Digitalización y sistemas de producción conectados marcan las tendencias del futuro de la producción
El estado operativo de las máquinas conectadas puede consultarse y evaluarse con fines estadísticos en todo momento, lo cual, unido a herramientas inteligentes gestionadas mediante sistemas igualmente inteligentes, conforma el entorno de los procesos industriales del futuro. El valor añadido para los usuarios se multiplica si implantan estructuras de servicio avanzadas en sus instalaciones, tales como vidrios inteligentes o proyecciones de realidad aumentada de herramientas complejas. Un mundo digital en el que también coexisten soluciones orientadas a la gestión segura de los datos generados y la revolución tecnológica que supone la fabricación aditiva junto a materiales innovadores, como los polímeros reforzados con fibra de carbono (CFRP), que se emplean para fabricar, por ejemplo, husillos de máquina-herramienta, agilizan y optimizan los procesos, el dimensionamiento adaptado de las herramientas y la mayor eficiencia de estas mejoran sensiblemente la productividad en la fabricación de componentes de precisión por corte de viruta. A continuación, se describen algunos ejemplos de las tendencias y los conceptos que marcan la pauta de la tecnología de producción actual.
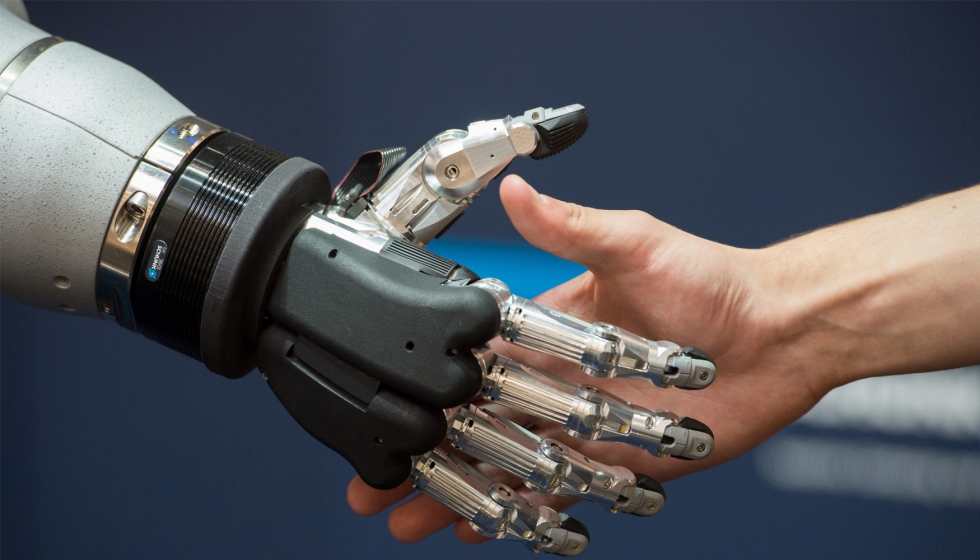
Fabricación aditiva
La fabricación aditiva se está haciendo rápidamente un hueco en el entorno industrial. Uno de los aspectos que a todas luces está ganando importancia es la garantía de calidad en la fabricación generativa, especialmente cuando se trata de componentes importantes para la seguridad en el sector aeronáutico. Pero la fabricación aditiva son muchas tecnologías, no una. Por ejemplo, la soldadora por deposición láser de Trumpf, que consiste en que, mediante el láser se genera un baño fundido en la superficie del componente en el cual se introduce el polvo metálico con ayuda de un inyector. Este proceso de producción se emplea para aplicar capas de protección contra el desgaste, reparar componentes y crear nuevas estructuras. También DMG MORI cuenta con su propia tecnología: con la nueva Lasertec SLM pueden fabricarse componentes de 300 x 300 x 300 mm como máximo a partir del lecho de polvo. La Lasertec 65 3D puede incluso fabricar componentes con un diámetro de 650 mm y una altura máxima de 560 mm mediante un proceso aditivo.
Pero las capas funcionales y las estructuras de los componentes también se pueden crear sin utilizar láser, con una tecnología de recubrimiento mediante impresión en 3D desarrollada por la firma germana J.G. Weisser Söhne GmbH. Mediante un proceso de impresión rotativa, el material simple semiacabado se deposita en la superficie del componente, fundiéndose por efecto de la fricción generada e integrándose en él. Una tecnología pionera pero que, presenta de momento una desventaja importante: en la fase actual de desarrollo de esta tecnología no es posible crear estructuras complejas.
Por otra parte, el proceso de deposición de polvo de metal ideado por Hermle tampoco requiere tecnología láser. Se trata de un proceso de inyección térmica en el que el metal en polvo se acelera hasta alcanzar altas velocidades con un gas de arrastre y se aplica en capas mediante una boquilla sobre la superficie del componente. Entre las ventajas de esta técnica destaca el hecho de que puede emplearse prácticamente cualquier material, siempre que pueda reducirse a polvo, así como la posibilidad de aplicar mezclas de hasta siete materiales distintos en cualquier proporción en superficies de forma no predeterminada.
