Reparación mediante soldadura de herramientas para trabajo en caliente
29 de julio de 2011
Los aceros de herramienta están divididos en 2 grupos, los aceros para trabajo en frío y los aceros para trabajo en caliente. Las herramientas de corte tales como los taladros, cuchillas de corte, herramientas de trimado, hojas de cizalla, etc., pertenecen predominantemente al grupo de herramientas para trabajo en frío. Estas herramientas están diseñadas para trabajar a baja temperatura (cortar, taladrar, conformar) en formas como perfiles, tubos, planchas, barras, etc., donde el calor se genera como resultado del proceso de trabajo de corte, conformado, taladrado y del proceso de fricción de la herramienta sobre el metal. La temperatura de la herramienta raramente alcanza los 250 °C, eliminándose la necesidad de utilizar metales base resistentes al calor.
En el caso de herramientas para trabajo en caliente, tales como estampas de forja, moldes de inyección, hojas de cizalla en caliente, rodillos de laminación en caliente, etc., el metal trabaja a elevadas temperaturas. En estos casos las propiedades requeridas son de resistencia a la temperatura elevada, buenas propiedades de templado y elevada resistencia al desgaste por fricción, presión e impacto a altas temperaturas.
Durante muchos años, la reparación de las herramientas deterioradas ha seguido un procedimiento estándar provocando enormes ventajas económicas y técnicas puesto que el acabado final mediante mecanizado o desbaste se reducía o era incluso innecesario. La producción de nuevas herramientas de corte en serie mediante recargue por soldadura es económico si el ahorro respecto al coste del metal base es superior que el coste de la soldadura. Es por ello que en general, sólo las herramientas de grandes dimensiones se fabrican mediante recargue con soldadura. Sin embargo, los costes no son siempre un factor decisivo. Utilizando un material base más blando, la resistencia al agrietamiento es superior y la posibilidad de recubrir la herramienta se hace más interesante, puesto que se evitan muchos problemas de los aceros base.
Métodos de soldadura
Soldadura con electrodos revestidos
En la soldadura de aceros de herramienta, la soldadura con electrodos revestidos cuenta aproximadamente con un 50% del mercado de los consumibles utilizados (productos comercializados por UTP).
Los electrodos revestidos de rutilo cuentan con un arco estable y suave que permite soldar a bajo amperaje. El cordón de soldadura es suavemente ondulado, con una apariencia lisa, ideal para soldar bordes cortantes. La escoria se desprende por sí sola.
Los electrodos de revestimiento básico crean un arco más intenso con una penetración mayor y un cordón de recargue más grueso. La apariencia del cordón no es tan fina como al utilizar el electrodo de rutilo. El depósito de soldadura tiene una elevada tenacidad. La escoria no se ha de retirar al realizar sucesivas pasada, lo que es una ventaja en largos trabajos de soldadura.
Siempre y que sea posible utilice la técnica de cordón en hilera, la ondulación o entramado debería evitarse. Si se necesitan varias capas es más conveniente aplicar 3 capas con un electrodo de 2,5 milímetros de diámetro en lugar de 2 capas con un electrodo de 3,2 milímetros de diámetro. Deposite cortos cordones, elimine la escoria e inmediatamente después golpee ligeramente el cordón. Utilice este procedimiento hasta obtener el recargue suficiente. Enfríe lentamente bajo una funda aislante o en horno. Puede ser necesario un tratamiento térmico posterior.
Soldadura TIG
La soldadura TIG es un proceso particularmente interesante para pequeñas herramientas y pequeños trabajos de reparación. La ventaja es que se pueden reparar complicados filos de corte y obtener formas detalladas. Un electrodo de tungsteno de pequeño diámetro permite al soldador concentrar una elevada temperatura en un punto pequeño, así como depositar el consumible de soldadura sin dañar el material base y sin producirle ninguna deformación. Para controlar el amperaje al mínimo posible, la máquina debería disponer de un interruptor controlador a la altura del pie del soldador. Las varillas TIG están disponibles en un amplio rango de aleaciones bajo denominación UTP. El gas protector debería ser Argón con una pureza del 99.996 % en volumen.
Soldadura MIG/MAG
El proceso de soldadura MIG/MAG es particularmente interesante para la deposición de grandes cantidades de consumibles de forma económica, bajo la marca UTP. Las aplicaciones más típicas son la producción de grandes hojas de cizalla con un material base poco aleado, el relleno de matrices de forja para cambiar el diseño, el recargue sobre conos y rodillos, etc.
