Euromaher presenta novedades en fundición tras la GIFA 2023
El pasado mes de junio tuvo lugar una de las ferias más destacadas del sector de la fundición a presión, la GIFA 2023, en la ciudad alemana de Düsseldorf. En esta 15ª edición estuvo presente Euromaher junto a dos de sus más destacados representados italianos: Colosio y OMSG. Desde Euromaher trasladan la importancia que ha tenido en el mercado español esta cita en la que se congregaron muchos de los clientes de la compañía española, Representaciones Euromaher, y donde pudieron ver las últimas innovaciones de sus principales fabricantes.
Los visitantes al stand de Colosio y OMGS, representadas por Euromaher, en la GIFA, pudieron asistir a la actualización de su maquinaria y conocer de primera mano de muchas de las optimizaciones tecnológicas que podrán desarrollar en algunas de sus máquinas actuales o que podrán incorporar en las próximas inversiones.
Entre las opiniones principales de sus clientes “predominó la satisfacción por el tiempo de dedicación en los diferentes expositores y la importancia que tuvieron algunas de las innovaciones que podrán incorporar aquellos que van a realizar inversiones a corto plazo. Las empresas que se decantan por una inversión a largo plazo destacaron la fiabilidad y seguridad que les aporta la marca, además de contar con importantes mejoras y más sostenibles que comportan un ahorro económico”, explican desde Euromaher.
Ambos stand fueron un indicador importante de las innovaciones que orientarán el futuro de la inyección y la fundición en la maquinaria para el tratamiento de superficies de Euromaher, “además de reforzar el vínculo con nuestros clientes y crear nuevas conexiones con los nuevos visitantes”.
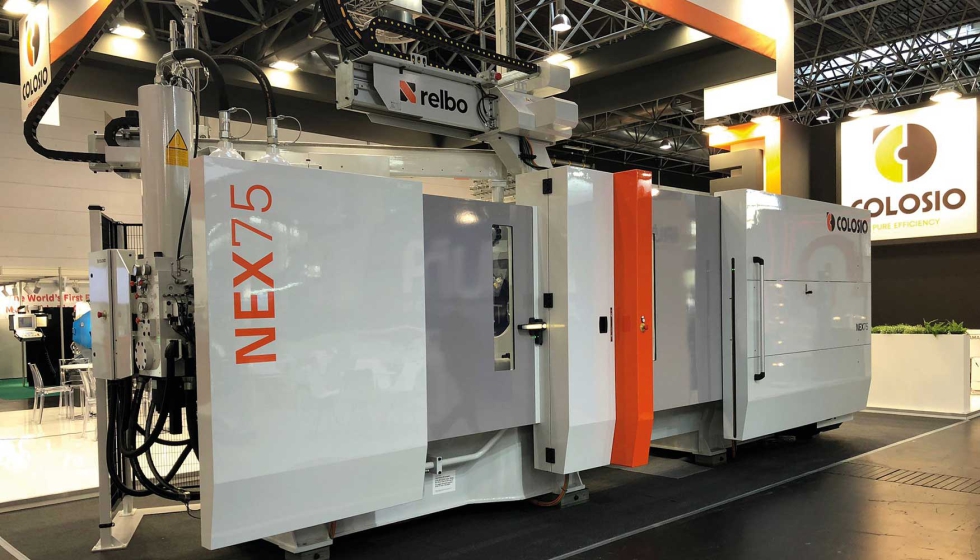
NEX, la nueva generación
El Grupo Colosio comenzó su andadura en la década de los 70 hasta convertirse en la actualidad en uno de los principales exponentes en el sector de la fundición a presión con la característica principal de ser de los pocos fabricantes capaces de producir internamente toda la prensa de inyección, integrada y completa dentro de la célula con todos los accesorios de automatización. A lo largo de estos más de cincuenta años se han enfrentado a diversos procesos de mejora, como este último proceso de modernización de la imagen de la compañía con nueva identidad corporativa. Un cambio protagonizado por el rediseño del logotipo y la web, nuevo diseño del material gráfico y la presentación de la nueva generación de maquinaria NEX.
