Testimonio de Ralf Hagen, gerente de ingeniería E&A de Nestlé Alemania, y de Thomas Rienessl, director de desarrollo de negocios para la industria en B&R
Se acabaron los tiempos de inactividad no planificados
Para aquellos que buscan implementar soluciones de inteligencia de fabricación en plantas industriales antiguas, B&R ofrece ahora la Orange Box. Las soluciones de adquisición y análisis de datos se pueden implementar fácilmente mediante el establecimiento de los parámetros de configuración necesarios, sin tener que modificar ningún hardware ni software existente y con independencia de quien suministre el sistema de control existente. Ralf Hagen, gerente de ingeniería E&A de Nestlé Alemania, y con Thomas Rienessl, director de desarrollo de negocios específicos para la industria en B&R, explican cómo la Orange Box transforma plantas industriales antiguas en instalaciones inteligentes.
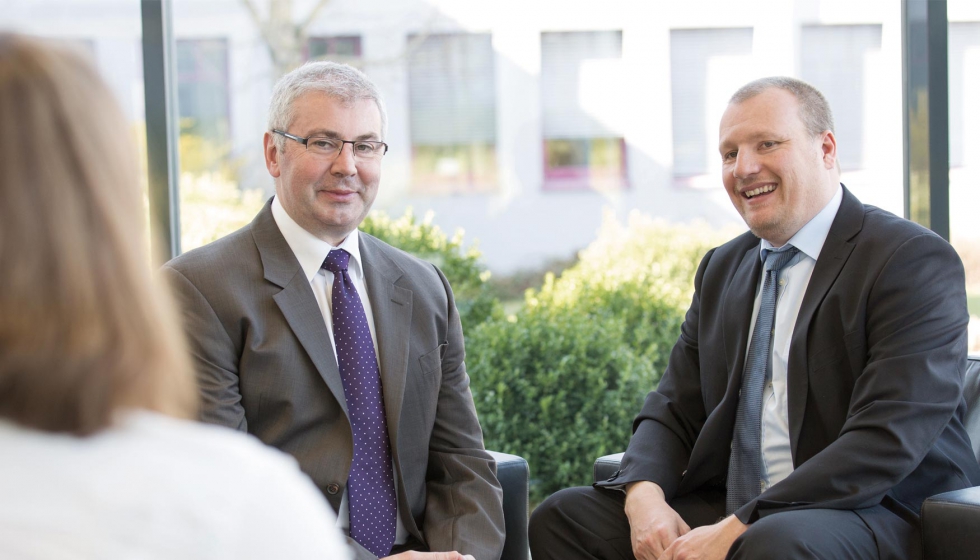
¿Qué convierte a una instalación en una fábrica inteligente?
Ralf Hagen (Nestlé): En una fábrica inteligente, los componentes necesitan comunicarse e interactuar de una manera mucho mejor de lo que estamos acostumbrados. Debe haber una cadena lógica ininterrumpida para cada pedido de un cliente de manera que se puede ejecutar de forma automática, de principio a fin. Una máquina debe saber cuándo debe acelerar o ralentizar, cuándo debería solicitar materiales adicionales o cuándo debería rechazarlos. Actualmente, estas decisiones todavía requieren la experiencia de los operarios humanos, pero en el futuro las máquinas deben ser capaces de manejarlos de forma autónoma.
¿Y qué es lo que convierte a una fábrica en inteligente desde la perspectiva de la automatización?
Thomas Rienessl (B&R): Una de las características de una fábrica inteligente es, sin duda, eficacia en los recursos, con un consumo reducido y con la consiguiente reducción de los costes de funcionamiento. Prácticamente todos los equipos modernos están automatizados por componentes inteligentes que generan enormes cantidades de datos. Por ello, los fabricantes están buscando formas para utilizar estos datos y ser más competitivos. Esto puede significar hacer procesos de producción más ágiles y sensibles, por ejemplo, o aumentar la disponibilidad al evitar el tiempo de inactividad no planificado.
¿Son ya 'inteligentes' todas las plantas de Nestlé?