Con la soldadura de arco pulsado se puede obtener depósitos sin proyecciones. Generalmente, la soldadura se realiza mediante hilo continuo de 1,2 ó 1,6 milímetros de diámetro. Para hilos de acero de elevada aleación se utiliza argón o una mezcla como gas de protección.
Los hilos tubulares (comercializados con la marca Soudokay) se utilizan cuando no están disponibles los hilos macizos de una aleación determinada, tales como en aleaciones de cobalto. Estos hilos se sueldan también con gas de protección. También es posible utilizar los hilos tubulares o incluso arco sumergido cuando se necesite una mayor velocidad de deposición, ya que también suelen estar disponibles en diámetros de hilo superiores (figura 1).
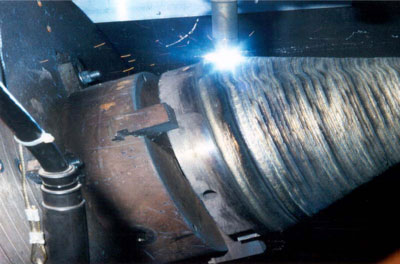
Normas para soldadura de aceros para herramientas
La experiencia de Böhler Welding Group, ante todo la marca UTP y Soudokay, en la reparación y mantenimiento de herramientas de trabajo en caliente permite hacer las siguientes sugerencias:
- Limpiar la zona de soldadura, eliminando todos los contaminantes, tales como pintura, aceite y grasa. Chaflanar los bordes. Preparar las zonas rotas y grietas dándoles forma de U. Analizar la superficie mediante líquidos penetrantes para asegurarse de la inexistencia de defectos o grietas.
- Seleccionar el material de relleno apropiado, así como el electrodo de trabajo y con el diámetro óptimo para cada caso.
- Los hilos deben estar perfectamente limpios (para evitar la porosidad) y los electrodos secos. Secar si es necesario siguiendo las recomendaciones del suministrador.
- Los aceros de herramienta no se suelen soldar a temperatura ambiente. El precalentamiento y la temperatura de paso de cada capa está determinado por el tipo de material base, el tamaño y la forma de la herramienta (peligro de endurecimientos puntuales y agrietamiento). En algunos casos el precalentamiento puede alcanzar temperaturas de 400 °C, aunque para pequeñas reparaciones la temperatura de precalentamiento podría mantenerse a 150 °C.
- La soldadura debe realizarse con la mínima cantidad de aportación calorífica posible, lo que significa utilizar el mínimo amperaje y voltaje posible. Limpiar el cordón de soldadura a menudo, eliminando los residuos y la escoria.
- En las herramientas para trabajo en frío susceptibles a agrietarse aplicar cordones de soldadura cortos con electrodos de pequeño diámetro o hilo para evitar el riesgo de grietas producidas por las tensiones de contracción.
- Para cambiar el diseño de las herramientas, las soldaduras deberían realizarse en condiciones de recocido suaves y con una temperatura de precalentamiento elevada.
- El depósito de soldadura debe ser golpeado inmediatamente después de la deposición de la soldadura y antes que la temperatura descienda de 350 °C, siendo esta la mínima temperatura entre pasadas para aceros de herramienta altamente aleados. Nunca golpear el material en frío.
- Depositar material en exceso (1,5-2 milímetros) para permitir un correcto mecanizado/amolado.
- Tras el proceso de soldadura, se debe dejar enfriar el material lentamente y en algunos casos, realizar un recocido para evitar las tensiones de soldadura. El tratamiento térmico posterior debe realizarse cuando se producen depósitos de soldadura de grandes dimensiones, tales como el relleno para el cambio de diseño de la estampa.
Soldadura de herramientas para trabajo en caliente
Los aceros para trabajo en caliente tienen, debido a su composición química, alta resistencia al calor, retención de la dureza y buena resistencia al desgaste a elevadas temperaturas, presión y fricción hasta 550 °C (tabla 1).
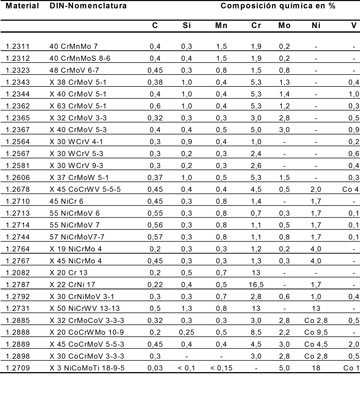
Los aceros NiCrMo son, debido a su elevada tenacidad, particularmente interesantes contra condiciones de alto impacto (1.2713, 1.2714).
La soldadura de aceros para trabajo en caliente se puede realizar con consumibles de acero martensítico, endurecibles por trabajo y endurecibles por precipitación (tabla 2). Los aceros CrMo deben precalentarse a una temperatura aproximada de 400°C y los aceros NiCrMo a 300°C (figura 2).