Con esta nueva serie de máquinas, el Grupo Colosio sorprendió en la feria, en concreto, el modelo NEX 75 fue presentado al completo con sus accesorios. Un modelo diseñado para ofrecer un rendimiento, una precisión y una fiabilidad superiores en la producción de componentes de aleaciones de aluminio, magnesio y latón. A lo largo de los próximos meses, todas las innovaciones de esta nueva generación se extenderán al resto de tonelajes de su maquinaria.
Una de las novedades más aplaudidas por los visitantes en línea con la actualidad y que muestra el compromiso del grupo por mantenerse a la vanguardia es su asistente virtual. Como indica Francesco Sauda, Export Sales Manager “VITA es un software de mantenimiento predictivo que le permite ver los problemas antes de que sucedan. Agregando el big data y toda la información que nos comunican las prensas, tendremos una base de datos que nos permite predecir el comportamiento de todos los componentes de la máquina. Este software también se desarrollará e integrará con nuevas funciones en los próximos meses. Nuestro asistente virtual equipado con inteligencia artificial, actualmente llamado Wilson, permitirá a los clientes tener siempre disponible un técnico virtual para solicitar información sobre la máquina y su programación. Evidentemente el tiempo nos permitirá enseñar cada vez más nociones a Wilson, para que pueda estar cada vez más preparado y flexible”.
El balance general de la feria para el Grupo Colosio “ha sido muy positivo. La nueva máquina de la serie NEX nos ha permitido llamar la atención de muchos visitantes y de gran variedad de países. Los clientes españoles también estuvieron muy presentes con interesantes visitas técnicas y comerciales de alto nivel.” Son conscientes de que el momento actual es muy tranquilo para las fundiciones, probablemente debido a la incertidumbre existente en el mundo del automóvil, pero están seguros de que “las innovaciones que han propuesto en GIFA son un importante punto de partida para permitir a nuestros clientes invertir en maquinaria más eficiente, más sostenible y más inteligente”.
Un balance optimista tras cinco días inmersos en la exposición que les impulsa a continuar con más fuerza y a emplazar a un nuevo encuentro en la Feria Euroguss en Nuremberg, que tendrá lugar del 16 al 18 de enero de 2024. Allí mostrarán la evolución de todos los proyectos iniciados este mes de junio en Alemania.
Características de la serie NEX
Unidad de inyección renovada. Sistema de energía regenerativa, extrema precisión en el control de fase de inyección, servo válvulas para control en tiempo real de velocidad y presión, posicionador digital del pistón de inyección.
Sistema de control de última generación. HMI intuitiva de última generación (Interfaz hombre-máquina) con pantalla táctil de 24” y control KeWheel para gestionar el movimiento de la máquina.
Tamaño reducido y mejora de la ergonomía. El análisis y estudio de componentes y materiales han permitido el desarrollo de una máquina más compacta con una ergonomía mejorada para el operador.
Mayor seguridad y menor mantenimiento. Protecciones del grupo de cierre mediante fotocélulas de alta precisión y accesibilidad a áreas de mantenimiento libres de interferencias. Aumento de la seguridad y simplificación de la gestión de mantenimiento.
Verde y sostenible. La integración con el sistema Greenline es completa, lo que se transforma en un consumo mínimo de energía y una reducción significativa del agua necesaria para la refrigeración.
