Avances recientes en los procesos de fabricación rápida y tratamiento superficial con láser
La limpieza es otro campo de aplicación interesante de la tecnología láser. Los últimos desarrollos se centran en la limpieza de dispositivos electrónicos, en los que es preciso eliminar de lacas soldables, contaminación, residuos poliméricos y capas de óxido de la superficie. Para ello, se utiliza radiación láser pulsada, con pulsos de 10 a 250 ns de duración. Debido a la alta intensidad y al corto intervalo de interacción, los recubrimientos no metálicos se evaporan, mientras que la superficie metálica del sustrato permanece intacta.
El pulido de superficies es un nuevo campo de aplicación para los láseres. En este proceso, la rugosidad superficial, originada por ejemplo tras un proceso de fresado o desbarbado, se alisan mediante la fusión de una fina capa de material. La velocidad de este proceso suele situarse entre 0,2 y 5 cm2/min. Esta técnica podría aplicarse al pulido de moldes de inyección y de fundición y a instrumentos médicos.
El proceso de fundido selectivo por láser (SLM) puede utilizarse para la fabricación directa de piezas de metal a partir de materiales en serie. Gracias a una técnica de fundido completo del material en polvo, se pueden conseguir densidades cercanas al 100 por cien, con buenas propiedades mecánicas. Los materiales que se están investigando son el acero inoxidable 1.4404, el acero para herramientas 1.2343 y el titanio TiA16V4. La utilización de la técnica SLM ofrece ventajas en ciertos procesos. La fabricación de prototipos funcionales a partir de materiales en serie permite ahorrar tiempo en comparación con los procesos convencionales, como la fundición. Otro ejemplo de estas ventajas es el uso del proceso SLM para la fabricación de pequeños lotes en serie o de piezas individuales (por ejemplo, implantes médicos), con gran flexibilidad y posibilidad de sustituir a otros procesos convencionales.
Revestimiento por láser
Haz láser
Boquilla de inyección de polvo
Flujo de polvo
Pieza base
Baño de fusión
Capa de revestimiento
Zona de dilución
Zona térmicamente afectada
Dirección de barrido

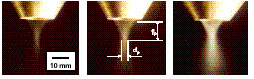
Slit size: tamaño de la rendija
inyección de polvo coaxial continua con distintos tamaños de rendija
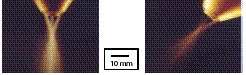
Conceptos sobre inyección de polvo
En el revestimiento mediante láser, el suministro del material de aporte es uno de los factores más importantes para el control del proceso. No obstante, los equipos que existen en estos momentos en el mercado se diseñaron para satisfacer las necesidades de los centros de investigación y, por ello, es necesario seguir trabajando para crear equipos que se ajusten a los requisitos de la industria en términos de fiabilidad, mantenimiento y vida útil. Existen tres técnicas de inyección de polvo:
• Inyección fuera del eje (un único flujo de polvo se inyecta de forma lateral al haz láser, Figura 1)
• Inyección coaxial continua (se inyecta un flujo de polvo cónico que cubre el haz láser, Figura 2)
• nyección coaxial discontinua (se inyectan tres o más flujos de polvo en sentido coaxial al haz, Figura 3).
La inyección de polvo fuera del eje es adecuada para el revestimiento de pistas anchas. En el caso de pistas con una anchura de entre 0,5 y 5 mm, se debe utilizar una rendija con sección transversal circular con un diámetro de entre 1,5 y 3,5 mm. Para pistas más anchas (5-25 mm), se debe utilizar una rendija con sección transversal rectangular (por ejemplo, 1,5 x 15 mm2). La técnica de inyección fuera del eje también puede utilizarse para el revestimiento de áreas de difícil acceso. No obstante, en la inyección fuera del eje, la boquilla está colocada en posición lateral al haz láser y, por tanto, no es una técnica adecuada para el revestimiento tridimensional.
En el caso de la inyección coaxial continua se utiliza un flujo de polvo cónico que cubre el haz láser. El flujo de polvo se caracteriza por los siguientes factores: diámetro en el punto focal del flujo de polvo (dp) y distancia entre la boquilla y el punto focal (fp) (Figura 4). A su vez, estos parámetros dependen del tamaño de la boquilla, el flujo del gas portador, el caudal de polvo y el tamaño de las partículas de polvo. Tal y como se ve en la Figura 5, con una boquilla mayor, el diámetro del punto focal aumenta. Lo mismo ocurre si el caudal de polvo se incrementa. Por su parte, la reducción en el tamaño de las partículas provoca una disminución del diámetro focal del flujo. El diámetro focal del flujo de polvo en la inyección coaxial continua suele estar comprendido entre 1 y 3 mm.
