Miralles se reinventa aumentando su eficacia global y reduciendo sus tiempos de cambios
En Miralles Displays & Packaging han conseguido por ende, gracias a la implicación metódica de cada uno de sus trabajadores, y guiados por la experiencia de Marc Tarral, que con menos de un año de dedicación, hayan aumentado su eficacia de la sección de offset en más de 35%, a la par que disminuían la merma. Asimismo, en idéntico período, los tiempos de cambio entre otros procesos han disminuido hasta en 40%. Es lo que resumen desde la planta catalana como un “hacer más y hacerlo mejor”.
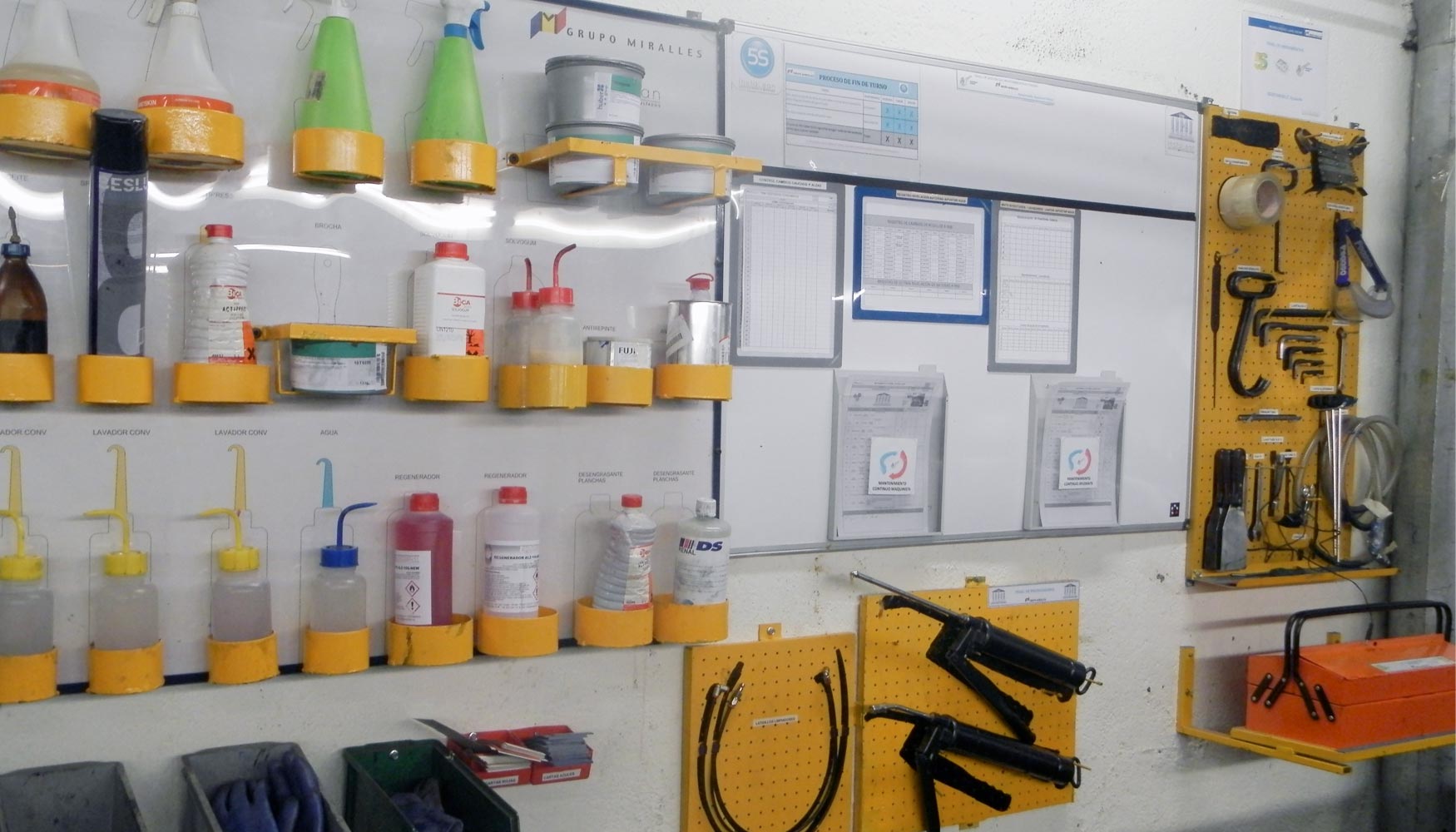
Miralles, caracterizada por su alta capacidad de diseño y acabado esencialmente en material PLV, kits promocionales, cajas de vino y packaging en general, apostó hace un año por la sólida experiencia de Insta Lean, la empresa liderada por el ingeniero francés, para lograr alcanzar el máximo de productividad a través de sus procesos de organización industrial a medida.
Apoyándose en todos los directivos, jefes de sección y operarios del departamento de Offset de la planta, InstaLean elaboró un procedimiento con forma de templo griego, donde ha sido prioritario construir los cimientos en primera instancia, para a continuación, pasar a los pilares.
