Sistema de regulación del rebobinado sin sensores
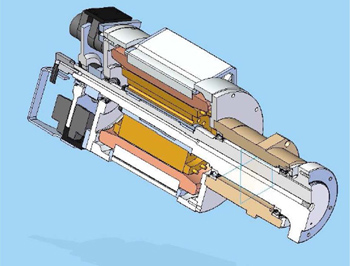
Antiguamente, cuando solo era posible regular la velocidad a través de un motor de corriente continua, la gran mayoría de máquinas ofrecían un control de corriente en su motor rebobinador. Mediante la incorporación de un potenciómetro se limitaba la potencia en el inducido y a través del clásico indicador de aguja se podía visualizar el nivel de esta corriente.
El principal problema del sistema era evitar que, al romperse el material, el motor tuviera tendencia a mantener su intensidad de corriente y aumentara su velocidad hasta el nivel máximo. Por otra parte, se obviaban las fricciones, generalmente elevadas, producidas por el sistema mecánico de transmisión.
Por esta razón, cuando el uso de la electrónica se extendió en el mundo industrial y un mayor afán de precisión se apoderó de los fabricantes, empezó a estandarizarse un sistema de regulación realimentado mediante un sensor de tensión en el material. De este modo, independientemente del tipo de control utilizado en el motor, se conseguía establecer y regular una tensión real y conocida.
Esta solución se ha mantenido durante muchos años gracias a su facilidad de aplicación independientemente de la mecánica utilizada. Sin embargo, los sistemas evolucionan a medida que se desarrollan nuevos avances tecnológicos. De esta manera, la aparición de motores asíncronos nos brinda la oportunidad de realizar con precisión un ajuste de tensión en el rebobinado sin la necesidad de utilizar sensores externos, con todas las ventajas que esto ofrece.
Todo sistema con regulación conlleva inevitablemente oscilación, por lo que los sistemas realimentados exigen una serie de ajustes para minimizar las variaciones. Por ello, la precisión de estos sistemas está limitada por las capacidades del personal que se dedica a su ajuste, haciendo más difícil encontrar el punto óptimo. Además, la obligación de un pasado de material estricto a través de los rodillos que contienen el elemento de lectura de tensión y la necesidad de conservar el ángulo de abrazamiento hacen que este sea un sistema mejorable.
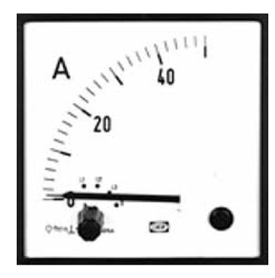
La irrupción en el mercado de motores síncronos trifásicos, diseñados para aplicaciones con altos niveles de par a bajas revoluciones, ha permitido desarrollar la idea de recuperar un sistema basado en los formatos antiguos y sin necesidad de utilizar sensores. Un sistema capaz de resolver los antiguos problemas de material, la necesidad de ajuste personalizado, las oscilaciones de la regulación y reducir los costes al prescindir de los elementos de lectura de tensión. El proyecto se ha materializado en la cortadora rebobinadora S-Turret de Comexi Proslit.
Para su desarrollo, se han utilizado motores que acoplan directamente el eje expansible de rebobinado con el eje del motor, formando un conjunto sólido y libre de cargas.
Gracias a este innovador montaje mecánico, la cadena cinemática entre motor y carga se reduce a los cojinetes que soportan el eje. De esta manera, se consigue una reducción drástica de las fricciones y una mayor estabilidad. Si a esta revolución mecánica le sumamos el gran número de ayudas electrónicas adoptadas por los novedosos equipos de control de motor, podremos registrar el par de rodadura necesario en cada una de sus revoluciones. La gráfica resultante de par/revoluciones nos permite anticiparnos al límite de par.
Por otro lado, la electrónica nos ofrece la posibilidad de sincronización de ejes reales con ejes virtuales (perfectos en cuanto a reacciones). Esta sincronización nos muestra valores reales del grado de aceleración del conjunto, por lo que no es difícil calcular el par de inercia de la masa que conforma la carga que deberemos adicionar en el momento de la aceleración.
El par de tensión necesario para tensar el material lo podemos calcular a partir del 'setpoint' requerido y del radio del rollo a bobinar. En este punto es crucial obtener un diámetro de la bobina estable y real para evitar oscilaciones de tensión o trabajar con una tensión distinta a la requerida. En la S-Turret el eje de rebobinado se traslada longitudinalmente a medida que crece el diámetro a través de dos servomotores sincronizados. Gracias a esta característica, la posición actual de los servomotores nos expresa directamente el radio de ésta, confiriendo al valor una estabilidad absoluta.
La suma de estos tres valores de par calculados se envía al equipo de regulación del motor como límite de par. Si sumamos a la ‘speedreference’ una cierta sobrevelocidad para tener margen de regulación, obtendremos lo que se puede calificar como ‘Sensor-lessrewinder’, (pendiente de patente), basado en los sistemas de regulación de los años 60.
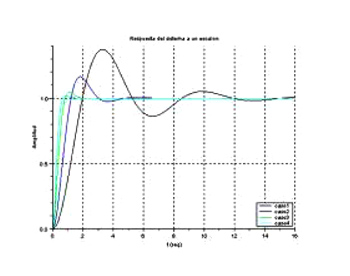