Geocisa realiza las obras del pozo de ataque de Kirtling St.
El Thames Tideway Tunnel (TTT) constituye uno de los mayores proyectos de Ingeniería Civil que se están llevando a cabo en este momento a nivel europeo. Se trata de un túnel destinado a servir de colector de margen, que discurre de oeste a este de Londres y a lo largo de la orilla del río Támesis. El túnel, que ha quedado divido en tres sectores (oeste, central y este), tendrá una longitud de más de 30 km de y 7,5 m de diámetro, transcurriendo hasta 66 m por debajo del río Támesis. Como parte destacada del proyecto, dentro del sector central, se encuentra el Pozo de Kirtling Street. Este pozo, entre otras funciones, se destinará a pozo de ataque para las dos primeras tuneladoras (TBM), desde aquí se ensamblarán las dos tuneladoras para ir avanzando en sentido este y oeste al mismo tiempo.
En la primavera de 2016 Geocisa fue la empresa seleccionada para la ejecución de los muros pantallas que servirán de contención para la ejecución del Pozo de Kirtling St. La solución adoptada ha sido la ejecución de las pantallas de hormigón armado mediante una hidrofresa capaz de alcanzar hasta 100 m de profundidad de excavación, y espesor de pantalla de hasta 1,5 m.
Para asegurar el éxito de los trabajos en plazo y presupuesto, Geocisa desplegó un equipo humano compuesto de especialistas altamente cualificados, que se ocuparon de la ejecución de los trabajos, así como de la gestión que requería una obra de estas características y, de esta manera, llegar a alcanzar los altos estándares de calidad exigidos en Reino Unido.
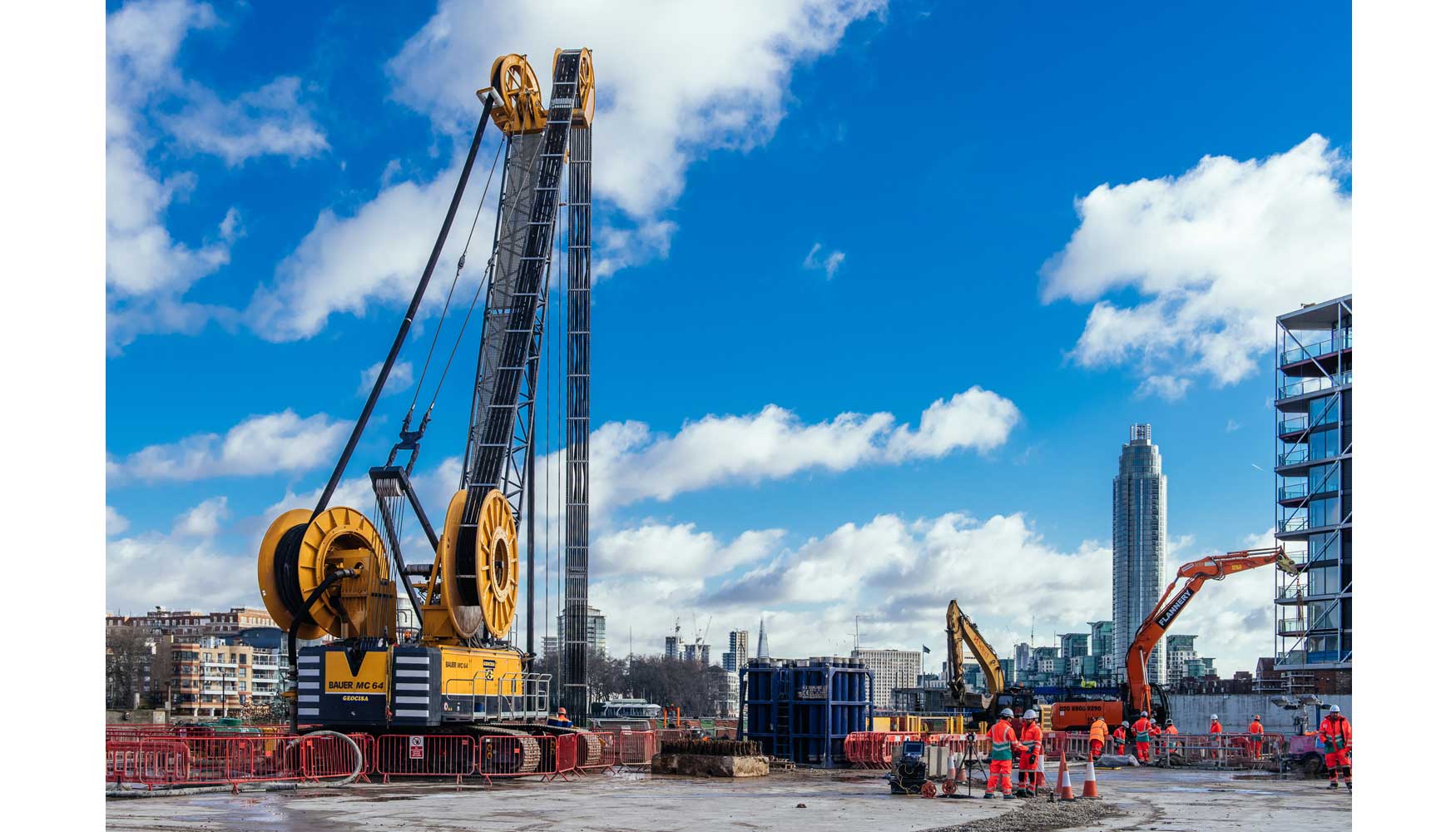
Antecedentes
La actual red de saneamiento de la capital británica data de mediados del siglo XIX. En 1850 más de 400.000 toneladas de aguas residuales eran vertidas directamente al río Támesis. Durante el inusualmente seco verano de 1858 se produjo el denominado 'Gran Hedor' durante el cual el olor de residuos humanos no tratados y vertidos al río Támesis fue insoportable en el área central de la ciudad de Londres. Este mismo año el Parlamento Británico aprobó una ley para habilitar la mejora del sistema de saneamiento de aguas de la metrópolis. El Ingeniero Jefe de la Junta Metropolitana de Obras (Joseph Bazalgette) ideó el nuevo sistema de la red de alcantarillado, que implicó dos años de desarrollo en su fase de proyecto, £3 millones de presupuesto y 15 años de ejecución. En aquel entonces supuso el mayor proyecto de ingeniería civil, jamás llevado a cabo en Inglaterra. Esta red comprendía 1.770 km de pequeño alcantarillado, que alimentaban a 134 km de colectores de gran diámetro que discurrían de oeste a este de la capital, paralelamente al río. Esta red de alcantarillado transportaba una mezcla de aguas residuales y de tormentas que descargaba en el río Támesis, aguas abajo de la capital (ver figura 1).
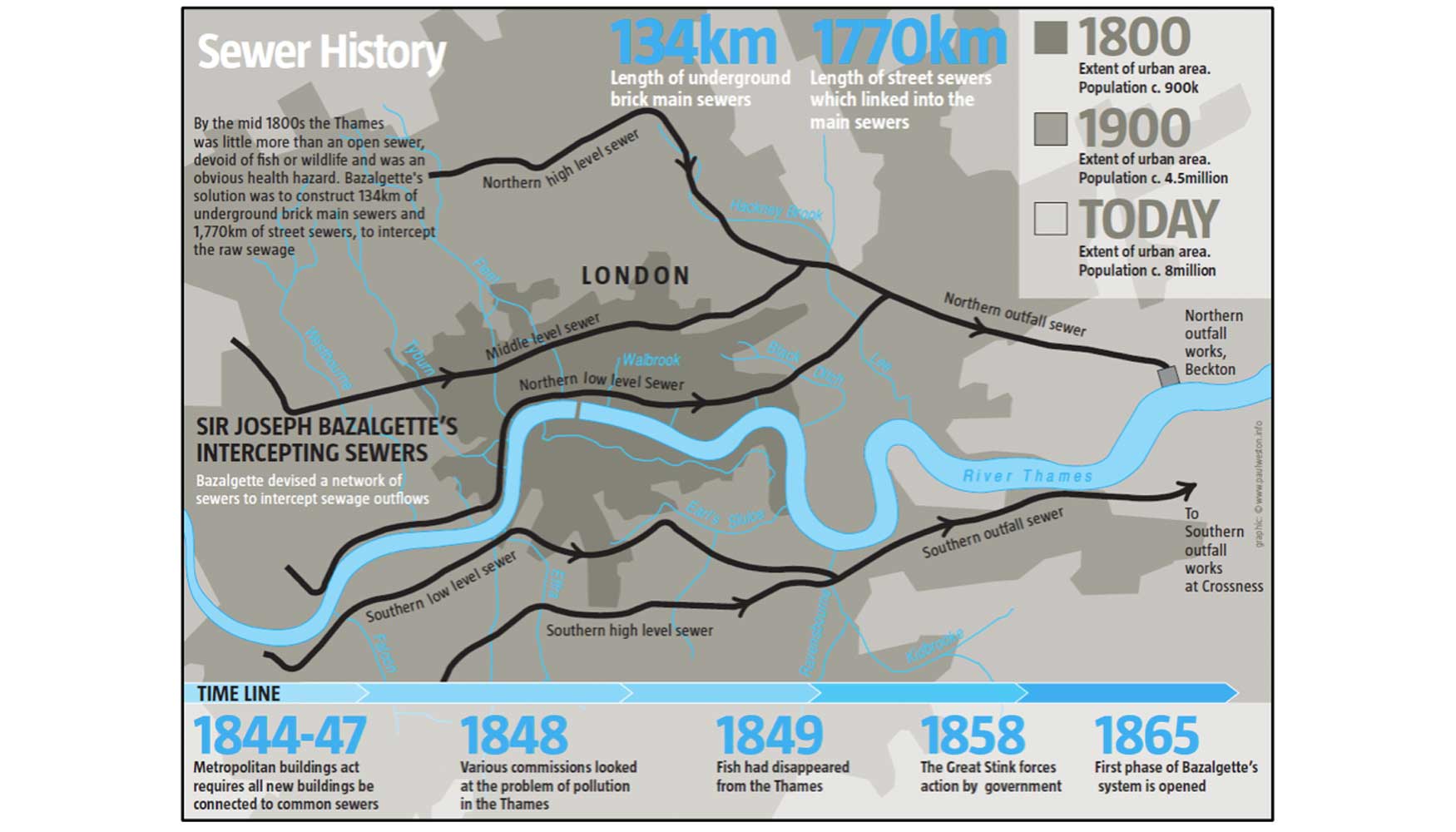
Joseph Bazalgette estimaba que este nuevo sistema de alcantarillado evitaría cerca de 12.000 muertes anuales por cólera y otras enfermedades transmitidas a través del agua. En aquel momento la ciudad de Londres contaba con 2,5 millones de habitantes pero Bazalgette también anticipó el crecimiento futuro de la metrópolis, diseñando su sistema para perdurar, aplicando la más alta calidad de construcción y una considerable capacidad de respuesta. Para hacer frente a avenidas excepcionales, incluyó 57 aliviaderos en su red de alcantarillado, permitiendo que el exceso de caudal vertiera de vuelta al río Támesis, evitando así inundaciones.
Este sistema de alcantarillado diseñado por Sir Joseph Bazalgette, ha dado respuesta a las necesidades de evacuación de aguas residuales de la ciudad durante más de un siglo y medio, pero aquellas avenidas excepcionales que predijo Bazalgette, ahora se producen una vez por semana, al haberse triplicado la población de la urbe y haber aumentado notablemente la superficie de la misma.
Actualmente cerca de 39 millones de metros cúbicos de aguas residuales, mezcladas con agua de lluvia, son vertidas a través de los aliviaderos al río Támesis. Casi el 40% de estas descargas se producen a través del aliviadero de Abbey Mills hacía el río Lee (afluente del río Támesis).
La compañía encargada de la gestión de la red de alcantarillado de Londres (Thames Water) ha desarrollado el Programa de Mejora Thames Tideway, cuyo objetivo es minimizar la cantidad de aguas residuales que vierten estos aliviaderos directamente al río Támesis, así como mejorar la red de alcantarillado de la ciudad. Las actuaciones de este Programa están dividas en tres fases: la primera consiste en la mejora de los tratamientos de aguas residuales, la segunda consiste en la construcción del Lee Tunnel y la tercera la construcción del Thames Tideway Tunnel (TTT). El TTT discurrirá desde Acton al oeste de Londres paralelo al río hasta antes de virar al noreste hacia Abbey Mills (ver figura 2). Desde Abbey Mills conectará con el Lee Tunnel para conducir las aguas residuales hasta la Estación depuradora de Beckton. Este colector de margen, discurrirá a gran profundidad para evitar la infinidad de servicios existentes bajo Londres. El colector fluye por gravedad, por lo tanto será más profundo en la zona final del este.
El proyecto supondrá un incremento de la capacidad de la red de alcantarillado y una mejora de la calidad del agua en el río, diseñado para dar uso durante los próximos 120 años y ser un legado para la capital. Creará unos 4.000 puestos de trabajo en los próximos años. Se prevé que esté finalizado en el 2023, ayudando en reducir el vertido de aguas residuales al río Támesis en 39 millones de metros cúbicos al año.
Thames Tideway Tunnel
De los dos túneles previstos dentro del Programa de Mejora Thames Tideway, el Thames Tideway Tunnel (TTT) será, desde el punto de vista de la ejecución, el túnel más complicado, convirtiéndose cuando esté terminado, en el túnel más profundo de todo Reino Unido. Tras 2,5 años de diseño y desarrollo del trazado del túnel se ha conseguido mejorar el mismo, reduciendo la longitud original en 7 km, pasando a medir 32 km. El presupuesto final de ejecución del TTT supondrá una inversión de 4.200 millones de libras.
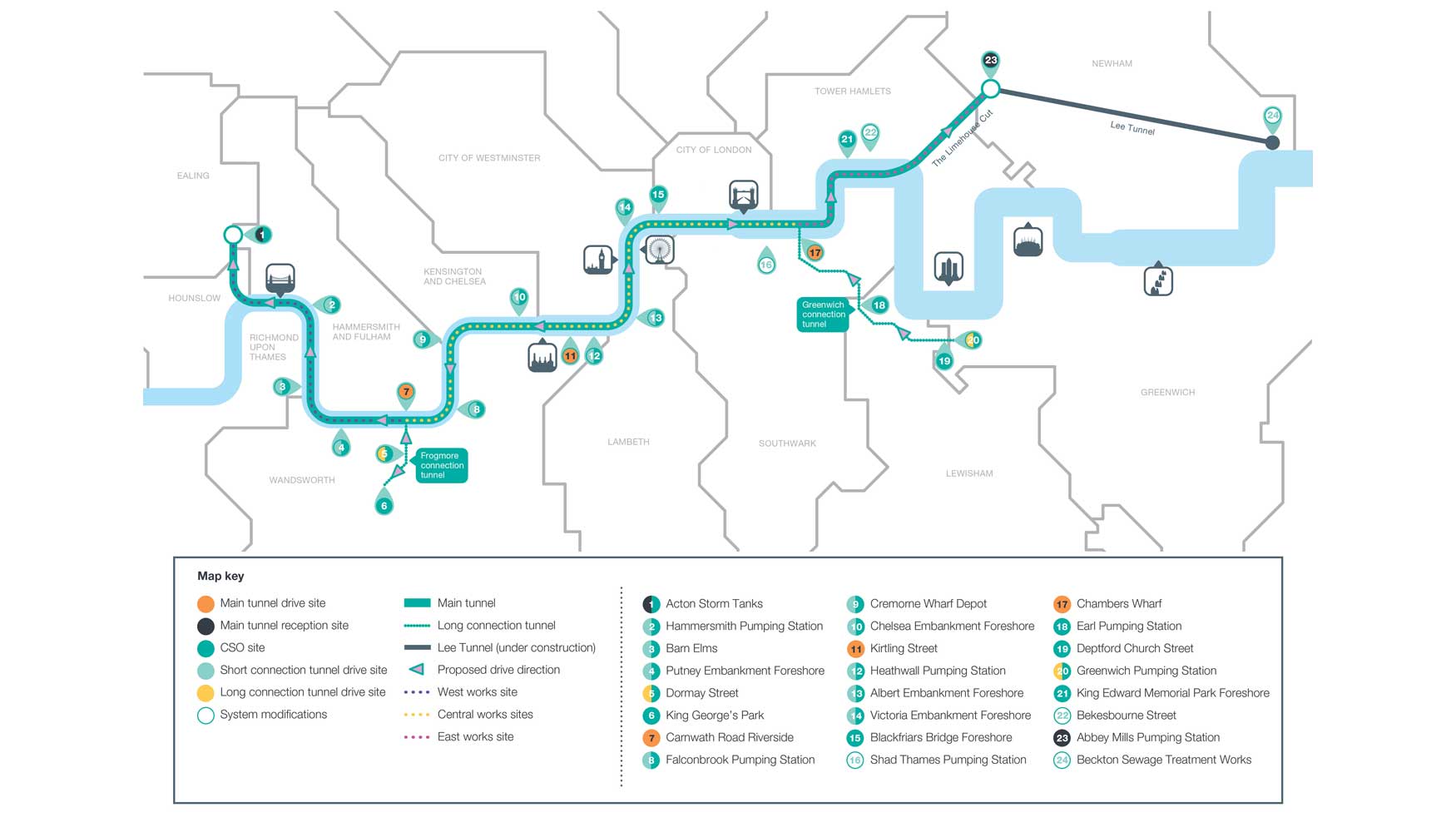
El TTT se ha dividido en tres partes que corresponden por su situación geográfica al Sector Oeste, Sector Central y Sector Este (ver figura 3). Cada uno de estos sectores ha sido adjudicado a diferentes contratistas, habilitando así que se estén ejecutando todos los tramos al mismo tiempo, para asegurar que el túnel se ejecuta dentro de los plazos previstos.
- West Section: Adjudicada a la Joint Venture formada por BAM Nuttall, Morgan Sindall y Balfour Beatty Group.
- Central Section: Adjudicada a la Joint Venture formada por Ferrovial Agroman UK y Laing O´Rourke.
- East Section: Adjudicada a la Joint Venture formada por Costain, Vinci Construction Grounds Projects y Bachy Soletanche.
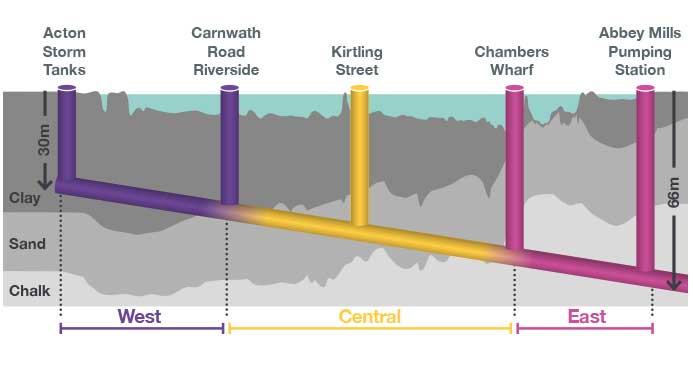
Sector Central
El consorcio formado por Ferrovial UK y Laing O´Rourke (FLO Joint Venture) ha sido adjudicatario del Sector Central por importe de 746 millones de libras.
Este Sector Central es el más largo de los tres en que se divide el TTT, con 12,7 km de longitud divididos en dos tramos de túnel de 7,2 m de diámetro que arrancan del pozo de ataque de Kirtling St., 5,1 km hacia el oeste y 7,6 km hacia el este. Estos túneles se ejecutarán con dos Tunnel Boring Machine (TBM) que comenzarán su excavación desde el pozo de ataque de Kirtling St. La encargada de dirigirse hacia el este es la bautizada como Úrsula y la que se dirigirá hacia el oeste será Millicent. Esta sección central también incluye la ejecución de 8 pozos de entre 9 y 30 m de diámetro y entre 42 y 62 m de profundidad, así como 6 túneles cortos de conexión de entre 30 y 257 m de longitud y entre 3,2 y 4 m de diámetro interior. De todos estos pozos destaca el pozo de ataque de Kirtling St. desde donde se introducirán las dos TBM para ejecutar simultáneamente ambos túneles.
Pozo de Kirtling Street
El pozo de Kirtling St. está situado en la orilla sur del río, integrándose dentro de la recuperación del área de Battersea Power Station, antigua central eléctrica actualmente en reconstrucción como centro comercial y zona residencial, dentro del barrio de Wandsworth.
Se trata de un pozo de planta circular de 32 m de diámetro y que se excavará interiormente hasta 62 m de profundidad. Este pozo constará de dos revestimientos, uno primario con una función de contención, que será ejecutado mediante una pantalla de hormigón armado de 1,20 m de espesor y 86,4 m de profundidad (ver figuras 4 y 5), y un revestimiento secundario e interior al primario, para conseguir una mayor estanqueidad en el pozo.