El paquete de software 3DXpert de la empresa estadounidense 3D Systems (Rock Hill, Carolina del Sur, EE UU) constituye una solución integral para la fabricación aditiva con metales. Esta empresa, que también fabrica máquinas de impresión en 3D, cuenta con una solución que ofrece una alternativa de creación aditiva de componentes apta para diversos productores y procesos. Una vez que se importan los datos y se coloca el componente, resulta sencillo crear y optimizar sus estructuras y geometrías de apoyo para la fase de producción.
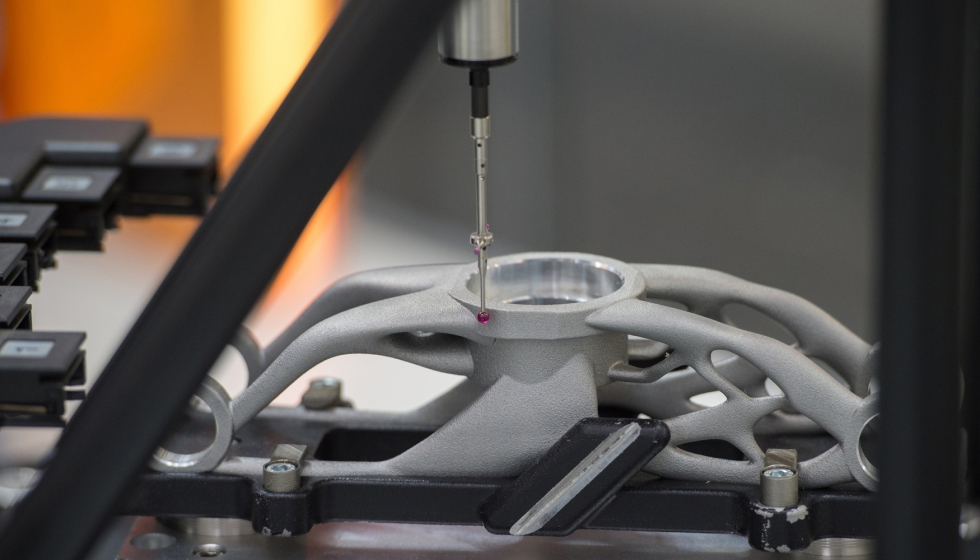
Unidos hacia la Industria 4.0. La iniciativa sectorial de la asociación VDW para la producción conectada
La Asociación Alemana de Fabricantes de Máquina-Herramienta (VDW) ha puesto en marcha una iniciativa sectorial en materia de producción conectada. Su objetivo es desarrollar y aplicar una norma para reunir un conjunto muy diverso de sistemas de control de máquinas en una interfaz común. En la fase inicial del proyecto interviene un equipo central integrado por VDW y empresas de primera línea como DMG MORI, Emag, Grob, Heller, Liebherr-Verzahntechnik, United Grinding y Trumpf. En el marco de esta iniciativa sin precedentes de colaboración entre VDW y empresas del sector de la máquina-herramienta se elaborarán equipos adaptados al futuro digital y se sentarán las bases para la ansiada Industria 4.0. El objetivo es conectar y unificar las operaciones de producción mediante la interacción segura con sistemas de procesamiento electrónico de datos (PED) y nubes.
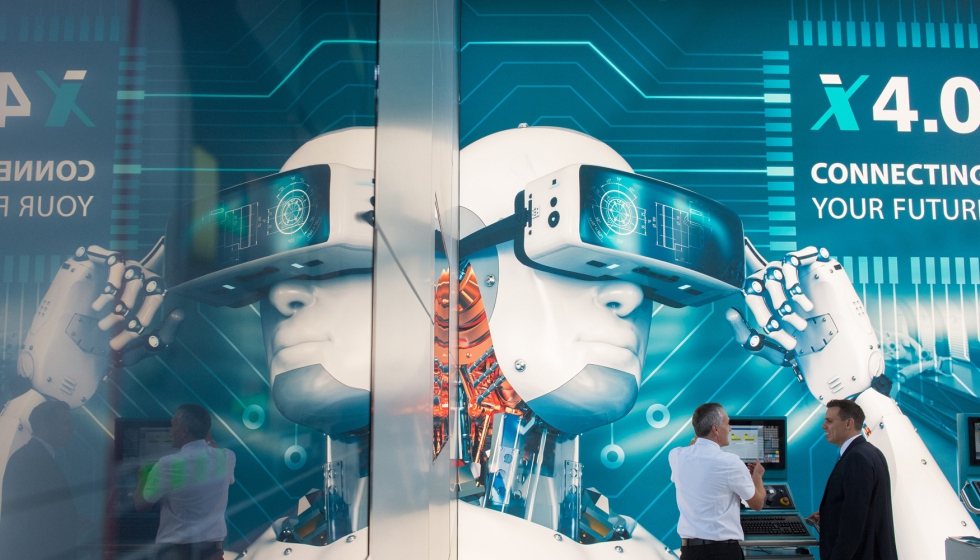
Herramientas inteligentes gracias a la tecnología integrada de sensores
El fabricante de herramientas Sandvik Coromant (Sandviken, Suecia) ha desarrollado una serie de herramientas que representan su visión de Industria 4.0, bajo el paraguas de la plataforma CoroPlus, una tecnología de sensores integrados en herramientas y portaherramientas empleados durante los procesos de mecanizado. En el caso de las barras de perforación con vibración amortiguada —herramientas silenciosas— los últimos pasos de mecanizado de los componentes complejos pueden supervisarse mediante sistemas basados en aplicaciones. El cliente puede pues comprobar si la herramienta se ha acoplado correctamente y el nivel de estrés térmico que soporta la barra de perforación. Por otra parte, los portaherramientas inteligentes envían datos sobre los tiempos de ejecución o el nivel de carga y de batería a una aplicación, posibilitando así el mantenimiento predictivo. Los cabezales de perforación fina pueden ajustarse al milímetro gracias a una aplicación diseñada para la perforación de orificios con diámetros muy precisos.