A través de los ‘Sistemas Ágiles’ (softwares de gestión industrial de elaboración propia), Marc Tarral sentó las bases de la mejora continuada en la planta catalana. En primer lugar, la puesta en marcha del programa de reporting automatizado Halcón, permitió a los responsables y a los operarios de controlar todos los parámetros de la eficiencia en tiempo real, conociendo en todo momento el status de los indicadores de la misma.
Seguidamente la metodología de Planta Visual o de 5S Reforzado permite el perfeccionamiento del consumo de consumibles, mejora los tiempos de reacción frente a posibles perturbaciones, así como estructura los cambios de forma estandarizada, lo cual finalmente, incrementa la motivación del personal. “Cada cosa en su sitio de forma visual, ergonómica y antes que todo, muy práctica”, cuenta un máquinista acerca de este procedimiento.
El InstaProcess es la siguiente base que Marc Tarral debió implementar en Miralles. Se trata de un sistema ágil que permite gestionar totalmente más de 30 procedimientos estandarizados con una gran orientación hacia el mantenimiento autónomo de las máquinas de impresión.
Luego de colocarle las bases al templo, Marc Tarral le ha edificado los pilares. Asimismo, resultó vital implementar el software Concorde de Lean Planning con el cual se logra hacerle una “guerra efectiva al derroche en planificación”. Es así, explica el fundador de Insta Lean, como en la sección de Offset de una gran planta de packaging como lo es Miralles, el responsable de la misma puede pasar hasta tres cuartas partes de su tiempo planificando, debido en parte, a la gran cantidad de proveedores internos que tiene. El Concorde logra igualmente que todo el personal se enfoque y se sincronice mutuamente, eliminando trabajo administrativo innecesario. “Antes la preparación de las planchas, tintas, barniz y cartoncillo tardaba hasta una semana para culminar con éxito el proceso, ahora el Concorde ayuda a ejecutarlo en tan sólo horas”, precisa el líder de Insta Lean.
A través el pilar SMED, los operarios de Miralles pueden tener preparado el siguiente cambio con la máquina aún en marcha, con lo cual la productividad aumenta ostensiblemente. Otro de los pilares es el TPM-1 o Mantenimiento Autónomo, realizado por los mismos operarios. Con este sistema, se logran detectar y solucionar todos los fallos y derroches latentes de la parte invisible del conocido ‘Iceberg de las Averías’ de los equipos industriales.
El último pilar a colocar es el software TPM-2 ó Plan Visual de Mantenimiento, que permite comunicar en tiempo real cualquier tipo de avería o incidencia priorizadas en función del impacto que tienen en el negocio. Este software las reporta indicando dónde y cuándo han ocurrido, representando a la parte visible del ‘Iceberg de las Averías’.
Sobre este conjunto de softwares, José Antonio Fernández, director de Recursos Humanos de la planta resalta que “ahora se puede analizar diariamente cada incidencia y no a final de mes como hacíamos antes de la puesta en marcha de este proyecto. Esto es importante, no ya para criticar, sino para aportar soluciones”.
El directivo también señala que las herramientas que InstaLean le hereda a la fábrica “le conceden la oportunidad a los mandos intermedios de centrarse en los problemas que se estén teniendo mientras los analizas por cada turno y cada máquina”.
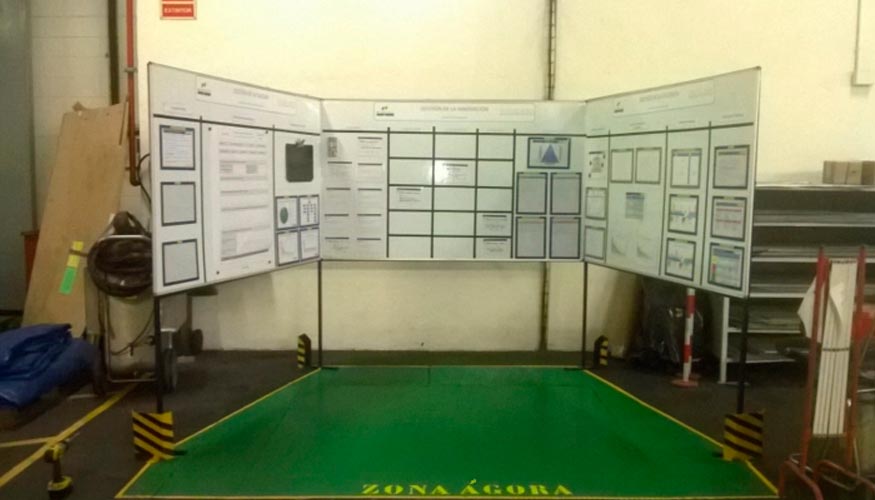
Finalmente, el ingeniero francés decidió que había llegado la hora de colocarle el frontón al templo. Se trata de la ‘Zona Ágora’, el lugar físico dentro de la planta donde se produce el encuentro y debate semanal entre los distintos operarios y la dirección. En la ‘Zona Ágora’, y valiéndose de los softwares Halcón y TPM-2, se revisan las incidencias y se le buscan alternativas a los derroches acaecidos por maquinaria. “A este proceso lo he llamado ‘la Búsqueda de Tesoros’ y plasma en paneles visibles cada idea de mejora propuesta y su estado de avance”, subraya el ingeniero de Insta Lean.