La ventaja principal que presenta la inyección coaxial continua frente a la inyección fuera del eje es que puede utilizarse en revestimientos tridimensionales. No obstante, la inclinación de la boquilla está limitada. Puesto que la homogeneidad del cono de polvo depende de la distribución del polvo dentro de la cámara de expansión de la boquilla, cuando la boquilla esté inclinada, el flujo se verá afectado por la gravedad. Se ha comprobado que el ángulo de inclinación máximo, sin que la geometría del revestimiento se vea significativamente afectada, es de 20º.
En el caso de la inyección coaxial discontinua, tres o más flujos de polvo se distribuyen alrededor del haz láser para formar el punto focal del flujo (Figura 3). El punto focal en estos casos suele presentar un diámetro de entre 2,5 y 4 mm. La principal ventaja de la inyección coaxial discontinua es que puede utilizarse para trabajos de revestimiento en tres dimensiones y con cualquier ángulo de inclinación de la boquilla. En la Figura 5 se muestra un flujo de polvo vertical y un flujo con una inclinación de 45º. El punto focal apenas se ve afectado por la inclinación. De hecho, se han probado boquillas que permiten utilizar un ángulo de inclinación de 180º (revestimiento inverso).
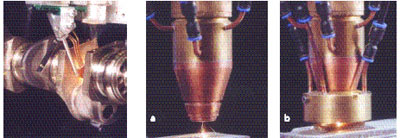
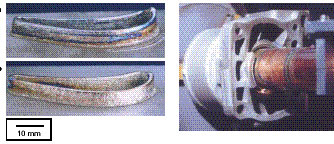
Fig. 7: Revestimiento de la superficie de rodadura de un cilindro del motor de una motocicleta mediante una cavidad óptica con unidad de inyección integrada; material base y material de aportación: aleación AlSi
Aplicaciones del revestimiento láser
La técnica del revestimiento láser puede utilizarse potencialmente en la reparación de cojinetes de cigüeñales de gran tamaño (camiones y barcos, grandes motores de plantas eléctricas). En la Figura 4 se muestra el revestimiento del cojinete del cigüeñal de un camión. Para llevar a cabo el revestimiento de los bordes del cojinete, es necesario utilizar una boquilla de inyección estrecha, de modo que en este caso no se puede utilizar un sistema de inyección coaxial.
La inyección coaxial se utiliza, por ejemplo, en el sector aeroespacial para reacondicionar algunas piezas de los motores de turbina, como las juntas o los extremos de los álabes. Puesto que en la mayoría de estos casos la pista que se va a revestir es pequeña, la mejor técnica es la inyección coaxial, dado el tamaño del punto focal del flujo. En la Figura 5 se muestra el revestimiento del extremo de un álabe en TiA16V4 sobre un sustrato liso. Además, mediante un revestimiento adicional, se puede minimizar la oxidación de la pieza (Figura 6). Aunque los tres tipos de inyección del polvo pueden utilizarse para distintas aplicaciones, los trabajos especiales exigen soluciones especiales. Un ejemplo de “trabajo especial” sería el revestimiento de una superficie interior. Cuando el diámetro de la rendija debe ser menor de unos 300 mm, no se puede utilizar ninguna de las tres técnicas descritas. En este caso, debe utilizarse una cavidad óptica especial con unidad de inyección integrada. En la Figura 7 se muestra el revestimiento de la superficie de rodadura de un cilindro del motor de una motocicleta. La cavidad óptica puede utilizarse con aberturas con un diámetro mínimo de hasta 50 mm.