Por su parte, BIG Kaiser (Rümlang, Suiza) ha desarrollado una tecnología similar con la ventaja de que no es necesario realizar ajustes manuales constantes en el dispositivo de preconfiguración de la herramienta, la cual puede desplegarse y replegarse para adaptarse a distintos diámetros directamente mediante una aplicación cargada en una tableta. Ello permite acortar la cadena de procesos y reducir los tiempos no productivos dedicados al ajuste de herramientas.
Herramientas avellanadoras inteligentes para el mecanizado del interior de componentes
Hermann Bilz, procedente de Esslingen, en la región de Suabia, cuenta con muchos años de experiencia en la producción de herramientas de avellanado. Estas fresas se emplean cuando el mecanizado se realiza en una superficie que solo es accesible a través de un orificio, como ocurre con las carcasas cerradas. Si se invierte el sentido de rotación, la cuchilla de la herramienta se despliega. Para poder extraer la herramienta del orificio tras el mecanizado, es necesario replegar la cuchilla. En el marco de un proyecto emprendido conjuntamente con O. Bilz y EWS, Hermann Bilz ha desarrollado una herramienta avellanadora que permite supervisar el proceso de replegado de la cuchilla. Los datos se transfieren al sistema de control de la máquina mediante un protocolo de comunicación desarrollado específicamente con dicha finalidad, el cual impide que la herramienta entre en contacto con algún punto de la superficie del componente si la cuchilla no se repliega correctamente.
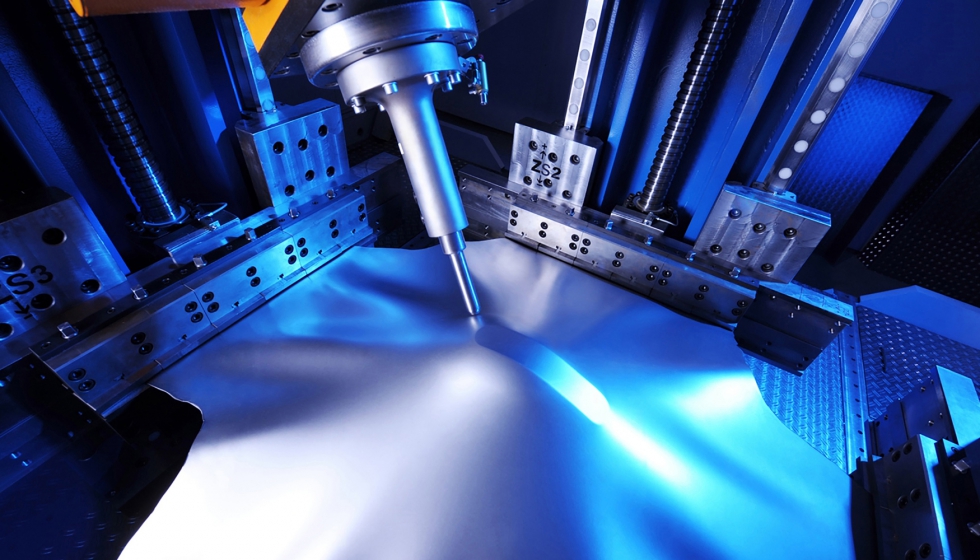
También los fabricantes de herramientas están desarrollando soluciones inteligentes, dotadas de sensores y tecnología que aporta información durante las operaciones de mecanizado. Foto: Thilovogel.
