Un equipo de empresas construye el estadio de Manaus con el equipo de Terex
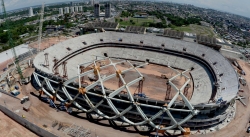
Se encuentra a 1500 km del mar, en medio de la selva amazónica, Manaus es donde el río Negro y el río Solimões discurren juntos para formar el Amazonas, el río más grande del mundo. Es también la capital del estado brasileño de Amazonia y era el centro del auge del caucho natural en el comienzo del siglo XX. Ahora, con su zona económica libre, es una parte importante de la economía de Brasil y el centro financiero de las relaciones comerciales mundiales. Manaus, se dice que es uno de los estadios más hermosos del mundo, será el anfitrión de 4 partidos durante la próxima Copa Mundial 2014.
Para la construcción del estadio "Arena da Amazonia" Manaos, se ha contado con tres compañías diferentes: Andrade Guitierrez, ENTEC y Tomiasi, que combinan sus conocimientos y equipos Terex para trabajar en uno de los estadios más innovadoras del mundo. Usaron plataformas de trabajo aéreas Genie y Torres Terex, orugas, todo terreno, accidentado y grúas.
Un diseño eficiente de energía con una capacidad máxima de 45.000 espectadores. Se han diseñado señales que simbolizan su ubicación en el Amazonas y bajo una pancarta de una copa mundial sostenible, el "Estadio de Arena Da Amazonas" cuenta con un diseño innovador y un certificado LEED.
La característica más llamativa del estadio es su techo, una estructura hecha con el apoyo mutuo de voladizos, cuya función es la de vigas de acero huecas junto con grandes canales para drenar los 2.200 mm de agua de lluvia que caen en promedio durante el año. Para hacer frente a la temperatura media de 30 ° C y 80% de humedad en Manaus, el techo del estadio será cubierto con membranas PTFE (Teflon) translúcidas que reflejan el calor, mientras que, al mismo tiempo pasa la luz. Además, la ventilación es proporcionada por paletas móviles dentro de la estructura del techo que permiten que fluya el viento y permiten una buena configuración en días sin aire.
Junto con un Sambodromo, instalaciones deportivas, piscina, centro comercial y otras instalaciones deportivas, el estadio será parte del "Complexo Esportivo Amazonas", un complejo de deporte y de ocio que se espera utilizar diariamente después de la Copa del mundo. El proyecto fue diseñado por "GMP Architekten" una firma de arquitectura alemana y la misma firma que diseñó el Commerzbank arena de Frankfurt para la Copa Mundial de 2006.
Primera fase
Las actividades de la construcción del estadio Arena Amazonas comenzaron con la demolición del estadio Vivaldão que estaba donde ahora se construye el nuevo estadio. Durante esta etapa, el césped fue recuperado y almacenado para uso futuro y un gran porcentaje del material del viejo estadio fue reciclado para su uso en la construcción del nuevo.
Cuando el viejo estadio fue demolido, comenzó la construcción de estructura básica del nuevo. Para esta fase, se sentaron bases y estructuras de soporte y dos grúas de torre de martillo Terex SK 575-32 fueron erigidas para levantar y colocar piezas prefabricadas de hormigón. Las grúas tenían alturas de 52 y 60 metros y longitudes de pluma de 54 y 59 metros, respectivamente. Las grúas tienen una capacidad máxima de 32 toneladas de carga y fueron montadas en bases de carriles más de 100 metros de largo. "Estas grúas tuvieron que recoger y colocar cientos de piezas prefabricadas que montan las gradas de asientos. Elegimos el SK por su robustez y capacidad de elevación", dijo Thiago Bezerra, ingeniero de Andrade Gutierrez S.A. "la configuración que elegimos es muy eficiente, ya que podemos cubrir una superficie grande con dos grúas de torre, esto ahorra costes y tiempo”
El montaje de la última fila de la hilera superior del Arena da Amazonia finalizó el 30 de mayo de 2012. Con esta fase completa, se acabó de construir la estructura del estadio y la fachada y la estructura del techo. El jefe de la oficina de gestión pública de proyectos para la Copa del mundo (UGP-COPA), Miguel Capobiango Neto, señaló que según el calendario, al final de la Asamblea de los stands estaba prevista en dos días. "Con este paso, nos concentraremos en el proceso de la obra, que es el sistema de techo/fachada, más sensible y complejo", dijo.
Durante la construcción de la estructura básica del estadio, las dos grúas de torre SK 575 realizaron la mayoría de los ascensores, pero cuando se necesitaban más movilidad y versatilidad, las elevación funciones fueron asumidas por Terex AC 200-1 y AC 350/6 todas las grúas de terreno, una grúa del terreno áspero RT 280 y un TC 780 camión grúa.
