Nuevos avances en el moldeo de aleaciones de magnesio
1 de diciembre de 2009
En el pasado, el desarrollo de las aleaciones de magnesio ha estado dirigido, principalmente, a reducir el peso de estructuras en el campo militar y aeronáutico. En el presente, el énfasis se ha centrado en reducir el peso de los vehículos en el campo de la automoción, reduciendo así el consumo de combustible y por consiguiente, la emisión de gases. Este factor es esencial en la sociedad actual por el impacto que tiene en la opinión pública las cuestiones medioambientales.
Es preciso resaltar que la utilización del magnesio en la industria de la automoción no es una innovación. En los años 30 empezó a ser frecuente incluir piezas de magnesio colado en los automóviles, siendo el VW-Beetle el ejemplo más destacado. Desde que se comenzó su fabricación en 1939, piezas como el cárter, la rueda dentada del eje de levas, la carcasa de la caja de cambios, muchas tapas y el eje de un generador eléctrico se fueron añadiendo hasta alcanzar un peso total de magnesio de 17 kilos en 1962, que implicaba una reducción de 50 kilos en el peso del vehículo. La producción del VW-Beetle utilizó casi 21.000 toneladas de aleaciones de magnesio en 1960 y el Grupo Volkswagen alcanzó un consumo total de 42.000 toneladas de aleaciones de magnesio en 1972, hasta que se redujo drásticamente su uso debido al cambio de refrigeración por aire a refrigeración por agua.
Actualmente, en la industria de la automoción, las aleaciones de magnesio se están utilizando tanto en el motor (cárter, cajas de engranajes, etc.) como en la estructura (asiento del motor, soporte del radiador, marco interno de la puerta, marco de techo convertible, etc.) o el interior (volante, faros, marcos de los retrovisores externos, etc.). Con el fin de reducir el peso total del vehículo, las aleaciones de magnesio han ido sustituyendo a sus competidoras en diferentes componentes importantes del vehículo, como son la caja de cambios o el depósito de combustible.
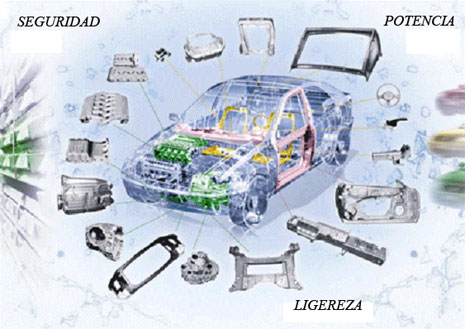
Aun siendo la automoción la industria dominante que consume la mayor proporción de aleaciones de magnesio, también se está extendiendo a otros sectores. El sector aeronáutico, por contrario, se resiste a sustituir piezas fabricadas en otros materiales por piezas de aleaciones de magnesio, debido principalmente a las condiciones extremas que se pueden alcanzar a alturas muy elevadas y a su deficiente tenacidad. No obstante, su uso comienza a introducirse en la construcción de helicópteros, ya que las condiciones de servicio no son tan severas como en la de los aviones y pueden desempeñar perfectamente su función.
El espectacular auge en eficiencia experimentado por las celdas de combustible en la última década ha impulsado de forma notable el desarrollo de dispositivos para la en acumulación de hidrógeno. La aplicación de este tipo de dispositivos a la industria del automóvil se encuentra en fase avanzada, estando previsto su uso en vehículos de serie dentro de pocos años. Dado su carácter móvil, estos sistemas precisan de una fuente de hidrógeno altamente eficaz. La solución del problema de cómo acumular H2 de forma eficiente, es, por tanto, de gran importancia. Hay cierta unanimidad en que la acumulación de hidrógeno en hidruros metálicos es el método más eficiente. Estos compuestos proporcionan, ante todo, seguridad en relación con los peligros inherentes a la combustión del hidrógeno, así como la mejor densidad volumétrica de hidrógeno y una completa reversibilidad. El candidato ideal es el hidruro de magnesio (MgH2), un compuesto abundante, de bajo coste económico y ligero, capaz de contener 7,6% de hidrogeno en peso.
