Control de posicionamiento 7DoF en tiempo real de un sistema robótico industrial
El departamento de Automatización y producción del Fraunhofer Institute for Manufacturing Technology and Advanced Materials (IFAM) en Stade, Alemania, ha sido un socio oficial de CFK Nord durante muchos años y lleva a cabo investigaciones en el campo de la tecnología de la automatización, especialmente en lo que se refiere a la integración de la tecnología robótica industrial en los procesos de mecanizado y ensamblado para la producción de aeronaves.
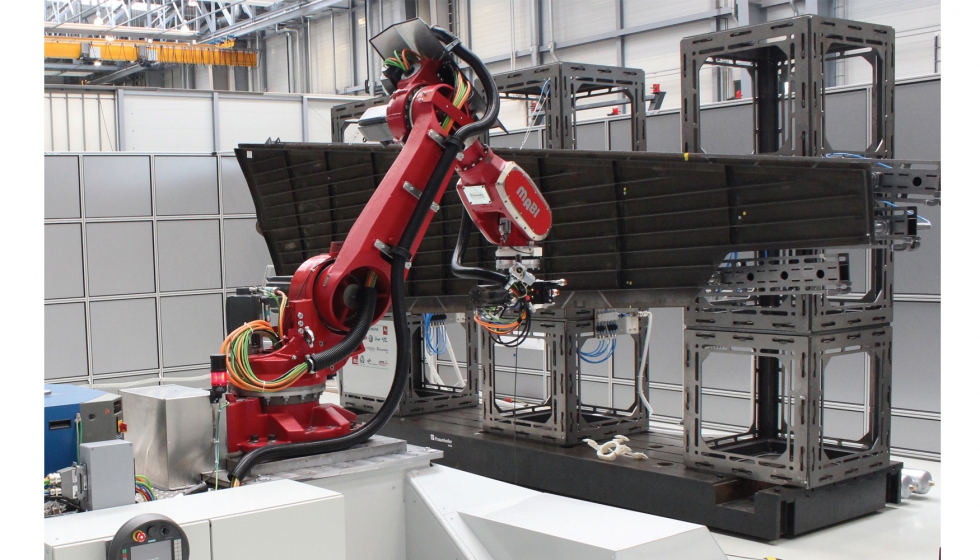
En Fraunhofer IFAM, las soluciones de sistema integrado y los conceptos de la planta se trabajan y se pueden implementar y optimizar en una escala de uno a uno, en una sala de pruebas de 4.000 metros cuadrados y con una altura de 15 metros por debajo del gancho de elevación, Esto permite el desarrollo de soluciones a partir de una sola fuente que se pueden transferir a aplicaciones de gran escala sin un retraso innecesario y con el mínimo de gasto, asegurando así el liderazgo al ofrecer nuevas e innovadoras tecnologías.
La producción libre de defectos se hace necesaria especialmente al fabricar piezas en puntos clave del proceso de producción, y esto solo es posible a través de un control definitivo del proceso. Por lo tanto, una herramienta importante es la prevención del error mediante el seguimiento de los parámetros que determinan la calidad del proceso. El fresado, la perforación y el corte por medio de inyección de agua son áreas determinantes en el campo del desarrollo del proceso. Los investigadores en Fraunhofer IFAM, en cooperación con Hamburg University of Technology (TUHH), integran robots industriales o máquinas de pórtico en procesos que simultáneamente requieren de una alta precisión y una alta movilidad de la herramienta junto con la pieza. Además, preparan soluciones para llevar a cabo el acoplamiento simultáneo de varias unidades de mecanizado sobre la misma pieza de trabajo.
Existe una gran demanda de mecanizado eficiente de grandes estructuras en la industria aeronáutica para reducir los tiempos de producción, y esto ha derivado en un uso creciente de robots industriales como una alternativa a las máquinas especializadas que están instaladas actualmente. Un inconveniente mayor de los robots industriales dentro de la aplicación del mecanizado es la insuficiente precisión absoluta provocada por su estructura en serie, la adaptación de los engranajes y las influencias externas como las fluctuaciones de temperatura. Además esto, las fuerzas de mecanizado que se presentan durante la fabricación de los componentes de polímero reforzado con fibra de carbono (CFRP) en la industria aeroespacial provocan desviaciones significativas del punto central de la herramienta (TCP) a partir de la ruta del punto medido debido a la baja rigidez del robot cinemático. No es posible medir estas desviaciones con la ayuda de codificadores giratorios internos en los motores, por lo tanto no se pueden afectar o compensar por rutinas de calibración y el controlador interno del robot.