Nueva interfaz entre máquina-herramienta y módulos ciberfísicos complementarios
La Industria 4.0 ofrece interesantes avances del futuro conectado de la tecnología de producción. Destaca el proyecto de investigación financiado con fondos públicos BazMod, cuyo objetivo es desarrollar una interfaz independiente y estandarizada para intercambiar medios, datos y energía entre máquinas-herramienta y distintos módulos ciberfísicos complementarios. Dicha innovación permitirá ampliar la funcionalidad de las máquinas-herramienta mediante sistemas ciberfísicos basados en sensores/actuadores (CPS) integrados en los equipos previamente en función del fabricante del que se trate.
Sistemas integrales de gestión de herramientas
Mención aparte merece la gestión integral de herramientas. Numerosos fabricantes de herramientas de precisión, como Iscar, Gühring o Sandvik, y empresas especialistas en metrología, como Zoller GmbH (Pleidelsheim), cuentan con soluciones de almacenamiento inteligente para herramientas, componentes y accesorios. Este tipo de sistemas son mucho más que una forma de tener las herramientas ordenadas. El usuario puede calcular los costes exactos asociados a la herramienta y cada uno de sus componentes, asegurarse de que las herramientas siempre están disponibles al instante y evitar seleccionar la herramienta incorrecta. Asimismo, los sistemas inteligentes se conectan a la máquina-herramienta y reciben información sobre cualquier desperfecto, activan el proceso de pedido al vendedor y proporcionan al operario una herramienta de características constructivas idénticas. Los flujos de herramientas en el entorno de producción son de este modo mucho más claros y transparentes.
Iniciativas de digitalización: el camino hacia la fábrica digital
Existen numerosas innovaciones en torno a IIoT (Internet industrial de las cosas). Es el caso de Adamos, que comenzó a funcionar el 1 de octubre de 2017 con la participación de doscientos expertos. Esta iniciativa nació de una alianza entre DMG MORI, Dürr, Software AG y Zeiss ASM PT y su objetivo es ofrecer soluciones para la producción digital conectada. DMG MORI utiliza además Open Connectivity para acceder a su ecosistema Celos y posibilitar un flujo de datos digitalizados y armonizados, incluso con equipos de terceros y en entornos de trabajo analógicos, acercándose así un paso más a su visión de fábrica digital.
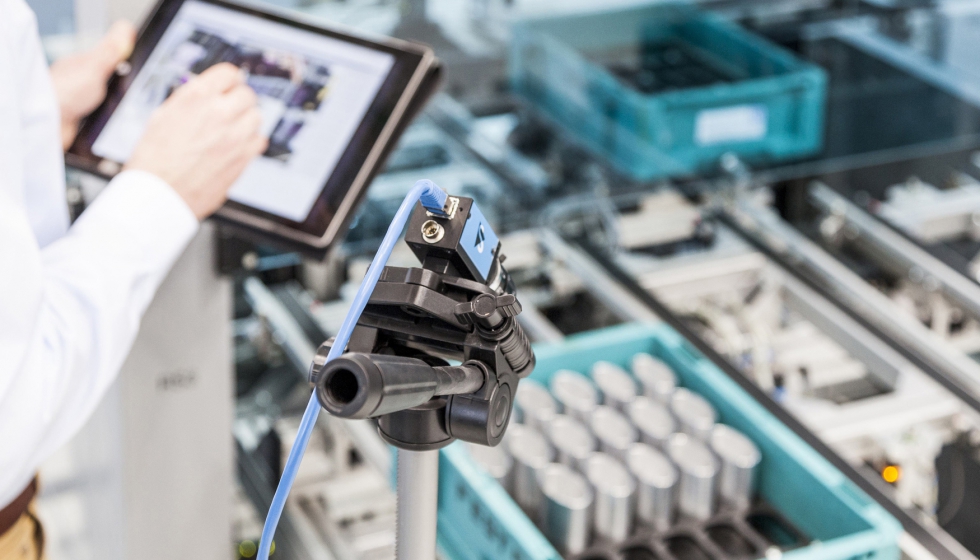
Conectividad de datos ya filtrados
Los sistemas pueden conectarse a distintos niveles. Lo que los usuarios de máquina-herramienta deben plantearse es si todos los datos deben enviarse a la nube inmediatamente. La respuesta es no, al menos, así lo afirma la empresa Bosch Rexroth, de Lohr am Main. Actualmente la red no posee la capacidad necesaria para transferir a la nube la ingente cantidad de datos que ya pueden captar los sensores de la máquina-herramienta. Por este motivo, Bosch Rexroth propone su Data Analytics Server, instalado en una máquina del fabricante Pfiffner. Su propuesta consiste en proporcionar capacidad de computación local adicional instalada en el armario de control de la máquina-herramienta para poder recopilar, almacenar y analizar datos del equipo y los procesos. Los datos pueden filtrarse de antemano para enviar a la nube comprimidos solo aquellos realmente necesarios y evitar sobrecargar las líneas de datos. Resta determinar qué datos deben enviarse, cosa que puede decidir el propio usuario empleando herramientas analíticas y programas de configuración que requieren un conocimiento previo mínimo.
