Sistema experto para la sensorización del molde en el proceso de inyección
El moldeo por inyección es un proceso complejo, en el que garantizar la calidad de la pieza final depende de varios factores relacionados entre sí, especialmente la temperatura y la presión dentro del molde durante el proceso de inyección [2,3]. Cualquier anomalía en alguno de los parámetros del proceso afecta a la calidad final de las piezas. Por esta razón, es necesario realizar una serie de modificaciones en los moldes hasta conseguir optimizar la calidad de la pieza a inyectar, así como configurar adecuadamente los parámetros de la máquina antes de pasar a la producción.
Existen numerosos estudios sobre cómo controlar el proceso de inyección. La mayoría de ellos se basan en la sensorización de las fases críticas del proceso. Por ejemplo, la presión y la temperatura en el molde durante la inyección son buenos indicadores que permiten predecir la calidad de la pieza final. Colocar sensores de presión y de temperatura en el interior del molde permite caracterizar las curvas que permiten identificar la calidad de la pieza final antes de abrir el molde, disminuyendo la inspección visual como medio de control de calidad.
Sin lugar a dudas, la información que proporcionan los sensores es de extrema utilidad para optimizar el proceso de inyección y evolucionar hacia un sistema ‘Turn-Key Intelligent Mould’ (Puesta a Punto de Molde Inteligente). Pero, para obtener la mejor información que permita predecir la calidad de la pieza final ¿cuál es el conjunto mínimo de sensores necesario?, y ¿cuál debe ser su ubicación en el interior del molde? La instalación de un sensor en un molde implica su perforación y, por tanto, un incremento tanto del coste del mismo como del tiempo necesario de ajuste del molde en la máquina. Por ello, se debe optimizar el número y ubicación de sensores en el molde.
El reto por tanto es el siguiente:
Dada una geometría de molde, un material, unos puntos de inyección establecidos y un conjunto de defectos que se desean evitar, el reto consiste en diseñar un sistema que proporcione el conjunto óptimo de tipos de sensores y su ubicación en el molde que proporcionen la información más útil para establecer un control de calidad eficaz durante la fase de producción.
‘La información más útil para establecer un control de calidad eficaz’ es un concepto difuso que sólo puede calcularse a través de simulaciones numéricas, lo que requiere un gran gasto computacional. En el centro tecnológico Ascamm se ha desarrollado un sistema que combina el conocimiento tácito de los expertos y el conocimiento explícito encontrado en los manuales y bibliografía, lo que permite reformular el reto de la siguiente manera:
Dada una geometría de molde, un material, unos puntos de inyección establecidos y un conjunto de defectos que se desean evitar, el reto consiste en desarrollar un nuevo sistema que permita extraer e implementar el conocimiento de los expertos respecto a los tipos de sensores y su ubicación en el molde que proporcionen la información más útil para establecer un control de calidad eficaz durante la fase de producción.
1. Parametrización del problema
El primer paso es identificar los parámetros que los expertos usan para poner sensores en un molde (datos de entrada):
1. Parámetros asociados a la geometría del molde:
- WT: espesor máximo de la pared de la cavidad del molde.
- # C: Número de cavidades.
- FL: longitud máxima de flujo. Este parámetro depende del número de puntos de inyección y de su localización en la geometría del molde.
Material |
Densidad (gr/cm3) |
Pared espesor (mm) |
ABS |
1.05 |
1.143 − 3.556 |
Acetal |
1.41 |
0.762 − 3.048 |
Acrylic |
1.19 |
0.635 − 3.810 |
Liquid crystal polymer |
1.76 |
0.762 − 3.048 |
Long-fiber reinforced plastics |
1.2 |
1.905 − 25.40 |
Nylon |
1.14 |
0.762 − 2.921 |
Polycarbonate |
1.2 |
1.016 − 3.180 |
Polyester |
1.43 |
0.635 − 3.175 |
Polyethylene |
0.95 |
0.762 − 5.080 |
Polyphenylene sulfide |
1.54 |
0.508 − 4.572 |
Polypropylene |
0.91 |
0.635 − 3.810 |
Polystyrene |
0.6 |
0.889 − 3.810 |
Polyurethane |
1.1 |
2.032 − 19.05 |
Rechupes / vacíos
|
Deformaciones |
Atrapamientos de aire / efecto Diesel
|
Marca del punto de inyección |
Marcas de fibra
|
Líneas de soldadura |
Piezas incompletas por falta de llenado
|
Marcas de humedad |
Ráfagas |
Puntos negros |
|
|
2. El tipo de material a inyectar es otra variable a tener en cuenta. Según los expertos, la densidad del material determina el tiempo de llenado. La tabla 1 muestra la lista de materiales usados para validar el sistema.