Este estudio muestra una oportunidad de mejorar la precisión de un robot de fresado industrial durante el proceso de fresado con la ayuda de un Leica Absolute Tracker AT960 usado como un sistema de medición externo. Para detectar la posición y la orientación del TCP de la herramienta de fresado durante el procesamiento se instaló un palpador Leica T-Mac en el eje para permitir llevar a cabo una medición 6DoF Los datos de posicionamiento del efector final se transmiten en milisegundos al controlador de la máquina CNC del robot a través del sistema bus EtherCAT en tiempo real, que calcula la corrección de la ruta. Además de la información de posicionamiento 6DoF, estos datos contienen mediciones de tiempo de alta precisión, por lo que se pueden considerar como una medición 7DoF. La introducción de una serie adicional de controles en el controlador CNC del robot permite una corrección precisa de la ruta en tiempo real, por lo que la geometría de la ruta del fresado satisface las exigentes tolerancias de la industria aeronáutica.
Descripción técnica del láser tracker
La habilidad de Hexagon Manufacturing Intelligence consiste en proporcionar y apoyar en ‘sensing, thinking, acting’, soluciones de sensibilidad, pensamiento y acción para los fabricantes industriales. La tendencia de la industria de siguiente nivel para ofrecer control de calidad en la línea en el proceso de producción requiere de la evolución innovadora de la industria de los sensores. En una aplicación de producción de gran volumen, como el ensamblado aeroespacial, los sistemas Leica Absolute Tracker miden la distancia y el ángulo horizontal y vertical hacia un reflector esférico instalado, proporcionando mediciones precisas 3DoF, 1.000 veces por segundo. El interferómetro absoluto (AIFM) asegura una precisión de seguimiento del orden de +/-10 micras sobre el alcance de trabajo completo del sistema, aún en objetivos en movimiento.
Al combinar las mediciones tradicionales de láser tracker con fotogrametría, la cámara integrada con mini-variozoom del Leica Absolute Tracker AT960 adicionalmente determina el balanceo, la inclinación y el ángulo de deriva en los palpadores con LED, como el Leica T-Mac. Esto permite que el sistema proporcione información precisa de la posición y orientación 6DoF con marcas temporales precisas. Para tareas adicionales como la inspección de piezas, estos datos se llevan a través de la interfaz LMF, en tanto que es posible la manufactura asistida por metrología 7DoF gracias a la adición del ‘feature pack’ Ethernet industrial en tiempo real basado en la norma EtherCAT.
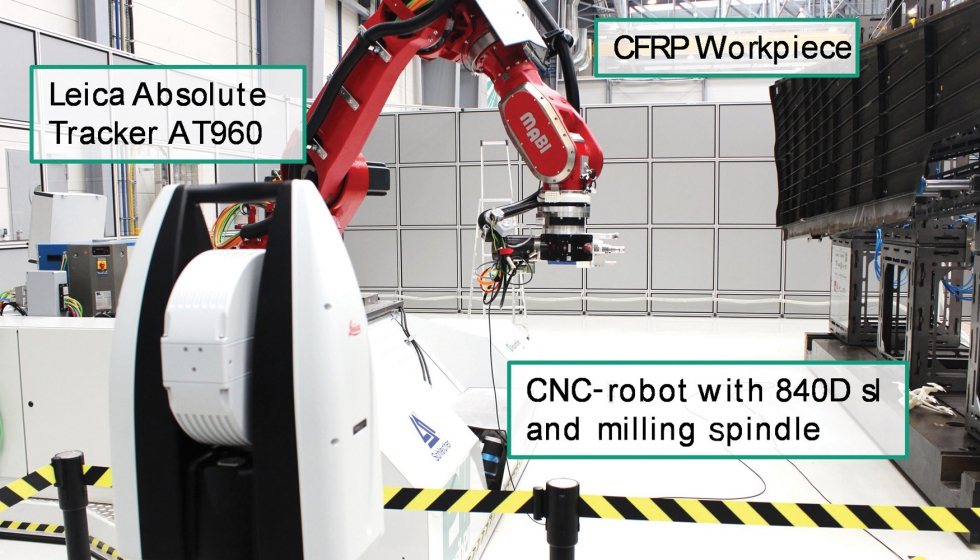
Descripción del sistema
Se usó un módulo robotizado para la fabricación de grandes estructuras para los experimentos efectuados en Fraunhofer IFAM (véase la figura 1). Para garantizar una máxima compatibilidad, el robot estaba equipado con un controlador Siemens Sinumerik 840D sl CNC. Este controlador es particularmente común para máquinas fresadoras de cinco ejes y ofrece diversas interfaces para diferentes aplicaciones.