Hagen: No. Y ello se debe en gran parte al tamaño de nuestra empresa. Las plantas más pequeñas tienen menos inercias cuando se trata de incorporar innovaciones, en la penetración de mercado y en las inversiones. Nuestras plantas varían mucho con respecto al sector y tamaño, por lo que el nivel de la fabricación inteligente realmente abarca todo el espectro.
¿Nestlé ha establecido metas precisas de producción?
Hagen: Con respecto a los KPI, sí. La definición más sencilla es en términos de eficacia general del equipo, o OEE por sus siglas en inglés. Hemos establecido objetivos OEE así como los plazos para su consecución.

Este es uno de los principales retos, pero seguro de que hay otros...
Hagen: Sin duda existen muchos más debido a las muchas correlaciones. Si la máquina tiene problemas con los períodos de inactividad no planificados, por ejemplo, también se tiende a tener problemas con la seguridad del operario. Cuanto más a menudo se tiene que realizar intervenciones en la máquina, mayor es el riesgo de lesiones. Otro aspecto clave es la eficiencia energética. Cuando una línea se encuentra en una situación de arranques y paradas constantes, estos procesos tienen un impacto real en el consumo energético. Al mismo tiempo, la calidad se ve negativamente afectada por los residuos que se producen cuando la máquina se pone en marcha o se detiene.
La seguridad, la energía, la calidad del producto: ¿son éstas las principales áreas en las que Nestlé está buscando la mejora?
Hagen: Sí, esas son las áreas que son los más fáciles de cuantificar a nivel mundial.
¿Tiene B&R que satisfacer estos mismos requisitos para otros clientes?
Rienessl: Ciertamente, pero las condiciones particulares son muy variadas. Los requisitos específicos de los clientes dependen en gran medida de la industria, ya sea en la fabricación puntual o en la fabricación en procesos más automatizados dependiendo de cuál sea ese nivel de automatización. El reto es siempre encontrar la manera de mejorar la producción de los medios y equipos actuales en uso. En teoría, para los conceptos como el modelo de referencia RAMI siempre se supone que se tiene acceso ilimitado a la última tecnología. En la práctica, sin embargo, las plantas de nuevas instalaciones siempre se ven superadas en número por las plantas industriales antiguas. Por lo tanto, el verdadero desafío en términos de productividad es sacar más provecho de los activos que ya se encuentran en las propias instalaciones.
¿Cómo llegó a contactar Nestlé con B&R para encontrar una solución a sus problemas?
Hagen: Contactamos con muchos proveedores potenciales, pero B&R fue el único que podía ofrecer el paquete total de estructura, marco, aplicaciones y modularidad que estábamos buscando. Queríamos a alguien capaz de encapsular la experiencia necesaria en un paquete probado a conciencia que se pudiera instalar, usar y actualizar con tan solo pulsar un botón de la misma forma como se realiza con una aplicación de un smartphone.
¿Puede contarnos algo más sobre las soluciones que han desarrollado con B&R?
Hagen: Hemos creado una solución que evoluciona de forma modular y orgánica, y en ella reside la belleza de la misma. Después de todo, vivimos en un mundo de cambio constante. Si uno instala sistema y dice “Perfecto, ahí lo tenemos”, uno va a tener problemas cuando llega el momento de migrar. Hasta ahora, el sistema B&R es el único que puede hacer esto.
