EQUIPOS Y TECNOLOGIAS PARA CORTE DE CHAPA
El corte de chapa mediante oxicorte (2ª parte)
Rico, J.C.(1); Valiño, G.(1); Cuesta, E.(1); Villanueva, A.(2)
(1) Profesores del Area de Ingeniería de los Procesos de Fabricación – Universidad de Oviedo
(2) Director de IDP, S.L.15/03/2002
4. PROBLEMÁTICA DEL CORTE DE CHAPA Y LA GENERACIÓN DE TRAYECTORIAS
Trabajar con una aplicación CAD/CAM destinada a la generación automática de trayectorias de corte 2D para máquinas de oxicorte requiere inevitablemente conocer toda la problemática específica que presenta este proceso.
Aunque este conocimiento se centra principalmente en los problemas que requiere la generación de trayectorias, inevitablemente lleva con frecuencia a tratar problemas relacionados con la geometría de partida, constatando la dificultad añadida que conlleva generar un trayectoria correcta si el perfil de la pieza no está perfectamente definido. Un tipo especial de geometría muy utilizada en calderería, como es el caso de aquellas que provienen del desarrollo plano de piezas 3D de chapa (tolvas, codos, etc.), también llevan asociado un tratamiento específico.
Otros problemas aportados por la experiencia de los usuarios, y relativos a temas técnicos como el control de los parámetros tecnológicos (espesor, velocidad, etc.) de cada proceso, el postprocesado de los programas CN y su correspondiente transmisión al control numérico de la máquina, etc., influyen también decisivamente en el modo en que se generarán las trayectorias.
4.2 Problemática referente a la geometría de partida
Un primer aspecto que debe contemplar una aplicación de CAD/CAM para corte automático de chapa en 2D es la "identificación del perfil" de la pieza a cortar, con la finalidad de garantizar una correcta generación de las trayectorias correspondientes. En este sentido, se hace imprescindible un reconocimiento automático de todas las entidades que conformen el dibujo seleccionado con el fin de determinar exactamente cuál es el perfil de la pieza y en su defecto, que errores presenta. Si durante esta identificación se detecta algún error, el sistema debe ser capaz de corregirlo (en la medida de lo posible) de acuerdo con el usuario.
La geometría de partida en cualquier sistema de CAD puede haber sido generada por el propio sistema o importada a través de formatos normalizados (DXF, IGES, etc.). Cuando esta geometría se realiza sobre el propio sistema de CAD y se orienta a la generación de trayectorias de corte en 2D, debe tratarse de un perfil plano perfectamente construido. En muchas ocasiones, esto no es así y a menudo el delineante o programador comete errores inherentes a su forma de trabajo, no selecciona adecuadamente los puntos iniciales o finales de un segmento para enlazarlo con el siguiente, duplica entidades (una encima del otro), se producen cruces de elementos que deben ser consecutivos, etc. Este tipo de problemas deben ser solucionados si se quieren evitar trayectorias erróneas, cortes repetidos de un mismo segmento/s, etc.
Otro tipo de problemas asociados a la geometría consiste en todas aquellas bifurcaciones, zonas de entidades que se solapan, etc., que se suelen producir durante el trazado manual debido al empleo de elementos auxiliares, textos o cotas que han debido ser borrados posteriormente, etc. Los problemas de este índole no son fáciles de detectar, ni siquiera ampliando la zona de trabajo. En el caso de cruces y/o bifurcaciones la detección puede ser relativamente sencilla, ampliando el dibujo hasta que el defecto sea visible. Probablemente una función de chequeo a nivel de toda la información asociada al plano o que recorra automáticamente el perfil en busca de elementos mal cerrados, puede ser muy conveniente es estos casos.
Si el perfil de la pieza a cortar no está correctamente cerrado, esto es, si el punto final de una entidad no coincide exactamente con el inicial de la siguiente, la trayectoria simplemente no puede ser generada por falta de continuidad. Si la distancia de separación de los elementos es grande, del orden del kerf o compensación de la herramienta (separación que depende del tipo de antorcha, presión del gas que se suministra, etc.), es posible que la geometría tenga realmente un final en dicho extremo. En el caso de que la distancia de separación sea igual o un poco mas pequeña que la sangría, la pieza cortada no se corresponderá con la que realmente se ha dibujado, y cuando esa distancia de separación es mucho mas pequeña (menor de 1 mm) lo más probable es que se trate de un error no detectado por el usuario. En todos estos casos, será imposible generar la trayectoria completa deseada.
