La opción inteligente para el conformado en caliente
A pesar de ser un proceso usado por la mayoría de fabricantes europeos, en los últimos años el uso del conformado en caliente de aceros al boro está extendiéndose a mercados como Asia y Norteamérica por las grandes prestaciones y reducciones de peso que se obtienen. Prueba de ello es la incorporación, en Fagor Arrasate, de una nueva instalación de estampación en caliente con destino el mercado norteamericano.
Altas prestaciones productivas
Su tecnología permite ofrecer a sus clientes una solución a medida que, por sus características de automatización, horno y prensa, se trata de una instalación optimizada para todo tipo de piezas de estampación en caliente, con los más altos estándares de calidad, capaz de producir piezas en tiempos de ciclo de 12 segundos y con una relación de tamaños-tonelajes que maximiza la rentabilidad de la instalación.
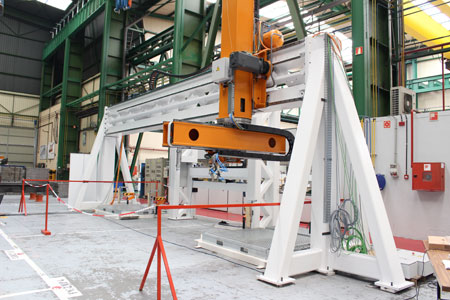
Desapilador de formatos
El desapilador de formatos es uno de los elementos clave que debe diseñarse para no ser cuello de botella de la instalación, ya sea con los parámetros de producción actuales o futuros, o ante eventuales reducciones de tiempos de ciclo de otros elementos de la instalación. Es por ello que se ha optado por una configuración básica mediante un feeder lineal de tres ejes capaz de mover pesos hasta 120 kg asegurando tiempos, marcaje incluido, de 10 seg. (1).
La alimentación de los formatos se realiza por medio de palés específicos que se cargan directamente sobre la posición de trabajo, sin necesidad de carros de carga intermedios, lo que reduce significativamente la necesidad de espacio en planta. En este caso concreto y con el objetivo de aportar total flexibilidad en el posicionamiento relativo de piezas entre el palé y la carga en el horno, el feeder lineal está provisto de un cuarto grado de libertad, que mediante un eje servocontrolado de giro sobre la garra porta piezas permite reposicionar en cualquier ángulo la pieza antes o después de su marcaje.
Otras características implementadas en el desapilador son la detección temprana de doble formato mediante sensor inductivo en la propia garra del feeder y dos cabezales de marcaje de formato ampliable a cuatro.
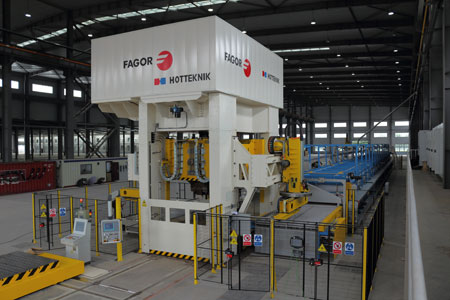
Hotteknik integra bajo un mismo equipo técnico tanto la prensa hidráulica como la automatización, e incluso los propios troqueles de estampación en caliente (Batz). Esta capacidad de concebir la línea como una unidad a todos los niveles permite garantizar unas prestaciones óptimas tanto en cadencia como en fiabilidad de la instalación.
Horno de rodillos
El horno de rodillos integrado tiene un ancho útil de 2.200 mm de forma que las piezas se alimentan de forma transversal al sentido de alimentación, asegurando altos ratios de productividad sin incrementar de forma excesiva la longitud de la instalación. De esta forma sólo en piezas excepcionalmente largas o estrechas se ve reducida la capacidad de procesado de la instalación y por término medio, aun con un horno de longitud útil inferior a los 30 metros, se consigue que este no sea el cuello de botella de la instalación.
A pesar de que el horno tiene su propio control independiente de la línea por ser de otro fabricante, Fagor Arrasate tiene una dilatada experiencia en su integración responsabilizándose del control central de los principales variables de proceso y funciones:
- Gestión de las seguridades en las zonas de entrada y salida.
- Señales de habilitación horno-línea.
- Código de pieza en proceso.
- Señales de fin e inicio de referencia.
- Gestión de alarmas de estado.
- Longitud de conformado (tamaño en la dirección del flujo de prensado): 175 - 1.600 mm.
- Ancho de conformado (tamaño en la dirección transversal del flujo de prensado): 700 - 2.200 mm.
- Grosor de conformado: 0,6 - 3,0 mm.
- Peso máximo del lote: 25 kg.
Esta adecuada integración permite no sólo un funcionamiento sencillo de la instalación, sino el cumplimiento de los requisitos de seguridad e higiene que establece la legislación vigente del país destino al que se destina la instalación.