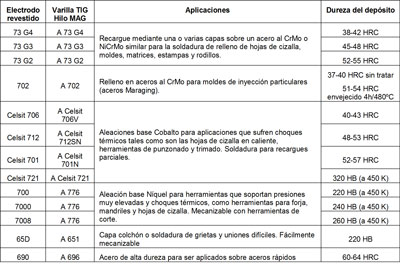
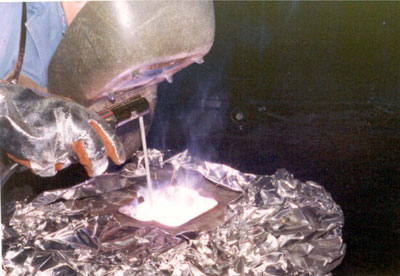
La soldadura puede realizarse mediante consumibles con características similares al metal base, obteniendo la dureza requerida. Estos aceros de herramienta deberían ser sometidos a un tratamiento de relajación de tensiones a una temperatura aproximada de 550°C cuando se deposita una cantidad substancial de material.
Para el recargue de moldes de inyección se recomienda el uso de un material martensítico endurecible por envejecimiento (acero Maraging, UTP 702), debido a su alta resistencia al desgaste (figura 3). Para este tipo de reparación la herramienta se ha de precalentar a una temperatura aproximada de 150 °C y soldado manteniendo esta temperatura. El material depositado tiene una dureza aproximada de 37 HRC. El endurecimiento por envejecimiento a 480°C durante 3 ó 4 horas produce una dureza de la herramienta de 53 HRC.
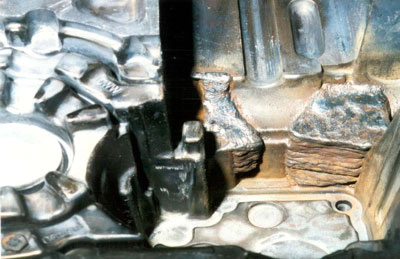
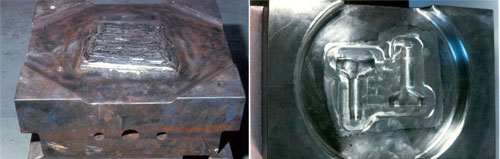
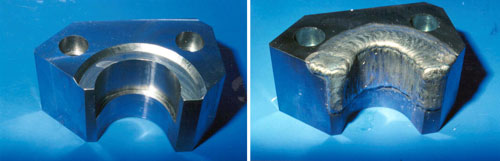
Soldadura de aceros rápidos
Los aceros rápidos tienen, dependiendo de su composición química y tratamiento térmico, una gran retención de dureza y de resistencia a la temperatura hasta los 600 °C. Las herramientas de corte producidas mediante aceros rápidos mantienen su filo largamente a temperaturas elevadas dotándolas de buenas propiedades de corte (figura 6).
Los aceros rápidos se utilizan también para herramientas de corte en frío ya que tienen una buena combinación de tenacidad y resistencia a la abrasión. Estas propiedades se obtienen debido a que contienen un elevado porcentaje de carburos especiales.
Para reparar aceros rápidos se utiliza UTP 690 o varilla TIG UTP A 696. El electrodo revestido de rutilo es fácil de utilizar y se distingue por su arco, superficie del cordón suave y escoria autodesprendible.
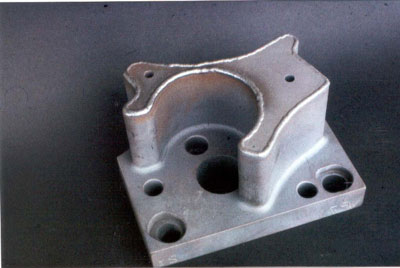
Estos consumibles se han desarrollado predominantemente para la producción de nuevas herramientas de corte utilizando materiales base de baja aleación o no aleados. También se utilizan para reparar herramientas grandes de corte y conformado. La dureza del depósito sin tratamiento es de alrededor de 60 HRC. Es necesario un segundo o tercer revenido a 550 °C para eliminar la austenita retenida (durante el enfriamiento la austenita transforma a martensita), dando una dureza final de 64 ó 65 HRC (endurecimiento secundario).
Cuando se reparan filos de corte, la zona dañada se ha de limpiar y precalentada a 150 °C. Este precalentamiento es suficiente si el deterioro es pequeño y/o las grietas no penetran en el material base. Si se necesita recargar grandes superficies, la herramienta se ha de precalentar entre 450 y 600 °C.