El último de los casos mencionado anteriormente es un problema frecuente cuando se trabaja con dibujos generados con otros sistemas de CAD. Aquí la pérdida de precisión en los decimales asociados a los puntos de la geometría que se tiene al utilizar formatos normalizados (DXF o IGES) puede provocar problemas de contornos abiertos muy difíciles de detectar (incluso con ampliaciones sucesivas) a simple vista, incluso del orden de 10-12 mm, y en consecuencia la imposibilidad de generar correctamente las trayectorias de corte.
4.3. Geometrías especiales de partida: superficies desarrollables para calderería
En los sectores de construcción metálica y sobre todo de calderería, aparece un tipo diferente de problemas debida al uso común de un tipo especial de piezas. Se trata de piezas formadas, total o parcialmente por superficies desarrollables de chapa que además presentan intersecciones entre sí.
El desarrollo plano de éstas superficies se han venido realizando tradicionalmente de forma manual, bien por métodos gráficos de triangulación, utilizando plantillas flexibles, etc. Los errores de precisión añadidos por la diferencia de espesor del trazado manual se suman a los debidos al redondeo de decimales, etc. y a la hora de su lectura por medio del copiador óptico de la máquina de corte, se traducen en una dificultad añadida para conseguir las tolerancias dimensionales requeridas, aún cuando éstas sean amplias (del orden de ± 1 ó 2 mm).
Para la clasificación de los desarrollos usualmente empleados en calderería, suelen considerarse una serie de elementos, agrupados por su forma:
- Cilindros
- Conos
- Codos
- Pantalones
- Tolvas
- Transformadores
De igual forma debe resolverse el desarrollo de todo de intersecciones, cilindro-cilindro, cilindro-cono, cilindro-codo, cono-codo, etc.
Los parámetros de definición de cada uno de los elementos varía, incluso dentro del mismo grupo de clasificación. Entre estos parámetros de definición se encuentra el número de divisiones deseadas por el usuario para obtener el desarrollo de las zonas no planas. En base a este número de divisiones, obtendremos en el desarrollo una mayor o menor precisión en las líneas del contorno que definirán la pieza en 3D. Un elevado número de divisiones puede provocar un programa CN excesivamente largo (cada división generará una línea) y, dependiendo del proceso y del material, esta precisión puede no ser factible (debido a una sangría demasiado grande, etc).
Asimismo, en el dibujo del desarrollo se deben incluir las posibles líneas de soldadura, con el fin de posibilitar la división de la pieza en dos o más partes cuando el tamaño del desarrollo completo exceda al de la chapa base. Las líneas de soldadura se han hecho coincidir, bien con las generatrices de menor longitud de cada desarrollo, o con líneas perpendiculares al borde de la pieza. De esta forma, se consigue que los cordones de soldadura sean lo más reducidos posibles, permitiendo un ahorro en el tiempo, o facilitando su montaje posterior.
En el caso de elementos simétricos, se debe contemplar la posibilidad de obtener sólo una de las partes de su desarrollo. El desarrollo completo se puede construir utilizando las herramientas del programa base CAD/CAM.
4.4. Problemática en la generación de trayectorias
Los requerimientos expuestos por las empresas a la hora de proceder a generar la trayectorias sobre una pieza (dibujo) se pueden agrupar en varios apartados según el proceso de corte considerado, según el espesor de la chapa implicada, según el tipo de CN (postprocesador) y su capacidad de memoria, etc. El estudio de la problemática en función del espesor de la chapa como parámetro más significativo, fue la elegida para estructurar el presente apartado, dada su mayor relevancia frente al resto de factores.