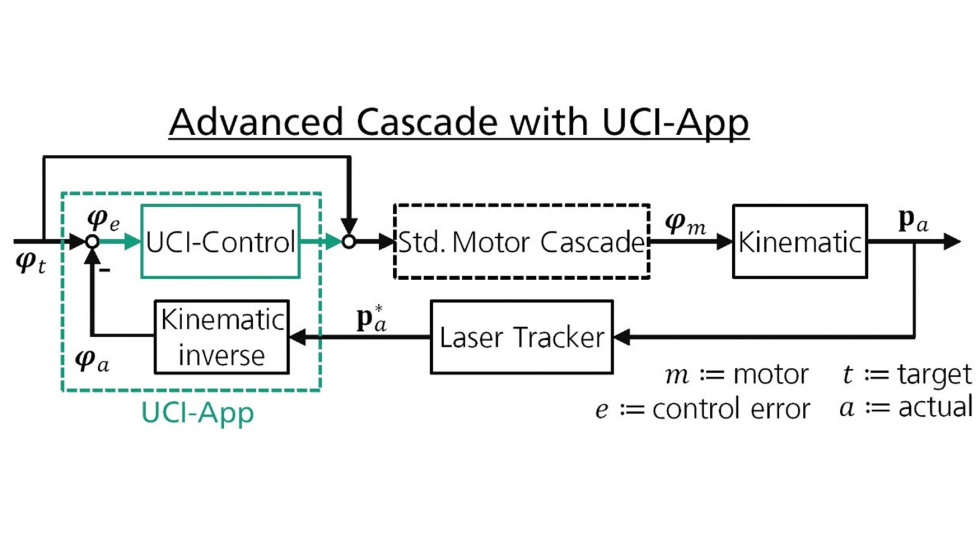
Para la aplicación que aquí se explica, el controlador ofrece la posibilidad de ejecutar correctamente el código C++, el cual se ejecuta en cada rutina de ciclo de control. Las señales de corrección en las uniones permiten al robot ejecutar la ruta corregida. Esta interfaz se denomina Universal Compensation Interface (UCI), con la aplicación de software asociada UCIApp (véase la figura 2).
Actualmente, los robots usan principalmente los conceptos de control en cascada para cada eje individual. Esto consiste en un ciclo de control de posición y ciclos de control actual de velocidad interna que incluyen controles previos de torsión y velocidad. Las cascadas internas trabajan con ciclos de tiempos más cortos que el bucle de control de posición, cuyo ciclo de tiempo generalmente es de 4 y 12 milisegundos Los parámetros de control se configuran de tal forma que el bucle de control permanece estable a lo largo de toda el espacio de trabajo y para diversas condiciones de carga y rutas de movimiento. Ya que los ejes del robot están mecánicamente acoplados y ya que el robot puede ser malinterpretado como un sistema de variables múltiples, la aproximación directa de los seis controles individuales uno a uno hace necesario un diseño de controlador robusto. Por lo tanto, las desviaciones basadas en modelos de error se observan y se compensan para las perturbaciones externas.
El bucle de control del láser tracker amplía este concepto al usar una cascada externa, consistente en mediciones 7DoF de láser tracker, el modelo de robot cinemático y el controlador actual – el UCI-Control. Con el fin de proceder con la aproximación de controles independientes de un solo eje, este control adicional también tiene lugar en el eje base. Los errores de posicionamiento TCP medidos por el AT960 se convierten en errores de uniones, tomando en cuenta el modelo cinemático inverso. Estos errores de uniones se agregan como valores de compensación a la planeación de la ruta del robot por el UCIControl y permiten una operación de alta precisión del robot.
En caso de un control puramente 3DoF, esta aproximación no es aplicable directamente, ya que la medición de tres coordenadas no es suficiente para calcular uniones de seis ángulos. En este caso, el control tiene lugar en el espacio cartesiano y un vector de corrección 3D se enviará al controlador del robot. Estas mediciones se transfieren con una latencia muy pequeña y una marca de tiempo altamente precisa. Con fines de claridad, de ahora en adelante este tipo de control se denominará como control 3DoF.