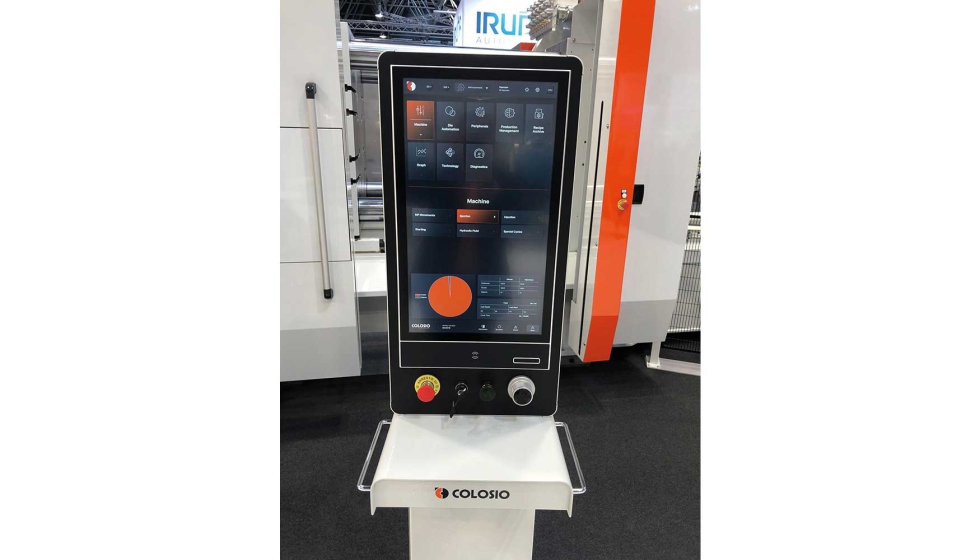
Sistema HMI. Control táctil y entrada KeWheel.
Relbo, flexibilidad y dinamismo
35 años de experiencia desde su creación por el Grupo Colosio para proporcionar soluciones de extracción y lubrificadores lineales y robotizados en el proceso de ‘Die-casting’ han conseguido que Relbo sea conocida en la actualidad en el mundo de la fundición a presión por suministrar dichas soluciones desde el punto 0 o adaptarse a las instalaciones ya existentes en sus clientes en todo el mundo.
En GIFA expusieron diferentes accesorios de lubrificación directa, de uno o dos ejes y robotizada, así como la configuración de las máscaras de lubrificación, con sus sistemas de enfriamiento de molde directo, cónico y la configuración con sus boquillas convencionales, micro pulverizado y ECO.
Dispone de teclado y pantalla táctil para programar y guardar las recetas requeridas en producción y la integración total, con control desde el HMI de las inyectoras Colosio.
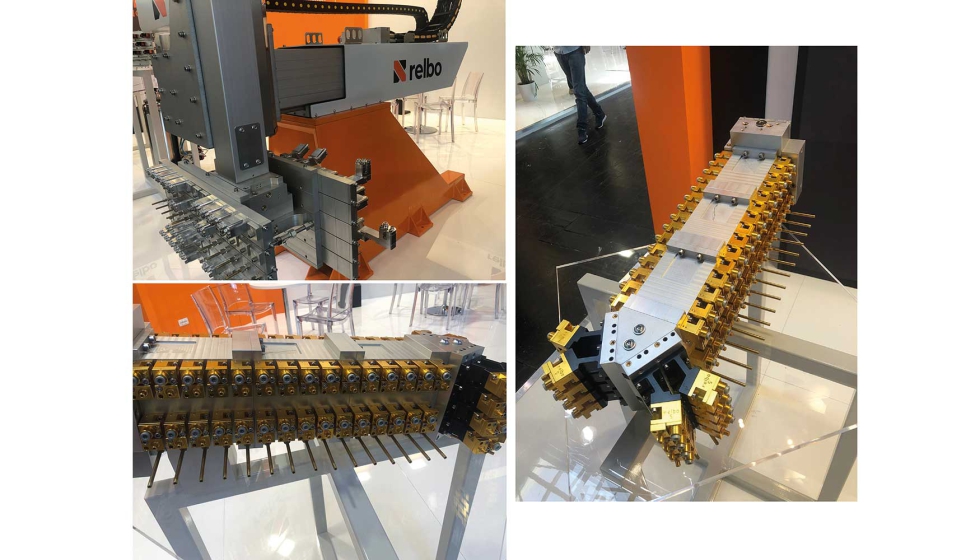
OMSG muestra su granalladora de tapiz para fundición
En esta ocasión, el modelo SG6 H2 con Tappeto Rampante y con transportador para la descarga de piezas CS ocupaba el expositor de la compañía. Es una máquina específica para el sector de la fundición con dispositivos especiales que únicamente se aplican en este sector como son el separador magnético para separar la tierra de fundición de la granalla metálica, by pass para la limpieza del abrasivo metálico durante los tiempos muertos (fases de carga y descarga), transportador vibrante de descarga piezas reforzado para el sector fundición y un filtro especial. Este tipo de granalladoras permiten ofrecer una elevada producción y óptimos acabados.