4.4.1. Problemática en pequeños espesores
El corte de chapa de pequeño espesor, menor de 3 mm, suele requerir mejores acabados. Implícitamente, éstos pequeños espesores llevan asociado una zona afectada térmicamente también menor, y si el sistema utilizado es el corte por agua o por láser nos podemos situar en el orden del milímetro o las décimas de milímetro con facilidad y con un buen control de los parámetros de corte. En el oxicorte o en el plasma podemos llegar a ZAT de 2 o 3 milímetros. Pero incluso así, puede haber piezas de chapa que requieran mejores acabados, no sólo en cuanto a la zona térmica sino también en cuanto a la rugosidad de la superficie de los bordes. Un buen acabado de las piezas (dado un material y espesor), que no exija posteriores operaciones de desbarbado, debe ser controlado por los parámetros tecnológicos propios del proceso (presión de O2, velocidades, etc.), pero no se debe olvidar que la forma de realizar las trayectorias de corte van a seguir jugando un papel muy importante. Sobre todo en dos zonas de la pieza:
- En las esquinas angulosas (con ángulo exterior >= 90º), donde la herramienta o soplete pase por velocidad nula
- En las zonas o puntos de Entrada/Salida (E/S) del corte del perfil de la pieza.
En las esquinas pronunciadas se debe disminuir la potencia, bien programándola en el postprocesado (láser) o controlando manualmente la presión del gas (oxicorte o plasma), para que la zona cercana a la esquina no resulte "dañada" o fundida. Sin embargo a menudo esta reducción de energía no es suficiente y requiere una importante experiencia del programador o del operador en los aspectos tecnológicos del proceso, por lo que se recurre a una solución consistente en generar "bucles de seguridad". Estos bucles se utilizan tanto en chapa delgada como de medio espesor (entre 3 y 4.76 mm), con la finalidad de mejorar el acabado en éstas zonas e incluso para poder conseguir el perfil real de la pieza.
Los bucles se obtienen modificando la trayectoria previamente generada (arco), de forma que se sustituye ésta por un lazo (triangular o circular) que sale y entra en forma tangencial con respecto al perfil (figura 11). Se evita de esta forma que la velocidad de desplazamiento del soplete se haga nula (o disminuya) en las zonas cercanas a las esquinas pronunciadas del perfil real, trasladando los cambios de velocidad y dirección a zonas alejadas del perfil.
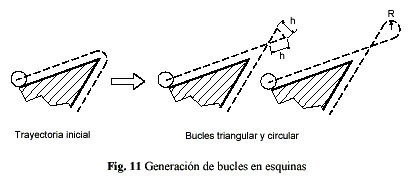
Respecto a las zonas donde se produce la E/S del corte, la forma en que ésta se realice, determinará el acabado. Así por ejemplo, la entrada perpendicular y salida perpendicular al perfil, suelen originar un "pico" o muesca indeseable sobre la pieza y, dependiendo del proceso, esta muesca puede llegar a tener un tamaño inaceptable. Cuando se programa una E/S con un cierto ángulo, se disminuye la muesca, y se puede llegar a eliminar por completo si se adopta una E/S tangencial al perfil o se provoca un solapamiento (pequeña zona por la que se pasa dos veces). Siempre que el perfil disponga de una esquina formada por tramos rectos se puede iniciar el corte en esa esquina de forma que no exista ninguna muesca en el resto del perfil. Todos estos aspectos se pueden observar en la figura 12.
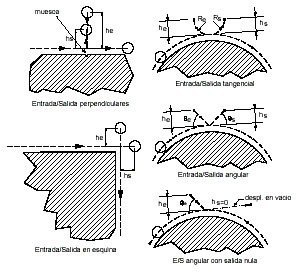
Fig. 12.- Programación de distintos tipos de entradas y salidas sobre un perfil
Por lo tanto, a la hora de programar la trayectoria, se debe contemplar la posibilidad de realizar distintos tipos de entradas y salidas al perfil. Los tipos preferidos por los usuarios son las entradas y salidas tangenciales (buen acabado) y las entradas y salidas angulares (esta última permite la entrada cuando el control no disponga de entrada al corte por medio de un tramo curvo con compensación). Es importante también poder programar distancias de salida nulas (figura 12), para evitar el reflujo de los gases (que daña la parte inferior de la chapa) al llegar el soplete a una zona que no tiene material (cuando se concluya el corte cerrando el perfil). Esta opción de distancia de salida nula es utilizada en grandes espesores. También debe contemplarse la posibilidad de generar un solapamiento de la entrada y la salida que asegura además el desprendimiento total de la pieza.
