Fagor Arrasate expone su liderazgo al público
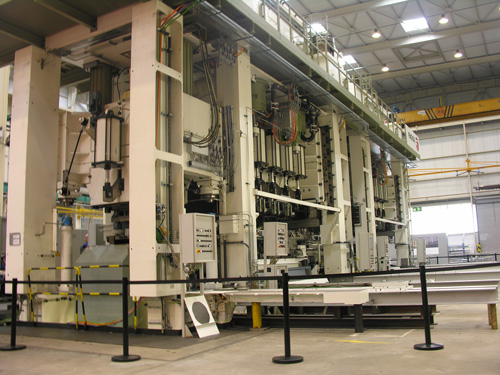
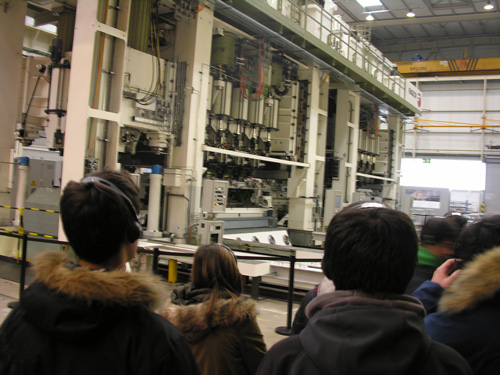
FlexCell, un equipo para estampar piezas con más flexibilidad, mayor productividad y menor inversión
Todo ello lo han podido comprobar los representantes de las grandes firmas automovilísticas y estampadores que han acudido a las jornadas de puertas abiertas en las factorías de Fagor Arrasate y Onapres, ambas pertenecientes a la Corporación Mondragón. Asimismo, han participado representantes del mundo académico y social. El evento se ha organizado para dar a conocer los nuevos desarrollos en el sector de la máquina-herramienta por deformación que han dado lugar a novedosas instalaciones destinadas a importantes clientes alemanes del sector automotriz.
En la planta de Fagor Arrasate en Mondragón se ha presentado el nuevo sistema de estampación FlexCell, un revolucionario equipo que permite estampar piezas de chapa metálica con mayor productividad y menor inversión, una combinación a todas luces ganadora. En efecto, actualmente se utilizan equipos diferenciados para fabricar las piezas medias de la carrocería y las piezas pequeñas. Para las primeras, las fuerzas de prensado necesarias son tan grandes que habitualmente se usan varias prensas colocadas en línea y robotizadas en las que la pieza se va fabricando paso a paso a una velocidad moderada de 9-10 gpm o hasta 14 gpm en líneas Wavelines. Para las piezas pequeñas, por el contrario, pueden usarse prensas transfer de 1.000 a 3.000 toneladas, con velocidades mayores hasta 24 gpm.
El nuevo sistema FlexCell permite realizar ambos trabajos en una única instalación. Consiste en varias prensas transfer concatenadas con elementos transferidores entre ellas. Trabajando en conjunto, FlexCell permite fabricar las piezas de mayor tamaño con una inversión menor que una línea de prensas. Pero, al contrario que en una línea, ambas prensas pueden trabajar también independientemente con piezas más pequeñas y a muy alta velocidad, lográndose aunar en un único sistema dos tipos de trabajo que hasta ahora requerían varias inversiones independientes.
Durante las visitas planificadas, los invitados han podido apreciar el nuevo sistema aplicado a la fabricación de llantas para coches, un proyecto que se ha realizado para la firma Volkswagen en Alemania.
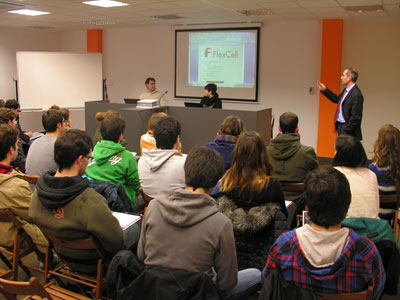
Línea de prensas hidráulicas flexible
Por otro lado, en la planta de Onapres en Zamudio se ha podido ver una línea de prensas hidráulicas flexible para probar troqueles (‘try-out’) y también para producción de series cortas. Los visitantes han podido presenciar el funcionamiento de una gran máquina de 2.500 toneladas dotada de un cojín CNC inteligente de 9 puntos con capacidades de pre-aceleración y acompañamiento; un novedoso sistema de seguridad contra caídas de carro y amortiguadores de corte capaces de soportar la fuerza total de la máquina amén de otra serie de nuevos dispositivos y controles que hacen que estas máquinas sean capaces de probar troqueles que fabrican piezas mucho más complejas que las habituales. El resultado es que el diseño de los vehículos puede ser más avanzado y seguro. Las máquinas presentes en Zamudio se instalarán próximamente en la firma Audi.
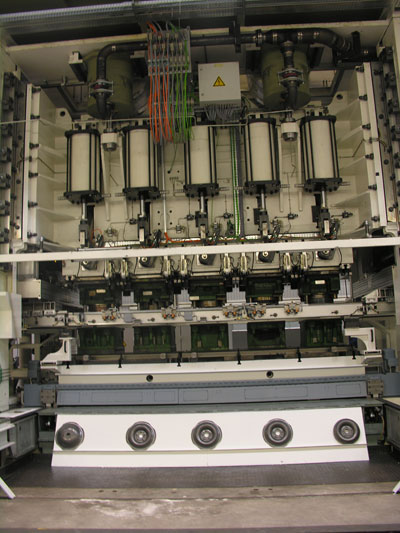