3. Finalmente, los tipos de defectos a evitar también determinan la tipología y la posición de los sensores. La Tabla 2 muestra los principales defectos considerados en el sistema.
A partir de estos datos, los expertos son capaces de seleccionar los tipos de sensores más apropiados y su posición dentro del molde. Los datos de salida del sistema a desarrollar son una lista del tipo:
2. Metodología
La metodología desarrollada para resolver el problema anteriormente descrito, sigue las fases básicas de los sistemas basados en el conocimiento: (1) adquisición de conocimiento implícito y explícito para el aprendizaje y (2) extracción del conocimiento para generar soluciones.
El conocimiento industrial se puede clasificar en dos tipos: el conocimiento objetivo, que se puede encontrar en los manuales y bibliografía, y el conocimiento subjetivo o tácito, que está determinado por el factor humano (motivación, cualificación, experiencia, etc.). El conocimiento objetivo se puede representar en forma de reglas, mientras que el conocimiento subjetivo está representado en forma de casos. Los sistemas híbridos combinan ambos, el razonamiento basado en casos y las reglas [5, 6, 7]. Los principales argumentos para el uso de sistemas híbridos son:
- El razonamiento basado en casos emula el razonamiento de los expertos para tomar una decisión.
- La incorporación de nuevos casos aumenta significativamente la efectividad del sistema.
- Los conocimientos objetivos y subjetivos se implementan de forma separada, lo que permite darle mayor peso a unos u otros según convenga.
- Los casos son almacenados de forma acumulativa.
Un sistema de Razonamiento Basado en Casos (Case Based Reasoning, CBR) es una metodología de Inteligencia Artificial que permite resolver problemas recordando situaciones previas similares y reutilizando la información y el conocimiento sobre esa situación [4].. La idea original básica es resolver problemas nuevos adaptando las soluciones dadas a otros similares resueltos con anterioridad. La primera tarea en el ciclo de CBR es la recuperación de uno o más casos similares de la base de casos donde está almacenada la experiencia pasada. Para poder llevar a cabo la tarea de recuperación es necesario tener un algoritmo de recuperación y una medida de similitud que serán utilizados para obtener un conjunto de casos similares. Si no se encuentra un caso similar, se aplica el sistema de Razonamiento Basado en Reglas (Rules Based Reasoning, RBR).
La metodología utilizada en este estudio se ha basado en una primera fase de adquisición de conocimiento e implementación de las estructuras necesarias para representar dicho conocimiento, tanto el objetivo como el subjetivo. Por un lado, las reglas se crean en base a las recomendaciones de los fabricantes de sensores y estudios científicos que tratan de modelar casos genéricos. Esto se hace mediante el uso de un sistema basado en reglas. Por otro lado, los datos empíricos basados en la experiencia, se obtienen por medio del conocimiento de los técnicos expertos que es recogido a través de cuestionarios.
Una serie de casos representativos han sido objeto de estudio por parte de técnicos experimentados. Sus respuestas para encontrar la solución óptima son almacenadas en una base de datos como “conocimiento tácito” y es recuperado en una segunda fase de extracción. Esta fase está se centra en proporcionar una solución al usuario
3. Razonamiento Basado en Casos (CBR)
Tal y como se ha explicado anteriormente, el razonamiento basado en casos reutiliza información de situaciones pasadas. Al igual que en muchos algoritmos de aprendizaje automático, un caso está formado por varios atributos independientes que dan una descripción del problema y una solución para el caso. Así, la contribución de un atributo para una clase se puede determinar de forma independiente de los otros atributos. Este requisito simplifica los algoritmos de aprendizaje y genera un rendimiento robusto [1]. El CBR es un proceso que consta de cuatro pasos:
- RECUPERAR el caso o casos más similares.
- REUTILIZAR ese caso para resolver el problema.
- REVISAR la solución propuesta.
- GUARDAR las partes de esta experiencia que se consideren útiles para resolver futuros problemas.
La principal ventaja de CBR es la gran capacidad de adaptación a nuevos casos ya que se basa en extrapolar la solución. Aunque también existen algunos inconvenientes:
- Precisión: Los sistemas CBR necesita una gran cantidad de datos para ser precisos. La curva de aprendizaje de este tipo de sistemas tarda en ser estable.
- Puesta en marcha: Tal y como se ha comentado anteriormente, la necesidad de tener una base de datos significativa hace que el tiempo de puesta en marcha sea algo mayor que otras soluciones.
