Automatización de la planta de Sal Nylon en Gerona
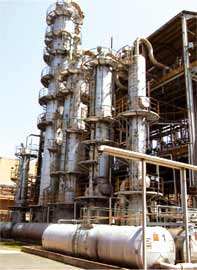
Su capacidad de adaptación a las necesidades y demandas del mercado, así como la filosofía de automatización de sus plantas química y textil para la fabricación de polímeros e hilos de PA66 con costes muy reducidos, la posiciona como líder en Europa y la segunda en el mundo. Nylstar ha automatizado todas sus instalaciones, tanto en la planta química como en la planta textil, confiando en equipos Omron ya desde los primeros pasos de la automatización de la fábrica.
En el año 2003 se ha sustituido todo el sistema de control –en servicio desde el año 1973– por un sistema basado en PLC Omron, que ha permitido trasladar la supervisión a otra sala de control existente. Esto ha permitido aumentar el nivel de productividad, fiabilidad y seguridad, a la vez que dar un salto cualitativo notable en la vigilancia y seguimiento de la planta. El diseño, montaje y puesta en marcha del proyecto se ha realizado con ingeniería propia.
Proceso de fabricación de polímeros
La otra gran materia prima para la fabricación de la poliamida 6.6 es el Ac.Adípico. Mediante la reacción de salificación entre el Ac.Adípico y el HMD-puro se obtiene la sal nylon al 52 por ciento.
En el siguiente proceso y mediante la utilización de reactores de evaporación se concentra la sal nylon hasta el 85 por ciento. Esta sal se envía a los reactores de polimerización donde en unas condiciones de presión y temperatura adecuadas se obtiene el polímero poliamida 6.6.
La materia fundida a 270ºC se extrusiona en el mismo reactor de polimerización y sale a través de la hilera de la válvula de colada, donde se enfría y corta mediante los granuladores.
La apariencia final del producto es un granulado de 3x2,5x2,5 milímetros de distintas características en función de la aplicación. Este granulado se envía mediante transporte neumático a las hilaturas de la fábrica textil para fabricar hilos de poliamida o a ventas.
Sustitución del sistema de control
La preservación de los niveles de fiabilidad y seguridad han estado presentes en la automatización de la planta adoptando soluciones como:
- Redundancia de equipos SAI para suministro eléctrico al sistema de control.
- Redundancia y conmutación automática de redes de supervisión (sysmac link-ethernet).
- Un PLC para cada columna para minimizar riesgos en situación de avería.
- Controladores discretos en comunicación con los PLC para los lazos críticos de control, evitando así posibles peligros en la planta química, pues se tratan productos corrosivos, y reduciendo el riesgo laboral.
- La automatización ha dado fiabilidad y seguridad a las instalaciones, reduciendo también los costes de fabricación.
En cada una de las seis columnas se ha instalado un autómata CS1H de Omron para que controle su actividad. Asimismo, existen PLC en el proceso de salificación y en los servicios generales. Aunque el funcionamiento del proceso de salificación es independiente de la rectificación, ambos comparten algunos parámetros, por lo que los PLCs que controlan ambos procesos están comunicados en “sysmac link”; si alguna parte del proceso se para, un autómata debe conocerlo para asegurar que el proceso complementario siga funcionando. De la red “device net” conectada al PLC de servicios generales, cuelgan los controladores de temperatura E5EK de Omron para garantizar el funcionamiento de los lazos críticos en caso de un supuesto fallo del PLC. Si este PLC fallase, los lazos críticos seguirían funcionando, con lo cual se garantizaría el restablecimiento de los servicios mínimos del sistema.
Existen cinco lazos críticos que controlan aquellas variables que afectan a todas las columnas: dos circuitos vapor, niveles de depósitos y la temperatura del agua a 45ºC.
Los PLCs que controlan la actividad de las columnas están comunicados mediante la red “sysmac link” de Omron, si bien existe la red “ethernet” como vía de comunicación principal, a través de la cual los PLC se comunican con el scada de la sala de control.
Existe una vigilancia de la red “ethernet” y en caso de fallo se realiza una conmutación automática a “sysmac link”.
El “scada” utilizado es el “intouch”. En el desarrollo del “scada” se ha tenido en cuenta a los operarios que han estado trabajando en fábrica y que estaban habituados al antiguo sistema, por lo que la imagen del sinóptico anterior se reproduce en la pantalla de forma similar para facilitar la adaptación de los operarios a la nueva tecnología aplicada, pero con las ventajas en el seguimiento y control del proceso.
En la pantalla del “scada” se pueden visualizar las alarmas y combinar las distintas variables del sistema en un sólo gráfico para supervisar los lazos de regulación.
Según Joaquím Serrat, jefe de conservación, fluidos e ingeniería de Nylstar en Blanes, “la productividad conseguida tras la automatización del proceso de rectificación ha sido la esperada, hemos conseguido reducir los costes de producción manteniendo e incluso incrementando los niveles de seguridad y el plazo de amortización de la inversión ha sido de un año y medio. Estamos satisfechos: la aplicación ha quedado perfecta, con niveles de seguridad máximos”.