Las grúas todo terreno y camiones pertenecen a la empresa Entec Longhi S.A. y fueron utilizadas para múltiples tipos de elevación, para colocar componentes de acero pesados. "Para este tipo de trabajo, necesitábamos grúas que pudieran manejar la variedad de diferentes medios de elevación, tales como levantar objetos pesados y largos. Las grúas eran también necesarias para moverse de un lugar a otro, y configurarse de una forma relativamente rápida. Elegimos una CA 200-1 y una AC 350/6". Reinaldo Longhi, director de operaciones de Entec, dijo. "Hemos tenido las grúas en el sitio con el contrapeso máximo. La longitud del brazo y la capacidad de estas máquinas son muy sólidas, que ningún accesorio destinado más rápido establecer tiempos para cada nueva ubicación de elevación. Estas dos grúas manejan la mayoría de los ascensores alrededor del estadio. También trajimos un TC 780 cuando para incrementar el número de ascensores dentro del plazo limitado. Recibimos mucha lluvia, más de 2000 mm por año en promedio, así que tenemos que ser precisos y eficientes."
Las grúas se utilizaron durante 6 meses y se pusieron más de 90 ascensores. Algunos de ellos a 25 metros de altura, con un radio de 24 metros y 28 toneladas de elevación. Thiago Bezerra, ingeniero de Andrade Guitierrez comentó "de las once grúas trabajando en este sitio, ocho fueron Terex.” Durante el proceso de acabado, las plataformas de trabajo aéreas Terex asumieron un papel importante. Andrade Gutierrez ha utilizado la Genie GS 2646 de tijera eléctrica para montar los accesorios. "La GS 2646 fue diseñada para satisfacer las necesidades exigentes de la industria. Aquí estamos en un plazo muy apretado, no podemos permitirnos perder el tiempo. Por eso nos decidimos por esta plataforma extremadamente fiable y fácil de manejar. "dijo Bezerra.
La corona del estadio: el techo
El techo de este estadio proporciona funcionalidad, moderando las temperaturas y el drenaje de inmensas cantidades de agua. Las señales de diseño han sido hechas por habitantes indígenas del Amazonas. El techo autoportante es anclado a las estructuras del estadio mediante barras de lazo y de más de 200 piezas de acero más 6670 toneladas, todo con los componentes más grandes de 22 metros de largo y 30 toneladas de peso. El viaje de las piezas que componen la estructura de la azotea se inició a más 7,000 km de Portugal, donde la empresa Martifer S.A. las produce. Las piezas fueron enviadas por barco directamente al puerto de Manaus.
Después de ser descargadas, las piezas fueron cargadas a semi camiones con la ayuda de un apilador del alcance Terex TFC 45.
La construcción de la estructura de azotea de acero la parte más compleja del estadio. La construcción fue dividida en once etapas, incluyendo la erección de estructuras prefabricadas, construcción y colocación de estructuras de apoyo temporal para soportar el peso de la estructura durante la construcción y la fase final, cuando se colocan las piezas superiores. Una vez completada, la estructura se convierte autosuficiente y los soportes temporales pueden eliminarse. Una vez que las partes llegaron, el trabajo fue coordinado casi como una línea de montaje. Los barcos llegaron de Portugal periódicamente con las piezas, que fueron descargadas y transportadas donde se encontraban las grúas de Terex, previamente utilizadas para tareas de elevación prefabricadas. Se levantaron las piezas individuales de la estructura y se colocaron con una grúa Terex CC en 2400-1, perteneciente a Tomiasi.
Antes de ser unidos, los sub-ensambles parciales necesitaban ser levantados. Esta era la tarea del CC 2400-1 perteneciente a ingeniería Tomiasi. "Somos una de las mayores empresas de trabajo pesado en la región norte, y el CC 2400-1 es una de nuestras "herramientas" más usadas. Tuvimos que levantar los sub-ensambles parciales de hasta 92 toneladas de peso. Al principio, estábamos trabajando en un radio de 20 metros o menos y no necesitamos usar el contrapeso adicional superlift, pero cuando tuvimos que colocar el techo atado bien dentro del estadio, el radio era mucho más grande, así que lo conectamos.", dijo Marcelo Vinhote da Silva, commercial analyst de Tomiasi. "Vamos muy bien de tiempo y esperamos estar aquí hasta el final del año."
Una vez que la estructura de azotea está terminada y es autosuficiente, el último paso es instalar la membrana PTFE. Se espera que se produzca a finales de 2013.