La impresión 3D
La fabricación substractiva está en retirada: el artista que a golpes de herramienta logra una estátua de un bloque de madera o cemento. La manufactura aditiva con láser es una realidad, incluidas piezas de alta precisión para misiles de la aeronáutica militar. Con la manufactura tradicional y de molde no se logra tan alta precisión en el suministro de componentes. Por supuesto, GE Aviation, BAE y Rolls Royce está usando la impresión 3D. El uso de tecnologías de escaneo 3D permite la réplica de objetos reales sin el uso de moldeo.
En el sinterizado de polímeros con escaneado láser una delgada capa de polvo orgánico se extiende sobre la superficie. La temperatura es un poco inferior a la temperatura de fusión del polímero. El láser de impulsos contiene una imagen digital, que hay que gravar sobre el políumero. El láser, muy finamente enfocado, va fundiendo el polvo, para crear la imagen, cada grano de polvo funde y rápidamente se solidifica.
El proceso se repite todas las veces que sea necesario, hasta completar la imagen sobre la plataforma de polvo, añadiendo cada capa sobre la inferior. El escaneado funciona de modo normal, formando líneas paralelas sobre la plataforma. Sobre la capa que el láser acaba de gravar superpone otras capas, para lograr la impresión tridimensional. El láser ha de ser de alta potencia, uno de CO2, al menos de 200 W. El grano de polvo iluminado por el láser funde casi instantáneamente.
Para aumentar la velocidad de sinterizado se pueden usar varios láseres. La empresa alemana EOS usa cuatro. Las líneas horizontales del escaneado se superponen un poco unas líneas sobre otras, para no perjudicar la calidad de la imagen. Un sistema automático se cuida de apartar el polvo de resina sobrante, cada grano tiene un tamaño de 0,1 micra, y aun menor. Así en la impresión 3D se logran paredes de un espesor de 70 micras. Unas dimensiones aptas, de mucha precisión para prótesis médicas, componentes ópticos y en relojeria. En un motor aeronáutico, la turbina, las distancias entre piezas adjuntas son microscópicas. La impresión 3D se creó para fabricar prototipos pero ya se usa en alguna empresa para loa fabricación en serie de piezas que luego se destinan a aviones y automóviles.
Como diferentes materiales requieren métodos diversos hay una amplia variedad de impresoras 3D, su coste está descendiendo, y bajan las barreras para usar la nueva tecnología. La sinterización por láser se abarata, porque puede usar la fabricación por filamento fundido, una técnica de extrusión, no aditiva, y las patentes expiran.
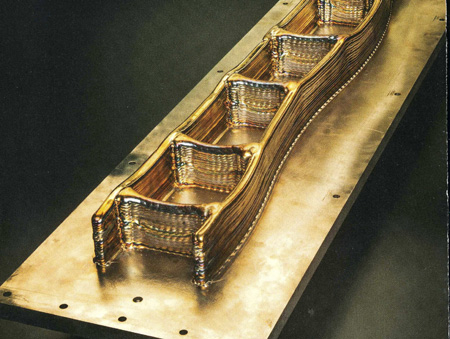
Impresión 3D de una pieza de titanio de 120 cm de longitud por fabricación aditiva. Costó 37 horas desde el modelo digital a la terminación de la pieza. Es fruto de la colaboración de BAE Systems y la Universidad de Cranfield.
Alta costura con polvo de poliuretano
La foto adjunta de tela esponjosa de poliuretano termoplástico ha sido creada por Marcus Rechberger, de Hamburgo sobre la resina Desmopan con granos de polvo de 0,1 micra. Ha sinterizado con láser para lograr la impresión 3D.
En otra foto adjunta una mujer modelo luce un vestido negro de poliuretano esponjoso de M.Rechberger. El haz de láser solidifica el polvo de poliuretano, siguiendo un diseño tridimensional del tejido que está creando. La impresión 3D también sirve para fabricar piezas de zapatos, sombreros, objetos de moda. Se puede fabricar un zapato a la medida del cliente, por supuesto, un zapato flexible. Antes un prototipo se usaba para la fabricación en serie, pero no resultaba económico ir haciendo cambios en el prototipo. Ahora hemos ganado en flexibilidad, y podemos modificarlo. El láser para sinterizar ha sido fabricado por Bayer Material-Science, de Dormagen, Alemania.
El método es sencillo: se logra una superficie ultra delgada de polvo de poliuretano, el láser va fundiendo polvo de poliuretano y creando el tejido esponjoso que necesitamos. Cada grano de polvo se funde y solidifica inmediatamente siguiendo el diseño tridimensional del ordenador con su geometría predefinida. Para hacer crecer verticalmente un objeto tridimensional se aplican sucesivamente delgadas capas de polvo, de acuerdo con el diseño informático, y logramos el tejido esponjoso del traje de moda, que luce la modelo.
Con este método se puede fabricar cualquier objeto de plástico, por ej.: una flor de plástico abierta o cerrada, de la foto adjunta. Se logra en un tiempo muy corto. El láser funciona con tal precisión, que puede lograr estructuras con un error no superior a 0.1 micra. Sus aplicaciones son innumerables.

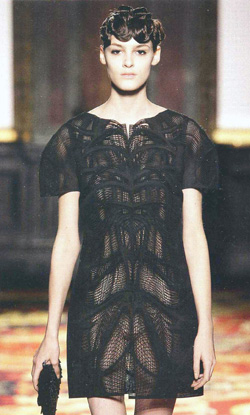
3D por inyección
A diferencia de la estereolitografia, la impresión 3D por inyección está optimizada para obtener velocidad, coste bajo y facilidad de uso, una técnica muy útil en ingeniería. La impresora crea el modelo de capa en capa esparciendo una capa de polvo (plástico, resina) e inyecta un coaligante por inyección. El proceso se repite en cada capa. El espesor típico de capa es de 0.1 mm. Hay la necesidad del soplado de polvo sobrante, después del proceso de impresión. Las impresiones de polvo coaligado pueden ser endurecidas con cera.
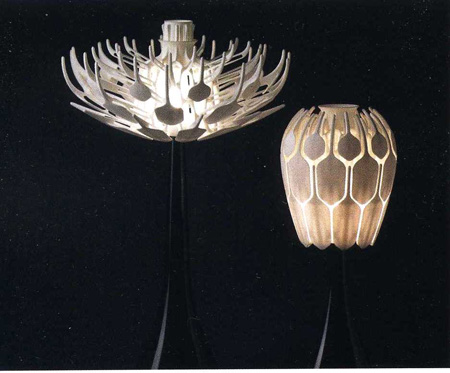
Estereolitografia

Fotopolimerización por luz ultravioleta
En esta fotopolimerización un recipiente de polímero líquido es expuesto a la luz de un proyector bajo condiciones controladas. El polímero líquido expuesto endurece. La placa de montaje se mueve hacia abajo en incrementos pequeños, y el polímero es expuesto de nuevo a la luz. El proceso se repite hasta que el modelo es construido. El polímero líquido restante es entonces extraído del recipiente, dejando únicamente el modelo sólido. El ZBuilder Ultra es un ejemplo de sistema de Polimerización por luz ultravioleta para el prototipado rápido.