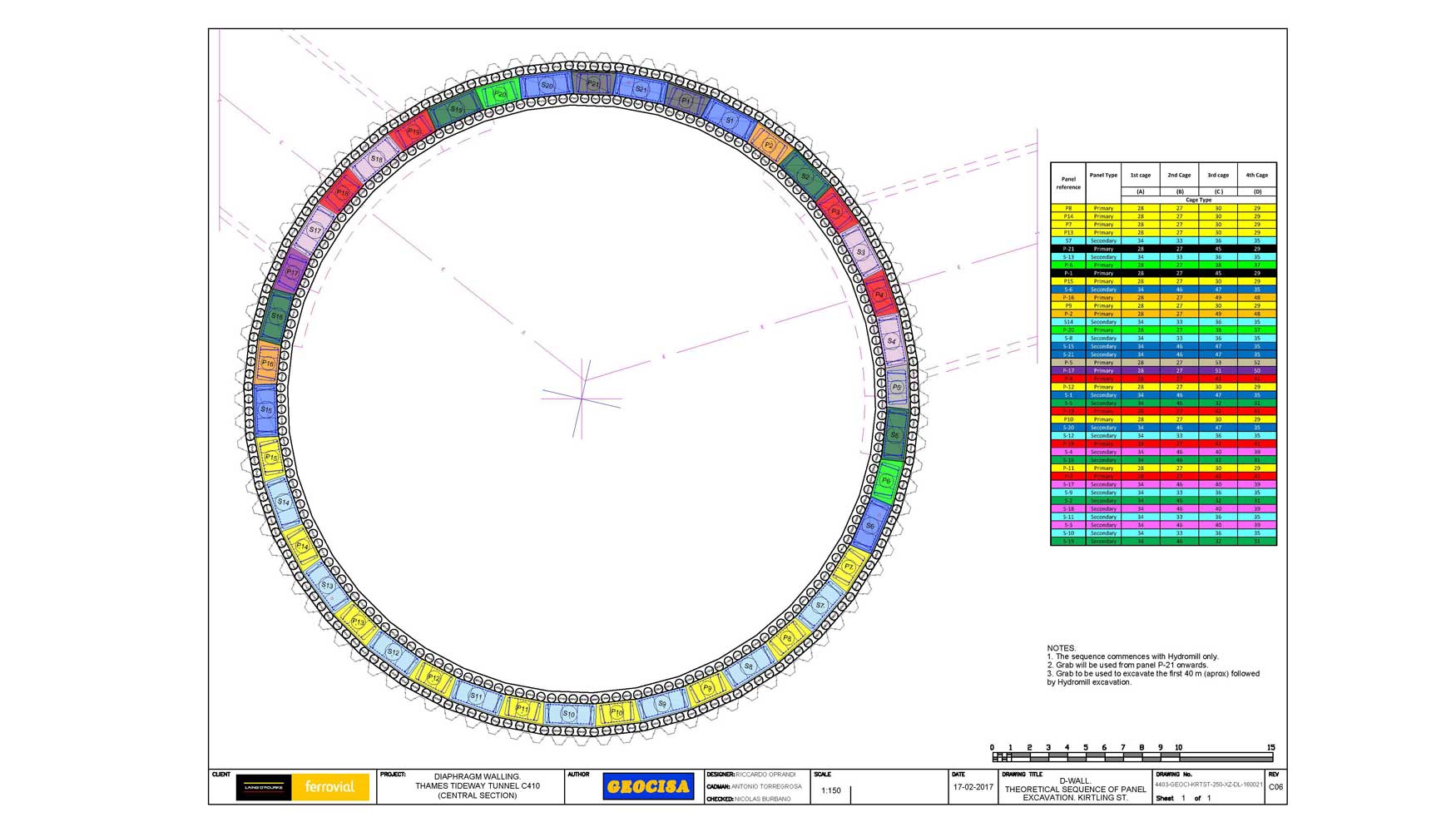
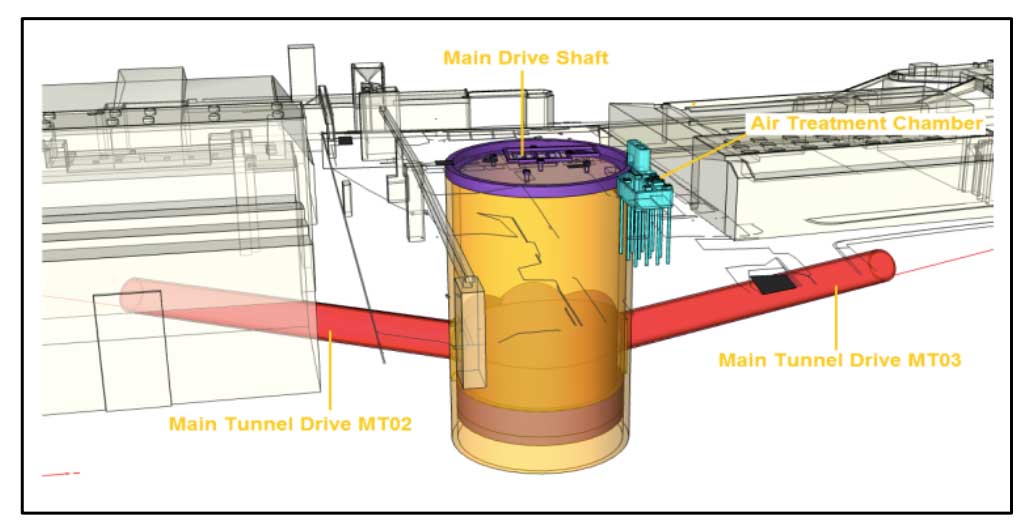
En mayo de 2016 Geotecnia y Cimientos S.A (Geocisa) fue contratada para la ejecución de las pantallas de hormigón armado que servirían de contención para la ejecución del pozo. Desde este mismo instante se comenzó a trabajar activamente con nuestro cliente colaborando en los aspectos de diseño propio de nuestra especialidad, así como aportando información sobre los equipos que iban a ejecutar los trabajos. Debido a las elevadas exigencias de verticalidad que marcaba el proyecto (1 en 400, lo que supone una desviación máxima de 21 cm a 86 m de profundidad) y la gran profundidad a la que se situaba el pie de la pantalla, Geocisa decidió afrontar la ejecución de la excavación con hidrofresa. En esta ocasión nos decantamos por una hidrofresa del fabricante BAUER Maschinen GmbH, en concretó se trató de una fresa BC-35 montada sobre una grúa MC-64 montando el sistema de mangueras Hose Drum System (HDS) (ver figura 6).

Características del terreno y soluciones técnicas adoptadas
El pozo de Kirtling St. se encuentra ubicado a escasos 20 metros de la orilla sur del río Támesis. La tipología del terreno que nos encontramos aquí es la estratigrafía típica de esta zona de Londres, formada de arriba hacia abajo por (ver figura 7):
- unos primeros metros (3 a 5 metros) de relleno antrópico (Made ground),
- seguido de una zona aluvial con elevado contenido orgánico (Aluvium), con una potencia de entre 5 y 9 metros,
- que da paso a la denominada arcilla de Londres (London Clay), que en esta zona tenía una potencia de unos 32 metros,
- más adelante se encuentra el denominado Lambeth Group, formación que intercala capas de arcilla rígidas con capas de arenas y gravas, con una potencia aproximada de 17 metros,
- la siguiente formación se trataba de la denominada Thanet Sand consistente en una capa de arenas finas con una potencia de 10 metros,
- finalmente se encuentra el denominado Chalk, se trata de una formación de tiza o creta blanca donde se intercalan bolos de tamaño decimétrico de sílex (Flint).
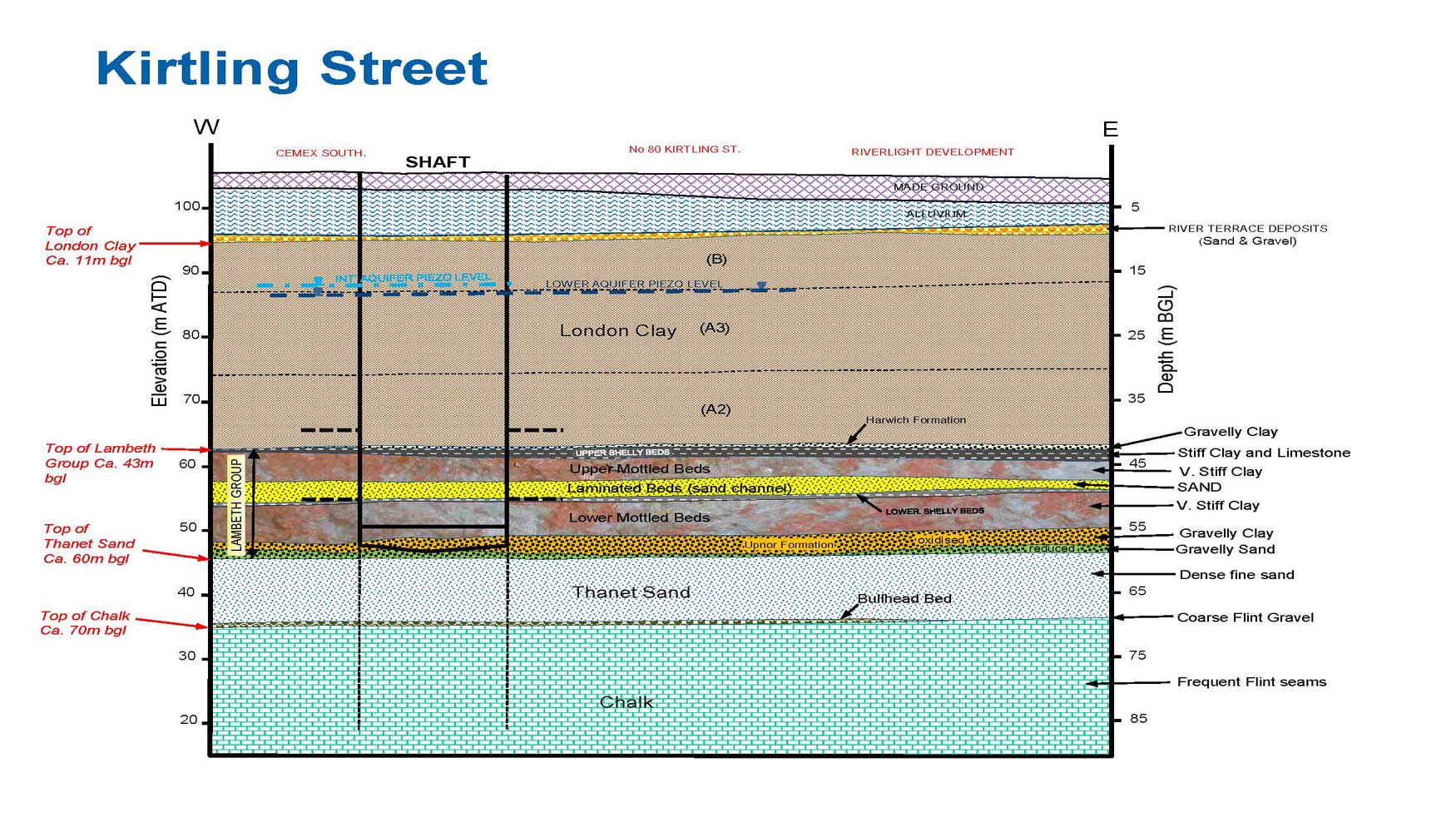
Tras un primer análisis del terreno, a través del cual se debería excavar las pantallas, nos surgieron los primeros retos que deberíamos resolver, antes de comenzar la fase de ejecución.
Los terrenos donde se localizaba el pozo de Kirtling St. habían estado destinados a usos industriales y concretamente en los últimos años había albergado una planta de hormigón. Los primeros metros del terreno estaban afectados por antiguas cimentaciones y en concreto de varias decenas de pilotes de hormigón armado que habían servido de cimentación de los silos de la planta de hormigón. También existía la sospecha de que estos primeros metros del terreno, estaban contaminados por vertidos incontrolados de hidrocarburos. Para hacer frente a este problema se plantearon varias soluciones; primeramente se decidió realizar un recinto de tablestacas perimetralmente al pozo, que permitiera retirar parte de los terrenos posiblemente contaminados. Se optó por localizar y retirar los pilotes existentes mediante medios mecánicos. Finalmente se decidió ejecutar lo que se denominó una extensión del muro guía. Consistió en la ejecución de 343 pilotes de hélice continua, 350 mm de diámetro y 12 m de profundidad, por debajo del muro guía y que sirvieran tanto para transmitir los esfuerzos del muro guía a un terreno competente, así como para evitar colapsos de la excavación, en los primeros metros donde el terreno no tenía casi cohesión y donde dispondríamos de poca carga hidráulica de lodo de perforación, para hacer frente a esta inestabilidad.
Durante la Segunda Guerra Mundial, en la denominada Batalla de Inglaterra entre 1940 y 1941, se produjeron bombardeos de objetivos industriales y centros civiles que comenzaron con intensos ataques a Londres. Algunos de los proyectiles lanzados por las tropas alemanas, quedaron sin explotar y sepultados bajo el terreno. Este es uno de los problemas a los que se deben enfrentar todos los movimientos de tierras que se llevan a cabo en Londres, pero que especialmente interfiere en los trabajos de cimentación. Para minimizar los riesgos de encontrar algún artefacto sin explotar, se implantó en obra una inspección previa a los trabajos de cimentación, por una empresa especializada, que mediante equipos dotados de magnetómetros realizan una inspección de los primeros metros del terreno para detectar si existe algún proyectil sin explotar, denominada localmente, UXO (UnExploded Ordnance).
Otra de las dudas que rondaba por nuestras cabezas, antes del comienzo de los trabajos, era el comportamiento de las ruedas de corte de la hidrofresa en la London Clay. Antes del comienzo de nuestras excavaciones no se disponía de una amplia experiencia acerca del comportamiento de las ruedas de corte de la hidrofresa en la London Clay. Las hidrofresa manufacturadas por Bauer, habitualmente pueden montar tres tipos diferentes de ruedas de corte, en función del tipo de terreno que se pretenda excavar. En esta ocasión nos decantamos por montar las denominadas ruedas estándar (ver figura 8), diseñadas con dientes de corte dispuestos de forma estratégica para generar un corte continuo del terreno y pensadas especialmente para excavar en suelos mixtos, donde se intercalen suelos densos con rocas blandas. Una de nuestras mayores preocupaciones era que la London Clay se 'embozara' en las ruedas de corte, impidiendo un adecuado avance de la excavación. Para afrontar este reto, Geocisa UK con la colaboración de ECODRILL, del Grupo empresarial KMMB (representante de BAUER Maschinen GmbH en España), decidió innovar probando un nuevo sistema de ruedas de corte que BAUER acababa de presentar en la Bauma 2016. Se trató de las denominadas ruedas de corte híbridas, diseñadas para perforar en terrenos mixtos y desarrolladas especialmente para terrenos arcillosos (ver figura 9). Teniendo en cuenta nuestra experiencia perforando con hidrofresa en suelos arcillosos, decidimos desarrollar un sistema de cepillos limpiadores (ver figura 10) para poder reducir al máximo los tiempos perdidos en la limpieza de las ruedas de corte tras atravesar suelos arcillosos. El sistema desarrollado por Geocisa UK fue todo un éxito, disminuyendo los tiempos de limpieza de ruedas de corte de casi dos horas a menos de 30 minutos.
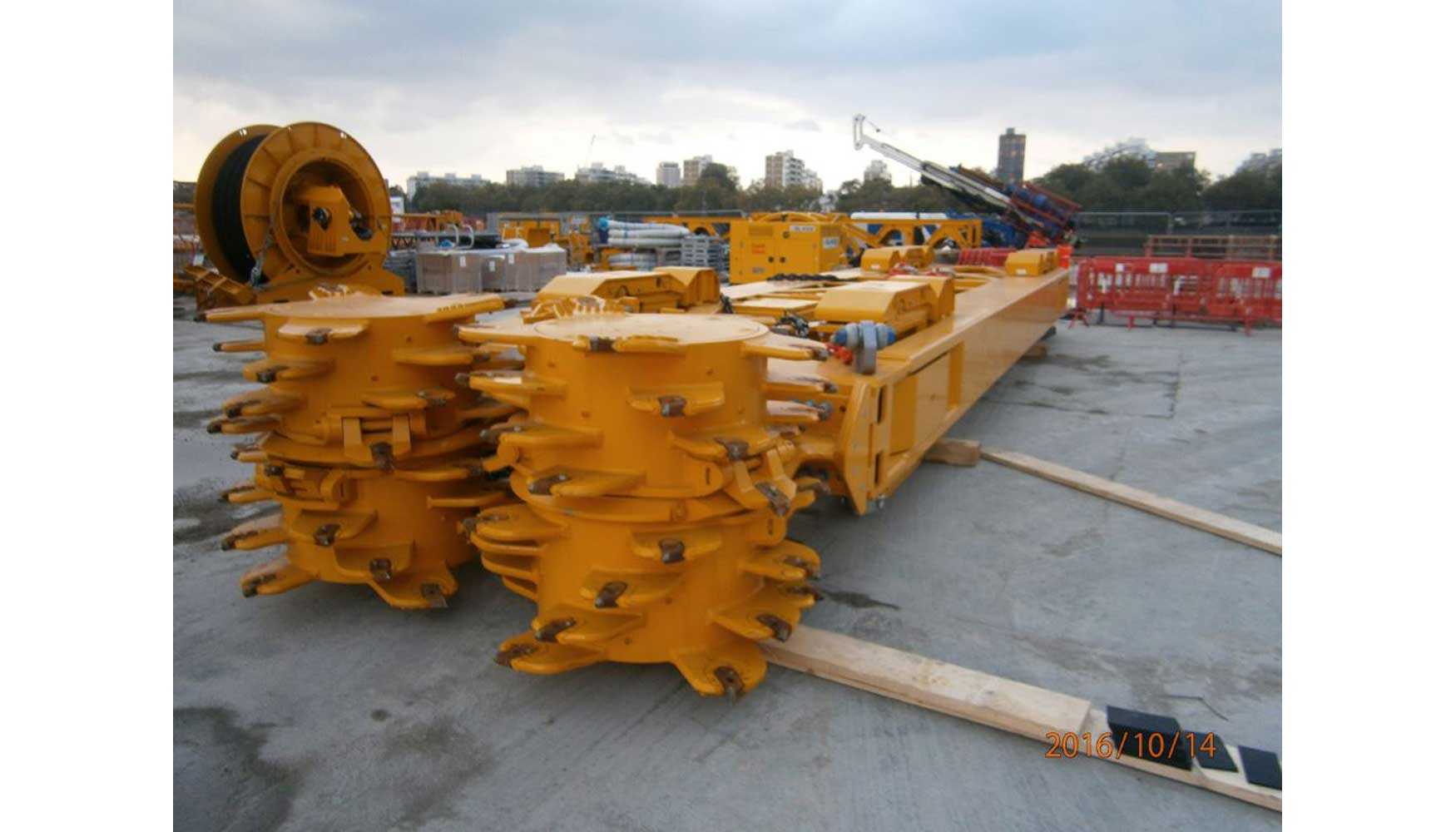
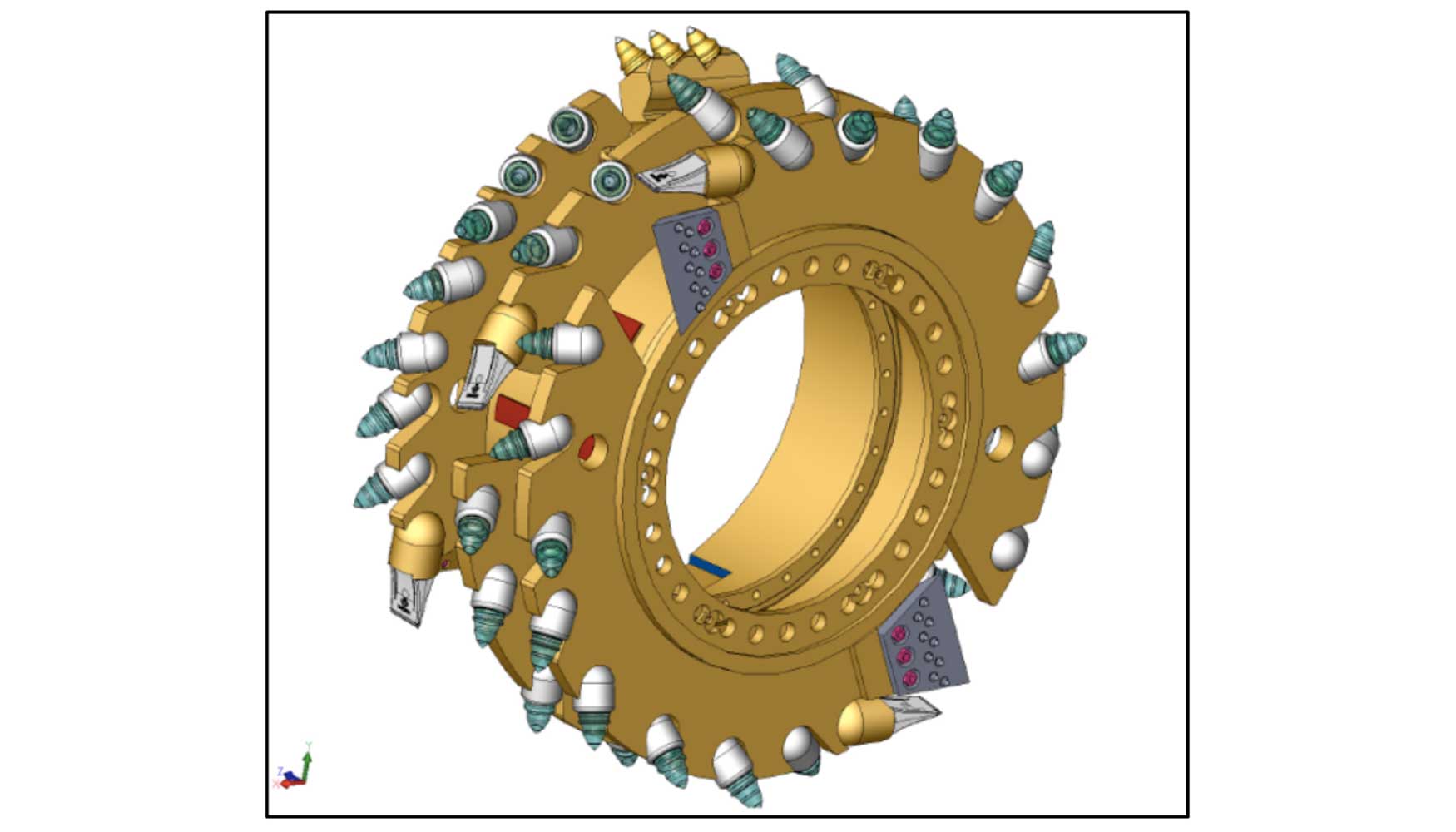
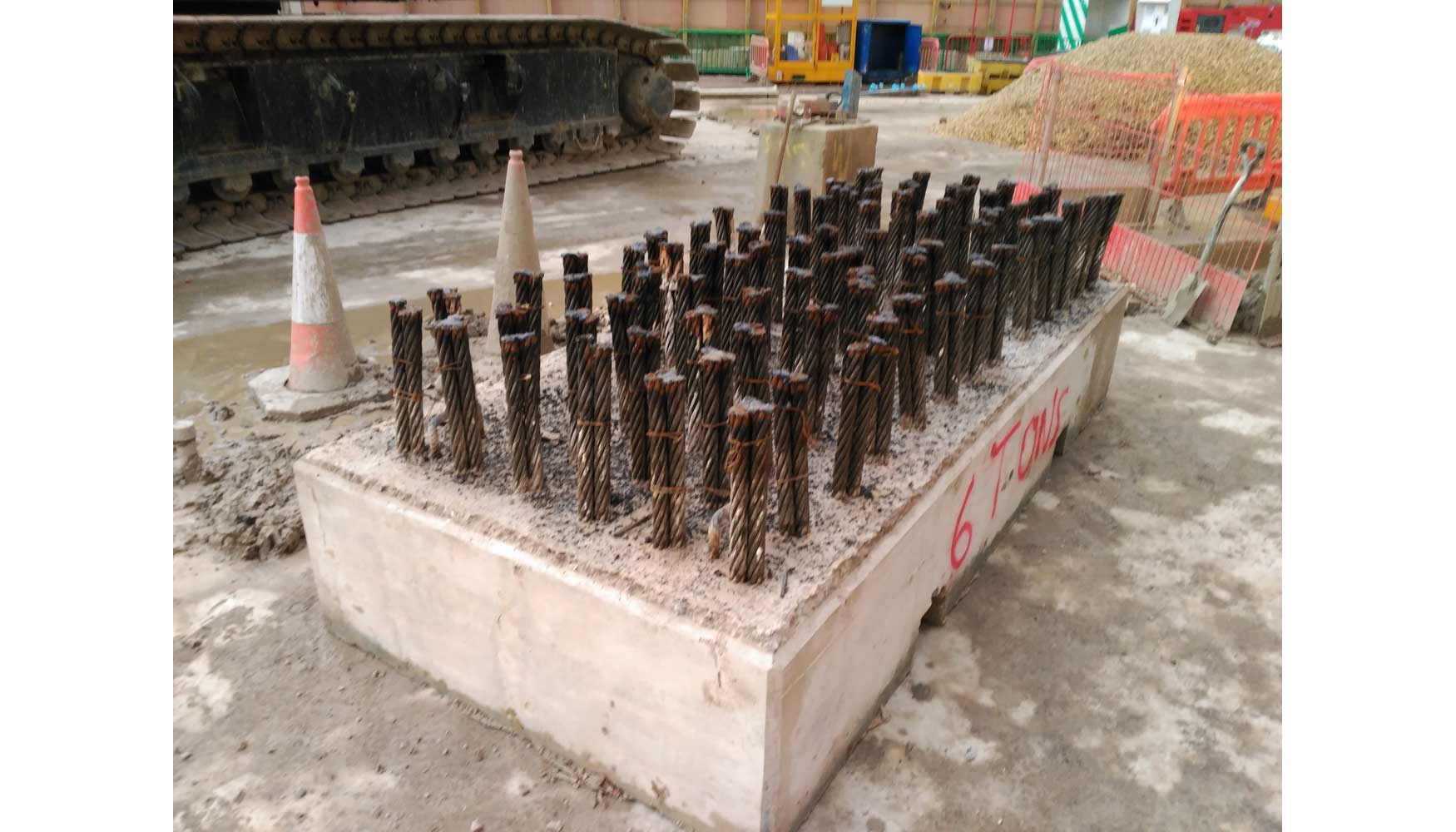
El informe geotécnico del proyecto identificaba un estrato de muy alta resistencia en el contacto Thanet Sand y Chalk (Figura 7). Se trataba de las denominada Bullhead Bed, consistente en bloques de sílex de dimensiones en torno a 15-20 cm cementados, que se encontraban formando capas de 50 cm de espesor, con resistencias a compresión simple (RCS) de 200 MPa para la capa en su conjunto y piedras de sílex con RCS de 800 MPa. Para hacer frente a este problema, decidimos desplazar una cuchara de excavación de pantallas y un trepano de 12 ton de peso. De esta manera evitaríamos los bajos rendimientos de intentar avanzar en esta capa con la hidrofresa, así como los posibles bloqueos tanto de las ruedas de corte como de la bomba de succión de la hidrofresa, por los bolos de sílex.