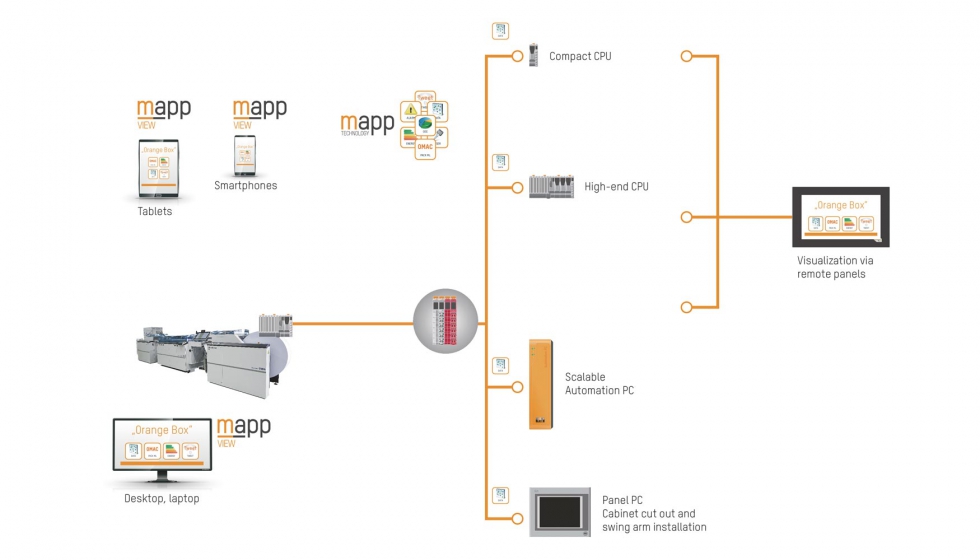
¿Podemos afirmar que la Orange Box es una solución personalizada desarrollada específicamente para Nestlé?
Rienessl: La Orange Box es una solución muy versátil, abierta para la recogida, la normalización y la evaluación de los datos en tiempo real. Si los requisitos cambian, la Orange Box simplemente cambia con ellos. En esencia, se trata de una combinación de tecnología MAPP y escalabilidad+ de B&R. La Orange Box permite que los operarios de máquinas puedan comprobar los parámetros relevantes in situ e intervenir inmediatamente en cuanto sea necesario. Cuando se habla sobre la alta disponibilidad, es esencial que las desviaciones se detectan a tiempo y que se tomen de inmediato las medidas correctivas adecuadas. Eso es exactamente lo que la Orange Box le permite hacer, y la razón por la que ha sido tan bien acogida.
¿Para qué tipo de aplicaciones es adecuada la Orange Box?
Rienessl: La Orange Box puede utilizarse en cualquier industria, pero está particularmente bien adaptada para las plantas donde en el proceso de producción interviene un gran número de máquinas. Básicamente hay dos tipos de clientes para los que resulta especialmente indicada: fabricantes industriales y fabricantes de máquinas de gran tamaño.
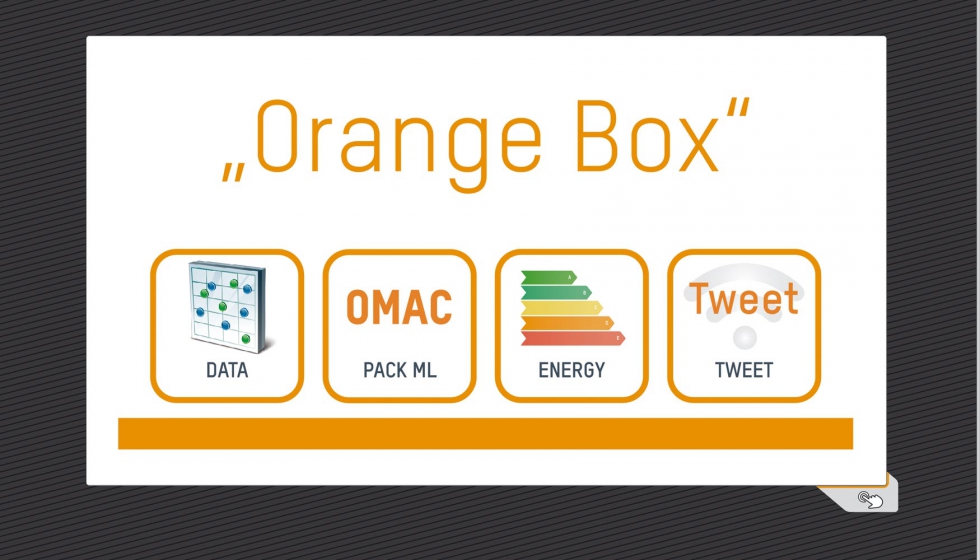
¿Cómo ha sido su experiencia con la Orange Box en la planta de Nestlé en Osthofen?
Hagen: La instalación y la puesta en marcha del prototipo resultó ser aún más rápida y sencilla de lo que esperábamos. Ahora estamos trabajando en la mejora de los resultados del análisis y la forma en que se visualizan para su uso diario como en reuniones de cambio de traspaso.