La generación de las trayectorias de corte debe posibilitar la creación de "puentes" entre piezas con la finalidad de que los perfiles así cortados no se desprendan prematuramente de la chapa base e incluso que permanezcan unidos una vez cortada toda la chapa. Una solución de este tipo suele ser muy recomendable en el corte por láser de pequeños espesores, evitando que la herramienta pueda colisionar con alguna pieza "ladeada" sobre la chapa, sobre todo cuando no se dispone de sensores de interferencias (control de la distancia boquilla-chapa).
En la figura 13 pueden observarse los dos tipos de puentes mas utilizados: puentes exteriores, generados entre piezas para mantenerlas unidas entre sí; y puentes interiores, dejando pequeñas zonas del contorno sin cortar. Los puentes interiores disminuyen además la pérdida de rigidez que producen los sucesivos cortes cuando la chapa es muy delgada (< 2 mm).

Fig. 13.- Programación de puentes interiores y exteriores
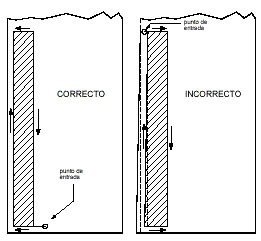
Fig. 14.- Correcta elección del punto de entrada y del sentido de recorrido para evitar distorsiones en la chapa
Un último aspecto que debe ser tenido en cuenta, causado por la fragilidad de la chapa que se acentúa a medida que transcurre el corte, atañe también a chapas de medio espesor (hasta 5 o 6 mm). Las trayectorias deben tener el sentido de recorrido de la pieza de tal forma que la parte donde queda el borde inservible de la chapa, zona más débil, se corte en último lugar. Este efecto (figura 14), puede provocar alabeos y deformaciones en las piezas finales. Se ha considerado dentro del apartado siguiente puesto que también se produce en chapas de medio espesor y además se prefiere el agrupamiento de las figuras en función de la problemática. En este caso la solución vendrá dada por la posibilidad del cambio del sentido de recorrido.
4.4.2. Problemática en medios y grandes espesores
Cuando se trabaja con chapa en medios y grandes espesores (> 4.76 mm), el coste del material se incrementa sustancialmente. Esto obliga a ser todavía mas cuidadoso debido al riesgo que supone cualquier desperdicio de material. Como se desprende de los aspectos tecnológicos vistos hasta el momento, sólo el oxicorte y el plasma (aunque también recientemente el corte por agua) permiten el corte de grandes espesores. Los problemas de pérdida de rigidez o movimiento de las piezas sobre la chapa base ya no tienen sentido en este caso, pero siguen siendo válidas las necesidades de programación de diferentes tipos de E/S al corte de las piezas, sobre todo para eliminar la salida (apagando el soplete justo al terminar el perfil) impidiendo daños por reflujo de gases.
También debe contemplarse la posibilidad de realizar salidas programadas fuera del perfil que vayan hasta el borde exterior de la chapa. Esta trayectoria tiene la finalidad de facilitar (incluso permitir en algunos casos) la extracción de la pieza una vez cortada. En este caso, el problema se presenta cuando se corta chapa muy gruesa (espesores del orden de 200 mm o más), puesto que el perfil transversal de corte en este rango de espesores resulta ser cónico y en consecuencia impide la posterior extracción de la pieza. En la figura 15 pueden observarse como deberían programarse 3 salidas diferentes para facilitar la extracción de la pieza.
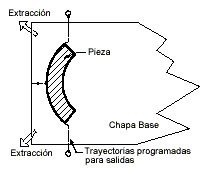
Fig. 15.- Trayectorias de corte para extraer la pieza
Otro aspecto que se presenta durante el corte de chapas de grandes espesores, en este caso por encima de los 60 mm, es la necesidad de elevada presión del gas en el soplete (> 6 bar). Esta alta presión, necesaria para el corte, produce una elevada cantidad de chispas con desprendimientos fundidos del material en la zona donde el chorro incide sobre la chapa que queda por cortar. Si este chorro de chispas se dirige contra el operario, impedirá su visibilidad y no podrá realizar una inspección "in situ", lo que a veces resulta muy necesario (por ejemplo, cuando se realiza un control manual de la velocidad de avance en las entradas o en perfiles complicados).