Durante la feria recibieron un alto número de visitantes de todas partes del mundo con una significativa presencia de visitantes turcos. La mayor afluencia procedía del sector de la fundición ferrosa (hierro y acero) más que del sector de la inyección. En líneas generales, la valoración final de la feria ha sido muy buena “incluso mejor de lo que esperábamos. La mayor parte de los clientes que nos visitaron estaban realmente interesados y dispuestos a invertir en los próximos 12-24 meses”.
De cara al futuro, las novedades más importantes en este sector seguirán por los sistemas automáticos en las fases de carga/ descarga piezas, la ejecución y manipulación automáticas de los contenedores y los sistemas de pesaje electrónico de los contenedores, entre las principales.
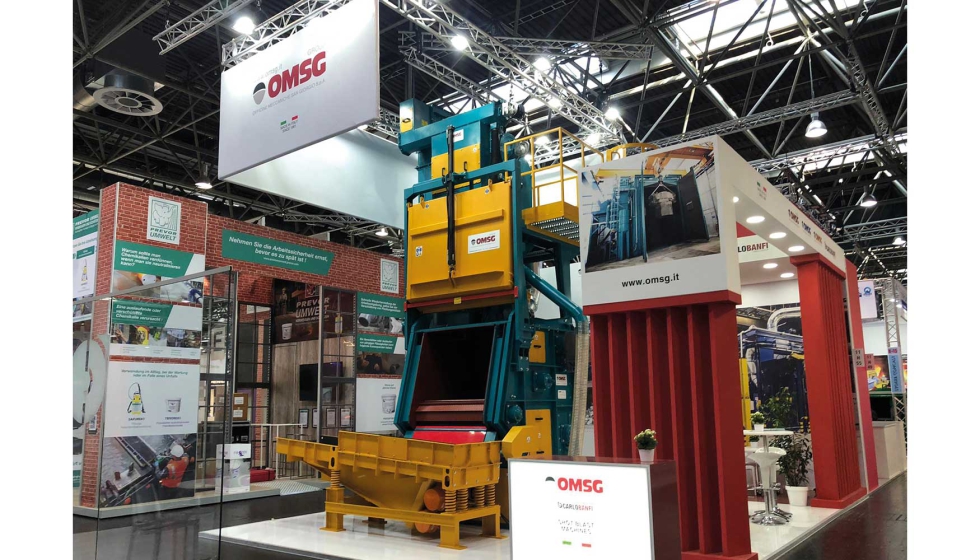
Funcionamiento del SG6 H2 con tappeto rampante
Las piezas a tratar se depositan sobre un transportador cerrado en forma de anillo y guiado de tal modo que forma una cavidad donde las piezas exponen su superficie uniformemente a la acción del abrasivo.
El trabajo de granallado está facilitado gracias a la acción de las turbinas y del tamizado de las piezas. La carga del material se efectúa a través de una puerta frontal de guillotina, mientras que la descarga se produce automáticamente invirtiendo el sentido de rotación del transportador.
Las turbinas centrífugas están situadas en el techo de la máquina, para producir un flujo de abrasivo uniforme y eficaz. La superficie interior de la zona de granallado está protegida con materiales resistentes al desgaste.