El revestimiento por láser puede utilizarse para reparar álabes de turbinas. En el ejemplo de la imagen (Figura 8), en primer lugar, se estableció una cadena de proceso cíclica. Para reparar un álabe mediante revestimiento por láser, se utilizan los datos CAD de la pieza para generar las trayectorias NC (pistas que se van a revestir). Si no se dispone de los datos CAD o si las dimensiones del álabe han cambiado con el uso, será necesario digitalizar la geometría del álabe erosionado. Para calcular el volumen a generar, también debe digitalizarse un álabe de referencia. Mediante un sistema CAD/CAM y macros CAD/CAM, este volumen se divide en capas y, a continuación, se crean las trayectorias NC ISO con los parámetros del proceso (potencia del láser, velocidad de barrido, solapamiento y estrategia de llenado o acumulación). Las trayectorias NC ISO se convierten en trayectorias NC legibles por una máquina en un paso de proceso posterior. El programa NC generado se transfiere al sistema de control NC. Con esto obtenemos un proceso de revestimiento por láser totalmente automatizado.
La modelización permite predecir los resultados y es una fase esencial para entender el proceso y reducir el trabajo experimental. Las simulaciones más fiables se basan en el método de elementos finitos. En el ILT, se creó un modelo en el que se tenía en cuenta el flujo de calor y masa dentro del baño de fusión así como los datos de masa en la inyección de polvo. Con esto, se puede simular la generación de un alma como la mostrada en la Figura 9. En estos momentos, el modelo se está perfeccionando y se utilizará para optimizar las estrategias de revestimiento para reparaciones.
La chapa de acero suele protegerse contra la corrosión mediante un galvanizado en continuo seguido de un recubrimiento en bobina con polímeros (técnica “Duplex”). No obstante, cuando posteriormente esta chapa se corta en un proceso de fabricación, la superficie metálica de los bordes queda expuesta a la corrosión y, por tanto, se necesita otro recubrimiento. Algunos experimentos han demostrado que es posible revestir con zinc y polímeros mediante láser. Puesto que los polímeros se descomponen a bajas temperaturas, no se puede utilizar una inyección directa (Figura 1). En estos casos, se coloca el haz láser por delante del flujo de polvo, calentando la superficie del borde de la chapa. Las partículas poliméricas se funden por la transmisión de calor. En la Figura 10 se puede ver una muestra sometida a un ensayo de 1.000 horas de aspersión de sal: la parte del borde de la chapa que había sido revestida mediante RILSAN (capa de un espesor de unos 0,2 mm) no muestra corrosión alguna. En el caso de recubrimientos de cinc (capa de un espesor de unos 10-60 _m) se obtuvieron resultados similares.
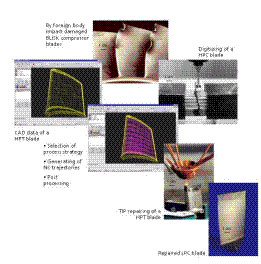
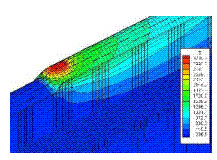
Limpieza y pulido con láser
Para la fabricación y montaje final de dispositivos electrónicos son necesarios numerosos procesos de limpieza y activación. Así, es necesario eliminar de la superficie lacas soldables, contaminación, residuos de polímeros, capas de óxido. En algunos procesos posteriores, como las uniones (soldado, unión por adherencia) y revestimiento (por ejemplo, galvanizado), la limpieza de las superficies resulta especialmente importante. Las técnicas de limpieza convencionales suelen basarse en procesos químicos o mecánicos y, en muchos casos, el procesado y eliminación de los residuos es caro. Por otra parte, la tendencia a la miniaturización exige el uso de procesos de limpieza de alta precisión. La técnica láser elimina todos estos inconvenientes asociados a las técnicas de limpieza tradicionales. Dependiendo de las propiedades de absorción de los revestimientos y de los materiales de base, pueden utilizarse láseres pulsados de CO2, Nd:YAG o de excímeros con pulsos de 10 a 250 ns de duración. Debido a la alta intensidad y a la corta interacción temporal, las capas de recubrimiento no metálicas se evaporan, mientras que la superficie metálica del sustrato permanece intacta. Un ejemplo de limpieza de dispositivos electrónicos es el desescamado y descalcificación de tapones pequeños (Figura 11).
Otro campo de aplicación del láser es el pulido de superficies (Figura 12). En este proceso, la rugosidad superficial, originada por ejemplo tras un proceso de fresado o desbarbado, se alisan mediante la fusión de una capa fina del material. La altísima precisión de este proceso evita que se produzcan aristas redondeadas o desviaciones geométricas. La velocidad suele situarse entre 0,2 y 5 cm2/min en función del material, la rugosidad inicial y final exigida. Para llevar a cabo estas funciones, en las líneas de producción es fácil integrar un láser de Nd:YAG con fibra, pulsado o continuo. Algunos campos en los que se podría aplicar esta técnica son el pulido de moldes de inyección y de fundición o los instrumentos médicos.