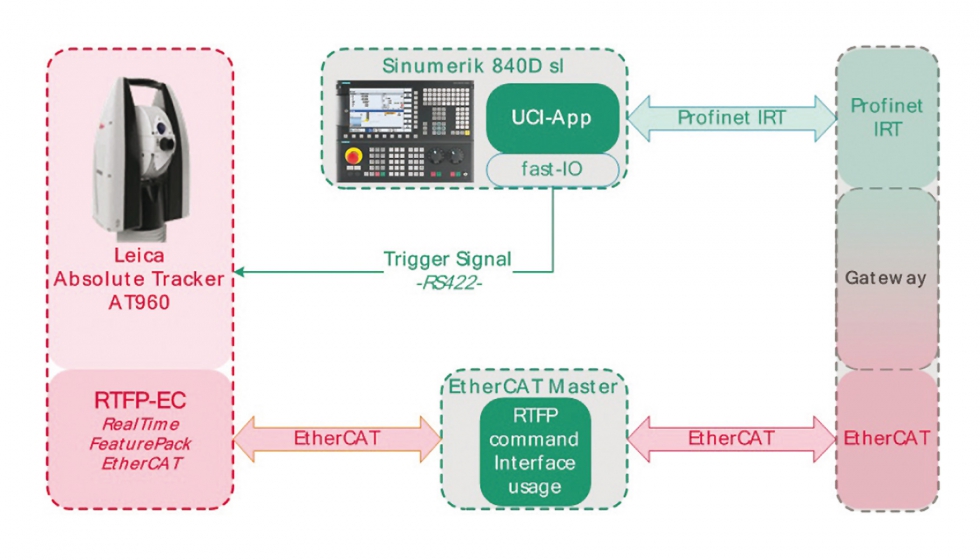
Para transferir datos entre el AT960 y el controlador del robot, diversos sistemas bus en tiempo real serán implementados. El AT960 usa EtherCAT para proporcionar datos de posicionamiento y posición, así como la marca de tiempo en tiempo real, mientras que el Sinumerik 840D sl trabaja con base en el Profinet IRT (figura 3). La sincronización entre EtherCAT y los ciclos Profinet IRT tiene lugar en un puerto de enlace, el cual convierte los protocolos bus. Este factor complica la activación determinística y el uso de un proceso de medición, y puede evitarse con la aplicación de una señal de activación basada en RS422.
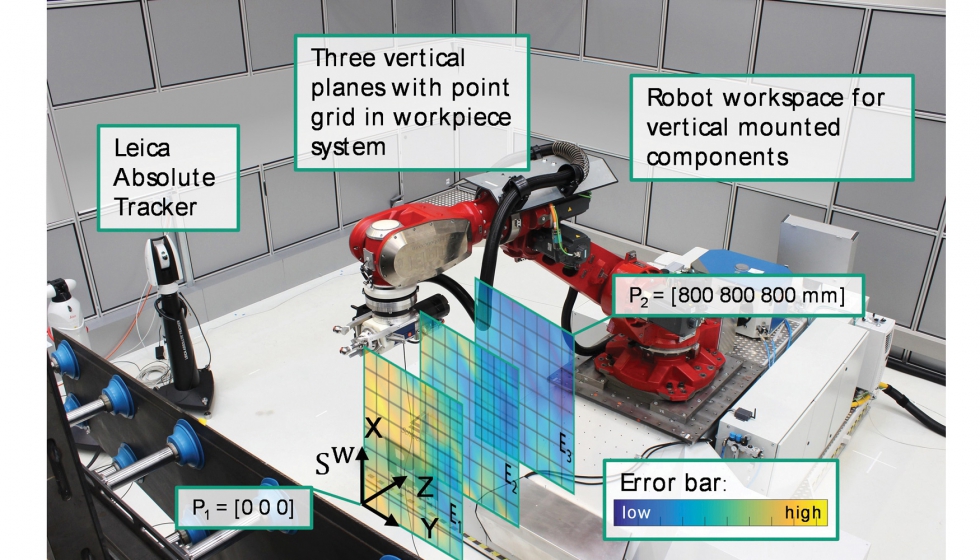
Para ese propósito, la UCI-App envía una señal precisa de activación al controlador del AT960 en cada ciclo de tiempo CNC y guarda la marca de tiempo correspondiente. Con la confirmación de la recepción de la señal de activación, el AT960 envía la posición actual o datos de posicionamiento y la marca de tiempo vía EtherCAT a un PC industrial, el cual funciona como el EtherCAT-Master y envía los datos al control CNC a través del puerto de enlace. La UCI-App compara la marca de tiempo del activador y los paquetes de datos de posicionamiento recibidos y relaciona los datos correspondientes. Por lo tanto, se lleva a cabo una transferencia entre EtherCAT y Profinet IRT incluyendo la resolución de medición crítica de tiempo.