Tras esta fase de análisis previo, en mayo de 2016 Geocisa comenzó a colaborar con el contratista principal del Sector Central (FLO Joint Venture) en el diseño propio de los trabajos de cimentación. Esta colaboración se centró principalmente en el desarrollo de cuatro diseños:
- a) Diseño del muro guía y pilotes de apoyo del mismo.
- b) Diseño de la mezcla de hormigón adecuada para la ejecución de los trabajos.
- c) Diseño de la armadura no estructural de las pantallas.
- d) Diseño de las plataformas de trabajo por donde iban a moverse tanto la hidrofresa como las grúas de cimentación.
Tras un primer análisis del terreno y tras hacer un estudio de la estabilidad de la excavación basado en la normativa alemana DIN-4126, se concluyó que los terrenos inmediatamente por debajo de la plataforma existente, no tenían capacidad portante para soportar con seguridad las cargas que transmitirían los equipos de cimentaciones. También se desprendía del estudio de estabilidad, que podría existir una posibilidad de inestabilidad del terreno en los primeros metros de la excavación de la pantalla. Para abordar ambos problemas se decidió diseñar un muro guía que apoyara sobre unos pilotes que tendrían dos funciones, por un lado transmitir las cargas superficiales a un terreno más profundo con mejores capacidades portantes y por otro lado generar una pantalla discontinua a ambos lados de la misma, que minimizara el riego de colapso del terreno durante la excavación de las pantallas.
El proceso de diseño de la mezcla de hormigón comenzó con la publicación, por parte de la propiedad (Tideway), de las especificaciones del hormigón para pantallas. Estas especificaciones eran altamente exigentes e introducían un nuevo reto: la prohibición del uso de áridos marinos. Desde las primeras conversaciones con los suministradores de hormigón nos dejaron claro que no era factible conseguir suministros de áridos de procedencia no marina, así que comenzamos una estrecha colaboración con FLO JV para conseguir la aprobación del uso de áridos de procedencia marina en el proyecto. Debido a los requisitos de durabilidad (120 años), tuvimos que plantear un control exhaustivo del contenido de cloruros en los áridos y así conseguir que se aceptara el uso de áridos marinos en el proyecto. Otro de los requisitos incluidos en las especificaciones del hormigón para pantallas, era el uso de hormigones de alta resistencia, en concreto se trataba de un hormigón C40/50, es decir un hormigón que en probetas cilíndricas alcanzara una resistencia de 40Mpa a 28 días. Este requisito suponía un nuevo reto para el diseño de la mezcla de hormigón ya que si bien se debían asegurar las resistencias de proyecto, por otro lado había que conseguir un hormigón con baja ganancia de resistencia iniciales, que facilitara la ejecución de los paneles secundarios, ya que estos debían fresar parte de los paneles primarios adyacentes. Se decidió emplear un cemento tipo CEM-IIIB+SR con un 70% de escorias de alto horno, lo que implicaba tener una ganancia de resistencias iniciales algo menores que con un cemento tipo CEM I, y por otro lado se consiguió relajar las especificaciones iniciales, permitiéndose que la resistencia de 40Mpa, se pudiera alcanzar a los 56 días en lugar de a los 28 días.
El volumen de hormigón a verter en cada pantalla era de aproximadamente 285 m3. Lógicamente el hormigonado se tenía que realizar de forma continua y sin interrupciones. El compromiso de suministro de los distintos suministradores no excedía de 30 m3 a la hora, lo que suponía que el hormigonado de una pantalla nos llevaría del orden de 9 horas. El sistema de hormigonado de una pantalla se realiza por la técnica de hormigón sumergido, esto supone que la tubería de hormigonado (tubería tremie) baje hasta el fondo de la excavación y el hormigonado se realice del fondo de la pantalla hacia la superficie de la misma. Esto implica disponer de una mezcla con la fluidez adecuada para recubrir perfectamente las armaduras y desplazar la bentonita del panel, así como que tenga la capacidad de mantener esta fluidez durante el proceso de hormigonado.
Por otro lado la técnica de ejecución de pantallas con hidrofresa no requiere de la colocación de juntas entre los paneles de pantalla, ya que se ejecuta mediante la técnica de primarios-secundarios donde los paneles secundarios fresan el hormigón de los paneles primarios adyacentes, generando así la junta constructiva entre paneles. Este sistema de ejecución requiere que al tener que fresar parte de los paneles primarios con la hidrofresa, la ganancia de resistencia de estos paneles no sea muy rápida y así permitir la ejecución de los paneles secundarios, cuando todavía los paneles primarios no han desarrollado toda su resistencia. Una vez fijados los objetivos a alcanzar, comenzamos una estrecha colaboración con los suministradores de hormigón para desarrollar una mezcla que, por un lado cumpliera con las características técnicas y de durabilidad que imponía las especificaciones, pero por otro lado tuviera las características de fluidez y homogeneidad, para que resultara idónea para el hormigonado a través de tubería tremie. Esto implicó realizar diferentes ensayos de laboratorio con cada una de las distintas plantas suministradoras, que tras dar el resultado adecuado, se confirmaban realizando ensayos con amasadas realizadas en la propia planta y con la misma amasadora que suministraría a la obra. Se prestó principal atención a dos ensayos que nos aseguraran la docilidad de la mezcla con el paso del tiempo y la capacidad de la mezcla para atravesar la armadura de la pantalla. Estos fueron el Slump Flow Test (ensayo del escurrimiento UNE-EN-12350-8), que empleamos para medir la consistencia y fluidez del hormigón y el L-Box Test (método de la caja en L. UNE-EN-12350-10) que empleamos para evaluar la trabajabilidad del hormigón y su capacidad de penetración (ver figuras 11 y 12).
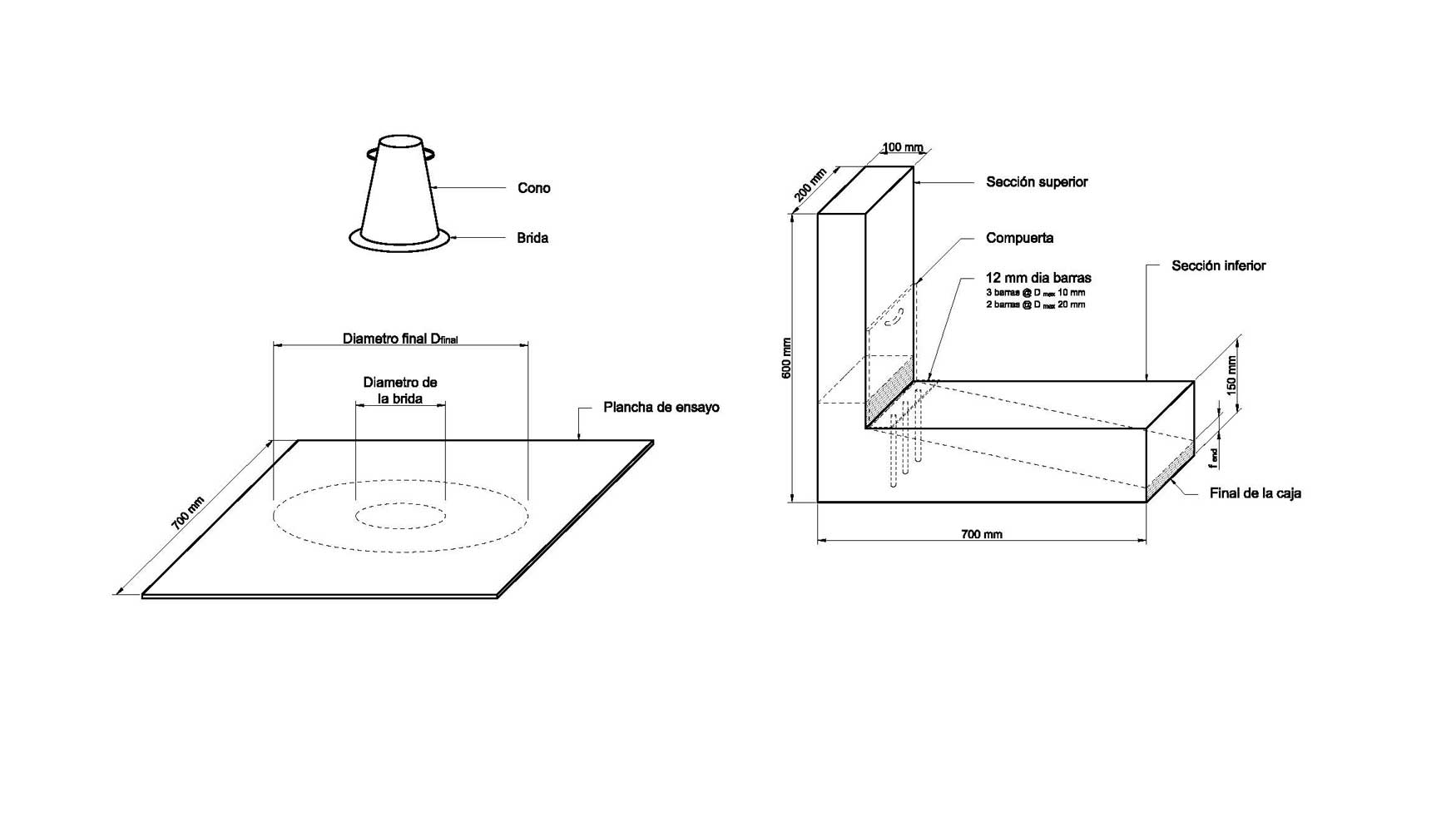
Figuras 11 y 12: Slump Flow y Test L-Box Test.
Geocisa UK fue la encargada de diseñar el armado no estructural de las pantallas. Este diseño consistió principalmente en:
- definir la armadura de rigidización de la pantalla, que permite que la armadura se pueda izar y pasar de la posición horizontal en el acopio de obra, a la vertical para instalarla dentro de la pantalla,
- definir y dimensionar los puntos de amarre de la armadura para su izado,
- definir el sistema para unir cada una de las diferentes secciones en que se dividía la armadura y
- definir el sistema de protección de los conectores embebidos dentro de la armadura.
Desde el primer momento, tanto por los requisitos de prevención así como por los de calidad, decidimos que las jaulas de armadura de pantalla se montarían fuera de las instalaciones de obra y una vez ejecutadas se trasladarían a obra, según se necesitaran. A pesar de tratarse de pantallas de 86,4 m de profundidad, solo estaban armados los primeros 63 metros, siendo los últimos metros de la pantalla de hormigón en masa. Para poder realizar el transporte de las armaduras por carretera se limitó la dimensión máxima de cada tramo de armadura a 18 m, lo que supuso que cada armadura quedara dividida en tres tramos de 18 m y un tramo de unos 14 m, que se iban uniendo en obra, una vez que se introducían en la excavación. Para asegurar la perfecta conexión entre tramos, las jaulas de armadura fueron diseñadas en 3D y montadas en factoría, siguiendo fielmente el diseño. En la factoría se realizaba el montaje de los 63 metros de una sola vez, para así asegurar que los diferentes tramos se enfrentaban perfectamente a su compañero. Posteriormente se desensamblaban los tramos para dejar la armadura lista para el transporte. El sistema que adoptamos para la unión de cada uno de los tramo de armadura fue el conocido como 'Fish-plate' (ver figura 13). Este sistema permite la conexión de las armaduras mediante cuatro tornillos por cada empalme, evitando la introducción de las manos de los operarios dentro de la armadura, lo que reduce los riesgos de atrapamientos. La pantalla llevaba embebida varios conectores de alta resistencia (tipo Macalloy 1030) de 50 mm de diámetro, para realizar la conexión de la pantalla con la losa de fondo. La protección de estas barras frente a la lechada del hormigón se realizó mediante el sistema conocido como 'Box-out'. Consistía en unas cajas de madera, hechas a medida, que protegían la cabeza de los conectores y rellenas de espuma, para evitar la entrada de lechada de hormigón. Una vez se comienza la excavación dentro de las pantallas, cuando se alcanza la cota donde se colocaron las box-out, se procede a retirar la tapa de la caja y descubrir los conectores (ver figura 14).
