Entrevista a Judit Jansana, jefa técnico comercial para Iberia y Latinoamérica de Titech
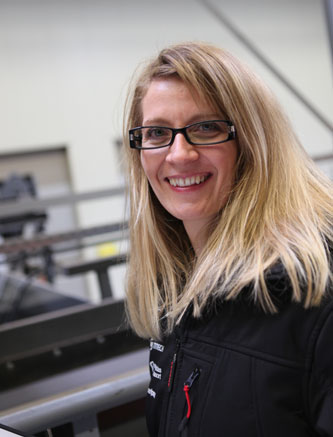
Hábleme de la Directiva 2012/19/UE sobre residuos de aparatos eléctricos y electrónicos (RAEE). ¿Qué retos traerá consigo?
Esta directiva, aprobada el pasado mes de enero de 2012 por el Parlamento Europeo, introduce objetivos más estrictos de recogida y reciclaje de los residuos de aparatos eléctricos y electrónicos.
¿Por ejemplo?
Exige la recogida de 45 toneladas de RAEE por cada 100 toneladas de aparatos puestos en el mercado nacional para 2016. Este porcentaje deberá aumentarse en 2019 hasta el 65% de los RAEE introducidos en el mercado o el 85% de los RAEE generados en el país. Además, se incrementan las cuotas de reciclado para cada categoría. Se establece también la prohibición del reciclaje de plásticos con retardantes a la llama con base de Bromo y se regula que todos los plásticos de RAEE deben ser tratados para la separación de dichos retardantes. Los Estados miembro disponen de un año más para transponer estas reglas, lo que supone todo un reto para países como España.
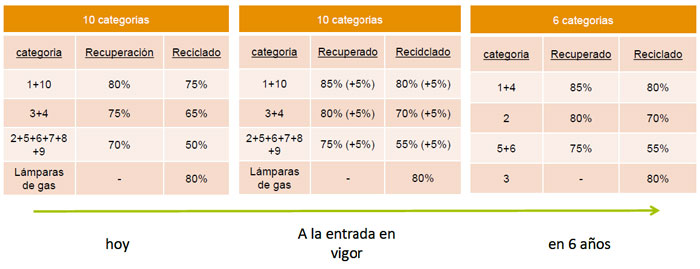
¿Está preparado nuestro país para afrontar con garantías las exigencias de la directiva?
Creo que sería justo decir que la nueva directiva presenta un reto importante para las plantas que están funcionando actualmente en nuestro país. Será necesario revisar el concepto tradicional de planta, en el que muchos procesos se realizan de forma mecánica o manual, y sustituirlo por la tecnología actual de clasificación por sensores. Esta nueva tecnología permite optimizar el proceso de recuperación de metales y obtener valiosos subproductos metálicos. Además, permite distinguir, clasificar y recuperar las distintas fracciones poliméricas con y sin retardantes de bromo, así como llevar a cabo un adecuado tratamiento de la fracción de finos, que cada día es más rica en metales preciosos.
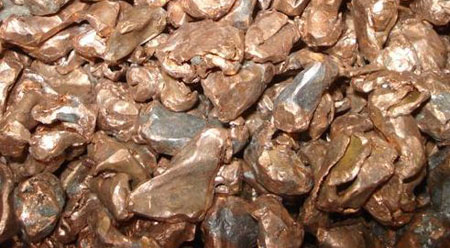
¿Qué deben hacer las plantas parar adaptarse a la citada directiva? ¿Cómo?
Los cables eléctricos de cobre y las piezas de cobre constituyen componentes valiosos que se encuentran en muchas fracciones consideradas a menudo como ‘residuales’ y que manualmente es realmente difícil de trabajar.
En una planta actual de RAEE, con separador de Corrientes de Foucault queda aún mucho metal no férrico, especialmente cables eléctricos y acero inoxidable, pero también placas (PCB), cobre y latón. Podríamos afirmar que, por término medio, una planta tradicional, después de este proceso aún tiene entre un 10% a un 15% de metales que se podrían recuperar y vender.
¿Y qué se puede hacer para incrementar las cuotas de reciclado?
