Corte con chorro de agua
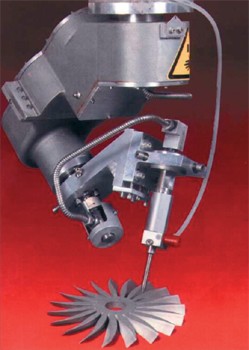
Tipos de bombas
A pesar de que las bombas tipo intensificador son las de mayor implantación dentro de los usuarios de esta tecnología, Flow desarrolló a principios de los años 80 unas bombas de accionamiento directo, de reducido tamaño, capaces de elevar la presión del agua a unos niveles que estaban muy por encima de lo que se estaba acostumbrado con este tipo de bombas. Esto se consiguió utilizando materiales tecnológicamente muy avanzados. El gran desarrollo de este tipo de bombas por parte de Flow, ha conseguido que actualmente se hayan convertido en la segunda alternativa en bomba de alta presión de la compañía, ya que se pueden alcanzar presiones de 3.800 bar con una eficiencia del entorno del 95%. Esto las convierte en unas bombas de bajo consumo y menor coste de mantenimiento, es decir, bajo coste de operación.
En el caso de las bombas tipo Intensificador, Flow también ha sido pionera en su desarrollo, comenzando su implantación a principios de los años 70 y continuando hasta nuestros días con más de 7.600 sistemas funcionando en todo el mundo. La bomba tipo intensificador genera la presión a través de una bomba de aceite. Esta presión es enviada a un intensificador (multiplicador de presión) que transforma, por efecto Pascal, la presión de aceite en presión de agua. En este tipo de bombas, Flow es la única que ha conseguido superar la barrera de los 4.100 bar de presión. Cuanto más elevada es la presión, mejores son los acabados que se consiguen, y mayor velocidad de corte.
La dedicación de Flow al avance de esta tecnología se constata con una inversión del 6 al 9% de su facturación anual en investigación y desarrollo. De ahí el reciente lanzamiento de una nueva bomba de hiper alta presión capaz de trabajar continuamente a 6000 bar.
La formación del haz de agua en el cabezal de corte
Este haz de agua es capaz de cortar una gran variedad de materiales. Los materiales blandos como las gomas, espumas, compuestos para las juntas de automoción, fibras de pañales e incluso los alimentos se pueden cortar solamente con agua a alta presión. En este caso solo utilizamos la energía cinética del agua para producir el corte.
Si además le añadimos granate como elemento abrasivo al haz de agua se pueden cortar todo tipo de materiales duros tales como metales, piel natural, mármol, cristal, o materiales reforzados con fibras. En este proceso el agua acelera las partículas del abrasivo para producir el corte dejando un aspecto satinado en su perfil.
Una vez generada esta presión, es transmitida a través de los conductos de alta presión hasta la cabeza de corte. En este punto, la energía de presión se transforma en energía cinética al atravesar un orificio de un tamaño aproximado de 0,3 mm. El chorro generado, que viaja a tres veces la velocidad del sonido, pasa a través de la cámara de mezcla, en la que se produce el efecto venturi para absorber el abrasivo y mezclarlo con el haz de agua. A partir de este punto, el chorro de agua y abrasivo pasa a través del tubo de mezcla, y acaba impactando contra el material a cortar.
El principio de los procesos de corte con agua pura, y de corte con agua y abrasivo es el mismo. La única diferencia, es que en este último se añade abrasivo en la parte inferior, para acelerar sus partículas contra el material. En este caso es necesario hacer llegar el abrasivo hasta el cabezal. Esto se consigue a través de diferentes sistemas, el más avanzado consiste en una tolva del entorno de los 200 kg de capacidad en la que se deposita el abrasivo. Esta está comunicada con un deposito presurizado, que es el responsable de enviar el abrasivo hasta la cabeza de corte. En ese punto se encuentra un dosificador de abrasivo que garantiza el aporte optimo por unidad de tiempo al cabezal.
Una herramienta muy útil patentada por Flow para el cabezal de corte, es lo que se denomina "sistema de asistencia de vacío en perforación Paser 3". Este sistema permite asegurar un proceso de perforación seguro y consistente, incluso en materiales muy frágiles como el cristal, la piedra o la cerámica. Así se evita la necesidad de pretaladrar mecánicamente las piezas.
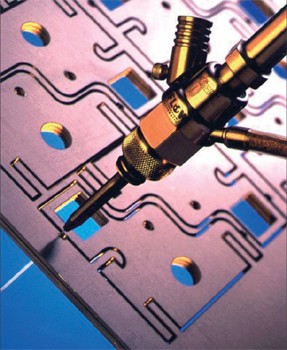
Corte de distintos materiales
Aunque los espesores de corte más comunes en esta tecnología oscilan entre los 0,5mm y los 120mm para materiales duros, en ocasiones los usuarios de corte con agua y abrasivo llegan a cortar hasta 350 mm de materiales como el acero inoxidable. En el corte de espesores reducidos, esta tecnología permite la colocación de varias capas una encima de otra para cortarlas a la vez manteniendo las calidades de corte con cierta homogeneidad, aumentando así en gran medida la productividad del proceso.
A pesar de que esta tecnología puede cortar todo tipo de materiales, hay algunos que por sus características intrínsecas son especialmente agradecidos a este tipo de corte. Por ejemplo el aluminio, acero inoxidable, latón, cobre, piedra, cerámica, entre otros.
La principal característica de esta técnica es que estamos ante un corte frío que no deforma el material, en el que las zonas de corte no quedan térmicamente afectadas. Esto permite obtener piezas terminadas, con muy buen nivel de acabado y facilita enormemente la realización de operaciones de mecanizado posteriores si fuera necesario. En el 90% de los casos las piezas cortadas por agua pueden tomarse como piezas terminadas. Cortando a menor velocidad es posible obtener una pieza totalmente terminada que no requiere mecanizado posterior. Es posible también aumentar la velocidad a cambio de obtener un peor acabado.
