L'autòmat programable, un univers de possibilitats en constant evolució
Va ser Dick Morly, actualment conegut com el pare dels PLCs, qui va estar involucrat en el desenvolupament d'aquest primer PLC per a GE, conegut com Modicon (Modular Digital CONtroller). L'objectiu i disseny d'un PLC no dista tant del d'un PC convencional. Tots dos estan formats principalment per entrades, sortides, memòria i una CPU. I de la mateixa manera, el seu objectiu elemental és, davant la commutació en una o diverses de les seves entrades, realitzar càlculs lògics i, com a resultat, activar o desactivar una o diverses sortides. No obstant això, hi ha un aspecte fonamental on un PLC difereix dels ordinadors ofimáticos: la robustesa. Est va ser, precisament, un dels aspectes fonamentals que GE buscava per als seus desenvolupaments: un dispositiu molt fiable, capaç d'operar en les complicades condicions industrials, amb rangs de temperatura, humitat i alimentació estesos, amb una alta resistència a les vibracions i als impactes i, per descomptat, amb una alta immunitat al soroll electromagnètic. Una altra diferència substancial és el nombre d'I/S (entrades i/o sortides) que és capaç de manejar un PLC. A diferència d'un PC convencional, qualsevol PLC actual part de centenars d'I/S fins a arribar als milers que pot gestionar un PLC actual de gamma alta.
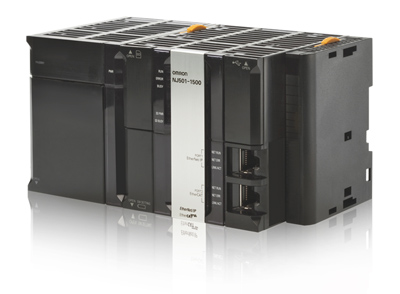
Del PLC al MAC
Durant aquests més de 40 anys, els PLCs han evolucionat en moltíssims aspectes i, si en els seus inicis la seva missió fonamental era substituir a la lògica cablejada, avui dia, amb els avanços tecnològics i la gran reducció de costos, el seu objectiu arriba molt més allà que el de fer càlculs lògics.
Així, a més del control de la lògica discreta, el control de processos continus amb senyals analògics o de sondes de temperatura va ser una de les primeres incorporacions al món del PLC.
Però ha estat a partir de l'any 2000 quan el món del PLC ha sofert un major avanç. Amb la reducció de costos en els equips electrònics més complexos i en l'electrònica de potència, van sorgir els controladors específics per a visió artificial, per ‘Motion Control’, seguretat, etc.
Amb tots aquests controladors, a part del PLC, va sorgir la necessitat imperiosa de la integració: amb diferents xarxes de comunicació, diferent programari de configuració, diferents llenguatges de programació, etc.
Avui dia, en l'afany de simplificar la integració de tots aquests sistemes, sorgeix el concepte de MAC (Machine Automation Controller) o PAC (Programmable Automation Controller), on el PLC evoluciona per suportar moltes de les disciplines abans comentades. De manera que des d'un únic programari, amb un leguaje i interface comú i sense cap problema d'interconnexió, un únic controlador pugui fer-se càrrec de l'automatització d'una màquina o una línia de producció sencera.
Estandardització
Un dels problemes que va aparèixer amb l'evolució i comercialització dels diferents models de PLC, és la fragmentació en els llenguatges de programació usats en cadascun dels equips, accentuat a més per llenguatges propis de les diferents marques.
El llenguatge amb el qual va començar tot va ser el ‘ladder’. Aquest llenguatge, es va inventar per representar d'una manera clara la lògica realitzada amb relés, i el diagrama de la qual, amb les diferents connexions i contactes, recorda al d'una escala (‘ladder’ en anglès) amb els seus diferents esglaons (‘rungs’).
No obstant això, amb la inclusió de nova funcionalitat en els PLCs van ser apareixent nous llenguatges, més adequats per realitzar altres tasques, com a càlculs aritmètics complexos, sentències condicionals o que permetien una major reutilització del codi.