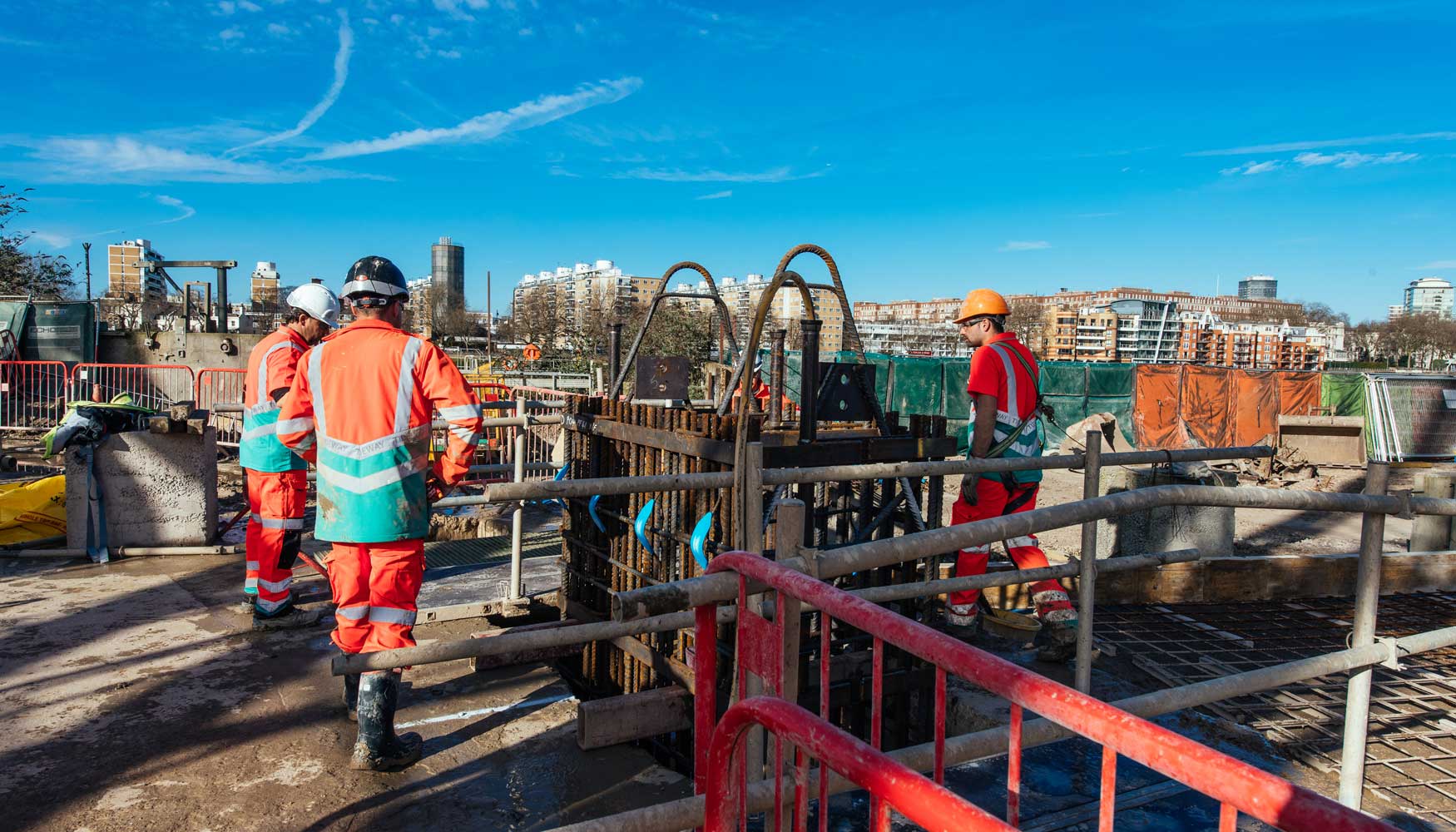
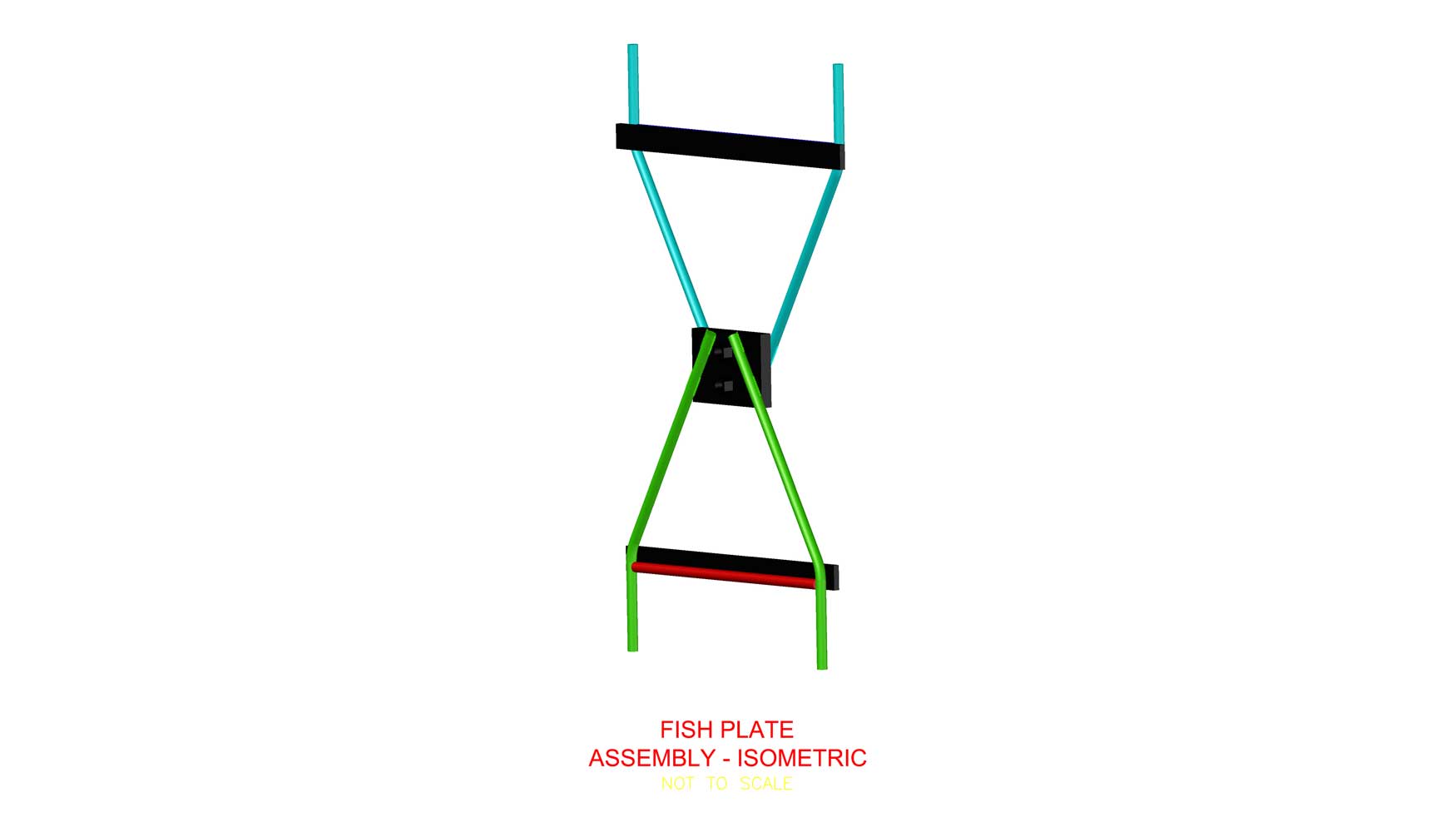
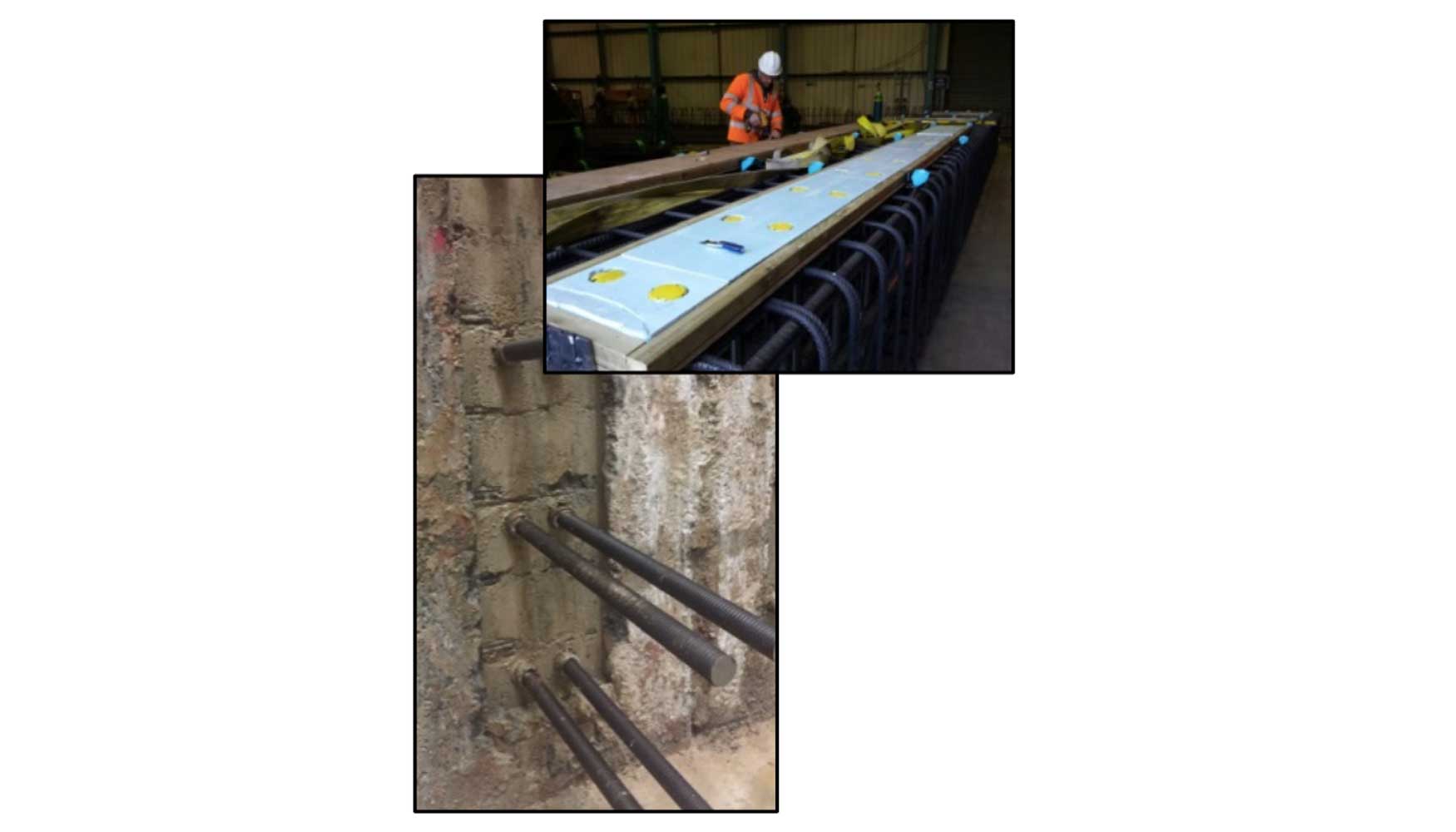
Por último, Geocisa, partiendo de las cargas de las grúas y equipos destinados a realizar los trabajos y considerando las cargas a elevar y las más desfavorables situaciones, diseñó las plataformas de trabajo por donde se moverían los equipos de maquinaría durante la ejecución de los trabajos.
Trabajos ejecutados
Tras esta primera fase de diseño, Geocisa UK comenzó los trabajos de pilotaje en julio de 2016. Estos trabajos consistieron en la ejecución de 343 pilotes de 350 mm de diámetro y 12 metros de profundidad para el apoyo del muro guía y evitar posibles colapsos de los primeros metros de la excavación.
Los pilotes se ejecutaron con mortero de baja resistencia que permitiera la posterior excavación de las pantallas sin dificultad. Una vez amorterado el pilote se introducía una barra corruga de 32 mm de diámetro, que serviría de conexión con el muro gruía. Los pilotes se ejecutaron mediante la técnica de hélice continua. El equipo de perforación elegido para su ejecución, fue una pilotera Bauer RG-19-T. Una vez terminados los pilotes se procedió a la ejecución del muro guía. Las principales funciones del muro guía son asegurar el correcto posicionamiento de la hidrofresa, asegurar la verticalidad de los primeros metros de la excavación, ayudar a la estabilidad de los primeros metros de la excavación y permitir el cuelgue de las armaduras dentro de la pantalla sin que apoyen en el fondo de la excavación (ver figura 15).
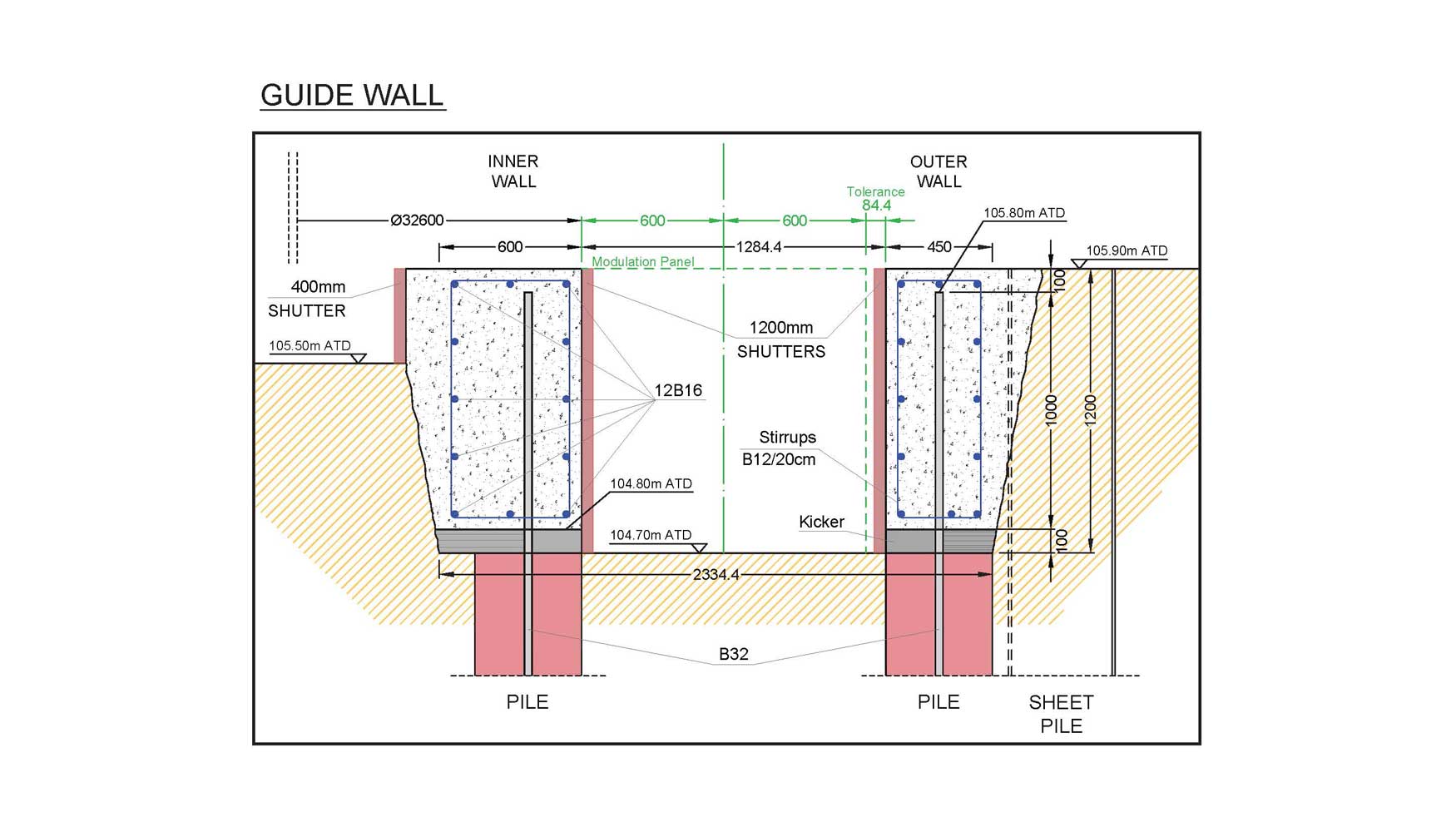
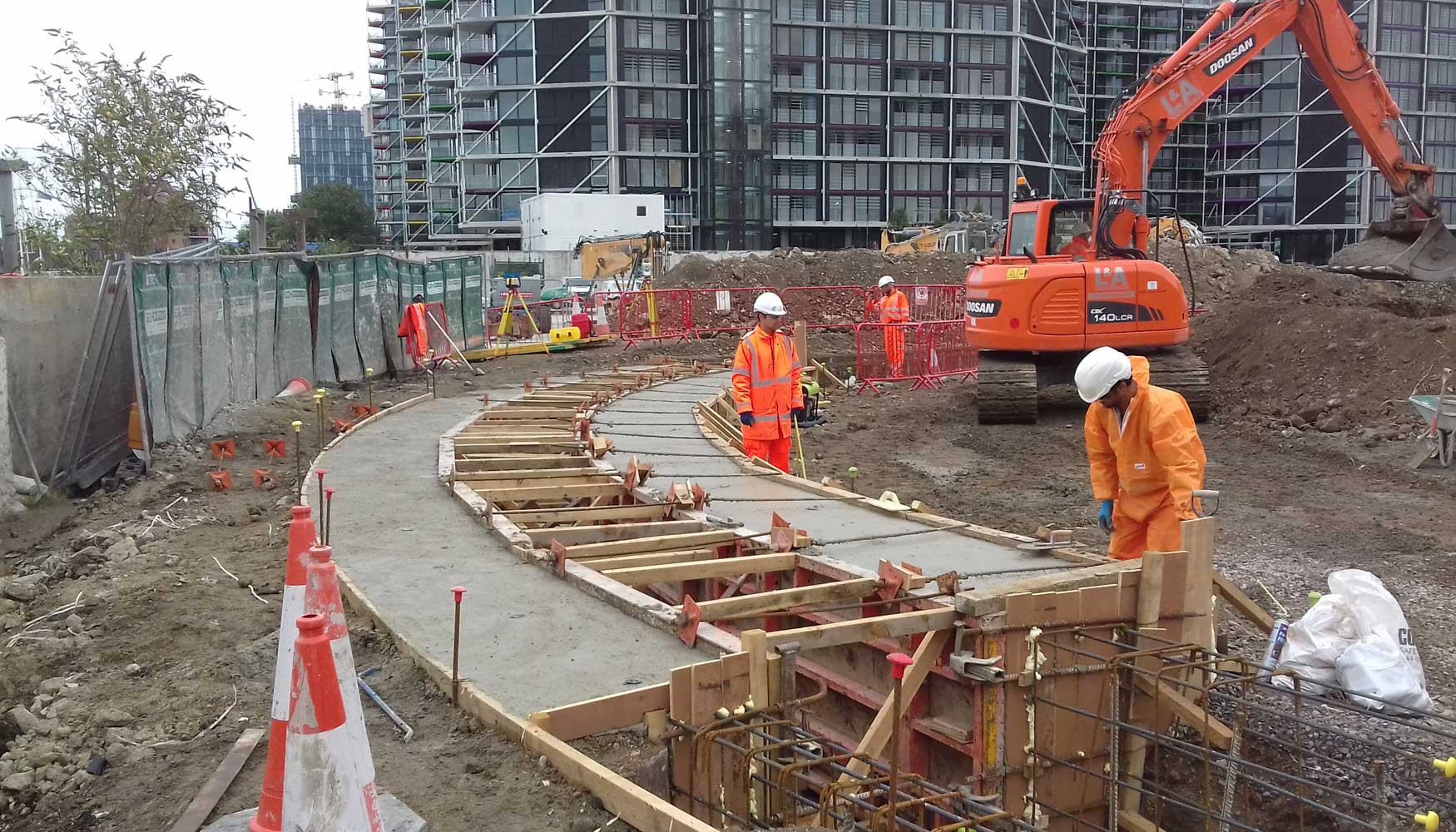
A la hora de planificar y organizar las necesidades de maquinaria que tendríamos en el proyecto, la planta de tratamiento de lodos fue una de nuestras prioridades. El dimensionar correctamente la planta de tratamiento de lodos y acertar con el sistema más adecuado para realizar el tratamiento de lodos sobrantes, consideramos que fue vital para el éxito de proyecto. Las principales características de la planta de lodos fueron las siguientes (ver figura 16):
- Dos silos de 40 Tm de capacidad cada uno para almacenaje de bentonita en polvo,
- Planta de fabricación continua de lodo bentonítico con capacidad de fabricar 60 m3 a la hora,
- 1.575 m3 de capacidad de almacenaje de bentonita, dividida en 3 depósitos de 525 m3 con bentonita fresca, de trabajo y para desechar.
- Central de desarenado con capacidad de tratamiento de 500 m3 hora.
- Bombas para el trasiego de lodos con caudales máximos de 450 m3 hora.
- Planta de tratamiento del lodo bentonítico de desecho compuesta por:
- Agitador de 20 m3 de capacidad.
- Filtro prensa con capacidad de tratamiento de unos 170 m3 día.
- Planta de tratamiento de pH, con capacidad de tratamiento de 120 m3 día.
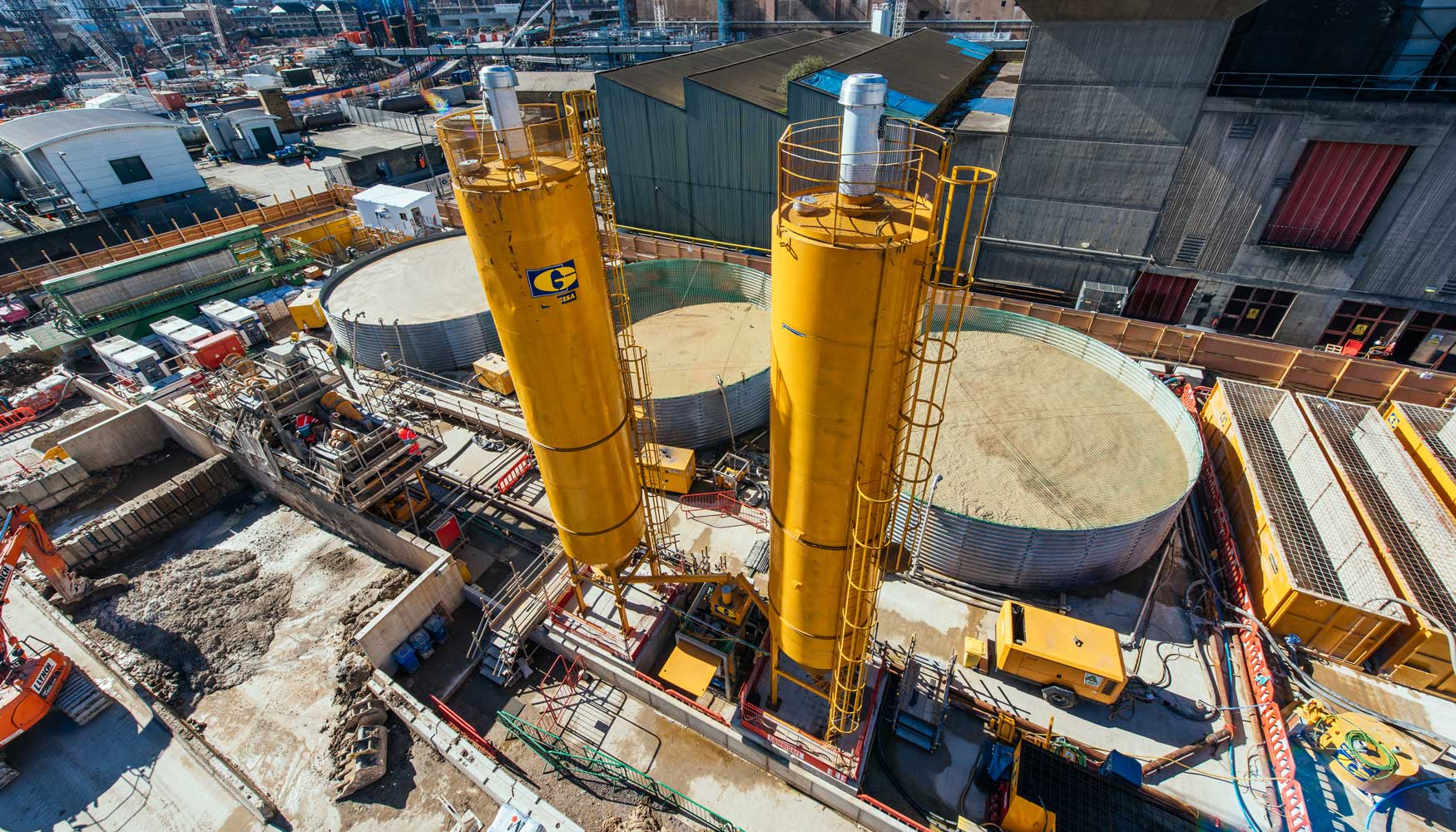
Excavación
La ejecución de pantallas con hidrofresa consiste en una técnica de perforación en la que la hidrofresa excava en el terreno mediante un sistema de circulación inversa, donde el terreno excavado se mezcla con el lodo de perforación, para ser bombeado fuera de la zanja y posteriormente ser tratado en la planta de desarenado.
El pozo de Kirtling contaba con 42 paneles de 1,2 m de espesor, 2,8 m de longitud y 86,4 m de profundidad. El sistema de ejecución de paneles con hidrofresa, se basa en paneles primarios y secundarios. Consiste en la ejecución de los paneles primarios para más tarde realizar los paneles secundarios, ubicados entre medias de dos paneles primarios y fresando parte de los paneles primarios adyacentes, para generar la junta constructiva entre ellos (ver figura 17). En total se ejecutaron 21 paneles primarios y otros 21 paneles secundarios.
Como comentábamos anteriormente, la hidrofresa excava moliendo el terreno y mezclándolo con el lodo de perforación, para bombearlo fuera de la zanja, mediante la bomba de succión con la que está equipada (ver figura 18). Dicha bomba se encuentra ubicada sobre las ruedas de corte a unos 3 m por encima del terreno. Esto implica que para perforar con la hidrofresa lo primero que se debe realizar es una pre-excavación de al menos tres metros de profundidad, rellenarla con lodo de perforación y así poder sumergir la hidrofresa y cebar la bomba de succión. Para optimizar la ejecución se introdujo un equipo de excavación de pantallas por accionamiento hidráulico que iba realizando esta pre-excavación en los paneles primarios, previamente al comienzo de la excavación con la hidrofresa. Decidimos sacarle más partido a este equipo, excavando los primeros 40 metros del panel, para que más tarde continuara la excavación la hidrofresa, hasta la profundidad definitiva. Este sistema de 'trabajo mixto' permitió que la hidrofresa excavara lo menos posible en la London Clay y así minimizar los problemas asociados a este terreno.
