Adachi, Proc. Japan Society of Mechanical Engineering, 1987, 53, 1877-1883. [8] www.m4sciences.com
[9] www.mitis.fr
[10] T. Ostra, G. Rodriguez, J. Camacho, A. Fernández, A. Rivero. Taladrado profundo asistido por vibraciones de baja frecuencia para la mejora de defectos superficiales y dimensionales. 18 Congreso de Máquina Herramienta y Tecnologías de Fabricación 2010.