En la imagen se aprecia el transportador CS de canal vibratorio para extraer las piezas granalladas al lado de la máquina en una posición lógica para el movimiento de los contenedores. El canal, de sección rectangular, es de chapa de acero soldada y especialmente reforzada para el sector de la fundición. Una rejilla colocada en el tramo final recupera la granalla que puedan llevar las piezas en una pequeña tolva. Goma antiabrasiva de medio espesor reviste la superficie interna. La vibración se obtiene mediante motovibradores eléctricos de masas excéntricas.
La función del separador magnético permite discriminar la granalla metálica de los demás contaminantes. La granalla y el polvo pasan por los diferentes niveles produciendo una capa de material de espesor fino y uniforme. Un flujo de aire desde el filtro-aspirador atraviesa la capa de material y permite desviar los contaminantes al decantador y el abrasivo limpio a la tolva principal.
Para continuar con la selección de la granalla en los tiempos de carga y descarga de las piezas dispone de un dispositivo por el que la granalla sale de la tolva principal a través del conducto by-pass de la turbina y va hacia el elevador de cangilones, que la recicla al dispositivo seleccionado. De este modo, al aprovechar estos tiempos de parada, se puede continuar y mejorar la separación de la granalla metálica de los posibles restos contaminantes.
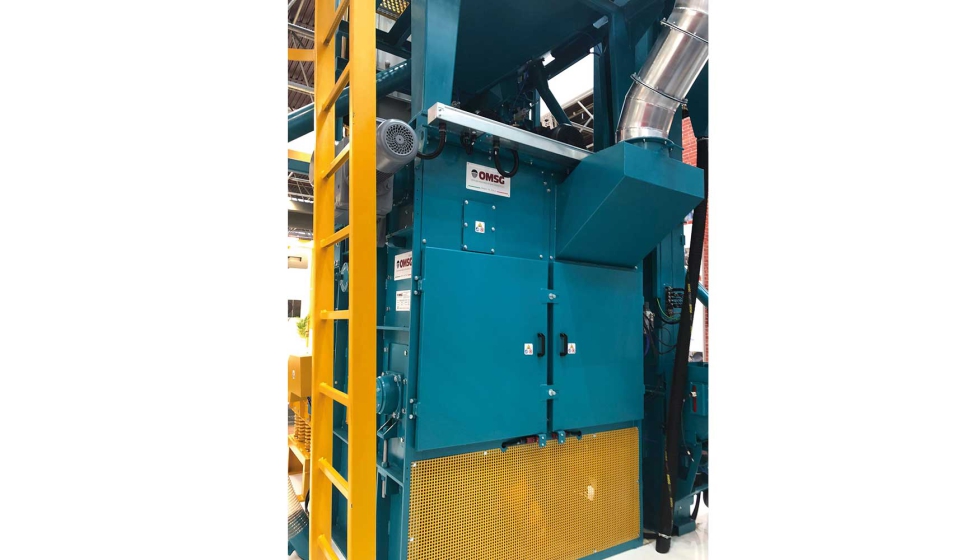
El empleo de este dispositivo permite elaborar las señales derivadas de los sensores instalados en el equipo. El operador, de este modo, puede elaborar y apuntar pautas, cada una relativa a una selección de parámetros variables (velocidad de proceso, velocidad de rotación turbinas, ciclos de granallado...
El sistema está preparado para efectuar un diagnóstico preciso de los dispositivos para asegurar su correcto funcionamiento y gestionar las anomalías según el nivel de gravedad.
Además del funcionamiento ‘Automático’ también dispone de la modalidad ‘Manual’ que permite el control individual de cada una de las operaciones, por exigencias de operaciones de mantenimiento o a discreción del operador. Todas las restricciones de seguridad que concatenan las distintas fases, siguen activas.
El dispositivo ofrece también la posibilidad de interaccionar, en la red Profinet, con otras actividades fuera del equipo, en particular, con el sistema de supervisión permitiendo establecer un proceso completamente integrado y controlado.