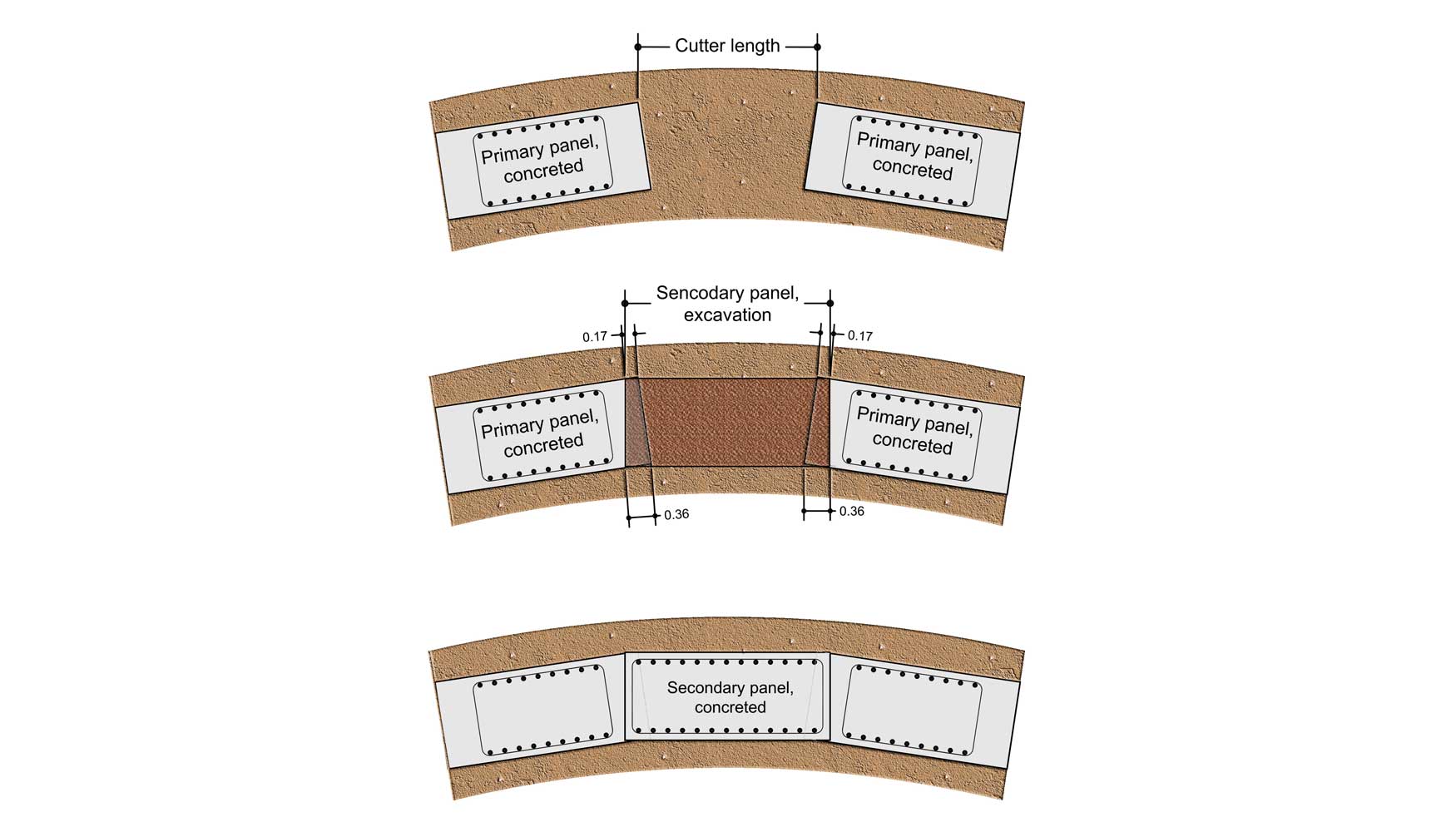
Uno de los retos que debían afrontar los equipos de excavación, era asegurar que los paneles serían excavados con una desviación inferior a 1/400, tal y como exigía el Pliego del Proyecto. La experiencia de Geocisa ejecutando pantallas con hidrofresa, era que con un sistema de control exhaustivo y disponiendo de control y corrección de la excavación en tiempo real, se podría alcanzar esta exigencia de verticalidad. La BC-35 disponía de un inclinómetro y un giróscopo incorporado en la hidrofresa que transmite a tiempo real información de la posición de la hidrofresa a la cabina del operador en cada momento de la excavación. Igualmente dispone de un sistema de corrección de la verticalidad formado por 12 'flaps' o empujadores en el cuerpo de la hidrofresa (ver figura 18) que actúan apoyándose contra el terreno, para corregir las desviaciones que se produzcan durante la excavación. El software de perforación del que dispone la hidrofresa (ver figura 19), permite que esta corrección se pueda hacer de manera automática o en modo manual. Aparte del propio sistema de control de la hidrofresa, decidimos realizar un ensayo de comprobación al final de la excavación, para confirmar que las pantallas se habían excavado dentro de las tolerancias admisibles. Se trataba de un ensayo mediante sonar, que proporciona el perfil de la excavación pudiendo determinar las sobre-excavaciones así como los desvíos si se producen, aunque no permite cuantificar con precisión dichos desvíos.
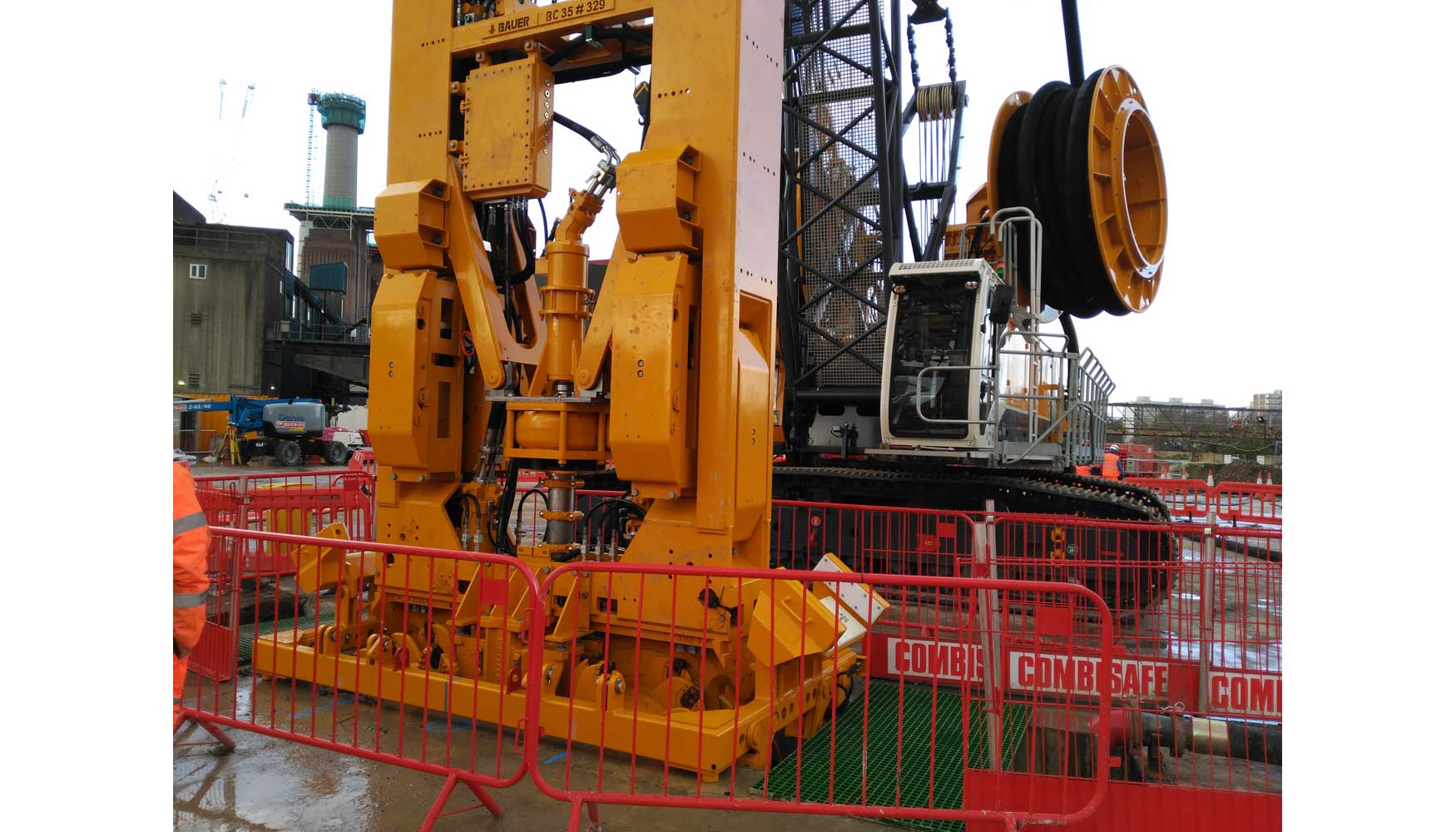
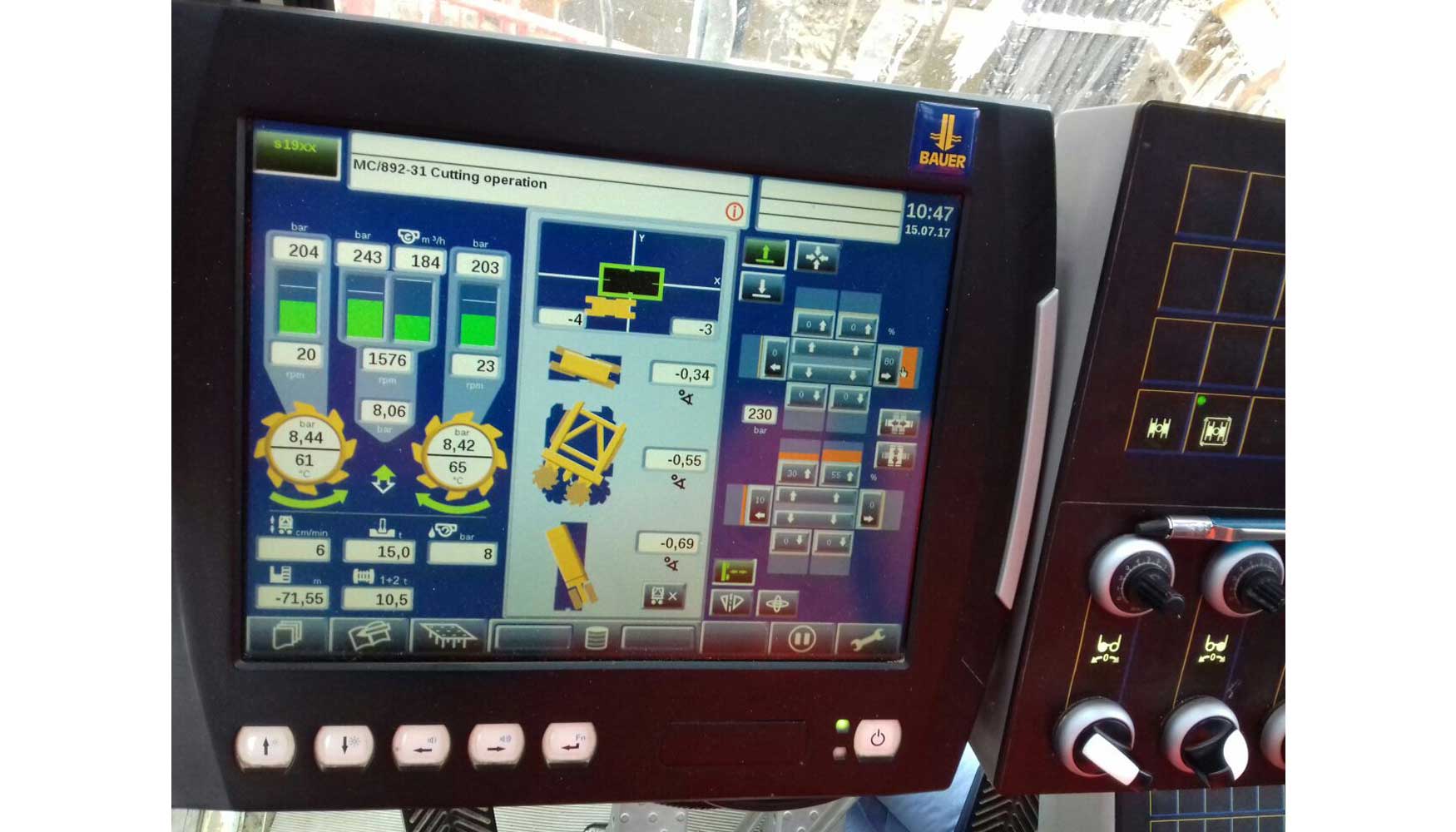
Desarenado y montaje de armaduras
A diferencia de una pantalla convencional, donde durante el proceso de excavación se retira el terreno en la zanja con la cuchara bivalva, en las pantallas ejecutadas mediante hidrofresa, el terreno se va mezclando con el lodo de perforación al ser fresado, implicando un mayor deterioro del lodo de perforación, al incorporarse al mismo todas las partículas de menor tamaño (menores de 60 µm) que no son capaces de separar los desarenadores. Una vez se finalizaba la excavación se procedía a la sustitución del lodo de perforación por un lodo fresco. De esta manera se eliminaba una bentonita que tras el proceso de excavación había incorporado gran cantidad de partículas finas en su mezcla, alcanzando una densidad en torno a 1,20 gr/cm3, por bentonita fresca con densidad aproximada de 1,02 gr/cm3. Este proceso de sustitución del lodo usado durante la excavación por lodo fresco, resulta de vital importancia para asegurar la calidad en el proceso de hormigonado.
Tras asegurar que el lodo de excavación cumplía con las características adecuadas para hormigonar el panel, se procedía a la colocación de las armaduras dentro del panel. Dependiendo del tipo de panel (primario o secundario) la armadura a instalar era de 1,8 m ó 2,6 metros de longitud respectivamente. Esto es debido a que, como se ha comentado anteriormente, el panel secundario fresa parte de los paneles primarios adyacentes para generar la junta constructiva entre paneles. Lógicamente esta zona destinada a ser fresada al ejecutar los paneles secundarios, no debe estar armada, por ello la dimensión de las armaduras de los primarios es menor que las de los secundarios. Al tratarse de excavaciones de 2,8 metros de longitud, cuando se coloca la armadura en un panel primario se debe centrar en el mismo y asegurar que durante el proceso de hormigonado esta armadura no se desplaza dentro de la zona de fresado de los paneles secundarios. Para asegurar esto se emplearon dos métodos; primeramente se utilizaron vigas separadoras, un perfil laminado (IPN-400) colocado a ambos lados de la armadura (ver figura 20) para evitar su desplazamiento durante el proceso de hormigonado. Este sistema, aun dando un buen resultado, requería cierto tiempo para el montaje de las vigas antes del hormigonado, así como su desmontaje durante el hormigonado. Más tarde se decidió diseñar un sistema de vigas de fibra de vidrio que se adosaría a ambos lados de la jaula de armadura del panel primario (ver figura 21), asegurando así su centrado dentro del panel y que, al ser fibra de vidrio, se podría fresar sin problemas por la hidrofresa. Estas vigas de fibra de vidrio se montaban antes de izar las armaduras resolviendo la demora que originaba el montaje y desmontaje de las vigas separadoras.
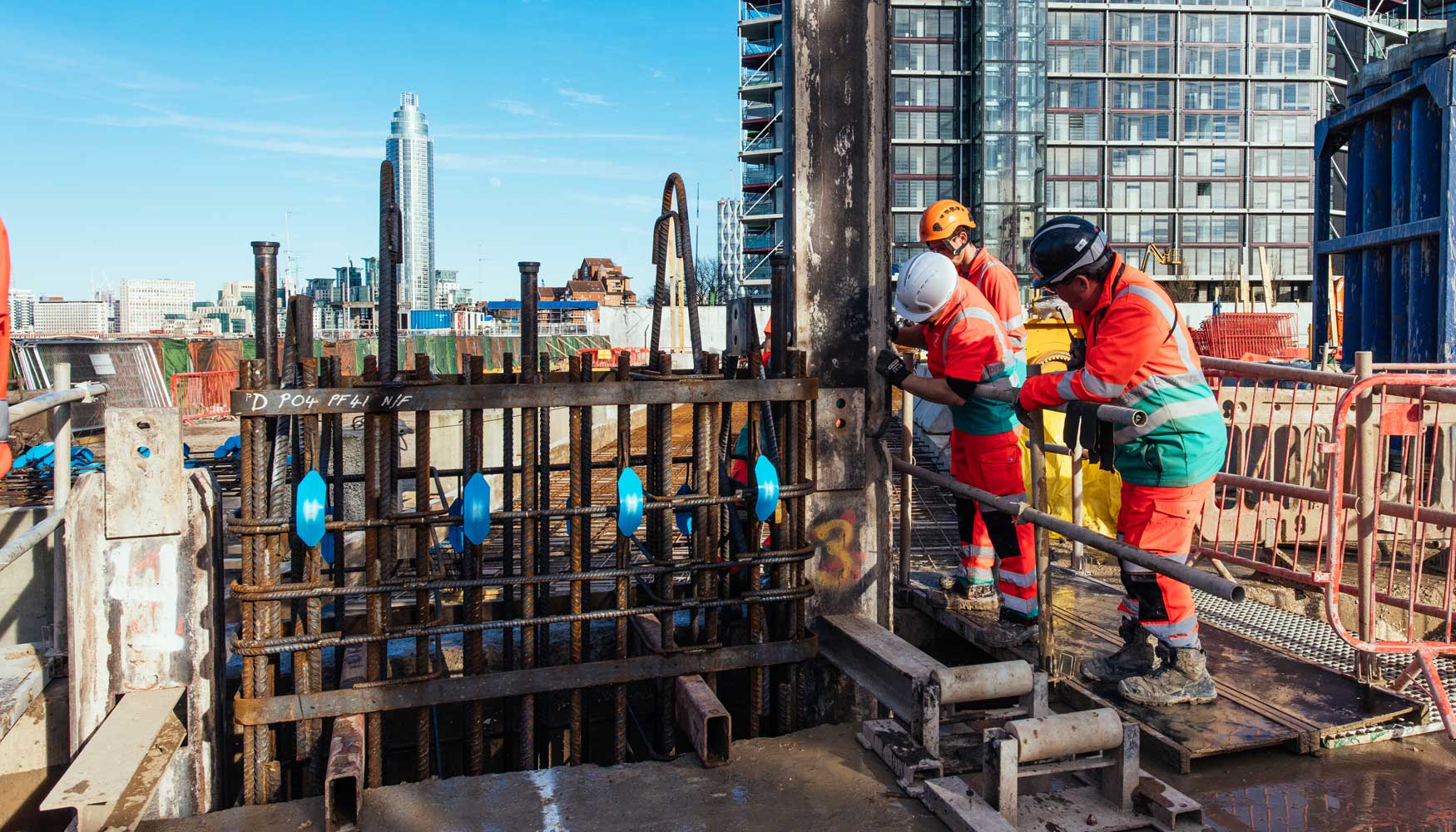
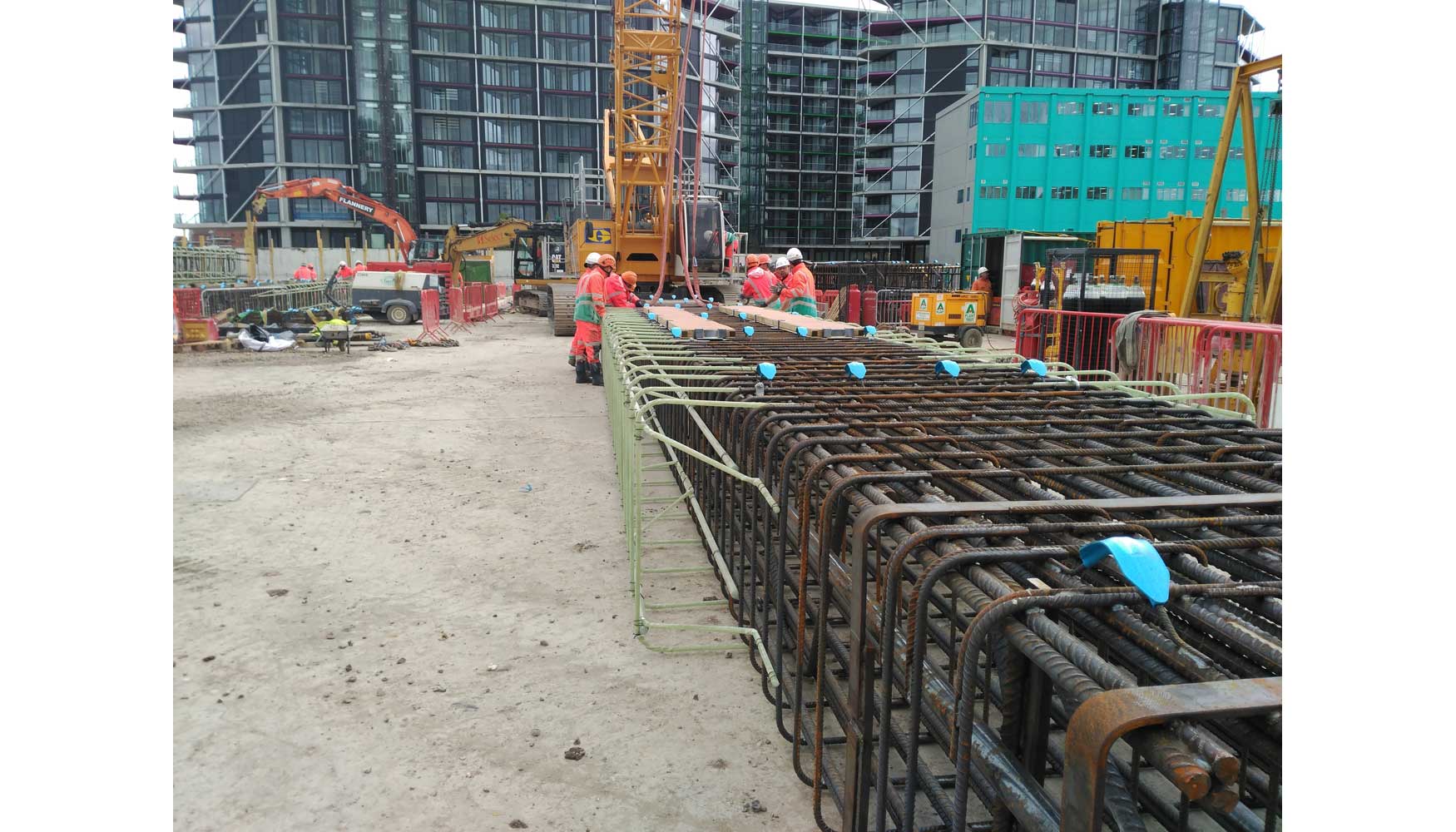
Las armaduras, por necesidades del transporte, venían fabricadas en cuatro tramos: tres de 18 metros de longitud y un tramo de 14 metros de longitud. El peso del tramo más pesado era de 12,8 toneladas y el peso de la armadura completa rondaba las 36 toneladas y 63 metros de longitud. La conexión de cada uno de estos tramos con el siguiente se realizaba mediante el sistema denominado 'Fish-plate' (ver figura 13). La gran ventaja de este sistema de unión radicaba en la sencillez y la seguridad que proporcionaba, evitando prácticamente que el operario tuviera que introducir las manos dentro de la armadura. El sistema consiste en colocar, en cada una de las armaduras a unir, dos platos de conexión (de acero) perforados para la colocación de dos tornillos de unión. Una vez se colocaba en posición vertical la armadura a unir, se enfrentaba a la armadura inferior, previamente colgada del muro guía y se unía con dos tornillos M-28 por plato de conexión. La unión de la tubería sónica de cada uno de los tramos, se diseñó optando por un sistema de 'roscas locas', que evitaba las habituales dificultades de conexión. La operación de izado de las armaduras se diseñó para ejecutarla inicialmente con una sola grúa de doble cabrestante (ver fig. 22). La falta de costumbre en el mercado británico de emplear este sistema, así como la incertidumbre que generaban algunos aspectos de Seguridad y Salud, hizo que se decidiera finalmente optar por el sistema más ampliamente extendido en el mercado británico, de realizar el izado mediante dos grúas, el denominado 'tandem lifting' (ver figura 23). El separador utilizado para asegurar el recubrimiento de la armadura fue del tipo 'Skid' (patín) que venía soldado de taller en la cara superior de la armadura y que se montaban en obra en la cara inferior de la misma (ver figura 24 y 25).