Així, a la fi de 1993, l'IEC va publicar la primera revisió de l'estàndard 61131, que al seu apartat tercer defineix els llenguatges de programació estàndard d'un PLC. Actualment són els següents:
- Ladder Diagram (LD, diafragma d'escala)
- Function Block Diagram (FBD, diagrama de blocs de funció)
- Structured Text (ST, text estructurat)
- Instruction List (IL, llista d'instruccions)
- Sequential Function Chart (SFC, gràfic de funcions seqüencials)
Això proporciona un ventall molt important de possibilitats a la programació dels controladors actuals. Fins i tot, alguns fabricants permeten barrejar varis d'ells en un mateix programa, fent que la tasca de desenvolupament sigui moltíssim més senzilla.
D'altra banda, la norma IEC anterior, no només es limita a definir els llenguatges de programació, sinó també els tipus de dades i alguns aspectes propis del funcionament del propi controlador: gestió de dades usant variables, ús de tasques, etc.
Aquesta estandardització, al costat d'unes altres, fa que d'una manera molt senzilla, es puguin utilitzar diversos controladors sense haver d'aprendre cap nou llenguatge o forma de programar.
Arquitectures actuals
Si fem un cop d'ull als controladors actuals (els MAC o PAC) que comentàvem abans, podem observar com l'arquitectura ha passat d'utilitzar CPUs pròpies, de tipus ASIC a microprocessadors estàndards de mercat; habitualment AMD o Intel.
Això porta amb si importants avanços en les possibilitats i velocitat dels controladors, la qual cosa al seu torn ha possibilitat la integració de més disciplines en un únic equip.
Així, en algun dels equips més potents del mercat, podem trobar, per exemple, microprocessadors Intel Atom, a 1,6 GHz, que proporcionen una velocitat de procés mai abans vista en controladors industrials.
Aquesta velocitat també depèn en gran mesura del programari que hagi de suportar aquesta CPU. Així, és habitual trobar controladors que executen Windows CE o Windows Embedded que, de forma habitual, necessiten més recursos per funcionar que altres Sistemes Operatius, anomenats ‘Hard Real Estafi US’, orientats al control industrial i que garanteixen una repetitividad i fiabilitat tan alta que són els triats per al control en altres sectors, com l'aeroespacial, el de defensa, en medicina, etc.
Exemples d'aquest tipus de ‘Hard Real Estafi US’ són QNX o el Microware US-9.
Sobre el sistema operatiu, els controladors MAC o PAC executen el programari ‘runtime’ del propi fabricador. Aquest programari ‘runtime’ sol ser modular i és l'encarregat d'executar les seqüències lògiques (mòdul PLC), del control de moviment (mòdul de ‘Motion Control’), del control de robots (‘kinematics’), CNC, etc.
Normalment existeix un mòdul principal que sol ser el de PLC, que s'encarrega de la lògica i realitza les trucades oportunes a la resta de mòduls quan en programa d'usuari requereix d'aquests mòduls.
Imaginem un programa senzill d'una màquina de cort al vol, encarregada de tallar cadascun dels envasos que passaran a la següent etapa dins de la línia de producció i on el punt exacte de tall vindrà dau per una marca en el propi envàs.
En la cinta transportadora, per on es desplaça el film (tira contínua d'envasos, encara sense tallar), es col·locarà una fotocélula, a una distància determinada de la fulla. Aquesta fotocélula serà l'encarregada de detectar les marques presents en el film perquè la fulla arribi a moure's a la velocitat adequada i arribi al punt de tall a la mateixa velocitat exactament de la cinta transportadora.
En aquest exemple, si el mòdul de PLC és el principal, s'encarregarà d'iniciar l'execució de programa i en cadascun dels moviments, farà una sol·licitud al mòdul de ‘Motion Control’. Aquests moviments estan molt bé definits, doncs actualment gairebé tots els fabricants utilitzen l'estàndard PLCopen (al seu torn, basat en l'IEC 61131-3) per al control de moviment i cadascuna de les instruccions que fan ús d'aquest mòdul comencen per MC. Per exemple:
- Inicialitzar els eixos i que els ‘drives’ lliurin potència als motors
- Realitzar la cerca d'origen en l'eix de la fulla
- Començar el moviment de la cinta, lineal i sense fi en l'eix de la cinta
- I una vegada detectada la marca, establir la sincronització necessària entre els dos eixos perquè la fulla rotatòria aconsegueixi la marca al moment just
- Volta a l'origen de l'eix de la fulla
Addicionalment, el mòdul principal, en aquest cas el de PLC, també sol estar encarregat d'altres tasques, com és el refresc de les I/S i l'atenció a perifèrics (atenció a ports USB, Ethernet, accés a targetes de memòria, etc.).
