Mayor precisión en máquinas-herramienta
15 de octubre de 2010
Ninguna máquina-herramienta es perfecta, ya que todos los ejes tienen algún fallo: los fallos de paso de husillo son muy típicos, lo mismo que un cierto combado en caso de ejes largos o inclinaciones en caso de estructuras muy altas. En todos estos casos se trata de fallos a los que los modernos controles CNC pueden dar respuesta mediante una serie de funciones especiales. No obstante, por lo general se realizan estas compensaciones por cada eje por separado. De este modo, no se tienen en cuenta otros fallos como las pequeñas desviaciones de la angularidad de los ejes entre sí, así como las ligeras torsiones. Muy a menudo estos fallos son eliminados mediante correcciones en el programa de CN, algo que implica la desventaja de que no es posible utilizar este programa en otra máquina antes de haberla adaptado.
La función '3D Error Compensation' de Fanuc permite compensar también estos fallos de eje en el espacio. En este sentido, es requisito la medición exacta del espacio de la máquina y de todos los ejes. Se trata de un proceso que muchas empresas han rehusado por el considerable trabajo que supone. No obstante, gracias a un nuevo procedimiento, se facilita considerablemente esta medición, tal y como ha podido experimentar un fabricante de modernos centros de taladrado. Sus máquinas CNC de alta velocidad se caracterizan, sobre todo, por su fiabilidad, durabilidad y alta precisión. Expresado en números: la precisión de posicionamiento en el sentido del husillo es de 0,006/300 milímetros y la precisión de repetición es de +/-0,002 milímetros. Con sus longitudes de eje útiles de 500, 400 y 330 milímetros, estas máquinas de mecanizado eficaz y preciso son de una construcción relativamente compacta. Estas máquinas se utilizan para el mecanizado de piezas de automóvil, piezas electrónicas, en el sector de relojería y bisutería, así como en la técnica médica.
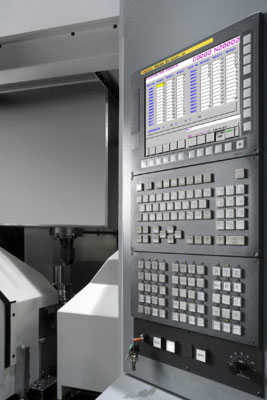
El sistema Etalon permite un calibrado sencillo
El fabricante ha utilizado la función '3D Error Compensation' para optimizar aún más la precisión de estos centros de taladrado. Ha utilizado el sistema de calibración de Etalon para la captación de las desviaciones geométricas restantes de los ejes de desplazamiento. Este sistema se compone del aparato de medición universal LaserTracer, así como de un software que, en base a los datos de medición, es capaz de calcular directamente las desviaciones de eje y de emitir los correspondientes datos de corrección. La precisión de medición extremadamente alta se consigue gracias a unos métodos muy sofisticados: como se utilizan tan solo las diferencias de longitud, se evitan las incertidumbres provocadas por mediciones angulares u otros medios auxiliares adicionales. Un principio patentado en el interior del aparato se encarga de eliminar las inevitables desviaciones mecánicas de los ejes de giro.
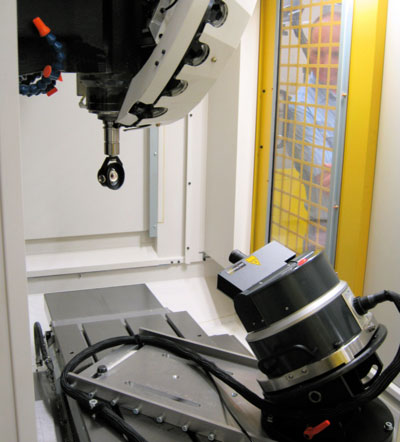
Para la determinación de las desviaciones de eje se ha colocado el LaserTracer de forma independiente en lugar de la pieza dentro de la máquina. Una placa de brazo universal ha permitido el posicionamiento del LaserTracer dentro de la limitada área de trabajo de la máquina. Aquí se ha instalado también la sonda de la temperatura del aire que se encarga de la corrección de la longitud de la onda del láser. Fuera de la máquina había además un sensor de presión del aire y de humedad del aire. En vez de la herramienta se ha fijado un reflector en el husillo.
La mayor parte del trabajo lo supone la planificación de la medición. En el software Trac-CAL se determina, por ejemplo, la ruta de medición que puede recorrer la máquina. En caso del centro de taladrado para la distancia entre puntos seleccionada las rutas de medición suponían un total de 998 puntos de medición. Para el modelo de fallo deseado de la máquina se han previsto cuatro posiciones diferentes con las correspondientes rutas de máquina para el LaserTracer. La simulación ‘Monte Carlo’ dio como resultado para las desviaciones paramétricas una incertidumbre máxima de 1 µm o de 1 µrad para la configuración de medición planificada.