Por su parte, José Antonio Pérez, jefe de la sección de Offset de la planta no oculta los sólidos beneficios que ha traído la implementación de los procesos de Insta Lean en la planta de Mollet del Vallès: “Marc Tarral nos ha legado unos procesos tan efectivos y nos ha instruido tan bien, que considero que ya no podríamos trabajar sin ellos. Todo se resume en una mejor producción y en una optimización de las máquinas”, reflexiona.
“Ahora oprimo un botón y ya me sale todo el reporte del día. Eso me ayuda a estar más tiempo en la maquinaria resolviendo posibles imprevistos”, aseguró Pérez.
El caso reciente de esta reconocida planta de packaging demuestra que con la metodología correcta, la constante implicación de sus operarios y mandos, así como la dirección motivada de un experto, se pueden mejorar las cuotas de producción para llegar a alcanzar la perfección.
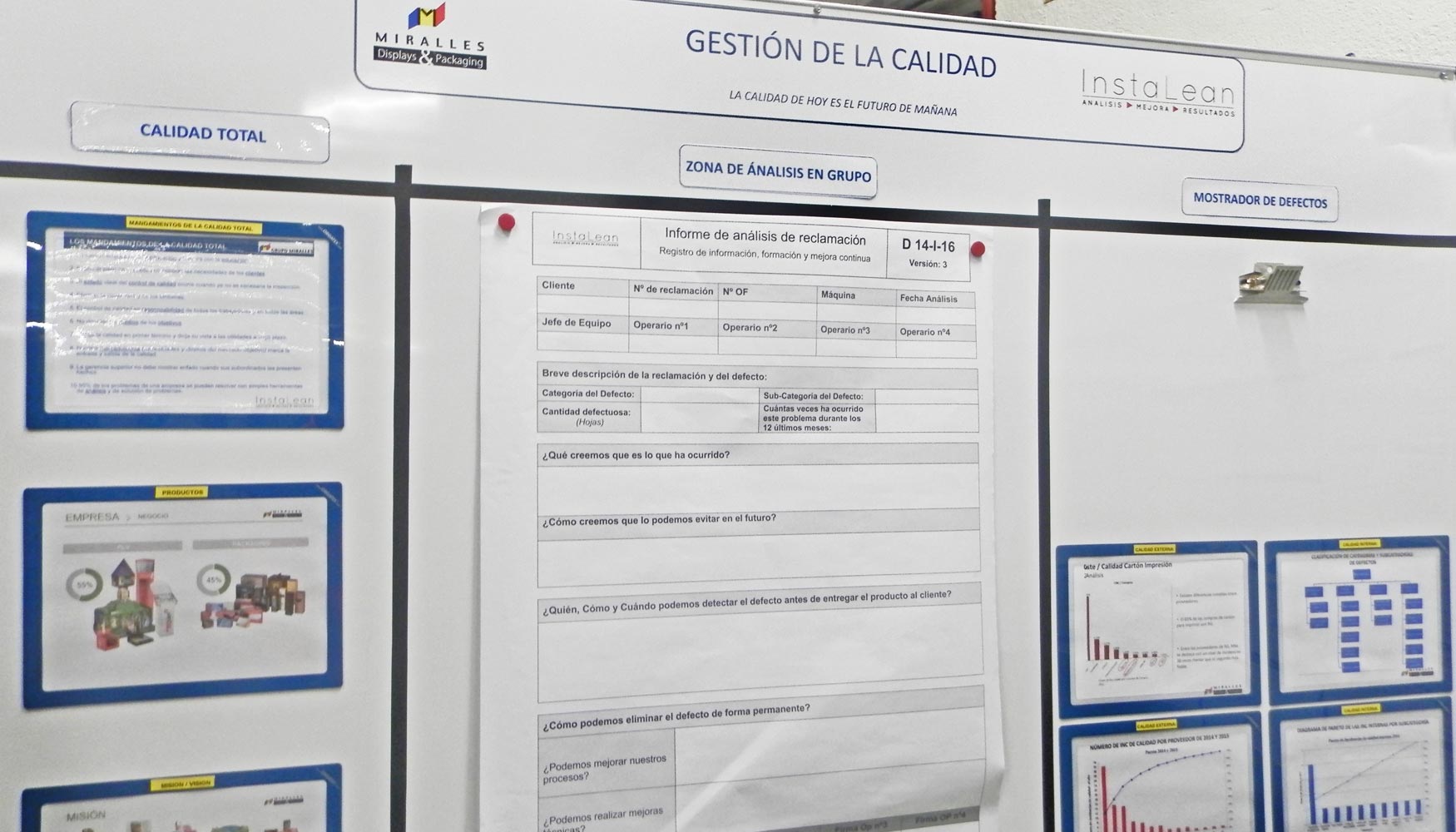