El sistema basado en reglas permite solucionar estos inconvenientes (ver figura 1).
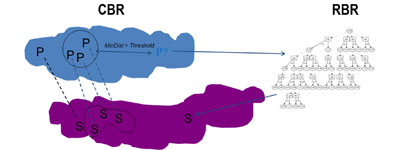
4. Razonamiento Basado en Reglas (RBR)
Las reglas implementadas en el sistema fueron extraídas de Kistler1, empresa fabricante de sensores, con el fin de solucionar los problemas encontrados por los inyectadores y moldistas. Para implementar tales reglas, primero se consideraron un conjunto de variables del sistema que se calculan a partir de los datos de entrada definidos en la sección 2:
- MIN_WT, MAX_WT: Rango recomendado de espesor mínimo/máximo de la pared, el cual depende del material seleccionado (véase la tabla 1).
- R = 0.2: Se considera que cuando el espesor de la pared es superior en un 20% al MIN_WT o inferior en un 20% al MAX_WT, la variable de espesor de la pared se convierte en un parámetro crítico para la selección de los sensores. R es un valor teórico y se puede cambiar dependiendo de las actuaciones.
- TH_MIN_WT = MIN_WT + MIN_WT * R: umbral a partir del cual, la pared de la pieza de plástico se considera muy fina, lo que requiere un tratamiento especial.
- TH_MAX_WT = MAX_WT - MAX_WT * R: umbral a partir del cual, la pared de la pieza de plástico se considera muy gruesa, lo que requiere un tratamiento especial.
- TH_CR = 200: Relación entre la longitud máxima de flujo teórica (FL) y el grosor de la pared (WT). Los expertos afirman que tal relación debería ser inferior a 200.
- TH_MAX_FL = TH_CR* TH_MAX_WT: Umbral a partir del cual la longitud de flujo es crítica.
Las reglas aplicadas se enumeran en la tabla 32.
Regla |
Recomendación |
T H _M I N _W T ≤ W T ≤ T H _M AX _W T F L ≤ T H _M AX _F L |
Presión, 1/3 de la longitud del flujo |
W T ≤ T H _M I N _W T |
Presión, final de la longitud del flujo |
F L/W T ≥ T H _C R |
Presión, final de la longitud del flujo Presión, cerca del punto de inyección |
DEFECTS = {WELD LINES} |
Presión, final de la longitud del flujo |
DEFECTS = {SINK MARKS} |
Presión, cerca del punto de inyección |
#C > 1 |
Temperatura, cerca del punto de inyección |
DEFECTS = {FLASHES | INCOMPLETELY FILLED PARTS} |
Temperatura, final de la longitud del flujo |
DEFECTS = {WARPAGE | JETTING | AIR ENTRAPMENT | G. FIBER STEACKS | DULL SPOTS | CHARRED STEAKS | WELD LINES} |
Temperatura, cerca del punto de inyección |
1 http://www.kistler.com/
2 Las normas no son excluyentes, por lo que, varias reglas pueden activarse en función de los datos de entrada.
5. Solución implementada
5.1. Representación de los casos
Se ha implementado un caso como una combinación de los datos de entrada y los datos de salida. Los datos de entrada son un vector de dimensión n que representa el problema, con una medida de similitud asociada (véase la sección 5.2). Tal vector coincide en gran parte con los mismos datos de entrada de la RBR definido en la sección anterior, y se resume en la tabla 4.
Nombre |
Descripción |
Tipo |
FL DS #C DEFECTS |
Máxima longitud de flujo (mm) Densidad del material (ver tabla 1) Numero de cavidades Defectos a evitar (ver tabla 2) |
CUANTITATIVO CUANTITATIVO CUANTITATIVO CUALITATIVO |
Nombreme |
Descripción |
Valores |
ST LC |
Tipo de Sensor Posición en el molde |
{Presión | Temperatura} {Cerca del punto de inyección | 1/3 de la longitud del flujo | 1/2 de la longitud del flujo | 2/3 de la longitud del flujo | Final de la longitud del flujo } |
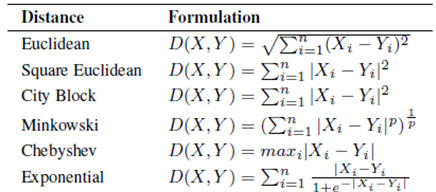
Los datos de salida son una lista que definen el tipo y la localización del sensor (ver tabla 5). A diferencia del RBR, la variable de material es un atributo de los casos porque los expertos consideran que es un factor determinante en la selección y colocación de los sensores dentro del molde.