Gestió de tasques i programes
Comentàvem unes línies abans que IEC 61131-3 definia no solament els llenguatges de programació, sinó que arribava a especificar l'arquitectura de funcionament dels controladors.
D'aquesta manera, els controladors basats en aquest estàndard tenen tots alguna cosa en comú: un model d'execució per tasques.
Existeixen dos models d'execució de tasques:
- Senar-Yielding (improductiu)
- Yielding (productiu)
En el primer d'ells, una tasca ha d'esperar al fet que una altra acabi per poder executar-se. En el segon, s'estableix un sistema de prioritats, de manera que una tasca amb una major prioritat pot interrompre a una altra i començar la seva execució. La tasca interrompuda reprendrà la seva execució quan acabi l'execució de les tasques de major prioritat.
Aquest últim sistema ofereix un rendiment major, a l'una que permet garantir el determinisme del sistema; és a dir, que una mateixa seqüència d'una determinada prioritat s'executi sempre en el mateix temps, independentment de la càrrega (nombre de seqüències en execució en aquest moment) del sistema. No obstant això, aquest últim sistema de gestió de tasques també és més complex i requereix d'un Sistema Operatiu de temps real, per la qual cosa no pot estar present en tots els controladors actuals.
En aquest sistema productiu existeixen tasques de diversa prioritat, com dèiem, encara que també poden existir tasques d'esdeveniments, d'atenció a perifèrics o, simplement, de processos interns.
Ens interessen aquelles tasques a les quals se'ls poden assignar programes d'usuari. Aquest model, definit per la norma IEC, permet assignar múltiples programes a cadascuna de les tasques de diferent prioritat.
Això comporta que els programes assignats a una tasca de major prioritat sempre s'executaran abans que els assignats a una tasca de prioritat inferior. I dins d'aquest model, els programes assignats a una mateixa tasca s'executaran cíclicament, un a continuació d'un altre. Aquest ordre habitualment es pot establir al programari de programació.
Tan important com una bona assignació de tasques, és l'assignació del refresc d'I/S, ja que un bon ajust de les prioritats i les assignacions permetrà portar els cicles de la màquina al mínim.
Aquest refresc de les I/S, quan es tracta d'unitats d'I/S locals no representa cap problema. Però no obstant això, quan es tracta d'unitats d'I/S distribuïdes o hem d'efectuar un control de moviment de la màxima precisió, és necessari recolzar-se en alguna de les millors xarxes de comunicacions del mercat, en la qual connectar aquests servo accionaments, I/S i una altra perifèria.
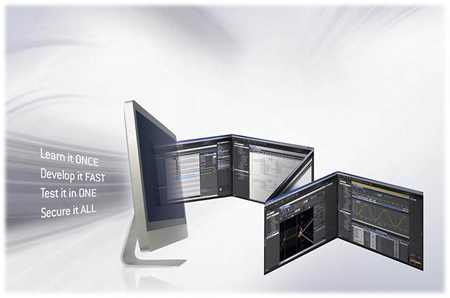
Xarxa de màquina
En l'actualitat existeixen múltiples xarxes que permeten integrar I/S, servos i molts altres dispositius. No obstant això, si mirem amb deteniment les especificacions tècniques, resultats reals i l'expansió que està sofrint al mercat, podem parlar d'EtherCAT com la xarxa que destaca sobre les altres, a nivell de màquina.
Una característica d'EtherCAT és que utilitza cable Ethernet estàndard per realitzar el cablejat entre el controlador i els diferents nodes de la xarxa. Al mateix temps, cada node disposa de dos ports: un d'entrada i un altre de sortida.
D'aquesta manera, es pot construir una xarxa ‘daisy-chain’ sense cap maquinari addicional i un cable totalment estàndard i econòmic. D'altra banda, EtherCAT és flexible i, si en un moment es necessita muntar una altra topologia de xarxa, diferent de la de cadena, existeixen bifurcadores al mercat que ens permeten crear qualsevol estructura en arbre.