Por todo lo expuesto anteriormente, la utilización de aleaciones de magnesio presenta unas expectativas muy prometedoras.
Aspectos preliminares en el moldeo de aleaciones de magnesio
Uno de los parámetros a considerar durante el moldeo de aleaciones de magnesio, es el efecto de los elementos de aleación en la fluidez del caldo. Una baja fluidez del caldo, puede originar una mala calidad de la pieza durante el moldeo. La figura 1 presenta el diagrama de fluidez del sistema Mg-Al-Zn (serie AZ), que son las aleaciones comerciales más comúnmente utilizadas por la industria. Por debajo del 2% de concentración de cinc, el caldo presenta una buena fluidez para su colabilidad. Sin embargo, para mayores concentraciones de cinc, se produce el agrietamiento en caliente durante el moldeo.
Un serio problema que plantea el uso de las aleaciones de magnesio es su avidez por el oxígeno, especialmente en estado líquido, que se manifiesta como una combustión que puede llegar a ser explosiva. Es, por tanto, necesario la utilización de atmósferas protectoras para evitar la ignición del caldo. La utilización de gases inertes como el argón tiene el problema de su elevado precio, por lo que su uso se ha restringido a la fabricación de aleaciones madre en hornos de inducción. Los gases que se utilizaron industrialmente son una mezcla de 5% SF6+ 95% CO2. El SF6 es un gas muy pesado que desplaza al oxígeno de la superficie del caldo, mientras que el CO2 actúa como gas portador del SF6. El mayor inconveniente de esta mezcla es que el SF6 contribuye a potenciar el efecto invernadero. Por esta razón, se han desarrollado nuevas mezclas de gases basadas en compuestos orgánicos (hidrofluorocarbonos (HFC)).
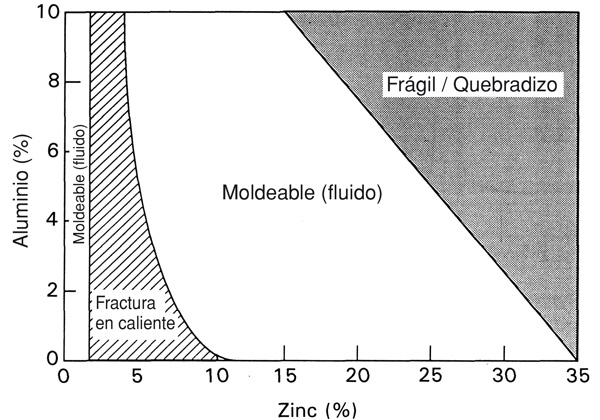
Técnicas de moldeo
Existen diferentes técnicas que se utilizan desde el punto de vista industrial. En este artículo se han dividido en dos clases, dependiendo de la aplicación o no de presión durante el moldeo. Por un lado, existen las técnicas tradicionales como el moldeo en arena, moldeo a la cera perdida o el moldeo en coquilla. El principal inconveniente de estas técnicas es la presencia de poros que reducen las propiedades mecánicas de las piezas. En las últimas dos décadas se han diseñado nuevos métodos de moldeo, que implican el aplicar una por presión, a fin de minimizar la presencia de poros. Entre estas técnicas, se pueden enumerar el ‘squezee casting’, el moldeo por inyección, el moldeo tixotópico y el reo-moldeo. A continuación se describirán un poco más en detalle cada una de ellas.
Moldeo de aleaciones de magnesio sin asistencia de presión
El moldeo en arena se basa en el vertido del caldo sobre un molde de arena, con la forma de la pieza que se quiere obtener. Este molde se genera a partir de una réplica de la pieza a fabricar. Es preciso el uso de aditivos tanto para eliminar la humedad de la arena del molde como para prevenir reacciones entre el caldo y el molde.