Razones adicionales para controlar el sentido de recorrido residen en que la parte sobrante debe quedar, durante el mayor recorrido posible, del lado donde hay más material. Si fuera preciso se cambiará el punto de entrada, en concordancia con dicho sentido (figura 16). Esto, junto con la elección de dicho sentido de acuerdo con la calidad del corte, de forma que la superficie de corte más perpendicular quede del lado donde está la pieza, (figura 13), evitará innecesarias distorsiones debidas al calentamiento, a falta de rigidez (en chapa de medio espesor, de 3 a 5 mm), etc., que producirán unas dimensiones inadecuadas. Por tanto, el programa de generación de trayectorias de corte deberá permitir el cambio del sentido de recorrido del perfil de la pieza cuando sea necesario (figura 14 y 16).
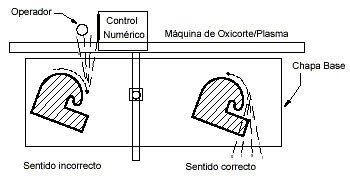
Fig. 16.- Cambio del sentido de recorrido para permitir inspección del trabajo
También en grandes espesores, es necesario efectuar no sólo un precalentamiento de la chapa base sino también unas perforaciones previas con el soplete en los puntos previstos de entrada de corte (trayectorias intermedias entre desplazamientos en vacío y en corte), permitiendo la posterior entrada al perfil del chorro de corte en condiciones óptimas. La generación de las trayectorias de corte deberá contemplar por tanto, la posibilidad no sólo de programar esas perforaciones previas (zonas de entrada), sino la de evitar las zonas próximas a dichas perforaciones, que son zonas muy difíciles de cortar por haberse endurecido por temple (figura 17 y 18).
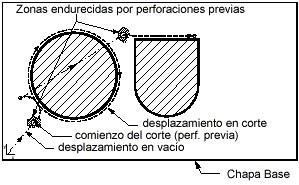
Fig. 17.- Programación de trayectorias con inicio del corte sobre taladros previos
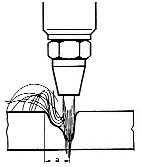
Fig. 18.- Detalle de la zona de entrada al corte en
medios y grandes espesores. La distancia “a” se
produce en el sentido de la trayectoria y está en
concordancia con el espesor.
medios y grandes espesores. La distancia “a” se
produce en el sentido de la trayectoria y está en
concordancia con el espesor.
La necesidad de aprovechamiento de material se hace mas patente en espesores medios y grandes. Podemos encontrar un buen ejemplo de ello en la posibilidad de generar piezas adosadas o con un lado común. Por ello, bien sobre un mismo programa de CN o bien sobre todas las piezas que forman parte de una chapa base, se generan algunas trayectorias con una compensación de herramienta determinada (por ejemplo, izquierda) y otras trayectorias con otra compensación (por ejemplo, derecha o con compensación nula).
Esta particularidad de cambio de compensación de herramienta dentro del mismo programa CN, no suele aparecer en los programas CAD/CAM de tipo comercial empleados en el corte de chapa. En cambio, su inclusión permitiría por ejemplo, cortar piezas adosadas (con un lado común), con el consiguiente ahorro de material, tiempo y coste asociado al corte (figura 19).
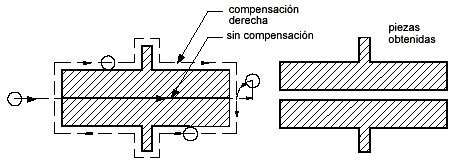
Fig. 19.- Trayectorias para el corte de piezas adosadas
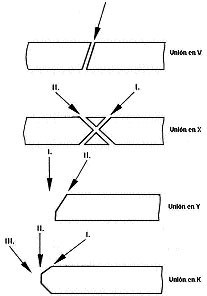
Fig. 20.- Preparación de chaflanes o juntas para soldadura
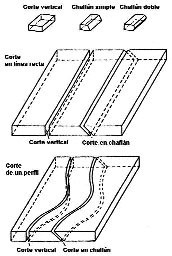
Fig. 21.- Perfiles resultantes preparados para soldadura
Cuando se procede a preparar la chapa para el montaje y posterior soldadura, se disponen cabezales de corte con sopletes girados, pudiendo también montarse dispositivos con sopletes dobles o triples. La programación del orden de encendido (I ,II y III en la figura 20) y la zona donde comienza y termina el chaflán, ya sea chaflán simple (unión en V), doble (unión en X o en Y), o triple (unión en K), debe tenerse en cuenta a la hora de la generación de trayectorias, de forma que el postprocesado pueda reconocer las líneas sobre las que debe aplicar el/los chaflanes. Esto permite dejar la pieza preparada para cualquier tipo de soldadura, tanto en perfiles curvos como rectos (figura 21).