Para pequeñas reparaciones utilizar la antorcha TIG con un electrodo de tungsteno de pequeño diámetro. Usar el mínimo amperaje posible, fundir la superficie cuidadosamente y depositar el hilo TIG en cordones en hilera.
En definitiva, UTP y Soudokay ofrecen una solución personalizada a cada tipo de acero y aplicación ofreciendo un consumible de soldadura adecuado (figura 7).
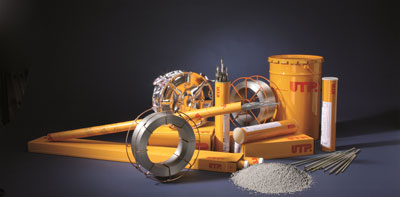
Nuevos desarrollos: UTP 750 y SK D35-G
Se trata de un material resistente al calor, para tanto grandes reconstrucciones como pequeñas reparaciones, particularmente expuestas a desgaste por fricción metal-metal y tensiones debidas a los choques térmicos. Tiene una estructura principalmente martensítica con una pequeña cantidad de ferrita. Algunas aplicaciones donde utilizar este consumible serían moldes, mandriles, herramientas de trimado, hojas de corte en caliente, herramientas de extrusionado, matrices de forja y herramientas sometidas a alta presión para conformado del acero. Debido a sus excelentes propiedades de deslizamiento metal-metal, es muy interesante para superficies deslizantes y de guía, aguantando también el desgaste por fatiga y cavitación. El resistente al revenido hasta 650 °C, resistente a la oxidación hasta 900 °C, nitrurable y resistente a la corrosión.
La dureza del depósito sin tratar es 48-52 HRC y está constituido por una estructura martensítica bastante tenaz. Tras un recocido a 850-900 °C la dureza es de aproximadamente 35 HRC, el depósito templado desde 1000°C-1150°C en aire es 48-52 HRC y tras el revenido a 700 °C es de aproximadamente 40 HRC. La composición química se encuentra en la tabla 3. La pieza debería precalentarse entre 150-400 °C dependiendo de su composición química, pudiéndose realizar un máximo de 4 pasadas.

El cobalto tiene un efecto endurecedor de la matriz del depósito y le da una resistencia especial al reblandecimiento con la temperatura. Además previene el revenido del acero hasta temperaturas anormalmente elevadas. El níquel aporta una mejora de la tenacidad de la matriz. Una de las ventajas más importantes que reporta el empleo del níquel, es evitar el crecimiento de grano en tratamientos térmicos, lo que sirve para conseguir elevar la tenacidad. Los aceros al níquel sometidos a temperaturas demasiado elevadas, quedan después del temple y revenido con muy buena tenacidad. Experimentalmente se observa que con los aceros aleados con níquel se obtiene para una misma dureza, un límite de elasticidad ligeramente más elevado y mayores alargamientos y resistencias que con aceros al carbono. El cromo aparte de mejorar la resistencia a la oxidación del depósito, ofrece (como también el molibdeno) un aumento de la resistencia al desgaste y de la dureza del depósito al combinarse con el carbono (formando carburos de cromo y molibdeno). El cromo mejora también la templabilidad, impide las deformaciones en el temple y aumenta la inoxibilidad.
Los fluxes o fundentes que llevan estos revestimientos son especiales. Se tratan de fundentes multicomponente con baja humedad que permiten obtener revestimientos con valores de tenacidad atípicamente elevados.
Referencias
- www.utp.de
- P.Crook, Cobalt and cobalt alloys, Properties and Selection: Irons, Steels, and High Performance Alloys, Vol 1, ASM Handbook, 1990, p 446-454
- W.I.Silence, Effect of Structure on Wear Resistance of Co-, Fe- and Ni-base Alloys, Wear of Materials, American Society of Mechanical Engineers, 1977, p.77
- E.B.Hinshaw, Welding of Nickel Alloys, Welding, Brazing and Soldering, Vol. 6, ASM Handbook, ASM International, 1993, p.740-751
- B.B.Weiss, G.E.Rotke and R.Stickler, Physical Metallurgy of Hot Ductility Testing, Weld J, Oct 1970, p.471-422
- J.M.Guilemany, J.M.Miguel, S.Armada, S.Vizcaino, F.Climent, Use of the Scanning White Light Interferometry in the characterization of wear mechanisms in thermal spray coatings, Mat. Characterization 47, 2001, 307-314
Agradecimientos
El equipo técnico quiere agradecer el excelente trabajo realizado por Pilar Lombardo, Emma Ribas y Cynthia Morales, sin el cual no hubiera sido posible publicar dicho artículo.