Però la principal característica d'aquesta xarxa no es troba en la facilitat de cablejat, sinó en la rapidesa. El funcionament, malgrat utilitzar cable Ethernet estàndard, dista molt de ser el d'una Ethernet convencional. I és que en EtherCAT, el mestre llança una trama de grandària fixa (determinat pel nombre de nodes i la informació a intercanviar per cadascun d'ells) i arriba al primer dels nodes. Aquest, llegeix la informació que necessita i escriu una altra informació en la trama, al seu espai reservat per a això.
A continuació, aquest node envia aquesta trama modificada al següent, i est torna a llegir i escriure dades a l'espai que té reservat per a això. En arribar a l'últim node, aquest retorna la trama, ja amb totes les dades, al mestre; sempre treballant en una xarxa ‘full-duplex’, per la qual cosa l'enviament i recepció es pot dur a terme simultàniament.
Un altre punt a destacar d'aquesta xarxa, és que cada node triga un temps virtualment zero (en la pràctica, menor d'1 µs) a llegir i escriure en la trama que viatja per la xarxa. De fet, es diu habitualment que la trama que passa per un node EtherCAT està sortint al següent node abans que acabi d'entrar.
En xifres, EtherCAT és tan ràpid que podria refrescar 178 eixos, intercanviant cadascun 64 bytes, en 1 ms. No obstant això, cap controlador industrial actual és capaç de processar aquesta quantitat d'informació en tan poc temps. I per descomptat, cap altra xarxa industrial arriba a aquest nivell de rendiment.
Així, al mercat, els controladors més avançats seran capaços de controlar (ja no solament intercanviar informació amb els mateixos) uns 32 eixos en 1 ms, amb el que el coll d'ampolla, que antigament es trobava en els busos de comunicacions, ara passa als propis controladors, permetent que aquests evolucionin d'aquí a uns anys sense haver de preocupar-se pel sistema de comunicacions.
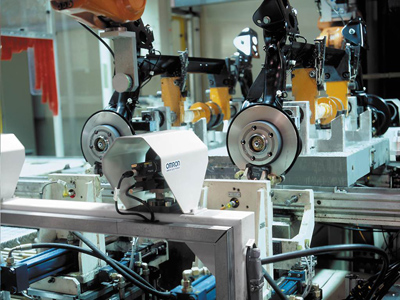
Futur
La integració de la part de PLC, de ‘Motion Control’, de visió, de robòtica, de ‘Safety’, de CNC, etc., no només porta amb si una homogeneïtat a l'hora de desenvolupar sinó que permet una integració total entre cadascuna de les disciplines a implementar permetent compartir variables, dades i una sincronització i precisió absoluta entre cadascun dels elements de la màquina.
Al mateix temps, el programari evoluciona creant veritables estudis de desenvolupament, des d'on es pot configurar, ja no solament el controlador, si no cadascuna de les diferents parts de la màquina, des d'un interface comú.
I aquest mateix programari haurà de ser l'encarregat de guiar-nos durant tot el procés de desenvolupament, assistint-nos i ajudant-nos en cadascun dels aspectes de configuració i programació. Però més enllà de permetre'ns programar un dispositiu concret, serà capaç de permetre'ns i assistir-nos en la creació d'una màquina completa.
Un pas encara més enllà, serà la comprovació i el testeo del nostre desenvolupament. Les millors eines actuals ja permeten realitzar una simulació de totes les disciplines implementades en la màquina (seqüència, control de moviment, visualització, etc.) i detectar i corregir errors abans fins i tot de tenir el maquinari. Però no solament això, sinó que el disseny en 3D de la màquina i la integració amb altres eines de regulació i processos, com Matlab permetran des de l'eina de programari dissenyar tota la màquina i assegurar, fins i tot abans de muntar-la, que funciona.
No hi ha dubte que el futur ens ofereix controladors més ràpids, potents, amb més memòria, etc., però al mateix temps amb funcions útils, que facin més fiables les màquines i que permetin un desenvolupament molt més ràpid.