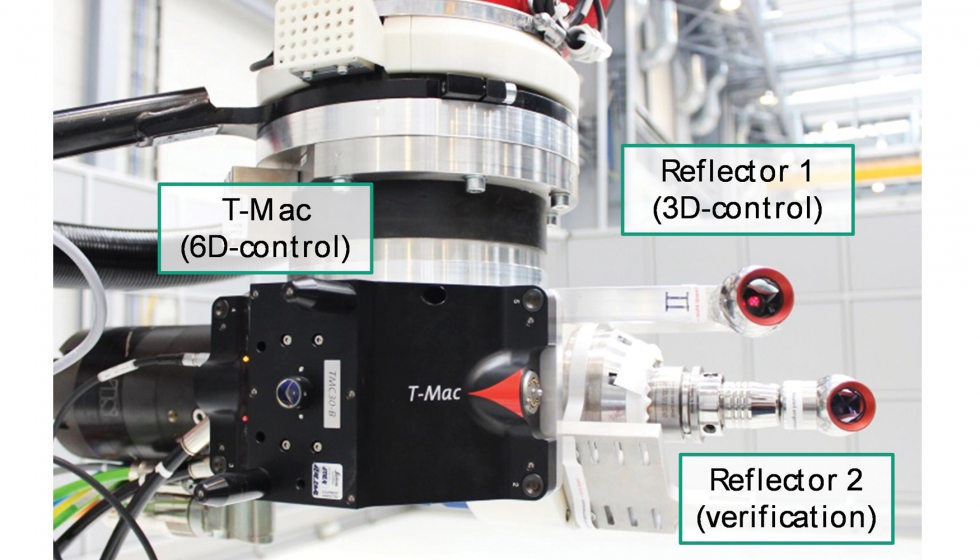
Registro de prueba para la investigación de la precisión
La configuración de la prueba para la determinación de la precisión absoluta del robot replica un proceso de fresado de un componente grande estructurado (figura 4). Tres planos verticales se aproximan a un patrón de puntos de nueve por nueve, el cual se coloca en un sistema de componente SW. El robot se detiene en cada uno de los puntos durante varios segundos hasta que las posibles vibraciones desaparecen, por lo que los datos de medición se pueden tomar correctamente. Durante este tiempo, el robot permanece inmóvil con respecto al controlador del láser tracker externo.
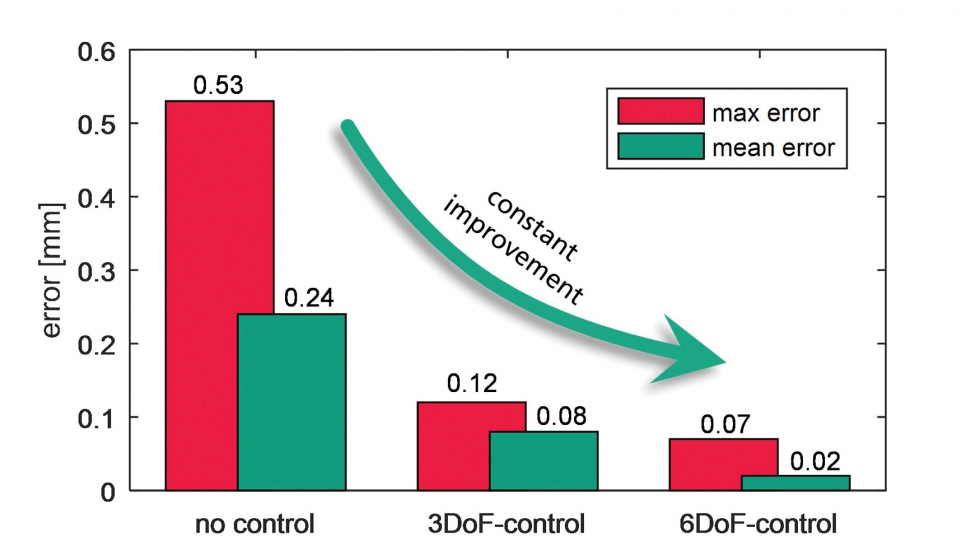
La precisión absoluta se medirá en tres rutinas de ejecución sin un control externo; con un control 3DoF y con un control 6DoF. El AT960 mide el Leica T-Mac para el control del posicionamiento y el reflector 1 para el control 3DoF (véase la figura 5). La posición absoluta se determina directamente en el TCP vía el Reflector 2 a través de un Leica Absolute Tracker independiente y dinámico en el mismo sistema de coordenadas de referencia.