Se debería trabajar en dos líneas. En primer lugar, maximizando la recuperación de estos metales, especialmente los no férricos todavía existentes en los flujos de rechazo. El problema es que una identificación y separación eficiente de estos metales no es posible con la tecnología de clasificación convencional. Así por ejemplo, tanto los recuperadores de cables como las posteriores fundiciones de cobre exigen un elevado grado de pureza. Esto sólo puede conseguirse eficazmente utilizando los nuevos sistemas de clasificación basados en sensores como los que ofrece Titech.
¿Y en segundo lugar?
Hay que llevar a cabo la recuperación y venta de nuevos subproductos: los plásticos y los finos. Esto incluye la separación de polímeros en sus distintas familias, así como la separación de fracciones metálicas entre sí: cables eléctricos, cobre, latón o placas de circuito eléctrico.
Valore el grado de equipamiento y tecnología de nuestras plantas en la actualidad para afrontar el reto.
En general, se observa una extendida tendencia a la operación manual de las plantas españolas, más allá de las operaciones de descontaminación que deben realizarse de esta forma por su complejidad. Esto hace que tengan altos costes operativos asociados a una baja capacidad y a una limitación del número de subproductos a generar. Diría que existen muy pocas grandes instalaciones con un mayor grado de automatización de sus procesos. Esto indica que aún nos queda mucho recorrido por hacer. La nueva directiva ayudará a dar ese salto tecnológico que permita aumentar la eficiencia de los procesos de recuperación.
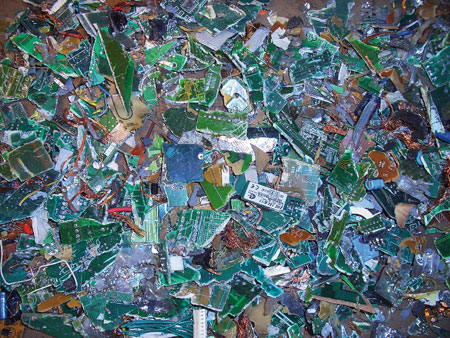
¿Qué componentes de los RAEE son considerados nocivos? ¿Por qué? ¿Cómo se tratan?
Los aparatos eléctricos y electrónicos contienen sustancias que pueden causar graves daños al medio ambiente y a la salud. Hay que tener en cuenta que en el mundo se generan 40 millones de toneladas de basura electrónica al año y que el volumen de esta chatarra crece entre el 16 y el 28% cada cinco años (el triple que los RSU). La inmensa mayoría contiene sustancias peligrosas tales como el bromo, cadmio, fósforo o mercurio, ya sean, por ejemplo, en las pilas y baterías que contienen o en los plásticos con retardantes a la llama.
La Directiva RoHS (Restriction of the Use of Certain Hazardous Substances) ha establecido restricciones al uso de materia prima secundaria que contenga alguna de las siguientes sustancias peligrosas que deben ser separados:
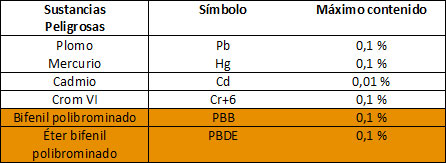
Hay que tener en cuenta, explica Jansana, que la Directiva RoHS únicamente es válida para la fabricación de nuevos aparatos eléctricos y electrónicos. Regula la recuperación y separación de partes peligrosas como placas que contienen condensadores, plásticos con retardantes a la llama y partes con plomo y prohíbe el uso de retardantes a la llama brominados. Su ámbito de aplicación es para todos los aparatos producidos tanto en la Unión Europea como los importados a la UE.
Según explica la jefa técnico comercial para Iberia y Latinoamérica de Titech, uno de los aspectos en los que incide es en la identificación y separación de plásticos que contengan materiales pirorretardantes bromados (BFR), que forman parte de circuitos impresos, carcasas de plástico o conectores y cables. Así, todos los plásticos de RAEE deben ser previamente tratados para la separación de los retardantes a la llama de Bromo del resto de plásticos, un proceso que requiere de nuevas tecnologías, pues muy difícilmente se podrá lograr esta distinción manualmente.
Por ello, sostiene Jansana, la tecnología de sensores mediante rayos X está cada vez más extendida para llevar a cabo esta operación, ya que garantiza “los mejores resultados, al distinguir los materiales por su densidad atómica”. En una instalación diseñada para esta aplicación, combinando un equipo de sensores NIR con otro con sensores de rayos X, es posible recuperar para su eliminación hasta el 97% de los plásticos con BFR, separando primero por tipos de plásticos con el sensor de infrarrojos, para luego separar dentro de cada familia los que tienen Bromo (BFR) de los que no.