Mecanizado conectado, pero sin la nube
Por su parte, el Connected Machining, de Johannes Heidenhain GmbH, permite gestionar el entorno de trabajo digital de forma fluida: procesos transparentes, secuencias de trabajo más breves y uso eficaz de los datos. En la misma línea Heidenhain cuenta con su herramienta Remote Desktop Manager, con la que los usuarios pueden acceder a ordenadores de la red y al software que está instalado en ellos directamente con el sistema de control y con tan solo pulsar un botón. Para comprobar el estado de las distintas máquinas integradas en la red no es necesario desplazarse; gracias al paquete de software StateMonitor basta con echar un vistazo a la pantalla y los indicadores de estado tipo RAG (rojo, amarillo y verde). Las soluciones de Heidenhain van dirigidas a empresas pequeñas y medianas con entre diez y quince máquinas, por lo que se han concebido deliberadamente sin funcionalidad en la nube, evitando así los riesgos asociados, por ejemplo, con la seguridad de datos. La conectividad se ciñe a los servidores locales.
El componente de un dron ilustra la digitalización de la cadena de valor añadido
Siemens AG ya había presentado hace tiempo su concepto de Internet de las cosas (IoT), plasmado en el ecosistema MindSphere: una plataforma de digitalización indicada para todos los sectores industriales. Con esta aplicación es posible digitalizar toda la cadena de valor añadido, como se demostró con un componente de un dron moldeado por inyección. Gracias a estos ejemplos prácticos y específicos, los fabricantes y operarios de máquina-herramienta pueden descubrir las ventajas de fusionar el entorno real y el virtual. A través de la aplicación Manage MyMachine, y desde un ordenador, puede obtenerse información en tiempo real sobre el código de mecanización en ejecución y el estado operativo de máquinas distribuidas por todo el mundo. Tal grado de apertura requiere, como es lógico, soluciones para proteger adecuadamente los datos. Identify3D es la respuesta a dicha necesidad, ya que ofrece trazabilidad de procesos digitales de fabricación para garantizar la protección de la propiedad intelectual, al tiempo que brinda acceso a datos de diseño y producción para desarrollar componentes con especificaciones técnicas precisas y en cantidad limitada.
Además de sus soluciones de conectividad, Siemens cuenta con nuevas herramientas de software, como Analyze MyWorkpiece, una aplicación gráfica intuitiva que permite visualizar y analizar la trayectoria del extremo de la herramienta para editar y mostrar distintas velocidades de desplazamiento y orientaciones.
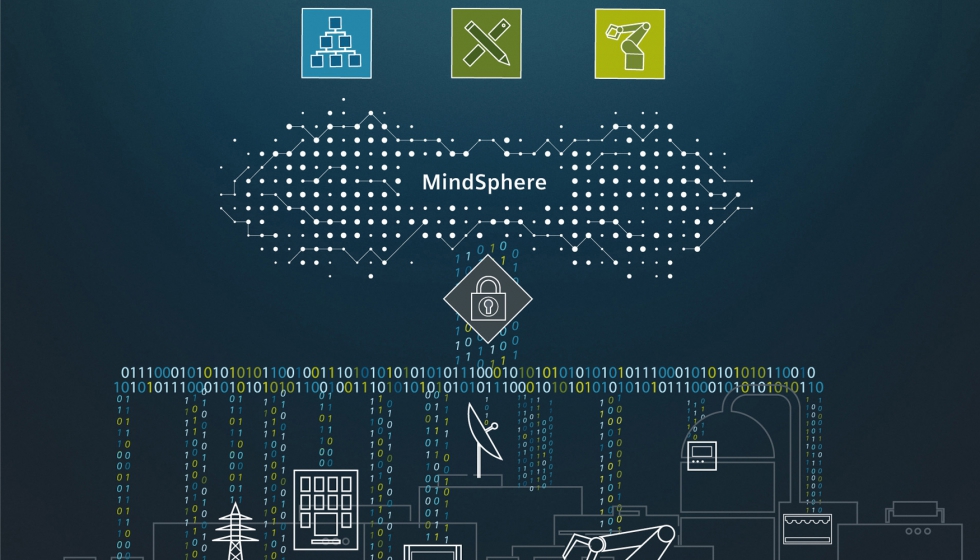
Alquiler de maquinaria
Para proporcionar a los usuarios aún más flexibilidad, Gebrüder Heller Maschinenfabrik de la localidad suabia de Nürtingen, ha creado el servicio de alquiler de máquina-herramienta Heller4Use. Los modelos contemplados son H2000 y H5000, que pueden alquilarse con carácter inmediato con un contrato de mantenimiento de plena cobertura. El usuario debe abonar una cuota fija mensual y una cantidad que depende del tiempo de funcionamiento del husillo, esto es, el tiempo real de utilización. Las máquinas están conectadas al ecosistema MindSphere de Siemens, por lo que el cliente se beneficia de la conectividad. El hecho de poder alquilar las máquinas permite a las compañías satisfacer sus necesidades durante los picos de producción sin tener que invertir en nuevos equipos, y les brinda la flexibilidad necesaria durante las fases iniciales de su proyecto empresarial.