Los valores medidos sin control muestran la precisión absoluta del robot mismo, o cual puede ser mejorado claramente con un control 3DoF o 6DoF. Se observará que los resultados del control 6DoF son superiores al control 3DoF. Los errores que quedan del control 3DoF se pueden rastrear en sentido inverso hasta la estrategia del control inferior y los errores iniciales de medición entre la pieza y el robot, así como los errores de orientación que surgen en el TCP debido a la consideración de los efectos de la adquisición y de los errores de posición. Lo último se tomará en cuenta a este respecto, ya que durante la producción la visibilidad del espacio cercano al reflector instalado en el TCP se puede ver limitado debido a la posible emisión del chip y a la complicada geometría del componente. Una distancia más grande entre el reflector y el TCP tendrá una palanca para el brazo más larga y se obtendrán errores grandes proporcionalmente de posición del TCP.
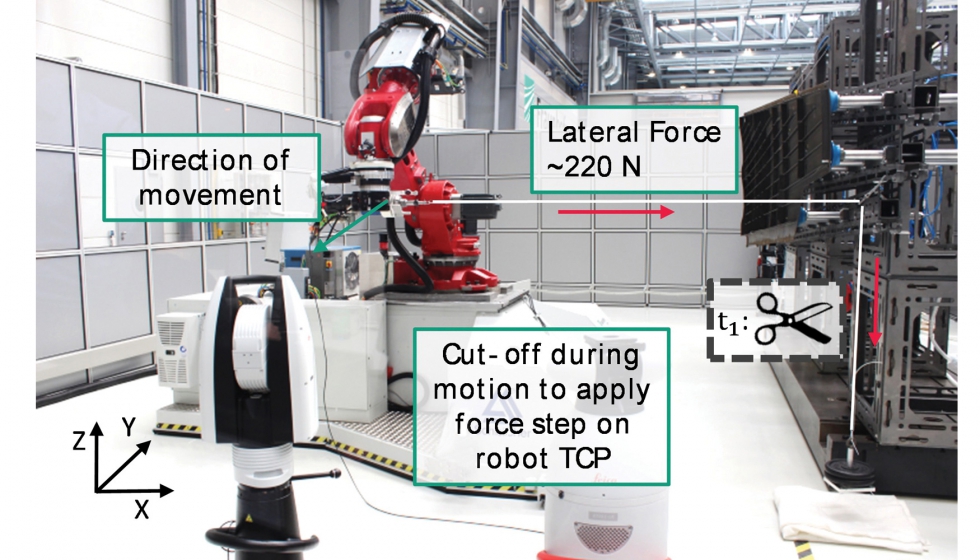
Pruebas de fuerza de tracción
La fuerza del controlador externo se demuestra mejor cuando el robot recibe el impacto por efectos externos que no han sido medidos con los codificadores internos de los motores. Entre estas están los efectos de expansión y de contracción en la estructura provocados por el calentamiento de los motores y de las estructuras, o los impactos de fuerzas externas para ejemplificar las fuerzas del proceso.