Hormigonado del panel
Cuando se tienen que realizar hormigonados de 9 horas continuadas vertiendo más 290 m3, en una obra situada en el centro urbano de una gran ciudad, una de las mayores preocupaciones es no tener ninguna interrupción durante el hormigonado. Para ello, desde el primer momento, consideramos importante realizar un análisis de los posibles riesgo a los que nos enfrentábamos y poner en marcha un plan de contingencia, acordado con nuestro suministrador, para afrontar cualquier imprevisto. La planta de hormigón para las pantallas, se encontraba ubicada a menos de 2,5 km de la obra, a pesar de ello y debido al denso tráfico del centro de Londres, algunas ocasiones requerían más de 30 minutos para completar el recorrido de la planta a la obra. Esto unido a la gran demanda de hormigón en la zona de Battersea Power Station, decidimos optar por aglutinar el mayor posible número de hormigonados en sábados. Un hormigonado de lunes a viernes, nos llevaba más de 9 horas, mientras que verter el mismo volumen de hormigón en sábado nos suponía entre 6 a 7 horas.
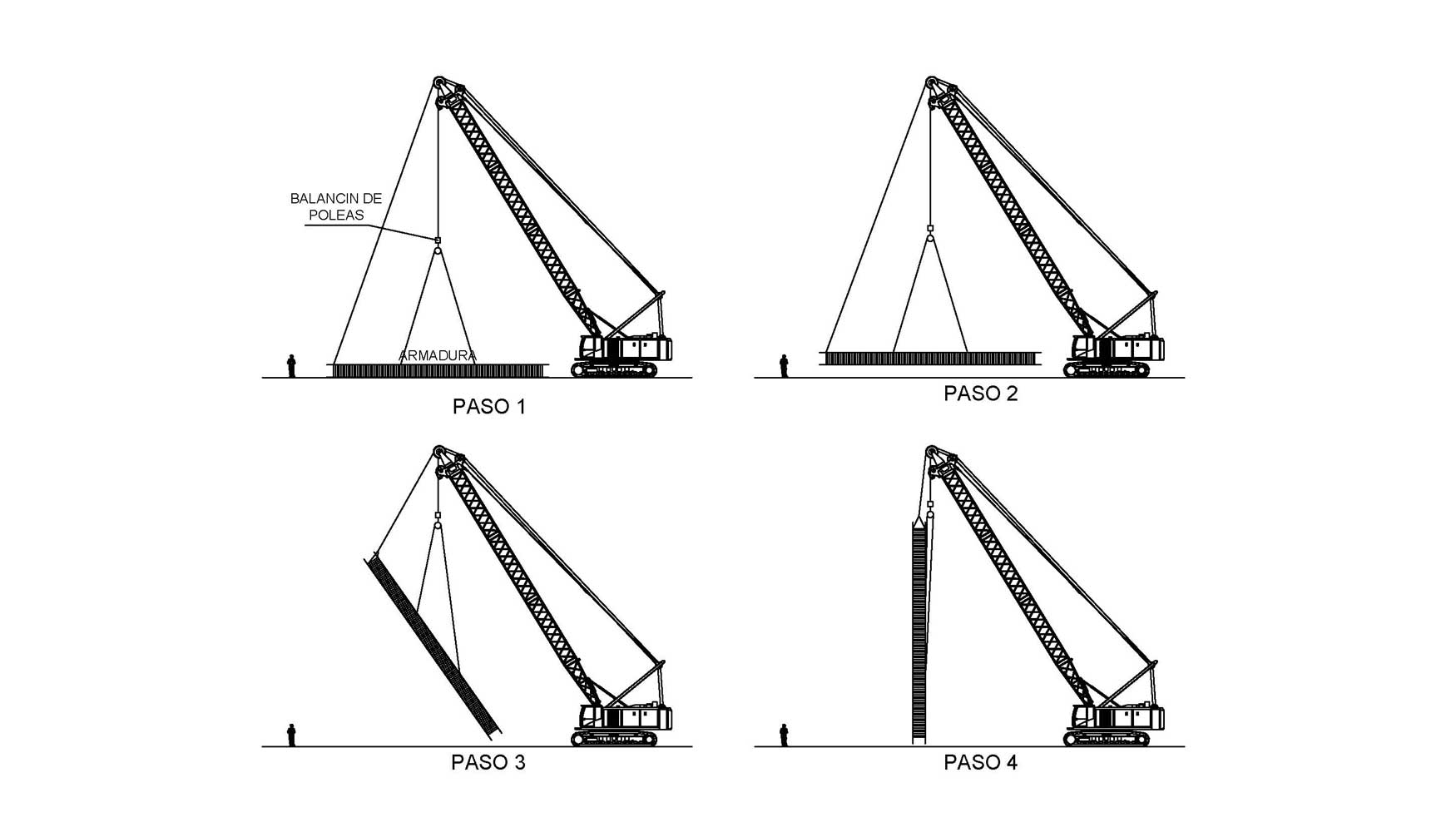
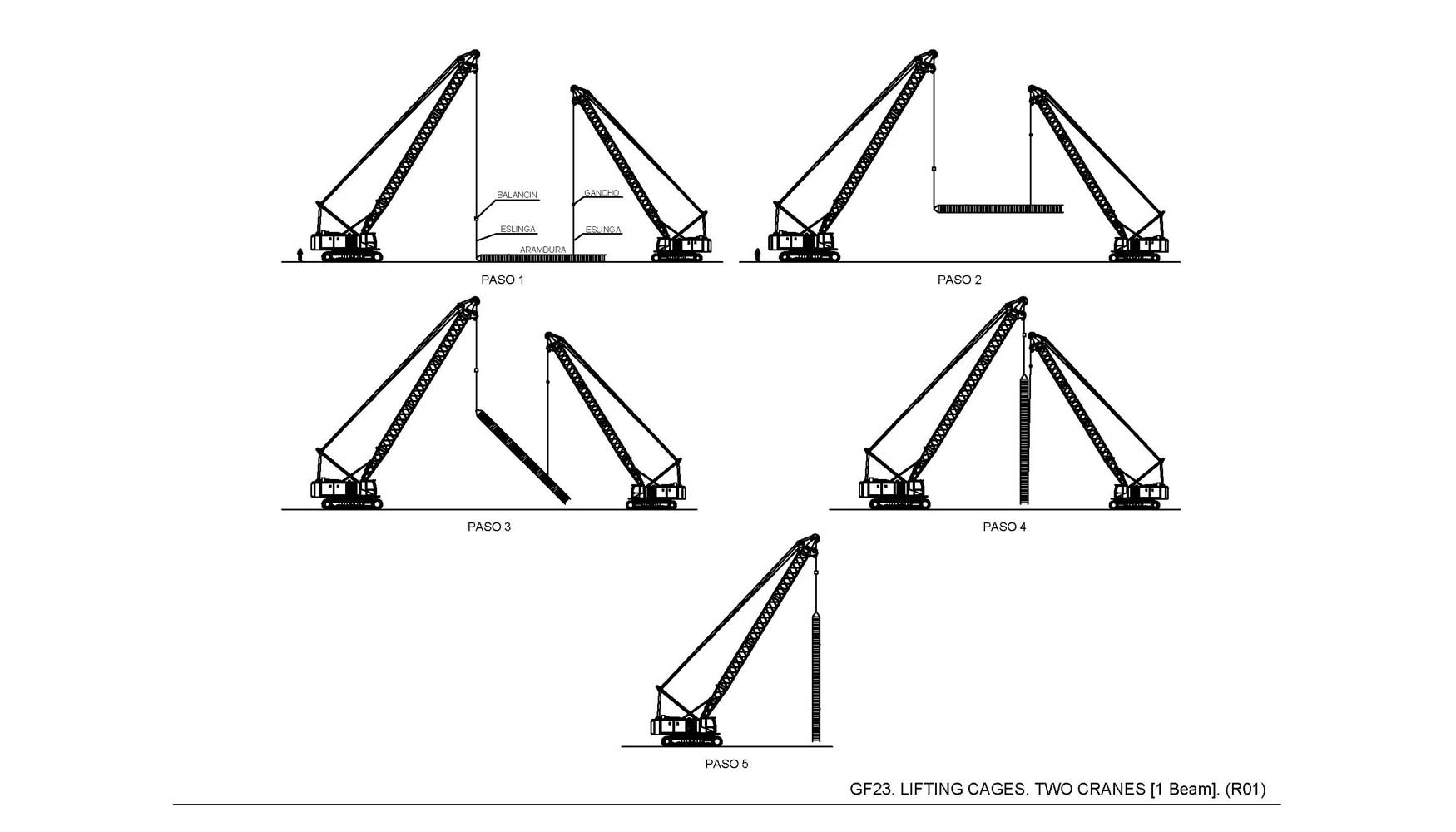
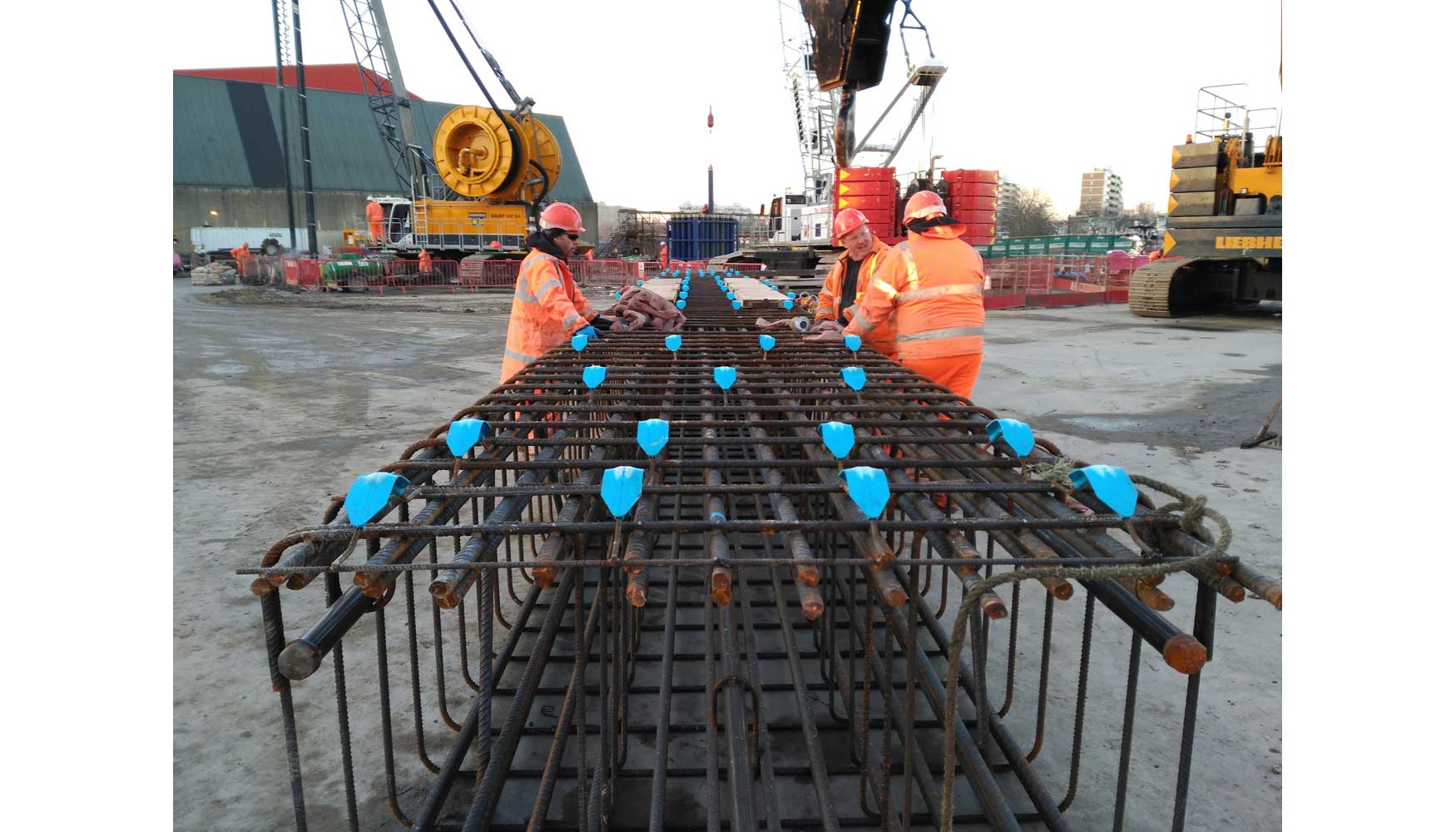
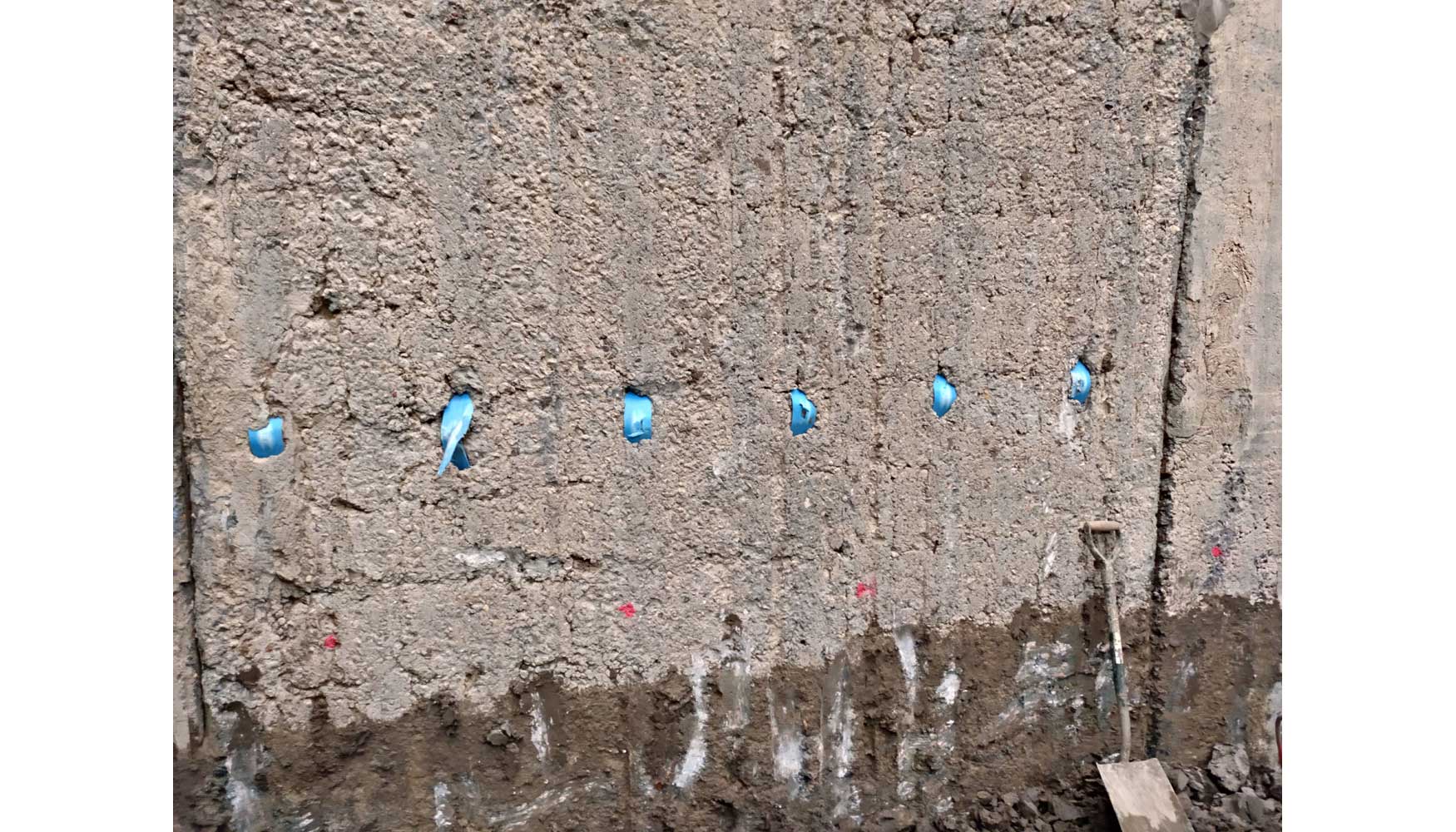
En la época de máxima producción se hormigonaron dos pantallas por semana y durante la ejecución de los últimos paneles secundarios se pasó a hormigonar una pantalla por semana. Los hormigonados se realizaban por la técnica de hormigón sumergido, a través de tubería tremie de 12 pulgadas de diámetro. Una de las actividades más delicadas durante el hormigonado de una pantalla es que el primer hormigón que se vierta, que va a emplazarse en el fondo de la excavación, envuelva de manera continua y rápida la tubería tremie para que el resto de hormigón vaya empujando este primeramente vertido. Para ello se acordó no comenzar el hormigonado de ninguna pantalla, hasta no tener tres cubas en obra, con sus ensayos previos realizados y superados. Para un más fácil manejo de la tubería tremie se diseñó, especialmente para esta obra, una jaula de tubería tremie que pudiera alojar los 86 metros de tubería (ver figura 26).