4.5. Problemática en la programación. Controles numéricos y postprocesadores
Aparte de los problemas ya mencionados, existe otra problemática asociada a la chapa que es prácticamente independiente del espesor. Estos problemas son debidos al propio proceso y afectan a la forma de programación, al posicionamiento de la chapa, a las particularidades del CN y del postprocesador, etc.
A este respecto cabe citar que los bordes de la chapa no suelen formar parte de las piezas, debido a su oxidación y al mal acabado que presentan. En algunos casos como en el oxicorte, esta exigencia se acentúa aun más debido al reflujo de gases, sobre la parte inferior de la chapa, al entrar a cortar el material. En chapa de poco espesor, se puede entrar a cortar el material desde el exterior, pero la zona adyacente, de unos 5 o 10 mm de "margen", no puede pertenecer a la pieza (distancias Xmin e Ymin en la figura 22). Se prefiere incluso entrar a cortar desde el interior de la chapa, dando por perdida esa pequeña zona de margen.
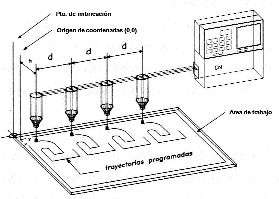
Fig. 22.- Puntos significativos para programación CN
El posicionamiento de la chapa base con respecto a la mesa (punto de imbricación), el origen de coordenadas (0,0) y del programa (situación inicial del soplete) deben ser controlados perfectamente por el sistema. El operario debe tener conocimiento de todos estos aspectos y si es posible, trabajar conjuntamente con el programador a la hora de prefijarlos.
En este mismo sentido, las funciones iniciales del programa que se encarguen de estas tareas, deben posibilitar una total movilidad de la chapa, por medio del punto de imbricación (vértice inferior-izquierdo de la chapa), al cual se referirá el origen de coordenadas (0,0 del programa CAD/CAM) y el origen de programa (0,0 del CN).
La finalidad de la modificación a voluntad de la distancia del origen de coordenadas al vértice de la chapa, estriba no sólo en conocer exactamente donde debe posicionarse el soplete al reiniciar de nuevo el corte tras una parada forzosa (virutas o elementos extraños en las guías, etc.) que en caso contrario ocasionaría el estropicio de la chapa, sino también porque usualmente este punto origen de coordenadas sirve para la toma de referencia en el caso del empleo de sopletes solidarios, midiéndose sobre él las distancias a las cuales se posicionarán las demás boquillas (figura 22). El programa desarrollado calcula automáticamente el punto que servirá como origen de coordenadas (situando en la intersección de las tangentes horizontal y vertical a las piezas más exteriores) y posiciona el punto de imbricación de la chapa a la distancia de seguridad (Xmin, Ymin). De esta forma, ningún perfil se aproxima más de lo permitido al borde de la chapa.
Antes del proceso de generación de trayectorias, el usuario debe disponer de funciones específicas para el correcto posicionado (manual o automático) de los perfiles de la/s pieza/s sobre la chapa base, que junto con la posibilidad de situar y/o modificar el punto de imbricación de la chapa sobre el dibujo, nos llevarán a la correcta selección del origen de programa y demás puntos significativos.
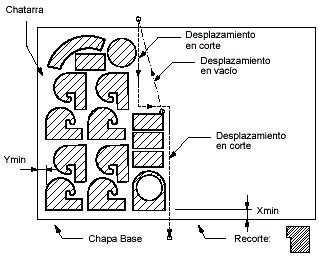
Fig. 23.- Distancias de seguridad al borde de la chapa y trayectoria de salida para obtener un recorte
También resulta interesante contar con la posibilidad de realizar trayectorias de corte que no exijan ninguna geometría previa dibujada. Esta opción tiene múltiples aplicaciones, la más usual consiste en poder incluir, en el mismo programa CN, una última trayectoria de corte destinada a generar un determinado recorte sobrante de la chapa base (figura 23) con una forma generalmente rectangular, que facilite su posterior almacenamiento y reaprovechamiento.