Las medidas de similitud se aplican sobre los datos cuantitativos. Se implementaron y se validaron las distancias indicadas en la tabla 6. Para los atributos cualitativos, el problema es diferente. ¿Cómo se mide la distancia entre dos tipos de defectos? Los tipos de defectos son variables binarias: cada defecto está presente (o no) en el caso. La distancia de dos objetos representados por las variables binarias se puede medir en términos de número de ocurrencias (frecuencia) positivas y negativas de cada objeto. Un atributo binario puede ser:
- Simétrico: Cuando los dos estados (0 y 1) tienen la misma importancia, y llevar el mismo peso, por ejemplo, un atributo que representa el género de una persona (masculino/femenino).
- Asimétrico: Si uno de los estados es más importante que el otro. El estado 1 representa el estado más importante, que suele coincidir con el estado menos común.
Por ejemplo, supongamos que tenemos las siguientes dos listas de defectos que deben evitarse:

Obj1 está representada por el vector (0, 1, 0, 1, 0, 1, 0, 0) y Obj2 con el vector (1, 1; 0; 0; 0; 0; 0; 0). Entonces, sea p el número de variables positivas en ambas listas, q el número de variables positivas en Obj1 pero no en Obj2, r el número de variables negativas en Obj1 que son positivas en Obj2, s las variables negativas para ambas listas y t el número total de variables, hemos implementado las siguientes distancias:
- Distancia mínima (simétrica): donde D (Obj1; Obj2) = (q + r) / t. En nuestro ejemplo, puesto que q = 2, r = 1 y t = 8, la distancia es de 0,375.
- Distancia de Jaccard (asimétrica): donde D (Obj1; obj2) = (q + r) / (p + q + r). En nuestro ejemplo, puesto que p = 1 la distancia es de 0,75
Las pruebas preliminares muestran que en nuestro sistema, la distancia de Jaccard da mejores resultados que el método distancia mínima, ya que es más importante que un defecto a evitar esté presente en un caso.
El algoritmo de recuperación para nuestra aplicación CBR sigue la estructura estándar, y se muestra en el algoritmo 1. Se muestra el algoritmo utilizando la distancia de Jaccard para los atributos cualitativos y la distancia euclídea de los atributos cuantitativos. En función de las entradas, las características del perfil de los usuarios y la tipología del molde, se puede decidir qué medida de similitud es la más adecuada.
Asumimos que los atributos numéricos y categóricos tienen el mismo peso, y por lo tanto, la función getNearestNeighbors suma ambos valores cuando seleccionamos los casos más cercanos. Dicha selección devuelve los NN casos con menor distancia (NN es variable).
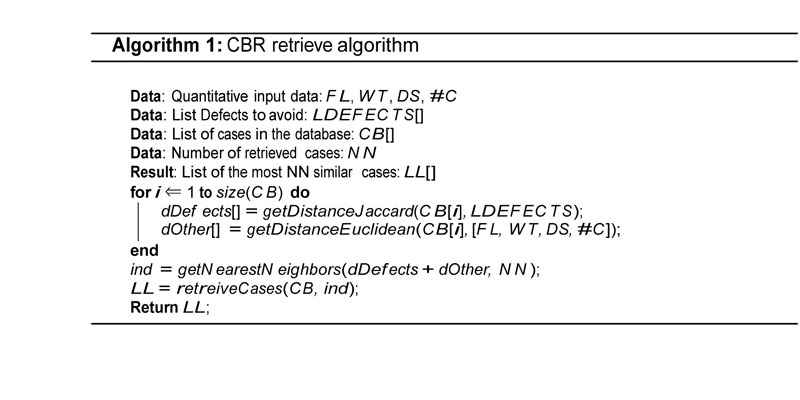
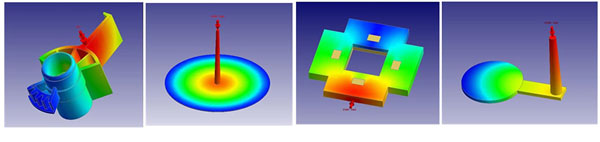
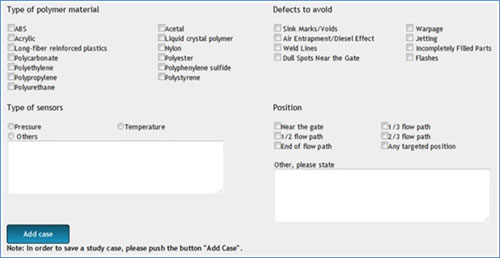
6. Solución software
El sistema desarrollado se compone de dos módulos. El primer módulo permite obtener el conocimiento de los expertos por medio de casos representativos. Se escogieron un número de geometrías representativas de un número de casos. Posteriormente se preguntó a los técnicos expertos que, en base a la geometría del molde y a otros parámetros de proceso, tales como la clase de material, defectos a evitar, etc., qué sensores pondrían y donde.