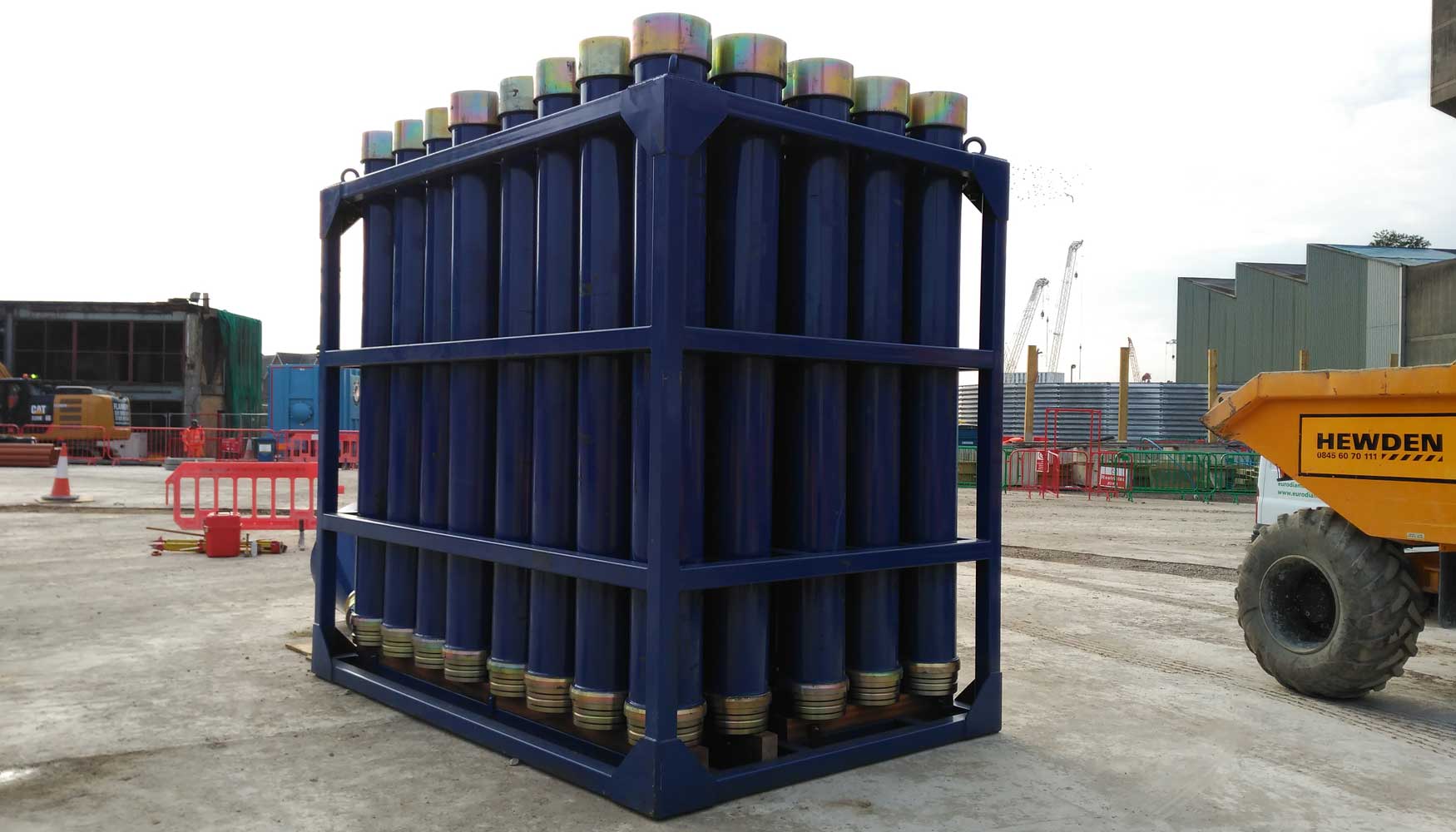
Desde los primeros hormigonados uno de nuestros objetivos era agilizar al máximo los tiempos empleados en realizar esta operación. Aproximadamente, por cada camión vertido se procedía a la retirada de un tramo de la tubería tremie. Esta operación implicaba del orden de 3,5 minutos por cada tramo retirado y requería detener el vertido de hormigón. Al final de una pantalla la suma de todos estos tiempos implicaba más de una hora y media de interrupciones en el hormigonado. Para evitar estas demoras, se diseñó una tolva de aluminio ligera (ver figuras 27 y 28), que pudiera manejar un operario a mano, para montar sobre la tubería tremie y continuar con el hormigonado de la pantalla, mientras se retiraba un tubo y se colocaba en su jaula. Para facilitar el trasiego del personal encargado del hormigonado alrededor de la pantalla, se diseñó una plataforma de hormigonado que permitía llevar a cabo las tareas de hormigonado sin riesgos.
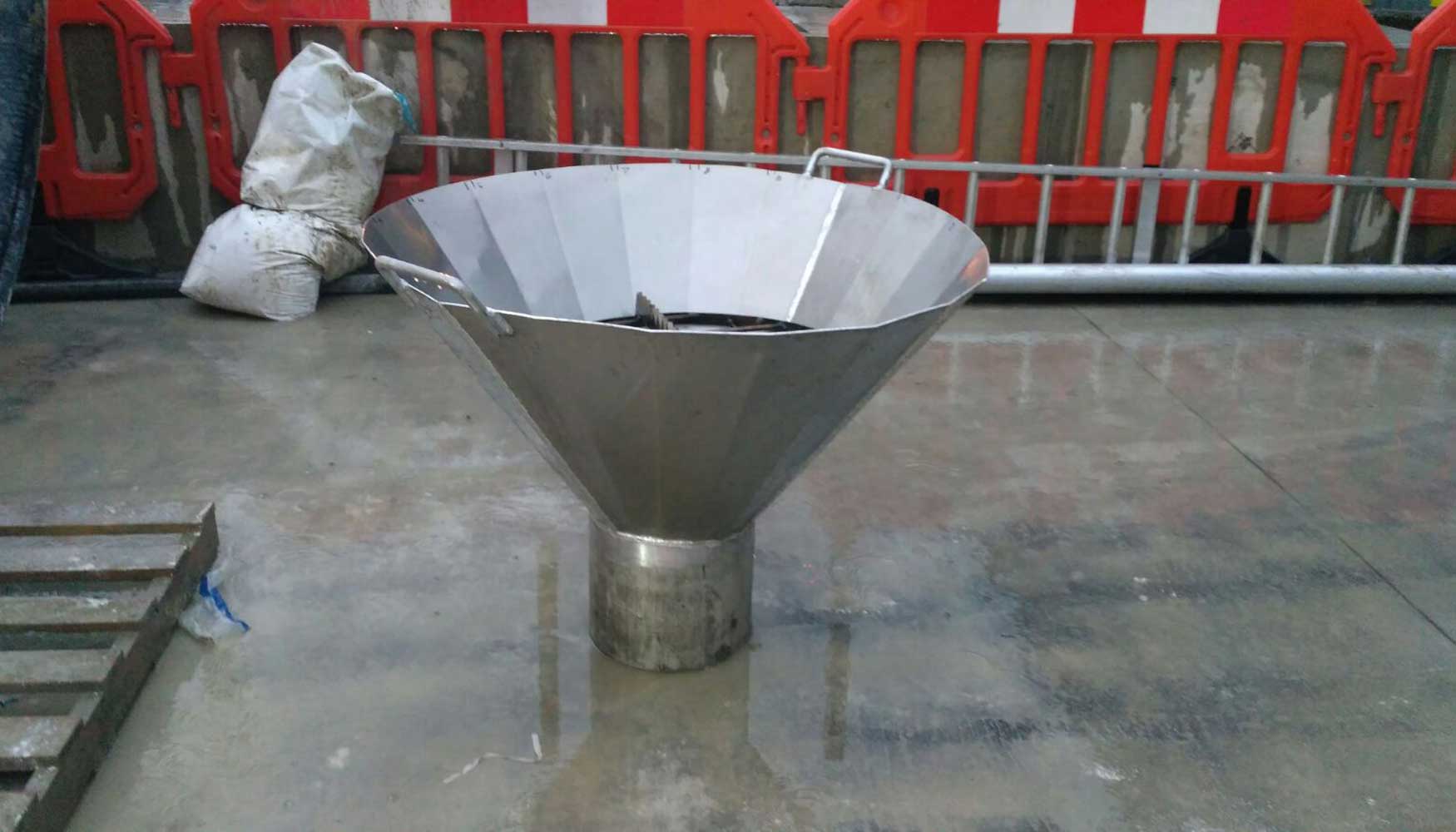
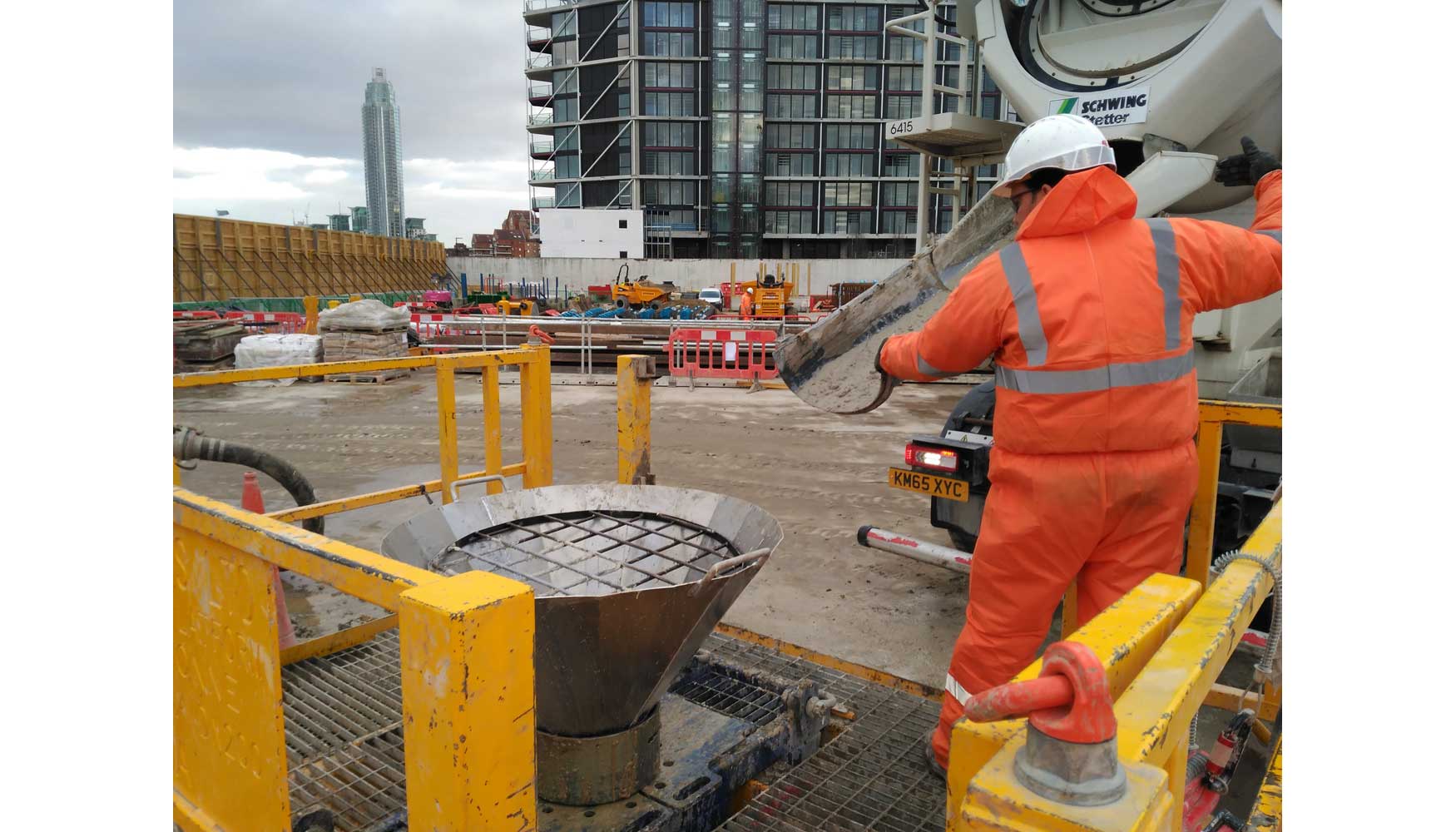
Seguimiento y control
Para la consecución del objetivo marcado, se ha desarrollado una labor de seguimiento y control exhaustivo por parte de Geocisa UK. Este control ha venido reflejado en cada uno de los siguientes apartados:
- Control de los lodos de perforación. El éxito en la ejecución de una pantalla con hidrofresa radica, en gran medida, en conseguir un lodo de perforación de altas prestaciones y mantener su capacidad con el paso del tiempo. Para ello decidimos instalar un laboratorio en obra (ver figura 29) desde donde se ensayarían los lodos durante la ejecución de los trabajos. Los parámetros a controlar que nos marcamos fueron los reflejados en la tabla 1. Al tratarse de un panel de gran profundidad, donde se atravesaban capas que podrían contener contaminantes, se decidió controlar los lodos durante la excavación de cada panel a diferentes profundidades, concretamente a 5 m, 10 m, 35 m, 60 m y al final de la excavación.
Lodo Fresco | Listo para reutilizar | Durante la excavación | Antes de hormigonar | |
Densidad (g/cm3) | 1,015 a 1,10 | Menos de 1,15 | Menos de 1,25 | Menos de 1,15 |
Viscosidad (sg) | 30 a 45 | 30 a 50 | 30 a 60 | 30 a 45 |
Filtro prensa (ml) | Menos de 30 | Menos de 50 | Menos de 60 | Menos de 60 |
pH | 7 a 9,5 | 7 a 11 | 7 a 11,5 | 7 a 11,5 |
Contenido arena (%) | N/A | N/A | N/A | Menor del 3% |
Tabla 1.
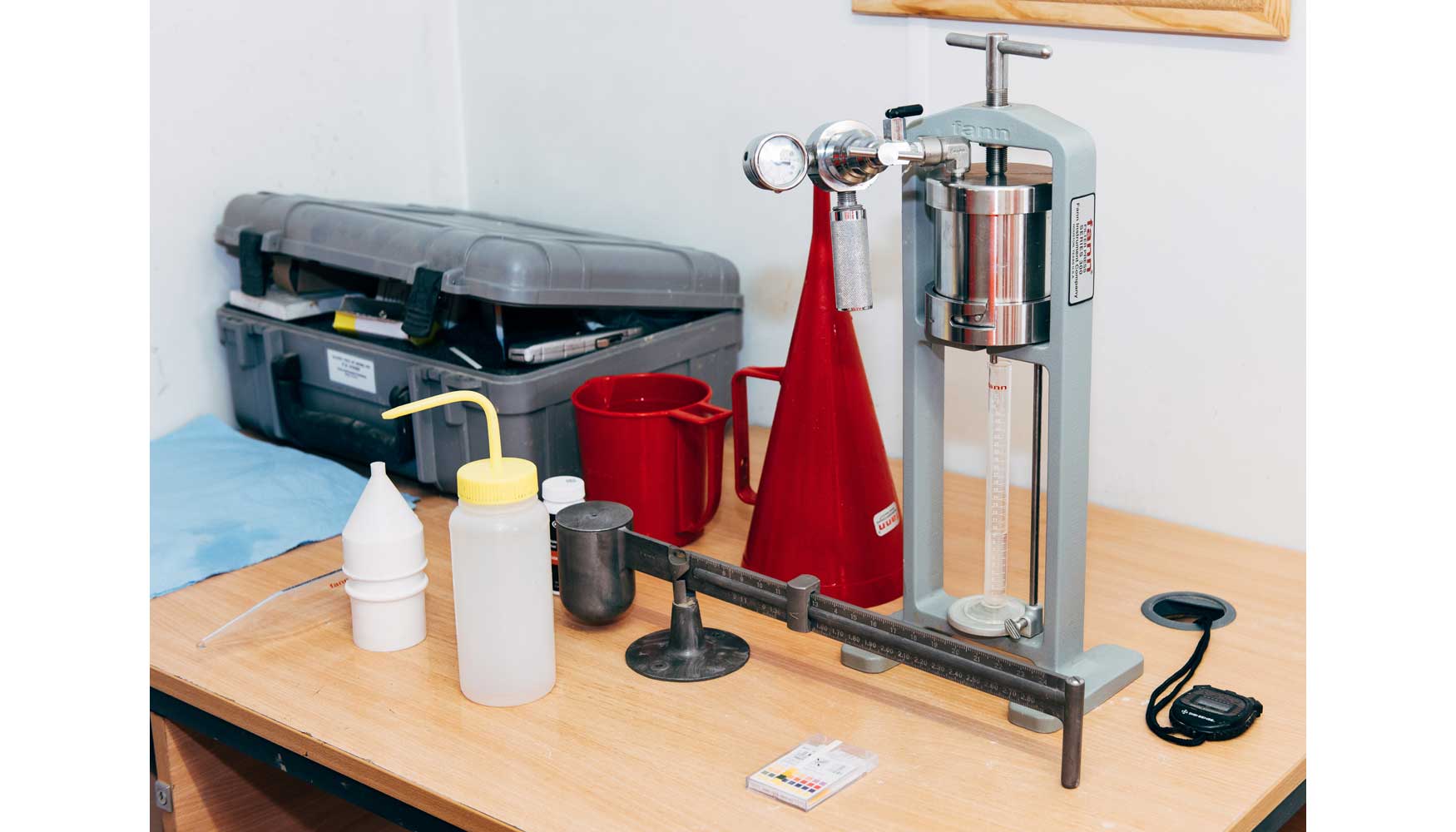
- Control de los parámetros de excavación de cada pantalla mediante registro continuo con el sistema B-Tronic instalado en la hidrofresa. Los parámetros registrados fueron: velocidad de excavación y empuje, además de cada una de las ruedas de corte y/o transmisiones: par de rotación, velocidad de rotación, presión hidráulica y temperatura de aceite. Toda esta información se almacenaba en la memoria interna del equipo pudiendo descargarse en tarjetas de memoria y analizarla con el software de gestión de la propia hidrofresa.
- Control de desviación de la excavación: Dada la profundidad de las pantallas y al alto requisito de verticalidad exigido (1/400), Geocisa UK decidió instalar un giróscopo complementario al equipo de inclinómetros que lleva instalados la hidrofresa de fábrica. Estos sensores iban proporcionando lecturas a tiempo real, de la posición exacta de la hidrofresa a su software de control, que representaba la información en la pantalla del operador. De esta manera se pudo asegurar que las excavaciones de los paneles se mantenía dentro de los límites de desviación admisibles.
- Control de la geometría de la excavación mediante sonar (ver figura 30). Para confirmar la información aportada por la hidrofresa acerca de la desviación de la excavación y para complementar esta información con datos sobre posibles colapsos de la excavación, Geocisa UK decidió realizar ensayos mediante sonar, al finalizar la excavación de cada panel y antes de comenzar con el montaje de la armadura. El equipo elegido para la ejecución de los ensayos fue un Drilling Monitor DM-604 de la casa Koden.
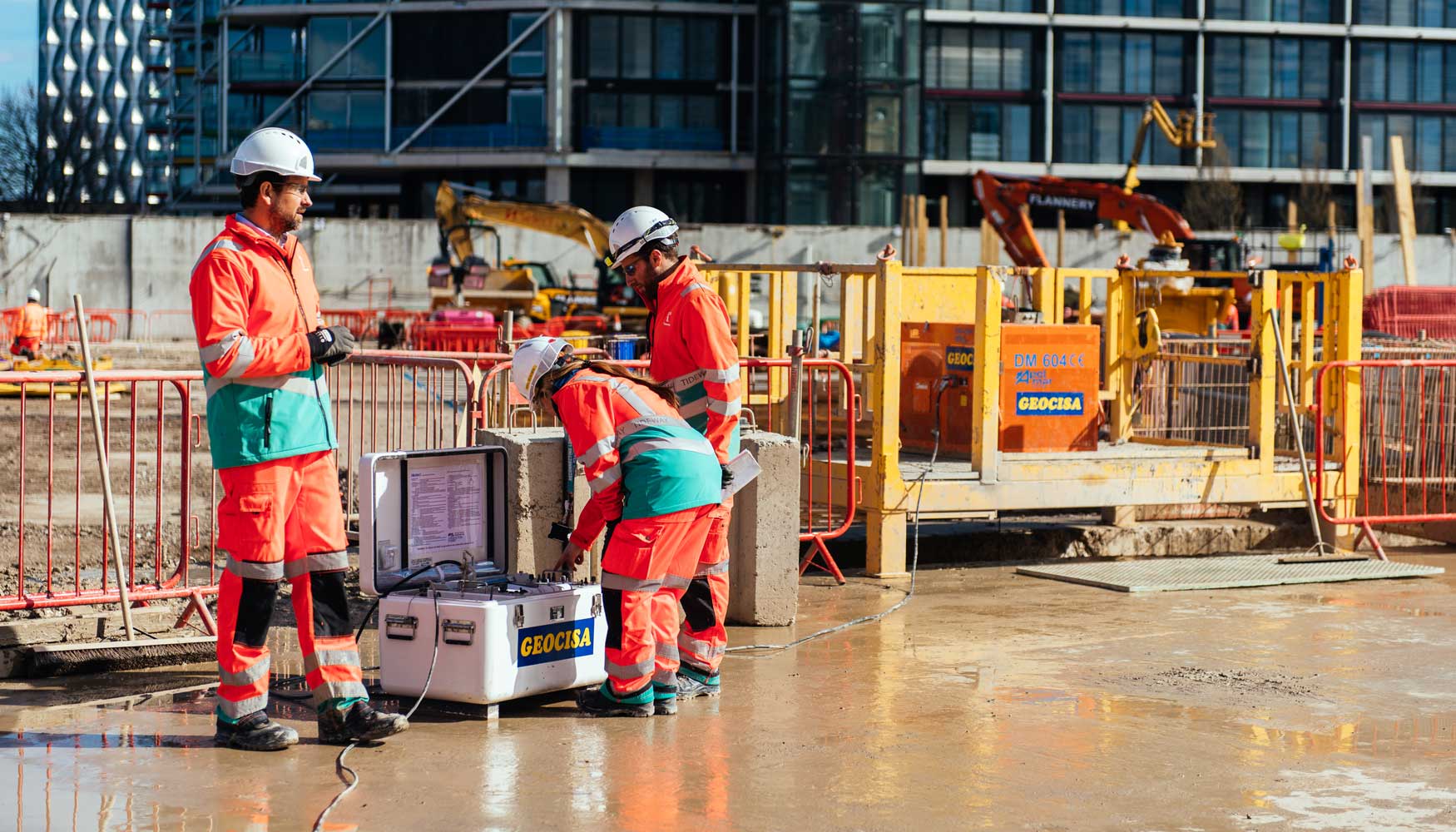
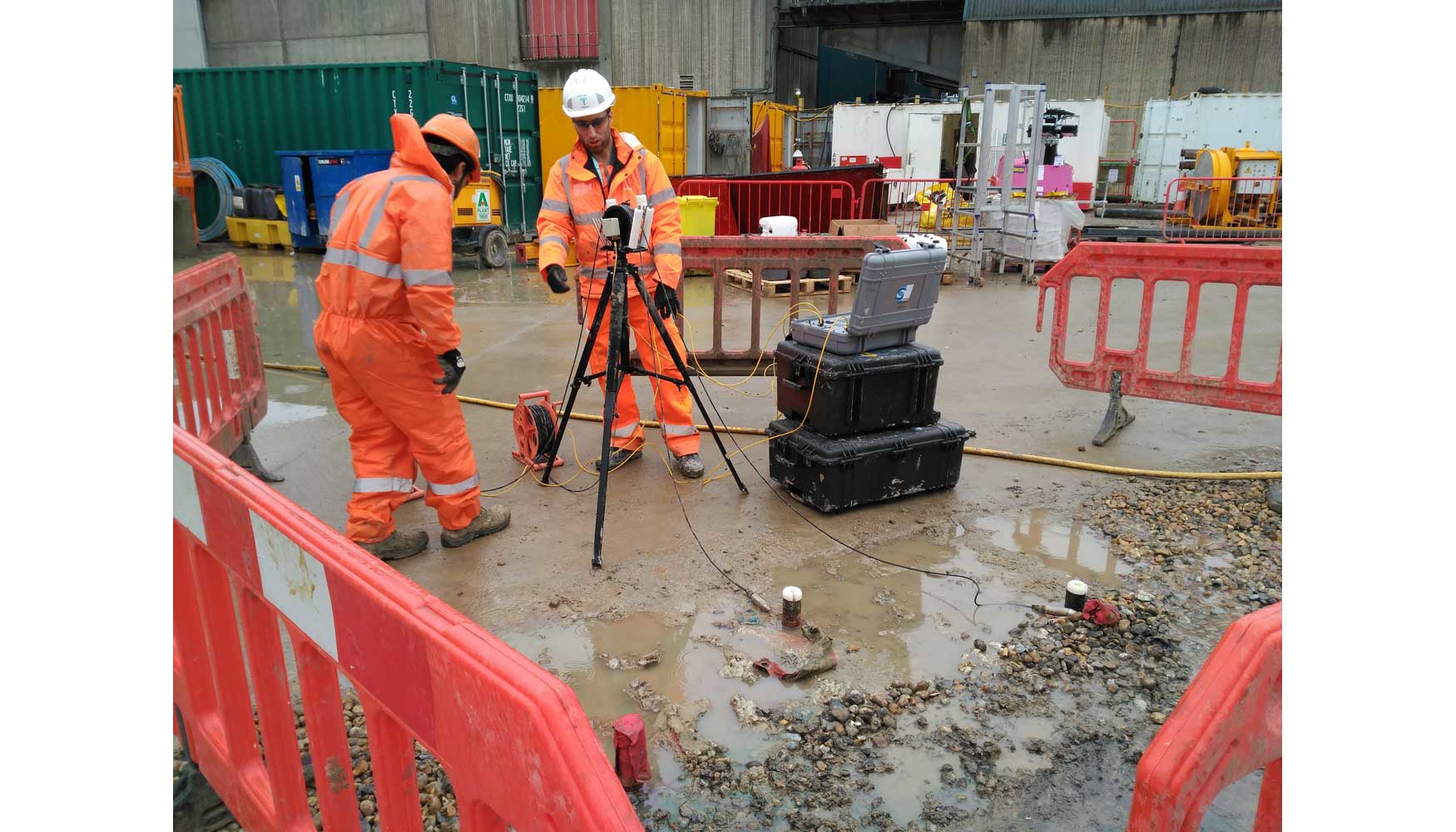
- Ensayos de integridad de las pantallas (ver figura 31): para confirmar la calidad del hormigonado se colocaron en cada pantalla tres tuberías de 2 pulgadas para la realización de ensayos Cross-hole. Después del hormigonado de cada panel y tras haber transcurridos al menos 8 días de curado, se realizaban los ensayos de integridad, que confirmaron que todas las pantallas habían quedado hormigonadas sin ninguna discontinuidad, ni descensos bruscos de energía en la señal.