La plataforma Industria 4.0 aplicada al tallado de engranajes
Por su parte, la empresa familiar Klingelnberg ha desarrollado la plataforma de TI basada en el concepto de Industria 4.0 y adaptada a las necesidades del sector del tallado de engranajes. Esta solución aporta conectividad en su sentido más estricto e información sobre toda la cadena de procesos de producción de engranajes. La plataforma de TI GearEngine es el eje vertebrador de este sistema ciberfísico de ciclo cerrado. Esta plataforma hace las veces de centro de conexión para las distintas máquinas-herramienta y otros servicios (como SmartTooling, un sistema de identificación de herramientas desarrollado por la propia empresa) y, mediante tres bases de datos, gestiona los datos sobre la configuración de los dientes de los engranajes, los equipos de producción y el historial de cada pieza. Las máquinas conectadas proporcionan información a la plataforma sobre las herramientas y dispositivos de sujeción empleados para el mecanizado del engranaje en curso.
Los beneficios de los vidrios inteligentes en el marco de Industria 4.0
La empresa Index-Werke GmbH & Co. KG Hahn & Tessky (Esslingen) cuenta con varias soluciones digitales innovadoras surgidas de su iniciativa iX4.0. Además de una plataforma de IoT en la nube para recibir y procesar datos sobre máquinas y procesos, esta nueva estructura de servicio destaca por el empleo de vidrios inteligentes para que el usuario pueda reparar en tiempo real su máquina en caso de producirse cualquier incidencia. Desde Esslingen, el servicio técnico de la empresa le ofrece asistencia visual y le transmite la información y las instrucciones a través de los vidrios instalados en la máquina. Este sistema permite agilizar las reparaciones y reducir los tiempos de parada.
Tecnología integrada de sensores para evitar rechazos
Renishaw (New Mills, Reino Unido) tiene en su haber sistemas para aplicaciones metrológicas y fabricación generativa. Soluciones metrológicas integradas y conectadas como Equator, un versátil instrumento de ensayo que incorpora un sistema de control inteligente de procesos CNC que permite efectuar correcciones en las herramientas de forma totalmente automatizada. Al estar totalmente integrado en el proceso de producción, los datos de corrección se transfieren del instrumento de medición a la máquina y quedan registrados para reutilizarse en procesos posteriores de fabricación. Gracias a este proceso continuo de reajuste, es posible evitar los rechazos por completo.
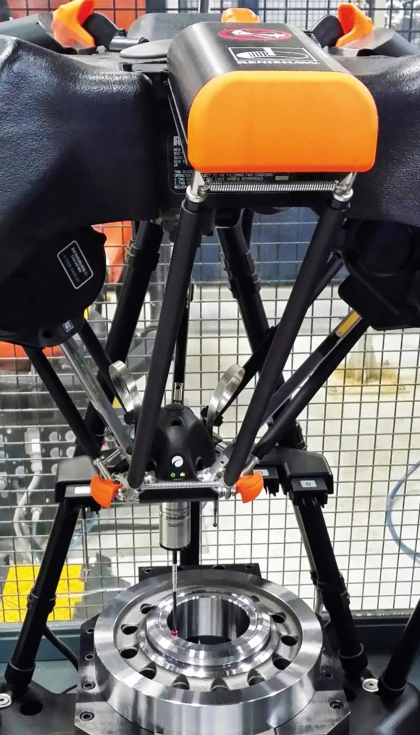
Las start-ups tecnológicas desarrollan aplicaciones web, pero también hardware
La start-up Picum MT, creada por el Instituto de Ingeniería de Producción y Máquina-herramienta (IFW) de la Universidad Leibniz de Hannover, ha adoptado un enfoque novedoso para facilitar el mecanizado de componentes de cualquier tamaño de forma flexible y rentable. En lugar de transportar el componente a la máquina-herramienta, es esta la que se traslada hasta el componente. Este robot inteligente llamado Picum One, de tan solo 100 kg de peso, está equipado con su propio software y novedosas prestaciones metrológicas. Según afirma esta empresa emergente, con este sistema se evitan costes operativos y de adquisición, así como las inexactitudes, que aumentan a medida que lo hace el tamaño de la máquina.
Carbon-Drive GmbH (Darmstadt) por su parte es una solución innovadora en el campo de la fabricación de husillos. Esta empresa emergente creada por la Universidad de Ciencias Aplicadas de Darmstadt es el primer fabricante del mundo de motores de husillo enteramente de carbono para máquina-herramienta. Los altos niveles de rigidez y termoestabilidad aportan a las aplicaciones incontables ventajas. Al tratarse de un material de menor masa, el husillo realiza un 50% más rápido todas las funciones de aceleración y deceleración, reduciéndose así el consumo energético, los costes y los tiempos de inactividad. Las propiedades de los materiales que pueden adaptarse in situ son las idóneas para integrar equipo metrológico que permita supervisar en tiempo real el proceso de corte del metal.