La mayor ventaja del moldeo en arena es que permite producir piezas de gran tamaño y formas complejas de la inmensa mayoría de las aleaciones de magnesio a precios muy competitivos. Sin embargo, entre sus desventajas destacan las bajas tolerancias del producto final, que suelen requerir un pulido o mecanizado de la superficie, y que presenta una baja productividad en relación con otras técnicas de moldeo ya que el molde se destruye para recuperar la pieza. Las velocidades de solidificación durante el moldeo en arena es mucho menor que otro tipo de moldeo.
El moldeo a la cera perdida es una técnica similar al moldeo en arena, si bien la fabricación del molde es mucho más compleja. La ventaja del moldeo a la cera perdida con respecto al moldeo en arena es que presenta una alta velocidad de producción, un excelente acabado superficial y que además se pueden fabricar piezas con formas complejas. Al igual que el moldeo en arena se puede aplicar a la inmensa mayoría de las aleaciones de magnesio. Como desventajas, cabe destacar, que es un proceso largo, requiere de un equipamiento caro y además, también requiere del uso posterior de técnicas de endurecimiento mediante tratamientos térmicos y/o superficiales.
Finalmente, en el moldeo en coquilla, el caldo se vierte sobre un molde metálico, generalmente de acero o cobre. El moldeo en coquilla presenta unas altas velocidades de producción de piezas. Su acabado superficial es excelente y las microestructuras obtenidas son más finas que la resultante del moldeo por arena o a la cera perdida. Al igual que las otras dos técnicas, se puede aplicar en la inmensa mayoría de las aleaciones de magnesio, excepto en el sistema (Mg-Zn-Zr). Como desventajas de proceso, cabe destacar que es necesario el recubrimiento de la coquilla para alargar su período de vida útil.
Moldeo de aleaciones de magnesio con aplicación de presión
Moldeo por inyección en cámara fría
La carga de metal fundido se transporta mediante una cuchara de colada, desde el crisol a un contenedor donde un émbolo accionado hidráulicamente empuja el metal hacia el interior del molde. Es importante mencionar la necesidad de introducir una cantidad de material mayor del necesario para fundir la pieza. Este material adicional se aplica con el fin de compensar la contracción que se produce durante la solidificación.
El moldeo por inyección en cámara fría consta de cuatro pasos. En primer lugar, el molde se cierra y el metal fundido se pasa, mediante una cuchara de colada, al contenedor de la cámara fría. A continuación, el émbolo empuja el metal fundido hacia el interior de la cavidad del molde, donde se mantiene la presión hasta que solidifica. Seguidamente, el molde se abre y el émbolo avanza, para garantizar que la pieza fundida permanezca en molde eyector. Finalmente, los expulsores empujan la pieza fundida, la sacan del molde eyector y el pistón retorna a su posición original.
El moldeo por inyección en cámara fría permite mayores presiones y velocidades de inyección que el moldeo en cámara caliente, lo que permite producir piezas más compactas. Además, los costes del mantenimiento del equipo son mucho menores. Sin embargo, la precisión en el control de la temperatura del metal no es grande, lo que implica una menor fluidez y menor capacidad para producir piezas con paredes de poco espesor. Otra desventaja del moldeo por inyección en cámara fría es que el metal esta expuesto a la oxidación, y por tanto requiere el empleo de un gas protector.
Moldeo por inyección en cámara caliente
El émbolo y el cilindro, que forman el mecanismo de inyección, se sumergen en el metal fundido que se encuentra en el crisol (o recipiente refractario) que es parte integral de la máquina. Se aplica a aquellas aleaciones que no atacan o erosionan al crisol donde se contiene el caldo fundido
En primer lugar, se cierra el molde y se eleva el émbolo, abriendo el orificio y permitiendo que el metal fundido llene el cilindro. Seguidamente, el émbolo desciende y sella el orificio empujando el metal fundido hacia el molde. La presión se mantiene hasta que el caldo solidifica. A continuación, se abre el molde. El émbolo retorna, permitiendo que el metal fundido residual retorne a través de la tobera y el sifón. Finalmente, se expulsa la pieza.