- Control de recubrimiento de las armaduras. Dado que los requisitos de durabilidad de la obra eran altamente exigentes (120 años), se prestó gran atención al aseguramiento de los recubrimientos en las armaduras de pantallas, centrándonos en el diseño de los separadores a utilizar, así como en realizar un control exhaustivo post-construcción, que confirmara que dichos recubrimientos se habían alcanzado. Para ello durante la excavación interior del pozo, se fue comprobando en cada pantalla y cada 5 metros de profundidad, una superficie de pantalla de 1 m x 1 m donde se tomaban 4 lecturas del recubrimiento mediante un 'cover-meter'. El 'cover-meter' es un instrumento para localizar barras de acero y medir el recubrimiento existente en una estructura de hormigón armado. El sistema detecta las barras de refuerzo, determinando la profundidad a la cual se encuentran respecto al punto donde se sitúa el medidor (ver figura 32). Allí donde el recubrimiento fue inferior al exigido, este se incrementó siguiendo los procedimientos de remediación establecidos con anterioridad al comienzo de la excavación.
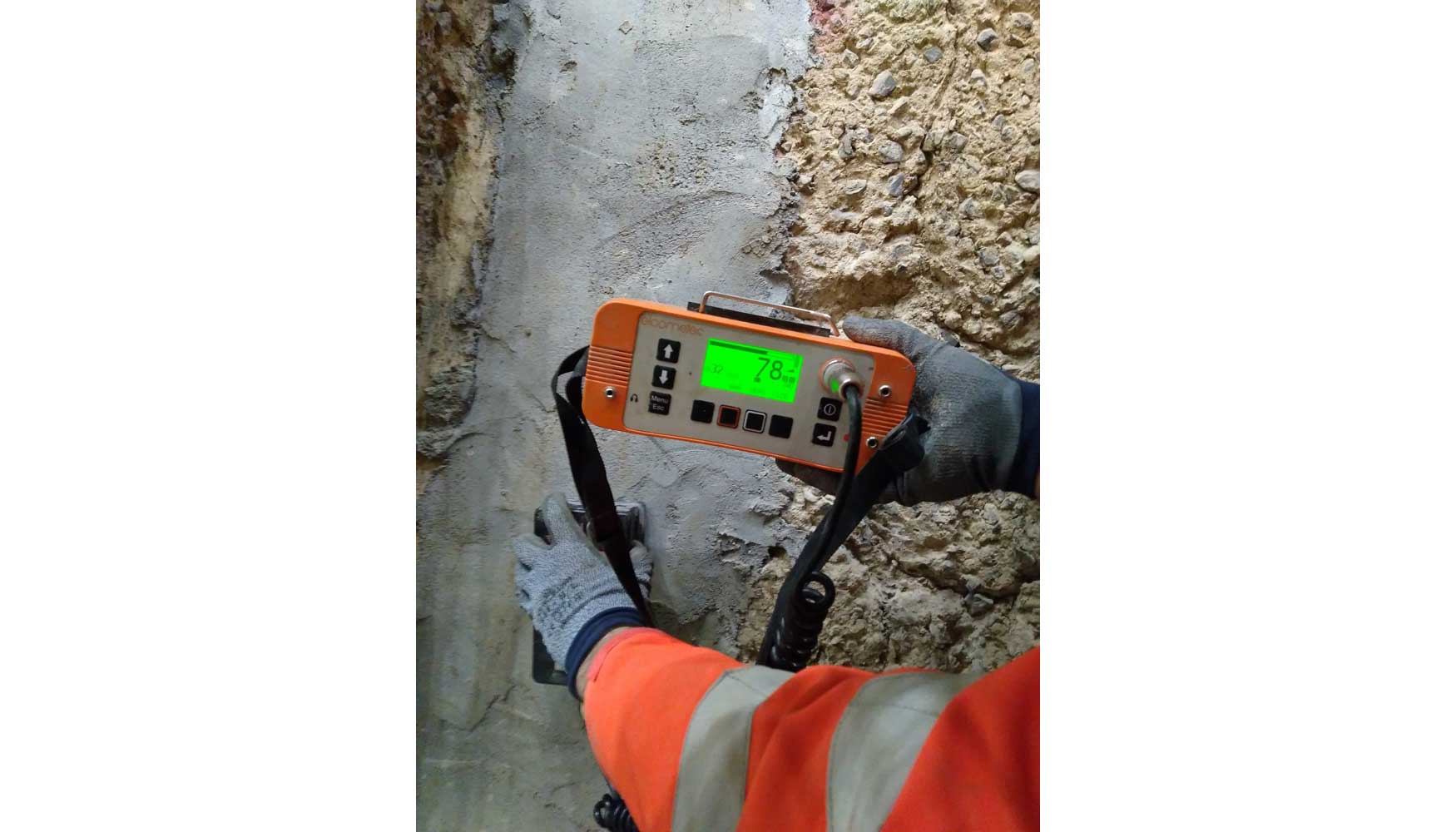
Conclusiones
Geocisa UK comenzó la ejecución de las pantallas para el pozo de ataque de Kirtling St. en noviembre de 2016 y se terminaron a comienzos de agosto de 2017. Desde esta fecha en adelante y hasta la finalización de la excavación dentro del pozo, se mantuvo un equipo de seguimiento y supervisión, de los trabajos de excavación llevados a cabo en el pozo. Este equipo de supervisión, se ocupó de registrar todas las anomalías que se encontraron en el muro pantalla, para categorizarlas y siguiendo el Método de Trabajo (Method Statement) establecido con anterioridad, determinar si requerían de reparación y en tal caso, aplicar el procedimiento de reparación adecuado (ver figuras 33 y 34).
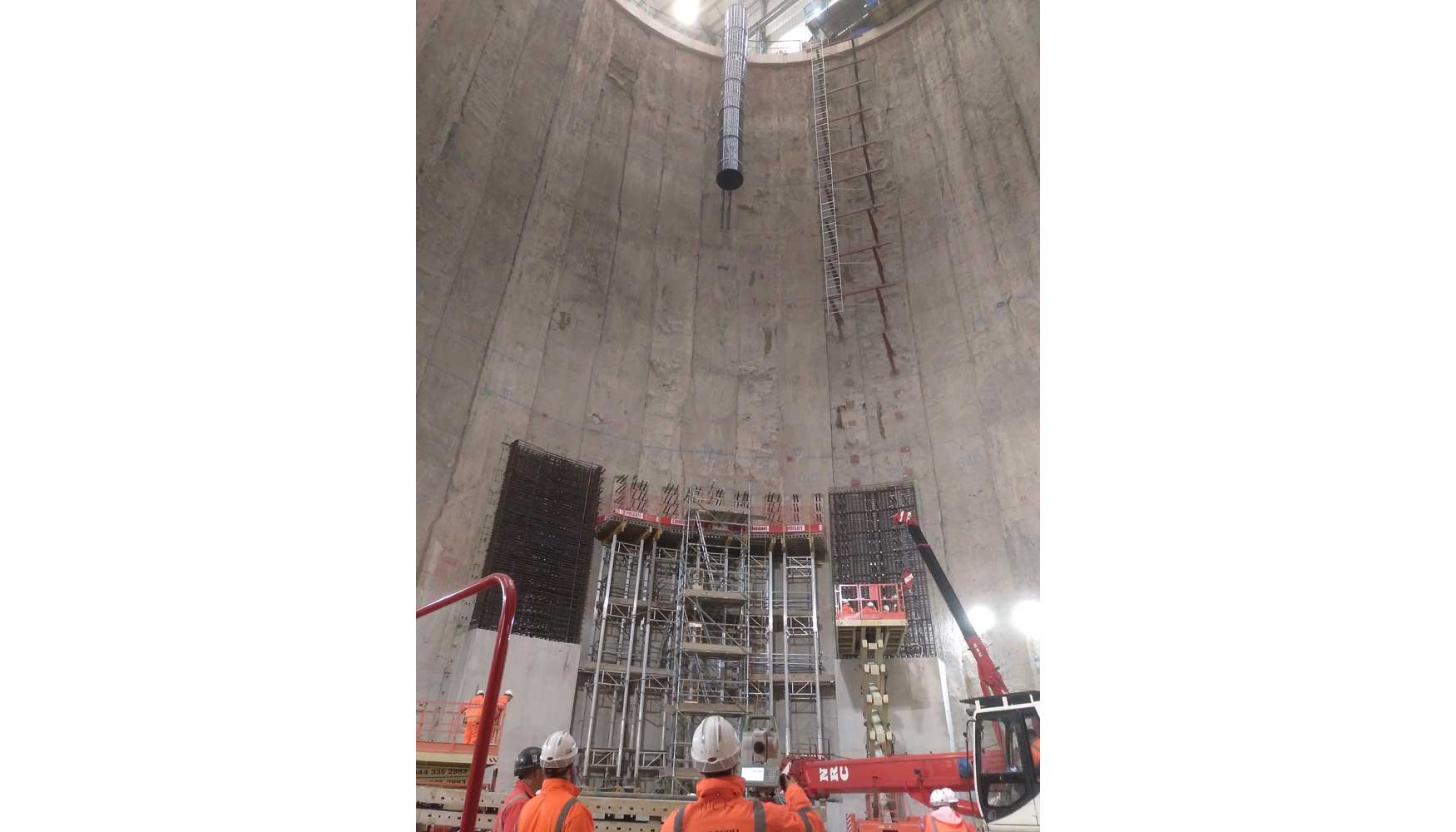
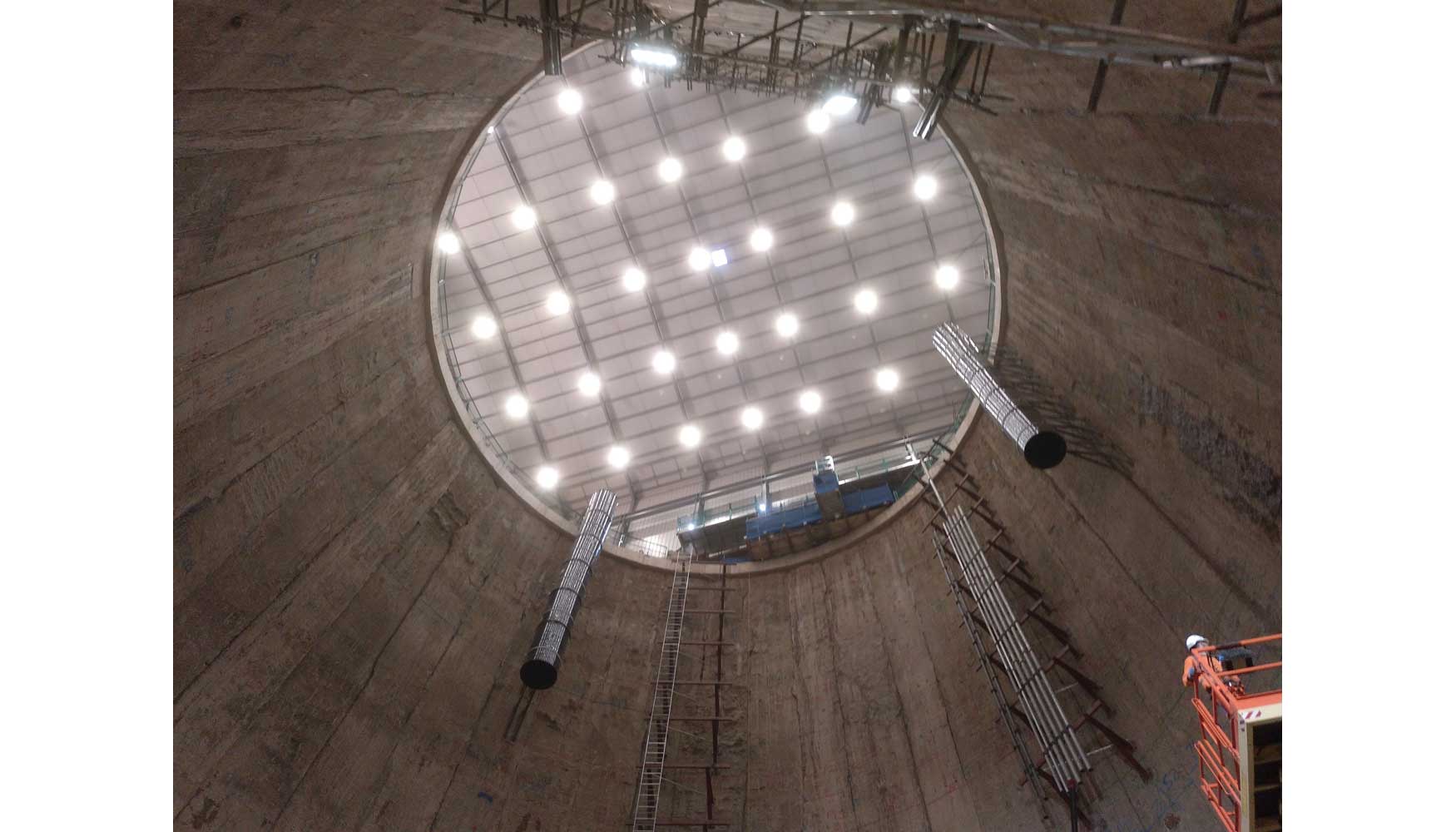
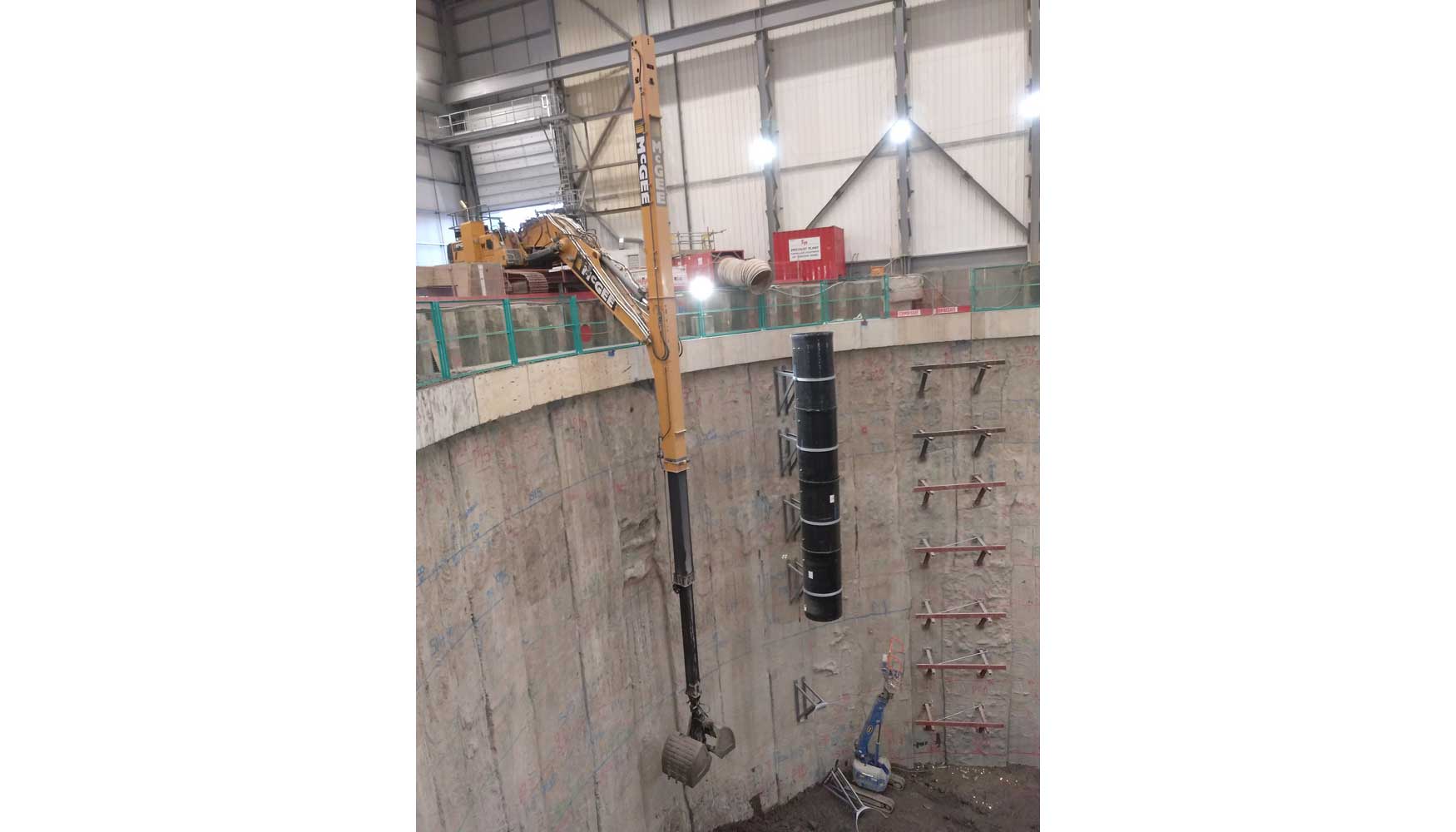
La excavación interior del pozo finalizó en agosto de 2018, sin que apareciera ninguna anomalía reseñable en las pantallas ejecutadas (ver figuras 33 y 34), más que pequeñas inclusiones de bentonita dentro de alguna pantalla, así como alguna pequeña zona con recubrimiento de menor espesor que el especificado. En cuanto a las exigencias de verticalidad de las excavaciones, se ha cumplido con las expectativas depositadas tanto en los equipos de maquinaria, con los que se han realizado las excavaciones, así como el equipo humano de operadores, que ha realizado la excavación de las pantallas.
Durante la ejecución de los trabajos se excavaron más de 9.800 m2 de pantallas, se vertieron más de 12.900 m3 de hormigón y se colocaron más de 1.140 toneladas de acero corrugado. Para ello se consumieron más de 4.900 dientes de perforación con incrustaciones de widia y más de 1.100 picas de widia. Todo este esfuerzo ha supuesto la ejecución con éxito del segundo pozo más profundo en todo Reino Unido realizado con pantallas y el más profundo ejecutado por Geocisa en sus 50 años de actividad.
Agradecimientos
Especial agradecimiento al equipo humano que ha hecho capaz la ejecución de los trabajos, tanto desde oficina como en la propia obra, así como al departamento de estudios de Geocisa por su incansable trabajo durante la fase de licitación.