Torneado de alta velocidad mediante acoples innovadores
Dos innovaciones aportan importantes ganancias de productividad en las actividades de torneado: el fabricante sueco Sandvik Coromant ha desarrollado dos insertos de corte para desbastar y para pulir que, junto con trayectorias adaptadas de las herramientas, pueden mejorar sensiblemente el rendimiento de las operaciones de torneado de contornos. Modificando el acople pueden obtenerse velocidades de avance muy superiores.
Y los fabricantes de herramientas Vandurit (Leverkusen) y de máquina-herramienta Emag (Suabia) han revolucionado el torneado en torno vertical. Durante el proceso de alimentación de piezas, la cuchilla de la herramienta se mueve alrededor del contorno a velocidades de f = 0,4 a 0,5 mm/revolución en operaciones de fresado en duro de 100 Cr6 (60 HRC±2). Por otra parte, estas herramientas tienen una vida útil más larga, ya que la cuchilla se desgasta de manera uniforme. Para este proceso se dispone de dos insertos de corte, uno de desbastado y otro de pulido.
Procesos más eficientes gracias al nuevo modelo automático multihusillo MS40C-8
Para la fabricación en masa de piezas torneadas de alta precisión se emplean máquinas multihusillo automáticas con distintas posiciones en las que cada husillo lleva a cabo una fase de torneado hasta completar el proceso de mecanizado del componente. Index-Werke (Esslingen) ha desarrollado el nuevo modelo multihusillo MS40C-8, que consta de 8 husillos y un diámetro de 40 mm. Esta máquina se desmarca de la competencia por sus múltiples opciones de mecanizado de la parte posterior de las piezas y por optimizar el proceso de fabricación de componentes relativamente complejos.
Una versátil rectificadora de cinco ejes
Por su parte, Mägerle (United Grinding), procedente de la localidad suiza de Fehraltorf, ha diseñado un nuevo centro de rectificado de cinco ejes, el cual constituye un nuevo referente en materia de flexibilidad y funcionalidad. Además de llevar a cabo operaciones convencionales de rectificado, este equipo realiza labores de fresado y perforación. Por su gran versatilidad y sus diversas funciones, esta máquina está especialmente indicada para el sector aeroespacial. Los cambios simultáneos de herramienta y rodillo afilador permiten trabajar con discos diamantados y garantizan unas tasas elevadas de ablación de gran precisión incluso con cortes largos.
Rectificado de engranajes sin lubricante refrigerante
La italiana Samputensili (Bentivoglio), especialista en tallado de engranajes, ha dado a conocer la primera rectificadora en seco de engranajes del mundo. El aceite refrigerante ya no es necesario tras el acabado duro de los dientes. Con SG 160 Skygrind el desbastado consta de una fase inicial de afinado a la que sigue otra de pulido. Esta máquina ya se ha incorporado a varios procesos industriales. La transición al mecanizado en seco contribuye significativamente a la producción eficiente y respetuosa con el medio ambiente.
Fabricación eficiente de componentes estructurales de bastidores
Grob-Werke, procedente de la localidad bávara de Mindelheim, ha desarrollado tres modelos especialmente indicados para el mecanizado de componentes estructurales de bastidores: G500F, G520F y G600F. Estas máquinas ofrecen un amplio espacio de trabajo y una gran flexibilidad y capacidad de eliminación de virutas, además de una excelente respuesta dinámica gracias a su eje impulsor, especialmente diseñado para el mecanizado de metales ligeros. Las distintas variables de esta máquina compacta están indicadas para el mecanizado en seco, en húmedo o con una cantidad mínima de lubricante, y pueden operar de forma independiente o integradas en un proceso automatizado de producción.
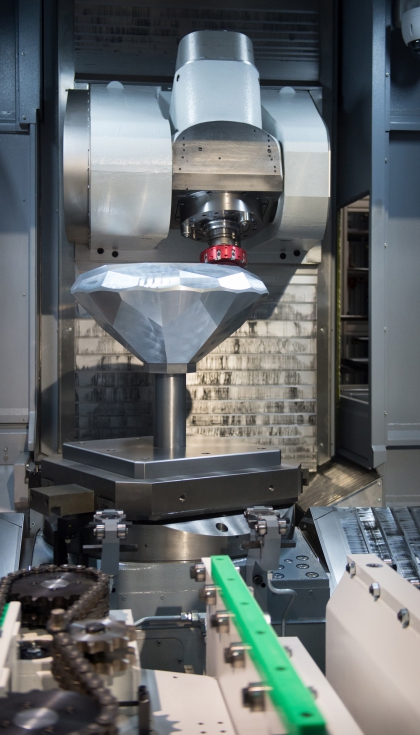
Soluciones de refrigeración para máquina-herramienta más eficientes e inteligentes
La conectividad también ha llegado al mundo de los compresores de refrigeración. Los sistemas de refrigeración de las máquinas-herramienta deben controlar la temperatura con gran precisión, además de ser eficientes y proporcionar datos sobre el estado de la herramienta en las aplicaciones de Industria 4.0. La solución de refrigeración por líquido Blue e+, de Rittal GmbH & Co. KG (Herborn), cumple todos estos requisitos. Esta empresa sita en Hesse ha logrado un ahorro energético del 70% integrando una nueva tecnología de compresor y ventilador controlados por el usuario que alcanza, de serie, un margen de error de 0,1 ºK. El refrigerador también cuenta con funciones inteligentes gracias a su PLC, que permite evaluar digitalmente los datos medidos, como la corriente y la tensión eléctrica, la temperatura y los diferenciales térmicos, con fines de control energético.