¿Cuál es el proceso que debe seguir un RAEE para su total reciclado?
Una planta de recuperación de RAEE debe estar diseñada con una combinación específica de diferente maquinaria. Primero hay que descontaminar el material manualmente. Para ello se utiliza un triturado suave que rompe la carcasas y permite un rápido acceso a su interior por parte de personal de triaje, el cual extrae pilas, condensadores, baterías y tóneres entre otrosmateriales; luego ya puede pasar a una trituración más fina hasta una granulometría de alrededor 20 a 30 milímetros.
¿A partir de ahí?
Se instalan en cascada el separador magnético para la retirada de metales férricos y el separador de Corrientes de Foucault para los metales No férricos muy masivos. Es a partir de este punto donde empieza realmente la innovación tecnológica con el uso de equipos de separación automática basados en sensores: (electromagnéticos (EM3) para la recuperación de todos aquellos metales no recuperados por el Foucault, sobre todo cables eléctricos, placas de circuito impreso más pobres en metales, inoxidables, etc. Una vez agotados los metales en el flujo se empieza la recuperación y clasificación polimérica.
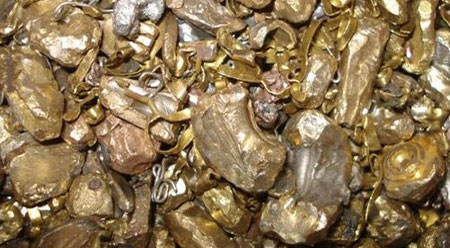
¿Cómo?
Mediante equipos dotados de sensores espectrométricos de cercano infrarrojo o NIR y de equipos de rayos X, para la separación de plásticos con y sin retardantes a la llama brominados. Se puede ir un paso más allá en la recuperación a través del uso de la cámara de color (CCD), con lo que se consiguen crear monofracciones metálicas: de sólo placas, sólo cobre, sólo latón, sólo cables eléctricos, etc. Todo ello sin necesidad de granular ni de emplear mesas densimétricas.
¿Y para aquellos que hayan optado por granular?
También se pueden separar el cobre y el latón del resto de metales mediante el separador con cámara de color de alta resolución. El reto y la dificultad están en el cambio de mentalidad al tener que pasar de un proceso simple y muy manual a uno altamente tecnificado, en el que, por un lado, el personal debe adaptarse a trabajar con las máquinas y, por otro, la empresa debe ampliar su red de ventas de subproductos y adaptar su red comercial a los nuevos productos y calidades. Según las calidades de producto final obtenido incluso se puede realizar una venta directa a las fundiciones.
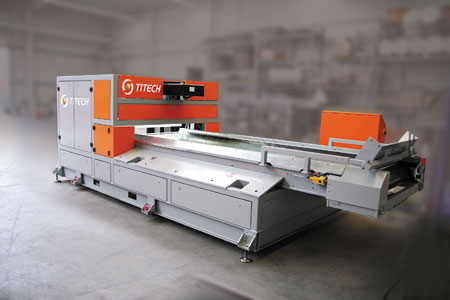
Tecnología Titech
Según explica Judit Jansana, jefa técnico comercial para Iberia y Latinoamérica de Titech, las ventajas de la tecnología basada en sensores son las siguientes:
- Los equipos Titech son muy flexibles, se pueden combinar varios sensores en un mismo separador por lo que es ideal para plantas pequeñas.
- Permiten obtener fracciones de alta calidad incluso aptos para venta directa a fundición.
- Maximizan la recuperación de los metales, fracción más valiosa dentro de los RAEE. Toda la tecnología Titech es en seco por lo que los costes operativos son muy bajos.
- Ayuda al cumplimiento de la nueva directiva con la distinción entre los retardantes bromados de los que no lo son.
- La empresa ayuda a sus clientes a ser más competitivos con menores costes operativos, con máximos beneficios por la venta de subproductos y máxima recuperación.
- Los equipos tienen una configuración modular y una integración simple en plantas ya existentes.
- Titech ofrece una amplia gama de equipos con distintos anchos de trabajo para trabajar con altos o bajos caudales
- El periodo de amortización para las máquinas es corto, gracias a los elevados precios de venta de los subproductos obtenidos.