¿Cuáles son sus planes de futuro para la Orange Box?
Hagen: Nuestra intención es disponer de un análisis inteligente que identifique las causas fundamentales de un problema antes incluso de que éste llegue a producirse. Durante los próximos cuatro años, queremos llegar a una posición en la que las máquinas nos adviertan por adelantado de un paro inminente, en vez de tener que solucionarlo posteriormente tal como lo hacemos ahora. Nuestra intención final es que no se produzcan tiempos de inactividad no planificados y que la Orange Box nos ayude a incrementar tanto la disponibilidad como el rendimiento de la máquina.
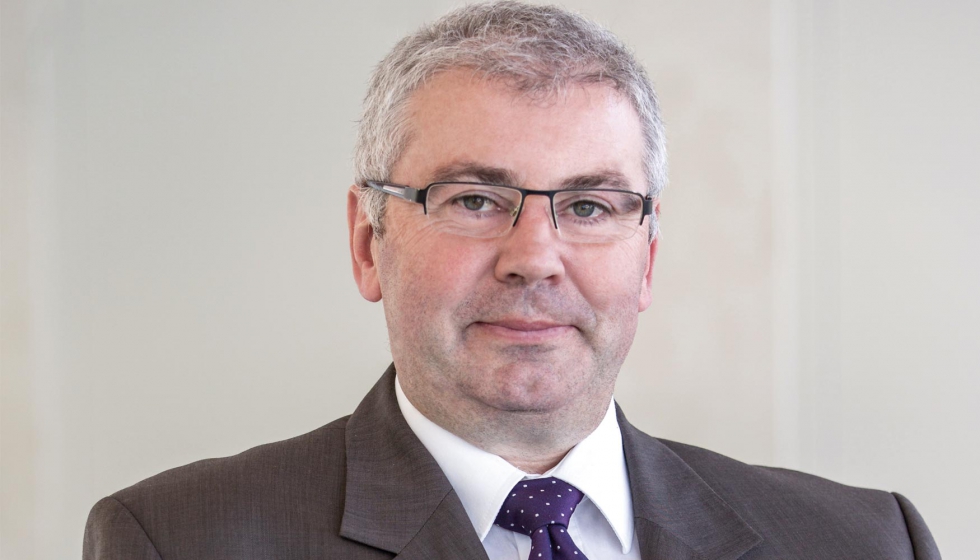
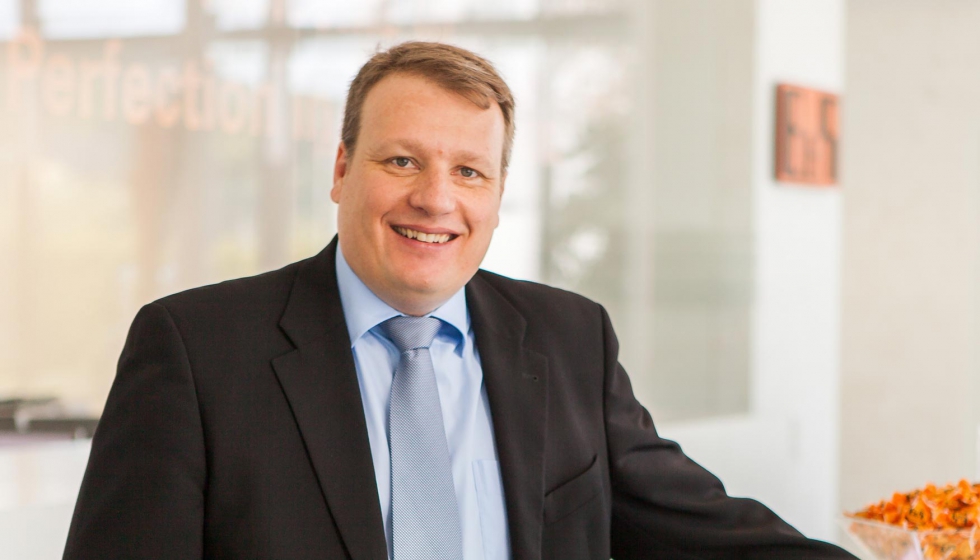