Rodamientos y sistemas de guiado inteligentes
Finalmente, Schaeffler Technologies AG & Co. KG (Schweinfurt) ha innovado en sus sistemas de guiado lineal y rodamientos de husillos y desarrollado un nuevo material más duradero, para fabricar rodamientos de alto rendimiento. Según afirma la empresa, los fallos de los sistemas de guiado suelen deberse a una lubricación incorrecta. El sistema de guiado lineal mecatrónico INA DuraSense garantiza la durabilidad superior del equipo basada en la lubricación a demanda.
Y con su FAG SpindelSense, Schaeffler aporta a la industria una unidad lista para instalar de monitorización del husillo principal que detecta las cargas inadmisibles mediante sensores integrados de corrientes de Focault desarrollados por la misma casa, con dos posiciones de desplazamiento radiales y una axial y dos grados de inclinación. El movimiento se capta, pues, en los cinco ejes fundamentales.
Otra de las innovaciones de Schaeffler es un rodamiento de husillo de alta velocidad fabricado con un nuevo material de alto rendimiento: el Vacrodur. La vida útil nominal de las aplicaciones en las que predomina la fricción mixta aumenta veinticinco veces en comparación con los rodamientos fabricados con acero antifricción para rodamientos. En el caso de la fricción elastohidrodinámica, con este nuevo material la vida útil de los rodamientos de los husillos es trece veces más larga. Esta innovación está destinada a copar los sectores en los que se trabaja con velocidades operativas y límite extremadamente elevadas.
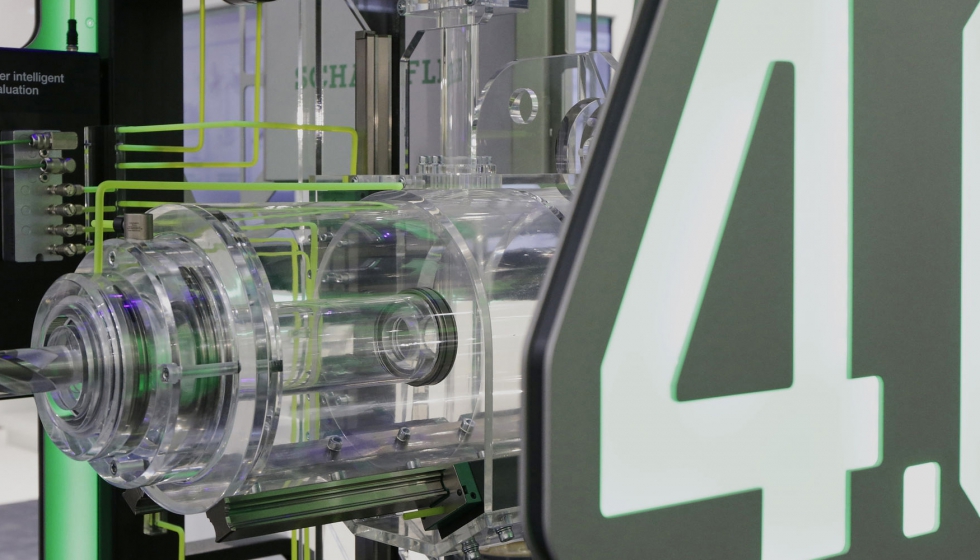
En resumen, y conscientes de la tendencia hacia la digitalización, los fabricantes trabajan incesantemente para presentar al mercado herramientas y equipos provistos de sensores e interfaces digitales de comunicación que proporcionan datos a sistemas de producción digitales conectados. Estas tecnologías de última generación persiguen, sin embargo, los objetivos de siempre: una mayor trazabilidad de los procesos de producción, la optimización de recursos y un aumento de la flexibilidad y la productividad. Los muchos desarrollos tecnológicos incorporados a las máquinas, herramientas y componentes aportan su grano de arena para alcanzar dichas metas. Sin olvidar las innovaciones en el ámbito de la fabricación aditiva una tecnología que sin duda favorecerá la implantación rentable de esta tecnología emergente.