Carga-descarga de prensa
La carga de formatos y descarga de piezas de la prensa es una de las partes más importantes de la instalación por su alto grado de automatización y sincronización de elementos. Para ello, se ha optado por un feeder tipo LR5-120 de uso general con cuatro grados de libertad capaz de trasladar y posicionar un elemento de forma ágil y flexible gracias a sus 5 accionamientos servoaccionados de alta eficiencia.
Para esta exigente aplicación los tres ejes cartesianos básicos usan una transmisión de accionamiento directo mediante piñón-cremallera, y el eje de giro que facilita el cambio en modo semiautomático de las garras porta piezas.
Este innovador manipulador es la versión más robusta de feeders pudiendo soportar sobre su extremo una carga hasta 120 kg, superando con creces las necesidades de manipulación en piezas estampadas de automoción. Más allá de las capacidades intrínsecas del propio feeder la singularidad del sistema desarrollado por Fagor-Hotteknik radica en la sincronización Prensa-Feeder. Para ello ambos feeders son accionados por motores servocontrolados Siemens-Simotion en todos sus ejes, y el conjunto equipado con un sistema especialmente desarrollado para sincronizar los ejes de carga-descarga junto con el eje que supone el accionamiento de la prensa. (2) El hecho de que todos los ejes que actúan de forma simultánea de ambos feeders de carga y descarga, así como el de la propia prensa dan una gran rapidez y robustez al ciclo completo de estampado en caliente, haciéndolo rápido y estable en el tiempo.
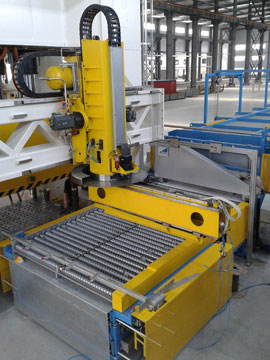
Prensa hidráulica servocontrolada
El tonelaje de la prensa es importante no sólo para conseguir el conformado de las piezas sino para asegurar un cierre con alta presión superficial que permita una transferencia de calor más rápida y por tanto la reducción del tiempo de troquel cerrado. Además considerando que en función del tamaño de pieza se pueden procesar en un único golpe de 2 a 4 piezas de forma simultánea, las últimas instalaciones requeridas por los clientes y que poco a poco se está convirtiendo en un standard para el sector estampador cuentan una prensa de 1.200 toneladas y unas dimensiones de mesa de 3.000 x 2.200 mm. La principal característica de esta gama de prensas de producción es estar equipada con un bloque de control con servoválvulas capaz de realizar un control en ciclo cerrado de la posición del carro en menos de 1ms, lo cual permite una perfecta sincronización y control de posición del carro de la prensa.
Equipos adicionales
Además de los componentes descritos la instalación se compone de cajones de rechazo tanto en la zona de desapilado como a la salida de la mesa de rodillos del horno. Así mismo, está equipada con una cinta de salida de piezas de alta capacidad, compuesta por láminas metálicas, que asegura tanto la resistencia a la temperatura de las piezas ya conformadas, como la durabilidad sin deformarse debido a los continuos impactos producidas por las mismas. Se disponen, además de cuatro circuitos de refrigeración de troquel, de circuitos de presión auxiliares multifunción para los troqueles, que permiten funciones de pisado o expulsor.
Ventajas de la innovadora solución Fagor
- Solución compacta que ocupa un menor espacio en planta.
- Alta productividad con tiempos de ciclo de 12 s.
- Flexibilidad y versatilidad para procesar 1, 2 ó 4 piezas en un mismo golpe.
- Fácil manejo por su Innovador Control de la automatización.
- Trazabilidad y control de proceso.
Monitorización y trazabilidad de proceso
Punto clave en el proceso coingeniería y adecuación de la instalación a las necesidades del cliente son los distintos puntos de control a lo largo de todo el proceso que permiten garantizar una producción estable y control de la calidad de pieza. Desde el control de doble chapa en la zona de marcado y el control individualizado, control de temperatura de formato multipunto al posicionamiento en el troquel y salida de la pieza conformada.
Además se realizan una medición de toda una batería de parámetros indirectos que afectan al proceso térmico de enfriamiento: características del agua de refrigeración en los distintos circuitos (presión, caudal, temperatura) tanto a la entrada como a la salida, tiempo real de troquel cerrado, fuerza real de cierre, tiempo de transferencia de piezas del horno al troquel… Por cada pieza procesada, más de 30 parámetros pueden ser almacenados, lo cual, junto a la calibración de los elementos de medición sitúa a este tipo de instalaciones por encima del estándar CQI-9, ofreciendo a los ingenieros de proceso un perfecto conocimiento de qué es lo que realmente está pasando pieza a pieza, ayudando a reducir los riesgos inherentes a un proceso térmico de esta naturaleza.