La Figura 2 muestra las cuatro figuras utilizadas en este cuestionario. Para cada geometría es posible añadir más de un caso (ver figura 3). Además, el sistema evalúa el perfil del experto con el fin de ponderar sus respuestas dependiendo de la experiencia mostrada.
El segundo módulo implementa el sistema híbrido descrito anteriormente con el fin de dar recomendaciones a aquellos usuarios que no tienen experiencia en la sensorización de moldes. El número de recomendaciones se puede modificar, aunque se establece en 2, donde la primera opción es la opción más recomendada. Para fines de validación, es posible comparar cada una de las soluciones. Dicha comparación se usa para ponderar los casos similares y proporcionar la solución más óptima.
Conclusiones
En este trabajo se ha descrito el desarrollo e implementación de un sistema híbrido basado en el conocimiento que combina el razonamiento basado en casos y el razonamiento basado en reglas. Las principales fases presentes en el desarrollo de un sistema basado en el conocimiento (adquisición y generación de conocimiento), han sido implementadas como dos aplicaciones web diferentes.
El proceso de razonamiento basado en reglas se ha definido siguiendo las recomendaciones encontradas en el estado del arte. En el caso del razonamiento basado en casos, se han implementado y analizado diferentes medidas de similitud. Los primeros análisis han mostrado que la distancia Euclídea y la distancia Jaccard dan los mejores resultados para los atributos cuantitativos y los binarios/cualitativos, respectivamente.
El sistema híbrido resultante puede ser el punto de entrada para los simuladores numéricos, permitiendo reducir el área de superficie de la geometría del molde a analizar y, por tanto, reduciendo el tiempo computacional.
El resultado es una herramienta que ayuda a decidir que sensores y en qué lugar situarlos en el molde. Con todo ello se consigue un molde con un tiempo mínimo de configuración y con un ratio bajo de piezas defectuosas gracias a la monitorización continua del proceso basado en el procesamiento inteligente de los datos recibidos durante la inyección a través de sensores colocados en el molde.
Agradecimientos
Este trabajo ha sido realizado en el marco del proyecto Mold4ProdE (FP7-NMP2-SE-2010-246450) parcialmente financiado por la Comisión Europea.
El consorcio Mold4ProdE, con un total de 3.9 millones de euros de presupuesto, se compone de 25 organizaciones europeas, entre las que se encuentra el centro Tecnológico Ascamm. A lo largo de 3 años se ha desarrollado un sistema que permite aumentar la eficiencia de los procesos de inyección de plástico mejorando el diseño y puesta en marcha de las herramientas de inyección.
Para más información del proyecto Mold4ProdE visitar la página web www.mold4prode.org
Referencias
[1] A. Aamodt and E. Plaza. Case-based reasoning: foundational issues, methodological variations, and system approaches. AI Communications, 7(1):39–59, 1994.
[2] X. Berjaga, Á. Pallarés and J. Meléndez. A framework for case-based diagnosis of batch processes in the principal components space. In Proceedings of the 14th IEEE international conference on Emerging technologies & factory automation, ETFA’09, pages 745–753, Piscataway, NJ, USA, 2009. IEEE Press.
[3] eMold Project. eMold: Total Life Cycle Approach for Efficient and Networking Plastic Injection Moulding Processes. http://www.emold.eu/home, 2006.
[4] W. Hu and S. Masood. An intelligent cavity layout design system for injection molds. International Journal of CAD/CAM, 2(1):69–75, 2002.
[5] R.S. Jiang, D.H. Zhang, and K. Wang, W.H.and Bu. Intelligent design of investment casting mold based on a hybrid reasoning method. CHINA FOUNDRY, 6(1):20–23, 2009.
[6] C.K. Kwong and G.F. Smith. A computational system for process design of injection molding: combining blackboard-based expert system and case- based reasoning approach. The International Journal of Advanced Manufacturing Technology, 14(4):239–246, 1998.
[7] S.K. Ong, Prombanpong S., and K.S. Lee. An object-oriented approach to computer-aided design of a plastic injection mold. Journal of Intelligent Manufacturing, 6(1):1–10, 1995.