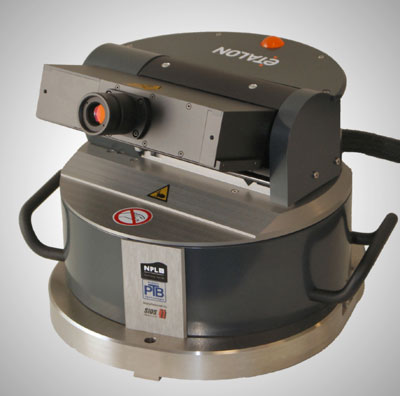
La calibración requiere muy poco tiempo
Los técnicos de medición elaboraron cuatro programas de máquina con un formato de código G para el control del centro de taladrado que se copiaron después al control mediante un soporte de datos. Se desactivaron las compensaciones disponibles. A continuación, se iniciaron los cuatro programas uno tras otro y transformaron el LaserTracer en los tiempos secundarios. Ya durante las mediciones fue posible afirmar la repetibilidad especificada de la máquina de menos de 2 µm. El desarrollo de un programa duraba menos de siete minutos. El proceso de calibración completo, incluidos los trabajos de preparación y transformación, requirió tan solo 90 minutos.
Los técnicos utilizaron un sistema de medición de temperatura de Etalon para poder tener en cuenta la dilatación de las reglas graduadas de los ejes para la calibración. Durante todo el tiempo de calibración, este sistema proporciona información detallada sobre las diferentes temperaturas de las reglas graduadas. Se han montado tres sensores muy cerca de las diferentes reglas graduadas. La transmisión de las temperaturas se realizó a través de un transmisor inalámbrico hacia la estación base. La estación base se conecta al ordenador de análisis que procesa las correspondientes correcciones. El resultado de la evaluación era que las temperaturas eran bastante estables pero que éstas variaban mucho de un eje a otro.
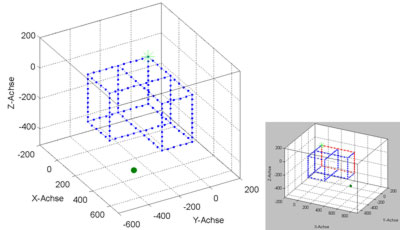
En base a las mediciones se ha calculado un modelo de fallo reducido, ya que para este tipo de máquina las desviaciones rotatorias del último eje carecen de importancia. De este modo, fue posible determinar las desviaciones de posición, las perpendicularidades de los ejes entre sí y, en parte, las inclinaciones, guiñadas y rodaduras. A continuación se copiaron los datos de corrección al control CNC y se activó la compensación.
'3D Error Compensation' muestra un gran efecto
Para mostrar la eficacia de la corrección aritmética de Fanuc '3D Error Compensation' sobre la precisión espacial, finalmente se ha vuelto a medir la máquina. La comparación de las desviaciones restantes con y sin la compensación activada mostró una clara mejora de todas las desviaciones paramétricas. Como media se redujo en un 77%, lo que se traduce en una mejora de la precisión con el factor 4. En la posterior prueba independiente según la norma ISO 230-2 y 6 con el software Trac-Check se confirmó este aumento de la precisión.
Los resultados obtenidos con Fanuc '3D Error Compensation' varían naturalmente en función de la medición y de las posibilidades mecánicas de la máquina. Pero siempre se conseguirá un plus de precisión. Concretamente para fabricantes de máquina-herramienta que ponen especial énfasis en la precisión de sus productos, la función '3D Error Compensation' es una opción de éxito de poco coste y gran provecho. Pero también los usuarios finales pueden beneficiarse de las nuevas posibilidades: cualquier máquina de tres a cinco ejes equipada con un control CNC de Fanuc de las series 30i o 31i-A5 puede ser medida con posterioridad y mejorada gracias a la función '3D Error Compensation'.
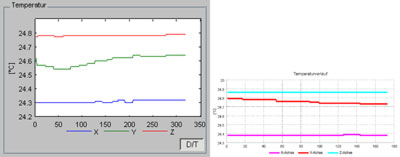
Especialista en calibración
La empresa Etalon AG, Braunschweig, está especializada en la calibración, la supervisión y el aumento de la precisión de máquinas de medición y máquinas herramienta. La empresa se fundó en el año 2004 como externalización de la Physikalisch Technische Bundesanstalt (PTB). En la actualidad tiene una red de distribución a nivel mundial. Clientes de renombre de la construcción de máquinas, de la técnica de medición industrial, en la construcción de vehículos y en la investigación apuestan por la tecnología de Etalon.
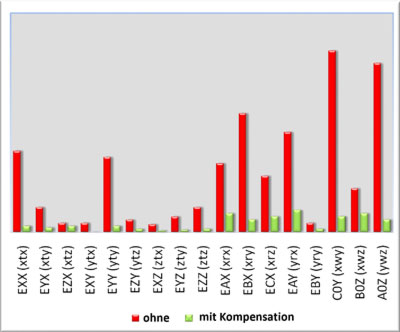