En este caso, es posible el control preciso de la temperatura del metal, mejora la fluidez y permite menores presiones de inyección, lo que somete al equipo a menores esfuerzos. Una mayor fluidez permite un mejor llenado de la cavidad, lo que produce piezas más compactas, y permite paredes de menor espesor. Además, el cilindro, el cual está sumergido en la colada, se llena automáticamente, lo que acorta el tiempo del ciclo, y facilita el control de la temperatura del metal. Es importante mencionar que el metal fundido es sometido a una menor oxidación que en el caso de la cámara fría.
Como desventajas cabe destacar que, al emplearse presiones de inyección y velocidades más bajas, las piezas fundidas pueden ser menos compactas y contener mayor porosidad. Es evidente que el moldeo por inyección en cámara caliente tiene mayores costos de mantenimiento que la inyección en cámara fría.
Moldeo en estado semisólido, tixotópico y el reo-moldeo
En los procesos de moldeo por inyección la aleación se funde y se inyecta sobre un molde. El hecho de tener el material completamente líquido presenta algunos problemas. En primer lugar, la gran diferencia en peso atómico entre el magnesio y los elementos de aleación (Al, Zn, Mn, Ca, Si, Sr, tierras raras, …) provoca la segregación de los metales pesados hacia la parte inferior del crisol. En segundo lugar, la alta presión de vapor de magnesio y cinc causa la evaporación de estos elementos y la variación de la composición de las aleaciones respecto a su composición nominal. Por último, existe un grave problema de oxidación debido a la afinidad del magnesio liquido por el oxigeno. La solución a estos inconvenientes se basa en trabajar en estado semisólido entre las temperaturas de líquido y sólido.
El proceso del moldeo tixotópico es la inserción en un molde (o herramienta) de acero, de una aleación en estado semisólido para fabricar un componente en su forma final, que es automáticamente extraído. Se parte de virutas de magnesio o aleación de magnesio, las cuales se llevan al estado semisólido. La presencia de una fracción del material en estado sólido disminuye la contracción que se experimenta durante la solidificación del líquido, lo que produce una reducción de la porosidad hasta de un 50% y el aumento de la resistencia mecánica del material y de la ductilidad. Es interesante mencionar que las piezas están libres de inclusiones y óxidos. Al igual que en el moldeo por inyección, las velocidades de solidificación son diferentes en cada parte de las piezas. Estas inhomogeneidades provocan variaciones de la microestructura y de las propiedades mecánicas a lo largo de la pieza.
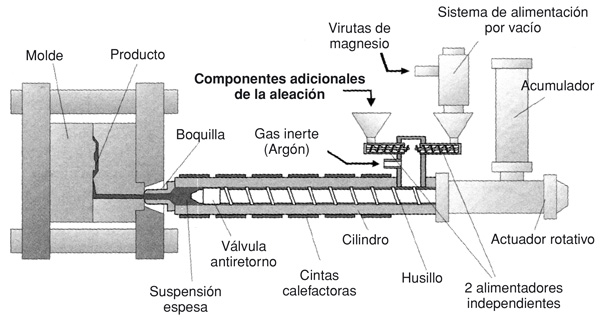
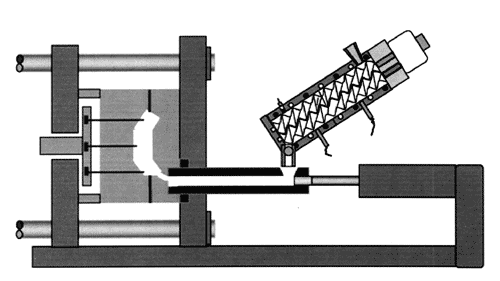