Fundición selectiva con láser
En los últimos años (referencias 7-11) han surgido numerosos procesos de manufactura generativa (los llamados procesos de prototipado rápido). En general, en estos procesos se utiliza un material o una composición específicos. Con el fin de superar esta limitación de un material concreto, Fraunhofer ILT y TRUMPF están trabajando en el desarrollo de un proceso láser de función selectiva o SLM (siglas de Selective Laser Melting). El punto de partida, al igual que en los procesos de fabricación generativos, es un modelo CAD 3D que se subdivide en capas de un espesor determinado. La pieza final se crea mediante un proceso repetitivo de adición de capas, en el que la información sobre el área y el contorno de cada capa se transfieren mediante un haz láser. Podemos destacar dos diferencias fundamentales en comparación con otros procesos generativos: por un lado, el material utilizado es un polvo de metal de un solo componente, como acero inoxidable 1.4404, acero para herramientas 1.2343 o titanio TiA16V4; por otro lado, el proceso físico consiste en una refundición completa de las capas de polvo con una unión metalúrgica entre las capas y una densidad de aproximadamente el 100% en un paso. Gracias a estas características, el campo de aplicación de esta tecnología ha podido ampliarse y extenderse del prototipado rápido a la fabricación rápida de piezas funcionales y herramientas en serie. Con los materiales antes mencionados puede obtenerse una densidad cercana al 100%. Además, gracias a esta alta densidad, las piezas SLM presentan buenas propiedades mecánicas. La rugosidad y la precisión dimensional son factores decisivos para el uso y aceptación del proceso SLM en la industria. En este sentido, la rugosidad Rz de las muestras SLM se sitúa en torno a los 30 y 40 ºm y depende principalmente de la estructura de las capas y de las partículas fundidas unidas a la superficie de las piezas.
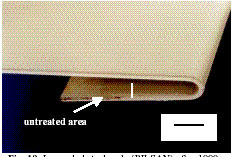
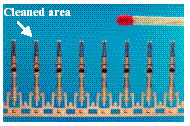
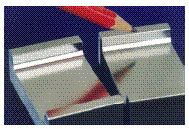
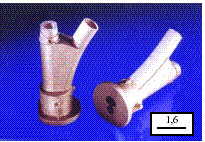
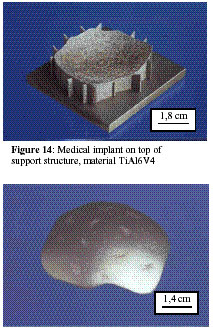
Fig. 15: Implante médico tras acabado superficial
Prototipos funcionales
Los dos objetivos más importantes que deben alcanzarse con un prototipo funcional son: la obtención de una pieza con unas propiedades similares a las de una producida en serie y la reducción del tiempo de desarrollo del producto. Ambos requisitos pueden cumplirse con ayuda de un proceso SLM. Aunque el tiempo de procesado real de una pieza pueda ser mayor debido al tiempo que requiere la producción de la capa, el proceso completo de fabricación exige bastante menos tiempo que un proceso convencional. En las tecnologías tradicionales, la producción de moldes es una fase que consume, en especial, mucho tiempo. Mediante el empleo de materiales en polvo es posible crear prácticamente cualquier tipo de geometría a partir de datos CAD; de esta manera, ya no son necesarios los materiales semiacabados ni tampoco las fases de postprocesado (por ejemplo, la creación de programas de maquinado complejos u otras fases de fabricación). En resumen: la fundición selectiva con láser permite fabricar piezas complejas en menos tiempo y a partir de materiales con propiedades en serie.
Una aplicación del láser en el prototipado es la fabricación de piezas que por lo general se crean en serie mediante moldeo por inyección de metal (MIM). El proceso SLM permitió disminuir el tiempo de fabricación de las piezas de la Figura 13 de dos semanas (incluida la producción del molde) a siete horas. El material es acero inoxidable 1.4404, que también se utiliza para la producción de piezas en serie.