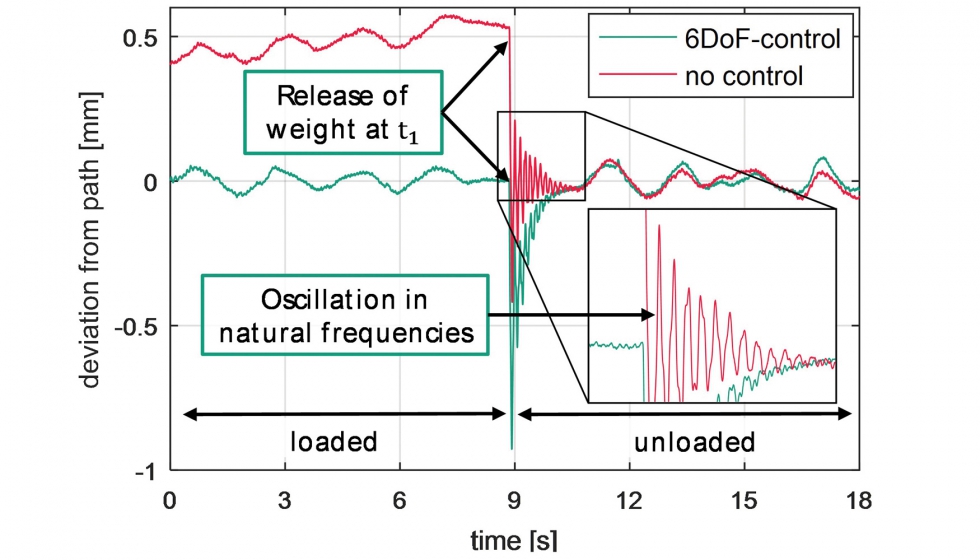
Las fuerzas externas funcionan tanto en la estructura como en los engranajes del robot. Dependiendo de la dirección del efecto, estas fuerzas varían el error de posición resultante. Además, durante el proceso de fresado pueden surgir fuerzas potentes del proceso de fluctuación, por lo que una compensación previamente calculada o un modelado se hace muy complicado. Para simular especialmente la entrada del corte del fresado y las rutas de salida que surgen como consecuencia, se elige una configuración como la que se muestra en la figura 7.
En el experimento, se aplica una fuerza constante y ortogonal en la dirección del movimiento con la ayuda de pesos con un intervalo de alimentación constante. Estas fuerzas divergen del robot a partir de su ruta planeada debido a su composición estructural. En el tiempo t1, el peso se remueve de forma abrupta. Esto resulta en un incremento repentino de la fuerza, lo cual excita las frecuencias naturales del sistema. Se espera entonces que el robot se mueva sobre la ruta del objetivo con respecto a la precisión de la ruta.
El resultado será un error en la ruta de 0,5 milímetros si el control externo se desactiva. Después de eliminar los pesos, el robot sigue su ruta como se esperaba. Al usar el control 6DoF, se puede observar la fuerza de este concepto de control. El control 6DoF resiste cualquier tipo de efecto del peso antes del incremento de la fuerza y lleva al robot de vuelta a su ruta planeada. Ya que la dinámica del control y la amplificación de la cascada interna no pueden ser influenciadas por medio de la UCI-App, en este caso es posible identificar los límites del controlador. Una alta estimulación externa, especialmente en el intervalo de la primera frecuencia de resonancia del robot, difícilmente se puede prevenir. Solo el incremento del ancho de banda del controlador del estado y velocidad de la cascada interna puede ofrecer mejoras en este punto, a partir del cual un bucle de control externo traería beneficios equitativamente.
En otras palabras, esto significa que el error se puede compensar, siempre y cuando el ancho de banda de las fuerzas modificadoras actuales sea menor que el ancho de banda del bucle de control del láser tracker externo.
Asimismo, estas mediciones muestran que, mientras las fuerzas externas de operación sean estáticas o tengan una baja frecuencia, es posible prevenir correctamente las desviaciones de la ruta planeada con la ayuda del control 6DoF. Ya que los cambios típicos de temperatura tienen un comportamiento de baja frecuencia, también se puede esperar que las influencias de la temperatura se ajusten usando un control 6DoF.
