Automatització de la planta de Sal Nylon a Girona
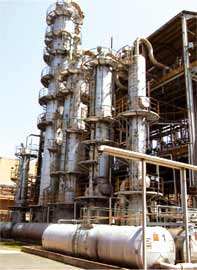
La seva capacitat d'adaptació a les necessitats i demandes del mercat, així com la filosofia d'automatització de les seves plantes química i tèxtil per a la fabricació de polímers i fils de PA66 amb costos molt reduïts, la posiciona com a líder a Europa i la segona en el món . Nylstar ha automatitzat totes les seves instal·lacions, tant a la planta química com a la planta tèxtil, confiant en equips Omron ja des dels primers passos de l'automatització de la fàbrica.
L'any 2003 s'ha substituït tot el sistema de control-en servei des de l'any 1973 - per un sistema basat en PLC Omron, que ha permès traslladar la supervisió a una altra sala de control existent. Això ha permès augmentar el nivell de productivitat, fiabilitat i seguretat, alhora de fer un salt qualitatiu notable en la vigilància i seguiment de la planta. El disseny, muntatge i posada en marxa del projecte s'ha realitzat amb enginyeria pròpia.
Procés de fabricació de polímers
L'altra gran matèria primera per a la fabricació de la poliamida 6.6 és el Ac.Adípico. Mitjançant la reacció de salificación entre el Ac.Adípico i el HMD-pur s'obté la sal niló al 52 per cent.
En el següent procés i mitjançant la utilització de reactors d'evaporació es concentra la sal niló fins al 85 per cent. Aquesta sal s'envia als reactors de polimerització on en unes condicions de pressió i temperatura adequades s'obté el polímer poliamida 6.6.
La matèria fosa a 270 º C s'extrusiona en el mateix reactor de polimerització i surt a través de la filera de la vàlvula de bugada, on es refreda i talla mitjançant els granuladors.
L'aparença final del producte és un granulat de 3x2, 5x2, 5 mm de diferents característiques en funció de l'aplicació. Aquest granulat s'envia mitjançant transport pneumàtic a les filatures de la fàbrica tèxtil per fabricar fils de poliamida o vendes.
Substitució del sistema de control
La preservació dels nivells de fiabilitat i seguretat han estat presents en l'automatització de la planta adoptant solucions com:
- Redundància d'equips SAI per a subministrament elèctric al sistema de control.
- Redundància i commutació automàtica de xarxes de supervisió (sysmac link-ethernet).
- Un PLC per a cada columna per minimitzar riscos en situació d'avaria.
- Controladors discrets en comunicació amb els PLC per als llaços crítics de control, evitant així possibles perills a la planta química, ja que es tracten productes corrosius, i reduint el risc laboral.
- L'automatització ha donat fiabilitat i seguretat a les instal·lacions, reduint també els costos de fabricació.
En cadascuna de les sis columnes s'ha instal·lat un autòmat CS1H d'Omron perquè controli la seva activitat. Així mateix, hi ha PLC en el procés de salificación i en els serveis generals. Encara que el funcionament del procés de salificación és independent de la rectificació, tots dos comparteixen alguns paràmetres, de manera que els PLCs que controlen ambdós processos estan comunicats en "sysmac enllaç", si alguna part del procés s'atura, un autòmat ha de conèixer per assegurar que el procés complementari segueixi funcionant. De la xarxa "device net" connectada al PLC de serveis generals, pengen els controladors de temperatura E5EK d'Omron per garantir el funcionament dels llaços crítics en cas d'un suposat error del PLC. Si aquest PLC fallés, els llaços crítics seguirien funcionant, amb la qual cosa es garantiria el restabliment dels serveis mínims del sistema.
Hi ha cinc llaços crítics que controlen les variables que afecten a totes les columnes: dos circuits vapor, nivells de dipòsits i la temperatura de l'aigua a 45 º C.
Els PLCs que controlen l'activitat de les columnes estan comunicats mitjançant la xarxa "sysmac enllaç" d'Omron, si bé hi ha la xarxa "ethernet" com a via de comunicació principal, a través de la qual els PLC es comuniquen amb el scada de la sala de control.
Hi ha una vigilància de la xarxa "ethernet" i en cas de fallada es realitza una commutació automàtica a "sysmac link".
El "scada" utilitzat és el "InTouch". En el desenvolupament del "scada" s'ha tingut en compte als operaris que han estat treballant en fàbrica i que estaven habituats a l'antic sistema, de manera que la imatge del sinòptic anterior es reprodueix a la pantalla de manera similar per facilitar l'adaptació d'els operaris a la nova tecnologia aplicada, però amb els avantatges en el seguiment i control del procés.
A la pantalla del "scada" es poden visualitzar les alarmes i combinar les diferents variables del sistema en un sol gràfic per supervisar els llaços de regulació.
Segons Joaquim Serrat, cap de conservació, fluids i enginyeria de Nylstar a Blanes, "la productivitat aconseguida després de l'automatització del procés de rectificació ha estat l'esperada, hem aconseguit reduir els costos de producció mantenint i fins i tot incrementant els nivells de seguretat i el termini d'amortització de la inversió ha estat d'un any i mig. Estem satisfets: l'aplicació ha quedat perfecta, amb nivells de seguretat màxims ".