Ursa trabaja en la estrategia de descarbonización de sus soluciones con cada vez mayor porcentaje de material reciclado en su composición
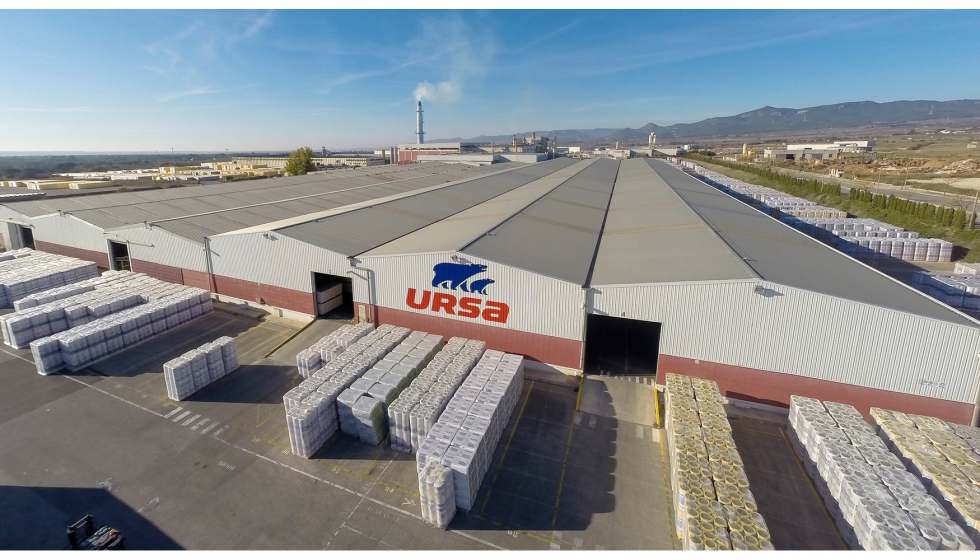
Tener una estrategia de descarbonización claramente definida para cada uno de sus materiales es una de las principales líneas de trabajo actuales de Ursa. La compañía está centrando gran parte de los esfuerzos de su departamento de I+D+i en el cierre del ciclo de vida de sus materiales.
Con motivo de la celebración del Día Mundial del Reciclaje, celebrado el 17 de mayo, Ursa ha compartido un vídeo documental en el que se muestra el trabajo realizado en sus plantas de fabricación para contar con cada vez un mayor contenido de material reciclado en la composición de los productos aislantes que fabrica.
En el día en el que se conmemoran los importantes avances realizados por la industria y se recuerda el largo camino que falta por recorrer, se ha conocido que prácticamente la mitad de los materiales extraídos en el mundo a día de hoy, son empleados en el sector de la construcción, responsable del más del 30% de las emisiones de CO2 de todo el planeta, porcentaje que podría aumentar a casi el 50% para 2050, según datos de la Fundación Ellen MacArthur en colaboración con Material Economics.
Con el título, ´Las tres R de Ursa: Reducir, Reutilizar y Reciclar´, el documental muestra la segunda vida que están teniendo muchos productos tras ser utilizados en la fabricación de los materiales de aislamiento de la compañía. La realidad es que Los materiales aislantes de Ursa ya cuentan con hasta un 85% de material reciclado en su composición.
En el caso del poliestireno extruido (Ursa XPS) producido en la fábrica del Pla de Santa María (Tarragona) se ha conseguido aprovechar totalmente las mermas y recortes de su propia fabricación y dar un segundo uso a muchos materiales de otras industrias que tendrán una larga vida proporcionando confort a los habitantes de los edificios.
Isaac Arrastia, jefe de Producción de Ursa XPS, afirma que “tenemos una media de utilización de material reciclado para fabricar nuestro XPS de entre un 70 y un 80%, pero hay muchísimos días en los que llegamos al 100%. Conseguimos que no se deseche nada e incluso el recorte de nuestro propio material vuelve a introducirse en el proceso”.
Porcentajes similares de material reciclado se incluyen en la fabricación de la lana mineral de vidrio que Ursa produce en la otra fábrica del Pla de Santa María. La lana mineral de Ursa, es un recurso natural que se obtiene originalmente de la sílice, pero la compañía ha hecho un gran esfuerzo para sustituir la materia prima primaria por material reciclado como el vidrio procedente de la industria automovilística. El responsable de Calidad de la fábrica de lana mineral de Ursa, Pedro Uriz, explica que el vidrio reciclado es completamente compatible con el resto de materias primas utilizadas: “en el interior del horno, que llega a temperaturas superiores de 1.200 grados centígrados, la materia prima original y el material reciclado se funden hasta conseguir una masa de vidrio fundido homogénea. Ambos componentes aportan las propiedades necesarias al vidrio para la producción óptima de la lana mineral dándonos un producto ganador a nivel ambiental”.
Gracias a esta apuesta de Ursa se da cumplimiento a la regla de las 3R (Reduce, Reutiliza y Recicla). El objetivo es dar respuesta a los Objetivos de Desarrollo Sostenible que reclaman una energía asequible y menos contaminante; innovación; ciudades y comunidades sostenibles y producción y consumo responsable.