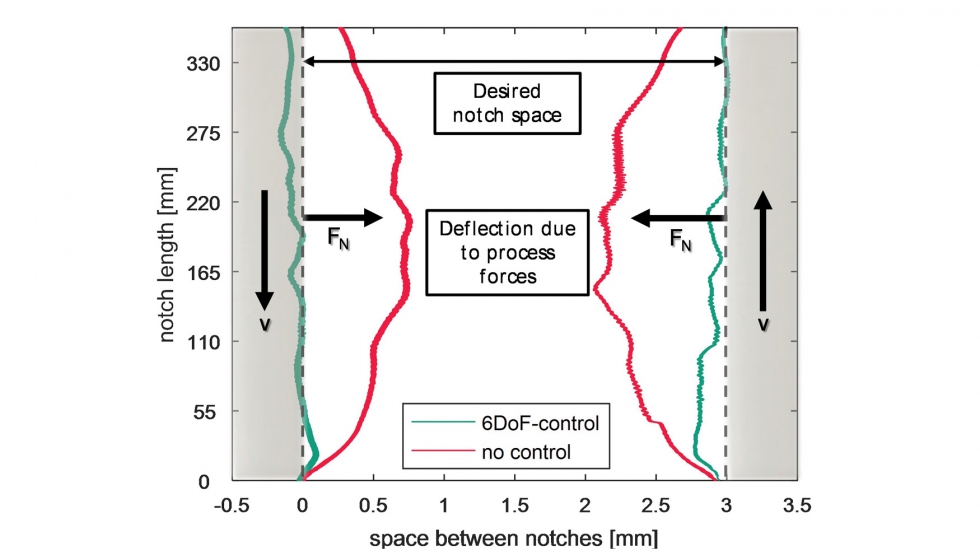
Prueba de fresado
La idoneidad del control externo para la mejora de la precisión en procesos de mecanizado se valida por la prueba de fresado que se explica a continuación. Las pruebas de fresado se llevaron a cabo en el material de poliuretano Necuron 1007, el cual generalmente se usa para el modelado en el conformado. Debido a su estructura homogénea, resulta adecuado para las pruebas de fresado, ya que es posible mantener constantes las fuerzas de fresado al cambiar los parámetros del mecanizado. Para generar fuerzas considerables de mecanizado, se usó una máquina con un diámetro de 15 milímetros, tres bordes de corte y un intervalo de alimentación de 2.500 milímetros por minuto, girando a un intervalo de 6.000 rpm.
Para cada experimento, se efectuó el fresado de dos muescas paralelas en direcciones opuestas. Esto provocó fuerzas normales que apuntaban hacia cada una y reducían el ancho de la barra restante entre ambas muescas. El ancho de las barras se puede verificar con la ayuda de mediciones sencillas para determinar la deflexión a partir de la ruta planeada durante el proceso de fresado. Además, la ruta actual del TCP del robot se registra con la ayuda del segundo tracker. Para evitar la estimulación de alta frecuencia durante el proceso, se eligió una aceleración muy pequeña. El ancho de barra deseado entre las ranuras debe ser de tres milímetros. Como se ve, la ruta se sigue con la ayuda del control 6DoF mientras el robot se desvía de su trayectoria objetivo sin control externo.
Estos resultados confirman las observaciones del experimento anterior con fuerzas externas de tracción. Es posible obtener la trayectoria de fresado recto dentro del intervalo de la repetibilidad de la trayectoria del robot con la ayuda de un sistema de soporte de láser tracker externo. De esta manera, se obtiene un beneficio significativo de mejora de la calidad en el mecanizado de componentes grandes.
Conclusión y resumen
En 2015, aproximadamente 1.200 nuevas aeronaves fueron puestas en funcionamiento por Airbus. Junto con pedidos anteriores, Airbus debía entregar aproximadamente 7000 aeronaves en el año siguiente, ya que la demanda crece constantemente, especialmente para aeronaves de tamaño mediano. Con la limitada capacidad de producción en las plantas de manufactura de la industria aeronáutica, la demanda de automatización está creciendo rápidamente. El reemplazo de grandes máquinas de pórtico y el cambio hacia una producción más flexible en el sentido de la ‘Fábrica del futuro’ promueve la demanda de nuevos conceptos y soluciones para las plantas. Fraunhofer IFAM, junto con Hexagon Manufacturing Intelligence, ha demostrado cómo la manufactura de alta precisión puede aparecer en el futuro, haciendo uso del control externo 6DoF en un robot de fresado industrial.
La solución demostrada incluye una integración y fusión completa de tecnología de medición 7DoF y un control de la máquina en un entorno en tiempo real y cerrado con acceso directo a los datos de medición y control. La integración de un bucle de control externo permite obtener mejoras en la precisión del posicionamiento del robot hasta el rango de repetibilidad de la cinemática. Particularmente en la industria aeroespacial, cuyo objetivo principal se encuentra en las bajas tolerancias para los procesos de fresado y perforación, y al mismo tiempo trabajar con grandes dimensiones estructurales, el diseño general del sistema que aquí se muestra es claramente aplicable. En combinación con plataformas móviles, el espacio de trabajo altamente preciso del sistema del robot – aún sin una calibración completa del robot – se puede comparar con el rango de trabajo de las herramientas de maquinaria y, a cambio, ofrece un ahorro en los costos de inversión para las cimentaciones de cargas pesadas y sistemas especiales. Los resultados que aquí se presentan muestran la integración de un láser tracker en tiempo real a un módulo de robot para fresado adaptable es una alternativa altamente eficiente para el procesamiento automatizado de grandes componentes en las fábricas del futuro.