Para corte de vidrio y materiales frágiles se dispone de un sistema denominado "Asistencia de vacío en perforación", que evita que el material se rompa cuando el agua impacta sobre el mismo, pues tiene tendencia a romperse. Con un proceso en el que se hace circular el abrasivo dentro de la cabeza de corte antes de que pase el agua, se consigue que el agua llegue con abrasivo, por lo tanto erosiona el material y no deteriora la perforación.
Así pues, la posibilidad de cortar materiales es espectacular. Casi todos los materiales de la naturaleza pueden ser cortados con esta tecnología, tanto con agua como con agua con abrasivo.
A continuación se muestra una tabla orientativa de velocidades de corte con una máquina Flow de última generación. Las velocidades se muestran en un margen muy amplio, que determina el acabado de la pieza. La velocidad más alta en cada material, determina la velocidad límite de separación del mismo, y la más lenta es la velocidad a la que se consigue el mejor acabado para ese material y espesor:
Cabeza de corte de tres dimensiones
Estas máquinas tienen aplicaciones especialmente en el mundo del automóvil y en el aeroespacial, y los materiales que se cortan con este sistema son el titanio, aluminio y fibras de carbono, entre otros.
También tiene aplicaciones en el corte de papel y en el corte de juntas, donde se utiliza una máquina con 5 cabezales de corte.
El futuro de la tecnología de corte con chorro de agua
El análisis de estos factores ha llevado a buscar los aspectos tecnológicos que permitan rebatir y mejorar esas situaciones. Gran parte de ello ya está conseguido, habiéndose aportado soluciones radicales a esos problemas.
Por ejemplo, con el corte dinámico, presentado por primera vez en el país en Maquitec 2002, se obtiene la capacidad de producir totalmente piezas acabadas sin ningún tipo de conicidad en la superficie de corte, además de conseguir una precisión muchísimo mayor de la que hasta ahora se podía alcanzar con las máquinas convencionales. En el futuro se podrán producir piezas en el entorno de las centésimas de mm en ausencia de cono y, si por otro lado la precisión obtenida en la actualidad fuera suficiente, se podría cortar de 2 a 3 veces más deprisa que hasta ahora. Con esta tecnología se ganará bien en calidad o precisión, bien en velocidad de proceso.
Durante más de 20 años los sistemas de corte con agua han probado su amplio espectro de aplicaciones. Sin embargo, hasta este momento siempre ha existido un límite insuperable: cuanto más rápida fuera la velocidad de corte más se retrazaba el haz y, por tanto, se hacían patentes más defectos en la superficie de corte. En su recorrido de arriba abajo, el haz se abre de forma cónica o en forma de V, y en las esquinas de las piezas este retraso del haz puede significar un daño importante a su geometría.
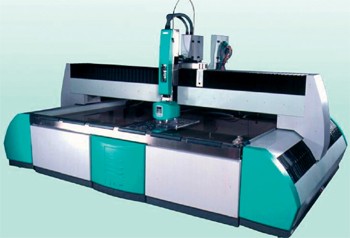
La clave de este nuevo proceso es un conjunto de complicados modelos matemáticos, distintas variables con la deflexión del haz de luz y la relación entre su punto de entrada y de salida.
Para trabajar con esta tecnología basta con que el operador introduzca el tipo de material, su espesor y la calidad deseada en el corte. Un sistema cinemático muy avanzado gestiona el camino optimo de corte calculado por los modelos matemáticos.
La conicidad queda virtualmente eliminada; incluso a alta velocidad se pueden conseguir esquinas y arcos perfectos.
El corte comparativo de piezas idénticas muestra cómo con la tecnología de corte dinámico la tolerancia y conicidad de las piezas es inmensamente menor, siendo los tiempos de ciclo idénticos. Si, por el contrario, se mantiene una tolerancia y calidad equivalente, el corte dinámico reduce drásticamente el tiempo de ciclo. Velocidad y precisión al mismo tiempo: ahora es posible conseguir ambas para cualquier figura en cualquier material y espesor.
El otro aspecto importante de futuro es la presión de corte, en tanto en cuanto, la mayor energía disponible para el corte contribuirá al aumento en la velocidad del mismo.
Hoy en día ya están disponibles equipos que operan a 5.000 bar, y en poco tiempo se dispondrá de equipos que proporcionarán de manera continuada y con cierta confianza 6.000 bar. Por tanto, la energía va ser muchísimo mayor y se podrán cortar bien materiales de espesor mucho mayor, o bien materiales con muchísimo menos aporte de abrasivo que, en definitiva, es lo que dificulta esta tecnología o la hace costosa.
Actualmente, a 6000 bar se pueden cortar planchas finas de metal sin abrasivo con sólo la energía desarrollada por el agua. Estas son las dos facetas que realmente marcan el futuro inmediato de la tecnología de corte de agua y las que, de alguna manera, abren una competencia directa con los métodos tradicionales térmicos como pueden ser el láser, el plasma de alta definición, el oxicorte e incluso, en el área de precisión, con la electro-erosión por hilo.
Como resumen final las características más destacadas y diferenciadoras del corte con agua son:
- Al no ser un método de tipo térmico no produce deformaciones, no altera las propiedades del material y por tanto no necesita operaciones de acabado posterior, por lo que a un relativo bajo coste se obtiene una buena calidad de acabado.
- Puede cortar todo tipo de materiales y espesores (flexibilidad del proceso)
- El aprovechamiento de material y la productividad que ocasiona
- No es contaminante, respetuoso con el medio ambiente.
- Amplia capacidad de desarrollo futuro