Piezas individuales
Otro campo de aplicación interesante de las tecnologías SLM es la producción de implantes médicos. En los últimos años, el uso de tecnologías de prototipado rápido se ha extendido y convertido en algo común en esta área. Mediante un software especial CAD 3D se crean modelos a partir de los datos de CT (tomografía computerizada) de los pacientes y, a continuación, tomándolos como base, se crean modelos maestros mediante tecnologías de prototipado como la estereolitografía. Con la aplicación de la tecnología SLM, va a surgir una nueva cadena de proceso para los implantes médicos, una cadena en la que se va a pasar directamente de los datos CT a la fabricación del implante individual sin fases intermedias como el moldeo. En esta cadena de fabricación, mediante un sistema de producción totalmente automatizado, como una máquina SLM, se podrían fabricar piezas individuales o piezas en pequeños lotes a partir de distintos materiales. El implante que se ve en la Figura 14 y 15 ha sido fabricado en siete horas, incluidos todos los procesos posteriores, como la eliminación de la estructura de soporte y el acabado superficial. El implante está hecho en TiA16V4, una aleación de titanio con excelentes características de biocompatibilidad.
La casi ilimitada libertad geométrica ha abierto nuevas opciones en el diseño de los canales de refrigeración, algo decisivo para rentabilizar al máximo los procesos de fabricación. El diseñador de la refrigeración del molde ya no tiene que preocuparse por facilitar los procesos posteriores con tecnologías convencionales (por ejemplo, taladrado). Los canales de refrigeración pueden diseñarse, por ejemplo, de modo que estén a la misma distancia de la cavidad, adaptados a la forma de la cavidad (geometría libre) y, en general, en áreas inaccesibles para los sistemas convencionales (Figura 16). La refrigeración de geometría libre, al mejorar el enfriamiento, tiene un efecto directo en el tiempo del ciclo de inyección y en la calidad de las piezas. El intervalo del ciclo de inyección disminuye con el número de piezas producido, de modo que el diseño de canales de refrigeración especiales es una técnica perfecta para los insertos de moldes en serie. En contra de lo que ocurre con otras tecnologías de prototipado de metales, el proceso SLM permite fabricar estos insertos a partir de materiales en serie, es decir, es un proceso de fabricación rápida. La posibilidad de utilizar canales de refrigeración de geometría libre y el ahorro de tiempo hacen del proceso SLM un suplemento interesante para los métodos de fabricación de moldes tradicionales, como el EDM (maquinado por descarga eléctrica).
Conclusiones
Los ejemplos expuestos demuestran el potencial del láser en los tratamientos superficiales. Un factor esencial es la mejora de la calidad del haz (por ejemplo, barra láser de Nd:YAG) y el desarrollo de nuevos láseres de alta eficiencia (láser de Nd:YAG bombeado por diodos), avances que ayudarán a reducir los costes y contribuirán a que el láser pueda utilizarse en un mayor número aplicaciones. De cara al futuro, la investigación se ocupará también de la automatización y el control de procesos, para aumentar la fiabilidad. Por otro lado, los avances en la modelización servirán para comprender mejor el proceso y reducir el tiempo de estudio de los parámetros.
El uso de materiales de serie en el proceso SLM ofrece nuevas posibilidades en la creación de prototipos y en la fabricación directa de piezas. Además, la posibilidad de fabricar piezas con nuevas características geométricas complementa los métodos de fabricación convencionales en diversos campos (fabricación de implantes médicos, usos aeroespaciales y fabricación de herramientas y moldes). Fraunhofer ILT va a continuar sus investigaciones en cooperación con varios socios industriales con el objetivo de conseguir geometrías más complejas y ampliar la gama de materiales y materiales compuestos. En cuanto a la fabricación de herramientas y moldes, el objetivo es reducir los tiempos de manufactura, mejorar la calidad mediante refrigeración de geometría libre y aumentar la vida útil de las piezas.
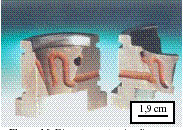
Referencias
El ministerio alemán de Educación y Ciencia (BMBF) ha financiado el proyecto “Modulare Diodenlaser- Strahlwekzeuge” (MDS) y por su parte, la CE ha financiado del proyecto “Awfors”, mediante los cuales se han obtenido algunos de los resultados sobre revestimiento por láser que se han descrito antes.